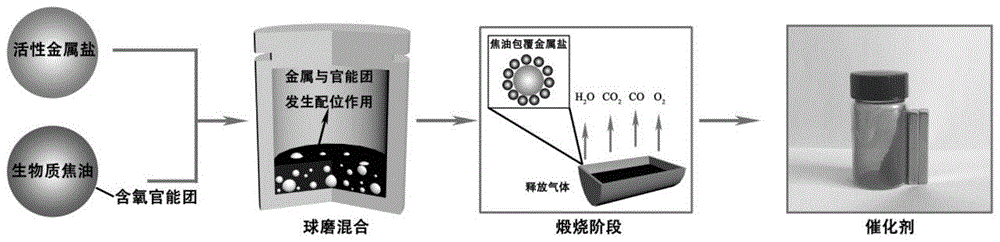
本发明涉及一种生物质焦油绿色无溶剂资源化处理新方法,属于环境保护与资源综合利用领域中的固体废弃物处理处置新技术。技术背景作为一种可再生、储量巨大的能源,生物质能现已引起了人们的广泛关注,具有广阔的应用前景。中国作为农业大国,每年会产生大量的废弃生物质——农林废弃物,其中近9000万吨的农林废弃物用于发电产业,能有效的节约煤炭资源,较少二氧化碳排放。然而,这些生物质通过热化学途径转化为电能的过程中,会不可避免地产生一种副产物——焦油。这是一种组分复杂、可冷凝的有机物混合体,最高产率可达40%以上。这种副产物焦油不仅会污染阻塞设备,还会造成环境污染。因此,开发高价值利用的方法十分重要。生物质热解焦油富含芳香族化合物,具有碳含量高、灰分低和热塑性等特点,是潜在的优质碳质前驱体。因此,可用于负载活性催化物质或是活化制备多孔碳材料。特别是,碳质材料易与其他具有催化活性的物质结合形成复合材料,两者之间能够产生协同作用,从而具有较高的催化性能,是理想的低成本载体材料。在废水处理工艺中,芬顿法是一种成本低廉、操作简单、适用范围广的工艺,通过催化剂亚铁离子催化过氧化氢产生具有高活性的羟基自由基,高效氧化处理废水中的有机物。然而,亚铁离子这种均相催化剂在实际废水处理过程中需要高酸性环境,并且处理后会形成较难分离去除的铁泥,这些缺点限制了它的应用。而固体氧化铁可作为非均相类芬顿催化剂克服这些缺点,替代传统的亚铁离子催化剂。同时,氧化铁具有光催化性能,可作为光催化剂协同催化降解污染物。复合材料通过不同物质之间的协同效应,会表现出比单一物质更高的催化性能。活性铁物质(零价铁、氧化铁等)与其他活性金属(锰、钴、镍等)复合得到的催化剂往往具有更好的催化性能。并且,过渡金属可以催化碳质材料在一定温度下转化为石墨碳,而石墨碳又是一种具有电子迁移率高、传质速度快、光吸收能力强等诸多优点的制备非均相催化剂的理想载体。因此,可将废弃物焦油作为碳质前体与铁等活性金属结合制备催化剂,达到对废弃物资源的高价值利用。传统的催化剂材料制备方法需要将载体浸没在金属盐溶液中,会产生大量的废水,因此发展一种工艺简单、无溶剂的绿色合成方法是十分有价值的。技术实现要素:本发明的目的是为解决生物质焦油无法高价值利用的问题,将焦油与其他活性物质进行复合,合成制备具有催化性能的催化剂材料,该材料具有较高的催化性能、适应酸碱工作环境、易回收以及可循环使用。本发明要解决的技术问题是提供一种工艺简单、快速高效的焦油基催化剂绿色合成方法,采用球磨法对材料进行机械混合,避免传统制备方法中需要使用溶液的缺点;同时利用球磨的机械力使活性物质在焦油载体上均匀分散,从而提高催化剂的催化性能。本发明的目的通过以下技术方案实现:一种生物质热解焦油资源化利用的新方法,包括以下步骤:(1)将生物质焦油与草酸铁按一定比例加入到球磨罐中,按照设定的程序球磨一定时间后取出;(2)将步骤(1)中得到的粉末混合物进行高温煅烧;(3)将步骤(2)中煅烧得到材料冷却后存于氮气氛围下,得到合成的石墨基类芬顿催化剂。进一步地,在步骤(1)中,草酸铁可由硝酸铁、氯化铁、硫酸铁等铁盐代替,生物质焦油为任何生物质经过热化学处理后得到的副产物焦油,生物质焦油与铁盐的质量比为2:1~10:1。可选地,在步骤(1)中,混合物的配方可为焦油、铁盐和镍盐(或其他过渡金属盐,如锰、钴等)混合,质量比为4:1:1~20:1:1。进一步地,在步骤(1)中的具体球磨方式是:直径5mm、10mm和20mm的氧化锆珠的质量比为3:4:3,球料比为10:1~20:1,以300~500r/min运行10min后停止5min,重复多次满足球磨时间1~6h。进一步地,在步骤(2)中,将混合物置于空气气氛下煅烧,按程序升温5~10℃/min,升至300~500℃,保持2~6h,得到含有金属氧化物的催化剂。可选地,在步骤(2)中,将混合物置于氮气气氛下煅烧,按程序升温5~10℃/min,升至800~1200℃,保持2~4h,得到含有多价态金属的催化剂。进一步地,在步骤(3)中,煅烧后的催化剂过100目筛细化后保存于氮气气氛下。与现有技术相比,本发明具有以下优点和有益效果:(1)本发明得到的催化剂材料由石墨与金属盐通过球磨法混合后煅烧合成的,煅烧前金属盐表面包覆了焦油,使得煅烧后得到的催化剂具有微观纳米尺寸;同时具有多孔的结构和石墨碳结构,活性金属在载体表面均匀分布,从而具有优异的催化性能。(2)本发明的技术方案中,利用球磨法对废弃物焦油与金属盐进行混合,避免了传统浸渍法对水溶液的要求,符合绿色化学的要求,是一种操作简单、快速高效的绿色合成技术。(3)本发明所述技术方案中,原料废弃物焦油的成本低廉;合成过程避免水溶液的使用,节约用水;设备成本低廉,可用于大规模生产合成催化剂。(4)本发明最终得到一种石墨基类芬顿催化剂材料,可用于催化过氧化氢分解产生羟基自由基对污染物进行降解,也可用于光催化降解污染物。附图说明图1为本发明的合成机理示意图。图2为本发明实施例1的磁性分离示意图。图3为本发明实施例1的tem图像。图4为本发明实施例1的xrd图像。图5为本发明实施例2的tem图像。具体实施方式下面结合具体处理步骤,对本发明作进一步详细说明,但本发明的实施方式包括但不局限于下述实例。凡利用等同替换方式或等效交换方式所获得的替代方案,均处于本发明的保护范围之内。实施例1:本发明实施例1提供了利用生物质焦油制备石墨基单金属类芬顿催化剂的方法,包括如下步骤:(1)将生物质焦油、硝酸铁按质量比10:1比例加入到球磨罐中,以500r/min运行10min后,静置5min以防止罐内温度过高,重复12次,使球磨时间达到2h,随后取出混合均匀的粉体;(2)将上述步骤(1)中得到的粉末混合物放入管式炉中,在氮气气氛下煅烧,以5℃/min的升温速率,升温到1000℃,恒温4h;(3)将步骤(2)中煅烧得到材料冷却后取出,过100目筛细化后存于氮气氛围下,得到石墨基单金属类芬顿催化剂,该催化剂中含有多价态的铁活性物质,包括零价铁、四氧化三铁、碳化铁。图2为实施例1的磁性分离示意图,由于材料中铁活性物质的存在,制备的催化剂能通过磁性从溶液中分离。图3为实施例1的tem图像,可以看到制备的催化剂具有多孔的形貌结构,并且形成了类似碳纳米管的管道结构,图像中的阴影部分说明活性铁在催化剂中均匀分布。图4为实施例1的xrd图像,结果说明制备的催化剂中存在石墨碳、零价铁、四氧化三铁以及碳化铁晶相。实施例2:本发明实施例2提供了利用焦油制备石墨基单金属类芬顿催化剂的方法,包括如下步骤:(1)将生物质焦油与草酸铁按质量比8:1比例加入到球磨罐中,以300r/min运行10min后,静置5min以防止罐内温度过高,重复24次,使球磨时间达到4h,随后取出混合均匀的粉体;(2)将上述步骤(1)中得到的粉末混合物放入马弗炉内,在空气气氛下煅烧,以5℃/min的升温速率,升温到400℃,恒温4h;(3)将步骤(2)中煅烧得到材料冷却后取出,过100目筛细化后存于氮气氛围下,得到石墨基类芬顿催化剂,该催化剂中的主要活性物质为石墨碳和三氧化二铁。图5为本发明实施例2的tem图像,可以看出在边缘部分具有半透明的石墨片层结构,图像中的黑色阴影均匀分布,说明球磨混合阶段使催化剂中的活性物质均匀分布在碳载体上。实施例3本发明实施例3提供了利用焦油制备石墨基单金属类芬顿催化剂的方法,包括如下步骤:(1)将生物质焦油与草酸铁按质量比5:1比例加入到球磨罐中,以300r/min运行10min后,静置5min以防止罐内温度过高,重复12次,使球磨时间达到2h,随后取出混合均匀的粉体;(2)将上述步骤(1)中得到的粉末混合物置于石英舟内放入管式炉中,在氮气气氛下进行高温煅烧,以5℃/min的升温速率,升温到800℃,恒温4h;(3)将步骤(2)中煅烧得到材料冷却后取出,过100目筛细化后存于氮气氛围下,得到石墨基类芬顿催化剂,该催化剂中含有石墨碳以及多价态的铁活性物质,包括零价铁、四氧化三铁、碳化铁。实施例4本发明实施例4提供了利用焦油制备石墨基双金属类芬顿催化剂的方法,包括如下步骤:(1)将生物质焦油、硝酸铁和硝酸镍按质量比10:1:1比例加入到球磨罐中,以400r/min运行10min后,静置5min以防止罐内温度过高,重复12次,使球磨时间达到2h,随后取出混合均匀的粉体;(2)将上述步骤(1)中得到的粉末混合物放入马弗炉中,在空气气氛下煅烧,以5℃/min的升温速率,升温到300℃,恒温4h;(3)将步骤(2)中煅烧得到材料冷却后取出,过100目筛细化后存于氮气氛围下,得到石墨基双金属类芬顿催化剂,该催化剂中含有多种活性金属物质,包括三氧化二铁、氧化镍、铁酸镍等晶相。实施例5本发明实施例5提供了利用焦油制备石墨基双金属类芬顿催化剂的方法,包括如下步骤:(1)将生物质焦油、草酸铁和草酸钴按质量比15:1:1比例加入到球磨罐中,以500r/min运行10min后,静置5min以防止罐内温度过高,重复24次,使球磨时间达到4h,随后取出混合均匀的粉体;(2)将上述步骤(1)中得到的粉末混合物放入管式炉中,在氮气气氛下煅烧,以5℃/min的升温速率,升温到800℃,恒温4h;(3)将步骤(2)中煅烧得到材料冷却后取出,过100目筛细化后存于氮气氛围下,得到石墨基双金属类芬顿催化剂,该催化剂中含有多种活性金属物质,包零价铁、钴、四氧化三铁晶相。对比例1:(1)将草酸铁单独加入到球磨罐中,以300r/min运行10min后,静置5min以防止罐内温度过高,重复12次,使球磨时间达到2h,随后取出粉碎均匀的粉体;(2)将上述步骤(1)中得到的粉末置于石英舟内放入管式炉中,在氮气气氛下进行高温煅烧,以5℃/min的升温速率,升温到800℃,恒温4h;(3)将步骤(2)中煅烧得到材料冷却后取出,过100目筛细化后存于氮气氛围下,得到所需用于进行对比的类芬顿催化剂,该催化剂中主要为四氧化三铁。对比例2:(1)将草酸铁单独加入到球磨罐中,以300r/min运行10min后,静置5min以防止罐内温度过高,重复24次,使球磨时间达到4h,随后取出混合均匀的粉体;(2)将上述步骤(1)中得到的粉末混合物放入马弗炉内,在空气气氛下煅烧,以5℃/min的升温速率,升温到400℃,恒温4h;(3)将步骤(2)中煅烧得到材料冷却后取出,过100目筛细化后存于氮气氛围下,得到用于对比的类芬顿催化剂,该催化剂中的主要活性物质为三氧化二铁。选用亚甲基蓝为目标污染物,利用本发明制备的类芬顿催化剂对其进行催化降解实验来验证催化剂的性能。模拟废水中亚甲基蓝的浓度为25mg/l,分别加入实施例1~5和对比例1~2制备得到的类芬顿催化剂,加入的催化剂浓度为0.5g/l。将溶液与催化剂粉末混合均匀后,在摇床中震荡30min以达到吸附平衡,取样过滤测定溶液中亚甲基蓝的浓度(c0)。随后加入一定量的过氧化氢,确保浓度为0.1m,反应1h后取样过滤,测定溶液中亚甲基蓝的浓度(ct)。用紫外分光光度计在663nm测定溶液中亚甲基蓝的浓度。催化剂对亚甲基蓝的催化降解率(re)利用公式:re=(c0-ct)*100%/c0进行计算。根据表1的实验结果可知,由焦油制备的石墨基类芬顿催化剂对亚甲基蓝具有较好的催化降解性能,对亚甲基蓝的催化降解去除率最高达到99.5%。实验结果表明,石墨与活性金属通过协同作用能够加快对过氧化氢的催化分解,从而产生羟基自由基对有机污染物进行氧化降解。表1实施例1~5和对比例1~2类芬顿催化剂对亚甲基蓝的催化降解结果催化剂的稳定性对其性能有重要影响,因此对实施例1和实施例2制备的类芬顿催化剂进行了稳定性测试。对模拟亚甲基蓝废水(25mg/l)在中性条件下进行了五次重复催化降解实验,每次实验运行后,对催化剂进行磁性分离,并用去离子水清洗用过的催化剂三次。清洗后的催化剂真空干燥干燥12小时,以降解60分钟的溶液浓度作为评价结果。根据表2的实验结果可知,实施例1和实施例2制备的催化剂具有较好的稳定性,重复运行5次后,仍然具有较好的催化降解能力,这样的特点与催化剂的石墨结构和多种活性铁物质的存在有关。表2实施例1和实施例2对亚甲基蓝的催化降解稳定性测试结果循环次数实施例1实施例2第一次99.2%94.3%第二次97.4%91.8%第三次95.1%88.3%第四次92.3%86.5%第五次91.2%83.1%当前第1页12