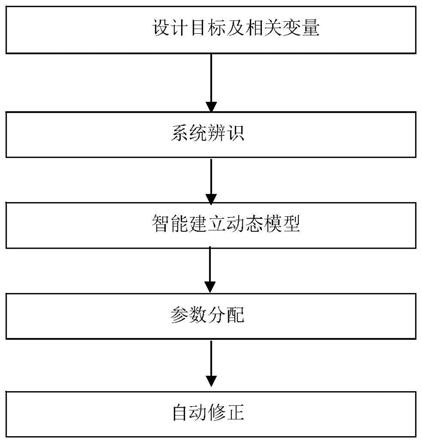
1.本发明属于冶金自动控制技术领域,特别是提供了一种用于翻车机全自动给料的控制方法。
背景技术:2.翻车机的5个给料漏斗下方各有一台变频电机驱动的振动给料器,通过振动给料器的振动将漏斗里的物料振动到皮带机上进行输送。振动给料器的振动速度是由plc控制变频器的输出频率来调节的。5个漏斗给料时在皮带机上形成料流,皮带机出口的皮带秤用来反馈实际料流的流量。在翻车机自动给料系统中,控制量是设定流量,被控量是皮带秤反馈的皮带流量,从设定流量到反馈的流量要经过模拟量输出模块、变频器、振动给料电机、皮带机再到皮带秤。一般纯滞后时间在15s以上,故皮带秤所反馈的实际流量其实是滞后时间之前的设定流量。此工艺流程决定了滞后不可避免,流量不能及时反馈,系统所承受的扰动会产生明显超调,使得控制系统稳定性变差,调节时间过长,系统控制难度增大。
3.目前国内钢铁行业的翻车机给料系统由于存在非线性、超大纯滞以及物料的比重差异等原因,无法实现自动控制,基本上都采用手动给料方式,部分厂内已经开始通过改造实现全自动给料作业,其通常做法是在每列车建立给料模型后,继续确定给料参数,存在给料系统时间过长、系数变化大、流量控制不稳定等情况,对翻车机的作业效率影响大。因此通过优化或改进给料模型的建立,缩短寻找给料参数时间,确定合适的给料参数,对提高翻车机作业效率具有重要的作用和意义。
技术实现要素:4.本发明的目的在于提供一种用于翻车机全自动给料的控制方法,解决了解决给料系统建立给料模型后需要继续确定给料参数,存在给料系统时间过长、系数变化大、流量控制不稳定等问题。根据翻车机给料系统的组成工作运行特性,采用一种给料参数智能构建、自动修正的全自动给料控制方案,从而实现翻车机全自动给料作业中参数的智能构建、自动修正功能。具体包括:
5.设计目标及相关变量
→
系统辨识
→
智能建立动态模型
→
参数分配
→
自动修正。
6.设计目标及相关变量:
7.根据皮带秤反馈的瞬时流量和给定目标值,以最短的时间得到一个合理的输出量(变频器总给料速度),合理分配到5个料斗中,使翻车机5个漏斗能够平稳、高效地给料,确保皮带秤瞬时流量稳定在目标设定值附近。全自动给料作业模型智能构建、自动修正给料系统的相关变量包括:被控量,即翻车机皮带秤所测得的瞬时流量;给定值,即皮带瞬时流量的目标值稳定在4000t/h;输出量,即5个料斗对应的振动给料器变频器频率给定值;控制原理为:
8.每一列车中的煤种和车型都是单一的,模型是相对稳定的,故本发明提出一套具有系统辨识功能的可动态建立数学模型的修正补偿自动给料系统,系统框图如图1所示。
9.具体的控制系统流程图如图2所示。
10.即在每一列车开始智能构建阶段,通过plc程序设定给料作业模型,用一套固定测试且周期递增的参数给料一段时间后得出该列车所对应的模型数值,据此模型数值通过给料量与模型数值之间的线性关系计算出初始给料的参考值、皮带超量给料保护值等,然后比较5个漏斗料斗料位,将初始给料的参考值按设定比例分配给各个漏斗变频器;根据皮带瞬时流量与给料流量目标值的比较,分段对初始给料的参考值进行调整,并将其增减量按设定方式(如果瞬时流量大于给料流量目标值在一定范围外,以秒为单位减少目标值20t/h,反之减少目标值20t/h)分配到各个漏斗,直至流量调整到目标值并保持稳定,然后将该给料参数存储到参数数据库中。
11.系统辨识:
12.本环节的主要目的就是利用一开始给料的前3min时间,通过对输入输出的周期采样计算,自动计算出本系统的动态放大倍数,同时解决了煤种识别问题和非线性放大问题。具体说明如下:
13.(1)输入输出采样。
14.由于5个漏斗的机械参数是相同的,各个漏斗在相同的振动频率下给料能力也是相同的;为防止在系统辨识期间出现大流量压停皮带的事故,故在初始阶段只开启3个漏斗,并将其给料系数都调节为1.0;开始给料时,对输入的设定值进行周期为1s的增量为20的递增式设定,即初始设定值为1000t/h,隔1s后为1020t/h,依次类推,一直将设定值增加至4000t/h,共耗时150s,与此同时通过采样程序将这150个设定值记录到输入采样表中(输入用x表示);经过20s纯滞后时间后,通过采样程序将皮带秤的流量反馈值记录在输出采样表中(输出用y表示),输出采样比输入采样延时20s结束,这时就完成了系统辨识的数据采样阶段。
15.(2)非线性系统的线性化,计算动态放大倍数,采样完成后,首先将输出采样表的数值除以3,得到单个漏斗实际给料量的采样y;众所周知,由于非线性系统很难得到精确的数学模型,所以一般采用将其线性化的方法来解决;本系统的非线性比较严重,直接线性化会导致数学模型的严重失真,故根据输入采样的初始值和最终值将输入值和对应的输出值划分为10个区间(即每15个采样为1个区间),对这10个区间分别进行线性化,得出各个区间的系统放大倍数a(a通过区间内各个输出采样和输入采样的比值平均值计算得来),至此10个区间的动态放大倍数计算完成。
16.智能建立动态模型:
17.一般静态纯滞后系统的开环传递函数如下表示:
18.g(s)=g0(s)e-τs
=k0*e-τs
/(t0+1)
19.其中g0(s)为不包括纯滞后时间τ的对象模型,τ为纯滞后时间,为系统放大倍数,为动态时间常数;由于系统的放大倍数是根据输入采样而动态变化的,所以程序会根据漏斗的实际输入值而自动匹配相应的放大倍数,从而使系统的开环传递函数呈现动态性。
20.参数分配
21.分配原则是漏斗料位最高的给料参数最大,反之最小;在计算出初始总给料系数后,根据各漏斗料位按比例分给5个漏斗的给料参数,先给1-5号中最高料位的料斗分配参数buvmax,由于变频器输出的电机频率存在上限(最大频率为50hz,对于设定参数为1.5),
现场单个料斗给料系数不能超过1.5,若buvmax>1.5,则直接给其分配给料参数1.5,并将初始总给料系数减去1.5作为再次分配的总给料系数,再对其余4个料斗进行分配;分配方式依此类推,直至5个漏斗分配完毕。
22.自动修正
23.5个漏斗初始给料参数分配完成25s后,根据皮带当前瞬时流量与目标流量的差值d,对给料系数进行调整;定义d在正负50之间为死区,将d分为8档:d≤-300,-300<d≤-150,-150<d<-50,50<d<150,150≤d<300,300≤d<450,450≤d<700,d>700;根据不同档位设定不同的总调整增量i和调整周期t;超量时敏感度大,设置调整周期短,总调整增量i为负数,不足量时差值绝对值越大,调整总调整增量i值为正值越大;调整总调整增量i按一定比例分配给5个漏斗,使料斗系数小量连续调整,保证系统趋于稳定;根据前期建立的模型,在2700~3900t/h之间建立重量模型对应的给料参数存储数据库(每100t为一段,即2700~2800,2800~2900以此类推),用于存储不同重量模型值,在经过实际给料运行测试调整,皮带秤在规定的时间内稳定在目标流量正负20t/h的总给料参数值,即在目标流量稳定达到程序设定条件后自动将当前5个漏斗设定给料参数相加,存储到给料参数存储数据库中。
24.在给料参数存储数据库中已存在测试过的给料参数总设定值时,如果在作业过程中该参数被系统调用,经过一段时间的运行,在目标流量稳定达到程序设定条件后,如果流量能够稳定35s,则系统会自动比较实际运行参与测试过的给料参数总设定值偏差是否在合理范围内;如果偏差不在合理范围内,则自动将给料参数存储数据库中存储的测试过的给料参数总设定值替换为当前5个漏斗相加的给料参数值的自动修正。
附图说明:
25.图1为全自动给料系统框图。
26.图2为全自动给料系统控制原理图。
具体实施方式:
27.实施过程中各个漏斗需要单独控制,总输出量要求平稳,所以当其中的一个漏斗的料位较高需要增加给料系数时,其他漏斗要相应地降低给料系数。原系统的各个漏斗的给料系数为0.63-1.3区间内变化,把漏斗的初始值都设定为1,总给料系数为(1/5+1/5+1/5+1/5+1/5)*5=5,当其中一个漏斗的系数增加为1.1时,总系数就增加到了5.1,这样总的输出流量必然增加,在调试过程因为分子增加了0.1,我们让分子也增加0.1,即增加了1.1/5.1,而其它漏斗系数则从1将为了1/5.1,总的输出系数为(1.1/5.1+1/5.1+1/5.1+1/5.1+1/5.1)*5=5保持不变,实现了总输出流量的稳定。总和不变的策略经过测试运行,不能适应所有的料种试验,这就需要再次试验参数分配和自动修正。
28.动态数学模型建立后建立预估器补偿模型(补偿后的等效对象模型中消除其纯滞后特性),力图将被过程中被延迟了的时间的被控量提前送入调节器,因而调节器能提前动作,这样通过补偿装置消除了纯滞后特性在闭环中的影响,从而明显地减小过程的超调量,缩短过度过程时间,有效地提高控制水平。计算出总的给料系数后按照上述系数分配的原则进行参数分配,五个漏斗的初始参数按照一套经验系数进行分配,分别为0.65,1.3,1.1,
1.3,0.65,如果出现料位总是较低的情况,可以根据料斗料位情况分配固定系数给此料斗。
29.在后续列车的卸车过程中先通过自学习模式阶段,首先通过固定给料参数4.8测出所卸车物料皮带流量为3350,正处在2700~3900t/h的区间范围内,如果参数存储数据存在已经实际测试过的给料参数总设定值,直接调用该总参数作为初始总给料系数,然后对5个漏斗进行参数分配。该方式直接跳过寻找合适给料总参数的过程,减少了调整频次,同时也保证了给料流量的稳定。
30.在给料参数存储数据中已经存在测试过的给料参数总设定值时,如果在作业过程中该参数呗系统调用,经过运行证明在目标流量稳定达到设定条件后,如果流量能够稳定30s,则系统会自动比较实际运行参与测试过的给料参数总设定是够在合理范围内。如果偏差不在合理范围内,则自动将参数存储数据库中存储的测试过的给料参数总设定值替换为当前5个漏斗相加的给料参数值之和。