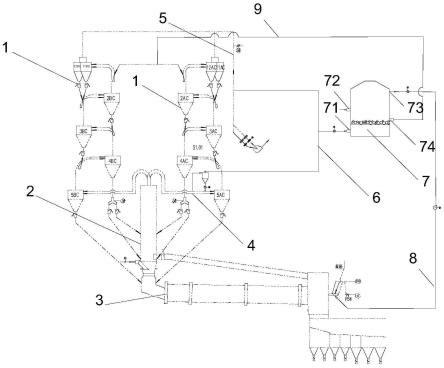
1.本发明属于废弃物处置及资源化利用领域,尤其是涉及一种利用水泥窑高效资源化处置油泥的系统和方法。
背景技术:2.含油污泥已被国家列为危险废物。油泥中有机污染物来源于原油中的油分,而无机污染物主要包括无机盐和重金属,此外还有大量病原菌和寄生虫等,会对土壤、水体、大气环境产生污染,甚至会通过食物链进入人体。由于产生量大、成分复杂、处理难度大,油泥处理一直是困扰石油石化行业的难题。另外,油泥中含有大量的石油类资源,可回收原油实现资源化利用。
3.当前油泥处理技术普遍存在适用范围窄,处理成本高的问题,导致油泥处理率较低;同时这些技术对回收油之后的残渣缺乏考虑,因此一些技术只适用于油泥的预处理,必须辅以深度处理方法,才能满足危废填埋的入场标准要求。热解法油品回收率高、三相产物均可再利用,适用于各种油泥,有较大的应用前景。发改委《战略性新兴产业重点产品和服务指导目录(2016版)》中鼓励发展“油泥回转式连续低温热解装备”;三部委在《国家鼓励发展的重大环保技术装备(2020年版)》中再次说明含油污泥热解处理装备被列入应用类,污油泥热分解处理成套装备被列入推广类。
4.含油污泥的种类较多、性质较为复杂,相对应的处理工艺技术和设备装置也呈现多元化。常用技术包括:调质机械分离、萃取、热裂解、热脱附、水泥窑协同处置等。油泥无害化的处理技术主要包括焚烧、填埋、固化技术等。热解技术作为一种新型方法优势非常明显,其回收的甲烷、二氧化碳、乙烷等气体以及柴油等液态回收物作燃料是利用含油污泥中所含能源的一种综合利用方式,是含油污泥处理的主流方向之一。目前,热解系统温度高,耗能大以及回收油、处置能力提升以及处理成本降低仍是热解技术需要解决的难题。水泥窑协同处置技术利用水泥窑内温度高、热容量大、工况稳定、停留时间长等特点,在不影响水泥正常生产和质量的前提下,可同步实现油泥的无害化焚烧处置,一般是通过配伍-调质-泵送技术路线处置各类含油污泥,主要以无害化处置为主,资源化利用程度不高。
5.综上所述,现有技术存在的问题是:
6.(1)油泥热解需要配置氮气等惰性氛围,同时油品类气相产物需要冷凝、净化处理。
7.(2)水泥窑协同处置只是将油泥通过配伍便于输送后,直接送至分解炉等高温区,对水泥窑热工系统冲击较大,且只是单纯将油泥处置而未资源化利用。
技术实现要素:8.针对现有技术存在的上述技术问题,本发明公开了一种利用水泥窑高效资源化处置油泥的系统和方法。
9.本发明的第一目的在于提供了一种利用水泥窑高效资源化处置油泥的系统,该水
泥窑包括依次连接的五级预热器、分解炉和回转窑;所述分解炉上设有鹅颈管,五级预热器上设有废气总管;所述系统包括油泥热解配气单元、油泥热解单元、油泥热解气高效利用单元和油泥渣资源化利用单元;
10.所述油泥热解配气单元由水泥窑废气总管出口和鹅颈管出口汇合后的管路形成,为油泥热解单元提供热解必须的温度和气氛条件;鹅颈管处气体经过旋风筒除尘,水泥生料粉尘回取气处;
11.所述油泥热解单元为置有油泥的固定床,用于将油泥在250℃~500℃低温条件下热解;所述固定床包括气体入口、油泥入口、热解气出口、油泥热解产物出口;即油泥通过油泥入口进入固定床的反应区,气体入口与油泥热解配气单元连接以获得热解气,反应后的热解气经热解气出口排出;在固定床内加入蓄热料,待热解单元温度升至250℃~500℃后继续维持1~2小时后卸料;
12.所述油泥热解气高效利用单元包括与油泥热解气出口连接的管路,管路末端与回转窑头罩上的煤粉入口连接,从而将油泥热解后的烃类热解气送至回转窑当燃料重复利用;
13.所述油泥渣资源化利用单元包括连接在油泥热解产物出口与五级预热器之间的相应管路,用于将无需粉磨的油泥热解渣,直接送至水泥生料端即五级预热器的c1级旋风筒之前,进而参与水泥的配料。
14.进一步的,所述油泥热解配气单元提供的气体满足以下条件:
[0015][0016]
caρaqa(t
a-t)+cbρbqb(t
b-t)=m(1-m)cm(t-20)+80mmcw+rmm+mmrq(t-100)
[0017]
其中,废气总管中氧气系数;qa:废气总管取气量;
[0018]
鹅颈管中氧气系数;qb:鹅颈管取气量;
[0019]
ca:废气总管中气体比热容;ρa:废气总管中气体密度;ta:废气总管气体温度;
[0020]
cb:鹅颈管中气体比热容;ρb:鹅颈管中气体密度;tb:鹅颈管气体温度;
[0021]
m:油泥质量;m:油泥含水率;cm:油泥干基比热容;cw:水的比热容;r:水蒸气汽化潜热;rq:水蒸气的比热容;t:热解单元控制温度。
[0022]
进一步的,所述热解气出口、油泥热解产物出口均与油泥入口相对设置,且热解气出口位于油泥热解产物出口的上方。
[0023]
进一步的,所述蓄热料为卵石、钛铁矿石、磁铁矿石、金刚砂;粒度满足:d
10
=0.9~1.5mm,其中,d
10
指有10wt%的蓄热料能通过的筛孔孔径;d
80
指有80wt%的蓄热料能通过的筛孔孔径。满足d
10
和k
80
要求的蓄热料大小均匀、具有较大的比表面积,鼓泡或者流化效果较好,可以提高油泥的热解效率。
[0024]
本发明的另一目的在于提供了一种利用水泥窑高效资源化处置油泥的方法,包括如下步骤:
[0025]
a、分别在油泥热解配气单元的水泥窑窑尾废气总管和鹅颈管出口处取气体输送至热解单元,鹅颈管处气体经过旋风筒除尘,水泥生料粉尘回取气处;
[0026]
所取气体满足以下公式:
[0027][0028]
caρaqa(t
a-t)+cbρbqb(t
b-t)=m(1-m)cm(t-20)+80mmcw+rmm+mmrq(t-100);
[0029]
废气总管中氧气系数;qa:废气总管取气量;
[0030]
鹅颈管中氧气系数;qb:鹅颈管取气量;
[0031]
ca:废气总管中气体比热容;ρa:废气总管中气体密度;ta:废气总管气体温度;
[0032]
cb:鹅颈管中气体比热容;ρb:鹅颈管中气体密度;tb:鹅颈管气体温度;
[0033]
m:油泥质量;m:油泥含水率;cm:油泥干基比热容;cw:水的比热容;r:水蒸气汽
[0034]
化潜热;rq:水蒸气的比热容;t:热解单元控制温度;
[0035]
b、油泥热解单元内部装有蓄热料,待油泥热解单元温度升至250-500℃后继续维持1-2小时后卸料,过程中部分难热解的残留物通过与蓄热料的相互碰撞粒径变小继续热解,同时对残留物也起到了粉磨的作用。
[0036]
c、热解气输送至回转窑作为高品位燃料使用;
[0037]
d、在五级预热器的c1级旋风筒之前均匀加入热解渣,该热解渣无需粉磨,参与到水泥窑的配料中。
[0038]
本发明具有的优点和积极效果是:
[0039]
本发明利用油泥热解产生的烃类物质供给水泥窑作为燃料,过程中不需冷凝及净化处理,同时热解气燃烧后与水泥窑气氛一起部分提取作为油泥热解需要的惰性氛围,无需再增加氮气等提供所需的缺氧条件;油泥热解渣由于含油量少,可参与水泥生料配料,杜绝了水泥窑协同处置油泥时对窑系统的冲击。
附图说明:
[0040]
图1是本发明的利用水泥窑高效资源化处置油泥的系统示意图。
[0041]
图中;1、五级预热器;2、分解炉;3、回转窑;4、鹅颈管;5、废气总管;6、油泥热解配气单元;7、油泥热解单元;71、气体入口;72、油泥入口;73、热解气出口;74、油泥热解产物出口;8、油泥热解气高效利用单元;9、油泥渣资源化利用单元。
具体实施方式
[0042]
下面将对本发明实施例中的技术方案进行清楚、完整地描述;显然;所描述的实施例仅仅是本发明一部分实施例;而不是全部的实施例。基于本发明中的实施例;本领域普通技术人员在没有做出创造性劳动前提下所获得的所有其他实施例;都属于本发明保护的范围。
[0043]
实施例1
[0044]
本实施例提供了一种利用水泥窑高效资源化处置油泥的系统,该水泥窑包括依次连接的五级预热器1、分解炉2和回转窑3;所述分解炉2上设有鹅颈管4,五级预热器1上设有废气总管5;本发明的系统是在该水泥窑的基础上设置油泥热解配气单元6、油泥热解单元7、油泥热解气高效利用单元8和油泥渣资源化利用单元9;
[0045]
所述油泥热解配气单元6由水泥窑废气总管出口和鹅颈管出口汇合后的管路形成,主要为油泥热解单元提供热解必须的温度和气氛条件;鹅颈管处气体经过旋风筒除尘,
水泥生料粉尘回取气处。气体满足以下条件:
[0046][0047]
caρaqa(t
a-t)+cbρbqb(t
b-t)=m(1-m)cm(t-20)+80mmcw+rmm+mmrq(t-100)
[0048]
废气总管中氧气系数;qa:废气总管取气量
[0049]
鹅颈管中氧气系数;qb:鹅颈管取气量
[0050]
ca:废气总管中气体比热容;ρa:废气总管中气体密度;ta:废气总管气体温度
[0051]
cb:鹅颈管中气体比热容;ρb:鹅颈管中气体密度;tb:鹅颈管气体温度
[0052]
m:油泥质量;m:油泥含水率;cm:油泥干基比热容;cw:水的比热容;r:水蒸气汽化潜热;rq:水蒸气的比热容;t:热解单元控制温度
[0053]
所述油泥热解单元7具体为置有油泥的固定床,主要用于将油泥在250℃~500℃低温条件下热解;所述固定床包括气体入口71、油泥入口72、热解气出口73、油泥热解产物出口74;即油泥通过油泥入口72进入固定床的反应区,气体入口71与油泥热解配气单元6连接以获得热解气,反应后的热解气经热解气出口73排出;具体的,所述热解气出口73、油泥热解产物出口74均与油泥入口72相对设置,且热解气出口73位于油泥热解产物出口74的上方;为减轻油泥在热解过程中团聚现象,在固定床内加入蓄热料,待热解单元温度升至250℃~500℃后继续维持1~2小时后卸料,蓄热料为卵石、钛铁矿石、磁铁矿石、金刚砂等耐磨稳定性物质,在热解过程中蓄热料不停与难热解的油泥残留物摩擦,使得残留物粒径变小继续热解,提高热解效率的同时还能将油泥热解渣粒度降至水泥生料程度。具体的,蓄热料的粒度满足:d
10
=0.9~1.5mm,其中,d
10
指有10wt%的蓄热料能通过的筛孔孔径;d
80
指有80wt%的蓄热料能通过的筛孔孔径。满足d
10
和k
80
要求的蓄热料大小均匀、具有较大的比表面积,鼓泡或者流化效果较好,可以提高油泥的热解效率。
[0054]
所述油泥热解气高效利用单元8包括与油泥热解气出口73连接的管路,管路末端与回转窑窑头罩上的煤粉入口连接,从而将油泥热解后的烃类热解气送至回转窑当燃料重复利用。
[0055]
所述油泥渣资源化利用单元9包括连接在油泥热解产物出口74与五级预热器之间的相应管路,主要是将无需粉磨的油泥热解渣,直接送至水泥生料端即五级预热器的c1级旋风筒之前,进而参与水泥的配料。
[0056]
实施例2:
[0057]
本实施例公开了采用实施例1的系统高效利用油泥的方法,包括如下步骤:
[0058]
a、分别在油泥热解配气单元6的水泥窑废气总管和鹅颈管出口处取气体输送至热解单元7,鹅颈管处气体经过旋风筒除尘,水泥生料粉尘回取气处。
[0059]
所取气体满足以下公式:
[0060][0061]
caρaqa(t
a-t)+cbρbqb(t
b-t)=m(1-m)cm(t-20)+80mmcw+rmm+mmrq(t-100);
[0062]
废气总管中氧气系数;qa:废气总管取气量;
[0063]
鹅颈管中氧气系数;qb:鹅颈管取气量;
[0064]
ca:废气总管中气体比热容;ρa:废气总管中气体密度;ta:废气总管气体温度;
[0065]
cb:鹅颈管中气体比热容;ρb:鹅颈管中气体密度;tb:鹅颈管气体温度;
[0066]
m:油泥质量;m:油泥含水率;cm:油泥干基比热容;cw:水的比热容;r:水蒸气汽化潜热;rq:水蒸气的比热容;t:热解单元控制温度。
[0067]
b、油泥热解单元内部装有粒度要求满足d
10
=0.9mm,k
80
<2.0的蓄热料,待油泥热解单元温度升至250℃后继续维持2小时后卸料,过程中部分难热解的残留物通过与蓄热料的相互碰撞粒径变小继续热解,同时对残留物也起到了粉磨的作用。
[0068]
c、热解气(主要含烃类物质)输送至水泥窑窑头作为高品位燃料使用;
[0069]
d、在五级预热器的c1级旋风筒之前均匀加入热解渣,该热解渣无需粉磨,参与到水泥窑系统的配料中。
[0070]
实施例3:
[0071]
本实施例公开了采用实施例1的系统高效利用油泥的方法,包括如下步骤:
[0072]
a、分别在水泥窑窑尾废气总管和鹅颈管处取气体输送至热解单元,鹅颈管处气体经过旋风筒除尘,水泥生料粉尘回取气处。气体满足以下条件:
[0073][0074]
caρaqa(t
a-t)+cbρbqb(t
b-t)=m(1-m)cm(t-20)+80mmcw+rmm+mmrq(t-100)
[0075]
废气总管中氧气系数;qa:废气总管取气量;
[0076]
鹅颈管中氧气系数;qb:鹅颈管取气量;
[0077]
ca:废气总管中气体比热容;ρa:废气总管中气体密度;ta:废气总管气体温度;
[0078]
cb:鹅颈管中气体比热容;ρb:鹅颈管中气体密度;tb:鹅颈管气体温度;
[0079]
m:油泥质量;m:油泥含水率;cm:油泥干基比热容;cw:水的比热容;r:水蒸气汽化潜热;rq:水蒸气的比热容;t:热解单元控制温度。
[0080]
b、油泥热解单元内部装有粒度要求满足d
10
=1.5mm,k
80
<2.0的蓄热料,待热解单元温度升至500℃后继续维持1小时后卸料,过程中部分难热解的残留物通过与蓄热料的相互碰撞粒径变小继续热解,同时对残留物也起到了粉磨的作用。
[0081]
c、热解气(主要含烃类物质)输送至水泥窑窑头作为高品位燃料使用;
[0082]
d、在五级预热器的c1级旋风筒之前均匀加入热解渣,该热解渣无需粉磨,参与到水泥窑系统的配料中。
[0083]
以上对本实施例进行了详细说明,但所述内容仅为本发明的较佳实施例,不能被认为限定本发明的实施范围。凡依本发明申请范围所作的均等变化与改进,均应仍归属于本发明的专利涵盖范围之内。