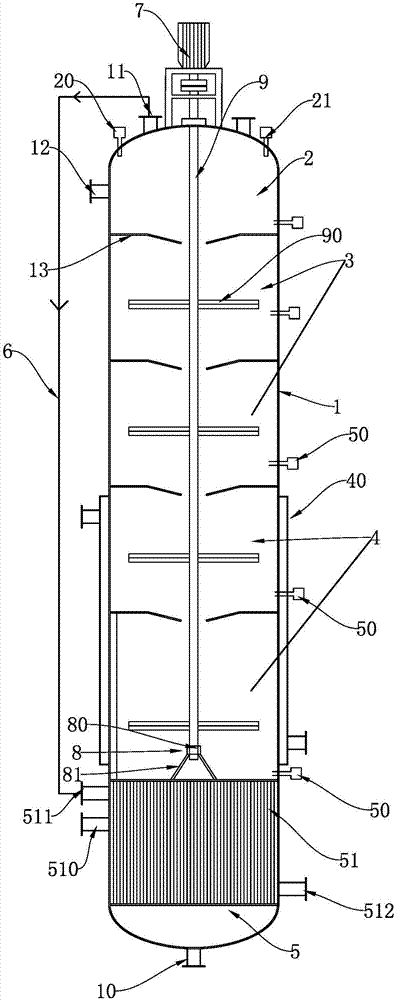
本发明涉及无机硅生产
技术领域:
,尤其涉及一种连续式液相反应器以及利用该反应器生产液体硅酸钠的工艺方法。
背景技术:
:传统的生产工艺是将石英砂与纯碱投入专用的高温焙烧炉中,加热熔融,反应充分后放料,冷却形成固体玻璃状硅酸钠,再加水加碱加压溶解成液态硅酸钠产品,此工艺过程长,消耗大量能源,不利于国家产业政策。另一种是以石英砂、烧碱为原料,混合后,加入反应釜内经加温加压制得。液相法生产硅酸钠工艺简单,但存在工艺流程长,只能生产低模数产品等缺陷,且未反应的石英砂及杂质形成大量的废渣,后续处理较困难,既造成原料的浪费,又不符合我国的资源节约政策。现在所用反应或溶解装置为搅拌反应釜,反应为间歇式,操作时需进行进排料,进排汽等操作,因此存在反应釜生产效率低,反应釜容积设计受限导致大规模生产时反应釜数量多,多釜并联操作量大,进排料需交叉操作,人工成本高,自动化程度低,设备投资大,占地面积多等多种问题。此外现有的反应釜生产硅酸钠时生产效率较低,得到液体产品的模数在1.4-2.5之间,无法生产高模数产品;因此针对上述问题,有必要建立一种连续式液相反应器以及利用该反应器生产液体硅酸钠的工艺方法。技术实现要素:本发明所要解决的技术问题是:针对现有技术的不足,提供一种液体硅酸钠生产用液相反应器,利用该反应器降低了成本和消耗,实现了自动化控制,大大提高了生产效率。本发明所要解决的另一个技术问题是:建立一种利用连续式液相反应器生产液体硅酸钠的工艺方法,利用该工艺方法缩短了反应时间,提高产品模数,提高了原料转化率和生产效率。为解决第一个技术问题,本发明的技术方案是:一种液体硅酸钠生产用连续式液相反应器,包括反应器本体,所述反应器本体的底部设有进料口,所述反应器本体的顶部设有排气口,所述反应器本体的上部一侧设有出料口,所述反应器本体的内部设有多层隔板,所述隔板将反应器本体由上至下依次分隔为沉降区、保温反应区、放热反应区和预热区,所述反应器本体内部设有搅拌装置,所述搅拌装置依次穿过沉降区、保温反应区和放热反应区;所述放热反应区相对应的反应器本体外部设有加热装置,所述预热区设有预热装置;所述沉降区设有液位传感器和压力传感器,所述沉降区、所述保温反应区、所述放热反应区和所述预热区分别设有温度传感器,所述液位传感器、所述压力传感器和所述温度传感器分别电连接控制器。作为一种改进的技术方案,每层隔板为两个,每层的两个隔板之间设有间隙,其中每个隔板包括与反应器本体内壁相连接的连接部以及与连接部的末端相连接的倾斜部,每层的两个隔板呈漏斗状排布在反应器本体内部。作为一种改进的技术方案,所述预热装置设有第一蒸汽进口、第二蒸汽进口和蒸汽出口,所述排气口通过管道连通第二蒸汽进口。作为一种改进的技术方案,所述预热装置为列管式换热器,所述列管式换热器包括壳体,所述壳体的两端分别设有管板,所述壳体内设有多个列管,所述列管与壳体之间形成壳程,所述多个列管的两端穿过管板,且所述多个列管与管板焊接连接。作为一种改进的技术方案,所述搅拌装置包括搅拌轴,所述搅拌轴的一端连有电机,所述搅拌轴的另一端连有搅拌轴固定器,所述搅拌轴上设有多个搅拌桨。作为一种改进的技术方案,所述搅拌轴固定器包括轴承座和支架,所述搅拌轴的另一端安装在轴承座上,所述轴承座通过支架固定在预热装置的顶部。作为一种改进的技术方案,所述反应器径高比为1:3-6,所述预热区、放热反应区、保温反应区以及沉降区的容积比为1:1.5-2.5:1.5-2.5:0.5-1.5。为解决第二个技术问题,本发明的技术方案是:一种利用连续式液相反应器生产液体硅酸钠的工艺方法,所述工艺方法包括以下步骤:(1)反应物料石英砂、空心微珠和烧碱溶液混合后从加料口进入液相反应器的预热区,控制预热区反应温度为80-100℃,反应物料经过预热后进入放热反应区,启动搅拌装置,控制搅拌装置转速为60-80转/分;(2)反应物料进入放热反应区后,控制放热反应区的温度为160-180℃,反应物料在放热反应区反应1.5-2.5h后再进入保温反应区;(3)反应物料进入保温反应区,控制保温反应区的温度为140-155℃,反应物料经在保温反应区反应3-6h后进入沉降区;(4)反应物料进入沉降区,控制沉降区内反应物料距离出料口的液位为200-300mm,并控制液相反应器内部的压力为0.8-1.0mpa。作为一种改进的技术方案,所述反应物料石英砂、空心微珠和烧碱溶液的摩尔比为1.2-3.0:0.3-0.8:1。作为一种改进的技术方案,所述烧碱溶液为离子膜烧碱,所述离子膜烧碱中氢氧化钠的含量为30-50wt%。采用了上述技术方案后,本发明的有益效果是:(1)在实际生产中,反应物料(砂碱浆料)从进料口进入反应器本体的预热区,利用预热装置预热后,物料再进入放热反应区,经过放热反应区外部的加热装置的加热,物料反应一段时间再进入保温反应区,物料在保温反应区反应一段时间再进入沉降区;反应液中的含固量依次递减,最终在沉降区内达到最低,产物最后从出料口排出反应器;整个反应过程中,工作人员可通过控制器控制反应器内的压力、控制各反应区内的温度和搅拌装置,利用该液相反应器实现了连续化生产,并可实现压力、温度的自动化控制,大大降低了生产的消耗及成本。(2)由于每层隔板为两个,每层的两个隔板之间设有间隙,其中每个隔板包括与反应器本体内壁相连接的连接部以及与连接部的末端相连接的倾斜部,每层的两个隔板呈漏斗状排布在反应器本体内部。物料经过搅拌装置搅拌后,反应器底部物料会向反应器本体的上方流动,将隔板设计成这一形状,可降低物向上流动时的阻力,有助于底部物料向上流动。(3)由于预热装置设有第一蒸汽进口、第二蒸汽进口和蒸汽出口,排气口通过管道连通第二蒸汽进口。物料在反应过程中进入放热反应区时,经过放热反应区的外部加热装置的加热,物料开始释放热量,生成的蒸汽从排气口进入预热装置内部。采用这一设计将反应生成的热量充分进行利用。(4)由于预热装置为列管式换热器,列管式换热器包括壳体,壳体的两端分别设有管板,壳体内设有多个列管,列管与壳体之间形成壳程,多个列管的两端穿过管板,且多个列管与管板焊接连接。采用这一设计,结构简单,还实现了对物料的预热。(5)由于搅拌装置包括搅拌轴,搅拌轴的一端连有电机,搅拌轴的另一端连有搅拌轴固定器,搅拌轴上设有多个搅拌桨。在实际生产中,工作人员通过控制器启动电机,在电机的驱动下搅拌轴和搅拌桨对反应器本体的物料进行搅拌混合;通过设置搅拌装置可实现了对反应物料的搅拌混合,更有助于物料反应;通过搅拌轴固定器将搅拌轴固定,可防止搅拌轴转动时反生晃动。(6)由于搅拌轴固定器包括轴承座和支架,搅拌轴的另一端安装在轴承座上,轴承座通过支架固定在预热装置的顶部。搅拌轴穿过轴承座,在电机的驱动下周向运动;搅拌轴固定器采用这一设计,结构简单,而且实现了对搅拌轴的固定,避免了搅拌轴转动时发生晃动。(7)本发明的工艺方法中,采用上述结构的液相反应器作为反应装置,并且反应原料添加了空心微珠,并将反应物料石英砂、空心微珠和烧碱溶液的摩尔比控制为1.2-3.0:0.3-0.8:1,由于空心微珠具有低表面张力、良好的渗透率等优良的性能,化学活性高,与烧碱反应后作用于二氧化硅表面,形成多聚硅酸盐,促进二氧化硅与烧碱进行化学反应,并且将石英砂、空心微珠和烧碱溶液的摩尔比控制为2.6:0.6:1,反应率可高达98.6%,并且当反应率达到80%时反应时间可缩短至6小时,降低了反应所需的能耗,提高了原料的利用率,减轻了后续过滤精制的压力和难度,大大提高了生产效率;同时减少了反应进行所需的蒸汽消耗量,大大降低了生产成本。此外采用上述反应器生产硅酸钠时可以得到高模数的产品,产品模数可高达3.6。附图说明图1为本发明一种液体硅酸钠生产用连续式液相反应器的结构示意图;图2为图1中隔板的结构示意图;图3为图1中预热装置的结构示意图;其中,1-反应器本体,10-进料口,11-排气口,12-出料口,13-隔板,2-沉降区,20-液位传感器,21-压力传感器,3-保温反应区,4-放热反应区,40-夹套,5-预热区,50-温度传感器,51-预热装置,510-第一蒸汽进口,511-第二蒸汽进口,512-蒸汽出口,6-管道,7-电机,8-搅拌轴固定器,80-轴承座,81-支架,9-搅拌轴,90-搅拌桨。具体实施方式为了使本发明的目的、技术方案及优点更加清楚明白,以下结合附图和实施例,对本发明进行进一步详细说明。应当理解,此处所描述的具体实施例仅仅用以解释本发明,并不用于限定本发明。实施例1一种液体硅酸钠生产用连续式液相反应器,如图1、图2和图3共同所示,包括反应器本体1,反应器本体的底部设有进料口10,反应器本体1的顶部设有排气口11,反应器本体1的上部一侧设有出料口12,反应器本体1的内部设有多层隔板13,隔板13将反应器本体1由上至下依次分隔为沉降区2、保温反应区3、放热反应区4和预热区5(反应器径高比为1:3-6,预热区、放热反应区、保温反应区以及沉降区的容积比为1:1.5-2.5:1.5-2.5:0.5-1.5),反应器本体1内部设有搅拌装置,搅拌装置依次穿过沉降区2、保温反应区3和放热反应区4;放热反应区4相对应的反应器本体1外部设有加热装置40(为夹套,夹套设有蒸汽进口和蒸汽出口),预热区5设有预热装置51;沉降区2设有液位传感器20和压力传感器21,沉降区2、保温反应区3、放热反应区4和预热区5分别设有温度传感器50,液位传感器20、压力传感器21和温度传感器50分别电连接控制器6。在实际生产中,反应物料(砂碱浆料)从进料口进入反应器本体的预热区,利用预热装置预热后,物料再进入放热反应区,经过放热反应区外部的加热装置的加热,物料反应一段时间再进入保温反应区,物料在保温反应区反应一段时间再进入沉降区;反应液中的含固量依次递减,最终在沉降区内达到最低,产物最后从出料口排出反应器;整个反应过程中,工作人员可通过控制器控制反应器内的压力、控制各反应区内的温度和搅拌装置,利用该液相反应器实现了连续化生产,并可实现压力、温度的自动化控制,大大降低了蒸汽的消耗及生产成本。为了更好的证明利用本发明的反应器可降低生产成本以及蒸汽的消耗,将本发明的反应器和现有技术间歇式反应器进行了对比,具体详见表1。表1同为20m3单台反应器的数据对比对比参数间歇式反应器(20立方)连续式反应器(20立方)填充量(%)7595反应量(吨/天)50160反应率(%)73>80蒸汽消耗(吨/吨)0.120.05电耗(度/吨)155.5工日(个/千吨)409其中,每层隔板13为两个(隔板与反应器本体内壁焊接连接),每层的两个隔板13之间设有间隙,每个隔板13包括与反应器本体1内壁相连接的连接部130以及与连接部130的末端相连接的倾斜部131,每层的两个隔板13呈漏斗状排布在反应器本体1的内部。搅拌轴穿过每层两个隔板之间的间隙,搅拌轴对反应器本体内的物料进行搅拌混合,物料经过预热区预热后,依次进入放热反应区、保温反应区和沉降区。其中,预热装置51设有第一蒸汽进口510、第二蒸汽进口511和蒸汽出口512,排气口11通过管道6连通第二蒸汽进口511。物料在反应过程中进入放热反应区时,经过放热反应区的外部加热装置的加热,物料开始释放热量,生成的蒸汽从排气口进入预热装置内部。其中,预热装置51为列管式换热器,列管式换热器包括壳体,壳体的两端分别设有管板,壳体内设有多个列管,列管与壳体之间形成壳程,多个列管的两端穿过管板,且多个列管与管板焊接连接。蒸汽从第一蒸汽进口和第二蒸汽进口进入壳程,对列管内的物料进行预热。其中,搅拌装置包括搅拌轴9,搅拌轴9的一端连有电机7,搅拌轴9的另一端连有搅拌轴固定器8(包括轴承座80和支架81,搅拌轴140的另一端安装在轴承座80上,轴承座80通过支架81固定在预热装置51的顶部管板上),搅拌轴9上设有多个搅拌桨90。搅拌轴通过搅拌轴固定器固定后,在驱动电机的作用下对反应器本体内的物料进行搅拌混合。实施例2一种利用连续式液相反应器生产液体硅酸钠的工艺方法,包括以下步骤:(1)反应物料石英砂(sio2含量99.2%以上)、空心微珠和烧碱溶液混合后(石英砂、空心微珠和烧碱溶液的摩尔比为1.2:0.3:1)从加料口进入液相反应器的预热区,控制预热区反应温度为80℃,反应物料经过预热后进入放热反应区,启动搅拌装置,控制搅拌装置转速为60转/分;(2)反应物料进入放热反应区后,控制放热反应区的温度为160℃,反应物料在放热反应区反应1.5-2.5h后再进入保温反应区;(3)反应物料进入保温反应区,控制保温反应区的温度为140℃,反应物料经在保温反应区反应3-4h后进入沉降区;(4)反应物料进入沉降区,控制沉降区内反应物料距离出料口的液位为200mm,并控制液相反应器内部的压力为0.80mpa。此工艺条件下液体硅酸钠产品的模数为1.45。实施例3一种利用连续式液相反应器生产液体硅酸钠的工艺方法,包括以下步骤:(1)反应物料石英砂(sio2含量99.2%以上)、空心微珠和烧碱溶液混合后(石英砂、空心微珠和烧碱溶液的摩尔比为2.6:0.6:1)从加料口进入液相反应器的预热区,控制预热区反应温度为90℃,反应物料经过预热后进入放热反应区,启动搅拌装置,控制搅拌装置转速为70转/分;(2)反应物料进入放热反应区后,控制放热反应区的温度为170℃,反应物料在放热反应区反应1.5-2.5h后再进入保温反应区;(3)反应物料进入保温反应区,控制保温反应区的温度为150℃,反应物料经在保温反应区反应4-5h后进入沉降区;(4)反应物料进入沉降区,控制沉降区内反应物料距离出料口的液位为250mm,并控制液相反应器内部的压力为0.9mpa。此工艺条件下,液体硅酸钠产品的模数为3.0。实施例4一种利用连续式液相反应器生产液体硅酸钠的工艺方法,包括以下步骤:(1)反应物料石英砂(sio2含量99.2%以上)、空心微珠和烧碱溶液混合后(石英砂、空心微珠和烧碱溶液的摩尔比为3:0.8:1)从加料口进入液相反应器的预热区,控制预热区反应温度为100℃,反应物料经过预热后进入放热反应区,启动搅拌装置,控制搅拌装置转速为80转/分;(2)反应物料进入放热反应区后,控制放热反应区的温度为180℃,反应物料在放热反应区反应1.5-2.5h后再进入保温反应区;(3)反应物料进入保温反应区,控制保温反应区的温度为155℃,反应物料经在保温反应区反应5-6h后进入沉降区;(4)反应物料进入沉降区,控制沉降区内反应物料距离出料口的液位为300mm,并控制液相反应器内部的压力为1.0mpa。此工艺条件下,液体硅酸钠产品的模数为3.6。为了更好的证明利用本发明的连续式反应器建立的硅酸钠生产工艺方法,反应原料中加入空心微珠,可显著提高二氧化硅转化率,并且大大提高了生产效率,做了几个对比例。具体结果见表2和表3。对比例1与实施例3不同的是,反应原料中没有加入空心微珠,其余操作相同。对比例2与实施例3不同的是,反应物料石英砂、空心微珠和烧碱溶液混合后(石英砂、空心微珠和烧碱溶液的摩尔比为2.6:0.6:1),但是采用的是间歇式反应器。对比例3与实施例3不同的是,反应装置为间歇式反应器,反应物料不含有空心微珠。表2空心微珠加入量对反应率的影响表3空心微珠对反应率的时间影响如表2、表3数据显示,采用本发明的反应器,在反应原料中添加空心微珠,可显著提高反应率,最高可达98.6%,同时缩短了反应时间,大大提高了生产效率,同时实现了产品模数的可控性,保证了不同模数液体的生产。以上所述仅为本发明的较佳实施例而已,并不用以限制本发明,凡在本发明的精神和原则之内所作的任何修改、等同替换和改进等,均应包含在本发明的保护范围之内。当前第1页12