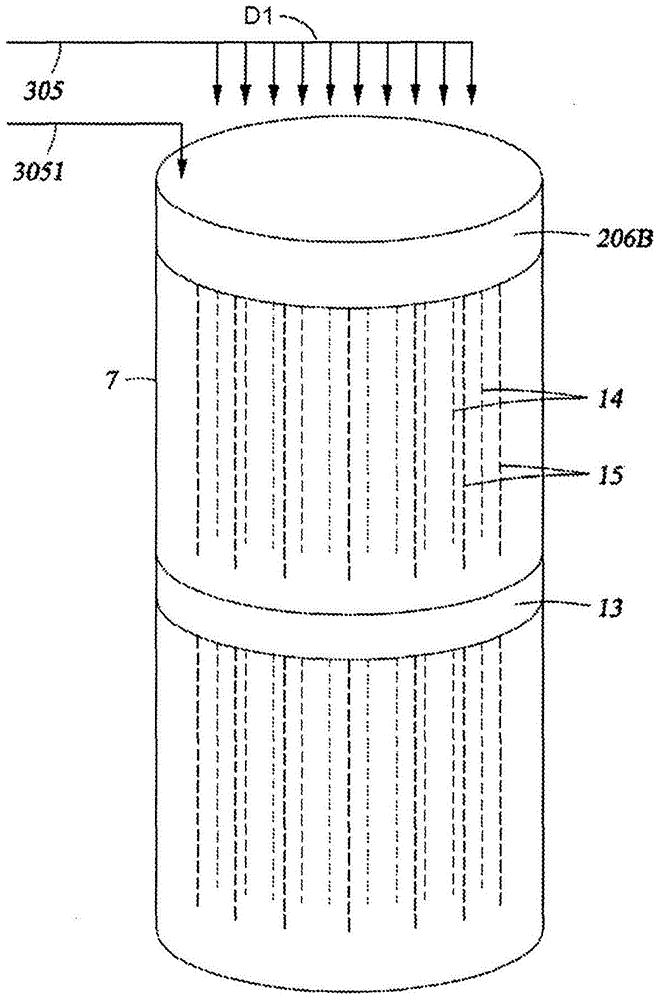
混合器/流动分布器相关申请的交叉引用本申请要求于2011年12月20日提交的U.S.S.N.临时申请号61/578,086和于2012年2月7日提交的EP申请号12154200.5的标题为“混合器/流动分布器”的优先权,该文献的整个公开内容引入本文供参考。技术领域本发明涉及混合器/流动分布器和它们的应用,例如在再生反应器中的应用。本发明涵盖用于控制氧化,例如用于使反应器,例如再生性逆流反应器热再生的方法和设备。
背景技术:燃烧可以用于使用于循环高温化学的反应器,例如再生反应器再生。通常,再生反应器循环是对称(反应化学与再生化学相同)或不对称的(反应化学和再生化学不同)。一类不对称再生反应器,例如用于热解的那些,包括第一和第二区,其中每个区包含至少一个再生床。在放热氧化步骤中例如如下加热该反应器(或再生):将燃料和氧化剂传导至位于第一和第二区之间的混合-分布区,在混合-分布区中混合和分布该燃料和氧化剂,使该燃料和氧化剂燃烧,然后将该燃烧产物传导穿过第二区并离开反应器。在热解步骤期间,将热解原料传导穿过第二区,然后穿过第一区,从而将该热解原料热解并将热从第二区传送到所述第一区。一些再生反应器将燃料和/或氧化剂直接地输送至混合-分布区,而没有让那些料流穿过所述第一或第二区。现有技术参考文献公开了经由穿入反应器系统的喷嘴、分布器或燃烧器将燃料和/或氧化剂导入,该反应器系统使用一般垂直于反应流向并通常穿过反应器容器侧壁的装置。例如,在常规Wulff裂化炉中的放热步骤期间,空气轴向流过再生体,并且经由穿入炉子侧面的喷嘴导入燃料,以与空气(燃烧和释放热)在再生体之间的开放区中结合。再生反应器的一个特征是通过将产物热直接地同流换热(recuperating)到原料中而以高效率执行反应。将燃料或氧化剂经由在反应器以外的喷嘴、分布器或燃烧器径向地导入是不利的,原因在于再生反应器系统不用来将该反应物料流预加热。换言之,让燃料和/或氧化剂的一些部分绕过再生反应器系统将降低反应器系统的效率。已经尝试经由轴向布置在一个或多个再生床内的导管将燃料和/或氧化剂引导至在再生反应器中间或在再生反应器中间附近的位置。例如,美国专利号4,240,805公开了使用轴向布置在再生床内的管子将氧化剂(空气)运载至在再生流路中间附近的位置。这将热朝重整区输送。最近,美国专利号7,815,873公开了经由在第一区内的基本上平行的流路将燃料和氧化剂提供给位于混合-分布区中的混合器-分布器。该混合-分布区位于第一和第二再生区之间,并且该混合器-分布器包括会聚和发散区以改进反应器的热效率。希望进一步的改进。
技术实现要素:发明概述在一个实施方案中,本发明涉及再生方法,包括:(a)经由至少一个第一导管传导燃料和经由至少一个第二导管传导氧化剂,所述第一和第二导管位于反应器系统的同流换热区(recuperationzone)中;(b)使所述燃料的至少一部分与所述氧化剂的至少一部分在混合-分布区中结合并反应以产生热和第一反应产物,所述混合-分布区位于(i)所述反应器系统中和(ii)所述同流换热区下游和反应区上游,所述混合-分布区包括具有MD≤15.0%,压降≤0.3巴(绝对)和总燃料-氧化剂流量≥10.0kg/hr的混合器-分布器;和(c)将所述反应产物传导穿过所述反应区并将所述热的至少一部分从所述反应产物转移至所述反应区。在又一个实施方案中,本发明涉及烃转化方法,包括:(A)为反应器提供燃料和氧化剂,所述反应器包括至少一个混合器-分布器;(B)将所述燃料和氧化剂沿燃料-氧化剂流动方向转移至所述混合器-分布器;(C)在所述混合器-分布器中混合和分布所述燃料-氧化剂流体并使所述氧化剂的至少一部分与所述燃料的至少一部分放热反应以足够将所述反应器的至少一部分加热至≥800℃的温度,所述混合器-分布器包括:(i)至少一个第一挡板和多个第一孔,所述第一挡板和多个第一孔布置在所述混合器-分布器中的第一位置;(ii)至少一个第二挡板和至少一个第二孔,所述第二挡板和第二孔位于所述混合器-分布器中的第二位置,其中(a)所述第一位置在所述第二位置的相对于燃料-氧化剂流体的上游,和(b)所述第一位置具有比所述第二位置更大数量的孔;和(iii)所述混合-分布区的内边界,所述内边界(a)与所述第一挡板的周边和所述第二挡板的周边连接或(b)与所述第一和所述第二挡板的周边足够接近以基本上防止所述燃料-氧化剂流体穿过所述混合-分布区除非经由所述第一和第二孔;(D)沿基本上是所述燃料-氧化剂流动方向的反向的方向为加热的反应器提供第一混合物,所述第一混合物包含烷烃;和(E)将所述第一混合物暴露于所述加热的反应器中的≥800℃的温度下并从所述反应器提取足够的热以将所述第一混合物的烷烃的至少一部分转化成不饱和烃。附图简述图1示意性地示出了本发明使用再生性逆流热解反应器的一个实施方案。图2示意性地示出了图1的反应器7内所选的燃料通道和氧化剂通道的位置。图2A示意性地示出了反应器7的末端9,阴影区示出了燃料孔道14的近似位置。图3A示意性地显示了包括五个穿孔板的混合器-分布器。图3B和3C示意性地示出了板1、3、4和5的穿孔当中的间隔和角度关系。图4示意性地示出了板1-5的板表面积和总穿孔表面积。图5示意性地示出了与板2相邻设置的旋涡装置。优选实施方案的详细描述本发明部分地基于这样的观察结果,即可以通过使用包括多个设置在混合-分布区内的孔的混合器-分布器改进混合和分布效能。在一个实施方案中,混合器-分布器的孔包括多个对燃料和氧化剂的流动开放的空穴,所述空穴位于所述混合-分布区内的或与所述混合-分布区紧邻的一个或多个平面上。例如,空穴可以(i)位于混合-分布区内的一个或多个板上,(ii)位于混合-分布区的边界的一个或多个凸起上(例如,朝向该混合-分布区的中心部),或(iii)安排(i)和(ii)的组合。所述板和/或凸起可以例如,基本上平行,并且可以在所述混合-分布区内间隔有基本上相等的板间间隔。已经发现,使用包括下面所规定的孔安排的混合器-分布器与使用会聚-发散区的混合器-分布器,例如美国专利号7,815,873中描述的那些相比提供改进的混合和分布,尤其是在L:D比≤3.0,例如≤2.0,例如在0.5-1.5的范围内时。术语“L:D比”具有与美国专利号7,815,873中相同的意义,该文献在此整体引入作为参考。还已经发现,常规混合器-分布器,例如包括会聚-发散区的那些对(a)气体流量改变,和(b)在(i)所述反应器组件和(ii)所述混合器-分布器组件之间的轴向失准敏感。已经发现,包括孔排列的混合器-分布器(例如,呈多个基本上平行的穿孔板形式)对此种气体流量改变和混合器-分布器失准明显不那么敏感。在逆流再生式热解反应器系统中使用所述混合器-分布器导致与使用常规混合器-分布器的反应器系统相比效率显著增加。因为混合和流动分布得到改进,再生步骤使用比常规混合器-分布器更少的燃料和氧化剂来达到相同的反应器加热量和反应器加热均匀性。此外,当燃料和热解原料从相同的烃源获得时,在再生步骤期间更少的燃料用量使得更多烃可用于转化成C2不饱和物,从而增加总产率。在一个实施方案中,混合-分布区设置在再生反应器系统的第一和第二反应器之间,其中每个反应器包括例如,至少一个再生床。包括多个孔的混合器-分布器设置在混合-分布区内。混合-分布区可以具有合适的横截面形状以便用于再生反应器系统,例如多边形(三角形、矩形、五边形、六边形等),圆形,椭圆形等,包括它们的组合。孔可以是,例如一个或多个挡板装置中的穿孔,所述挡板装置包括所述混合-分布区的边界的多个板和/或凸起。所述挡板装置基本上阻止反应物(例如,燃料和/或氧化剂)穿过混合-分布区的流动,除非经由所述孔。这可以例如如下实现:将挡板装置的周边接近于混合-分布区的内边界设置以便基本上阻止燃料和/或氧化剂经由基本上避开混合器-分布器的至少一些孔的流程的流动。所谓的基本上阻止是指燃料和/或氧化剂的流量的少于10%(按重量计),例如<5%避开所述混合器-分布器的至少一些孔。现将根据具有长度L和横截面面积A的混合-分布区描述一个实施方案,其中(i)“长度”沿这样的方向限定,该方向与燃料和氧化剂从上游到下游横穿混合-分布区的平均流动平行,且"横截面面积"相对于与L基本上垂直的平面限定。混合-分布区13设置在再生性逆流反应器系统,例如图1所示的反应器系统内。混合-分布区的横截面面积可以例如,(i)在L内基本上恒定和/或(ii)基本上与第一反应器7和/或第二反应器1的横截面面积相同,如图1所示。区16和7各自包括至少一个再生床,其中术语"再生床"是指包含有效储存和传递热的材料的反应器床。在这个实施方案中,至少一个混合器-分布器设置在混合-分布区内,所述混合器-分布器包括至少两个穿孔板。混合-分布区13的长度L通常取作区16和7的再生床中间的距离,即从区7中的再生床的下游端到区16中的再生床的上游端的距离,其中下游相对于燃料和氧化剂的流动。虽然按照设置在此种混合-分布区内的穿孔板描述了本发明,但是本发明不限于此,并且该描述不希望阻止在本发明更宽范围内的其它实施方案,例如其中混合-分布区具有不同形状,其中混合-分布区具有不规则的横截面面积,其中至少一些孔不位于混合-分布区内的板上等的实施方案。本发明不限于具有一个混合器-分布器的实施方案。例如,在一个实施方案中,第一反应器7是呈延伸的矩形体形式的蜂窝器,该矩形体具有基本上相等矩形横截面的上游和下游面。蜂窝器包括面对面连接的四个部分S1-S4,所述部分各自是呈延伸的矩形体形式的蜂窝器,该矩形体具有基本上相等矩形横截面的上游和下游面。在这个实施方案中,每个部分可以包括燃料通道和氧化剂通道。多个蜂窝器部分(如S1-S4中的部分)的使用促进对于大直径反应器系统的应用。在一些实施方案中,每个部分在区域13中使用一个混合器以促进主要流过该部分中的通道的第一和第二反应物的混合。在那些实施方案中,可以存在与所存在的所述部分大致相同数目的混合器。在大直径反应器中,所述部分的数目可以非常大,以数打或甚至数百来计算。例如,在一个实施方案中,反应器系统包括(i)包括100个部分的第一反应器和(ii)每个所述部分有一个混合器。对于本说明书和所附权利要求书来说,术语“穿孔板”是指具有对气体的流动开放的孔的固体,所述固体具有厚度(“T”)、横截面面积(“A”)、有效板直径(“Dp”,其中Dp=2(A/π)1/2),且T/Dp之比≤1.0,例如≤0.5,例如≤0.2。板厚度T是与穿孔紧邻的平均板厚度(或当与一个孔紧邻的厚度不同于与另一个孔紧邻的厚度时,是这些值的算术平均值)。例如,可以与板附接以便将该板定位在混合-分布区中的支撑装置(例如,将板与混合-分布区的边界连接的环和/或翼片)从板厚度中排除。板的特征中的一个或多个(例如穿孔的位置)可以适宜地参照中心轴描述。板的中心轴定义为基本上与所述板的将板的几何中心(“重心”)截取的平面垂直的线,其中术语重心是指该物体的所有点的平均位置(一阶矩)。例如,具有均匀密度的圆板的重心是在圆周中心处的点。两个或更多个板可以按大致共轴的方式定位,其中术语“共轴”是指所述板的中心轴(i)紧密接近和(ii)基本上平行。在这上下文中,术语“紧密接近”是指板的中心轴由≤板的有效直径(或当板具有不相等尺寸时,更小的板的有效直径)的10%的距离隔离,例如≤5%。术语“基本上平行”是指与板的任何平面的截取角度差≤10°,例如≤5°。多个板的中心轴(称作公共中心轴)是板的中心轴的最佳拟合(例如,数值平均)。在一个实施方案中,混合器-分布器包括两个穿孔板。例如,混合器可以包括:(a)具有(i)横截面面积Ap1、(ii)厚度Tp1和(iii)具有总横截面面积Ah1的多个孔的第一板,和(b)第二板,所述第二板具有(i)横截面面积Ap2,(ii)厚度Tp2和(iii)具有横截面面积Ah2的一个基本上中心的孔。板2可以与同流动方向基本上正交并将混合-分布区13平分的平面(平面2)紧邻设置,板1可以与(i)同平面2基本上平行并且(ii)设置在平面2的相对于燃料和氧化剂(当它们穿过混合-分布区时)的平均流动的上游的平面(平面1)紧邻设置。平面1和2可以间隔以提供0.1-10.0,例如0.2-2.0,例如0.5-1.5的L:D比(对于这一实施方案的混合器-分布器),L是(对于这一实施方案)在区7中的再生床的下游端到区1中的再生床的上游端之间沿着中心轴测量的。任选地,板是基本上共轴的,比例Ap1:Ah1≥2.0且比例Ap2:Ah2≥1.5。Ah2任选地在Ah1的75.0%至Ah1的125.0%的范围内,例如在Ah1的85.0%至Ah1的115.0%,例如Ah1的90.0%至Ah1的110.0%的范围内。虽然不希望受任何理论或模型的束缚,据信使Ah1和Ah2具有基本上相似的尺寸导致横穿混合器-分布器的更低的压降并减少孔当中反应物(燃料和氧化剂)流速的改变。位于板1上的孔(例如,穿孔)的总数任选地在位于板2上的孔的数目的2倍至8倍,例如3倍至6倍的范围内。对于具有有效直径Dp的板,该板的厚度可以由关系T/Dp≤0.5,例如≤0.2决定。任选地,板2具有在Tp1的75.0%至Tp1的125.0%,例如Tp1的90.0%至Tp1的110.0%,例如Tp1的95.0%至Tp1的105.0%的范围内的厚度Tp2。任选地,板1的下游面与板2的上游面间隔距离Sp1-p2,其中Sp1-p2沿着混合器-分布器的中心轴测量并且在板1的Dp的5%-50%,例如5%-20%的范围内。当板1和2具有基本上相等的周长,Sp1-p2可以在0.25Sb-5.0Sb的范围内,其中Sb等于Ah1除以板1的周长。混合器-分布器一般与混合-分布区共轴设置。当混合器-分布器的有效长度小于混合-分布区的有效长度,混合器-分布器任选地在该区中沿着中心轴为中心。任选地,Ap2在Ap1的75.0%至Ap1的125%,例如Ap1的85.0%至Ap1的115%,例如Ap1的90.0%至Ap1的110.0%的范围内。在一个实施方案中,板1和2具有基本上相同的表面积和厚度,例如,它们是具有基本上相等的直径和厚度的圆形或多边形板。在图3A-3C和图4中所示的实施方案中,混合器-分布器包括多个穿孔板,例如至少两个穿孔板。例如,混合器-分布器可以包括:(a)至少一个第一板,所述第一板具有横截面面积Ap1并具有总横截面面积Ah1的多个孔,其中Ap1:Ah1≥2.0;和(b)第二板,第二板具有(i)比第一板更少的孔,(ii)在大约75.0%·Ap1至125.0%·Ap1的范围内的横截面面积Ap2,和(iii)具有横截面面积Ah2的一个基本上中心的孔,其中Ah2在大约90%·Ap1至110.0%·Ap1的范围内。任选地,混合器-分布器还包括第三、第四和/或第五穿孔板。如图3A所示,板3与板2的与板1相对的那面邻接,板4与板3的与板2相对的那面邻接设置,板5与板1的与板2相对的那面邻接。任选地,构成混合器-分布器的板具有以下特征中的一个或多个:(i)所述板的至少一个具有多边形、椭圆形、圆形横截面;(ii)所述板中的至少两个具有基本上相等的横截面面积;(iii)穿过所述板中的每一个的孔(该孔包括穿孔)具有多边形、椭圆形或圆形横截面或它们的组合;(iv)所述板中的至少两个具有基本上相同的厚度;(v)至少一个板的厚度不与其它板的那些相同;(vi)至少一个板具有基本上均匀的厚度;(vii)至少一个板具有基本上不均匀的厚度,例如当所述板中的一个或多个包括压花穿孔,例如一个或多个孔的厚度不与板的厚度相同时;(viii)混合器-分布器包括至少三个具有基本上相等的间隔的板;(ix)混合器-分布器包括至少三个具有不相等间隔的板,例如当板1和2的间距(表示为图3A中的Sp1-p2)不与板2和3的间距(表示为Sp2-p3)相同时;或(x)第二反应器1中的混合器的最下游板和再生材料的上游端之间的表示为Sz1的间距与第一反应器7中的第一上游板和再生材料的下游端之间的表示为Sz7的间距近似相等。混合器-分布器可以进一步包括额外的混合分布元件,例如板、旋涡装置、流动集中器、流动扩张器等,如美国专利号7,815,873所述。任选地,混合器-分布器包括降低(例如阻止)燃料和/或氧化剂在避开板的孔的路径中的流动的装置。例如,混合器-分布器可以与混合-分布区13的内壁紧邻设置,以引导燃料和氧化剂朝向和穿过混合器-分布器流动,并且这基本上阻止这些气体通过其它流路在区7和1之间的流动。现将更详细地描述混合器-分布器的一个实施方案,该混合器-分布器包括如图3A所示安排的穿孔圆形板。虽然按照这一实施方案描述了混合器-分布器,但是本发明不限于此,并且本说明书不希望排除其它实施方案,例如具有更少板,非圆形横截面面积的板,不相等厚度,非圆形孔,重叠孔,压花孔等的那些。在一个实施方案中,第一板(“板1”)是具有横截面面积Ap1和多个具有总横截面面积Ah1的基本上圆形的孔的基本上圆形的板,其中Ap1:Ah1≥2.0。任选地,所述板具有以下性能中的一种或多种:所述板具有500mm2-5.0×106mm2,例如2000mm2-5.0×104mm2,例如3000mm2-3.0×104mm2的横截面面积;所述板具有T/Dp≤0.3,例如在0.05-0.15的范围内;所述板具有基本上均匀的厚度;每个孔具有横截面面积≥0.01·Ap1,例如,0.01·Ap1-0.2·Ap1;所述板不含有这样的孔,该孔具有在该板的平面上与板的中心轴相距小于0.1Dp的中心轴;该板的直径在25mm-2,500mm,例如50mm-250mm,例如65.0mm-200.0mm的范围内。在一个实施方案中,第一板包括多个不相重叠的、基本上圆形的孔,其中没有孔设置在板的中心轴的0.1Dp内。任选地,穿过板1的孔的数目等于穿过板2的孔的数目的“n”倍,其中n在2-20,例如3-6的范围内。在一个实施方案中,孔的数目等于6。任选地,每个孔具有基本上相等的面积,如图3B的右手面所示,并具有基本上相等的厚度。任选地,所述孔按圆形图案等距,该圆形图案具有半径R1p1,如图3C所示。R1p1一般经选择使得没有孔与板的周边重叠,并且可以例如,在0.05·Dp1-0.4·Dp1的范围内。间隔角α1可以由等距孔的数目和直径测定。例如,当板1包括在3-9个范围内的多个等距不相重叠的孔时,α1可以在大约40.0°-大约120.0°的范围内。第二板(“板2”)是与第一板相邻设置的基本上圆形的板,如图3A所示。在一个实施方案中,第二板具有(i)在75.0%·Ap1至125.0%·Ap1,例如90.0%·Ap1至110%·Ap1的范围内的横截面面积Ap2,和(ii)具有横截面面积Ah2的一个基本上中心的圆形孔,其中Ap2:Ah2≥1.5。换言之,板2的中心孔可以具有与板的中心轴隔离(在该板的平面中)≤0.1Dp,例如≤0.05Dp,例如≤0.01Dp的中心轴。任选地,Ah2在75.0%·Ah1至125%·Ah1,例如85.0%·Ah1至115%·Ah1,例如90.0%·Ah2至110.0%·Ah1的范围中。任选地,板2的厚度和横截面面积与对板1规定的那些范围相同。任选地,板2具有与板1基本上相同的厚度、厚度均匀性和横截面面积。任选地,板2含有一个或多个额外的孔。额外的孔可以具有,例如,总横截面面积≤0.6·Ah2。一般而言,板1具有比板2更大数目的孔,板2在混合器-分布器的板(例如,如图3A所示的任选的板3、4和5的那些)当中具有更少数目的孔。在一个实施方案中,第三板(“板3”)是与板2相邻设置的基本上圆形的板,如图3A所示。板3具有横截面面积Ap3和具有总横截面面积Ah3的多个孔,其中Ap3:Ah3≥2.0。任选地,板3的性能,例如厚度、厚度均匀性、横截面面积、孔数目/尺寸/几何结构等与对板1规定的那些范围相同。任选地,Ap3在75.0%·Ap1至125.0%·Ap1,例如90.0%·Ap1至110.0%·Ap1的范围内,例如在0.10·Ap1至[Ap1+(0.02·Ap1)]的范围内。在一个实施方案中,板3包括多个不相重叠的孔,其中没有孔与在板的中心轴的0.1Dp内的区域重叠。任选地,穿过板3的孔的数目等于穿过板2的孔的数目的“m”倍,其中m在2-20,例如3-6的范围内。在一个实施方案中,板3具有六个基本上圆形的孔。任选地,每个孔具有基本上相等的横截面面积,如图3B的右手面所示,并具有基本上相等的厚度。任选地,所述孔按圆形图案等距,该圆形图案具有半径R1p3,如图3C所示。R1p3一般经选择使得没有孔与板的周边重叠,并且可以例如,在0.5·Dp3-0.4·Dp3的范围内。间隔角α3可以由等距孔的数目和直径决定。例如,当板3包括六个等距的不相重叠的孔时,α3大致是60.0°。在一个实施方案中,板3与板1基本上相同(例如,n=m)。当板1和3各自包括多个等距孔时,板1和3的孔的图案可以在相对旋转位置内对齐。在这样的实施方案中,每个板可以具有不同的旋转取向,其中旋转围绕着板的中心轴。一个板相对另一个板的相对旋转位置适宜地参照包括公共中心轴的平面描述,并由公共中心轴作为边界(仅存在于该轴的一面上)。这一参考面与每个板的交点提供公共的参考轴(“CRA”),显示为图3B中的水平线,由该参考轴可以测量旋转角。板上孔的相对旋转位置定义为参考轴和将该板的重心与同该参考轴最接近的孔的重心连接的辐射线之间的角度(“δ")。如果板具有处于基本上不同半径的孔,则具有基本上相似半径的每组孔可以具有它们自己的δ。当角度要求增加或扣除时,遵循如下惯例:与参考轴的正角在参考轴的沿着公共中心轴观察时的逆时针面上,其中从板1的与板2相反的那面(即,如图3A中所示从板5“上面”)观察。在其中板1和3各自具有3至9(例如,6)个基本上等直径的圆形孔和其中R1p1=R1p3=R1的一个实施方案中,板1和3的相对旋转位置(δ1)相对于如图3B所示的公共参考轴(水平绘制)在-30.0°至30.0°的范围内。在一个实施方案中,混合器-分布器可以进一步包括任选的板4。如图3A所示,板4是与板3相邻设置的圆形板,使得板3在板4和2之间。在一个实施方案中,板4具有(i)横截面面积Ap4,其中Ap4在75%·Ap1至125.0%·Ap1,例如90.0%·Ap1至110.0%·Ap1的范围内,(ii)具有总横截面面积Ah4的多个孔,其中Ap4:Ah4≥2.0,和(iii)多于板3的孔数目。任选地,板4的厚度和横截面面积与对板3规定的那些范围相同。任选地,板4具有与板2基本上相同的厚度、厚度均匀性和横截面面积。任选地,板4的孔各自具有0.01·Ap4至0.2·Ap4的横截面面积。任选地,所述板具有这样的孔,该孔具有与板的中心轴重叠的横截面面积。任选地,所述板具有这样的孔,该孔具有基本上设置在该板的对称轴上的中心。在一个实施方案中,板4具有基本上均匀的厚度T4并包括多个不相重叠的圆形孔,其中一个孔与板的中心轴基本上同轴设置。任选地,穿过板4的孔的数目等于穿过板3的孔的数目的“p”倍,其中p在≥2或≥3.0的范围内。在一个实施方案中,板4具有19个基本上均匀厚度(基本上等于板的厚度)和基本上相等的横截面面积的圆形孔,如图3B的左手边所示。当一个孔以板的对称轴为中心时,其余孔可以例如,按第一和第二圆形图案等距,第一圆形图案具有半径R1p4,且第二圆形图案具有半径R2p4,如图3C所示。R1p4一般经选择使得没有孔与板的中心孔重叠且R2p4经选择使得没有孔与板4的周边重叠。R1p4和R2p4各自可以例如在0.05·Dp4至0.4·Dp4的范围内。间隔角β4和γ4可以由如图3C所示的等距孔的数目和直径决定。当4至8(例如6)个等距的不相重叠的孔按R1p4等距时,β4可以例如在大约45.0°至大约90.0°的范围内。当8至16(例如,12)个等距不相重叠的孔按R2p4等距时,γ4可以例如在大约22.5°至大约45.0°的范围内。在一个实施方案中,混合器-分布器可以进一步包括任选的板5。如图3A所示,板5可以是与板1相邻设置的圆形板,使得板1在板5和2之间。板5可以具有(i)横截面面积Ap5,其中Ap5在0.10·Ap1至[Ap1+(0.02·Ap1)]的范围内,(ii)具有总横截面面积Ah5的多个圆形孔,其中Ap5:Ah5≥2.0,和(iii)比板1多的孔数目。任选地,板5的性能,例如厚度、厚度均匀性、横截面面积、孔数目/尺寸/几何结构等与对板4规定的那些范围相同。在一个实施方案中,板5具有基本上均匀的厚度T5并包括多个不相重叠的孔,其中一个孔与板的中心轴基本上同轴设置。任选地,穿过板5的孔的数目等于穿过板1的孔的数目的“q”倍,其中q在≥2.0或≥3.0,例如3-6的范围内。在一个实施方案中,板5具有19个基本上均匀厚度(基本上等于板的厚度)和基本上相等的横截面面积的圆形孔,如图3B的左手边所示。当一个孔以板的对称轴为中心时,其余孔可以例如,按第一和第二圆形图案等距,第一圆形图案具有半径R1p5,且第二圆形图案具有半径R2p5,如图3C所示。R1p5一般经选择使得没有孔与板的中心孔重叠且R2p5经选择使得没有孔与板5的周边重叠。R1p5和R2p5可以各自例如在0.05·Dp5至0.4·Dp5的范围内。间隔角β5和γ5可以由如图3C所示的等距孔的数目和直径决定。当4至8(例如6)个等距的不相重叠的孔按R1p5等距时,β5可以例如在大约45.0°至大约90.0°的范围内。当8至16(例如,12)个等距不相重叠的孔按R2p5等距时,γ5可以例如在大约22.5°至大约45.0°的范围内。在其中板4和5各自具有两个孔环的一个实施方案中,内环具有6个且外环具有12个大致均匀间隔的孔,板4和5上的6孔内环的相对旋转位置(δ2)在相对于如图3B所示的公共参考轴(CRA)(水平绘制)的-30.0°至+30.0°的范围内,且板4和5上的12孔外环的相对旋转位置(δ3)在相对于如图3B所示的公共参考轴(CRA)(水平绘制)的-15.0°至+15.0°的范围内。板4和5上的两个孔环可以具有0.0°至15.0°的相对于彼此的相对旋转位置(|δ2-δ3|)。在一个实施方案中,板4和5上的两个孔环具有12.0°至15.0°的相对于彼此的相对旋转位置(|δ2-δ3|)。板4和5可以具有例如0.0°至30.0°的相对于板1和3的相对旋转位置(|δ1–δ2|)。在一个实施方案中,板4和5相对于板1和3的旋转位置(|δ1–δ2|)在0.0°至5.0°的范围内。在一个实施方案中,板4和5相对于板1和3的旋转位置(|δ1–δ2|)在25.0°至30.0°的范围内。在一个实施方案中,板3相对于板4和板5相对于板1的旋转位置如上面概括的那样固定,但是板3-4对和板1-5对的相对旋转位置不固定在任何特定值。在一个实施方案中,混合器-分布器还包括任选的旋涡装置。此种旋涡装置当使用时可以提供,例如,0.1-3.0,例如0.1-1.3的旋流数(aswirlnumber),旋流数可以使用J.M.Beer的燃烧空气动力学(CombustionAerodynamics),第5章,KriegerPublishing,1983中描述的方法测定。虽然本发明的混合器-分布器对同流换热器区7的床和区13的混合器-分布器之间的失准较不敏感,但是已经观察到,当将旋涡装置设置在板1和板2(板1在板2的相对于第四混合物的平均流动方向的上游)之间时,可以进一步降低这种敏感性。当使用旋涡装置时,燃料和氧化剂混合通过这些气体的径向流入由如图5所示的旋涡叶片B界定的腔室而得到辅助。该旋涡叶片将燃料和氧化剂(和任何反应产物)径向地向内引导,同时赋予圆周速度。旋涡气体穿过板2的孔,从而增加混合的量。虽然图5中显示为6个径向倾斜翅片,但是可以使用不同数目的旋涡叶片(B),并且这些叶片可以按有效用于产生旋涡的其它形状配置,条件是由旋涡产生设备(在这个实施方案中,旋涡叶片)产生的旋涡产生大约0.1-大约3.0,例如大约0.1-大约1.3的旋流数,所述旋流数指定在板2的孔的进口处。可以使用备选的旋涡产生通道形状,例如常规旋涡产生通道形状,但是本发明不限于此。例如,可以在叶片之间使用螺旋形通道或空间。可用于混合器-分布器的旋涡装置的实例示意性地显示在图5中。成形为达到所指出的旋流数的旋涡块是与板2的上游表面等距紧邻的。旋涡块可以具有,例如,高度h1,其中h1≤Sp1-p2,其中Sp1-p2是板1和2的间距,如图3A所示。相对的旋涡块之间的最小距离是Di,其中Di≥跨越板2的中心孔的最小距离的1.0倍。挡板(例如,板6)可以设置在旋涡装置的上游和板1的下游,如图5所示。在一个实施方案中,旋涡块沿着Di和外直径Do之间等距的曲线等距,其中板6是具有外直径Do和厚度h2的圆形板。任选地,板2、旋涡块和板6以面对面接触方式连接,彼此按序排列,如图5所示。在一个实施方案中,混合器-分布器配置用来使其开放体积最小化,同时维持足够的混合以混合(i)≥50.0wt%的第一反应物,例如≥75.0wt%,例如≥90.0wt%与(ii)≥50.0wt%,例如≥75.0wt%,例如≥90.0wt%的第二反应物,wt%基于输送到区13的第一或第二反应物(视情况而定)的重量。术语“开放体积”是指混合器-分布器(包括任选的板3、4和5和任选的旋涡装置,当使用它们时)的总体积,比混合器-分布器的材料结构的体积小。例如,混合器-分布器可以具有长度L和有效直径D,其中(i)有效直径D=2(A/π)1/2,和(ii)A是混合器-分布器的横截面面积。在这个实施方案中,L和D经选择以达到燃料和氧化剂在区13内的足够混合和分布,同时使开放体积最小化。任选地,L/D在0.1-8.0,例如0.2-2.0,例如0.3-1.0的范围内。任选地,混合器-分布器具有是同流换热器区7、反应区1和混合-分布区13的总体积的≤20.0%,例如≤15.0%,例如≤10.0%的总体积。对于现有技术混合器-分布器,例如美国专利号7,815,873的那些,混合器-分布器的总体积基于权衡以下情况选择:(i)在混合-分布区中有效地混合燃料和氧化剂;(ii)横穿在由混合器-分布器表示的(圆形或多边形)机筒的端部表示的横截面将总燃料和氧化剂的流动均匀地分布;和(iii)横穿混合区提供较低压降。本发明的混合器-分布器是改进,至少部分地是因为构成本发明混合器-分布器的穿孔板提供增强的燃料-氧化剂混合和这些气体的流动分布,而不会显著地增加压降--尤其是在较小混合器-分布器L/D,例如0.2-2.0,例如0.3-1.0的范围中。为了达到相同的混合、分布和压降程度,现有技术混合器-分布器将要求比本发明的具有相同有效直径D的混合器-分布器的长度L长≥10.0%,例如≥25.0%的混合器-分布器长度L。术语“混合有效性”(ME)是在区13内且与区13紧邻的第四混合物的氧化剂组分经由氧化消耗的所述第四混合物的燃料组分的量(wt%),该wt%基于第四混合物的燃料组分的重量。任选地,ME≥75.0wt%,例如≥95.0wt%,例如≥99.0wt%。任选地,混合器-分布器具有≤0.3巴(绝对压力),例如≤0.1巴,例如≤0.05巴的在燃料和氧化剂混合期间的压降。任选地,混合器-分布器具有的在氧化和热解阶段期间的压降是在这些阶段期间反应器(区1、13和7)中的总压降的≤50%,例如≤20%,例如≤10%。对于本发明混合器-分布器,混合-分布区的体积主要由穿孔板(上面规定)的厚度和板间间距决定。当混合器包括具有大致相同横截面、横截面面积、厚度、周长(P)和总孔表面积(Ah)的板时,板间间距一般在0.25SB-5.0SB的范围内,其中SB等于Ah除以P。任选地,板间间距在0.05·Dp至0.50·Dp,例如0.05·Dp至0.20·Dp的范围内。任选地,板与床间距(Sz1,Sz7)在板间间距的100%至300%,例如100%至200%之间。任选地,L=T+I,其中T是板厚度之和(每个板厚度如上面所规定)且I是总间距,其是板间间距和板与床间距之和。任选地,总间距在混合-分布区,例如三板混合器中的板间间距和板与床间距当中等分,板1和2的间距和板2和3的间距和Sz1和Sz7各自等于0.25×I。任选地,混合器-分布器的板大致以区13为中心,例如混合器-分布器上游板和第一反应器7中的再生材料的下游端之间的距离Sz7与混合器-分布器的下游板和第二反应器1中的再生材料的上游端之间的距离Sz1基本上相同。除对燃料-氧化剂混合有效之外,混合器-分布器还有效用于沿与区13中的燃料和氧化剂的平均流动方向垂直的方向将气体流动基本上均匀分布。术语“基本上均匀分布”是指轴向气体速度在将混合器-分布器(区13)与区1或区7分离的横截面面积内的均匀性。轴向是垂直于将混合区13与区1或区7分离的平面的方向。通常,轴向平行于公共中心轴,并且在笛卡儿坐标中,在本文称作“z”方向。分离性平面内的横截面面积的每个元素可以对于相关轴向速度进行评价,通过计算流体动力学或通过试验测量进行。基本上均匀分布是指流动分布不均值(flowMaldistributionvalue)“MD”≤15.0%,例如≤10.0%,例如≤5.0%,其中MD等于(i)轴向速度的标准偏差(σvz)除以(ii)由与混合-分布区的下游端紧邻的混合器-分布器的横截面界定的平面中的平均轴向速度(|<vz>|),表示为%。σvz等于vz的偏差的平方根,所述偏差和|<vz>|通过测量至少100个近似等间距的点的轴向速度而测定;所述点位于混合器-分布器的横截面内的平面上,该横截面与混合-分布区的下游端紧邻。任选地,所述混合器-分布器还提供与所述混合-分布区的下游端近似的均匀温度分布,由温度差异度(“TV”)表征,其中TV≤60.0℃,例如在1.0℃-60.0℃,例如10.0℃-50.0℃的范围内。TV等于在混合器-分布器的横截面面积内测量的气体温度的标准偏差,该横截面面积在与混合-分布区的下游端紧邻的平面中。气体温度的标准偏差等于气体温度偏差的平方根,所述偏差通过测量近似等间距的至少100个点(位置)的温度而测定;所述点位于混合器-分布器的横截面内的平面上,该横截面与混合-分布区的下游端紧邻。术语“偏差”如ExperimentsinModernPhysics,第10章:“TheElementsoftheTheoryofStatistics”,p.446;AcademicPress1966中所限定。应该理解,混合器-分布器可以绕着板2的横截面基本上对称,例如功能上基本相似于第一和第二混合物的逆流操作。虽然混合器-分布器的混合功能在逆流中不发挥工艺作用,但是混合器-分布器按逆流方向的构型受益于第一和第二混合物的基本上无阻的流动(例如,横穿区13的低压降),同时在第一和第二混合物朝向同流换热器区7离开混合器-分布器区13时提供较均匀分布的第一和第二混合物。参数例如(i)MD、(ii)TV、(iii)混合器区中的第四混合物的氧化剂组分经由氧化消耗的第四混合物的燃料组分的量、和(iv)在操作期间的混合器-分布器压降至少部分地取决于燃料和氧化剂的质量流量。虽然单个混合器-分布器(如图3A-C和4所述)可以用作逆流反应器内的唯一混合元件,但是可能希望使用多个这样的并联操作的混合器-分布器以减少由混合器-分布器中的每一个处理的反应器-系统体积的比例,尤其是在非常大的反应器系统中。这样的多个混合器-分布器描述在例如美国专利号7,815,873中。当使用延伸的多个平行区段组(相对于第四混合物的平均流动方向)时,这些区段中的每一个可以包括例如,个体混合器-分布器例如上面描述的和图3A-C、4和5中所示的那些。例如,个体混合器-分布器部分可以成形有六边外部横截面形状以便容易以大阵列填充。混合器-分布器一般由能够承受预期在反应区中经历的高温的材料构造或制造。在一个实施方案中,混合器-分布器装置由能够承受温度≥1.20×103℃,例如≥1.60×103℃,例如≥2.0×103℃的材料构造。例如,板1-3,任选的板4和5,任选的旋涡装置和任选的挡板6中的一个或多个由陶瓷材料例如二氧化硅、氧化铝、氧化锆、碳化硅、氮化硅、氧化钇等中的一种或多种构造。反应器系统中的应用在一个实施方案中,混合器-分布器用于逆流再生床反应器系统。此种反应器系统可以用于操作(例如,连续地或半连续地)两步非对称循环反应,例如包括氧化(再生)步骤和吸热反应步骤的循环。适合的反应器系统包括,美国专利申请公开号2007/0191664、美国专利号7,491,250;美国专利申请序列号61/349,464和美国专利申请公开号2007/0144940和2008/0142409中描述的那些,它们都全文通过参考引入本文。代表性逆流再生床反应器系统的实例描绘在图1中。术语“反应器”是指用于化学转化的设备和它们的组合,包括例如美国专利号7,943,808中公开的反应器组合和系统,该文献全文引入本文作为参考。反应器包括三个区,第一(“同流换热器”)区7、混合-分布区13和第二(“反应”)区16。区16和7各自包括至少一个再生床,其中术语“再生床”是指包含有效储存和传递热的材料的反应器床。在一个实施方案中,再生床包括基床或填充材料,例如玻璃或陶瓷珠或球体,金属珠或球体,陶瓷(包括,氧化铝、二氧化硅、氧化钇、氧化锆等和它们的混合物)或金属蜂窝器材料,陶瓷管,挤出整料(monolith),催化剂等。第一和第二反应器床可以具有相同形状和尺寸,但是这是不要求的。在这个实施方案中,区13包括图3A-C和4的混合器-分布器,包括任选的组件例如板3、4和5;旋涡装置;挡板6等。在一个实施方案中,第一或第二反应器床中的至少一个包括蜂窝器整料。蜂窝器整料包括,例如挤出的多孔结构例如用于汽车催化转化器等的那些。术语“蜂窝器”是指具有在其中设置的多个流路或通道的固体,蜂窝器通道具有通道长度(T),通道横截面面积(A),有效通道直径(Dpsg,Dpsg=2(A/π)1/2),且T/Dpsg之比≥1.0,例如≥10.0。混合器-分布器的孔的相似的T/Dpsg<1.0,这种特征可用于将混合器-分布器的板与区16和7的蜂窝器区分。虽然蜂窝器可以具有圆形横截面,但是这是不要求的,并且该术语不限于任何特定的整体结构、形状或拓扑结构。在其中使用蜂窝器整料的实施方案中,该蜂窝器整料据认为能够实现低压力损失转移同时提供接触时间和传热。为了吸热,例如热解步骤将该反应器系统加热,其中该吸热步骤使用的热的至少一部分由氧化步骤提供。在图1的实施方案中,加热可以在放热反应区域2063中进行,该区域可以例如设置在与第一反应器7的下游端11紧邻的第一点和与第二反应器16的下游端18紧邻的第二点之间;“下游”在这种情况下是相对于燃料和氧化剂的平均流动。至少一个混合器-分布器位于区13中,例如图5的混合器-分布器。一般将第一反应物(包含例如燃料)和第二反应物(包含例如氧化剂例如空气)引导至与板5的上游面紧邻的位置(“上游”相对于反应器中第一和第二反应物的平均流动方向)。第一和第二反应物分布和混合,例如当它们穿过板5的孔时,然后将总反应物连同任何氧化产物一起传导穿过板1-4的孔,以便第二反应物的组分的进一步混合、分布和反应。氧化步骤一般导致反应器系统温度分布图中的高温区,高温区的至少一部分位于区域2063中。温度分布图示意性地显示为图1中的类似于高斯(Gaussian)的形状。氧化步骤因此包括以下特征:(i)通过将燃烧热的至少一部分传递到第一反应器7的端部11下游的反应器系统将区13和第二反应器16加热和(ii)将通过第一反应器上游区域(上游相对于第一和第二反应物的流动)中的第一和第二反应物回收的显热的至少一部分朝第一反应器的下游区、区域13或第二反应器中的一个或多个传递以使反应器系统热再生。因此,温度分布图的右手和左手边缘中的每一个的至少一段从它们的起始位置在氧化步骤开始时向下游平移,如图1中箭头21和8所示。在加热反应器系统后,气体横穿反应器系统的流动方向对于热解步骤进行反向。热解步骤在热解步骤开始的时候,反应区16处于高温且同流换热器区7处于比反应区16更低的温度。经由导管2046将第一混合物(反应物原料,例如热解原料)引导进入反应区16的第一端18。在图1的实施方案中,热解区2064可以例如设置在与第二反应器16的上游端18紧邻的第一点和与第一反应器7的下游端9紧邻的第二点之间;“上游”和“下游”相对于第一混合物的平均流动。不言而喻的是,本发明可以在没有精确界定(a)区域2063和2064的边界的情况下实践。虽然区域2063(放热反应区域)与热解区2064至少部分地共同延伸,但是区域2063的上游端(“上游”相对于第四混合物的平均流动)一般与其中足够的燃料和氧化剂结合以产生放热反应的位置紧邻。区域2063的下游(相对于第一混合物的平均流动)端一般与第二反应器16的下游端紧邻,如图1所示,但是这是不要求的,并且在至少一个实施方案中,区域2063的下游端设置在远下游,例如在导管2066中。在由图1表示的实施方案的至少一个中,热解区2064的上游端与第二反应器16的上游端18紧邻。热解区2064的下游端可以例如,与第一反应器7的下游端9紧邻。任选地,在热解期间从反应器系统提取的主要量(例如,>50%)的热产生在区域2064的与区域2063共同延伸的部分中。热解可以例如在高强度热解条件下进行。就包含烃的原料例如第一混合物的热解而言,术语“高强度”是指热解操作条件导致原料烃的≥10.0wt%转化成乙炔,基于原料中烃的总重量。热解可以在热力热解条件,例如高强度热力热解条件下进行,其中术语“热力热解”是指热解使用的热的<50.0%如下提供:(a)使热解原料放热反应,例如通过使氧化剂与第一混合物的烃和/或氢气发生放热反应和/或(b)使热解原料与气态和/或液态燃烧产物接触而将热解原料加热。术语“热力热解反应器”是指这样的热解反应器,其中热解使用的热的≥50.0%由来自反应器组件(例如与反应器连接的固体表面例如管状物或床材料)的传热提供;任选地,热解使用的热的≥80.0%或≥90.0%由此种传热提供。在一个实施方案中,将第一混合物引导至热解阶段206,其中将它暴露到在热力热解条件,例如高强度热力热解条件下的温度≥1.20×103℃中,以将第一混合物的至少一部分转化成第二混合物。将第二混合物的至少一部分,例如包含C2不饱和物、分子氢和饱和烃的气相部分传导离开反应器系统,例如,到任选的升级阶段。第二混合物的可燃不挥发性部分的一部分可以保留在阶段206中,例如作为沉积物。在一个实施方案中,热解在高强度热力热解条件下进行,例如通过将第一混合物暴露到大约1.40×103℃至大约2.30×103℃,例如大约1.45×103℃至大约1.80×103℃的温度中保持≤大约0.3秒,例如≤0.05秒的停留时间。任选地,停留时间≤0.05秒,例如≤0.02秒。任选地,第一混合物的≥25.0wt%(例如≥50.0wt%或≥75.0wt%)达到≥1.40×103℃,例如大约1.50×103℃至大约1.675×103℃的峰值裂解气体温度,基于第一混合物的重量。术语“峰值裂解气体温度”是指当本体热解料流气体穿过热解反应器(例如,裂化区或辐射区)时,由它们达到的最高温度。本领域技术人员将领会,与隔板紧邻的温度可以更高,并且可以在一些无限小边界层中,实际上接近固体温度。然而,这里涉及的热解温度应该认为是本体气体温度,其是能通过不与固体材料接触的设备(例如热电偶)测量的温度。在一个实施方案中,进行热解,使其持续足以使第一混合物的≥50.0wt%,例如≥75.0wt%,例如≥90.0wt%(基于该第一混合物的重量)暴露到热解条件下保持停留时间≤大约0.3秒,例如≤0.05秒的持续时间(t1)。在一个实施方案中,t1≤20.0秒,例如≤10.0秒,例如≤5.0秒。任选地,t1在0.1秒至10.0秒的范围内。在一个实施方案中,热解步骤包括以下条件中的一种或多种:第一混合物达到峰值裂解气体温度≥1.40×103℃,例如1.45×103℃至2.20×103℃,例如1.50×103℃至1.90×103℃,或1.60×103℃至1.70×103℃;总压力≥1.0巴(绝对压力),例如1.0巴至大约15巴,例如2.0巴至10.0巴;停留时间(在高强度条件期间)≤0.1秒,例如≤5.0×10-2秒,例如≤5.0×10-3秒和/或0.1秒至10.0秒的t1。继续参照图1,第一混合物从反应器系统提取热,而导致第二混合物由第一混合物通过热解的衍生。随着这一步骤进行,温度分布图中的移转发生,例如温度分布图的右手边的至少一段移转(为了说明目的,该段示意性地由虚线边界涵盖),该移转的方向由箭头17指示。这种移转的量可能受例如,反应器系统的传热特性影响。将第二混合物的至少一部分,例如气相中的部分从第二反应器的下游端20传导至第一反应器7的上游端11,并经由与下游端9紧邻的导管2065传导离开第一反应器,如所示。在热解开始的时候,第一反应器7具有比第二反应器16小的温度。随着第二混合物横穿第一反应器7,第二混合物被淬火(quenched)(例如,冷却)至接近第一反应器下游端9的温度。随着第二混合物在第一反应器7中淬火,温度分布图的左手边的至少一段向第一反应器7的下游端9移动,如箭头19指示,对于说明目的,该段示意性地由虚线边界涵盖。在由图1表示的实施方案的至少一个中,热解区2064的上游端与第二反应器16的上游端18紧邻。热解区2064的下游端与第一反应器7的下游端9紧邻。因为淬火加热了第一反应器7,所以氧化步骤任选地包括将第一反应器冷却,例如以使温度分布图的左手边的至少一段朝着离开第一反应器7的端部9移动,如图1中的箭头8示意性显示。现将更详细地描述可用于热解步骤的第一混合物,和可以衍生自第一混合物的第二混合物。第一混合物在一个实施方案中,第一混合物包含烃并且任选地还包含分子氢和/或稀释剂。烃的类型不是关键的;例如,烃甚至可以包括烃非挥发物,包括在热解反应器的入口处存在的温度、压力和组成条件下不在气相里的那些。在一个实施方案中,烃衍生自一种或多种源材料,例如天然气、石油等。包含烃的源材料的实例包括以下物质中的一种或多种:衍生自石油的烃;合成气(包含一氧化碳和氢气的混合物);甲烷;含甲烷的料流,例如煤层甲烷、生物气、伴生气体、天然气和它们的混合物或组分;合成原油;页岩油;或衍生自植物或动物质的烃料流。适合的烃源材料包括美国专利号7,943,808和7,544,852中描述的那些,所述文献全文引入本文供参考。第一混合物可以衍生自热解上游的源材料(一种或多种),但是这是不要求的。例如,在一个实施方案中,将衍生自第一源材料的烃和衍生自第二源材料的氢气分开地传导至热解反应器,将所述烃和氢气结合以产生与热解反应器紧邻(例如在热解反应器内)的第一混合物。任选地,烃具有(或衍生自一种或多种源材料,该源材料具有),例如6.0wt%-25.0wt%,8.0wt%-20.0wt%(例如,不是天然气),或20.0wt%-25.0wt%(例如,天然气)的氢含量。任选地,第一混合物还包含稀释剂,例如≥1.0wt%的稀释剂,基于第一混合物的重量。适合的稀释剂(其可以是稀释剂混合物)包括以下物质中的一种或多种:分子氢,含氧化合物,例如水,氮气(N2),硫化氢,C4+硫醇,胺,胺的混合物,非烃非挥发物(不论可燃与否),包括耐火无机物,例如耐火含氧化合物,惰性气体(包括惰性气体混合物)等。在一个实施方案中,第一混合物包含≤10.0wt%稀释剂。在一个实施方案中,第一混合物包含≤2.0份/百万重量份(ppmw)的得自所有来源的不燃性非挥发物(例如,灰;ASTMD-189)的总量,基于所述第一混合物的重量,例如≤1.0ppmw。任选地,第一混合物包含≤5wt%的得自所有源的可燃性非挥发物(例如,焦油、沥青烯,ASTMD-6560)在第一混合物中的总量,基于第一混合物中的第一烃的重量,例如≤1.0wt%,例如≤100.0ppmw或≤10.0ppmw,只要可燃性非挥发物的存在不导致≥2.0ppmw(例如,≥1.0ppmw),基于第二混合物的重量。在一个实施方案中,第一混合物具有以下性能中的一种或多种:(i)第一混合物中的分子氢的至少15.0wt%(基于第一混合物中的分子氢的总重量)是衍生自第二混合物或其一种或多种产物的分子氢。在另一个实施方案中,第一混合物包含≥50.0ppm硫,基于第一混合物的重量。在一个实施方案中,第一混合物具有以下组成:(a)第一混合物包含(i)≥10.0wt%烃,例如≥25.0wt%烃和(ii)≥1.0wt%分子氢,例如≥15.0wt%分子氢,重量百分率基于第一混合物的重量和/或(b)第一混合物包含(i)≥0.10摩尔%的烃,例如0.10摩尔%-90.0摩尔%和(ii)≥0.01摩尔%的分子氢,例如0.01摩尔%-90.0摩尔%,摩尔百分率基于第一混合物的摩尔数。第二混合物在一个实施方案中,第二混合物包含≥1.0wt%的不饱和物和≥1.0wt%的可燃性非挥发物,基于第二混合物的重量。任选地,第二混合物还包含以下物质中的一种或多种:氢气、甲烷、乙烷或稀释剂,任选地还包含苯、具有≥3个碳原子的烷属烃(异-、环-和/或正-)等。在一个实施方案中,第三混合物衍生自一个或多个升级/处理阶段中的第二混合物,例如,通过将第二混合物与氢气、甲烷和/或可燃性非挥发物中的一种或多种分离。在另一个实施方案中,第三混合物包含第二混合物,基本上由第二混合物组成,或由第二混合物组成,例如第二混合物的在再生性逆流热解反应器的下游端处于气相中的那部分。通过热解由第一混合物制备第二混合物是吸热反应,其从热解反应器系统收回热。当连续地或半连续地循环反应器系统时,通过在插入的氧化步骤期间产生的热替换由热解步骤使用的热的至少一部分,其中反应器系统的一个循环包括氧化步骤和热解步骤。现将更详细地根据图1和2描述氧化(再生)步骤。氧化步骤再生必须将热从(i)混合-分布区13和任选地(ii)同流换热器区7传递到反应区16,以使反应器系统热再生用于热解步骤。通过将第一和第二反应物,例如燃料和氧化剂混合和分布与区13紧邻产生第四混合物(再生气体,例如燃烧气体)。将第一反应物(包含燃料)经由导管305引导至同流换热器区7。将第二反应物(包含氧化剂)经由导管3051引导至同流换热器区7。任选地,第一分布装置(D1)可以用于将第一反应物传导进入燃料通道14和/或第二分布器装置(例如,充气间206B)可以用于将第二反应物传导进入氧化剂通道15,燃料通道和氧化剂通道设置在同流换热器区7内。因为燃料和氧化剂通道是基本上独立的流路(例如,彼此之间几乎没有或没有流体连通),所以第一和第二反应物的混合一般直到区13才发生,其中第一和第二反应物组合而产生第四混合物。经由充气间206A和导管2066将至少部分地衍生自第四混合物的燃料组分的至少一部分的氧化的第五混合物传导离开反应器系统。第一和第二反应物离开同流换热器区7,并在区13中组合而产生第四混合物。通过保持这些反应物在区13的上游基本上分离(上游相对于第一和第二反应物的平均流动),将(i)从同流换热器区朝再生器区输送的和(ii)在放热反应期间释放的热朝反应器系统的对热解有好处的区域引导。术语“基本上分离”是指通过与区13上游的第二反应物的氧化剂组分反应消耗第一反应物的燃料组分的≤50.0wt%,例如≤25.0wt%,基于输送到分布器(D1)的第一反应物的燃料组分的重量。这样,从第四混合物的燃料和氧化剂组分的反应释放的热的大部分直到气体已经从同流换热器区7离开进入混合-分布区13才会产生。任选地,同流换热器区7的通道14和15基本上平行于燃料和氧化剂的平均流动方向取向。例如,通过由挤出蜂窝器整料、填料、起皱材料的堆叠层等构成的再生床提供此类通道。当同流换热器区7包括填充床或泡沫整料(未显示)时,这些床材料应该配置用来保持第一和第二反应物基本上分离。径向分散和第一反应物-第二反应物混合的量可以如美国专利号7,815,873所述测量和/或计算。图2示意性地示出了反应器系统和其流动分布器的另一个视图。分布器D1(用来将燃料引导进入通道14)具有与通道14对齐的多个孔(显示为图1和2中的小箭头)。充气间206B提供氧化剂进入通道15的流动。D1的孔可以与孔道15的开口对齐,但是不密封到该开口。通过不将D1的孔“密封”到通道14,则通道14和15可以在逆流或反应循环期间使用,从而提高系统的总效率。这种“开放”的分布器(D1)还可以用于包括多个热解反应器系统的实施方案,例如,其中反应器/同流换热器床移动(例如,旋转)进入或离开气体料流的那些。图2A示意性地示出了反应器7的端视图,其中阴影区代表分布器D1(用来将燃料引导进入通道14)的近似位置。在氧化步骤期间,第一和第二反应物经过同流换热器区7,将得自先前热解步骤的储存在同流换热器区中的热的至少一部分提取。然后将加热的反应物引导进入区13,如图1和2所示。混合器-分布器装置通过将从同流换热器区7排出的第一和第二反应物结合产生第四混合物,然后分布该第四混合物,尤其是该第四混合物的燃料和氧化剂组分以在反应区16上游的反应器系统的横截面内达到更均匀氧化。该第四混合物的氧化剂组分与(i)第四混合物的燃料组分和(ii)位于该反应器系统中的可燃性非挥发物反应而产生第五混合物,该第五混合物可以进一步包含未反应的第四混合物,如果有的话。在这个实施方案中,氧化步骤的总持续时间t2大于或等于第二反应器从氧化提取足够的热以实现热解步骤所需要的时间。换言之,进行氧化步骤这样的持续时间,该持续时间大于或等于足以使温度分布图的峰朝足以加热热解区2064以使第一混合物在热解步骤期间暴露到温度≥1.20×103℃下的第二反应器移动的时间。t2的值取决于因素例如阶段206中使用的反应器的几何结构,反应器的传热特性和制造反应器的材料,和热解步骤需要的热的量。任选地,t2在0.1秒至10.0秒的范围内。在一个实施方案中,t2大于或等于将热解区2063加热至这样的温度所需要的时间,该温度足以使第一混合物的≥50.0wt%,例如≥75.0wt%,例如≥90.0wt%在热解步骤期间暴露至温度≥1.20×103℃下,重量百分率基于第一混合物的重量。在一个实施方案中,t2≤20.0秒,例如≤10.0秒,例如≤5.0秒。应该理解的是,流动控制装置(例如,阀门、旋转反应器床、止回阀、通气缝、限流器、定时系统等中的一种或多种)可以用于控制气体流流、动作、定时和使流动系统之间的物理床在第一、第二、第四和第五混合物之间交替,和一个或多个所述步骤之间当使用时的任选的吹扫气。适合的喷雾器、分布器等公开在美国专利号7,815,873中;该文献全文引入本文作为参考。虽然本发明与常规喷雾器、分布器、充气间等在阶段206中的使用不矛盾,但是本发明不限于此。现将更详细地描述第四和第五混合物。第四混合物第四混合物包含第一和第二反应物。第一反应物可以包含,例如≥10.0wt%燃料,基于第一反应物的重量,例如≥50.0wt%燃料。第二反应物可以包含,≥10.0wt%氧化剂,基于第二反应物的重量,例如≥20.0wt%氧化剂。所述燃料可以衍生自用于使第一混合物衍生的相同源材料。任选地,所述燃料具有与第一混合物基本上相同的组成。燃料和氧化剂可以与美国专利号7,943,808中公开的那些相同。任选地,燃料衍生自以下物质中的一种或多种,包含以下物质中的一种或多种,基本上由以下物质中的一种或多种组成,或由以下物质中的一种或多种组成:氢气,CO,甲烷,含甲烷的料流例如煤层甲烷,生物气,伴生气体,天然气和它们的混合物或组分等。使第一反应物的燃料组分和第二反应物的氧化剂组分放热反应提供热解所使用的热的至少一部分,例如热解所使用的热的≥50%,例如≥75%,或≥95%。必要时,补充热可以通过例如燃烧器或加热炉,例如在反应器外面但是与其热连通的加热炉提供给再生性逆流热解反应器。第一和第二反应物在再生性逆流热解反应器内混合而产生第四混合物,当该第四混合物横穿热解反应器的至少一部分时,燃料和氧化剂则例如通过氧化反应例如燃烧而反应。第一反应物包含燃料,例如分子氢,合成气(CO和H2的混合物),或烃,例如≥10.0wt%烃(包括其混合物),或≥50.0wt%烃,或≥90.0wt%烃,基于第一反应物的重量。第二反应物包含氧化剂,例如分子氧。第二反应物中的氧化剂的量和用来产生第四混合物的第一和第二反应物的相对量可以按照第二反应物中使可燃性非挥发物在反应器系统中氧化所需要的氧化剂的量(“X”)和使第一反应物的燃料组分基本上化学计量氧化所需要的量(“Y”)规定。在一个实施方案中,第四混合物中氧化剂的总量是Z(X+Y),其中Z在0.8-10.0,例如1.0-3.0的范围内且量X和Y基于摩尔。当Z>1.0时,可以使用过量的氧化剂,例如以便如美国专利号7,943,808中所公开那样缓和氧化步骤期间的反应温度,和/或以便在反应器系统内输送热。第四混合物一般在设置于第一反应器的孔道下游的混合-分布区中产生。虽然第四混合物定义为第一反应物和第二反应物的组合,组合的料流一般包括由位于第一反应器的通道中的可燃性非挥发物的氧化产生的物质。任选地,该组合料流还包含由第一和第二反应物在第一反应器的一个或多个孔道中,或其上游的位置中由于第一和第二反应物的多根并合(comingling)而反应产生的物质。一般而言,多根并合的量小,如美国专利号7,943,808中公开那样。第四混合物中的氧化剂的量超过使基本上全部的第四混合物的燃料组分氧化所需要的量可能是有好处的,例如,以便(i)使位于反应器系统的在第一反应器孔道下游的区域中的可燃性非挥发物氧化,(ii)使在第四混合物的燃料组分氧化期间的温度缓和和/或(iii)将热在反应器系统的在混合-分布区下游的区域内传递。过量氧的所需量可以如下提供:提高氧化剂在第二反应物中的相对量和/或提高第二反应物在第四混合物中的相对量。任选地,第四混合物还包含稀释剂,例如≥1.0wt%的稀释剂,基于第四混合物的重量。适合的稀释剂(可以是稀释剂混合物)包括以下物质中的一种或多种:例如,含氧化合物(水、二氧化碳等),不燃性物质例如分子氮(N2)和燃料杂质例如硫化氢。在一个实施方案中,第四混合物包含≤96.0wt%稀释剂,例如50.0wt%-95.0wt%稀释剂,基于第四混合物的重量。在一个实施方案中,将稀释剂作为第二反应物的组分提供给第四混合物。例如,第二反应物可以包含60.0摩尔%-95.0摩尔%稀释剂和5.0摩尔%-30.0摩尔%氧化剂,基于第二反应物的摩尔数,例如当第二反应物是空气时。任选地,第二反应物具有0.5-20.0,例如4.0-12.0的稀释剂与氧化剂的质量比。第二反应物(和第四混合物)进一步包含稀释剂可能是有好处的,例如以便(i)缓和第四混合物的燃料组分氧化期间的温度和/或在反应器系统内传热。在一个实施方案中,第一反应物包含≥90.0wt%分子氢,基于第一反应物的重量且第二反应物包含≥90.0wt%空气,基于第二反应物的重量。当第二反应器包含≥90.0wt%空气时,基于第二反应物的重量,则由它们制备的第四混合物可以包含,例如≥1.0wt%分子氧,例如5.0wt%-25.0wt%,例如7.0wt%-15.0wt%,≥0.1wt%燃料,例如0.2wt%-5.0wt%,重量百分率基于第四混合物的重量,第四混合物的其余部分是分子氮稀释剂,例如≥50.0wt%稀释剂,例如60.0wt%-94.50wt%稀释剂,基于第四混合物的重量。在一个实施方案中,在氧化步骤期间第四混合物的质量流量是第一混合物在热解步骤期间的流量的≥1.0倍,例如是第一混合物在热解步骤期间的流量的1.0-6.0倍。第五混合物第五混合物包含(i)衍生自第四混合物的燃料和氧化剂彼此之间和与反应器内的可燃性非挥发物的放热反应的产物,任选的(ii)稀释剂,当稀释剂存在于第四混合物中时,和/或(iii)未反应的燃料和氧化剂。当燃料和氧化剂的放热反应涉及烃燃烧时,或当稀释剂存在于第四混合物中(例如N2或H2S)时,第五混合物可以包含二氧化碳,并可以进一步包含硫氧化物、氮氧化物等。实施例实施例1为再生性逆流热解反应器装备本发明的混合器-分布器。反应器是圆柱对称的并具有下表中,参照图3A-3C和图4规定的尺寸。混合器-分布器具有五个具有基本上相同直径和厚度的圆形板,这些值也规定在表1中。板的孔是具有如图4所示的数目和排列的圆孔,并具有规定的直径和间距。表1尺寸值床直径mm95.3总反应器长度mm609同流换热器床(第一反应器)长度mm209热解床(第二反应器)长度mm314混合器区长度mm86.4板与板间间距mm9.53板5与床间距mm10.8板4与床间距mm10.8板厚度mm5.41板4,5空穴尺寸mm12.9板1,3空穴尺寸mm19.6板2空穴尺寸mm52.1δ2deg-15δ1deg15板4,5R1mm20.1板4,5R2mm40.0板1,3R1mm29.2在氧化步骤期间,第四混合物在反应器同流换热器区的下游产生,该第四混合物包含1.2wt%分子氢(燃料),12.7wt%分子氧(氧化剂)和86.1wt%氮气(稀释剂),基于第四混合物的重量。在1.172巴(绝对压力;2.3psig)的进料压力下,燃料速率是2.96×10-4Kg/s且氧化剂速率是0.024Kg/s。混合器-分布器将第一和第二反应物混合而产生第四混合物并将该第四混合物分布而提供流过第二反应器的较均匀气流,该第二反应器呈蜂窝器整料形式。使用板3和4使流体在该蜂窝器整料内均匀地再分布。观察到减少板1和2之间的空穴重叠改进了燃料和氧化剂的混合。混合器-分布器具有0.8巴的压降,和5.7%的MD,70%的TV和98.3wt%的ME。实施例2提供再生性逆流反应器,该反应器与实施例1的反应器相同,不同之处在于用美国专利号7,815,873图6的混合器-分布器代替该实施例的混合器-分布器。使用如实施例1中规定的相同原料和条件操作燃烧步骤。该混合器-分布器具有等于大约9.2%的MD。讨论使用本发明的混合器-分布器(实施例1)提供优于现有技术中的混合器(实施例2)的改进的混合-分布性能,表明第四混合物的分布得到改进,而导致更有效的氧化步骤。特别地,实施例1的混合器-分布器具有(i)显著减小的MD和(ii)与实施例2的混合器-分布器的那些相同或更好的压降、TV和ME值。