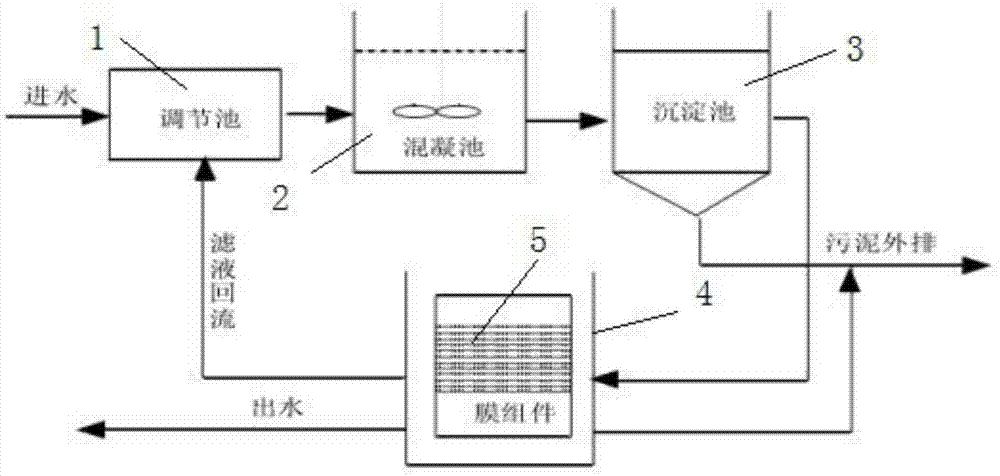
本发明涉及工业废水处理
技术领域:
,特别是一种将絮凝和微滤膜结合进行处理工业废水的装置及方法。
背景技术:
:随着当代工业日新月异的发展,工业用水量和废水的排放量也在日渐增加,在世界各国,水质都出现了程度不尽相同的污染。与此同时,水污染和水资源危机已成为约束经济可持续发展的两个重要原因。为了缓解水资源危机,工业废水回收和处理技术的研究也逐渐成为人们的密切关注的焦点[1]。因此,建立一个完善的、拥有高经济效益的水回用系统,实现废水资源化与无害化,是目前废水处理的主流趋势之一。现在被广泛应用的工业废水处理方法可以依据它的作用原理,划分为物理法、化学法、生物法和物理化学法这四大类。其中,物理法可进一步分为调节法、过滤法、沉淀法等;化学法分化学沉淀法、中和法、混凝法、氧化还原法等;生物法分厌氧生物处理法和好氧生物处理法等;而物理化学法则分为吸附法、膜分离法、离子交换法、萃取法、气提法等。这其中的膜分离法是在上个世纪50年代萌生起来的一门新兴科学,然后,再到上世纪70年代便开始大规模应用在各个工业领域以及科研方面,使其逐渐受到关注。目前常用的膜分离方法有反渗透、电渗析、微滤、纳滤、超滤和液膜等。微滤技术便是从19世纪初开始研究的,它是膜分离法中最早形成产业链的一种方法。最早在1850年左右出现过以天然或人工合成的聚合物制成的微孔过滤膜。作为世界上较早期被开发并应用的膜技术,微滤膜能够截留大小约为0.1-1μm之间的颗粒,并且使无机盐和小分子等溶质可以透过微滤膜,而细菌、大分子量胶体及悬浮物等物质就会在膜表面被截留。此外,微滤膜技术还是一种精密度很高的过滤技术。在废水净化方面,通常的做法是通过将细菌、颗粒性杂质以及悬浮物等和水分离,以便使滤液达到一定的合格标准。一般而言,可以根据需要去选择合适的膜过滤工艺。通过调节废水特性,能够提高膜技术的分离效率。但是微滤膜技术也有其局限性,如成膜过程、成膜条件受废水特性的影响。因此,亟待开发一种将絮凝和微滤膜结合进行处理工业废水的装置及方法。技术实现要素:本发明的目的是要解决现有技术中存在的不足,提供一种将絮凝和微滤膜结合进行处理工业废水的装置及方法。为达到上述目的,本发明是按照以下技术方案实施的:一种将絮凝和微滤膜结合进行处理工业废水的装置,包括调节池、絮凝池、沉淀池、安装有微滤膜组件的渗透池,工业废水与调节池的进水口连接,调节池的出水口与絮凝池的进水口连接,絮凝池内加入有絮凝剂,絮凝池的出水口与沉淀池的进水口连接,沉淀池底部设有污泥排出口,微滤膜组件设置在渗透池中部,沉淀池上部设置的溢流口与渗透池底部的进水口连接,渗透池上部设有净水出口、渗透池底部设有排泥口。进一步,所述絮凝剂为feso4或聚合氯化铝pac。进一步,所述微滤膜组件为聚偏氟乙烯pvdf微滤膜,孔径为0.1-0.4μm。进一步,所述微滤膜组件下方的渗透池底部还设有曝气头,曝气头通过管道与渗透池外的气泵连接,管道上设有气体流量计。进一步,微滤膜组件下方的渗透池侧壁通过泵与调节池的进水口连接。一种将絮凝和微滤膜结合进行处理工业废水的方法,使用上述将絮凝和微滤膜结合进行处理工业废水的装置,包括以下步骤:将工业废水送入调节池,然后进入事先加了絮凝剂的絮凝池里对工业废水进行絮凝操作,絮凝后的工业废水进入沉淀池进行沉淀,沉淀池上部的滤液进入渗透池经微滤膜组件进行过滤,由渗透池的出水口得到净水。与现有技术相比,本发明将微滤膜分离技术与化学絮凝、沉淀技术相结合,原水(工业废水)通过加入絮凝剂进行预处理,使得废水中的悬浮颗粒失去稳定性,胶粒物相互凝聚使微粒增大,形成絮凝体,然后絮凝体达到一定体积后由于重力作用经沉淀池沉淀下来,再通过微滤膜组件的过滤作用,经过两种处理方法相结合,最后使水达到水质标准,对工业废水的净化效果好。附图说明图1为本发明的结构示意图。图2为渗透池的结构示意图。图3为本发明实施例中的上清液和混浊液微滤膜截留效果比较。图4为本发明实施例中的进水mlss浓度与出水ni离子浓度的关系。图5为本发明实施例中的进水mlss浓度与出水cu离子浓度的关系。图6为本发明实施例中的微滤膜直接过滤和絮凝后微滤膜过滤效果比较。图7为本发明实施例中的孔径对微滤膜截留效率的影响。图8为本发明实施例中的进水浓度对微滤膜截留效率的影响。具体实施方式为使本发明的目的、技术方案及优点更加清楚明白,以下结合实施例,对本发明进行进一步的详细说明。此处所描述的具体实施例仅用于解释本发明,并不用于限定发明。如图1所示,本实施例的一种将絮凝和微滤膜结合进行处理工业废水的装置,包括调节池1、絮凝池2、沉淀池3、安装有微滤膜组件5的渗透池4,工业废水与调节池1的进水口连接,调节池1的出水口与絮凝池2的进水口连接,絮凝池2内加入有絮凝剂,絮凝池2的出水口与沉淀池3的进水口连接,沉淀池3底部设有污泥排出口,微滤膜组件5设置在渗透池4中部,沉淀池3上部设置的溢流口与渗透池4底部的进水口连接,渗透池4上部设有净水出口、渗透池4底部设有排泥口41,净水出口可以连接水泵44。进一步,所述微滤膜组件5下方的渗透池底部还设有曝气头45,曝气头45通过管道与渗透池4外的气泵42连接,管道上设有气体流量计43。本实施例中,所述絮凝剂为feso4或聚合氯化铝pac。本实施例中,所述微滤膜组件5为聚偏氟乙烯pvdf微滤膜,孔径为0.1-0.4μm。本实施例中,微滤膜组件5下方的渗透池4侧壁通过水泵(图中未画出)与调节池1的进水口连接,以对渗透池中工业废水再次进入调节池1,然后再进行絮凝和微滤。为了验证上述实施例的可行性,采用上述实施例的一种将絮凝和微滤膜结合进行处理工业废水的装置来处理电镀废水中的铜和镍,具体实验过程如下:采用的絮凝剂是:feso4和pac。实验所用的废水是:某公司电镀车间的电镀废水。处理前水质指标如表1所示。除此之外,再配制含有cu2+、ni2+离子均为50.0mg/l的水样。表1电镀废水水质指标(单位:mg/l)水样zncunifecaalcdmncodph1116.257.74380.414110.020.151.34232.51.94249.74031.97761155.9\1.10143.02.02采用的微滤膜是:实验采用的膜是聚偏氟乙烯pvdf微滤膜,大小为300×250×450毫米。所用的仪器和试剂有:搅拌仪、分光光度计、电子天平、烧杯、cuso4、niso4、naoh、七水合硫酸亚铁、聚合氯化铝、乙醇,碘、氨水、碘化钾等。使用上述将絮凝和微滤膜结合进行处理工业废水的装置,将工业废水送入调节池,然后进入事先加了絮凝剂的絮凝池里对工业废水进行絮凝操作,絮凝后的工业废水进入沉淀池进行沉淀,沉淀池上部的滤液进入渗透池经微滤膜组件进行过滤,由渗透池的出水口得到净水。由絮凝实验可验证得到feso4和pac絮凝剂分别在投加量为15、12.5mg/l和12.5、7.5mg/l时对cu2+、ni2+去除效果最好,对应的值为99.50%、93.15%和99.82%、92.03%;ph值为8.5、9.5时对铜离子和镍离子的絮凝效果最好。(1)混浊液和上清液对微滤膜过滤的影响比较试验分别量取两份12l水样1的电镀废水,调节ph值大约为8~9,各加入15ml的feso4溶液,其中一份快速搅拌,时间为1分钟,另一份慢速搅拌,时间为20分钟,等待絮凝沉淀后,设曝气量为0.2m3/h,再用孔径为0.1μm的微滤膜过滤,测定出水中cu2+、ni2+的含量。分别考查含有不同污泥浓度的混浊液和上清液对微滤膜过滤造成的影响。同种条件下,将feso4溶液替换成pac溶液,进行絮凝-微滤膜过滤实验。此时pac溶液的搅拌条件也变为15分钟慢速搅拌和1分钟快速搅拌。(2)不同预处理方式对膜截留率的影响分别量取三份12l水样1的电镀废水,一份用naoh调节调ph值、一份加入feso4絮凝剂、另一份加入pac絮凝剂,待絮凝沉淀后,取上清液分别加入到三个相同的膜反应器中,设置曝气量为0.2m3/h,然后用孔径为0.1μm的微滤膜过滤,出水后测算cu2+和ni2+的去除率。考查调ph后直接过滤和絮凝后再过滤两种方法的膜截留率比较。(3)微滤膜孔径对微滤膜截留率的影响分别量取四份12l水样1的电镀废水,调节废液的ph值为8.5左右,其中两份加入feso4溶液,另外两份加入pac溶液,待絮凝沉淀后,设置曝气量为0.2m3/h,再分别在同一种絮凝剂中使用孔径为0.1和0.4μm的微滤膜管过滤,分别测定不同孔径的膜对cu2+和ni2+的去除率。(4)微滤膜进水浓度对膜截留率的影响分别量取六份cu2+和ni2+浓度为50、500和1000mg/l的混合废水,每一份废水都在最适宜且相同的条件下加入絮凝剂絮凝沉淀后再用微滤膜进行过滤,各自测定微滤膜过滤进、出水中cu2+和ni2+的浓度并且推算出膜截留率。实验结果及其分析计算膜截留率r。式中:膜截留率用r表示,单位为%;重金属的离子浓度用c表示,单位为mg/l。计算膜渗透通量j。v=m/ρ(2)式中:渗透液的质量用m表示,单位为kg;渗透液的密度为ρ,单位为kg/m3;j为膜渗透通量,单位为m3/(m2*s);微滤膜的有效过滤面积设为a,单位为m2;时间为dt内废液透过的体积表示为dv,单位为m3;dt为膜过滤的时间间隔,单位为s。(1)上清液和混浊液对微滤膜过滤的影响比较试验的实验结果如表2和图3、4所示。表2是经不同絮凝剂絮凝后上清液和含有不同程度污泥浓度的混浊液进行膜过滤的结果比较;图3是上清液和混浊液过滤膜截留效果比较;图4是进水mlss浓度与出水cu和ni离子剩余浓度的关系。分析图3中cu2+和ni2+的去除率趋势线变化可以得知,加入最佳投加浓度的絮凝剂絮凝后,上清液过滤的膜截留率明显低于混浊液过滤的膜截留率。同时,由图4和5可以得知,出水cu和ni离子的浓度随着mlss(混合液污泥浓度)的增大先降低,然后趋于平缓,后又继续增大。因为随mlss增大,在一样曝气量的情况下对膜表面的剪切能力会逐渐减低,细小颗粒等就很容易被截留,进而积淀在膜的表面逐渐形成一层凝胶层,凝胶层会越来越厚,使得膜通量慢慢地降低,甚至导致膜孔堵塞,大大增加了渗透阻力,最后会增加出水时间或者导致不出水。所以在实验过程中,废水的mlss浓度范围应选为0.5~1.0g/l效果最好。表2上清液和混浊液过滤试验结果(2)调ph后直接过滤和絮凝后再过滤两种方法的膜截留率比较分析图6可知,图中,a表示调ph值后过滤,b表示feso4絮凝剂絮凝后过滤,c表示pac絮凝剂絮凝后过滤;废水调ph值后直接过滤的效果并不如加絮凝剂絮凝后再过滤的效果好,且用feso4絮凝后再经微滤膜过滤的cu和ni离子去除率比用pac絮凝后再过滤的离子去除率要高。所以,使用feso4絮凝剂比氢氧化物调节ph和pac絮凝剂更容易截留重金属离子。同时可以发现使用feso4絮凝再过滤后,镍的去除率为34.5%左右,铜的去除率为62%左右,由此可知不同颗粒大小、物理化学特性的污染物,可能因种种因素而导致膜的去除率不同。(3)微滤膜孔径对膜截留率的影响由图7可知,当电镀废水絮凝沉淀后通过孔径分别为0.1μm和0.4μm的微滤膜,发现0.1μm孔径的膜出水澄清、颜色较浅、呈黄色;0.4μm孔径的膜出水相对较浑浊,颜色比较深。电镀废水用pac絮凝后,使用孔径为0.1μm的膜过滤截留效果明显好于0.4μm孔径的膜,使用feso4絮凝后再经不同孔径的膜过滤对cu和ni离子的去除效果不太明显,这是因为feso4絮凝剂絮凝后形成的絮体较大,亦可以被孔径为0.4μm的微滤膜截留。(4)膜进水浓度对膜截留率的影响分析表3中可知,絮凝过滤后废水中剩余的ni2+浓度随初始浓度的升高而越来越高,但是对比进水浓度和出水浓度可以发现膜的截留效率基本与进水浓度无直接联系。如图8所示,膜对铜和镍离子的截留效率平均在61%和42%左右,随进水浓度变化不明显。因此进水浓度在1000mg/l以下的范围下,进水浓度对膜截留率并无太大的影响。表3不同浓度条件下微滤膜过滤效果(说明:絮凝后上清液的浓度即膜的进水浓度)通过上述实验数据,分析两种絮凝剂的综合收益,如表4所示。由表4可知,在适宜的ph条件下,pac絮凝剂与feso4絮凝剂对铜和镍离子的去除率差距并不明显,而且pac絮凝后污泥产生量比feso4要多。feso4的ph值范围与pac也相差无几,在色度和cod去除方面也有相对明显的效果。另外市场上feso4比pac价格更低,所以考虑污泥产生量、重金属离子去除率、价格等方面的综合收益,选择feso4为絮凝剂更符合经济实用性原则。表4feso4和pac综合情况比较综述,本发明将微滤膜分离技术与化学絮凝、沉淀技术相结合,对工业废水的净化效果好,能扬长避短,最大限度发挥各自的优势,是今后微滤膜分离技术的发展趋势。本发明的技术方案不限于上述具体实施例的限制,凡是根据本发明的技术方案做出的技术变形,均落入本发明的保护范围之内。当前第1页12