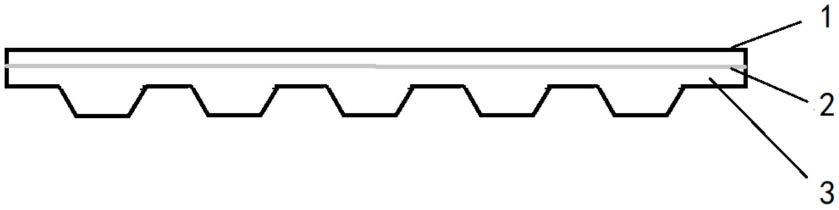
1.本发明涉及一种导电同步输送带及其制备方法,属于生产线技术领域。
背景技术:2.随着自动化水平的提高,光伏行业的芯片制造也引入了自动化设备,而在芯片镀膜阶段,需要将芯片输送到镀膜机指定位置,完成镀膜。
3.目前输送芯片采用的是带凸点的钢带,由于钢带表面光滑,虽然添加了凸点用于提高钢带的耐磨性,但是,随着加工速度的提升,摩擦系数远远达不到要求,导致芯片滑动偏离指定位置,从而大大影响了芯片镀膜的效率,为了解决这一问题,需要设计一款导电同步输送带。
4.现有的具有导电性的同步输送带采用钢丝绳作为骨架材料,外面包覆tpu 材料;具体是将通过放线架控制的钢丝绳均匀的排列在模具辊上,再把tpu材料熔融后挤出堆积到钢丝绳上,经过辊筒冷却压制得到。此方法的不足之处是:
5.1.由于钢丝绳是由钢丝缠绕而成,同步输送带在使用过程中,钢丝绳内部的钢丝由于长期使用会出现局部断裂,导致某段钢丝绳的导电性能失效,从而影响整个同步输送带的导电效果,大大降低了同步输送带的使用寿命。
6.2.每次生产都需要重新排布钢丝绳,并通过放线架控制每根钢丝绳的张力是均匀一致的。该过程耗时耗力,大大降低了生产效率。
7.3.为了满足同步输送带的拉断强度,需采用直径为2mm左右的钢丝绳作为骨架材料,包覆上tpu后,该同步输送带的厚度高达8mm,远厚于原有的钢带,大大降低了输送带的耐屈挠性,无法配套原有设备进行使用。
技术实现要素:8.针对现有技术存在的上述问题,本发明提供的导电同步输送带在保证导电性能的同时,提高输送带的摩擦性能,确保高速运转下,芯片处于指定位置,降低生产成本,提高生产效率,延长同步输送带的使用寿命。
9.本发明提供的技术方案如下:
10.一种导电同步输送带,通过如下步骤制得:
11.步骤a)将一打孔不锈钢片非水平角度放入模具辊;
12.步骤b)调整模具辊的转速,将熔融tpu堆积于不锈钢片两侧;
13.步骤c)步骤b)所得半成品经辊筒冷却压制,得导电同步输送带成品。
14.优选地,步骤a)的不锈钢片以0-30
°
的角度进入模具辊,以给熔融的tpu 材料预留一定的空间,确保熔融tpu材料在钢片的底面堆积,确保钢片被tpu 完全包覆,从而控制产品下表面的厚度。
15.优选地,步骤b)模具辊的转速为0.5r/min-0.8r/min。
16.优选地,模头温度180-200℃。
17.采用打孔的不锈钢钢片作为骨架层,所述骨架层的上表面和下表面分别设置有上表层和下表层,所述上表层和下表层为聚氨酯层。
18.所述下表层设有等间距的齿,所述下表层的齿与齿轮咬合运行。较佳地,所述齿厚度为2-7mm。
19.优选地,所述钢片的厚度为0.4-1.2mm(满足输送带的拉断强度的同时满足曲挠性)。
20.优选地,所述钢片上孔尺寸为:长14-17mm,宽14-17mm。
21.优选地,所述孔可按任意规则排布,但为满足产品导电性能的需求,所述孔之间的间隙为3-5mm。
22.优选地,所述导电同步输送带的厚度为4-12mm。
23.此外,由于所述导电同步输送带带有齿,故其厚度本来就是不均的,故而本身就具有一定的曲挠性。
24.与现有技术相比,本发明的有益效果是:
25.1.采用本发明替代钢片输送带,输送带表面摩擦力增大,有效避免了芯片因高速运转而在输送带上的滑移,从而导致滑移芯片的位置偏移,大大提高了生产效率。
26.2.采用本发明替代钢片输送带,所述同步输送带绕设在齿轮外,所述齿轮带动输送带同步运转,通过齿与齿之间的咬合,可避免类似钢片运输带在辊筒上运转出现的打滑情况,提高了芯片的输送精度,大大降低了芯片镀膜的错误率,有效降低了因生产残次品而出现的材料浪费。
27.3.采用打孔的钢片替代钢丝绳,一方面,由于钢片是一个完整的导电体,在使用过程中不会出现钢丝绳局部断裂而影响整个产品导电效果的情况,满足输送带的导电性能,能有效避免芯片电荷堆积(钢丝绳在长期使用过程中易断裂,影响输送带的导电性能,则可导致芯片电荷堆积,而本发明提供的导电同步输送带的骨架为钢片,不易断裂,故能避免芯片电荷堆积),确保芯片镀膜效果的稳定性,也大大延长了产品的使用寿命;另一方面,由于内部使用钢片,从而降低了本发明提供的导电同步输送带的厚度,提高了导电同步输送带的曲挠性,使得导电同步输送带可以配合现有设备使用,避免了设备更换而提高的生产成本。
28.4.采用钢片替代现有的钢丝绳后,省去了排线工序,简化了生产工艺,提高生产效率。
附图说明
29.图1为本发明提供的一种导电同步输送带的示意图;
30.其中,1、上表层;2、骨架层;3、下表层。
具体实施方式
31.下面结合附图和实施例对本发明做进一步具体的说明。
32.实施例1
33.本发明可以通过以下技术方案来实现:
34.本发明提供的导电同步输送带,是将一打孔的不锈钢钢片作为骨架层2以一定的
角度(0-30
°
)进入模具辊,以给熔融的tpu材料预留一定的空间,确保熔融tpu材料在钢片的背面堆积,再控制模具辊的转速为0.5r/min-0.8r/min(控制熔融tpu的堆积量,确保钢片被tpu完全包覆),其中,模头温度180-200℃,从而控制产品下表面的厚度,这样把tpu材料熔融后挤出堆积到钢片两侧,再经辊筒冷却压制而得。所得的导电同步输送带的下表层设有等间距的齿,这样可以让导电同步输送带通过与齿轮咬合而运行。较佳地,该导电同步输送带的厚度为4-12mm,其中齿厚度为2-7mm。由于导电同步输送带带有齿,故其厚度本来就是不均的,故而满足了输送带所需的曲挠性。
35.上述骨架层2钢片的设置,替代现有的钢丝绳后,省去了排线工序,简化了生产工艺,提高生产效率。而采用不锈钢钢片还可以满足输送带的导电性能,即在使用过程中不会出现钢丝绳局部断裂而影响整个产品导电效果的情况,从而有效避免芯片电荷堆积,影响镀膜效果,大大延长了产品的使用寿命;骨架层2 的上表面和下表面分别设置有上表层1和下表层3。
36.其中,钢片的厚度为0.4-1.2mm,以满足输送带的拉断强度的同时满足曲挠性。且钢片上孔的尺寸为长15mm,宽15mm,各孔之间的间隙为4mm,以满足产品导电性能的需求。
37.采用钢片外包覆tpu的设计,可使输送带表面摩擦力增大,一方面,上表层1有效避免了芯片因高速运转而在输送带上的滑移,从而导致滑移芯片的位置偏移,大大提高了生产效率;另一方面,同步输送带绕设在齿轮外,下表层3 上的齿与齿轮咬合,齿轮带动输送带同步运转,则可避免类似钢片运输带在辊筒上运转出现的打滑情况,提高了芯片的输送精度,大大降低了芯片镀膜的错误率,有效降低了因生产残次品而出现的材料浪费。
38.对上述制得的导电同步输送带与现有钢片输送带进行性能测试试验,结果如表1和表2所示。
39.表1摩擦系数
[0040] 钢片输送带导电同步输送带相对于钢材的静态摩擦系数0.30.5相对于钢材的动态摩擦系数0.160.27
[0041]
表2疲劳数据
[0042] 钢丝绳同步输送带本项目同步输送带使用6个月导电性能正常/镀膜效果稳定导电性能正常/镀膜效果稳定使用12个月导电性能异常/镀膜效果不稳定导电性能正常/镀膜效果稳定