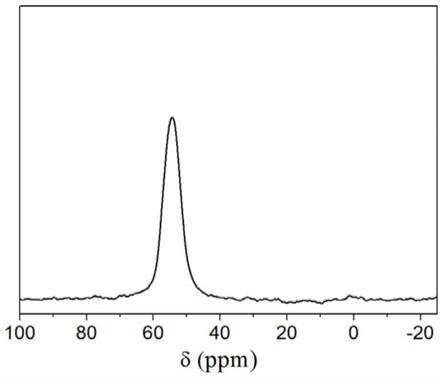
1.本发明属于催化化学与化学工程的技术领域,尤其是涉及一种失活的无粘结剂分子筛催化剂的再生方法。
背景技术:2.苯和乙烯气相烷基化制乙苯为酸催化反应,工业使用的催化剂一般为分子筛催化剂,尤其是无粘结剂分子筛催化剂,具有酸性催化活性中心,随着反应时间的进行,催化剂会逐渐的失活,失活的原因主要有以下几点:反应过程中产生的积碳会沉积在催化剂的孔道或者表面,从而堵塞催化剂的微孔孔道,并覆盖酸性活性中心,导致催化剂的催化性能下降;另外,工业乙苯催化剂在长时间的运行过程中,催化剂酸性活性中心存在流失现象,一些骨架铝转变为非骨架铝,同样导致催化能力下降。当催化剂的性能下降到一定的程度,需要对其进行再生处理。
3.cn105597842 b公开了一种乙苯催化剂的再生方法,再生过程为:将失活的乙苯催化剂用0.1-20.0wt%有机胺或有机铵溶液处理2-20小时、在氮气气氛下于100-200℃烘干2-10小时、在空气气氛下400-800℃高温焙烧2-10小时,其中,失活催化剂和有机胺或有机铵溶液的固液比为(5-50):1,处理温度为50-120℃。该再生方法仅能维持失活催化剂的骨架结构和增加部分介孔孔道来恢复乙苯催化剂的性能,但存在再生后催化剂堆密度降低,因失活导致破坏的骨架四配位铝活性中心无法得到恢复。
技术实现要素:4.针对现有技术中的不足,本发明提供了一种失活的无粘结剂分子筛催化剂的再生方法。通过本发明再生方法再生后的催化剂,堆密度高,装填在反应器中能保证装填重量,且反应过程中不容易破碎,骨架四配位铝活性中心占比高,尤其是失活的苯和乙烯气相烷基化制乙苯催化剂再生后,用于苯和乙烯气相烷基化制乙苯反应中,活性高,乙苯选择性好,二甲苯产量明显降低。
5.本发明提供了一种失活的无粘结剂分子筛催化剂的再生方法,包括:
6.(1)将失活的无粘结剂分子筛催化剂和酸溶液接触,得到半成品a;
7.(2)将半成品a、硅铝溶胶和增强剂接触,得到半成品b;所述的增强剂为阿拉伯胶、果胶、角叉胶、藻蛋白酸钠中的一种或多种;
8.(3)将半成品b通过处理,得到再生后的无粘结剂分子筛催化剂。
9.上述技术方案中,无粘结剂分子筛催化剂可以为用于苯和乙烯烷基化制乙苯的无粘结剂分子筛催化剂。所述的分子筛可以硅铝分子筛,优选为zsm-5分子筛。
10.上述技术方案中,优选地,步骤(1)中所述的酸为盐酸、硝酸、硫酸、草酸、柠檬酸中的一种或多种。
11.上述技术方案中,优选地,步骤(1)中所述的酸溶液为水溶液,浓度为0.1wt%-5.0wt%。
12.上述技术方案中,优选地,步骤(1)中所述的失活的无粘结剂分子筛催化剂和酸溶液的质量比例为,无粘结剂分子筛催化剂:酸溶液=(0.05-0.5):1。
13.上述技术方案中,优选地,步骤(1)中将失活的无粘结剂分子筛催化剂和酸溶液接触得到半成品a的过程为:将失活的无粘结剂分子筛催化剂和酸溶液在密闭空间中搅拌,搅拌温度为50-100℃,搅拌时间为2-10小时,然后经洗涤和干燥,得到半成品a。其中洗涤可以用去离子水洗除催化剂中的酸溶液,干燥条件如下:在温度为100-170℃条件下干燥6-12小时。
14.上述技术方案中,优选地,步骤(2)中所述的硅铝溶胶为由硅源、铝源和水(优选为去离子水)接触得到硅铝溶胶。
15.上述技术方案中,优选地,所述硅源为硅溶胶、白炭黑、硅粉中的一种或多种;所述铝源为硫酸铝、硝酸铝、氯化铝、异丙醇铝中的一种或多种。
16.上述技术方案中,优选地,所述硅源、铝源和水的摩尔比例分别为,硅源:铝源=(50-400):1;水:硅源=(5-10):1。其中硅源以sio2计算,铝源以al2o3计算。
17.上述技术方案中,优选地,所述硅铝溶胶的制备方法为,将硅源、铝源和水在密闭空间中搅拌,搅拌温度为80-120℃,搅拌时间为6-24小时。
18.上述技术方案中,优选地,步骤(2)中所述半成品a、硅铝溶胶和增强剂的质量比例为,硅铝溶胶:半成品a=(0.1-0.5):1;增强剂:半成品a=(0.005-0.03):1。
19.上述技术方案中,优选地,步骤(2)中将半成品a、硅铝溶胶和增强剂接触得到半成品b的过程为:将硅铝溶胶和增强剂在40-60℃混合搅拌2-5小时,然后加入半成品a在密闭空间中加热处理,处理温度为120-170℃,处理时间为12-72小时。
20.上述技术方案中,优选地,步骤(3)中将半成品b通过处理得到再生后的无粘结剂分子筛催化剂的过程为:将半成品b经干燥和焙烧,得到再生后的无粘结剂分子筛催化剂。其中,干燥条件如下:干燥温度为100-170℃,干燥时间为6-12小时;焙烧条件如下:焙烧温度为500-600℃,焙烧时间为5-10小时。
21.本发明另一方面提供了一种再生后的无粘结剂分子筛催化剂,其中由上述再生方法制得。
22.上述技术方案中,再生后的无粘结剂分子筛催化剂的堆密度为0.5-0.6g/ml,优选为0.52-0.58g/ml。优选地,再生后催化剂的堆密度与新鲜催化剂的堆密度相对比值为0.98-1.0。
23.上述技术方案中,优选地,再生的无粘结剂乙苯催化剂中骨架四配位铝占总铝的比例为98-100%,优选为99-100%。优选地,再生后催化剂骨架四配位铝占总铝的比例与新鲜催化剂骨架四配位铝占总铝的比例的相对比值为0.98-1.0。
24.本发明第三方面提供一种苯和乙烯气相烷基化的方法,采用再生后的无粘结剂分子筛催化剂。
25.上述技术方案中,所述的苯和乙烯气相烷基化的操作条件如下:反应温度330-400℃,反应压力为0.8-2.0mpa,乙烯质量空速为0.2-2.5h-1
,苯/乙烯摩尔比为4-7。
26.本发明具有如下有益效果:
27.1、本发明失活的无粘结剂分子筛催化剂的再生方法,能够使再生后的无粘结剂分子筛催化剂的堆密度较高,骨架四配位铝活性中心的恢复率高,催化剂的机械强度及催化
性能恢复到新鲜催化剂的水平。
28.2、本发明失活的无粘结剂分子筛催化剂的再生方法,特别适用于苯和乙烯气相烷基化催化剂,再生后的催化剂用于苯和乙烯气相烷基化反应中,活性高,选择性好,产物烃化液中二甲苯含量明显下降,可以达到600ppm以下,优选达到550ppm以下,恢复到新鲜催化剂的水平。
附图说明
29.图1为本发明实施例1再生的无粘结剂乙苯催化剂的铝核磁谱图;
30.图2为对比例1再生的无粘结剂乙苯催化剂的铝核磁谱图。
具体实施方式
31.下面结合具体实施方式对本发明进行详细的说明,但应当理解本发明的保护范围并不受具体实施方式的限制。
32.本发明中,再生的无粘结剂分子筛催化剂的堆密度以1000ml量筒为容器,加入400g催化剂后震动容器,待体积刻度线不再降低后,通过加入的催化剂重量除以实际体积计算得到堆密度,单位为g/ml。
33.本发明中,骨架四配位铝占总铝的比例通过铝核磁测试得到,采用美国varian公司生产的核磁共振仪进行测试,仪器型号为vnmrs-400wb,共振频率为104.2mhz,转速为10000rps,标准物为kal(so4)2·
12h2o。谱图中58ppm处的信号峰对应着骨架四配位铝状态,0ppm处的信号峰对应着骨架外六配位状态,58ppm处信号峰的面积占58ppm和0ppm处两个信号峰面积之和的比例,为骨架四配位铝占总铝的比例。
34.【实施例1】
35.本实施例用于失活的无粘结剂分子筛催化剂(乙苯催化剂,其由100wt%的zsm-5分子筛组成,机械强度为75n/cm)的再生,具体过程如下:将1吨失活的乙苯催化剂和20吨浓度为0.1wt%的盐酸水溶液混合,在密闭空间中于50℃搅拌10小时,结束后用去离子水洗除乙苯催化剂中的盐酸溶液,在100℃干燥12小时得到半成品a1。将600公斤白炭黑、133.2公斤十八水硫酸铝和900公斤去离子水混合均匀,在密闭空间中于80℃搅拌24小时得到硅铝溶胶。将100公斤硅铝溶胶和5公斤阿拉伯胶在60℃混合搅拌2小时,然后加入1吨半成品a1,在密闭空间中于120℃搅拌72小时得到半成品b1。将半成品b1在工业烘箱中于100℃烘干12小时,再在焙烧炉中于500℃焙烧10小时,得到再生后的乙苯催化剂c1。经测试,c1的堆密度为0.58g/ml。c1的铝核磁图谱如图1所示,仅在58ppm处出现一个信号峰,其骨架四配位铝占总铝的比例为100%。另外,新鲜乙苯催化剂的堆密度为0.59g/ml,骨架四配位铝占总铝的比例为100%;失活的乙苯催化剂的堆密度为0.50g/ml,骨架四配位铝占总铝的比例为85%。
36.【实施例2】
37.本实施例用于失活的无粘结剂分子筛催化剂(乙苯催化剂,其由100wt%的zsm-5分子筛组成,机械强度为70n/cm)的再生,具体过程如下:将1吨失活的乙苯催化剂和2吨浓度为5wt%的硫酸水溶液混合,在密闭空间中于100℃搅拌2小时,结束后用去离子水洗除乙苯催化剂中的硫酸溶液,在170℃烘干6小时得到半成品a2。将600公斤白炭黑、18.76公斤九
水硝酸铝和1800公斤去离子水混合均匀,在密闭空间中于120℃搅拌6小时得到硅铝溶胶。将500公斤硅铝溶胶和30公斤角叉胶在60℃混合搅拌2小时,然后加入1吨半成品a2,在密闭空间中于170℃搅拌12小时得到半成品b2。将半成品b2在工业烘箱中于170℃烘干6小时,再在焙烧炉中于600℃焙烧5小时,得到再生后的乙苯催化剂c2。经测试,c2的堆密度为0.52g/ml。c2的铝核磁图谱也仅在58ppm处出现一个信号峰,其骨架四配位铝占总铝的比例为100%。另外,新鲜乙苯催化剂的堆密度为0.52g/ml,骨架四配位铝占总铝的比例为100%;失活的乙苯催化剂的堆密度为0.46g/ml,骨架四配位铝占总铝的比例为88%。
38.【实施例3】
39.本实施例用于失活的无粘结剂分子筛催化剂(乙苯催化剂,其由100wt%的zsm-5分子筛组成,机械强度为72n/cm)的再生,具体过程如下:将1吨失活的乙苯催化剂和10吨浓度为3wt%的草酸水溶液混合,在密闭空间中于80℃搅拌5小时,结束后用去离子水洗除乙苯催化剂中的草酸溶液,在140℃烘干8小时得到半成品a3。将600公斤硅粉、18.76公斤九水硝酸铝和1000公斤去离子水混合均匀,在密闭空间中于100℃搅拌12小时得到硅铝溶胶。将300公斤硅铝溶胶和10公斤果胶在60℃混合搅拌2小时,然后加入1吨半成品a3,在密闭空间中于140℃搅拌26小时得到半成品b3。将半成品b3在工业烘箱中于140℃烘干9小时,再在焙烧炉中于560℃焙烧7小时,得到再生后的乙苯催化剂c3。经测试,c3的堆密度为0.56g/ml。根据c3的铝核磁图谱中58ppm和0ppm处两个信号峰的面积,计算其骨架四配位铝占总铝的比例为99%。另外,新鲜乙苯催化剂的堆密度为0.56g/ml,骨架四配位铝占总铝的比例为100%;失活的乙苯催化剂的堆密度为0.48g/ml,骨架四配位铝占总铝的比例为91%。
40.【实施例4】
41.本实施例用于失活的无粘结剂分子筛催化剂(乙苯催化剂,其由100wt%的zsm-5分子筛组成,机械强度为74n/cm)的再生,具体过程如下:将1吨失活的乙苯催化剂和20吨浓度为0.1wt%的盐酸水溶液混合,在密闭空间中于50℃搅拌10小时,结束后用去离子水洗除乙苯催化剂中的盐酸溶液,在100℃干燥12小时得到半成品a4。将600公斤白炭黑、133.2公斤十八水硫酸铝和900公斤去离子水混合均匀,在密闭空间中于80℃搅拌24小时得到硅铝溶胶。将100公斤硅铝溶胶和5公斤藻蛋白酸钠在60℃混合搅拌2小时,然后加入1吨半成品a4,在密闭空间中于120℃搅拌72小时得到半成品b4。将半成品b4在工业烘箱中于100℃烘干12小时,再在焙烧炉中于500℃焙烧10小时,得到再生后的乙苯催化剂c4。经测试,c4的堆密度为0.55g/ml。c4的铝核磁图谱仅在58ppm处出现一个信号峰,其骨架四配位铝占总铝的比例为100%。另外,新鲜乙苯催化剂的堆密度为0.55g/ml,骨架四配位铝占总铝的比例为100%;失活的乙苯催化剂的堆密度为0.49g/ml,骨架四配位铝占总铝的比例为84%。
42.【对比例1】
43.参照专利cn105597842b的方法对失活的无粘结剂乙苯催化剂进行再生,具体过程如下:将反应器中失活的无粘结剂分子筛催化剂(同实施例1的失活的乙苯催化剂)卸出后,用1.5wt%的四丁基氢氧化铵溶液处理5小时,其中,失活催化剂和四丁基氢氧化铵溶液的固液比为15:1、处理温度为85℃;然后将催化剂在氮气气氛下于145℃烘干4小时;最后将催化剂在空气气氛下550℃高温焙烧5小时,制得再生的乙苯催化剂d1。经测试,d1的堆密度为0.46g/ml。d1的铝核磁图谱如图2所示,根据d1的铝核磁图谱中58ppm和0ppm处两个信号峰的面积,计算其骨架四配位铝占总铝的比例为82%。
44.【对比例2】
45.将失活的无粘结剂分子筛催化剂(同实施例1的失活的乙苯催化剂)在焙烧炉中于600℃焙烧5小时,得到再生的乙苯催化剂d2。经测试,d2的堆密度为0.48g/ml。根据铝核磁图谱中58ppm和0ppm处两个信号峰的面积,计算d2骨架四配位铝占总铝的比例为85%。
46.【实施例4】
47.将实施例1-4及对比例1-2再生的无粘结剂乙苯催化剂c1-c4以及d1-d2,和实施例1-3中新鲜催化剂分别应用到苯和乙烯气相烷基化反应中,在反应温度370℃,压力为1.6mpa,乙烯质量空速为0.6h-1
,苯和乙烯摩尔比为5的条件下,测试烃化液中二甲苯含量、乙烯转化率以及乙基选择性。测试结果见下表1。
48.表1苯和乙烯气相烷基化反应结果
[0049][0050]
以上详细描述了本发明的具体实施方式,但是,本发明并不限于此。在本发明的技术构思范围内,可以对本发明的技术方案进行多种简单变型,包括各个技术特征以任何其它的合适方式进行组合,这些简单变型和组合同样应当视为本发明所公开的内容,均属于本发明的保护范围。