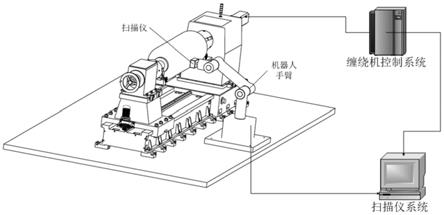
1.本发明涉及固体火箭发动机领域,提供了一种软质药柱芯模带药复合壳体实时缠绕成型装置,具体涉及软质药柱芯模、发动机壳体及喷管的一体化成型控制装置。
背景技术:2.传统发动机复合壳体及喷管成型技术采用金属或其他材料硬质芯模缠绕制备复合壳体,拆下芯模后,参考金属壳体的制造工序,然后再安装衬层、绝热层、药柱、外挂件等,但其中存在生产工艺复杂,不便于自动化生产改造;出于简化工艺便于自动化生产的需求,提出一种以粘弹性药柱为芯模进行壳体的一体化缠绕成型方法,但此过程中主要存在以下问题:
3.1)带药复合壳体的芯模(药柱)的刚性相比常规金属芯模的刚性较弱,在带张力缠绕的过程中,由于芯模变形会使缠绕的纤维层存在变形使缠绕件的截面发生变化,从而会引起成型后复合壳体的尺寸发生变化,显著影响产品尺寸和质量;
4.2)对于发动机外壳体结构的一体化成型过程,如壳体封头段与喷管的连接部分存在变截面结构,由于该结构为非圆柱面复杂结构,需要结合外型面尺寸逐层改变缠绕参数,可通过单层扫描单层缠绕的补偿方法,使其与设计模型截面径向尺寸一致。
技术实现要素:5.本发明解决的技术问题是:克服现有技术的不足,提供一种软质药柱芯模带药复合壳体实时缠绕成型装置,解决现有带药复合壳体成型过程中存在的软质药柱芯模变形问题及发动机外壳体结构一体化成型过程中存在的变截面问题。
6.本发明解决技术的方案是:一种软质药柱芯模带药复合壳体实时缠绕成型装置,所述复合壳体包括一体缠绕成型的前封头、筒段和后封头,该装置包括复合壳体缠绕成型三维检测单元、反馈成型控制单元:其中:
7.复合壳体缠绕成型三维检测单元,用于在复合壳体缠绕成型过程中完成单纤维层或一定纤维层数缠绕工作后,获取实际复合壳体外型面尺寸,所述外型面尺寸包括复合壳体的外径,以理论模型复合壳体任意一侧端面为xoy平面,其与复合壳体中心轴线交点作为坐标原点o,复合壳体中心轴线为z轴,建立参考坐标系,在参考坐标系下,将实际复合壳体外型面尺寸与当前纤维层理论模型尺寸比对,得到复合壳体的变形量与变形位置;
8.反馈成型控制单元,将变形量与预设阈值进行比较,将复合壳体沿z轴方向进行分区,如果变形量大于等于阈值对应的变形位置,将此轴向位置左右加固定数量的纱宽尺寸形成一个轴向范围,壳体沿着此轴向范围的区域列入需要调整区域,将剩余的区域列入不需要调整区域;依据外径偏小增加厚度、外径偏大减小厚度的原则,在需要调整区域变形位置调整下一层缠绕工艺参数以修改下一缠绕层的厚度来补偿变形量;在不需要调整区域的变形位置保持下一层缠绕设计参数不变;根据调整后下一层缠绕工艺参数自动输出机床运动参数控制下一缠绕层的缠绕过程。
9.所述缠绕工艺参数包括缠绕张力、纱宽。
10.所述采用固定间隔将变形量分为多个梯度,每个固定间隔对应固定的缠绕张力或者固定纱宽,根据变形量为几个固定间隔对应增加或者减少固定的缠绕张力或者固定纱宽;其中,增加厚度时,减小纱宽、减小张力;减小厚度时,增大纱宽、增大张力。
11.所述复合壳体缠绕成型三维检测单元包括机器人手臂和三维扫描测量装置;三维扫描测量装置安装在机器人手臂末端;
12.机器人手臂,在复合壳体缠绕成型过程中完成单纤维层或一定纤维层数缠绕工作后,带动三维扫描测量装置沿复合壳体轴向和环向移动;
13.三维扫描测量装置,通过扫描机构实时测量复合壳体外型面尺寸,所述外型面尺寸包括复合壳体的外径,以理论模型复合壳体任意一侧端面为xoy平面,其与复合壳体中心轴线交点作为坐标原点o,复合壳体中心轴线为z轴,建立参考坐标系,在参考坐标系下,将实际复合壳体外型面尺寸与当前纤维层理论模型尺寸比对,得到复合壳体的变形量与变形位置。
14.所述扫描机构为接触式扫描传感器或者激光非接触式扫描传感器。
15.所述接触式扫描传感器包括t型顶针球头部,t型顶针球头部内带弹力预紧装置、位移传感器;其中:
16.t型顶针球头部内带弹力预紧装置使t型顶针球头部与缠绕件外型面紧密接触,t型顶针球头部内带位移传感器,用于实时记录沿着缠绕件外型面运动的过程中球部与芯模轴之间的距离,从而得到实际复合壳体外型面尺寸。
17.所述接触式扫描传感器为激光三维扫描仪器,激光三维扫描仪器获取实际复合壳体以参考坐标系为基准孪生的三维模型,根据孪生的壳体三维模型获取实际复合壳体当前缠绕层外型面尺寸。
18.本发明与现有技术相比的有益效果是:
19.(1)、本发明由于采用了以药柱充当芯模的方法,实现了一体成型带药复合壳体制备技术的零的突破;简化了产品的生产工艺;大大缩短了产品的加工周期,降低了产品的生产成本;
20.(2)、本发明由于采用三维扫描装置实时测量当前缠绕层尺寸,反馈调节下一缠绕层的工艺参数的方法,在实际加工过程中解决了当前以软质药柱充当芯模一体成型带药复合壳体技术中存在的芯模变形引起的壳体型面产生的变形问题,以及延伸解决了变截面药柱缠绕补偿的问题;
21.(3)、本发明采用根据测量结果实时反馈,将缠绕层分区,根据变形量设置固定间隔,依据变形量间隔设置张力梯度、纱宽梯度,依据变形量间隔按梯度调整缠绕张力、缠绕纱宽参数实时补偿变形量的方法,突破了一体成型带药复合壳体制备技术的关键瓶颈。
附图说明
22.图1为本发明实施例应用的缠绕流程示意图。
23.图2为由本发明实施例系统组成的结构示意图。
24.图3(a)为本发明实施例测量方法的接触式在线测量装置结构示意图。
25.图3(b)为本发明实施例测量方法的t型顶针结构示意图。
26.图4为本发明实施例测量方法的非接触式在线测量装置结构示意图
具体实施方式
27.下面结合实施例对本发明作进一步阐述。
28.如图1所示,复合壳体缠绕过程在线监测与闭环成型控制装置主要是测量缠绕过程壳体外型面尺寸并与设计模型尺寸比对,分析缠绕件变形量及位置并调整缠绕参数在线补偿尺寸偏差,解决带药壳体带张力缠绕过程中软质芯模变形引起壳体尺寸变形、发动机壳体结构一体化成型时存在变截面等问题。所述复合壳体包括串联连接并一体缠绕成型的前封头、筒段和后封头。
29.如图2所示,本发明提供的一种软质带药芯模复合壳体缠绕成型控制装置,包括复合壳体缠绕成型三维检测单元、反馈成型控制单元:其中:
30.复合壳体缠绕成型三维检测单元,用于在复合壳体缠绕成型过程中完成单纤维层或一定纤维层数缠绕工作后,获取实际复合壳体外型面尺寸,所述外型面尺寸包括复合壳体的外径,以理论模型复合壳体任意一侧端面为xoy平面,其与复合壳体中心轴线交点作为坐标原点o,复合壳体中心轴线为z轴,建立参考坐标系,在参考坐标系下,将实际复合壳体外型面尺寸与当前纤维层理论模型尺寸比对,得到复合壳体的变形量与变形位置;
31.反馈成型控制单元,将变形量与预设阈值进行比较,将复合壳体沿z轴方向进行分区,如果变形量大于等于阈值对应的变形位置,将此轴向位置左右加固定数量的纱宽尺寸形成一个轴向范围,壳体沿着此轴向范围的区域列入需要调整区域,将剩余的区域列入不需要调整区域;依据外径偏小增加厚度、外径偏大减小厚度的原则,在需要调整区域变形位置调整下一层缠绕工艺参数以修改下一缠绕层的厚度来补偿变形量;在不需要调整区域的变形位置保持下一层缠绕设计参数不变;根据调整后下一层缠绕工艺参数自动输出机床运动参数控制下一缠绕层的缠绕过程。
32.所述缠绕工艺参数包括缠绕张力、纱宽。
33.所述采用固定间隔将变形量分为多个梯度,每个固定间隔对应固定的缠绕张力或者固定纱宽,根据变形量为几个固定间隔对应增加或者减少固定的缠绕张力或者固定纱宽;其中,增加厚度时,减小纱宽、减小张力;减小厚度时,增大纱宽、增大张力。
34.优选地,所述复合壳体缠绕成型三维检测单元包括机器人手臂和三维扫描测量装置;三维扫描测量装置安装在机器人手臂末端;
35.机器人手臂,在复合壳体缠绕成型过程中完成单纤维层或一定纤维层数缠绕工作后,带动三维扫描测量装置沿复合壳体轴向和环向移动;
36.三维扫描测量装置,通过扫描机构实时测量复合壳体外型面尺寸,所述外型面尺寸包括复合壳体的外径,以理论模型复合壳体任意一侧端面为xoy平面,其与复合壳体中心轴线交点作为坐标原点o,复合壳体中心轴线为z轴,建立参考坐标系,在参考坐标系下,将实际复合壳体外型面尺寸与当前纤维层理论模型尺寸比对,得到复合壳体的变形量与变形位置。
37.所述扫描机构为接触式扫描传感器或者激光非接触式扫描传感器。
38.优选地,接触式扫描传感器结构如附图3(a)所示,所述接触式扫描传感器包括t型顶针球头部,t型顶针球头部内带弹力预紧装置、位移传感器;其中:
39.如图3(b)所示,t型顶针球头部内带弹力预紧装置使t型顶针球头部与缠绕件外型面紧密接触,t型顶针球头部内带位移传感器,用于实时记录沿着缠绕件外型面运动的过程中球部与芯模轴之间的距离,从而得到实际复合壳体外型面尺寸。三维扫描测量装置通过分析程序实时比对当前缠绕层的实际与理论模型(以设计模型中当前层外型面与芯模轴之间的距离作为基准,实时比对测试数据,筛选出当前缠绕层的变形量与变形位置),得出当前缠绕层的变形量与变形位置。
40.优选地,非接触式扫描传感器如附图4所示,所述接触式扫描传感器为激光三维扫描仪器,激光三维扫描仪器获取实际复合壳体以参考坐标系为基准孪生的三维模型,根据孪生的壳体三维模型获取实际复合壳体当前缠绕层外型面尺寸。
41.三维扫描测量装置可将实际复合壳体的孪生三维模型与理论模型比对,得出外径变形量超过阀值的轴向变形位置,将此轴向位置左右加固定数量的纱宽尺寸形成一个轴向范围,壳体沿着此轴向范围的区域列为需要调整区域;接触式扫描传感器的测量结果为壳体沿着轴向的外径尺寸,将此尺寸与壳体理论外径比对,得出壳体的实际变形位置,然后筛选出需要调整区域。
42.实施例1
43.本发明某一具体实施例,采用复合壳体闭环成型控制系统,一体成型缠绕制备了一发ф300mm,长度1000mm的变截面软质药柱芯模的带药复合壳体。该实施例解决了粘弹性药柱充当缠绕芯模存在的芯模刚性不足,在带张力缠绕过程中容易发生变形引起缠绕层型面尺寸变化的问题,以及发动机外壳体结构一体化成型时存在的变截面问题,提升了产品质量的精细化控制。
44.显然,本领域的技术人员可以对发明进行各种改动和变型而不脱离本发明的精神和范围。这样,倘若本发明的这些修改和变型属于本发明权利要求及其等同技术的范围之内,则本发明也意图包括这些改动和变型在内。