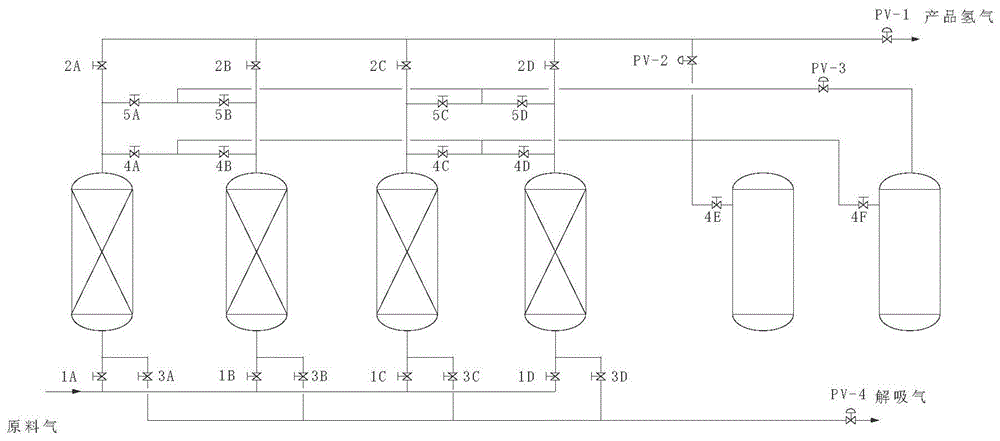
本发明属于变压吸附气体分离
技术领域:
,具体涉及一种变压吸附气体高回收率分离系统及其分离方法。
背景技术:
:变压吸附气体分离技术可以从混合气体中分离氢气、氦气、氮气、氧气、甲烷、一氧化碳以及二氧化碳气体,并广泛应用于炼油、化工、能源、冶金、环保等领域。变压吸附提纯氢气技术是应用最广、规模最大、技术最成熟的应用技术,可以从各种含氢气源(如重整气、低分气、变换气、焦炉煤气、甲醇弛放气、合成氨弛放气等)中制取纯度99%~99.999%的氢气,满足各类用氢场景的需求。变压吸附提纯氢气技术一般采用4~16塔工艺循环,在变压吸附循环工程中,每个吸附塔依次完成吸附步骤、均压降压步骤、顺放步骤、逆放步骤、冲洗步骤、均压升压步骤、最终升压步骤,对于抽空工艺用抽空步骤或抽空冲洗步骤代替冲洗步骤,在循环过程中每个吸附塔处于循环的不同阶段,各个吸附塔相互耦合共同完成气体分离工艺过程。变压吸附装置的主要性能指标有产品气的纯度、产品气的回收率、以及装置的投资等,一般变压吸附提氢的吸附压力在0.6~6.0mpag,均压次数在1~10次,要获得较高的氢气回收率就需要有足够多的均压次数,如2.5mpag的变换气一般采用4步均压。常规的变压吸附方法在工艺循环时,均压降压步骤与均压升压步骤相对应,均压次数有限,如4塔工艺专利zl00122638.x和us9695545b2均采用2步均压,当一个吸附塔处于均压降时,都有处于均压升的吸附塔与之对应,采用专利200510020305.x的10塔工艺可以有6次均压,即10-1-6工艺。然而吸附塔数量越多,程控阀门越多,系统越复杂,对于中小规模的变压吸附装置来说投资也越高。传统变压吸附技术不能在少量吸附塔工艺系统上实现多次均压,从而限制了其气体分离提纯的回收率。因此,本发明设计了一种变压吸附气体高回收率分离系统及其分离方法,通过增加中间罐,在吸附塔数量不变的情况下,增加多次均压,从而实现用少量的吸附塔达到多个吸附塔才能达到的均压次数,从而提高产品气的回收率以节约投资。并且,在增加均压次数时,分周期时间还保持不变,效率得以提高,多次均压共用一排程控阀门,流程更加简洁。技术实现要素:本发明要解决的技术问题是:提供一种变压吸附气体高回收率分离系统及其分离方法,解决现有技术传统中小规模变压吸附系统因吸附塔数量少导致产品气回收率低的技术问题。为实现上述目的,本发明采用的技术方案如下:一种变压吸附气体高回收率分离系统,包括若干个吸附塔,接入所述吸附塔的原料气输送管线和解吸气管线,从所述吸附塔接出的产品气外输管线,以及安装于原料气输送管线、解吸气管线和产品气外输管线上的程控阀;其特征在于,还包括n个中间罐,所述吸附塔接入有均压管线和冲洗管线,所述均压管线通过管道分别与n个中间罐连接,所述冲洗管线通过管道与至少一个中间罐连接。进一步地,所述均压管线与所述产品气外输管线之间连接有终升管线。进一步地,所述解吸气管线,所述产品气外输管线,所述终升管线,以及所述冲洗管线上均设有流量控制阀;优选地,n个中间罐分别与所述均压管线相连接的管道上均设有程控阀。进一步地,n不小于1;优选地,n个中间罐从第1个至第n个顺序编号,并且所述冲洗管线通过管道与第n个中间罐连接。进一步地,所述原料气输送管线所输送的原料气中氢气体积含量不小于40%,并且所述产品气外输管线所外输的产品气为氢气。进一步地,所述原料气输送管线所输送的原料气压力为1.2~6.0mpag。一种变压吸附气体高回收率分离系统的分离方法,吸附塔按如下步骤进行循环分离提纯气体:步骤ⅰ、吸附步骤;步骤ⅱ、非常规均压降步骤;步骤ⅲ、常规均压降步骤;步骤ⅳ、逆放步骤;步骤ⅴ、冲洗步骤;步骤ⅵ、常规均压升步骤;步骤ⅶ、非常规均压升步骤;步骤ⅷ、最终升压步骤。进一步地,在所述步骤ⅱ中,所述非常规均压降步骤为吸附塔处于均压降时分别与n个中间罐分n次进行均压降;优选地,当吸附塔分n次进行均压降时,从第1个中间罐至第n个中间罐依次进行均压降;进一步地,在所述步骤ⅶ中,所述非常规均压升步骤为吸附塔处于均压升时分别与n个中间罐分n次进行均压升;优选地,当吸附塔分n次进行均压升时,从第n个中间罐至第1个中间罐依次进行均压降。进一步地,在所述步骤ⅴ中,用第n个中间罐内的气体对处于再生阶段的吸附塔进行冲洗再生。进一步地,第n个中间罐内的气体仅供冲洗用,不用作均压升,此时第n次均压降步骤转变为顺放步骤,此顺放步骤调整到最后一次均压降之后进行。进一步地,所述吸附塔有4个,其采用16循环步序进行气体吸附分离,所述16循环步序具体如下表所示:其中,a:吸附;(1~n)ed:第(1~n)均压降;(n+1)ed:第(n+1)均压降;(n+2)ed:第(n+2)均压降;d:逆向放压;p:冲洗;(n+2)er:第(n+2)均压升;(n+1)er:第(n+1)均压升;(1~n)er:第(1~n)均压升;fr:最终升压;is:隔离;优选地,所述步骤1为60s,所述步骤2为30s,所述步骤3为20s,所述步骤4为30s,所述步骤5为60s,所述步骤6为30s,所述步骤7为20s,所述步骤8为30s,所述步骤9为60s,所述步骤10为30s,所述步骤11为20s,所述步骤12为30s,所述步骤13为60s,所述步骤14为30s,所述步骤15为20s,所述步骤16为30s。进一步地,所述吸附塔有5个,其采用20循环步序进行气体吸附分离,所述20循环步序具体如下表所示:步骤1塔2塔3塔4塔5塔⑴aispd(1~n)ed⑵a(n+1)erpp(n+1)ed⑶a(1~n)er(n+2)rp(n+2)ed⑷afrispd⑸(1~n)edaispd⑹(n+1)eda(n+1)erpp⑺(n+2)eda(1~n)er(n+2)erp⑻dafrisp⑼d(1~n)edaisp⑽p(n+1)eda(n+1)erp⑾p(n+2)eda(1~n)er(n+2)er⑿pdafris⒀pd(1~n)edais⒁pp(n+1)eda(n+1)er⒂(n+2)erp(n+2)eda(1~n)er⒃ispdafr⒄ispd(1~n)eda⒅(n+1)erpp(n+1)eda⒆(1~n)er(n+2)erp(n+2)eda⒇frispda其中,a:吸附;(1~n)ed:第(1~n)均压降;(n+1)ed:第(n+1)均压降;(n+2)ed:第(n+2)均压降;d:逆向放压;p:冲洗;(n+2)er:第(n+2)均压升;(n+1)er:第(n+1)均压升;(1~n)er:第(1~n)均压升;fr:最终升压;is:隔离;优选地,所述步骤⑴为30s,所述步骤⑵为12s,所述步骤⑶为30s,所述步骤⑷为22s,所述步骤⑸为30s,所述步骤⑹为12s,所述步骤⑺为30s,所述步骤⑻为22s,所述步骤⑼为30s,所述步骤⑽为12s,所述步骤⑾为30s,所述步骤⑿为22s,所述步骤⒀为30s,所述步骤⒁为12s,所述步骤⒂为30s,所述步骤⒃为22s,所述步骤⒄为30s,所述步骤⒅为12s,所述步骤⒆为30s,所述步骤⒇为22s。与现有技术相比,本发明具有以下有益效果:本发明通过增加中间罐,在吸附塔数量不变的情况下,增加多次均压,从而实现用少量的吸附塔达到多个吸附塔才能达到的均压次数,从而提高产品气的回收率以节约投资。并且,在增加均压次数时,分周期时间还保持不变,效率得以提高,多次均压共用一排程控阀门,流程更加简洁。附图说明图1为发明4塔工艺且n=2时分离系统的系统结构框图。图2为发明4塔工艺且n=5时分离系统的系统结构框图。图3为发明5塔工艺且n=3时分离系统的系统结构框图。具体实施方式为了使本发明的目的、技术方案及优点更加清楚明白,以下结合附图,对本发明进一步详细说明。显然,所描述的实施例仅仅是本发明一部分实施例,而不是全部的实施例。基于本发明中的实施例,本领域普通技术人员在没有做出创造性劳动前提下所获得的所有其他实施例,都属于本发明保护的范围。在本发明的描述中,需要说明的是,术语“中心”、“上”、“下”、“左”、“右”、“竖直”、“水平”、“内”、“外”等指示的方位或位置关系为基于附图所示的方位或位置关系,仅是为了便于描述本发明和简化描述,而不是指示或暗示所指的装置或元件必须具有特定的方位或者以特定的方位构造和操作,因此其不能理解为对本发明的限制。此外,术语“第一”、“第二”、“第三”仅用于描述目的,而不能理解为指示或暗示相对重要性。在本发明的描述中,需要说明的是,除非另有明确的规定和限定,术语“安装”、“相连”、“连接”应做广义理解,例如,可以是固定连接,也可以是可拆卸连接,或一体地连接;当然的,还可以是机械连接,也可以是电连接;另外的,还可以是直接相连,也可以是通过中间媒介间接相连,或者可以是两个元件内部的连通。对于本领域的普通技术人员而言,可以根据具体情况理解上述术语在本发明中的具体含义。如图1-3所示,本发明提供的一种变压吸附气体高回收率分离系统,包括若干个吸附塔,接入所述吸附塔的原料气输送管线和解吸气管线,从所述吸附塔接出的产品气外输管线,以及安装于原料气输送管线、解吸气管线和产品气外输管线上的程控阀;其特征在于,还包括n个中间罐,所述吸附塔接入有均压管线和冲洗管线,所述均压管线通过管道分别与n个中间罐连接,所述冲洗管线通过管道与至少一个中间罐连接。本发明所述均压管线与所述产品气外输管线之间连接有终升管线。所述解吸气管线,所述产品气外输管线,所述终升管线,以及所述冲洗管线上均设有流量控制阀;优选地,n个中间罐分别与所述均压管线相连接的管道上均设有程控阀。本发明n不小于1;优选地,n个中间罐从第1个至第n个顺序编号,并且所述冲洗管线通过管道与第n个中间罐连接。本发明所述原料气输送管线所输送的原料气中氢气体积含量不小于40%,并且所述产品气外输管线所外输的产品气为氢气。所述原料气输送管线所输送的原料气压力为1.2~6.0mpag。一种变压吸附气体高回收率分离系统的分离方法,吸附塔按如下步骤进行循环分离提纯气体:步骤ⅰ、吸附步骤;步骤ⅱ、非常规均压降步骤;步骤ⅲ、常规均压降步骤;步骤ⅳ、逆放步骤;步骤ⅴ、冲洗步骤;步骤ⅵ、常规均压升步骤;步骤ⅶ、非常规均压升步骤;步骤ⅷ、最终升压步骤。本发明在所述步骤ⅱ中,所述非常规均压降步骤为吸附塔处于均压降时分别与n个中间罐分n次进行均压降;优选地,当吸附塔分n次进行均压降时,从第1个中间罐至第n个中间罐依次进行均压降;进一步地,在所述步骤ⅶ中,所述非常规均压升步骤为吸附塔处于均压升时分别与n个中间罐分n次进行均压升;优选地,当吸附塔分n次进行均压升时,从第n个中间罐至第1个中间罐依次进行均压降。在所述步骤ⅴ中,用第n个中间罐内的气体对处于再生阶段的吸附塔进行冲洗再生。进一步地,本发明第n个中间罐内的气体仅供冲洗用,不用作均压升,此时第n次均压降步骤转变为顺放步骤,此顺放步骤调整到最后一次均压降之后进行。本发明所述吸附塔有4个,其采用16循环步序进行气体吸附分离,所述16循环步序具体如下表所示:步骤1塔2塔3塔4塔1aisp(1~n)ed2a(n+1)erp(n+1)ed3a(1~n)er(n+2)er(n+2)ed4afrisd5(1~n)edaisp6(n+1)eda(n+1)erp7(n+2)eda(1~n)er(n+2)er8dafris9p(1~n)edais10p(n+1)eda(n+1)er11(n+2)er(n+2)eda(1~n)er12isdafr13isp(1~n)eda14(n+1)erp(n+1)eda15(1~n)er(n+2)er(n+2)eda16frisda其中,a:吸附;(1~n)ed:第(1~n)均压降;(n+1)ed:第(n+1)均压降;(n+2)ed:第(n+2)均压降;d:逆向放压;p:冲洗;(n+2)er:第(n+2)均压升;(n+1)er:第(n+1)均压升;(1~n)er:第(1~n)均压升;fr:最终升压;is:隔离。优选地,所述步骤1为60s,所述步骤2为30s,所述步骤3为20s,所述步骤4为30s,所述步骤5为60s,所述步骤6为30s,所述步骤7为20s,所述步骤8为30s,所述步骤9为60s,所述步骤10为30s,所述步骤11为20s,所述步骤12为30s,所述步骤13为60s,所述步骤14为30s,所述步骤15为20s,所述步骤16为30s。本发明4塔变压吸附工艺循环,共16个步骤,包括4个吸附步骤,3个均压降步骤,1个逆放步骤,2个冲洗步骤,3个均压升步骤,1个最终升压步骤,循环周期560秒;其中第1均压降压步骤分解为n(n≥1)个均压降步骤,吸附塔依次分别与n个中间罐进行均压,且先与第1个均压罐均压,最后与第n个均压罐均压;第1均压升步骤分解为n(n≥1)个均压升步骤,吸附塔依次分别与n个中间罐进行均压,且先与第n个均压罐均压,最后与第1个均压罐均压;再生冲洗气来自第n个中间罐。当第n个中间罐内的气体仅提供冲洗气,不提供均压升时,工艺的均压次数为n+1,第n次均压降步骤转变为顺放步骤,此顺访步骤调整最后一步均压降之后进行。传统4塔工艺只有2次均压,而本发明4塔工艺循环增加了n次均压,通过增加均压次数,不仅提高了4塔工艺的回收率,也将4塔工艺的应用压力范围从1.6mpag扩展到6.0mpag,避免了传统工艺通过增加吸附塔数量来增加均压次数,从而降低了投资。图1是4-1-4循环工艺的系统结构框图,即4塔工艺,4步均压,n=2。该流程由4个吸附塔,2个中间罐,22台程控阀和4台调节阀组成,所有的均压过程和充压过程均由4#阀完成,流程简洁,阀门数量少。本发明4塔流程工艺,每增加一次均压,仅仅增加1个中间罐和1台程控阀门。图2是4-1-6循环工艺的系统结构框图,即4塔工艺,6步均压,n=5,其中第5个中间罐内的气体仅供冲洗步骤用,吸附塔与第5个中间罐的均压步骤变为顺放步骤,即非常规均压次数为4,常规均压次数为2,共6次均压,将第6均压降步骤分成均压降和顺放两步,在第6均压降后完成,再进行吸附塔与第5个中间罐的顺放步骤。本发明所述吸附塔有5个,其采用20循环步序进行气体吸附分离,所述20循环步序具体如下表所示:其中,a:吸附;(1~n)ed:第(1~n)均压降;(n+1)ed:第(n+1)均压降;(n+2)ed:第(n+2)均压降;d:逆向放压;p:冲洗;(n+2)er:第(n+2)均压升;(n+1)er:第(n+1)均压升;(1~n)er:第(1~n)均压升;fr:最终升压;is:隔离;优选地,所述步骤⑴为30s,所述步骤⑵为12s,所述步骤⑶为30s,所述步骤⑷为22s,所述步骤⑸为30s,所述步骤⑹为12s,所述步骤⑺为30s,所述步骤⑻为22s,所述步骤⑼为30s,所述步骤⑽为12s,所述步骤⑾为30s,所述步骤⑿为22s,所述步骤⒀为30s,所述步骤⒁为12s,所述步骤⒂为30s,所述步骤⒃为22s,所述步骤⒄为30s,所述步骤⒅为12s,所述步骤⒆为30s,所述步骤⒇为22s。本发明5塔变压吸附工艺循环,共20个步骤,包括4个吸附步骤,3个均压降步骤,2个逆放步骤,6个冲洗步骤,3个均压升步骤,1个最终升压步骤,循环周期470秒;其中第1个均压降压步骤分解为n(n≥1)个均压降步骤,吸附塔依次分别与n个中间罐进行均压,且先与第1均压罐均压,最后与第n个均压罐均压;第1均压升步骤分解为n(n≥1)个均压升步骤,吸附塔依次分别与n个中间罐进行均压,且先与第n个均压罐均压,最后与第1个均压罐均压;再生冲洗气来自第n个中间罐。当第n个中间罐内的气体仅提供冲洗气,不提供均压升时,工艺的均压次数为(n+1)。图3是5-1-5循环工艺的系统结构框图,即5塔工艺,5步均压,n=3。该流程由5个吸附塔,3个中间罐,22台程控阀和4台调节阀组成,所有的均压过程和充压过程均由4#阀完成,流程简洁,阀门数量少。5塔流程与4塔流程相比,增加了1个吸附塔,循环周期更短,适合更大规模的装置。本发明通过增加中间罐,在吸附塔数量不变的情况下,增加多次均压,从而实现用少量的吸附塔达到多个吸附塔才能达到的均压次数,从而提高产品气的回收率以节约投资。并且,在增加均压次数时,分周期时间还保持不变,效率得以提高,多次均压共用一排程控阀门,流程更加简洁。本发明公开了一种变压吸附气体分离方法与系统,其产品气优选氢气,该系统包含多个吸附塔和n(n≥1)个中间罐,通过将一个均压步骤分解为n个均压步骤,增加了变压吸附系统的均压次数,从而提升了装置的回收率,扩大了应用范围。本发明除了循环所需的吸附塔外,增加n个(n≥1)中间罐,将某一个均压降步骤分解为n个均压降步骤,均压降的吸附塔与n个中间罐(从第1个中间罐到第n个中间罐)依次进行均压降,将对应的均压升步骤分解为n个均压升步骤,均压升的吸附塔依次反向与n个中间罐(从第n个中间罐到第1个中间罐)进行均压升。本发明用第n个中间罐内的气体对处于再生阶段的吸附塔进行冲洗再生;第n个中间罐内的气体可仅供冲洗用,不用作均压升,此时第n次均压降步骤转变为顺放步骤;均压和最终升压采用一排阀门完成。每增加一次均压只需要增加1个中间罐和1台阀门。吸附塔的数量大于等于3,优选4和5;原料气的压力在1.2~6.0mpag;原料气中产物的体积含量大于等于40%;产品气优选氢气。本发明每个吸附塔在一个循环内依次经历如下步骤:吸附步骤;非常规均压降步骤,即吸附塔与n个中间罐进行均压,吸附塔压力降低,中间罐压力升高;常规均压降步骤,即两个吸附塔之间均压;逆放步骤;冲洗步骤;常规均压升步骤,即两个吸附塔之间均压;非常规均压升步骤,即吸附塔与n个中间罐进行均压,吸附塔压力升高,中间罐压力降低;最终升压步骤。最后应说明的是:以上各实施例仅仅为本发明的较优实施例用以说明本发明的技术方案,而非对其限制,当然更不是限制本发明的专利范围;尽管参照前述各实施例对本发明进行了详细的说明,本领域的普通技术人员应当理解:其依然可以对前述各实施例所记载的技术方案进行修改,或者对其中部分或者全部技术特征进行等同替换;而这些修改或者替换,并不使相应技术方案的本质脱离本发明各实施例技术方案的范围;也就是说,但凡在本发明的主体设计思想和精神上作出的毫无实质意义的改动或润色,其所解决的技术问题仍然与本发明一致的,均应当包含在本发明的保护范围之内;另外,将本发明的技术方案直接或间接的运用在其他相关的
技术领域:
,均同理包括在本发明的专利保护范围内。当前第1页12