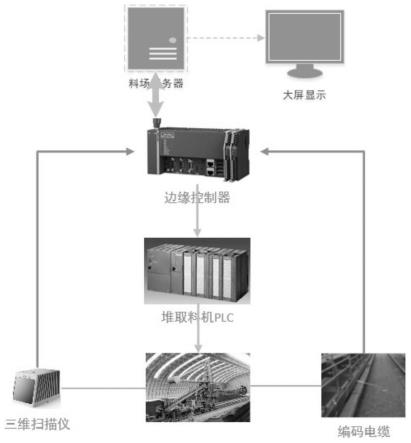
1.本发明涉及自动控制技术领域,具体为一种斗轮堆取料机的全自动堆料控制系统。
背景技术:2.目前散料场通常为人工操作堆取料机进行堆料,而散料场大多数为封闭料场,现场环境恶劣,粉尘浓度高,严重威胁到现场操作人员的身体健康。且驾驶室离堆取料机斗轮距离较远,尤其是夜晚作业,驾驶工人的视线严重受影响。人工操作过程中劳动强度较高,安全稳定运行完全由员工操作水平和工作状态决定,操作工长时间疲劳工作,容易导致精力分散而出现安全事故。由于每个堆取料机操作工的操作习惯和经验不一样,无法做到按统一标准进行堆料作业。且人工控制不可控因素多,从而导致堆料不规范、料堆堆形不规整,不便于后续的取料作业,为此我们提出一种斗轮堆取料机的全自动堆料控制系统用于解决上述问题。
技术实现要素:3.本发明的目的在于提供一种斗轮堆取料机的全自动堆料控制系统,以解决上述背景技术中提出的问题。
4.为实现上述目的,本发明提供如下技术方案:一种斗轮堆取料机的全自动堆料控制系统,包括堆取料机的自动控制系统、作业策略制定系统和防碰撞及故障检测安全系统,
5.所述堆取料机的自动控制系统包括堆取料机、控制系统和两个三维激光扫描仪,两个所述三维激光扫描仪分别固定在所述堆取料机的司机室两侧,所述堆取料机和两个所述三维激光扫描仪均电性连接在所述控制系统;
6.所述作业策略制定系统包括边缘服务器、传感器,所述边缘服务器电性连接三维激光扫描仪,所述传感器固定安装在堆取料机上用于控制堆取料机的运动动作;
7.所述防碰撞及故障检测安全系统包括摄像头、人车识别摄像头、防碰撞保护和故障检测装置,所述防碰撞保护和故障检测装置均安装在堆取料机车身前后及大臂上,所述人车识别摄像头固定安装在堆取料机上,所述摄像头固定安装在堆取料机关键位置。
8.优选的,所述堆取料机的自动控制系统利用边缘计算服务器进行边缘计算和控制。
9.优选的,所述堆取料机的自动控制系统利用三维成像技术,通过边缘计算服务器分析料堆的点云数据,为堆取料机堆料自动作业提供数据基础。
10.优选的,所述作业策略制定系统中控制堆取料机的运动动作包括自动行走、自动回转和自动俯仰;所述作业策略制定系统中控制堆取料机行走和旋转定位的传感器采用编码电缆和旋转编码器,俯仰采用倾角传感器和编码电缆;每种定位均采用两种以上的传感器进行冗余,能实时获取堆取料机的行走数据、俯仰和旋转的角度。
11.优选的,所述作业策略制定系统依据料场三维数据,通过自动堆料算法,制定合适
的堆料策略。
12.优选的,所述作业策略制定系统依据料场三维数据,通过堆料点计算算法,计算出合适的落料点。
13.优选的,所述防碰撞系统包含硬件防碰撞和软件防碰撞,硬件防碰撞是通过在机车前后和大臂上安装防碰撞装置;软件防碰撞是边缘计算服务器依据机车和料场相关参数,计算出安全距离,进行分等级报警。
14.优选的,所述故障检测安全系统的具体安全措施是在堆取料机上安装人车识别摄像头,进行分等级报警。
15.优选的,所述故障检测安全系统具体是在堆取料机关键位置安装摄像头,进行实时监控。
16.与现有技术相比,本发明的有益效果是:
17.1、堆料全自动化后,不再需要人工在现场进行堆料操作,减轻了工人的劳动强度;
18.2、采用全自动堆料方式堆料,可以避免人工操作时易产生的不确定性和不稳定性,提高堆料效率;
19.3、依据作业区域信息和来料的数据信息,通过边缘计算机精准计算后,制定堆料策略;依堆料策略进行堆料,料堆更规整,有利于堆取料机后续进行取料操作,并大大提升了料场的利用率。
附图说明
20.图1为本发明堆取料机全自动堆料控制系统硬件框图;
21.图2为本发明三维扫描仪扫描料堆的三维点云数据图;
22.图3为本发明料堆的静态图;
23.图4为本发明斗轮堆取料机全自动堆料控制系统的软件框图。
具体实施方式
24.下面将结合本发明实施例中的附图,对本发明实施例中的技术方案进行清楚、完整地描述,显然,所描述的实施例仅仅是本发明一部分实施例,而不是全部的实施例。基于本发明中的实施例,本领域普通技术人员在没有做出创造性劳动前提下所获得的所有其他实施例,都属于本发明保护的范围。
25.实施例
26.参照图1-4,该实施例提供了一种斗轮堆取料机的全自动堆料控制系统,包括堆取料机的自动控制系统、作业策略制定系统和防碰撞及故障检测安全系统,
27.堆取料机的自动控制系统包括堆取料机、控制系统和两个三维激光扫描仪,两个三维激光扫描仪分别固定在堆取料机的司机室两侧,三维扫描仪是全自动堆料控制系统的“眼睛”,实时扫描采集作业区域数据,为堆料自动控制提供数据。三维扫描仪的原理是创建物体几何表面的点云(point cloud),这些点可用来插补成物体的表面形状,从而建立物体的三维表面形状;堆取料机和两个三维激光扫描仪均电性连接在控制系统,堆取料机的自动控制系统利用边缘服务器进行边缘计算和控制,堆取料机的自动控制系统利用三维成像技术,通过边缘服务器分析料堆的点云数据,为堆取料机堆料自动作业提供数据基础,
28.作业策略制定系统包括边缘服务器(即边缘控制器)、传感器,边缘服务器电性连接三维激光扫描仪,传感器固定安装在堆取料机上用于控制堆取料机的运动动作;作业策略制定系统中控制堆取料机的运动动作包括自动行走、自动回转和自动俯仰;
29.边缘服务器将点云数据处理后,依据料场煤堆的三维立体图,结合堆料工艺和料场规则来设计堆料策略,计算落料点,斗轮首次落料点对位时,三维扫描仪提供斗轮空间位置的实时数据。在堆料作业时,实时反馈料堆高度。按堆料策略执行堆料操作,并依据剩余料量判断是否停止堆料,开始遛垛。调用三维成像模型,对目标料堆进行三维计算,制定遛垛方案,开始自动遛垛;
30.具体如图3为一个料堆的静态图,作业策略制定系统依据料场三维数据,通过自动堆料算法,制定合适的堆料策略,h是料高,r是底部堆圆的半径。定点堆料的落料点的计算与安息角、料场大小和料堆最大高度有关,料堆高度又与堆取料机上仰极限角有关。堆取料机的上仰极限高度h
仰
=l
·
sinα
仰
,其中l为悬臂臂长,α
仰
为堆取料机上仰极限角。悬臂离地面的高度h
地
=h
轨道
+h
悬臂
,其中h
轨道
为轨道表面距地面的高度,h
悬臂
为堆取料机悬臂水平打直距轨道的高度。因此可知,堆取料机可堆料堆的高度:h
堆
=h
仰
+h
地
。
31.通过料种查到常见料种的安息角,利用安息角θ和料堆高度,推出物料底部的堆积圆半径,得出堆料范围。料堆底部半径r
料
=h/tanθ,料堆底部直径d
料
=2r
料
。已知料堆底部大小,再结合料场的大小,通过边缘服务器算出堆料点和堆料轨迹。
32.系统根据边缘服务器提供的堆料作业轨迹进行作业,并将作业轨迹解析为堆取料机plc具体的控制指令。如启动堆料作业模式、大车行走的目标地址,旋转俯仰角度和大车寸动的距离等,堆取料机作业轨迹的行走和旋转定位的传感器采用编码电缆和旋转编码器,俯仰采用倾角传感器和编码电缆;每种定位均采用两种以上的传感器进行冗余,能实时获取堆取料机的行走数据、俯仰和旋转的角度;
33.如图4所示为系统软件框图,其中应用层采用b/s架构,便于直观管理和操作,人机交互简单,主要包含各个功能模块的管理、显示和设备诊断等功能。数据层对各生产环节采集到的数据分区域管理,并可实现数据互通,便于对数据进行整理、保存和生成相应报表数据,并提供到其他环节进行数据分析。控制层主要采用plc控制,对整个作业流程进行控制。增加边缘控制器,引入配套的算法进行精准控制,对生产数据进行深度挖掘和运用,实现最优控制的目标。执行层主要是控制相关的底层硬件设备,传感器采集数据,电机启停等。
34.防碰撞及故障检测安全系统包括摄像头、人车识别摄像头、防碰撞保护和故障检测装置,防碰撞保护和故障检测装置均安装在堆取料机车身前后及大臂上,防碰撞系统包含硬件防碰撞和软件防碰撞,硬件防碰撞是通过在机车前后和大臂上安装防碰撞装置;软件防碰撞是边缘计算服务器依据机车和料场相关参数,计算出安全距离,进行分等级报警。
35.人车识别摄像头固定安装在堆取料机上,摄像头固定安装在堆取料机关键位置,故障检测安全系统的具体安全措施是在堆取料机上安装人车识别摄像头,进行分等级报警,同时在堆取料机关键位置安装摄像头,进行实时监控,进而配合防碰撞系统为整个执行过程中的自动控制保驾护航。
36.尽管已经示出和描述了本发明的实施例,对于本领域的普通技术人员而言,可以理解在不脱离本发明的原理和精神的情况下可以对这些实施例进行多种变化、修改、替换和变型,本发明的范围由所附权利要求及其等同物限定。