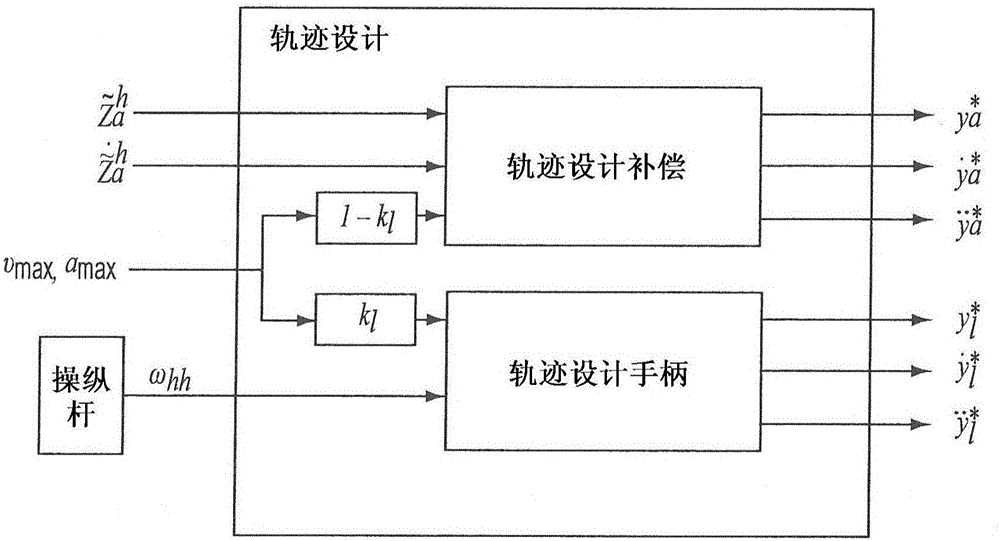
本发明涉及用于起重机的起重机控制器,该起重机包括用于提升悬挂在缆绳上的负载的提升齿轮(hoistgear)。根据本发明,起重机控制器包括主动升降补偿,主动升降补偿通过致动提升齿轮而至少部分地补偿由于升降而导致的缆绳悬挂点和/或负载堆积点的移动。起重机控制器还包括操作员控制件,操作员控制件参考操作员指定而致动提升齿轮。
背景技术:例如,从DE102008024513A1中已知的这种起重机控制器。提供了预测装置,预测装置参考被确定了的当前的升降移动和升降移动的模型而预测缆绳悬挂点的未来移动,其中,路径控制器当致动提升齿轮的时候考虑所预测的移动。但是,已知的起重机控制器对于一些需求不是足够灵活的。此外,在升降补偿失败的情况下可能发生问题。
技术实现要素:因此,本发明的目的是,提供改进了的具有主动升降补偿件和操作员控制件的起重机控制器。根据本发明,在第一方面,提供一种用于起重机的起重机控制器,所述起重机包括用于提升悬挂在缆绳上的负载的提升齿轮,所述起重机控制器包括:主动升降补偿件,所述主动升降补偿件通过致动所述提升齿轮而至少部分地补偿由于所述升降导致的所述缆绳的悬挂点和/或负载堆积点的移动,以及操作员控制件,所述操作员控制件参考所述操作员的指定而致动所述提升齿轮,所述提升齿轮的至少一个运动学约束量的分割能够在升降补偿件与操作员控制件之间调节。在第二方面,提供一种用于起重机的起重机控制器,所述起重机包括用于提升悬挂在缆绳上的负载的提升齿轮,特别地,该起重机控制器为根据上述的起重机控制器,包括主动升降补偿件,其通过致动所述提升齿轮而至少部分地补偿由于所述升降导致的所述缆绳的悬挂点和/或负载堆积点的移动,以及操作员控制件,其参考所述操作员的指定而致动所述提升齿轮,所述控制器包括两个分离的路径设计模块,通过所述两个分离的路径设计模块,用于所述升降补偿件和所述操作员控制件的轨迹彼此分离地计算,从而实现这个目的。在第一方面,本发明显示了用于起重机的起重机控制器,包括用于提升悬挂在缆绳上的负载的提升齿轮。提供了主动升降补偿件,主动升降补偿件通过致动提升齿轮而至少部分地补偿由于升降导致的缆绳悬挂点和/或负载堆积点的移动。而且,提供了操作员控制件,其参考操作员的指定而致动提升齿轮。根据本发明,提升齿轮的至少一个运动学约束量的分割可在升降补偿件和操作员控制件之间调节。这样,起重机操作员自己可以分开提升齿轮的该至少一个运动学约束量,从而确定它的哪个部分是对于升降的补偿可用的以及哪个部分是对于操作员控制件可用的。提升齿轮的该至少一个运动学约束量例如可以是提升齿轮的最大可用功率和/或最大可用速度和/或最大可用加速度。提升齿轮的该至少一个运动学约束量的分割因此可以包括提升齿轮的最大可用功率和/或最大可用速度和/或最大可用加速度的分割。有利地,通过至少一个加权因子实现该至少一个运动学约束量的分割,通过该至少一个加权因子,提升齿轮的最大可用功率和/或速度和/或加速度在升降补偿件和操作员控制件之间分开。特别地,提升齿轮的最大可用速度和/或最大可用加速度可以由起重机操作员在升降补偿件和操作员控制件之间分开。有利地,至少在部分区域上,可无级地调节该分割。因此,对于起重机操作员变得可能的是,敏感地分开提升齿轮的至少一个运动学约束量。根据本发明,可以进一步可能的是,通过将提升齿轮的全部的至少一个运动学约束量分配至操作员控制件而关断升降补偿件。因此变成可能的是,通过分割的调节而同时完全地关断主动升降补偿件。有利地,从被完全地关断的操作员控制件和/或朝向被完全地关断的操作员控制件,可以进行提升齿轮的该至少一个运动学约束量的分割的无级调节是可能的。这使得能在纯操作员控制件与主动升降补偿件之间实现稳定转换。在第二方面,本发明包括用于起重机的起重机控制器,该起重机包括用于提升悬挂在缆绳上的负载的提升齿轮。起重机控制器包括主动升降补偿件,该主动升降补偿件通过致动提升齿轮而至少部分地补偿由于升降导致的缆绳悬挂点和/或负载堆积点的移动。而且提供操作员控制件,该操作员控制件参考操作员的指定而致动提升齿轮。根据本发明,控制器包括两个分离的路径设计模块,通过该两个分离的路径设计模块,用于升降补偿件的轨迹和用于操作员控制件的轨迹彼此独立地计算。在升降补偿失败的情况下,起重机因此可以仍然通过操作员控制件而致动,而不用必须使用针对这个目的的单独的控制单元,并且如果没有这个,将导致不同的操作行为。有利地,在该两个分离的路径设计模块中,提升齿轮的位置和/或速度和/或加速度的轨迹均被计算。而且有利地,由该两个分离的路径设计模块指定的轨迹被累计并且用作用于提升齿轮的控制和/或调节的设定点值。此外,可以设置,使得提升齿轮的控制将测量值反馈到提升绞盘(winch)的位置和/或速度,因此比较了设定点值与实际值。而且,提升齿轮的致动可以考虑提升绞盘的驱动的动力学。特别地,可提供相应的引导控制以实现这个目的。有利地,其基于提升绞盘的驱动的动力学的物理模型的反转。有利地,该两个分离的路径设计模块每个独立地考虑该驱动的至少一个约束,并且因此产生可以实际地被提升齿轮接近的目标轨迹。有利地,起重机控制器在升降补偿件和操作员控制件之间分割至少一个运动学约束量。特别地,提升齿轮的最大可用功率和/或最大可用速度和/或最大可用加速度在升降补偿件和操作员控制件之间分开。有利地,在两个分离的路径设计模块中的轨迹然后被计算,考虑了相应地分配的至少一个运动学约束量,特别地,分别用于升降补偿件和操作员控制件的最大可用功率和/或速度和/或最大可用加速度。通过该至少一个运动学约束量的分割,控制变量约束可能不被完全地利用。但是,该至少一个运动学约束量的分割提供了使用两个完全独立的路径设计模块,其每个独立地考虑驱动约束。根据本发明的第一和第二方面每个被单独地主张,并且可以被独立地实现。但是,特地有利地,根据本发明的两个方面相互组合。特别地,根据本发明的第二方面的两个独立的路径设计模块的使用提供了该至少一个运动学约束量的分割的特别容易的可调性。特别地,可以由起重机操作员指定该至少一个运动学约束量的多少是可用于操作员控制件和升降补偿件的,其中,然后当计算用于致动提升齿轮的目标轨迹时,考虑这个分割作为两个路径设计模块的约束。在根据上文中描述的方面中的一个的起重机控制器中,根据本发明的升降补偿件可以包括优化功能,优化功能参考缆绳悬挂点和/或负载堆积点的所预测移动并且考虑可用于升降补偿件的功率而计算轨迹。特别地,计算了用于致动提升齿轮的轨迹,其考虑可用于升降补偿件的功率而尽可能地补偿了缆绳悬挂点和/或负载堆积点的所预测的移动。特别地,轨迹可以最小化由于缆绳悬挂点的移动和/或由于升降而发生的负载和负载堆积点之间的差动移动而导致的负载的残余移动。根据本发明的起重机控制器有利地包括预测装置,该预测装置参考所确定的当前升降移动和升降移动的模型而预测缆绳悬挂点和/或负载堆积点的未来移动,其中,提供测量装置,其参考传感器数据确定当前的升降移动。特别地,预测装置预测缆绳悬挂点和/或负载堆积点在竖直方向上的未来移动。在竖直方向上的移动在另一方面可以被忽略。可以配置预测装置和/或测量装置,诸如在DE102008024513A1所述。操作员控制件还可以参考操作员指定并且考虑可用于操作员控制件的至少一个运动学约束量而计算轨迹。有利地,操作员控制件因此也考虑了可最大用于操作员控制件的至少一个运动学约束量,并且因此计算了根据操作员的指定而致动提升齿轮的轨迹。通过考虑各自可用的至少一个运动学约束量,保证了提升齿轮可实际地沿行指定的轨迹。有利地,轨迹的确定均在上文中描述的路径设计模块中实现。有利地,起重机控制器包括至少一个控制元件,通过该至少一个控制元件,起重机操作员可以调节可用的至少一个运动学约束量的分割,并且特别地,可以指定加权因子。在根据本发明的起重机控制器中,可用的至少一个运动学约束量的分割有利地可以在提升过程中变化。因此,当需要更快提升时,起重机操作员能够例如为操作员控制件提供更多的功率。另一方面,当起重机操作员感觉到升降没有被足够地补偿时,可将更多功率提供到升降补偿件。例如,起重机操作员因此能够对于天气和升降的变化做出灵活反应。有利地,可用的至少一个运动学约束量的分割的变化通过改变加权因子而实现,如上文中描述的一样。有利地,根据本发明的起重机控制器包括计算功能,计算功能计算当前可用的至少一个运动学约束量。特别地,可以计算提升齿轮的最大可用功率和/或速度和/或加速度。由于提升齿轮的最大可用功率和最大可用速度和/或加速度可在提升期间改变,因此其可以通过该计算功能而适应于提升的当前环境。有利地,计算功能考虑了展开的缆绳的长度和/或缆绳力和/或可用于驱动提升齿轮的功率。例如,取决于展开的缆绳的长度,提升齿轮的最大可用速度和/或加速度可以是不同的,原因在于,特别在用非常长的缆绳提升的期间,展开的缆绳的重量在提升齿轮上施加载荷。此外,提升齿轮的最大可用速度和/或加速度可根据被提升的负载的质量而波动。而且,特别地,当使用具有蓄能器(accumulator,蓄电池)的混合驱动时,可用于驱动提升齿轮的功率可以根据蓄能器条件而波动。有利地,这将也被考虑。根据本发明,当前可用的至少一个运动学约束量均有利地根据起重机操作员的指定而在被升降补偿件和操作员控制件之间分开,特别地,参考由起重机操作员指定的加权因子。有利地,升降补偿件的优化功能最初可以包括在可用的至少一个运动学约束量的分割上的变化和/或在仅仅在预测跨度(horizon,范围)的末端处的提升期间可用的至少一个运动学约束量的变化。这在整个预测跨度上提供了稳定的优化功能。有利地,随着前行时间,被改变了的可用的至少一个运动学约束量则将被推过(pushthrough)到预测跨度的起点。有利地,根据本发明的升降补偿件的优化功能确定了被包括在提升齿轮的控制和/调节中的目标轨迹。特别地,目标轨迹意图指定提升齿轮的目标移动。优化可以通过离散化而实现。根据本发明,优化可以基于负载提升点的移动的更新预测而在每个时间步实现。根据本发明,目标轨迹的第一值均可用于控制提升齿轮。当更新了的目标轨迹当时是可用时,仅仅轮到其第一值被用于控制。根据本发明,可以用比控制更大的扫描时间来进行优化功能。这使得计算密集型优化功能能够选择更多的扫描时间,另一方面,对于计算密集度较小的控制,由于扫描时间较少,提供了更大的精度。而且,当没能找到有效解时,可以使得优化功能利用紧急轨迹设计。这样,当无法找到有效解时,适当的操作也被保证。有利地,操作员控制件参考由操作员通过输入装置指定的信号而计算操作员所期望的提升绞盘的速度。特别地,可以设置手柄。可以针对操作员控制件而计算期望的速度,作为由输入装置的位置指定的最大可用速度的一部分。有利地,通过最大可容许正冲击的积分而产生目标轨迹,直到达到最大加速度。因此保证了,操作员控制件不会使得提升齿轮过载。有利地,最大加速度对应于提升齿轮的最大可用加速度的被分配到操作员控制件的那部分。而且有利地,速度于是通过最大加速度的积分而增加,直到通过增加(加入)最大负冲击可实现所期望速度。因此保证了,在实现目标速度方面,加速度再次减小到零,使得在达到目标速度时由于加速度跳变造成的不必要的负载得以避免。本发明还包括具有如上所述的起重机控制器的起重机。特别地,起重机可以设置在浮码头(pontoon)上。特别地,起重机可以是甲板起重机(deckcrane)。替换地,它也可以是离岸起重机、码头起重机或者缆索挖掘机。本发明还包括具有根据本发明的起重机的浮码头,特别地,具有根据本发明的起重机的船。此外,本发明包括用于提升和/或降低定位在水中的负载的根据本发明的起重机和根据本发明的起重机控制器的使用,和/或用于从定位在水中(例如,在船上)的负载堆积位置提升负载和/或降低负载到定位在水中(例如,在船上)的负载堆积位置的根据本发明的起重机和根据本发明的起重机控制器的使用。特别地,本发明包括用于深海提升和/或用于装载和/或卸载船的根据本发明的起重机和根据本发明的起重机控制器的使用。本发明还包括用于控制包括用于提升悬挂在缆绳上的负载的提升齿轮的起重机的方法。有利地,升降补偿件通过提升齿轮的自动致动而至少部分地补偿由于升降导致的缆绳悬挂点和/或负载堆积点的移动。而且,通过操作员控制件,参考操作员指定,而制造提升齿轮。根据本发明,根据第一方面,提升齿轮的至少一个运动学约束量在升降补偿件和操作员控制件之间可变地分开。根据第二方面,用于升降补偿件和用于操作员控制件的轨迹彼此分离地计算。根据本发明的方法因此提供在上文中已经关于起重机控制器描述的相同优点。再次,两个方面特别优选地被相互组合。优选地,如已经根据本发明关于起重机控制器及其功能详细阐述的这样地执行该方法。而且有利地,根据本发明的方法起到的作用与已经在上文中阐述的一样。特别地,可通过如已在上文中阐述的一样的起重机控制器和/或通过如已在上文中阐述的一样的起重机来执行根据本发明的方法。本发明还包括具有用于执行根据本发明的方法的编码的软件。特别地,软件可以存储在机器可读数据载体中。有利地,根据本发明的起重机控制器可通过在起重机控制器上安装根据本发明的软件而实现。附图说明现在将被参考示例性的实施例和图详细地解释本发明。在图中:图1:显示了设置在浮码头上的根据本发明的起重机,图2:显示了用于升降补偿件和操作员控制件的分离的轨迹设计的结构,图3:显示了用于具有稳定冲击的设计轨迹的四阶积分器链(integratorchain),图4:显示了用于轨迹设计的不等距离散化,其朝向时间跨度的末端使用比在时间跨度的起点处更大的距离,图5:使用速度的实例显示了如何首先在时间跨度的末端处考虑变化的约束,图6:显示了用于操作员控制件的轨迹设计的三阶积分器链,其参考冲击增加(加入)而工作,图7:显示了操作员控制件的路径设计的结构,其考虑了驱动的约束,图8:显示了具有相关切换时间的示例性的冲击曲线(轮廓线,profile),用于参考路径设计而计算提升齿轮的位置和/或速度和/或加速度的轨迹,图9:显示了用冲击加入产生的速度和加速度轨迹的路线,图10:显示了具有主动升降补偿件和目标力模型(这里称为恒定张力模型)的驱动概念的综述,图11:显示了主动升降补偿件的致动的模块电路图,以及图12:显示了用于目标力模型的致动的模块电路图。具体实施方式图1显示了具有用于致动提升齿轮5的根据本发明的起重机控制器的起重机1的示例性的实施例。提升齿轮5包括用于移动缆绳4的提升绞盘。在起重机中,缆绳4在缆绳悬挂点2(在该示例性的实施例中,在起重机吊架的端部处的偏转滑轮)的上方引导。通过移动缆绳4,悬挂在缆绳上的负载3可以提升或者降下。可以设置至少一个传感器,其测量提升齿轮的位置和/或速度并且传输相应信号到起重机控制器。而且,可以设置至少一个传感器,其测量缆绳力并且传输相应信号到起重机控制器。传感器可以设置在起重机主体的区域中,特别地,在绞盘的固定架(mount)上和/或在缆绳滑轮的固定架上。在示例性的实施例中,起重机1设置在浮码头6上,这里是船。如同样显示在图1中的一样,浮码头6由于升降而绕其六个自由度而移动。设置在浮码头6上的起重机1和缆绳悬挂点2因此也移动。根据本发明的起重机控制器可以包括主动升降补偿件,主动升降补偿件通过致动提升齿轮而至少部分地补偿由于升降导致的缆绳悬挂点2的移动。特别地,由于升降导致的缆绳悬挂点的竖直移动至少部分地得到补偿。升降补偿件可以包括测量装置,测量装置从传感器数据确定当前升降移动。测量装置可以包括设置在起重机底座(foundation)处的传感器。特别地,这可以是陀螺仪和/或倾角传感器。特别优选地,设置三个陀螺仪和三个倾角传感器。而且,可以设置预测装置,其参考确定的升降移动和升降移动的模型而预测缆绳悬挂点2的未来移动。特别地,预测装置仅预测缆绳悬挂点的竖直移动。连同测量装置和/或预测装置,在测量装置的传感器的点处的船的移动可能可以被转换成缆绳悬挂点的移动。预测装置和测量装置有利地配置,像更详细描述在DE102008024513A1中的一样。替换地,根据本发明的起重机也可以是用于从设置在浮码头上的负载堆积点提升负载和/或降低负载到设置在浮码头上的负载堆积点的起重机,其因此随升降而移动。在这种情况下,预测装置必须预测负载堆积点的未来移动。这可以与上文描述的过程类似地实现,其中,测量装置的传感器设置在负载堆积点的浮码头上。起重机例如可以是码头起重机、离岸起重机或者缆索挖掘机。在示例性实施例中,提升齿轮5的提升绞盘被液压地驱动。特别地,设置液压泵和液压马达的液压回路,用于驱动提升绞盘。优选地,可以设置液压蓄能器,在降低负载时,其存储能量,使得当提升负载时可使用该能量。替换地,可以使用电驱动。电驱动也可以与能量蓄能器连接。在下文中,现在将显示本发明的示例性实施例,其中,本发明的大多数方面被结合地实现。但是,单独方面也可以被单独使用,以发展本发明的实施例,如在本申请的一般部分中描述的一样。1参考轨迹的设计为了实现主动升降补偿件的所需预测行为,使用包括引导控制和两自由度结构形式的反馈的顺序控制。由微分参数化法计算引导控制并且这需要稳定地可微分两次的参考轨迹。对于设计,决定了,该驱动可以沿该特定轨迹。因此,提升齿轮约束也必须被考虑。该考虑的起始点是,缆绳悬挂点的竖直位置和/或速度和其例如通过在DE102008024513中描述的算法,在固定的时间跨度上预测。此外,起重机操作员的手柄信号也包括在轨迹设计中,操作员通过该信号在惯性坐标系中移动负载。为了安全原因,在主动升降补偿失败的情况下,绞盘也可以仍然通过手柄信号而移动,这是必需的。利用用于轨迹设计的所使用的概念,用于补偿移动的参考轨迹的设计与从手柄信号产生的那些之间的分离得以实现,如显示在图2中的一样。在图中,和表示设计用于补偿的位置、速度和加速度,而和表示如基于手柄信号设计的用于叠加的缆绳的展开或者缠绕的位置、速度和加速度。在进一步执行的过程中,所设计的用于提升绞盘的移动的参考轨迹总是分别用y*,和表示,因为它们用作驱动动力学的系统输出的参考。由于分离的轨迹设计,当升降补偿件关断或者在手工操作中手柄控制的升降补偿件完全失败(例如,由于惯性测量单元(IMU)的故障)的情况下,可以使用相同的轨迹设计和相同的顺序控制器,从而产生与接通升降补偿件时相同的操作行为。为了不违反给定的速度vmax和加速度amax上的约束(不管是否完全独立的设计),vmax和amax通过加权因子0≤kl≤1(参见图2)分割。其被起重机操作员指定,因此提供了,单独地分割对于补偿和/或对于移动负载可用的功率。因此,补偿移动的最大速度和加速度是(1-kl)vmax和(1-kl)amax并且对于被叠加的缆绳的展开和缠绕的轨迹是klvmax和klamax。kl的改变可以在工作期间执行。由于最大的可能行进速度和加速度取决于缆绳和负载的总质量,因此vmax和amax也可以在工作中改变。因此,可分别适用的值同样地被传递到轨迹设计。通过分割功率,控制可变约束可能没有被完全利用,但是起重机操作员可以容易地和直观地调节主动升降补偿件的作用。kl=1的加权等于关断主动升降补偿件,由此被接通和关断的补偿之间的平滑转换变成可能的。本章的第一部分初始地解释了,用于补偿缆绳悬挂点的竖直移动的参考轨迹和的产生。这里,本质方面是,由于给定约束由Kl设定,利用所设计的轨迹,尽可能地补偿了竖直移动。因此,通过在全部时间跨度上预测的缆线悬挂点的竖直位置和速度和最优控制问题因此用公式表示,其被循环地求解,其中Kp表示预测的时间步的数量。随后讨论相关的数字解和执行。本章的第二部分进行用于移动负载的轨迹和的设计。其直接地从起重机操作员的手柄信号whh产生。通过最大可容许冲击的加入而实现计算。1.1用于补偿的参考轨迹在用于提升绞盘的补偿移动的轨迹设计中,必需从缆绳悬挂点的预测竖直位置和速度(考虑了有效驱动约束)而产生足够平滑的轨迹。这个任务随后被认为是约束的最优问题,可以在每个时间步骤,在线地解决该问题。因此,方法与模型预测控制的设计是类似的,但是,是在模型预测轨迹产生的意义上。作为用于优化的参考或者设定点值,使用了缆绳悬挂点的竖直位置和速度和其在具有Kp个时间步的全部时间跨度上的时间tk处被预测,并且用相应的预测时间计算,例如,通过描述在DE102008024513中的算法。考虑通过kl,vmax和amax有效的约束,最佳时间顺序于是可以被确定(针对补偿移动)。但是,与模型预测控制类似,仅仅如此计算出的轨迹的第一值用于顺序控制。在下一个时间步中,用缆绳悬挂点的竖直位置和速度的更新的(因此更精确)预测来重复优化。与传统的模型预测控制相比,具有连续控制的模型预测轨迹生成的优点一方面在于,控制部和相关稳定化可以用与轨迹生成相比更多的扫描时间来计算。因此,计算密集型优化可以转换成更慢的任务。在这个概念中,另一方面,紧急功能可以独立于用于优化没有找到有效解的情况的控制而实现。它包括被简化的轨迹设计,在这种紧急情况下,控制依赖于该被简化了的轨迹设计,并且该设计进一步地致动绞盘。1.1.1用于设计补偿移动的系统模型为了满足用于补偿移动的参考轨迹的稳定性的要求,它的三阶导数最早可以被认为是可跳变的。但是,考虑绞盘寿命,在补偿移动中在冲击上的跳变应当被避免,因此仅仅四阶导数可以被认为是可跳变的。因此,冲击必需至少被稳定地设计,并且用于补偿移动的轨迹生成参考图示在图3中的四阶积分器链而实现。在该优化中,其用作系统模型并且可以被在状态空间中表达为:ya=Xa这里,输出包括用于补偿移动的设计轨迹。为了用公式表示最佳控制问题并且考虑未来的实施,这个时间连续模型初始地在点阵上离散其中,Kp代表用于缆绳悬挂点的竖直移动的预测的预测步骤的数量。为了区分轨迹生成中的离散时间表示和离散系统时间tk,它用τk=kΔτ表示,其中,k=0,…,Kp并且Δτ是用于轨迹生成的跨度Kp的离散间隔。图4图示了选择的点阵是不等距的,使得在跨度上必需的支撑点的数量减小。因此,可以保持待解决的最佳控制问题的维度小。朝向跨度的末端更粗的离散化的影响对于设计轨迹没有不利影响,因为竖直位置和速度的预测朝向预测跨度的端部是较不精确的。可以参考解析解来精确地计算出对于这个点阵有效的时间离散系统表示对于来自图3的积分器链,它遵循ya(τk)=xa(τk),k=0,...,Kp-1,其中Δτk=τk+1-τk描述了对于各自的时间步而有效的离散步宽度。1.1.2最佳控制问题的公式化和求解通过求解最佳控制问题,将设计轨迹,其尽可能近地遵循缆绳悬挂点的被预测的竖直移动并且同时满足给定的约束。为了满足这个要求,优质函数如下列一样:其中,wa(τk)表示在各自时间步处有效的参考。由于这里仅仅缆绳悬挂点的预测位置和速度是可用的,因此相关的加速度和冲击设定为零。但是,这个不一致的指定(specification)的影响可以通过加速度和冲击偏差的相应加权而保持较小。因此:在正的半定(positivelysemidefinite)的对角矩阵上Qw(τk)=diag(qw,1(τk),qw,2(τk),qw,3,qw,4),k=1,...,Kp(1.7)从参考的偏差在优质函数中被加权。标量因子ru估计校正成果。虽然在整个预测跨度上ru、qw,3和qw,4是恒定的,但是qw,1和qw,2依赖于时间步τk选择。在预测跨度的起点处的参考值因此可以比在末端处的参考值更强地加权。因此,随着增大预测时间而减小的竖直移动预测的精确度可以在优质函数中描述。由于对于加速度和冲击的参考不存在,所以权数qw,3和qw,4仅仅处罚从零的偏差,因此,它们选定为比用于位置qw,1(τk)和速度qw,2(τk)的权数更小。用于最佳控制问题的相关的约束从驱动的可用功率和当前选择的加权因子kl(参见图2)中得出。因此,它适用于来自(1.4)的系统模型的状态:以及输入:这里,δa(τk)代表缩减因子,该缩减因子选择使得在跨度的末端处的各自的约束合计为在跨度的起点处的约束的95%。对于中间时间步,δa(τk)从线性插值得出。沿着跨度的约束的缩减相对于存在的可容许的解增大了方法的鲁棒性。虽然在工作中速度和加速度约束可以改变,冲击jmax和冲击的导数的约束是恒定的。为了增加提升绞盘和整个起重机的使用寿命,它们在最大可容许冲击负载方面被选择。对于位置状态,没有约束是可适用的。由于在工作中的最大速度vmax和加速度amax和功率的加权因子kl被外部地确定,因此速度和加速度约束也必然地对于最佳控制问题改变。被呈现的概念如下列一样考虑了相关的时变约束:约束一被改变,则更新的值首先就仅仅在对于时间步的预测跨度的末端处考虑。随着前行时间,它然后被推到预测跨度的起点。图5图示了这个过程(参考速度约束)。当减小约束时,应当附加地注意,其适合于其最大可容许导数。这表示,例如,速度约束(1-kl)vmax最大地可以如当前加速度约束(1-kl)amax允许的那么快地减小。因为更新的约束被完成(pushthrough),所以对于存在于约束中的初始条件xa(τ0)的解总是存在,其又不会违反更新的约束。但是,它将占用全部预测跨度,直到改变了的约束最终影响在跨度的起点处的设计轨迹。因此,最佳控制问题由将待被最小化的二次优质函数(1.5)、系统模型(1.4)和来自于(1.8)和(1.9)的不等式约束(线性二次方程优化问题(对于二次方程编程问题的QP问题)形式的)完整地给出。当第一次执行优化时,初始条件选定为xa(τ0)=[0,0,0,0]T。随后,在最后的优化步骤中被对于时间步τ1计算出的值xa(τ1)用作初始条件。在每个时间步,QP问题的实际解的计算通过称为QP解算器的数值方法而实现。由于用于优化的计算努力,用于补偿移动的轨迹设计的扫描时间大于主动升降补偿件的所有剩余元件的离散化时间;因此,Δτ>Δt。为了保证参考轨迹可用于更快速率下的控制,来自图3的积分器链的模拟在优化之外,用更快扫描时间Δt进行。一旦从优化中获得新值,则状态xa(τ0)就用作用于模拟的初始条件,并且在预测跨度的起点处的校正变量ua(τ0)作为恒定输入写在积分器链中。1.2用于移动负载的参考轨迹与补偿移动类似,可两次稳定地微分的参考轨迹对于叠加的手柄控制(参见图2)是必需的。当具有这些可由起重机操作员指定的移动时,对于绞盘,通常不期望有方向的快速变化,还发现,稳定设计的加速度的最小要求相对于绞盘的使用寿命是足够的。因此,与针对移动补偿设计的参考轨迹对比,对应于冲击的三阶导数已经可以被认为是可跳变的。如显示在图6中的一样,它也作为三阶积分器链的输入。除了关于稳定性的要求,设计轨迹也必须满足当前有效的速度和加速度约束,发现,对于手柄控制,将是klvmax和klamax。将起重机操作员的手柄信号-100≤whh≤100解释为,相对于当前最大可容许速度klvmax的相对速度设定(specification)。因此,根据图7,由手柄指定的目标速度是:如可见的,由手柄当前指定的目标速度取决于手柄位置whh、可变加权因子kl和当前最大可容许绞盘速度vmax。对于手柄控制的轨迹设计的任务现在可以表示如下:从手柄指定的目标速度开始,可产生可稳定微分的速度曲线,使得加速度具有稳定过程。作为用于这个任务的过程,通常所谓的冲击加入是值得推荐的。基本思想是,在第一阶段,最大可容许冲击jmax作用于积分器链的输入,直到达到最大可容许加速度。在第二阶段,速度以恒定加速度增大;以及在最后阶段,最大可容许负冲击被加入,使得达到期望的最终速度。因此,仅仅各个阶段之间的切换时间必须在冲击加入中确定。图8显示了,用于速度变化的冲击的示例性过程(与切换时间一起)。Tl,0表示重新设计发生的时间。时间Tl,1、Tl,2和Tl,3均表示各个阶段之间的计算出的切换时间。它们的计算在下列段落中概述。一旦对于手柄控制的新情况发生,则对生成的轨迹进行重新设计。用于手柄控制的目标速度或者当前有效的最大加速度klamax一变化,则新情况就发生。目标速度可以由于新的手柄位置whh或者由于kl或者vmax(参见图7)的新的指定而变化。类似地,通过kl或者amax的最大有效加速度的变化是可能的。当重新设计轨迹时,那个速度初始地从当前设计的速度和通过到零的加速度缩减而获得的相应加速度计算出:其中,最小必需时间由下式给出:并且,表示积分器链的输入,即,被加入的冲击(参见图6):依赖于当前设计的加速度被发现将是依赖于理论计算出的速度和期望的目标速度,输入的过程现在可以被表示出。如果则没有达到期望的值并且加速度可以进一步增大。但是,如果则太快并且加速度必须立即减小。从这些考虑因素,冲击的下列切换顺序可以对于三个阶段推导:其中ul=[ul,1,ul,2,ul,3]和输入信号ul,i被相应阶段加入。阶段的持续时间发现是ΔTi=Tl,i-Tl,i-1,其中i=1,2,3。因此,在第一阶段的末端处,设计出的速度和加速度是:以及在第二阶段之后:其中ul,2被假定=0。在第三阶段之后,最终,它遵循:对于切换时间Tl,i的精确计算,加速度约束起初被忽略,因此ΔT2=0。由于这个简化,两个剩余的时间间隔的长度可以如下表示:其中,代表实现的最大加速度。通过将(1.21)和(1.22)插入进(1.15)、(1.16)和(1.19)中,获得方程组,其可以被对求解。考虑最终获得如下:从在(1.21)和(1.22)中ΔT1和ΔT3条件,的符号必须是正的,。在第二步骤中,和最大可容许加速度klamax导致实际的最大加速度:相同地,真实发生时间间隔ΔT1和ΔT3最终可以被计算出。它们从(1.21)和(1.22)中用产生。仍然未知的时间间隔ΔT2现在从(1.17)和(1.19)中,用来自(1.21)和(1.22)的ΔT1和ΔT3确定为其中从(1.15)得出。切换时间可以直接从时间间隔获得:Tl,i=Tl,i-1+ΔTi,i=1,2,3.(1.26)待设计的速度和加速度曲线和可以利用各个切换时间而解析计算出。应当提到,通过切换时间设计的轨迹经常没有被完全地经过,因为在到达切换时间Tl,3之前,新情况发生,因此进行了重新设计,并且新的切换时间必须计算。如已经提到的一样,新情况通过whh、vmax、amax或者kl的变化而发生。图9显示了通过实例方式呈现的方法产生的轨迹。轨迹的路线包括可以由于(1.24)而发生的两种情况。在第一种情况中,最大可容许加速度在时间t=1秒处达到,后面是,具有恒定加速度的阶段。第二种情况发生在时间t=3.5秒处。这里,由于手柄位置,最大可容许加速度没有被完全达到。结果是,第一和第二切换时间一致,并且ΔT2=0适用。根据图6,相关位置路线通过速度曲线积分而计算出,其中,在系统开始处的位置通过当前从提升绞盘中展开的缆绳长度而初始化。2用于提升绞盘的致动概念原则上,致动包括两个不同的工作模式:主动升降补偿,用于从具有自由悬挂负载的船去耦该竖直负载移动;和恒定张力控制,用于避免一旦负载堆积在海床上就松弛缆绳。在深海起重期间,升降补偿件最初是其作用的。参考堆积操作的检测,自动地实现到恒定张力控制的切换。图10用相关参考和控制变量图示了总的概念。但是,两个不同的工作模式中的每个也可以被各自地实现,而没有另一工作模式。而且,如将在下文中描述的一样,恒定张力模式也可以独立于船上的起重机的使用和独立于主动升降补偿件而使用。由于主动升降补偿件,提升绞盘应当被致动,使得绞盘移动补偿了缆绳悬挂点的竖直移动,并且起重机操作员通过手柄在被认为是惯性的h坐标系中移动负载。为了保证致动具有所需要的用于最小化补偿误差的预测行为,它通过引导控制和稳定化部件(两自由度结构的形式的)实现。引导控制通过绞盘动力学的平输出,从微分参数化法而计算出,并且由用于移动负载的设计轨迹和以及用于补偿移动的负轨迹和(参见图10)产生。获得的用于驱动动力学和绞盘动力学的系统输出的目标轨迹表示为和它们代表用于绞盘移动以及因此用于缆绳的缠绕和展开的目标位置、速度和加速度。在恒定张力阶段期间,在负载处的缆绳力Fsl将被控制到恒定量,以免松弛缆绳。手柄因此在这个工作模式中被无效,并且基于手柄信号设计的轨迹不再被加入。绞盘的致动依次又由具有引导控制和稳定化部件的两自由度结构实现。精确负载位置zl和在负载处的缆绳力Fsl不可用作用于控制的测量量,因为由于长缆绳长度和大深度,因此起重机钩没有装配传感器单元。而且,不存在所悬挂负载的类型和形状的信息。因此,各个负载的特定参数(比如,负载质量ml、在质量上流体动力学增加的系数Ca、阻力系数Cd和浸入的体积)通常是不知道的,因此负载位置的可靠的估计在实际中几乎是不可能的。因此,仅仅展开的缆绳长度ls和相关速度以及在缆绳悬挂点处的力Fc可用作用于该控制的测量量。长度ls从利用增量编码器测量的绞盘角度和取决于缠绕层jl的绞盘半径rh(jl)间接地获得。相关缆绳速度可以通过具有适当低通滤波的数值微分法计算。施加到缆绳悬挂点的缆绳力Fc通过力测量销而检测。2.1用于主动升降补偿件的驱动图11图示了具有在频率范围内的模块电路图的用于主动升降补偿件的提升绞盘的致动。可以看到,从驱动的局部系统Gh(s)仅仅实现了缆绳长度和速度yh=ls和的反馈。结果,作为输入干扰而作用在缆绳系统Gs,z(s)上的缆绳悬挂点的竖直移动的补偿纯粹作为引导控制而进行;缆绳和负载动力学被忽略。由于输入干扰或者绞盘移动的不完全补偿,所以引起了固有缆绳动力学,但是在实际中,可以假定得到的负载移动在水中被极大地减弱并且衰退非常快。驱动系统的从校正变量Uh(s)到展开缆绳长度Yh(s)的传递函数可以近似为IT1系统并且产生:具有绞盘半径rh(jl)。由于该系统输出Yh(s)同时表示平输出(flatoutput),因此反向引导控制F(s)将是:并且可以被以微分参数化法形式在时域中写为:(2.3)显示用于引导控制的参考轨迹必须是可至少两次稳定微分的。包括稳定化Ka(s)和绞盘系统Gh(s)的闭合电路的传递函数可以从图11中获得,将是通过忽略补偿移动参考变量可以近似为具有恒定的或者固定的手柄偏转的斜坡信号,如在恒定目标速度存在的这种情况中的一样。为了避免这种参考变量的固定控制偏差,开环Ka(s)Gh(s)因此必须显示I2行为[9]。这可以例如通过PID控制器实现,其中,因此,它对于闭合电路遵循:其中,κAHC,i的精确值依赖于各自的时间常数Th而选择。2.2堆积操作的检测一旦负载碰着海床,则应当实现从主动升降补偿件切换到恒定张力控制。为这个目的,堆积操作的检测是必需的(参见图10)。对于这个以及随后的恒定张力控制,缆绳近似为简单的弹簧质量元件。因此,作用在缆绳悬挂点处的力如下近似计算:Fc=kcΔlc,(2.7)其中,kc和Δlc表示等效于缆绳弹性的弹簧常数和弹簧偏转。对于后者,它应用:等效弹簧常数kc可以从下列的固定观察中确定。对于用质量mf加载的弹簧,它在固定的情况下应用:kcΔlc=mfg.(2.9)(2.8)的变换产生:参考(2.9)和(2.10)之间的系数补偿,等效弹簧常数可以是:在(2.9)中,也可以看见,在固定的情况下弹簧的偏转Δlc受到有效负载质量me和缆绳质量的一半影响。这是由于,在弹簧中被悬挂的质量mf假设将集中在一点的事实。但是,缆绳质量沿着缆绳长度均匀分布,因此不会完全加载弹簧。尽管如此,缆绳的全部重力μslsg包括在在缆绳悬挂点处的力测量中。随着缆绳系统的这个近似,现在可以获得对于在海床上的堆积操作的检测的条件。在静止时,作用在缆绳悬挂点上的力由展开的缆绳的重力μslsg和负载质量的有效重力meg组成。因此,具有定位在海床上的负载的测量的力Fc近似是:Fc=(me+μsls)g+ΔFc(2.12)其中,ΔFc=-kcΔls,(2.13)其中,Δls表示在到达海床之后的展开的缆绳。从(2.13),它遵循,Δls与被测量的力的变化成比例,因为在到达地面之后,负载位置是恒定的。参考(2.12)和(2.13),现在可以获得下列条件,用于检测,同时其必须满足:■负弹簧力的减小必须小于阈值:■弹簧力的时间导数必须小于阈值:■起重机操作员必须减小负载。参考用手柄信号设计的轨迹来检查这个条件:■为了避免在浸入水中方面的错误检测,最小缆绳长度必须被展开:ls>ls,min.(2.17)负弹簧力的减小ΔFc均相对于在测量的力信号Fc中的最后的高点计算。为了抑制测量噪声和高频干扰,力信号由相应低通滤波器预处理。由于必须同时满足条件(2.14)和(2.15),因此,排除了作为动力学固有缆绳振荡导致的错误检测:由于作为动力学固有缆绳振荡,力信号Fc振荡,因此弹簧力的相对于最后的高点的变化和弹簧力的时间导数具有推移了的相位。因此,在动力学固有缆绳振荡的情况下,随着阈值和的适当选择,不能同时满足两个条件。为这个目的,缆绳力的静态部分必须下降,如在浸入水中上或者堆积在海床上的情况一样。但是,在浸入水中方面的错误检测被条件(2.17)防止。用于弹簧力变化的阈值依赖于在测量的力信号中的最后高点而如下计算:其中χ1<1并且最大值根据实验确定。用于力信号的导数的阈值可以从(2.7)的时间导数估计并且最大可容许手柄速度klvmax如下两个参数χ2<1和同样地根据实验确定。由于在恒定张力控制中,应用力控制而不是位置控制,因此目标力Fc*依赖于作用在负载上的所有静态力Fl,stat的和而指定为参考变量。为这个目的,Fl,stat在升降补偿的阶段考虑了已知缆绳质量μsls而计算:Fl,stat=Fc,stat-μslsg.(2.20)Fc,stat表示在缆绳悬挂点Fc处测量的力的静态力分量。它来源于测量的力信号的相应低通滤波。在滤波中获得的群延迟不是问题,因为感兴趣的仅仅是静态力分量并且时间延迟对其没有显著影响。从作用在负载上的所有静态力的和,在考虑了附加作用在缆绳悬挂点的缆绳的重力的情况下而获得目标力,如下列一样:其中,在缆绳中产生的张力由起重机操作员用0<ps<1指定。为了避免参考变量的设定点值跳变,在堆积操作的检测之后,实现从在检测中当前测得的力到实际目标力的斜坡形转换。为了从海床中拾起负载,起重机操作员手动地执行从恒定张力模式到具有自由悬挂负载的主动升降补偿件的变化。2.3用于恒定张力模式的致动图12显示了在恒定张力模式中,在频率范围内的模块电路图中实现的提升绞盘的致动。与图示在图11中的控制结构相比,这里反馈的是缆绳系统的输出Fc(s)(即,在缆绳悬挂点处测量的力),而不是绞盘系统的输出Yh(s)。根据(2.12),测量的力Fc(s)由力的变化ΔFc(s)和静态重力meg+μslsg组成,其在图中用M(s)表示。对于实际控制,缆绳系统依次又近似为弹簧质量系统。两自由度的结构的引导控制F(s)与用于主动升降补偿件的那个相同并且分别由(2.2)和(2.3)给出。但是,在恒定张力模式中,没有加入手柄信号,其是为何参考轨迹仅仅包括用于补偿移动的负目标速度和加速度和的原因。引导控制部起初依次又补偿缆绳悬挂点的竖直移动。但是,绞盘位置的直接稳定化不由Yh(s)的反馈实现。这个通过测量的力信号的反馈而间接地实现。测量的输出Fc(s)从图12中如下获得:具有两个传递函数:其中,用于停留在地面上的负载的缆绳系统的传递函数从(2.12)得出:Gs,F(s)=-kc.(2.25)如可以从(2.22)中获得的,补偿误差Ea(s)由稳定传递函数GCT,1(s)校正,并且绞盘位置被间接地稳定。在这种情况下,控制器的要求Ks(s)也由预期的参考信号产生,其在转换阶段之后由恒定目标力从(2.21)给出。为了避免具有这种恒定参考变量的固定控制偏差,开环Ks(s)Gh(s)Gs,F(s)必须具有/行为。由于绞盘的传递函数Gh(s)已经隐含地具有这种行为,这个要求可以用P反馈实现;因此,它应用: