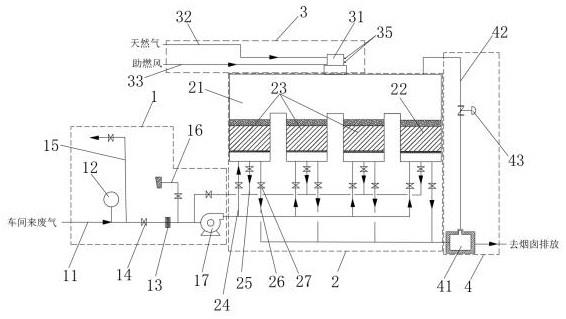
1.本发明涉及环保技术领域,具体为一种安全型在线自清洁工业有机废气处理系统。
背景技术:2.常规的蓄热式氧化反应器由三室、五室或更多的奇数室构成,以三室为例,运行时为一进一出一吹扫,五室则为二进二出一吹扫。
3.但是在某些制造行业,如:沥青调制、防水材料、焦炭相关、苯酐制备等细分行业,生产过程产生的有机废气往往成分相当复杂,废气往往含有类似焦油状态的粘性物质,这些类似焦油状态的粘性物质在蓄热式氧化反应器的蓄热材料低温区、共用通道、进出口风道、提升阀密封面等废气经过的各处形成沉积物,黏附在所有废气经过的表面;蓄热式氧化反应器的蓄热材料因废气通道狭窄,比表面非常大,非常容易被焦油状态的粘性物质堵塞。这些上述粘性物质在蓄热式氧化反应器系统的沉积堵塞造成以下后果:1、有机废气在蓄热材料内表面的堵塞造成将运行中断,无法长周期运行,影响主体生产设备的正常运行,造成非计划停车事件。
4.2、粘性物质在上述各处的严重沉积,将形成严重的安全隐患,这些物质一旦被高温引燃,将造成火灾事故。
5.3、在共用通道、出口风道、烟囱底部沉积的焦油状态的粘性物质的挥发物将污染经蓄热式氧化反应器处理达标的洁净气,导致洁净气排出不达标。
6.另外,由于rto操作温度>760℃,远高于大部分有机物的燃点和闪点,属于明火设备,因此当车间来废气发生大幅波动、或燃气、或内外环境满足闪爆条件时将发生闪爆事故,因此,其需要更加周全的安全预防措施。
技术实现要素:7.本发明的目的在于提供一种安全型在线自清洁工业有机废气处理系统,以解决上述背景技术中提出的粘性物质在蓄热式氧化反应器系统容易沉积堵塞,以及安全预防措施不周全的问题。
8.为实现上述目的,本发明提供如下技术方案:一种安全型在线自清洁工业有机废气处理系统,包括进气系统、蓄热室氧化反应系统、燃烧系统和排放系统,所述进气系统经蓄热室氧化反应系统与排放系统连接,所述燃烧系统位于蓄热室氧化反应系统上部;所述蓄热室氧化反应系统包括氧化室、反烧室和奇数个蓄热室,所述蓄热室和反烧室底部均安装有进口风道、吹扫风道和出口风道,且进口风道、吹扫风道和出口风道上均安装有相应的切换阀,所述进口风道和吹扫风道均与进气系统连接,所述出口风道与排放系统连接。
9.优选的,所述进气系统包括进气管道,所述进气管道与grto风机的进风口连接,所
述进气管道上安装有lel检查仪和阻火器,且lel检查仪和阻火器之间的进气管道上安装有切断阀,所述进气管道上连接有回气管道和导气管道,且回气管道和导气管道上均安装有切断阀,所述进口风道与grto风机的出风口连接,所述吹扫风道与grto风机的进风口连接。
10.优选的,所述燃烧系统包含燃烧器,所述燃烧器通过管路分别与天然气气源和助燃风系统连接,所述天然气气源与燃烧器之间的管路上安装有捡漏认证监测点,且捡漏认证监测点两侧安装有切断阀,所述燃烧器上安装有若干个炉膛火焰检测装置。
11.优选的,所述排放系统包含混风箱,所述混风箱的进风口处与出口风道连接,洁净气经混风箱排向烟囱,所述混风箱与氧化室顶部之间连接有高温热旁通管道,且高温热旁通管道上安装有气动阀。
12.优选的,所述蓄热室为三个或者五个,运行时,三室为一进气室一出气室一吹扫室,五室则为二进气室二出气室一吹扫室。
13.优选的,所述蓄热室氧化反应系统的炉内壁涂装有一层mm级的高效耐温绝热涂层,且高效耐温绝热涂层外侧设置有rto隔热材料陶瓷纤维棉层。
14.优选的,所述反烧室和蓄热室的内部结构相同,由下至上均设置有第一格栅、阻挡层、第二格栅和蓄热陶瓷,且第一格栅和第二格栅的炉壁上开设有检修门。
15.优选的,所述蓄热陶瓷的孔隙率由下至上逐渐变小。
16.与现有技术相比,本发明的有益效果是:该安全型在线自清洁工业有机废气处理系统,1、设置反烧室,利用蓄热式积蓄的热量,通过反烧过程,对蓄热陶瓷下部低温区和低温风道进行升温到一定温度,将原来沉积焦油状态的粘性物质升温气化,对这些低温区进行在线自清洁作业,气相部分返回进行二次焚烧处理;2、设置lel检查仪、捡漏认证监测点、炉膛火焰检测装置,实现废气浓度检测、燃气捡漏认证、炉膛火焰状态检测,进一步提升安全防护措施;3、蓄热陶瓷的孔隙率由下至上逐渐变小,增加整个床层的耐堵性能;同时,二层格栅之间增加一层阻挡层,用于驻留堵塞物,另外,在二层格栅之间增加一个检修门,方便通过该检修门对阻挡层进行清洗或更换,有效延长蓄热陶瓷使用周期。
附图说明
17.图1为本发明的整体结构示意图;图2为本发明的反烧室结构示意图;图3为本发明的高效耐温绝热涂层和rto隔热材料陶瓷纤维棉层结构示意图;图4为本发明的捡漏认证监测点结构示意图。
18.图中:1、进气系统;2、蓄热室氧化反应系统;3、燃烧系统;4、排放系统;11、进气管道;12、lel检查仪;13、阻火器;14、切断阀;15、回气管道;16、导气管道;17、grto风机;21、氧化室;22、反烧室;23、蓄热室;24、进口风道;25、吹扫风道;26、出口风道;27、切换阀;28、高效耐温绝热涂层;29、rto隔热材料陶瓷纤维棉层29;2201、第一格栅;2202、阻挡层;2203、第二格栅;2204、蓄热陶瓷;2205、检修门;31、燃烧器;32、天然气气源;33、助燃风系统;34、捡漏认证监测点;35、炉膛火焰检
测装置;41、混风箱;42、高温热旁通管道;43、气动阀。
具体实施方式
19.下面将结合本发明实施例中的附图,对本发明实施例中的技术方案进行清楚、完整地描述,显然,所描述的实施例仅仅是本发明一部分实施例,而不是全部的实施例。基于本发明中的实施例,本领域普通技术人员在没有做出创造性劳动前提下所获得的所有其他实施例,都属于本发明保护的范围。
20.请参阅图1-4,本发明提供一种技术方案:一种安全型在线自清洁工业有机废气处理系统,包括进气系统1、蓄热室氧化反应系统2、燃烧系统3和排放系统4,进气系统1经蓄热室氧化反应系统2与排放系统4连接,燃烧系统3位于蓄热室氧化反应系统2上部。
21.蓄热室氧化反应系统2包括氧化室21、反烧室22和奇数个蓄热室23,蓄热室23和反烧室22底部均安装有进口风道24、吹扫风道25和出口风道26,且进口风道24、吹扫风道25和出口风道26上均安装有相应的切换阀27,进口风道24和吹扫风道25均与进气系统1连接,出口风道26与排放系统4连接。
22.进气系统1将有机废气送入进口风道24,并通过切换阀27依次送入蓄热室23,有机废气在蓄热室23获得升温达到燃烧温度后,进入氧化室21充分燃烧,有机物被转化为co2与h2o,进而再依次进入下一个蓄热室23,若干个蓄热室23之间通过切换阀27进行切换,实现进气、出气和吹扫工作,同时将大量热量蓄积在蓄热室23的蓄热陶瓷2204中,洁净气温度降低至排烟温度后,通过出口切换阀27依次送入出口风道26,最终通过排放系统4排出;在原有奇数个蓄热室23的基础上,增加一个反烧室22,利用蓄热式积蓄的热量,通过反烧过程,对蓄热陶瓷2204下部低温区和低温风道进行升温到一定温度,将原来沉积焦油状态的粘性物质升温气化,对这些低温区进行在线自清洁作业,气相部分返回氧化室21做二次焚烧处理。
23.其中,切换阀27采用高效零泄漏提升阀,提升阀关闭时间控制在0.8s以内;提升阀的泄漏率控制在0.00015%以下;最大程度减少废气进口与出口之间内泄漏,有效提高grto炉的处理效率,保证grto的处理效率>99.6%,烟囱出口非甲烷总烃浓度可降至10mg/nm
³
以下,完好满足目前国内环保最高排放标准。
24.进气系统1包括进气管道11,进气管道11与grto风机17的进风口连接,进气管道11上安装有lel检查仪12和阻火器13,且lel检查仪12和阻火器13之间的进气管道11上安装有切断阀14,进气管道11上连接有回气管道15和导气管道16,且回气管道15和导气管道16上均安装有切断阀14,进口风道24与grto风机17的出风口连接,吹扫风道25与grto风机17的进风口连接。
25.lel检查仪12检测到有机废气浓度高于25%lel时,即关闭进气管道11上的切断阀14,同时开启导气管道16上的切断阀14,导出易爆废气。
26.其中,lel检查仪12与进气管道11上切断阀14之间的设置距离需要满足lel检查仪12响应时间+进气管道11上切断阀14关闭时间+2s,以保证lel检查仪12检测到的高浓度废气在进入rto炉之前被进气管道11上切断阀14阻断,同时通过导气管道16上的切断阀14开启,导出易爆废气。
27.燃烧系统3包含燃烧器31,燃烧器31通过管路分别与天然气气源32和助燃风系统33连接,如图4所示,天然气气源32与燃烧器31之间的管路上安装有捡漏认证监测点34,且捡漏认证监测点34两侧安装有切断阀14,实现双切断控制,以防止天然气阀门发生泄漏的情况,在每次执行点火前必须进行燃气捡漏认证,燃气捡漏认证通不过,将禁止点炉。
28.燃烧器31上安装有若干个炉膛火焰检测装置35,炉膛火焰检测装置35具有自检功能,可连续检测炉膛火焰状态,并将信号输送至燃烧器31控制器面板,为防止氧化室21与助燃风差压过小,致使燃气燃烧不充分,系统建立差压认证,差压认证通不过,将禁止点炉。
29.排放系统4包含混风箱41,混风箱41的进风口处与出口风道26连接,洁净气经混风箱41排向烟囱,混风箱41与氧化室21顶部之间连接有高温热旁通管道42,且高温热旁通管道42上安装有气动阀43。
30.当炉膛温度超过设定值,可准确开启气动阀43,高温热旁通管道42设置一定的长度,保证进入高温热旁通管道42的废气一定的停留时间,充分完成氧化。
31.蓄热室23为三个或者五个,运行时,三室为一进气室一出气室一吹扫室,五室则为二进气室二出气室一吹扫室。
32.如图3所示,蓄热室氧化反应系统2的炉内壁涂装有一层mm级的高效耐温绝热涂层28,且高效耐温绝热涂层28外侧设置有rto隔热材料陶瓷纤维棉层29。
33.在蓄热室氧化反应系统2的炉壁表面温度与环境温度之间的温差越大,蓄热室氧化反应系统2向环境的散热就越大,因此降低蓄热室氧化反应系统2的炉壁表面温度是节能的重要手段。在炉内壁面涂装一层mm级的高效耐温绝热涂层28,并且在高效耐温绝热涂层28外侧设置rto隔热材料陶瓷纤维棉层29,能够将原来的炉壁表面温度下降10℃以上,可以有效将蓄热室氧化反应系统2的环境散热减低25%以上,由此可以将热效率提高到96%以上。
34.如图2所示,反烧室22和蓄热室23的内部结构相同,由下至上均设置有第一格栅2201、阻挡层2202、第二格栅2203和蓄热陶瓷2204,且第一格栅2201和第二格栅2203的炉壁上开设有检修门2205,方便通过检修门2205对阻挡层2202进行清洗或更换,有效延长蓄热陶瓷2204使用周期。
35.蓄热陶瓷2204的孔隙率由下至上逐渐变小,下层的蓄热陶瓷2204孔隙率大于上层的蓄热陶瓷2204,主要是为了针对特殊行业的含氨(胺),同时又含卤素废气因燃烧以后容易产生固体凝聚物的工况,增加整个床层的耐堵性能。
36.工作原理:以三室为例,如图1所示,其蓄热室氧化反应系统2共包含三个蓄热室23和一个反烧室22,正常运行时,三个蓄热室23通过进口风道24、吹扫风道25以及出口风道26上的切换阀27进行切换,实现一进气、一出气、一吹扫,每个蓄热室23的切换时间约为120s-180s;而反烧室22是独立运行的,反烧室22运行时,其吹扫风道25上的切换阀27打开,进口风道24和吹扫风道25上的切换阀27关闭,此时,其运行状态相当于吹扫状态,不同的是,其切换时间长于吹扫的时间,以此能够获得更高的反烧温度,反烧室22的切换时间以反烧室22温度达到反烧温度所需时间为切换时间,反烧室22完成一个切换时间后,置换下正常运行的吹扫室,进行下一轮次的反烧作业;反烧室22与吹扫室抽出的尾气返回到grto风机17进口,返回到蓄热室氧化反应系统2进行二次焚烧,保证洁净气排放达标;
通过反烧过程,对蓄热陶瓷2204下部低温区和低温风道进行升温到一定温度,将原来沉积焦油状态的粘性物质升温气化,对这些低温区进行在线自清洁作业;在处理含焦油状态的粘性物质,易在低温区积累的工况下,能够保持低温区的有机沉积物始终处于处理工艺允许的状态,保证了grto炉的长周期运行,杜绝因堵塞造成的非计划停车或经常性的停车清理作业,将废气处理设备故障对主生产过程的影响降低到最小。
37.尽管参照前述实施例对本发明进行了详细的说明,对于本领域的技术人员来说,其依然可以对前述各实施例所记载的技术方案进行修改,或者对其中部分技术特征进行等同替换,凡在本发明的精神和原则之内,所作的任何修改、等同替换、改进等,均应包含在本发明的保护范围之内。