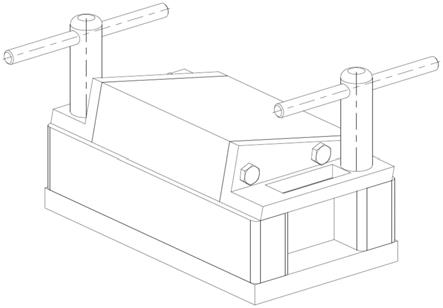
[0001]
本实用新型涉及一种适配器成型模具。
背景技术:[0002]
适配器作为飞行器弹射装置的重要组成部分,是飞行器与弹射装置之间的连接和支撑装置,其主要作用是在飞行器贮运、起吊、运输和弹射过程中,减缓飞行器因过载而产生的冲击和振动,在飞行器弹射时起导向作用。近年来,通过不断发展,为了适应不同的平台,适配器材料不断取得进展,所采用的材料主要有橡胶类(如天然橡胶、丁腈橡胶、丁基橡胶、乙烯丙烯橡胶、氯丁橡胶等)、聚氨酯弹性体、聚氨酯泡沫等材料或上述几种材料的混合物。从有关的文献资料来看,其中以聚氨酯弹性体和聚氨酯泡沫的应用最为广泛。适配器结构也发展得多种多样,同时加工成型方法也各不相同,目前尚无现成方案可解决某些异形适配器的成型问题,能满足适配器功能需求,同时提高使用性能。
技术实现要素:[0003]
为解决上述技术问题,本实用新型提供了一种适配器成型模具,该适配器成型模具能够保证适配器各技术要求,大大提高适配器使用性能,符合经济性、工艺性、实用性以及可操作性要求。
[0004]
本实用新型通过以下技术方案得以实现。
[0005]
本实用新型提供的一种适配器成型模具,包括底板;所述底板上垂直固连有模框,有上模可转动固定在模框中部,上模、模框、底板构成一中空腔体;所述上模的顶面平行于待成型的适配器导轨槽平面,且上模的顶面不平行于底板的上表面。
[0006]
所述底板上有下模,在底板中部有预埋件支撑座垂直设置在下模中。
[0007]
所述底板上侧面位置有斜模。
[0008]
所述模框上有左连接板和右连接板分别位于上模的两侧面并固定于上模,上模通过定位销定位于模框。
[0009]
所述定位销较上模和模框的安装平面高3mm。
[0010]
所述左连接板和右连接板的顶面齐平于上模顶面。
[0011]
本实用新型的有益效果在于:保证了适配器各尺寸精度要求、功能需求,经济性、实用性强;有效防止聚四氟乙烯贴膜脱落,保证适配器的整体性;既保证适配器在导轨面上的有效滑动,又满足耐磨、耐高温、防粘接性能要求;既保证定位需求又符合倾斜起模设计,符合结构与功能一体化设计;符合模具设计的经济性、工艺性、实用性以及可操作性要求。
附图说明
[0012]
图1是本实用新型的正等轴结构示意图;
[0013]
图2是图1的正剖视结构示意图;
[0014]
图3是图1在使用时的侧剖视结构示意图。
[0015]
图中:1-下模,2-上模,3-模框,4-底板,5-预埋件支撑座,6-斜模,7-左连接板,8-右连接板,9-螺杆,10-把手,11-金属预埋件,12-适配器基体,13-聚四氟乙烯贴膜。
具体实施方式
[0016]
下面进一步描述本实用新型的技术方案,但要求保护的范围并不局限于所述。
[0017]
如图1至图3所示的一种适配器成型模具,包括底板4;底板4上垂直固连有模框3,有上模2可转动固定在模框3中部,上模2、模框3、底板4构成一中空腔体;上模2的顶面平行于待成型的适配器导轨槽平面,且上模2的顶面不平行于底板4的上表面。
[0018]
底板4上有下模1,在底板4中部有预埋件支撑座5垂直设置在下模1中。
[0019]
底板4上侧面位置有斜模6。
[0020]
模框3上有左连接板7和右连接板8分别位于上模2的两侧面并固定于上模2,上模2通过定位销定位于模框3。
[0021]
定位销较上模2和模框3的安装平面高3mm。
[0022]
左连接板7和右连接板8的顶面齐平于上模2顶面。
[0023]
基于上述,本实用新型一体成型的方法如下:
[0024]
①
安装:将模框3和底板4固连,在模框3腔体内依次装配下模1、预埋件支撑座5、斜模6;
[0025]
②
预埋:将金属预埋件11放置于预埋件支撑座5上;
[0026]
③
粘接:在上模2的内顶面上粘接固定聚四氟乙烯贴膜13,后将上模2安装于左连接板7和右连接板8;
[0027]
④
发泡:将发泡材料加入至腔体内,合上上模2,将螺杆9拧入模框3中使上模2压紧于模框3;
[0028]
⑤
起模:待发泡完成,依次取下螺杆9、上模2,敲击底板4底面将适配器脱出,旋转并取出预埋件支撑座5得到成型的适配器。
[0029]
步骤
①
中,将模框3和底板4固连后放置于平整水平面上。
[0030]
步骤
④
中,通过把手10将螺杆9拧入。
[0031]
实施例
[0032]
采用上述方案,具体操作过程如下:
[0033]
首先,模具发泡前,先将底板4与模框3用螺栓固连在一起,放置于平整地面上,依次按安装连接关系将下模1、预埋件支撑座5、斜模6装配到模框3腔体内,与底板4接触,金属预埋件11按图所示放置于预埋件支撑座5上。
[0034]
其次,将聚四氟乙烯贴膜13稍微粘接固定到上模2导轨槽面上,分别与左连接板7和右连接板8用螺栓紧固连接后放置于一边,设置上模2与模框3定位销高于定位平面3毫米,将发泡材料加入型腔内,快速合上上模2,用把手10将螺杆9拧入螺纹孔中,使上模2压紧到模框3上表面。
[0035]
最后,模具发泡完成,拧松并取下螺杆9,将左连接板7、右连接板8沿垂直于上模2顶面方向抬起,用工具轻敲底板4底面起模孔,慢慢将适配器脱出,然后通过旋转并取出预埋件支撑座5得到完整适配器,将适配器基体12作进一步处理即完成加工。
[0036]
由此,上模顶面设计为与适配器导轨槽平面平行,模具顶面与底面不平行,通过预
埋件支撑座,实现适配器金属预埋件与适配器基体的整体成型,保证了适配器的功能需求,提高了使用性能;起模时,上模往一倾斜角度方向起模;将聚四氟乙烯贴膜粘接到上模导轨槽型腔面上,保证与适配器基体发泡时一体成型;上模与模框安装定位销只高出安装平面3毫米,既保证定位要求,又满足倾斜起模设计。