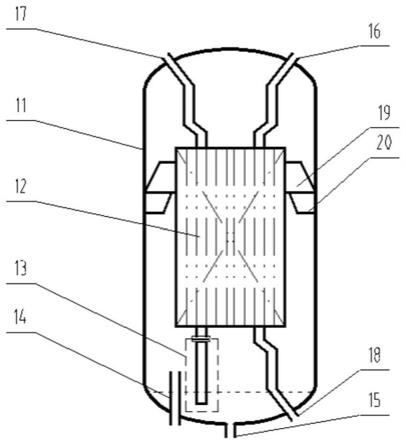
[0001]
本发明涉及有机废水处理技术领域,具体涉及一种内部集成有气液混合器的板壳式换热器及用其处理有机废水的方法和装置系统。
背景技术:[0002]
催化湿式氧化(catalytic wet air oxidation,简称cwao)法是在一定的温度(150~350℃)、压力(2~10mpa)和催化剂的作用下,经空气氧化,使污水中的有机物及氨分别氧化分解成co
2
、h
2
o及n
2
等无害物质来达到净化目的的方法。其是处理高浓度、有毒、有害、生物难降解废水的高效稳定的环保技术之一,具有应用范围广、净化效率高、占地面积小、能耗低、二次污染少等优点。
[0003]
但其在工业化的历程中,仍有诸多问题待优化。特别是在大规模废水处理中,物料升温所需热量很大(约占总成本30%),系统热集成效率决定了废水处理成本。废水与空气混合进料,可以共同预热至所需温度,避免废水与高压空气单独预热后混合,由于水相汽化气相潜热导致气液混合物温度下降,从而达不到反应所需温度而需要高温热源进一步加热,该部分能量占到系统总成本15%左右,同时额外增加的特材换热器也提高了装置建设成本。此外,水气两相在进入反应器之前充分混合接触,有利于提高水中溶氧量,促进有机物的氧化分解,提高了cod去除率。而气液混合的均匀性,决定了系统温度及压力的稳定性,对最终的cod去除率至关重要。
[0004]
传统换热器实现气液混合传热,有套管式及管壳式等形式。套管式换热器用材、占地较大,尤其是在物料为高温高压条件下,金属重量相对其他换热器大很多,成本较高。列管式换热器的壳程流速较低,气液容易分层,导致混合及传热效果变差,流动也不容易稳定。
[0005]
板壳式换热器,结构为将传统的板式换热器板芯置于耐压壳体中,由于其优良的传热性能及耐高压特性,得到广泛应用。同时板片内气液流速较高,可以维持良好的气液混合状态。为了维持换热器稳定高效运行,需要在换热器入口实现气液两相连续均匀混合。针对一般的气液混合,一般采用文丘里式,但是在cwao高压工况下,废水中有机物含量低,空气体积小,气液两相体积比在0.2~5:1,无法通过文丘里混合方式实现气液连续均匀混合。
[0006]
因此,开发一种适合高压下低气液比的气液混合热交换设备,对于传热效率及能耗影响很大,也直接决定了系统运行的稳定性,对该技术在环保领域的大规模应用具有重大意义。
技术实现要素:[0007]
为克服现有技术的不足,本发明的目的提供一种新的内部集成气液混合器的板壳式换热器,实现换热器冷热两侧均可高压气液混合进料,解决现有技术中文丘里等气体混合器不适用于高压低气液比的两相混合进料均匀分布的问题。
[0008]
本发明的另一目的在于这种新型集成气液混合器的板壳式换热器用于处理有机废水的方法,特别适用于cwao法。
[0009]
本发明的再一目的在于这种新型集成气液混合器的板壳式换热器用于处理有机废水的装置系统。
[0010]
为解决上述技术问题,本发明采用的技术方案如下:
[0011]
一种集成气液混合器的板壳式换热器,包括限定板壳式换热器内部空间的壳体、和位于壳体内部用于热交换的板芯以及气液混合器;所述板芯由至少一个板芯支承及连接部件与壳体连接;所述壳体的一端设有热侧进口和冷侧出口,分别与所述板芯一侧的热侧进口和冷侧出口相连;所述壳体的另一端设有气体进料管、液体进料管、热侧出口,所述板芯的另一侧设有冷侧进口、热侧出口,所述壳体的热侧出口与所述板芯的热侧出口相连;所述气液混合器的出口端与所述板芯的冷侧进口相连。
[0012]
在一个具体的实施方式中,所述的气液混合器包括气液混合主管,和位于所述气液混合主管内出口端一侧的至少一层混合元件,以及位于所述气液混合主管进口端的液体进料口和气体进料口。
[0013]
在一个具体的实施方式中,所述气体进料口为至少一根气体插入管,所述气体插入管从所述气液混合主管进口端的侧壁插入气液混合主管,所述气体插入管包括弯曲部及直管段,所述直管段端部开口并沿所述气液混合主管轴向向所述混合元件端延伸。
[0014]
在一个具体的实施方式中,所述气体进料口为2~6根气体插入管,所述气体插入管沿所述气液混合主管圆周方向均匀对称分布;优选地,所述气体插入管的直管段端部封闭,所述直管段侧壁开设有至少一排气体分布孔,每排气体分布孔至少有一个气孔,所述气体分布孔沿所述气体插入管直管段圆周方向均匀对称分布。
[0015]
在一个具体的实施方式中,所述直管段侧壁开设有2~15排气体分布孔,每排气体分布孔有3~9个气孔,所述气体分布孔沿所述气体插入管直管段圆周方向均匀对称分布;优选地,所述气体插入管直管段上的气体分布孔为圆形,开孔总面积为气液混合主管横截面积的1~20%,更优选为5%~15%。
[0016]
在一个具体的实施方式中,所述气液混合主管为一段竖直管或竖直与水平管组合的t型管,当为竖直管时,所述气液混合主管的进口端即为液体进料口;当为竖直与水平管组合的t型管时,所述水平管的两侧开口为液体进料口;优选为竖直管。
[0017]
在一个具体的实施方式中,所述气液混合主管为竖直与水平管组合的t型管,所述水平管的两侧开口为液体进料口,所述气体进料口为所述竖直管侧壁开设的2~15排气体分布孔,每排气体分布孔至少有一个气孔,优选每排气体分布孔有3~9个气孔,所述气体分布孔沿竖直管圆周方向均匀对称分布;优选地,所述竖直管上的气体分布孔为圆形,开孔总面积为气液混合主管横截面积的1~20%,更优选为5%~15%。
[0018]
在一个具体的实施方式中,所述的气体进料管向所述壳体内延伸,延伸至高度超过所述气液混合器的进口端。
[0019]
在一个具体的实施方式中,所述的混合元件为金属丝网、板片或陶瓷环中的任一种。
[0020]
在一个具体的实施方式中,所述的板芯由多层换热板片层叠而成,所述换热板片的厚度为0.4~2mm,优选为0.5~1mm;所述换热板片的间隙为3~20mm,优选为5~15mm;更
优选地,所述换热板片的间隙设置至少一个扰流元件,所述扰流元件为挡板。
[0021]
本发明的另一方面,一种有机废水的湿式氧化处理方法,将待处理的有机废水和空气经过前述结构的集成气液混合器的板壳式换热器,经混合预热后,再进入所述湿式氧化处理反应器进行湿式氧化反应。
[0022]
其中,所述有机废水和空气为高压低气速气液两相混合进料及出料,温度为130~280℃,压力为3~9mpag,且冷热侧均为气液两相混合物,气液两相体积比为0.2~5:1。
[0023]
本发明的再一方面,一种前述有机废水的湿式氧化处理方法的装置系统,包括用于储存高浓有机废水的原水储罐、高压泵、过滤器、高压缓冲罐、板壳式换热器、空压机、气液分离罐,尾气吸收塔和废水缓冲罐,其中,所述原水储罐通过管道经由高压泵依次连接于过滤器、高压缓冲罐和板壳式换热器液体进料管,空压机与板壳式换热器气体进料管相连,经板壳式换热器后的气液两相流再与反应塔进料口连接,反应后的高温气液两相流经过板壳式换热器热侧与进料冷侧气液两相流换热后,进入尾气吸收塔。
[0024]
与现有技术相比,本发明具有如下有益效果:
[0025]
(1)本发明的集成气液混合器的板壳式换热器,具体的气液混合和换热步骤为气液两相分别进入板壳式换热器的壳体内侧,然后分别进入气液混合主管,再经过混合元件进入板芯冷侧进行热交换,实现气液两相的均匀混合与换热。这种结构设计实现了换热器冷热两侧均可高压气液混合进料,解决了现有技术中文丘里等气体混合器不适用于高压低气液比的两相混合进料问题。
[0026]
(2)本发明的集成气液混合器的板壳式换热器,因其独特的结构设计,气液两相均匀混合后再经过板壳式换热器高效的换热,有效地保证了进入反应器的气液两相流的温度稳定性及气液均匀性。
[0027]
(3)本发明的集成气液混合器的板壳式换热器用于cwao法处理有机废水,因其出色的温度稳定性及气液均匀性,空气和废水中的有机物进入反应器后在整个反应器床层截面上得到了均匀分布和有效接触催化剂,有助于催化分解反应,保证了cod的去除率。
[0028]
(4)采用本发明的集成有气液混合器的板壳式换热器处理有机废水的装置系统,实现了20t/h以上规模的废水长期连续稳定运行,温度压力非常稳定,在反应塔内催化剂作用下,在反应温度为180~290℃,反应压力为5~8mpag下,停留时间为0.5~3hr,空气过量2%~50%的条件下,cod去除率达到90%以上,且取得了显著的技术效果。
附图说明
[0029]
图1为本发明一种处理高浓有机废水的装置系统流程示意图。
[0030]
图2为本发明集成气液混合器的板壳式换热器结构示意图。
[0031]
图3为本发明的一种气液混合器结构示意图,其气液主管为单根竖直管,气体进料管为伸入主管的多根管。
[0032]
图4为本发明的一种气液混合器结构示意图,其气液主管为竖直+水平管,气体进料管为伸入主管的多根管。
[0033]
图5为本发明的一种气液混合器结构示意图,其气液主管为竖直+水平管,气体进料管为主管侧壁的多排开孔。
[0034]
其中,1为原水储罐、2高压泵、3过滤器、4高压缓冲罐、5板壳式换热器、6空压机、7
反应塔、8气液分离罐、9尾气吸收塔、10废水缓冲罐、11壳体、12板芯、13气液混合器、14气体进料管、15液体进料管、16冷侧出口、17热侧进口、18热侧出口、19板芯支承、20连接结构、21液体入口、22气液混合主管、23气体分布孔、24混合元件、25气体插入管。
具体实施方式
[0035]
为了更好的理解本发明的技术方案,下面的实施例将对本发明所提供的方法予以进一步的说明,但本发明不限于所列出的实施例,还应包括在本发明的权利要求范围内其他任何公知的改变。
[0036]
如图2所示,本发明的内部集成气液进料混合器的板壳式换热器包括壳体11和位于壳体内部用于热交换的板芯12以及气液混合器13,所述壳体11限定板壳式换热器的内部空间,所述壳体11例如可以由316l、哈氏合金或钛合金等材质制造而成。所述板芯12由至少一个板芯支承19及连接部件20与壳体11连接;所述壳体11的一端设有热侧进口17和冷侧出口16,分别与所述板芯12一侧的热侧进口和冷侧出口相连;所述壳体11的另一端设有气体进料管14、液体进料管15、热侧出口18,所述板芯12靠近气体进料管14和液体进料管15的一侧设有冷侧进口、热侧出口,所述壳体的热侧出口18与所述板芯的热侧出口相连;所述气液混合器13的出口端与所述板芯的冷侧进口相连。
[0037]
其中,所述的气体进料管14优选向所述壳体11内延伸,延伸至高度超过所述气液混合器13的进口端,优选不超过气液混合主管22侧壁的气体分布孔23或气体插入管25位置,或恰好与该位置齐平。这种设计便于气相直接通过气体进料管14穿过液相进入板壳式换热器的内部气相空间,与位于板壳式换热器底部的液相形成稳定的气液界面,一般控制气液界面恰好或稍稍淹没气液混合器13的进口端,最好控制气液界面不超过气体插入管25的位置或者气液混合主管22表面的气体分布孔23的位置,从而有利于液相从气液混合器的液体进料口21进入气液混合器,以及气相从气体插入管25或者气液混合主管22表面的气体分布孔23进入气液混合抓管22,气液两相初步混合再进入混合元件24进一步均匀混合形成稳定均匀的气液两相流。
[0038]
作为所述的混合元件24,可以为一层或多层金属丝网、板片或陶瓷环中的任一种,优选2~6层,所述金属丝网、板片或陶瓷环均为本领域混合元件中的常见元件,没有任何特别的限制,通过混合元件的作用,进一步提升气液两相的混合均匀性。混合后的气液两相流进入板芯进行换热,均匀混合的气液两相流换热后得到温度稳定、气液分布均匀的气液两相流。
[0039]
作为所述的板芯,例如由多层换热板片层叠而成,所述换热板片的厚度为0.4~2mm,优选为0.5~1mm;所述换热板片的间隙为3~20mm,优选为5~15mm;更优选地,所述换热板片的间隙设置至少一个扰流元件,所述扰流元件为挡板。热介质通过热侧流过,与冷侧流过的气液两相流换热,从而实现冷侧料流热交换的目的。
[0040]
如图3所示,为本发明的一种气液混合器结构示意图,所述的气液混合器13包括气液混合主管22,所述气液混合主管22为单根竖直管,所述竖直管的一端为进口,另一段为出口;以及位于所述气液混合主管22内部出口端一侧的至少一层混合元件24,和位于所述气液混合主管进口端的液体进料口21和气体进料口,所述气液混合主管的进口端即为液体进料口21。所述气体进料口为伸入气液混合主管22的多根气体插入管25。所述气体插入管25
从所述气液混合主管22进口端的侧壁插入气液混合主管22,所述气体插入管25包括弯曲部及直管段,所述直管段端部开口并沿所述气液混合主管22轴向向所述混合元件端延伸,气相从气体插入管25通入从直管段端部开口进入气液混合主管22,并与液体进料口21通入的液体初步混合,再进入混合元件24进一步混合充分后流入板芯12换热。
[0041]
在一个优选的实施方式中,如图3所示,所述气体进料口为多根气体插入管25,优选2~6根,所述多根气体插入管25沿所述气液混合主管22圆周方向均匀对称分布,例如2~6根气体插入管25沿所述气液混合主管22半径r的0.5r~0.8r圆周处均匀对称分布;在一个优选的实施方案中,所述气体插入管25的直管段端部封闭,所述直管段侧壁开设有至少一排气体分布孔23,每排气体分布孔至少有一个气孔,所述气体分布孔沿所述气体插入管直管段圆周方向均匀对称分布。其中,位于所述气体插入管直管段同一横截面圆周方向的气孔为一排气体分布孔。同一排的气体分布孔沿着气体插入管直管段圆周方向均匀分布,多排气体分布孔之间沿着气体插入管直管段的长度方向均匀分布。例如,当每排只有一个气孔时,多排气体分布孔优选沿插入管直管段的长度方向交错均匀分布。更优选地,所述直管段侧壁开设有2~15排气体分布孔,每排气体分布孔有3~9个气孔,所述气体分布孔沿直管段圆周方向均匀对称分布,即同一排气体分布孔沿着气体插入管直管段圆周方向均匀分布,不同排的气体分布孔沿着气体插入管直管段的长度方向均匀分布;所述气体插入管直管段上的气体分布孔为圆形,开孔总面积为气液混合主管横截面积的1~20%,更优选为5%~15%,因为最终气体与气液混合物都是通过气液混合主管的横截面向上流动,控制所述气体分布孔的开孔率有利于气液混合。此时,壳体内充满的气体通过气体插入管25进入气液混合主管22,通入的气体从气体插入管25直管段侧壁开设的气体分布孔23均匀喷出,并与液体进料口21通入的液体充分混合,再进入混合元件24进一步混合充分后流入板芯12换热。
[0042]
如图4所示,为本发明的另一种气液混合器结构示意图,其气液混合主管22为竖直+水平管,气体进料口为伸入主管22的多根气体插入管25。所述气液混合主管22为竖直与水平管组合的t型管,所述水平管的两侧开口为液体进料口21。所述液相从t型管的水平管两侧开口进入气液混合主管22,与从气体分布孔23均匀喷出的气相充分混合,再进入混合元件24进一步混合充分后流入板芯12换热。此种情形下,所述气体进料口同样优选为多根气体插入管25,优选2~6根,所述气体插入管25沿所述气液混合主管22圆周方向均匀对称分布;所述气体插入管25的直管段端部封闭,所述直管段侧壁开设有至少一排气体分布孔23,每排气体分布孔至少有一个气孔,所述气体分布孔沿所述气体插入管直管段圆周方向均匀对称分布。更优选地,所述直管段侧壁开设有2~15排气体分布孔,每排气体分布孔有3~9个气孔,所述气体分布孔沿所述气体插入管直管段圆周方向均匀对称分布,具体均匀对称分布形式可与前述实施方式相同;所述气体插入管直管段上的气体分布孔为圆形,开孔总面积为气液混合主管横截面积的1~20%,更优选为5%~15%。
[0043]
如图5所示,为本发明再一种气液混合器结构示意图,其气液混合主管22为竖直+水平管,气体进料口为气液混合主管22侧壁的多排气体分布孔23。此时,无需气体插入管25,板壳式换热器内部的气体通过气液混合主管22管壁的气体分布孔23进入气液混合主管22,与t型管的水平管两侧液体进料口21进入的液相充分混合,再进入混合元件24进一步混合充分后流入板芯12换热。此种情形下,所述气液混合主管22的侧壁开设有至少一排气体
分布孔23。更优选地,所述气液混合主管22的侧壁开设有2~15排气体分布孔,每排气体分布孔至少有一个气孔,优选每排有3~9个气孔,所述气体分布孔沿主管圆周方向均匀对称分布,具体均匀对称分布形式可与前述实施方式相同;所述气体分布孔为圆形,开孔总面积为气液混合主管横截面积的1~20%,更优选为5%~15%。
[0044]
本发明的内部集成气液进料混合器的板壳式换热器的工作流程为:气相通过气体进料管14进入壳体11内部与板芯12外部的空间,液相通过液体进料管15同样进入此空间,空间内形成稳定的气液界面,并维持一定压力,然后气相、液相分别通过气体插入管25、液体进料口21相应部位进入气液混合器13的气液混合主管22,气体从气体分布孔23中均匀流出与液体初步混合,再经过混合元件24均匀混合后,进入板芯12,与热侧流过的热介质换热后从冷侧出口16维持气液两相混合流动状态流出,去往下游设备如反应器等。其中,热介质优选为下游设备返回的高温气液混合物经过热侧进口17进入板芯的热侧,与冷侧物料间壁式换热后由热侧出口18维持气液两相混合流出,板芯12与壳体11间通过板芯支承19及连接结构20连接。由于气液两相连续稳定地先进入壳体内空间,形成稳定的气液界面及压力后,再稳定均匀流入混合器内,可以实现气液连续稳定均匀混合,从而保证了下游换热后温度压力的均匀,以及反应塔内反应效果的高效稳定。
[0045]
如图1所示,为本发明一种处理高浓有机废水的装置系统流程示意图,涉及一种有机废水的湿式氧化处理方法,将待处理的有机废水和空气经过前述结构的集成气液混合器的板壳式换热器,经混合预热后,再进入所述湿式氧化处理反应器进行湿式氧化反应。具体地,一种有机废水的湿式氧化处理方法的装置系统,包括用于储存高浓有机废水的原水储罐1、高压泵2、过滤器3、高压缓冲罐4、板壳式换热器5、空压机6、气液分离罐8,尾气吸收塔9和废水缓冲罐10,其中,所述原水储罐1通过管道经由高压泵2依次连接于过滤器3、高压缓冲罐4和板壳式换热器5液体进料管,空压机6与板壳式换热器5气体进料管相连,经板壳式换热器5后的气液两相流再与反应塔7进料口连接,反应后的高温气液两相流经过板壳式换热器5热侧与进料冷侧气液两相流换热后,进入气液分离罐8,分离的气相进入尾气吸收塔9处理,液相进入废水缓冲罐10进一步去生化处理。
[0046]
现有技术中,实现气液两相在板壳式换热器入口均匀混合,大部分采用文丘里混合管,利用大量气体高流速经过喉径产生的负压吸入液体物料,液体物料往往以喷雾型式与气体实现均匀混合;文丘里混合均匀,结构简单,但需要较高气速,一般在较大的气液比时适用,对于气液两相流量较为接近的,无法通过文丘里混合器实现均匀混合。本发明中,所述有机废水和空气为高压低气速气液两相混合进料及出料,温度为130~280℃,压力为3~9mpag,且冷热侧均为气液两相混合物,气液两相体积比为0.2~5:1,通常,例如冷侧温度为130~280℃,一般热侧温度比冷侧温度高20~50℃,该集成气液混合器的板壳式换热器中,气液混合进料及出料的压力和气液两相体积比几乎不变,例如压力为3~9mpag,气液两相体积比为0.2~5:1。
[0047]
气液两相如果不能实现均匀混合,不但会造成换热器内传热不均匀,导致进入后续反应器的物料温度较大波动,同时还容易造成反应器内物料分布不均匀,同时压力波动,影响转化率及操作稳定性,反映在cwao废水处理中,表现为cod去除率波动且较低。
[0048]
本发明中气液两相,以空气及废水为例,分别进入板壳式换热器的壳体内侧,然后分别进入气液混合管,再经过混合元件进入板芯冷侧,实现气液两相的均匀混合与换热。换
热后高温的气液混合物进入反应塔,反应塔出口的高温气液混合物再通过板壳式换热器的热侧,与进料的气液混合物换热。
[0049]
本发明中,液体通过气液混合管下部的液体进料口进入主管,气体从侧面的插入管进入,并且设置气体分布孔,将气体均匀分散在液相流体中,气液初步混合后,再经过上部的混合元件实现更加均匀的混合。
[0050]
具体地,在催化湿式氧化废水处理技术(cwao)中,分别将含有甲醛、醋酸、甲醇、异丁醇、三甲胺等有机物的废水加压后与高压空气在板壳式换热器入口充分混合,预热至180~280℃后通入固定鼓泡床反应器内,气液全程均匀混合,较好地保证了进入反应器的温度稳定性及气液均匀性,空气和废水中的有机物进入反应器后在整个床层截面上的均匀分布和有效接触,充分发挥了催化剂的作用,保证了cod的去除率。采用本发明的带有进料气液混合器的板壳式换热器的系统流程,实现了20t/h以上规模的废水长期连续稳定运行,温度压力非常稳定,在反应塔内催化剂作用下,在反应温度为180~280℃,反应压力为5~8mpag下,停留时间为0.5~3hr,空气过量2%~50%的条件下,cod去除率达到90%以上,且取得了较好的技术效果。
[0051]
高浓有机废水(cod>5000mg/l)依次通过原水储罐、高压泵、过滤器、高压缓冲罐后,与空压机压缩的高压空气在板壳式换热器混合换热,在反应塔中进行接触并充分反应后,进入到气液分离罐,分离的气相通过尾气吸收塔处理后达标排放,分离的水相通过废水缓冲罐排放至下游生化处理系统。
[0052]
下面通过更具体的实施例进一步说明本发明方法的有益效果,但不构成任何的限制。
[0053]
如无特别说明,以下实施例及对比例中,反应塔7为气液固三相固定床鼓泡反应器,主体结构包含壳体、物料进出口、催化剂床层以及支承催化剂床层的格栅板等,结构形式参照万华化学集团股份有限公司开发的催化湿式氧化处理反应塔cn104761041a,除进料工艺参数和气液混合/换热方式外,其他未做特别说明之处,均可参考该现有技术。所用催化剂为中国科学院大连化学物理研究所开发的以ru为活性组分的催化剂(以下实施例及对比例中所提及的催化剂均指的是这种催化剂,该催化剂制备方法参照cn1583256a“一种处理工业废水的贵金属催化剂及其制备方法和应用”中的实施例3和4进行制备,其中活性组分贵金属ru含量为2wt%,载体为共沉淀法制备的zro
2-ceo
2
),以下实施例及对比例中反应空速均为1.33h-1
。
[0054]
实施例1
[0055]
按图1、图2及图3,气液混合管为竖直管,液相从底部的液体进料口进入,两根气体插入管从气液混合管的侧面伸入内部,并沿管长方向开设15排气体分布孔,每排孔4个沿圆周方向均匀分布,总开孔面积占竖直主管截面积的15%。将某苯酚丙酮装置产生的废水(含0.4%甲酸,0.2%丙酮)加压至6.5mpag后,与过量30%的高压空气混合,预热至240℃混合通入气液固三相固定床鼓泡反应器,发生湿式氧化反应,甲醛、醋酸被氧化为二氧化碳和水从而降低了cod,cod的去除率为93.0%,系统压力稳定,波动不超过0.2mpa。
[0056]
实施例2
[0057]
按图1、图2及图4,气液混合管为竖直管,液相从底部的液体进料口的两端进入,两根气体插入管从气液混合管的侧面伸入内部,并沿管长方向开设15排气体分布孔,每排气
体分布孔4个沿圆周方向均匀分布,总开孔面积占竖直主管截面积的15%。将某苯酚丙酮装置产生的废水(含0.4%甲酸,0.2%丙酮)加压至7.5mpag后,与过量20%的高压空气混合,预热至250℃混合通入气液固三相固定床鼓泡反应器,发生湿式氧化反应,cod的去除率为96.5%,系统压力稳定,波动不超过0.2mpa。
[0058]
实施例3
[0059]
按图1、图2及图5,气液混合管为竖直管,液相从底部的液体进料口的两端进入,气相从气液混合管侧面的气体分布孔进入内部,沿管长方向开设15排孔,每排孔6个沿圆周方向均匀分布,总开孔面积占竖直主管截面积的8%。将某苯酚丙酮装置产生的废水(含0.5%甲酸,0.3%丙酮)加压至6.5mpag后,与过量30%的高压空气混合,预热至245℃混合通入气液固三相固定床鼓泡反应器,发生湿式氧化反应,cod的去除率为95.2%,系统压力稳定,波动不超过0.2mpa。
[0060]
对比例1
[0061]
按图1、图2及图3,气液混合管为竖直管,液相从底部的液体进料口进入,两根气体插入管从气液混合管的侧面伸入内部,并沿管长方向开设15排气体分布孔,每排孔4个沿圆周方向均匀分布,总开孔面积占竖直主管截面积的15%。作为实施例1的对比例,将此气体插入管及气体分布孔堵塞,使气液共同从底部的液体进料口进入。将某苯酚丙酮装置产生的废水(含0.4%甲酸,0.2%丙酮)加压至6.5mpag后,与过量30%的高压空气混合,预热至240℃混合通入气液固三相固定床鼓泡反应器,发生湿式氧化反应。由于没有多点式均匀的气体进料口及气液初步混合,导致系统压力波动剧烈,压力最大波动达到0.6mpa,同时预热出口温度也在200~250℃范围内频繁波动,检测出料废水cod去除率波动较大,最低仅有80.6%。
[0062]
对比例2
[0063]
按图1、图2及图4,气液混合管为竖直管,液相从底部的液体进料口的两端进入,两根气体插入管从气液混合管的侧面伸入内部,并沿管长方向开设15排气体分布孔,每排气体分布孔4个沿圆周方向均匀分布,总开孔面积占竖直主管截面积的15%。作为实施例2的对比例,将此混合主管上方的混合元件去除。将某苯酚丙酮装置产生的废水(含0.4%甲酸,0.2%丙酮)加压至7.5mpag后,与过量20%的高压空气混合,预热至250℃混合通入气液固三相固定床鼓泡反应器,发生湿式氧化反应。由于气液初步混合均匀,但在进入板芯之前未经过混合元件的充分混合,仍有一定程度的不均匀性,导致系统压力在0.3mpa幅度内频繁波动,同时预热出口温度也在230~250℃范围内频繁波动,检测出料废水cod去除率波动较大,最低仅有87.6%。
[0064]
对比例3
[0065]
按图1及图2,取消标号13所示的气液混合器,气相液相分别进入图2中所示的壳体11与板芯12间的空隙,然后通过板芯12底部的开口直接进入板芯12中。作为实施例2的对比例,将某苯酚丙酮装置产生的废水(含0.4%甲酸,0.2%丙酮)加压至7.5mpag后,与过量20%的高压空气混合,预热至250℃混合通入气液固三相固定床鼓泡反应器,发生湿式氧化反应。由于气液未经混合,无法保持均匀进入板芯,导致物料换热严重不均匀,系统压力在0.8mpa幅度内频繁波动,同时预热出口温度也在200~250℃范围内频繁波动,检测出料废水cod去除率波动较大,最低仅有80.7%。相比对比例2,对比例3的系统压力及温度波动更
为剧烈,cod去除率也更低。
[0066]
由实施例和对比例可知,本发明的集成气液混合器的板壳式换热器用于处理有机废水,cod的去除率达到93.0%以上,系统压力稳定,波动不超过0.2mpa;相反,不采用本发明结构的集成气液混合器的板壳式换热器,系统压力波动剧烈,预热出口温度波动也较大,出料废水cod去除率波动较大,最低仅有80.6%,不利于工业化有机废水处理装置地连续稳定运行。
[0067]
尽管本发明的内容已经通过上述实施例作了详细介绍,但应当认识到上述的描述不应被认为是对本发明的限制。本领域技术人员可以理解,在本说明书的教导之下,可对本发明做出一些修改或调整。这些修改或调整也应当在本发明权利要求所限定的范围之内。