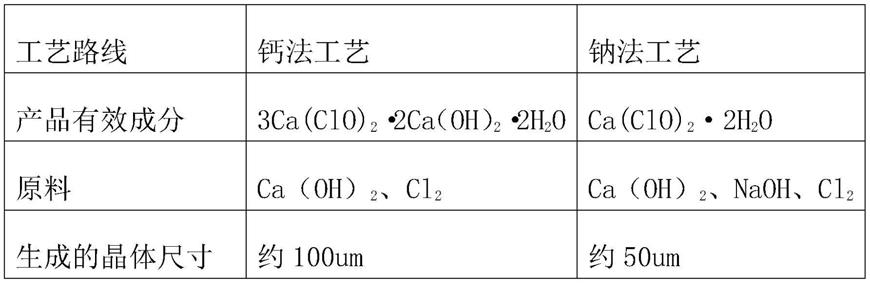
[0001]
本发明属于钙法漂粉精技术领域,具体涉及一种用于钙法粉状漂粉精产品生产的离心干燥系统及方法。
背景技术:[0002]
消毒剂广泛应用于卫生防疫、水体处理、食品杀菌和水产养殖等领域,漂白剂广泛应用于造纸、纺织和印染等行业,漂白消毒剂可分为有机和无机两大类,常见的无机类漂白消毒剂有漂粉精(次氯酸钙)、次氯酸钠溶液,过氧化氢和臭氧等。漂粉精主要成分是次氯酸钙,作为一种高效无机漂白剂和消毒剂,漂粉精具有稳定性强、无有毒残留和环保等优点,广泛应用于泳池消毒、水产养殖业消毒、工业及生活用水处理等领域。
[0003]
生产漂粉精的工艺路线主要有两种,分别为钙法工艺和钠法工艺。钙法漂粉精的有效成分是3ca(clo)2·
2ca(oh)2·
2h2o,通过ca(oh)2和cl2反应制备得到。钠法漂粉精主要成分是ca(clo)2·
2h2o,通过naoh、ca(oh)2和cl2反应制备得到,两种工艺路线对比情况见下表:
[0004]
表1漂粉精两种工艺路线技术对比表
[0005][0006][0007]
传统钙法漂粉精离心干燥流程:采用刮刀式离心机对氯化浆进行固液分离,将得到的含水量约20~25%wt的滤饼送入滚筒或流化床干燥器干燥后,得到粒状漂粉精产品,传统钙法漂粉精离心干燥技术有如下局限性:
[0008]
1、无法直接生产高附加值的粉状产品
[0009]
经滚筒或流化床干燥制成的漂粉精成品,呈大小不均的颗粒状,溶解性差,需经研磨后才能得到粉状产品。
[0010]
2、单元操作不连续
[0011]
(1)刮刀离心机批次操作,这种不连续的操作对上游氯化单元和下游干燥单元影响很大,产品品质不稳定的情况经常发生。
[0012]
(2)刮刀离心机需要专岗工人根据现场实际工况,控制进料出料,现场维护工作多,无法实现自动化控制,不利于漂粉精装置的大型化。
[0013]
3、关键设备产能低,装置投资高,占地大
[0014]
(1)刮刀式离心机单机产能低。例如钙法漂粉精生产常用的gkh-1250型卧式刮刀离心机,单台离心机每个离心周期(约1小时)仅能生产约300kg漂粉精,一套3万吨/年漂粉精装置需要12台离心机,设备置投资高,占地大。
[0015]
(2)漂粉精湿料中含次氯酸根离子和氯离子,与物料直接接触的材料需选用钛材,滚筒干燥器体积庞大(直径约2m,长度约20m),钛材耗量大。
[0016]
4、劳动强度大
[0017]
(1)氯化浆中的细小晶体会堵塞刮刀离心机的滤布,降低滤布的透过性,为了保证离心机的高效,每隔一段时间(1~3天),需人工拆洗滤布。
[0018]
(2)刮刀离心机噪声污染严重,故障频率高,检维修难度大。
[0019]
5、有效成分损失多,原料消耗定额高
[0020]
(1)离心初期,刮刀离心机未形成滤饼层,细微的漂粉精晶体会透过滤布,流失到离心母液中;
[0021]
(2)离心末期,刮刀离心机内部滤饼层较高,少量漂粉精会随着氯化浆会翻过挡液板,溢流到离心母液中;
[0022]
(3)要实现产品中含水率<4%,漂粉精湿料在滚筒干燥器内部停留时间需在1小时以上,而漂粉精是一种热敏性物质,停留时间过长,会造成部分漂粉精分解。
[0023]
上述三个过程会造成5~10%的有效成分损失,造成产品有效氯低,原料消耗定额高。
[0024]
6、能耗高
[0025]
(1)刮刀离心机和滚筒干燥器配套电机功率大,电耗高;
[0026]
(2)滚筒干燥器干燥热效率低,蒸汽消耗多。
技术实现要素:[0027]
为了解决现有技术存在的上述问题,本发明目的在于提供一种自动连续、避免堵塞的用于钙法粉状漂粉精产品生产的离心干燥系统及方法。
[0028]
本发明所采用的技术方案为:
[0029]
一种用于钙法粉状漂粉精产品生产的离心干燥系统,包括用于对氯化浆进行固液分离的卧螺离心机,卧螺离心机的湿料出口通过管道连接有混料器,混料器的出口通过管道连接有干燥器,干燥器的出口通过管道连接有旋风分离器,旋风分离器的气体出口连接有布带除尘器,旋风分离器的固体出口连接有漂粉精管,布带除尘器的固体出口与漂粉精管连接,漂粉精管与混料器之间还连接有干料管。
[0030]
自上游氯化单元送来的氯化浆送至专用卧螺离心机,氯化浆在卧螺离心机内进行固液分离,得到漂粉精含水量30~35%的湿料和离心母液,湿料送至混料器,离心母液送出界区外。湿料在混料器中和干燥后的漂粉精干料进行混合,将湿料含水率降低到20~25%湿料后,送入旋转闪蒸干燥系统。湿料经混入干燥后的漂粉精干料后含水率降低,避免湿料在干燥器中堵塞的情况。
[0031]
湿料被送入旋转闪蒸干燥器底部,在干燥器底部被打散成粉状,120~140℃至的热空气饼从干燥器底部被送入,与粉状湿料充分接触,湿料被干燥成粉状漂粉精产品(含水率<3%)后,从干燥器顶部被吹出,进入产品收集和除尘系统;粉状产品经旋风分离器和布袋除尘器收集后包装外送。热空气带着粉状漂粉精依次经过旋风分离器和布袋除尘器,粉状产品被收集和包装后作为成品销售,热空气布袋除尘达到排放标准后高点排放。
[0032]
作为本发明的优选方案,所述干燥器的底部通过管道连接有空气加热器,空气加热器的另一端通过管道连接有鼓风机。空气加热器对鼓风机送来的空气进行加热,再送至干燥器内对湿料进行充分干燥。
[0033]
作为本发明的优选方案,所述布带除尘器的气体出口通过管道连接有引风机。引风机能将气体排出,进行放空。
[0034]
作为本发明的优选方案,所述干燥器为旋转闪蒸干燥器。
[0035]
一种用于钙法粉状漂粉精产品生产的离心干燥方法,包括如下步骤:
[0036]
s1:将氯化浆送至卧螺离心机进行固液分离,得到漂粉精湿料和离心母液。将自上游氯化单元送来的氯化浆送至专用卧螺离心机,氯化浆在卧螺离心机内进行固液分离,得到漂粉精含水量30~35%的湿料和离心母液,湿料送至混料器,离心母液送出界区外。
[0037]
s2:将湿料送至混料器,与干燥后的漂粉精混合。湿料在混料器中和干燥后的漂粉精干料进行混合,将湿料含水率降低到20~25%湿料后,避免湿料送入干燥器后产生堵塞。
[0038]
s3:将混合的湿料送至干燥器中干燥,得到粉状漂粉精。湿料被送入旋转闪蒸干燥器底部,在干燥器底部被打散成粉状,120~140℃至的热空气饼从干燥器底部被送入,与粉状湿料充分接触,湿料被干燥成粉状漂粉精产品(含水率<3%)后,从干燥器顶部被吹出,进入产品收集和除尘系统;粉状产品经旋风分离器和布袋除尘器收集后包装外送。
[0039]
s4:将粉状漂粉精经旋风分离器分离,再用布袋除尘器收集,得到漂粉精成品,部分漂粉精成品送至混料器。热空气带着粉状漂粉精依次经过旋风分离器和布袋除尘器,粉状产品被收集和包装后作为成品销售,热空气布袋除尘达到排放标准后高点排放。
[0040]
作为本发明的优选方案,在步骤s2中,混料时,使混合后的湿料的含水率保持在20~25%。
[0041]
作为本发明的优选方案,在步骤s3中,所述干燥器为旋转闪蒸干燥器,干燥停留时间小于1min。
[0042]
作为本发明的优选方案,在步骤s3中,通过向干燥器中鼓入空气加热器加热的空气来对湿料进行干燥。
[0043]
作为本发明的优选方案,在步骤s3中,所述干燥器的进风温度控制在120~140℃。
[0044]
作为本发明的优选方案,在步骤s4中,通过引风机将布带除尘器排出的气体放空。
[0045]
本发明的有益效果为:
[0046]
1.本发明采用专门设计的卧螺离心机,固液分离机理为沉降分离加螺旋卸料,既实现了钙法漂粉精离心过程的自动连续生产,又解决了有效成分流失多、劳动强度大,产品品质不稳定的问题。
[0047]
2.由于卧螺离心机出口的湿料含水率高,为了防止旋转闪蒸干燥器堵塞停机,本发明采用了混料器对湿料和干粉进行混料,将湿料含水降低到约20~25%后送入旋转闪蒸干燥器,避免旋转闪蒸干燥器堵塞,保证了旋转闪蒸干燥器运行的稳定性。
[0048]
3.传统的钙法漂粉精滤饼多采用滚筒器进行干燥,干燥停留时间长,产品呈颗粒状;本发明采用专门设计的旋转闪蒸干燥器,具有停留时间短,分解率低,能耗低,可生产溶解性更好的粉状漂粉精等优点。
附图说明
[0049]
图1是本发明的结构示意图。
[0050]
图中,1-卧螺离心机;2-混料器;3-干燥器;4-旋风分离器;5-布带除尘器;6-空气加热器;7-鼓风机;8-引风机;41-漂粉精管;42-干料管。
具体实施方式
[0051]
下面详细描述本发明的实施例,所述实施例的示例在附图中示出,其中自始至终相同或类似的标号表示相同或类似的元件或具有相同或类似功能的元件。下面通过参考附图描述的实施例是示例性的,旨在用于解释本发明,而不能理解为对本发明的限制。
[0052]
实施例1:
[0053]
如图1所示,本实施例的用于钙法粉状漂粉精产品生产的离心干燥系统,包括用于对氯化浆进行固液分离的卧螺离心机1,卧螺离心机1的湿料出口通过管道连接有混料器2,混料器2的出口通过管道连接有干燥器3,干燥器3的出口通过管道连接有旋风分离器4,旋风分离器4的气体出口连接有布带除尘器5,旋风分离器4的固体出口连接有漂粉精管41,布带除尘器5的固体出口与漂粉精管41连接,漂粉精管41与混料器2之间还连接有干料管42。所述干燥器3为旋转闪蒸干燥器3。
[0054]
自上游氯化单元送来的氯化浆送至专用卧螺离心机1,氯化浆在卧螺离心机1内进行固液分离,得到漂粉精含水量30~35%的湿料和离心母液,湿料送至混料器2,离心母液送出界区外。湿料在混料器2中和干燥后的漂粉精干料进行混合,将湿料含水率降低到20~25%湿料后,送入旋转闪蒸干燥系统。湿料经混入干燥后的漂粉精干料后含水率降低,避免湿料在干燥器3中堵塞的情况。
[0055]
湿料被送入旋转闪蒸干燥器3底部,在干燥器3底部被打散成粉状,120~140℃至的热空气饼从干燥器3底部被送入,与粉状湿料充分接触,湿料被干燥成粉状漂粉精产品(含水率<3%)后,从干燥器3顶部被吹出,进入产品收集和除尘系统;粉状产品经旋风分离器4和布袋除尘器收集后包装外送。热空气带着粉状漂粉精依次经过旋风分离器4和布袋除尘器,粉状产品被收集和包装后作为成品销售,热空气布袋除尘达到排放标准后高点排放。
[0056]
为了给干燥器3提供稳定的热空气,所述干燥器3的底部通过管道连接有空气加热器6,空气加热器6的另一端通过管道连接有鼓风机7。空气加热器6对鼓风机7送来的空气进行加热,再送至干燥器3内对湿料进行充分干燥。
[0057]
更进一步,所述布带除尘器5的气体出口通过管道连接有引风机8。引风机8能将气体排出,进行放空。
[0058]
传统的钙法漂粉精固液分离采用刮刀离心机,固液分离机理为采用滤饼滤料过滤+刮刀卸料。本发明采用专门设计的卧螺离心机1,固液分离机理为沉降分离加螺旋卸料,既实现了钙法漂粉精离心过程的自动连续生产,又解决了有效成分流失多、劳动强度大,产品品质不稳定的问题。
[0059]
传统的钙法漂粉精滤饼多采用滚筒器进行干燥,干燥停留时间长,产品呈颗粒状。本发明采用专门设计的旋转闪蒸干燥器3,具有停留时间短,分解率低,能耗低,可生产溶解性更好的粉状漂粉精等优点。
[0060]
由于卧螺离心机1出口的湿料含水率高,为了防止旋转闪蒸干燥器3堵塞停机,本发明采用了混料器2对湿料和干粉进行混料,将湿料含水降低到约20~25%后送入旋转闪蒸干燥器3,保证了旋转闪蒸干燥器3运行的稳定性。
[0061]
本发明实现了钙法漂粉精离心干燥过程的连续操作,大幅降低了设备投资成本和运行成本,改善了工人劳动环境,降低了工人劳动强度,并生产出溶解性能更好和品质更稳定粉状漂粉精产品。本发明无技术难度,可能会被模仿。
[0062]
实施例2:
[0063]
一种用于钙法粉状漂粉精产品生产的离心干燥方法,包括如下步骤:
[0064]
s1:将氯化浆送至卧螺离心机1进行固液分离,得到漂粉精湿料和离心母液。将自上游氯化单元送来的氯化浆送至专用卧螺离心机1,氯化浆在卧螺离心机1内进行固液分离,得到漂粉精含水量30~35%的湿料和离心母液,湿料送至混料器2,离心母液送出界区外。
[0065]
s2:将湿料送至混料器2,与干燥后的漂粉精混合。湿料在混料器2中和干燥后的漂粉精干料进行混合,将湿料含水率降低到20~25%湿料后,避免湿料送入干燥器3后产生堵塞。
[0066]
s3:将混合的湿料送至干燥器3中干燥,得到粉状漂粉精,干燥停留时间小于1min。通过向干燥器3中鼓入空气加热器6加热的空气来对湿料进行干燥。所述干燥器3的进风温度控制在120~140℃。湿料被送入旋转闪蒸干燥器3底部,在干燥器3底部被打散成粉状,120~140℃至的热空气饼从干燥器3底部被送入,与粉状湿料充分接触,湿料被干燥成粉状漂粉精产品(含水率<3%)后,从干燥器3顶部被吹出,进入产品收集和除尘系统;粉状产品经旋风分离器4和布袋除尘器收集后包装外送。
[0067]
s4:将粉状漂粉精经旋风分离器4分离,再用布袋除尘器收集,得到漂粉精成品,部分漂粉精成品送至混料器2。热空气带着粉状漂粉精依次经过旋风分离器4和布袋除尘器,粉状产品被收集和包装后作为成品销售,热空气布袋除尘达到排放标准后高点排放。通过引风机8将布带除尘器5排出的气体放空。
[0068]
本发明采用专门设计的卧螺离心机1,固液分离机理为沉降分离加螺旋卸料,既实现了钙法漂粉精离心过程的自动连续生产,又解决了有效成分流失多、劳动强度大,产品品质不稳定的问题。
[0069]
由于卧螺离心机1出口的湿料含水率高,为了防止旋转闪蒸干燥器3堵塞停机,本发明采用了混料器2对湿料和干粉进行混料,将湿料含水降低到约20~25%后送入旋转闪蒸干燥器3,避免旋转闪蒸干燥器3堵塞,保证了旋转闪蒸干燥器3运行的稳定性。
[0070]
本发明根据钙法漂粉精氯化浆的性质,优化了卧螺离心机1的内部结构和运行参数,开发了钙法漂粉精专用卧螺离心机1,使得离心湿料含水率由40~45%降低到30~35%,湿料中的氯化钙的量也随之降低,使得漂粉精产品的有效氯提高约2~3%,解决了采用卧螺离心机1后产品有效氯无法达标的问题。
[0071]
卧螺离心机1处理能力大,一套3万吨/年漂粉精装置仅需2~4台卧螺离心机1(如
采用刮刀离心机,则需要12台),可大幅降低设备投资和装置占地。
[0072]
卧螺离心机1省去了换洗滤布的操作,基本免维护,大幅减少了维护检修的工作量,并且避免了离心和滤布冲洗阶段有效氯损失问题;
[0073]
相较于刮刀离心机,卧螺离心机1湿料含水率较高(卧螺30~35%,刮刀20~25%),如将该湿料直接送入干燥器3,会造成堵塞停机等问题。因此,本发明中设置了混料器2,将湿料和干燥后的漂粉精干料(含水率约3%)进行混合,将含水率降低到20~25%后送入下游干燥设备。
[0074]
与传统钙法漂粉精干燥流程相比,旋转闪蒸干燥系统自带打散功能,在湿料状态下,直接打散并干燥成为粉状产品,不需单独设置磨粉装置,避免了磨粉过程的火灾风险。
[0075]
根据钙法粉状漂粉精卧螺离心湿料的性质,优化了旋转闪蒸干燥系统的内部结构和运行参数,使得漂粉精产品含水率<3%。
[0076]
旋转闪蒸干燥器3进风温度120℃,干燥停留时间短(<1min),干燥过程有效氯分解损失可降低至1%(传统的滚筒干燥过程中有效氯分解5%);同时正常运行时旋转闪蒸干燥器3内的物料少(约50~100kg),与传统的滚筒干燥器3(容量为1000~1500kg)相比,大大降低了物料分解着火的危险性。
[0077]
漂粉精产品为粉状产品,粒径均匀溶解性能好,且粉状产品粒度可根据用户需求调整,有效氯满足国标。
[0078]
传统的钙法漂粉精滤饼多采用滚筒器进行干燥,干燥停留时间长,产品呈颗粒状;本发明采用专门设计的旋转闪蒸干燥器3,具有停留时间短,分解率低,能耗低,可生产溶解性更好的粉状漂粉精等优点。
[0079]
本发明不局限于上述可选实施方式,任何人在本发明的启示下都可得出其他各种形式的产品,但不论在其形状或结构上作任何变化,凡是落入本发明权利要求界定范围内的技术方案,均落在本发明的保护范围之内。