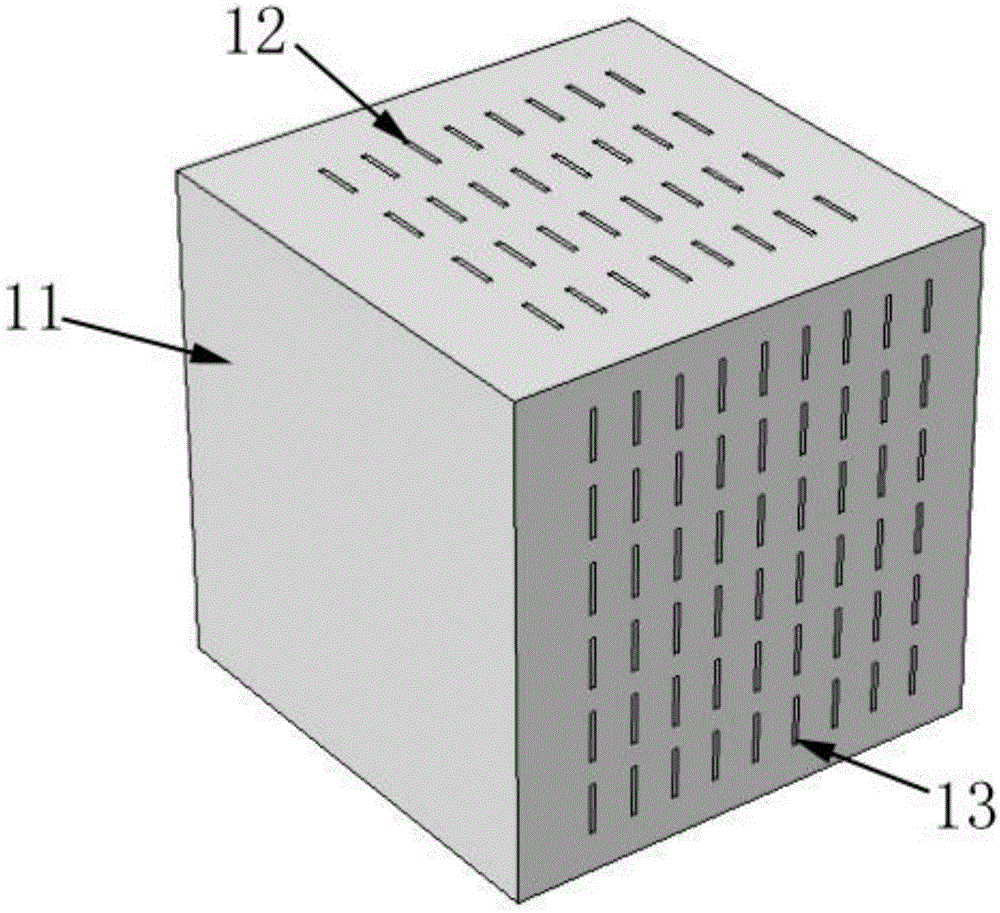
本发明涉及一种费托合成催化剂的再生方法,更具体地说,是一种基于微通道反应器的钴基费托合成催化剂的再生方法。
背景技术:
:微通道反应技术是二十一世纪化学工程学科的新技术之一,具有常规反应器不可比拟的优势,例如:反应通道为微米级别,表面积大,反应器具有很高的传质和传热速率,单位体积反应器反应负荷高,工程放大简单。而对于一些强放热催化反应,例如费托合成反应、加氢裂化反应,加强催化剂层的传热,控制反应的温度平稳是取得好的反应效果的前提和保证。利用微通道反应技术,可以实现高活性催化剂在等温条件反应,既克服了传统反应器传质扩散影响大、传热效果差的缺点。费托合成反应进行一段时间以后,由于催化剂表面形成积碳、活性金属被氧化、大分子覆盖活性中心等因素,使催化剂性能下降,需要对催化剂进行再生以恢复其性能。特别是对于微通道反应器,催化剂的装填和涂覆较为复杂,与传统的固定床和浆态床相比,需要更长的运转周期和催化剂寿命,催化剂再生不仅降低催化剂成本和运转成本,还能够减少因催化剂回收处理带来的消耗和环境污染。针对不同的费托合成工艺,研究人员已经开发了多种再生方法。针对浆态床费托合成催化剂再生,由于反应条件限制,离线再生是普遍采用的方式,一般包括脱蜡、氧化脱碳和还原等步骤,例如:在中国专利cn101844093b、cn101688125b中提出了一种用于浆态床反应的颗粒状催化剂的再生方法,包括脱蜡处理、氧化处理和还原处理等过程,其脱蜡过程采用二甲苯进行溶剂洗涤后再干燥的工艺。中国专利cn101703937b提出了一种浆态床费托合成催化剂的再生方法,催化剂需要经历萃取、气提、氧化和还原过程。催化剂脱蜡采用c7~c12的烷烃进行萃取,然后气提干燥。中国专利cn102791377b公开了一种费托合成催化剂的再生方法,催化剂首先经过链烷烃的洗涤脱油,再经5mpa的蒸汽处理,可以得到较好的再生效果。美国专利us4399234公开了一种催化剂的再生方法,主要过程是将催化剂在高温下与含氧气体或蒸汽接触,再生后的催化剂再通过含氢气体在高温下还原活化。美国专利us2369956公开了一种费托合成催化剂的再生方法,其采用酸将催化剂活性金属溶解,然后通过再沉淀催化剂金属以恢复催化剂。这种方法对于各种原因的催化剂失活均有效果,但会破坏催化剂结构,影响活性金属与载体和活性金属与助剂之间的相互作用,而且操作复杂,催化剂再生需要在其他专门设备中进行。中国专利cn102259036b公开了一种在线再生催化剂的方法,用于固定床费托合成催化剂再生,反应器中催化剂经过吹扫、溶剂洗涤、氧化和还原而得到性能恢复。从现有技术可以看出,在费托合成催化剂再生过程中,费托合成催化剂上的脱蜡步骤是主要采用溶剂洗涤,但溶剂洗涤过程,一方面对溶剂的要求很高,如对溶剂中硫、氮、氧、金属等杂质含量都有严格要求,以防止污染催化剂。另一方面,溶剂洗涤过程和洗涤后的含蜡溶剂再处理过程都是能耗和物耗较高的过程。技术实现要素:本发明的目的是提供一种用于微通道反应器的费托合成催化剂的再生方法。以解决现有技术中,再生过程能耗大和物耗高的技术问题。本发明所提供的再生方法,包括:(1)用惰性气体置换反应器内合成气,(2)反应器内通入氢气,在氢气气氛中,在裂化反应条件下,费托合成催化剂吸附的大分子烃类发生裂化反应,得到甲烷和轻烃,(3)步骤(2)处理后的费托合成催化剂接触含氧气体,在氧化条件下进行氧化,(4)步骤(3)氧化后的费托合成催化剂接触含氢气体进行还原,得到再生后费托合成催化剂,所述的费托合成催化剂为钴基负载型费托合成催化剂,在微通道反应器内,填充或涂覆所述的钴基负载型费托合成催化剂。所述的微通道反应器是指具有多列通道结构的反应器,通道呈层状结构平行和/或交错排布,通道用于装填、涂覆催化剂或者流通导热介质,本发明所述的微通道为宽度或深度尺寸在1000微米以下的孔道,通道长度超过1厘米。在本发明其中一种实施方式中,所述的微通道反应器内设置两种通道,即反应通道和导热介质通道。反应通道内填充或涂覆所述的钴基负载型费托合成催化剂,发生费托合成反应;导热介质通道流通气相或者液相的导热介质,用于导出反应热或者加热反应器。反应通道和导热介质通道交替设置,相互隔离,物料流通方向可并流、错流、或成一定角度(例如90度)。所述的在微通道反应器中的费托合成反应,反应条件为:压力为1~5mpa,温度为150~300℃,气时空速为1000~100000h-1,原料气中h2与co体积比为1~3,循环气与新鲜原料气比例为0.1~10,优选为:反应压力为2~4mpa,温度为180~250℃,气时空速为2000~40000h-1,原料气中h2与co比例为1.8~2.5,循环气与新鲜原料气比例为0.5~6。反应过程中需要在微通道反应器的导热介质通道通入介质导出热量,导热介质可以是气相,如空气、n2、h2、co2、水蒸汽等,也可以是液相,如水、导热油等。所述钴基负载型费托合成催化剂包含活性组分钴、助剂和载体,助剂选自过渡金属、稀土金属和非金属元素中的一种或几种,载体选自al2o3、sio2、tio2、zro2、分子筛中的一种或几种,以重量计,钴的含量为10%~50%。所述的钴基负载型费托合成催化剂是由共沉淀、浸渍、喷雾方法任一方法所制备。所述的钴基负载型费托合成催化剂为粉末时,装填在微通道反应器的反应通道中,或者采用壁载方式,将钴基负载型费托合成催化剂涂覆在反应通道的内壁或者支撑体上。支撑体可以是不锈钢网、不锈钢板、陶瓷板等具有一定强度的任何反应惰性物体。本发明所提供的再生方法其中一种实施方式中,在步骤(1)中用惰性气体置换反应器内合成气,所述的惰性气体选自n2、ar、he中的一种或几种,优选为n2,通入惰性气体的空速为2000~20000h-1,优选为5000~10000h-1。在通入惰性气体的同时,将反应器温度降低至180℃以下,优选降低至150℃。本发明所提供的再生方法其中一种实施方式中,在步骤(2)中,通入氢气的空速为2000h-1~8000h-1,优选为3000h-1~5000h-1,反应器压力为0.5mpa~10mpa,优选为1.0mpa~8.0mpa。步骤(2)中反应器内温度控制过程为:升温至200℃~300℃,恒温2h~10h,升温至300℃~450℃,恒温至排放气中甲烷含量低于1体积%时,降低反应器内温度,降至50℃。进一步优选升温至340℃~400℃,恒温至排放气中甲烷含量低于1体积%时,降低反应器内温度。升温速率不大于40℃/h,优选不大于30℃/h。在此过程中,费托合成催化剂吸附的大分子烃类发生裂化反应,得到甲烷和轻烃。优选,步骤(2)处理后的费托合成催化剂接触含氧气体前,通入惰性气体进行吹扫,吹扫合格后的费托合成催化剂接触含氧气体,所述的惰性气体选自n2、ar、he中的一种或几种;当驰放气中可燃气(h2+总烃)的体积分数小于0.1%时,视为吹扫合格。本发明所提供的再生方法其中一种实施方式中,步骤(3)中,在反应器温度低于50℃~80℃、压力0.5mpa~2.0mpa下,费托合成催化剂接触含氧气体,反应器入口含氧气体中氧体积分数为0.5%~2%。反应器通入含氧气体后,待反应器没有温度变化后,逐步提高反应器温度至400℃~450℃,升温速率不大于40℃/h,优选不大于30℃/h。待驰放气中co+co2含量不变后,提高含氧气体中氧体积分数,反应器入口含氧气体中氧体积分数为5%~15%;待驰放气中co+co2体积含量<0.05%后氧化结束。所述的费托合成催化剂氧化的目的是在可控范围内将费托合成催化剂的金属和表面积炭等有机物转变为金属氧化物和碳氧化物,因此在不损坏费托合成催化剂的前提下,任何氧化方式都可采用。本发明优选的含氧气体选自氧气和/或空气与惰性气体或水蒸汽的混合气体。具体地说,含氧气体可以是氧气和/或空气与惰性气体的混合气体,也可以是氧气和/或空气与水蒸汽的混合气体。进一步优选为氧气与惰性气体的混合气体。所述的步骤(2)裂化过程和步骤(3)氧化过程均为放热过程,优选在微通道反应器的导热介质通道通入导热介质以导出热量,所述的导热介质为气相:选自空气、n2、h2、co2、水蒸汽中的一种或几种,或者为液相:水或导热油。优选,步骤(3)氧化后的费托合成催化剂接触含氢气体前,通入惰性气体进行吹扫,吹扫合格后的费托合成催化剂接触含氢气体,所述的惰性气体选自n2、ar、he中的一种或几种;当驰放气中氧气的体积分数小于0.1%时,视为吹扫合格。本发明所提供的再生方法其中一种实施方式中,步骤(4)中,反应器内通入含氢气体,所述含氢气体中氢气的体积分数不大于10%,优选不大于5%,通入含氢气体的空速为500~5000h-1,优选1500~3000h-1,反应器温度为350℃~500℃,优选350℃~450℃,升温速率不大于60℃/h,优选不大于40℃/h,压力为0~2.0mpa,优选0~1.0mpa,反应器各点最大温差不大于5℃,优选不大于3℃。测量排放气中水含量,待小于5mg/l,优选小于2mg/l,提高含氢气体中氢气的体积分数为30%~60%,优选40%~50%,并恒温2~20h。本发明所述的催化剂再生过程可以在费托合成装置原位进行,也可以将带有催化剂的微通道反应器卸载后在专用装置进行。本发明与现有技术相比,具有以下优点:(1)利用钴基负载型费托合成催化剂的特性,实现了原位再生,并结合了微通道反应器特点和钴基负载型费托合成催化剂的裂化性能,在优化的再生条件下,使强放热的裂化反应在微通道反应器中可控发生,既避免了裂化反应放热对催化剂结构的破坏,也避免了催化剂大量积炭的产生,同时省略了溶剂洗涤步骤,有效降低了再生过程的物耗和能耗。(2)本发明提供的再生方法,对钴基负载型费托合成催化剂损害小,操作简便易于实现,无新增设备,再生后钴基负载型费托合成催化剂性能恢复好。附图说明图1为本发明微通道反应器其中一种实施方式结构示意图。图中编号11为微通道反应器,12为反应通道,13为导热介质通道。图2为本发明微通道反应器另一种实施方式结构示意图。图中编号21为微通道反应器,22为反应通道,23为导热介质通道。具体实施方式下面的实施例对本发明提供的方法予以进一步说明,但并不因此而限制本发明。实施例1如图1所示,微通道反应器11包含8层并排排列的反应通道12和9层并排排列的导热介质通道13,每条反应通道宽10mm、高1mm、长100mm,每层有4条反应通道12。每条导热介质通道宽10mm、高1mm、长100mm,每层有6条导热介质通道13。反应通道12和导热介质通道13呈90°交叉。在反应通道12中装填钴基负载型费托合成催化剂。本实施例中所用的钴基负载型费托合成催化剂的制备过程如下:取氧化铝粉,滴加蒸馏水至初润湿,记下消耗水的体积,然后按co含量(氧化物计)27重量%计算,配制出硝酸钴浸渍液,然后按re含量(氧化物计)0.1重量%计算,配制出高铼酸浸渍液。接着以此溶液浸渍氧化铝至初润湿,静置8小时,然后于120℃干燥4小时,在马福炉内450℃焙烧4小时,制得钴基负载型费托合成催化剂。所述钴基负载型费托合成催化剂粒度范围为50μm~200μm。制备好的钴基负载型费托合成催化剂装填在反应通道中,在0.1mpa下,在氮气气氛中,气体空速为1000h-1条件下,以30℃/h升温速率将反应器升温到120℃,在升温过程中反应器各点最大温差不大于1℃,恒温8h;恒温结束后通入氢氮混合气(氢气体积分数为5%)、气体空速为3000ml/ml催化剂/h,以指定速率10℃/h升温到280℃,在升温过程中反应器各点最大温差不大于2℃,温度升到后恒温12h。恒温结束后通入氢氮混合气(氢气体积分数为5%)、气体空速为2000ml/ml催化剂/h,以指定速率20℃/h升温到400℃,在升温过程中反应器各点最大温差不大于3℃,温度升到恒温6h后检测排放气体中水分含量为2mg/l,增加氢氮混合气氢气体积分数为40%,6h后检测排放气体中水分含量为2mg/l,改为纯氢气进料,恒温6h时后还原结束,开始以30℃/h降温。还原后的钴基负载型费托合成催化剂在反应条件:压力3.0mpa,温度220℃,合成气(原料气)组成为h2体积分数60%,co体积分数30%,n2体积分数10%,空速20000ml/ml催化剂/h,进行费托合成反应,产品由气相色谱进行分析,计算co的转化率、甲烷选择性和c5+烃类选择性。反应一段时间后,钴基负载型费托合成催化剂需要进行再生。首先切出合成气原料切入n2置换反应器,气时空速6000ml/ml催化剂/h,12小时后以20℃/h的速率降低催化剂床层温度至160℃。切入氢气,气时空速3000ml/ml催化剂/h,设定氢分压为4.5mpa,以升温速率10℃/h升温至280℃,升温过程检测排放气中甲烷含量;甲烷含量开始降低后,以升温速率20℃/h升温至400℃;排放气中甲烷含量低于1%时,以20℃/h的速率降低反应器温度至50℃,加氢裂化过程结束。切出氢气切入氮气,置换至驰放气中可燃气(h2+总烃)体积分数小于0.1%;在氮气中配入一定比例的空气,使反应器入口含氧气体中氧的体积分数为1%,催化剂因发生氧化反应温度上升至85℃,待反应器没有温度变化后,以每小时25℃逐步提高反应器温度至400℃。400℃恒温5h后,将反应器入口含氧气体中氧的体积分数增加为5%,恒温5h后,切换为空气恒温10h,当驰放气中co2体积分数<0.05%时氧化结束,以每小时30℃速度反应器降温至150℃。切出含氧气体切入氮气,置换至驰放气中氧气体积分数小于0.1%后切入含体积分数2%氢的氢氮混合气,气体空速为3000ml/ml催化剂/h,以20℃/h的速率降低催化剂床层温度至400℃,在升温过程中反应器各点最大温差不大于3℃,温度升到恒温6h后检测排放气体中水分含量为2mg/l,增加氢氮混合气氢气体积分数为40%,6h后检测排放气体中水分含量为2mg/l,改为纯氢气进料,恒温6h时后还原结束,开始以30℃/h降温,钴基负载型费托合成催化剂再生过程结束。再生后的钴基负载型费托合成催化剂在相同条件下进行费托合成性能测试,与新鲜催化剂、再生前催化剂性能对比结果在表1中列出。实施例2如图2所示,微通道反应器21包含8层并排排列的反应通道22和9层并排排列的导热介质通道23,每条反应通道22宽20mm、高1mm、长100mm,每层有3条反应通道22。每条导热介质通道23宽10mm、高1mm、长100mm,每层有6条导热介质通道23。反应通道22和导热介质通道23呈90°交叉。在反应通道22中装填涂覆了钴基负载型费托合成催化剂的催化剂支撑体。本实施例中所用的钴基费托合成催化剂为涂覆式整体催化剂,制备过程如下:钴基负载型催化剂涂覆于经过处理的波浪型不锈钢支撑体上,支撑体宽18mm、高0.8mm、长90mm。支撑体在丙酮溶液中超声波震荡30min,去除表面污垢。按照8%al粉、5%fe、3%nh4cl,其余为氧化铝,配成渗铝剂。将渗铝剂和不锈钢支撑体混合在一起,在850℃下焙烧120min。制成表面富含铝的不锈钢支撑体。在丙酮溶液中超声波震荡45min,去除表面污垢,以2.0℃/min的升温速度升温到500℃的焙烧120min,制备出表面富含氧化铝的不锈钢片。将硝酸和拟薄水铝石按照摩尔比h+/al3+=0.12进行混合,在70℃下搅拌1.0小时后,反应陈化12小时,得到陈化后的氧化铝溶胶;把溶胶和20%的聚乙二醇混合,搅拌成均匀浆液,按照滴加浸渍法进行涂敷。涂覆完成后,室温下干燥3小时,然后在120℃干燥3小时,升温速率0.5℃/min。干燥后涂敷件可以放入马弗炉中焙烧,焙烧温度为700℃,升温速率为0.8℃/min,时间为3小时,自然冷却至室温取出试样。将涂敷载体件放入含硝酸钴和偏钨酸铵的混合溶液进行饱和浸渍,之后进行干燥和焙烧。其中,干燥温度为120℃,干燥时间为3小时,焙烧温度为350℃,焙烧时间3小时。所述硝酸钴的用量使最终费托合成催化剂中氧化钴含量为45重量%,钨助剂含量约为2重量%。制备好的钴基费托合成催化剂支撑体插入反应通道中,在0.1mpa下,在氮气气氛中,气体空速为1000ml/g催化剂/h条件下,以指定速率30℃/h升温到120℃,在升温过程中反应器各点最大温差不大于1℃,恒温8h;恒温结束后通入氢氮混合气(氢气体积分数为5%)、气体空速为3000ml/g催化剂/h,以指定速率10℃/h升温到280℃,在升温过程中反应器各点最大温差不大于2℃,温度升到后恒温12h。恒温结束后通入氢氮混合气(氢气体积分数为5%)、气体空速为2000ml/g催化剂/h,以指定速率20℃/h升温到400℃,在升温过程中反应器各点最大温差不大于3℃,温度升到恒温6h后检测排放气体中水分含量为2mg/l,增加氢氮混合气氢气体积分数为40%,6h后检测排放气体中水分含量为2mg/l,改为纯氢气进料,恒温6h时后还原结束,开始以30℃/h降温。还原后的钴基负载型费托合成催化剂在反应条件:压力3.0mpa,温度220℃,合成气(原料气)组成为h2体积分数60%,co体积分数30%,n2体积分数10%,空速20000ml/g催化剂/h,进行费托合成反应,产品由气相色谱进行分析,计算co的转化率、甲烷选择性和c5+烃类选择性。反应一段时间后,钴基负载型费托合成催化剂进行再生。首先切出合成气切入n2置换反应器,气时空速6000ml/g催化剂/h,12小时后以20℃/h的速率降低反应器温度至160℃。切入氢气,气时空速3000ml/g催化剂/h,设定氢分压为3.0mpa,以升温速率10℃/h升温至265℃,升温过程检测排放气中甲烷含量;甲烷含量开始降低后,以升温速率20℃/h升温至360℃;排放气中甲烷含量低于1%时,以20℃/h的速率降低反应器温度至50℃,加氢裂化过程结束。切出氢气切入氮气,置换至驰放气中可燃气(h2+总烃)体积分数小于0.1%;在氮气中配入一定比例的空气,使反应器入口含氧气体中氧的体积分数为1%,钴基负载型费托合成催化剂因发生氧化反应温度上升至85℃,待反应器没有温度变化后,以每小时25℃逐步提高反应器温度至350℃。350℃恒温5h后,将反应器入口含氧气体中氧的体积分数增加为5%,恒温5h后,切换为空气恒温10h,当驰放气中co2体积分数<0.05%时氧化结束,以每小时30℃速度降温至150℃。切出含氧气体切入氮气,置换至驰放气中氧气体积分数小于0.1%后切入含体积分数2%氢的氢氮混合气,气体空速为3000ml/g催化剂/h,以20℃/h的速率降低反应器温度至400℃,在升温过程中反应器各点最大温差不大于3℃,温度升到恒温6h后检测排放气体中水分含量为2mg/l,增加氢氮混合气氢气体积分数为40%,6h后检测排放气体中水分含量为2mg/l,改为纯氢气进料,恒温6h时后还原结束,开始以30℃/h降温,钴基负载型费托合成催化剂再生过程结束。再生后的钴基负载型费托合成催化剂在相同条件下进行费托合成性能测试,与新鲜催化剂、再生前催化剂性能对比结果在表2中列出。表1表2新鲜催化剂再生前实施例2反应器温度,℃220220220反应压力,mpa3.03.03.0空速,ml/g催化剂/h200002000020000co转化率,%90.680.789.8ch4选择性,%7.411.67.6c5+选择性,%88.684.788.9当前第1页12