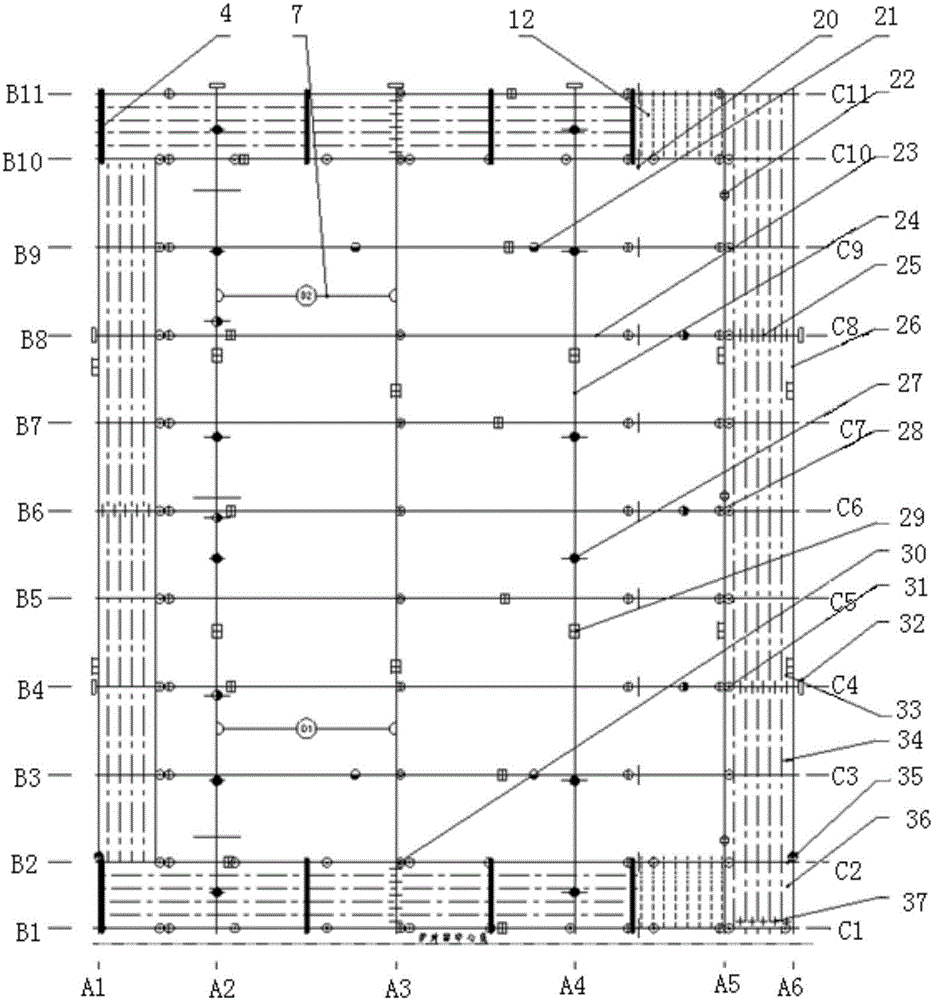
本发明涉及一种锅炉炉膛检修平台。
背景技术:
:锅炉炉膛检修平台是炉膛内高效、多功能的高空检修施工作业机具,它代替了传统的脚手架,通过检修人员操作,使平台调整到所需位置施工作业。具有结构合理、使用方便、安全可靠,工作效率高、劳动强度轻和检修工期短等特点,是目前火电行业中得到广泛应用的定型产品,可供炉膛内各部检修用,已在国内大中型电站投入使用。大多数的锅炉炉膛检修平台,都是采用2A12材质的工字铝型材通过钢制连接件组装而成的平台结构架,因此,采用这种结构的平台再加上四周铺设的跳板,自重就能高达4吨多。故而对于生产企业来讲,如何降低锅炉炉膛检修平台自重,是目前炉膛检修平台发展的一个重要研究方向。为了降低检修平台整体重量,在考虑成本的情况下,选择较为便宜的轻质材料铝合金制连接件来代替钢制连接件,是本领域技术人员易于想到的一种技术手段,但是,由于平台结构架是一种空间结构,包括若干横向工字铝型材和若干纵向工字铝型材,相互之间通过何种结构形式的铝制连接件的搭接而构成一个整体,则需要本领域技术人员进行详细的研究后才能确定。在连接时,连接面之间可能存在错位、转向等,采用一体成型的铝制连接件,对于整体成型工艺的要求会比较高,此时,就会需要采用焊接工艺焊接不同形状的铝型材来制成所需的连接件;而对于铝型材的焊接质量,也是本领域需要重视的一个要点,尤其是对于使用于检修平台的连接件来讲,焊接质量直接影响产品的安全性能。一般地,检修平台是通过卷扬机的驱动,在锅炉炉膛内完成升降操作;由于锅炉炉膛内径一般都是几十米,而检修平台的外围尺寸几乎与锅炉炉膛内壁尺寸匹配,因此,检修平台面积过于庞大,在升降过程中或者作业过程中,即便较小的偏移,其外围也可能通过导向轮与炉膛内壁碰触;而现有的导向轮在检修平台上的安装尺寸较为固定,基本不可调节,因此,导向轮的滑轮架极易损坏,同时,导向轮与检修平台直接的连接方式通常为刚性连接,因此,在导向轮与炉膛内壁碰触时,极易造成检修平台的晃动,影响检修平台的安全。技术实现要素:针对上述技术问题,本发明提出一种锅炉炉膛检修平台,其通过改进现有的跳板结构形式,在减轻跳板质量的前提下,能够有效地提高跳板的力学性能。为了实现上述技术目的,本发明采用如下技术方案:一种采用M形跳板的锅炉炉膛检修平台,包括平台主体以及起吊设备;所述的平台主体,包括主梁、副梁、折叠梁、限位梁以及跳板梁,并在平台主体的外周平铺跳板,跳板的内圈配装有围栏;围栏通过围栏支座安装在平台主体上;主梁与副梁通过连接卡板实现两者的垂直相交;折叠梁通过折叠接头与副梁实现可折叠连接,所述的跳板为M形跳板,包括跳板平台以及设置于跳板平台下方的支撑结构;所述跳板平台的横截面呈等腰梯形状设置,支撑结构安装在前述等腰梯形状跳板平台的小端;所述支撑结构包括设置在跳板平台中部位置处的第一支撑结构,第一支撑结构的两侧对称地设置有第二支撑结构、第三支撑结构,第三支撑结构设置在跳板平台的端部位置处,而第二支撑结构则位于第一支撑结构、第三支撑结构之间;其中:所述的第一支撑结构,包括第一内层支管、第一外层支管;第一内层支管、第一外层支管的横截面均为等腰梯形状,第一内层支管套接在第一外层支管的内腔,且第一内层支管、第一外层支管的中线重合;所述的第二支撑结构,包括第二内层支管、第二外层支管;第二内层支管、第二外层支管的横截面均为等腰梯形状,第二内层支管套接在第二外层支管的内腔,且第二内层支管的中心相对于第二外层支管的中心向跳板的中心位置处偏移;所述的第一支撑结构、所述的第二支撑结构的大端均与跳板平台连接;所述的第三支撑结构,截面呈直角梯形状设置,其倾斜端与跳板平台连接。作为本发明的进一步改进,所述等腰梯形状跳板平台的倾角为60-65°。作为本发明的进一步改进,所述第一内层支管、第一外层支管、第二内层支管、第二外层支管的倾角均一致,取值介于70-80°之间。作为本发明的进一步改进,第一内层支管的斜边与第一外层支管斜边之间的间距为1-2mm;第一内层支管的底边与第二内层支管的底边之间的间距为1-2mm。作为本发明的进一步改进,第二内层支管的外侧斜边与第二内层支管的外侧斜边之间的间距是第二内层支管的内侧斜边与第二内层支管的内侧斜边之间的间距的2-4倍。作为本发明的进一步改进,第二内层支管的外侧斜边与第二内层支管的外侧斜边之间的间距是3-4mm;第二内层支管的内侧斜边与第二内层支管的内侧斜边之间的间距1-2mm。作为本发明的进一步改进,所述平台主体的四周配装有弹性限位轮机构。作为本发明的进一步改进,弹性限位轮机构包括限位轮、滑轮架、导轨轴、弹簧、导轨套以及导轨座;其中,限位轮通过滑轮架连接在导轨轴一端,导轨轴另一端套接于导轨套的内腔,并且导轨轴与导轨套之间设置所述弹簧,导轨套侧壁上沿导轨套的轴向设有限位槽,一导向部件穿过所述限位槽后与所述导轨轴固定连接;所述导轨套的底部连接导轨座,所述导轨座具有能够卡接在工字梁的一侧翼板上的滑槽,滑槽上设有螺栓孔,通过连接螺栓使得所述导轨座与工字梁之间固定。作为本发明的进一步改进,导轨轴为空心轴;弹簧置于导轨轴的内腔,且弹簧的一端与滑轮架固定,另一端则穿过导轨轴后与导轨套连接。作为本发明的进一步改进,所述导向部件为一螺栓。根据上述的技术方案,相对于现有技术,本发明具有如下的有益效果:1、M形跳板的优点力学性能测试:模型体积/mm3最大变形/mm体积相对减少量原始4.62×1066.173×10-5/“M”型4.205×1066.009×10-59%原始的跳板,其具有的支撑机构为矩形状立柱。结论:通过以上的分析可知,“M”型跳板相对于原始跳板总重减少了9%,并且最大变形也有一定程度的降低,相对来说也更加安全。由此可知,本发明不仅可以降低成本,而且安全性也有了较大的提高。2、弹性限位轮机构的优点本发明一种锅炉炉膛检修平台及其弹性限位轮机构,由于限位轮与平台之间具有导轨轴、弹簧以及导轨套组成的缓冲结构,使得限位轮与工字梁之间实现了一定的能量缓冲,当导向轮与炉膛内壁碰触时,不会导致限位轮的滑轮架损坏的技术问题。附图说明图1为本发明锅炉炉膛检修平台的主视图;图2为图1的侧视图;图1、图2中,1为单层π字梁;2为围栏管;3为双层π字梁;4为跳板梁;5为围栏横杆连接件;6为安装在围栏管和围栏立杆之间的双卡扣a;7为限位梁;8为围栏支杆;9为安装在围栏管和围栏支杆之间的双卡扣b;10为围栏立杆;11为支吊立杆;12为跳板;13为保护器;14为保护绳;16为吊绳;17为螺旋锁具扣;18为角铝;19为钢丝绳;20为折叠接头;21为围栏支杆座;22为拉吊点;23为副梁;24为A2、A3、A4梁;25为跳板双头间固定;26为A1、A5、A6梁;27为主吊点;28为副吊点;29为双梁连接件;30为支吊立杆座;31为围栏支座;32为限位轮装置;33为单梁连接件;34为跳板接头;35为折叠梁;36为跳板;37为跳板单头固定;图3为连接卡板的主视图;其中,110为第一卡板;120为第二卡板;图4为图3的侧视图;其中,1101为第一滑槽;图5为图3的俯视图;图6为每两个交叉工字梁之间连接结构示意图;其中,140为工字梁A;150为工字梁B;图7为第一铰链连接板主视图;其中,210为第一铰链连接板;2102为铰接座;图8为图7侧视图;其中,2101为第二滑槽;图9为第二铰链连接板主视图;其中,310为第二铰链连接板;3101为第三滑槽;3102为夹板;3103为铰接座;图10为图9侧视图;图11为可折叠工字梁连接结构示意图;其中,240为工字梁C;350为工字梁D;图12为可折叠工字梁折叠后的结构示意图;图13为本发明中限位轮装置的主视图;其中,321为限位轮;322为固定扣;图14为图12的侧视图;其中,323为滑轮架;324为导轨轴;325为弹簧;326为导向部件;327为导轨套;328为导轨套底部;329为导轨座;330为连接螺栓。图15是围栏支座的局部放大图;图16是围栏座卡板的结构示意图;图17是围栏连接管的结构示意图;图中:围栏座卡板31-1;围栏座滑槽31-1a;围栏座卡接板31-1b;围栏连接管31-2;外管壁卡槽31-2a;内管壁卡槽31-2b;图18是工字梁(以A梁为例)拼接的结构示意图;图19是接头卡板的结构示意图;图18中:1-1、分体梁a;1-2、接头卡板;1-3、分体梁b;图20是主吊点一个方向的剖视图;图21是主吊点另一个方向的剖视图;图20-21中:27-1、U形结构;27-2、卡槽;27-3、连接孔;图22是拉吊点的结构示意图;图中:22-1、卡槽;22-2、加强立柱;图23是本发明所述跳板的结构示意图;图中:12-1为跳板平台;12-2为第三支撑结构;12-3为第二支撑结构;12-4为第一支撑结构;L为等腰梯形状跳板平台大端的宽度;c为等腰梯形状跳板平台的高度;H为第一支撑结构、第二支撑结构、第三支撑结构的高度;a为第三支撑结构的宽度;b为第一内层支管的斜边与第一外层支管斜边之间的间距、第二内层支管的内侧斜边与第二内层支管的内侧斜边之间的间距;d为第二内层支管的外侧斜边与第二内层支管的外侧斜边之间的间距;e为第一内层支管的底边与第一外层支管底边之间的间距、第二内层支管的底边与第二外层支管底边之间的间距;f为第一支撑结构、第二支撑结构底端的宽度;α为第一支撑结构、第二支撑结构斜边的倾角。具体实施方式下面将结合本发明实施例中的附图,对本发明实施例中的技术方案进行清楚、完整地描述,显然,所描述的实施例仅仅是本发明一部分实施例,而不是全部的实施例。以下对至少一个示例性实施例的描述实际上仅仅是说明性的,决不作为对本发明及其应用或使用的任何限制。基于本发明中的实施例,本领域普通技术人员在没有作出创造性劳动前提下所获得的所有其他实施例,都属于本发明保护的范围。除非另外具体说明,否则在这些实施例中阐述的部件和步骤的相对布置。表达式和数值不限制本发明的范围。同时,应当明白,为了便于描述,附图中所示出的各个部分的尺寸并不是按照实际的比例关系绘制的。对于相关领域普通技术人员已知的技术、方法和设备可能不作详细讨论,但在适当情况下,所述技术、方法和设备应当被视为授权说明书的一部分。在这里示出和讨论的所有示例中,任何具体值应被解释为仅仅是示例性的,而不是作为限制。因此,示例性实施例的其它示例可以具有不同的值。为了便于描述,在这里可以使用空间相对术语,如“在……之上”、“在……上方”、“在……上表面”、“上面的”等,用来描述如在图中所示的一个器件或特征与其他器件或特征的空间位置关系。应当理解的是,空间相对术语旨在包含除了器件在图中所描述的方位之外的在使用或操作中的不同方位。例如,如果附图中的器件被倒置,则描述为“在其他器件或构造上方”或“在其他器件或构造之上”的器件之后将被定位为“在其他器件或构造下方”或“在其他器件或构造之下”。因而,示例性术语“在……上方”可以包括“在……上方”和“在……下方”两种方位。该器件也可以其他不同方式定位(旋转90度或处于其他方位)。如图1、图2所示,如图1、图2所示,其公开了本发明所述的锅炉炉膛检修平台的结构示意图,锅炉炉膛检修平台包括平台主体以及起吊设备;所述的平台主体,通常包括主梁、副梁、折叠梁35、限位梁7以及跳板梁4,并在平台主体的外周平铺跳板12,跳板12的内圈配装有围栏;围栏通过围栏支座31安装在平台主体上;主梁与副梁通过连接卡板实现两者的垂直相交;折叠梁35通过折叠接头20与副梁实现可折叠连接;跳板梁4也是通过连接卡板安装在处于外侧的两根副梁上。所述的主梁、副梁,均包括若干段分体梁,相邻的两段分体梁a、分体梁b通过接头卡板拼接。附图中,B1-B11梁均为副梁;A1-A6梁均为主梁;C1-C11梁均为折叠梁35;D1、D2是限位梁7,其中:主梁有两类,一类是单层π字梁,另一类则是双层π字梁,A1、A5、A6是单层π字梁,A2、A3、A4是双层π字梁;当然,主梁也可以选用工字梁;限位梁D1、D2间隔地安装在主梁A2、A3之间;副梁、折叠梁均选用工字梁。各副梁相互平行,各主梁相互平行,各折叠梁也相互平行。各主梁均与副梁垂直相交,并在垂直相交处通过连接卡板连接。处于端部的两根主梁,即主梁A1、A6安装在副梁的上侧,而其余主梁则安装在副梁的下侧。为便于起吊设备的安装,在主梁上,特别是梁A2、A4上安装有多个主吊点27;而便于折叠梁35的折叠或展开,则在安装折叠梁的副梁上设置有若干拉吊点22。图3-图6详细地公开了一种工字梁十字交叉处的连接卡板,用于连接处于垂直相交位置处的工字梁A140、工字梁B150,其中工字梁A140可以为主梁,工字梁B150可以为副梁,当然两者也可以互换;该连接卡板包括一折弯板,所述折弯板具有截面位于不同高度上的两个卡板,分别是第一卡板110和第二卡板120,所述第一卡板110的一组相互平行的外边缘向下折弯形成第一滑槽1101,所述第一滑槽1101与工字梁A140的翼板之间滑动配合,所述第一滑槽1101的背部朝向工字梁B150的方向具有第二卡板120,第二卡板120与工字梁B150的翼板平行;所述第一卡板110和第二卡板120上均设有螺栓排孔,通过在第一卡板110上的螺栓排孔中配装连接螺栓,使得第一卡板110与工字梁A140相固定,通过在第二卡板120上的螺栓排孔中配装连接螺栓,使得工字梁B150与工字梁A140之间压紧固定。为防止卡板连接松动后事故发生,本发明工字梁A140、工字梁B150在第二卡板120螺栓排孔的相邻两个螺栓孔之间,设置有应变片。通过在第二卡板120上设置应变片,从而实现对第二卡板120与工字梁之间的接触压力进行实时检测。所述第一滑槽1101背部通过内凹的弧面与第二卡板120连接。所述折弯板采用A356铝合金制成的一体成型件。与同样是铝合金材料制成的工字梁配合连接后,相较于现有钢结构平台来说,重量大大减轻。所述折弯板也可以不是一体成型件,此时采用6061-T6制成,且第一卡板110和第二卡板120之间通过焊接方式连接。作为本发明的进一步改进,工字梁B150与工字梁A140在第二卡板120螺栓排孔的相邻两个螺栓孔之间,设置有应变片。通过在第二卡板120上设置应变片,从而实现对第二卡板120与工字梁之间的接触压力进行实时检测,防止卡板连接松动后事故发生。将上述的连接卡板用于本发明所述检修平台的主梁和副梁交叉位置处时,将上述的工字梁A140定为主梁,工字梁B150定为副梁,此时,第一滑槽1101与主梁的翼板之间滑动配合,所述第一滑槽1101的背部朝向副梁的方向具有第二卡板120,第二卡板120与副梁的翼板平行;则安装时,通过在第一卡板110上的螺栓排孔中配装连接螺栓,使得第一卡板110与主梁相固定,通过在第二卡板120上的螺栓排孔中配装连接螺栓,使得副梁与主梁之间压紧固定。图7至图12较为详尽地公开了一种折叠接头,连接在工字梁C240、工字梁D350之间,能够实现工字梁C240、工字梁D350之间的折叠或者展开,包括铰接在一起的第一铰链连接板210和第二铰链连接板310;所述第一铰链连接板210具有与工字梁C240的翼板滑动连接的第二滑槽2101;第二铰链连接板310具有与工字梁D350的翼板滑动连接的第三滑槽3101以及能够将工字梁C240、工字梁D350腹板端部拼接的两个夹板3102;所述的两个夹板3102分设在工字梁C240、工字梁D350腹板端部拼接缝位置处两侧,同时,所述第二滑槽2101、第三滑槽3101以及两个夹板3102上均设置有螺栓连接孔,且两个夹板3102上的螺栓连接孔为配对孔;通过在第二滑槽2101的螺栓连接孔中配装连接螺栓,将所述第一铰链连接板210与工字梁C240的翼板相固定;通过在第三滑槽3101的螺栓连接孔中配装连接螺栓,将所述第二铰链连接板310与工字梁D350之间相固定;通过在两个夹板3102上的螺栓连接孔中配装连接螺栓,将工字梁C240的腹板端部与工字梁D350的腹板端部拼接成一体。上述的工字梁C240、工字梁D350具体到本发明所述的检修平台上,可知工字梁C240为副梁,工字梁D350为折叠梁。作为本发明折叠接头一个优选实施例,所述第二滑槽2101通过第一铰链连接板210的两侧边缘向下弯折而形成。作为本发明折叠接头的一个优选实施例,所述第二铰链连接板310的两侧边缘向下弯折形成所述第二滑槽2101后,继续弯折以形成两个相背布置的L形夹板3102。作为本发明折叠接头技术方案一个优选实施例,所述夹板3102上开设的螺栓连接孔有6个,其中三个螺栓连接孔呈等边三角形布置于与工字梁C240的腹板端部正对的夹板3102板面,余下三个螺栓连接孔也呈等边三角形布置于与工字梁D350的腹板端部正对的夹板3102板面。作为本发明折叠接头技术方案一个优选实施例,所述的L形夹板3102中,与第三滑槽3101相对布置的折边以及与第一铰链连接板210相邻的侧边交汇的位置处,存在一个直角三角形的缺角。作为本发明折叠接头技术方案一个优选实施例,所述第二滑槽2101的背面向上设置有一块具有铰接孔a的立板a;所述第三滑槽3101的背面向上设置有一个铰链座,所述的铰链座包括两块相间布置的具有铰接孔b的立板b;立板a置于两块立板b之间,且立板a上的铰接孔a和两立板b上的铰接孔b为配对孔;通过在立板a上的铰接孔a和两立板b上的铰接孔b中安装销轴,将第一铰链连接板210、第二铰链连接板310铰接在一起。作为本发明折叠接头技术方案一个优选实施例,第一铰链连接板210和第二铰链连接板310均采用6061-T6铝合金制成;且立板a与第二滑槽2101之间通过焊接固定,立板b与第三滑槽3101之间也通过焊接固定;立板a与第二滑槽2101之间、立板b与第三滑槽3101之间焊接固定。如果是一体制件的话,可以采用A356铝合金制成。将上述的折叠接头应用于本发明所述的检修平台,可将所述的工字梁C定为副梁,工字梁D定为折叠梁35,此时,所述第一铰链连接板210具有与副梁的翼板滑动连接的第二滑槽2101;第二铰链连接板310具有与折叠梁的翼板滑动连接的第三滑槽3101以及能够将副梁、折叠梁腹板端部拼接的两个夹板3102;所述的两个夹板3102分设在副梁、折叠梁腹板端部拼接缝位置处两侧,同时,所述第二滑槽2101、第三滑槽3101以及两个夹板3102上均设置有螺栓连接孔,且两个夹板3102上的螺栓连接孔为配对孔;通过在第二滑槽2101的螺栓连接孔中配装连接螺栓,将所述第一铰链连接板210与副梁的翼板相固定;通过在第三滑槽3101的螺栓连接孔中配装连接螺栓,将所述第二铰链连接板310与折叠梁之间相固定;通过在两个夹板3102上的螺栓连接孔中配装连接螺栓,将副梁的腹板端部与折叠梁的腹板端部拼接成一体。参见图13~图14所示,本发明公开了一种弹性限位轮机构,包括限位轮321、滑轮架323以及导轨轴324;还包括弹簧325、导轨套327以及导轨座329;其中,限位轮321通过滑轮架323连接在导轨轴324一端,导轨轴324另一端套接于导轨套327的内腔,并且导轨轴324与导轨套327之间设置所述弹簧325,导轨套327侧壁上沿导轨套327的轴向设有限位槽,一导向部件穿过所述限位槽后与所述导轨轴324固定连接;所述导轨套327的底部328连接导轨座329,所述导轨座329具有能够卡接在工字梁的一侧翼板上的滑槽,滑槽上设有螺栓孔,通过连接螺栓330使得所述导轨座329与工字梁之间固定。进一步的,导轨轴324为空心轴;弹簧325置于导轨轴324的内腔,且弹簧325的一端与滑轮架323固定,另一端则穿过导轨轴324后与导轨套327连接。进一步的,所述导向部件326为一导向螺栓。进一步的,为了进一步减轻平台整体连接后的重量,所述导轨座329、导轨套327选用6016-T6铝合金材质制成;且导轨座329、导轨套327通过焊接固定,导轨座329、导轨套327之间焊接固定。上述的弹性限位轮机构,配装在平台主体的四周,由于限位轮321与平台之间具有导轨轴324、弹簧325以及导轨套327组成的缓冲结构,使得限位轮321与工字梁之间实现了一定的能量缓冲,当导向轮与炉膛内壁碰触时,不会导致限位轮321的滑轮架323损坏的技术问题。参见图15~图17所示,本发明公开了一种围栏支座,用于将围栏安装在平台主体上,与处于平台主体外侧的工字梁连接,主要安装在B梁(副梁)以及C梁(折叠梁)上;所述围栏支座包括围栏座卡板31-1以及围栏连接管31-2;所述围栏座卡板31-1具有与工字梁翼板配合的围栏座滑槽31-1a,该围栏座滑槽31-1a上开设有螺栓孔,通过在螺栓孔中配装连接螺栓,将围栏座卡板31-1安装在工字梁上;所述围栏座卡板31-1在围栏座滑槽31-1a的背部中间位置处设置有围栏座卡接板31-1b;围栏连接管31-2的内壁设置有与围栏座卡接板31-1b配合的内管壁卡槽31-2b,而围栏连接管31-2的外管壁则设置有若干均布的具有防滑作用的外管壁卡槽31-2a;围栏连接管31-2通过内管壁卡槽31-2b与围栏座卡接板31-1b的配合,安装在围栏座滑槽31-1a的背面。围栏包括围栏管、围栏立杆、安装在围栏管和围栏立杆之间的双卡扣a、围栏支杆、安装在围栏管和围栏支杆之间的双卡扣b;其中围栏立杆通过扣件与围栏连接管31-2连接,而围栏支杆则与工字梁连接。所述的围栏座卡板31-1以及围栏连接管31-2均采用6061-T6铝合金制成。所述围栏连接管31-2的端面与围栏座滑槽31-1a的背部通过焊接工艺焊接固定通常,用于搭建平台主体的主梁、副梁较长,因此,一般需要采用接头卡板1-2将若干分体梁拼接而成,具体参见图18-图19,该接头卡板1-2为一断面成U形状的连接板,该U形状的连接板跨接在相邻的两段分体梁a1-1、分体梁b1-3之间,分体梁a1-1、分体梁b1-3接缝相接,U形状连接板的封闭端开设有若干安装孔,分体梁a1-1、分体梁b1-3对应着U形状连接板的封闭端所开设的安装孔设置有对应的连接孔,采用螺栓即可将分体梁a1-1、分体梁b1-3拼接成一体。图20-21具体地公开了本发明所述主吊点的结构示意图,该主吊点包括U形结构27-1,U形结构27-1的两个侧臂上对应地开设有卡槽27-2,用于卡接主梁的上侧翼板;同时,U形结构27-1的两个侧臂开设对穿的连接孔27-3,用于安装起吊设备;由此可知,本发明通过将U形结构27-1从主梁下侧的翼板套接,实现主吊点与主梁的连接,而通过卡槽27-2对主梁上侧翼板的卡接,能够进一步巩固主吊点在主梁上的定位,防止与主梁呈45°倾角的拉绳拉动拉吊点在主梁上移动。图22具体地公开了本发明所述拉吊点的结构示意图,包括卡槽22-1以及加强立柱22-2,所述卡槽22-1呈T形状,该T形状卡槽22-1的横段部分卡槽能够卡接住副梁的一侧翼板,而T形状卡槽22-1的竖直段部分卡槽能够夹持住副梁的腹板;加强立柱22-2背向T形状卡槽的横段部分延伸而形成,且加强立柱22-2与折叠梁35固定,由此使得折叠梁、副梁通过拉吊点形成了三角形连接结构。图23具体地公开了本发明所述跳板的具体结构,所述的跳板为M形跳板,包括跳板平台12-1以及设置于跳板平台12-1下方的支撑结构;所述跳板平台12-1的横截面呈等腰梯形状设置,支撑结构安装在前述等腰梯形状跳板平台12-1的小端,而等腰梯形状跳板平台12-1的大端宽度为L、高度为c;所述支撑结构包括设置在跳板平台12-1中部位置处的第一支撑结构12-4,第一支撑结构12-4的两侧对称地设置有第二支撑结构12-3、第三支撑结构12-1,第三支撑结构12-1设置在跳板平台12-1的端部位置处,而第二支撑结构12-3则位于第一支撑结构12-4、第三支撑结构12-1之间;其中:所述的第一支撑结构12-4,包括第一内层支管、第一外层支管;第一内层支管、第一外层支管的横截面均为等腰梯形状,第一内层支管套接在第一外层支管的内腔,且第一内层支管、第一外层支管的中线重合;所述的第二支撑结构12-3,包括第二内层支管、第二外层支管;第二内层支管、第二外层支管的横截面均为等腰梯形状,第二内层支管套接在第二外层支管的内腔,且第二内层支管的中心相对于第二外层支管的中心向跳板的中心位置处偏移;所述的第一支撑结构12-4、所述的第二支撑结构12-3的大端均与跳板平台12-1连接;所述的第三支撑结构12-1,截面呈直角梯形状设置,其倾斜端与跳板平台12-1连接。所述等腰梯形状跳板平台12-1的倾角为60-65°。所述第一内层支管、第一外层支管、第二内层支管、第二外层支管的倾角α均一致,取值介于70-80°之间。第一内层支管的斜边与第一外层支管斜边之间的间距、第二内层支管的内侧斜边与第二内层支管的内侧斜边之间的间距,记为b,取值为1-2mm;第二内层支管的外侧斜边与第二内层支管的外侧斜边之间的间距,记为d,取值为3-4mm。第一内层支管的底边与第一外层支管底边之间的间距、第二内层支管的底边与第二外层支管底边之间的间距,记为e,取值为1-2mm;第一支撑结构、第二支撑结构底端的宽度,记为f,取值为13-16mm;第三支撑结构的宽度为a,取值为7-10mm。本发明采用M形跳板的优点:力学性能测试:模型体积/mm3最大变形/mm体积相对减少量原始4.62×1066.173×10-5/“M”型4.205×1066.009×10-59%原始的跳板,其具有的支撑机构为矩形状立柱。结论:通过以上的分析可知,“M”型跳板相对于原始跳板总重减少了9%,并且最大变形也有一定程度的降低,相对来说也更加安全。由此可知,本发明不仅可以降低成本,而且安全性也有了较大的提高。另外,本发明还公开了一种铝合金焊接方法,可以用于连接卡板中,第一卡板和第二卡板之间的焊接;可以用于折叠接头中,立板a与第二滑槽之间、立板b与第三滑槽之间的焊接;可以用于弹性限位轮机构中,导轨座、导轨套通过焊接固定,导轨座、导轨套之间的焊接;也可以用于围栏支座中,围栏连接管的端面与围栏座滑槽的背部之间的焊接。包括清洗工艺、预热工艺、焊接工艺以及焊后加强处理工艺,其中:一、清洗工艺本发明主要采用的是化学方法清理待焊接铝合金工件表面的氧化物和油污;具体涉及到的试剂有酒精、pH值为11-13的弱碱性清理溶液;其中:弱碱性清理溶液包括组份偏硅酸钠、柠檬酸钠以及碳酸氢钠,偏硅酸钠、柠檬酸钠以及碳酸氢钠三者的质量配比是(10-16):(2-4):(20-25)。使用时,先采用酒精擦拭待焊接铝合金工件表面,以去除待焊接铝合金工件表面的油污,然后用清水洁净后,再采用上面所配制的弱碱性清理溶液清理掉待焊接铝合金工件表面的氧化物,最后采用清水清洗后,干燥即可。具体地,将经过酒精擦拭的待焊接铝合金工件浸入50-60℃的弱碱性清理溶液中浸泡10分钟以上,取出工件用冷水冲洗并清除工件表面上的残留物,然后在80℃下烘干30分钟。二、预热工艺采用感应加热设备,将工件预热至150-200℃后,采用刚性夹具将待焊接的工件紧固在焊接工作台上,以控制焊接变形。考虑到铝合金材质具有的高导热性特点,本发明所述的刚性夹具,具有的夹头,采用保温材料复合板,包括固定板、保温材料板以及夹板,保温材料板压设在固定板和夹板之间,固定板安装在夹具上,而夹板则夹持住铝合金工件,保温材料板可以选用石棉泡沫板;由此可知,本发明一方面可以实现与工件的刚性固定,防止工件在焊接过程中因受热膨胀变形;另一方面,由于配置石棉泡沫板,可以使两个工件的焊接坡口之间的焊缝熔池中保温时间长,不易出现未熔合和未焊透气孔和裂纹现象;有效解决气孔和夹杂问题。三、焊接工艺本发明采用变极性TIG焊机对工件进行焊接处理。具体地,包括以下步骤:考虑到本发明所述的铝合金工件采用的是铝合金6061材质,通常地,较为常用的焊丝采用的是ER5356,而采用ER5356焊丝焊接后的焊缝金属,具有的抗热裂性强度不高,而另一种推荐用的焊丝ER4043,虽然具有较好的抗热裂性,但是,由于其为含硅5%的合金焊丝,因此,在焊接过程中,会形成Mg2Si,从而影响焊缝金属的塑性和强度,另外,ER4043焊丝的焊缝金属存在变色现象。本发明的焊缝金属包括5层,分别为打底焊层、中间焊层以及盖面焊层,其中:打底焊层和盖面焊层采用同样的焊丝ER5356,分别包括2层,而中间焊层则采用ER4043焊丝,具体的工艺参数如下:第一层采用ER5356焊丝,电流调节范围为250-290A、电流极性采用交流,保护气体采用100%Ar(纯度≥99.99%);气体流量为10±3升/分钟。待第一层焊缝表面温度降低至220℃时,进行第二层焊接,第二层采用ER5356焊丝,电流调节范围为250-290A,且第二层焊接时的电流数值大于第一层焊接时的电流数值;电流极性采用交流,保护气体采用100%Ar(纯度≥99.99%);气体流量为10±3升/分钟。待第二层焊缝表面温度降低至230℃时,进行第三层焊接,第三层采用ER4043焊丝,电流调节范围为250-290A、电流极性采用交流,保护气体采用100%Ar(纯度≥99.99%);气体流量为10±3升/分钟。待第三层焊缝表面温度降低至220℃时,进行第四层焊接,第四层采用ER5356焊丝,电流调节范围为250-290A,且第四层焊接时的电流数值与第二层焊接时的电流数值一致;电流极性采用交流,保护气体采用100%Ar(纯度≥99.99%);气体流量为10±3升/分钟;待第四层焊缝表面温度降低至铝合金件的预热温度或者略高于铝合金工件的预热温度时,进行第五层焊接,第五层采用ER5356焊丝,电流调节范围为250-290A,且第五层焊接时的电流数值与第一层焊接时的电流数值一致;电流极性采用交流,保护气体采用100%Ar(纯度≥99.99%);气体流量为10±3升/分钟;本发明在进行焊接工艺操作时,通过选择不同类型的焊丝进行多层焊接,以改善选择一种焊丝焊接具有的力学性能缺陷;另外,本发明还通过在中间层两侧的焊缝金属焊接时,采用对称设置的工艺参数(第一层和第五层一致,第二层和第四层一致),使得焊缝金属在层间为对称构造,有效地改善焊接构件的力学性能。四、焊后加强处理工艺焊接完成后立即采用HMX1100-30A箱式气氛炉对6106铝合金焊件进行热处理。具体过程如下:第一步,固溶处理。将炉子的加热速度设为10-15℃/min,加热到450-520℃后,将基本冷却到室温的焊件放入加热炉内,保温30min。保温完成后取出,迅速放入冷水池(室温20-25℃)中作淬火处理,冷却至室温,工件从炉子中转出至冷水池的时间不超过1分钟;第二步:将冷水冷却后的工件焊接处置于深冷处理装置中,以(10-15)℃/min的速率迅速冷却至-80~-110℃后,维持半小时,再以(3-6)℃/min速率缓慢冷却至-140~-160℃后,维持半小时,最后以1-1.5℃/min的速率慢慢冷却到(-190)℃左右,维持2个小时,结束深冷处理过程。第三步、将经过深冷处理装置处理过的工件放入加热保温装置,以(1-3)℃/min的速率缓慢加热至(80-90)℃后,维持半小时,再以(10-15)℃/min的速率迅速升温至200-220℃后,保温1个小时;第四步、取出工件,冷却至室温即可。采用HVA-10A维氏硬度计对接头的硬度进行测量(压头载荷选择5kg,测试标准GB/T2654-2008),由测量结果分析可知焊态的平均硬度值焊缝处约为75.6HV,热影响区约为85.2HV,经过焊后的热处理,硬度值分布趋于均匀,平均值达到了90.5HV,约为母材硬度的98%(母材硬度为95HV)采用YDL-2000万能机进行拉伸性能测试(测试标准为GB/T2649-1989,GB/T2651-2008),如下表所示。注:101/102/103代表母材,201/202/203代表焊态,301/302/303代表处理态从上面的实验结果可以看出,6061铝合金母材的抗拉强度达到了276MPa,伸长率为12%,具有很好的强度和塑性;尽管本发明在清洗工序、预热工序以及焊接工序均进行了充分考虑,但是,最终得到的焊接接头拉伸断裂位置在焊缝区,抗拉强度有232MPa,相当于母材的84.06%,伸长率有所降低,只有6.4%,可见TIG熔焊时接头抗拉强度有所下降,这与硬度试验结果出现的软化现象相符,并且塑性也有所下降;处理态接头断裂位置也在焊缝区,试件断裂方向几乎与焊缝表面垂直,抗拉强度达到264MPa,相当于母材95.65%,伸长率为10.5%,接头抗拉强度得到很好恢复,塑性较焊接接头也有所恢复。焊接后处理对6016铝合金焊接接头的强度恢复以及塑性恢复均有很大的帮助,能够满足使用的要求。当前第1页1 2 3