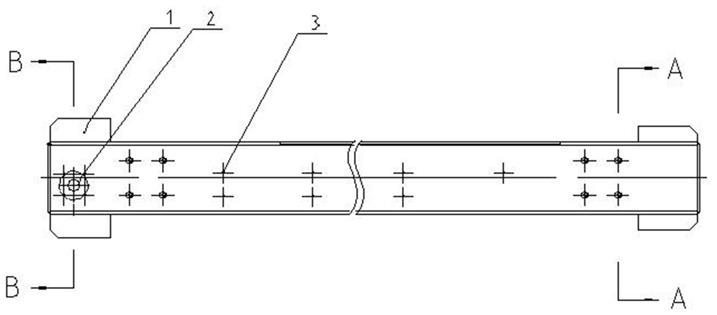
1.本实用新型涉及压滤机领域,尤其涉及一种压滤机复合拼焊式主梁。
背景技术:2.现有技术中压滤机主梁的结构大部分采用实心钢板形式,如需满足主梁较长跨度的抗弯性能和液压缸大作用力的抗拉性能,需要主梁实心钢板很厚,这样就造成资源的浪费和制造成本的增加。
3.专利号201010221700.5采用厢体式梁,其内设置纵横交错的加强板来满足力学性能,其加大了焊接难度且焊接工时增加。上、下止推板体采用固定销的形式在油缸大拉伸力的作用下有受剪切力开裂、断裂风险。主梁固定采用空心钢管对穿螺套,在大的轴向拉伸力作用下会有套管变形或剪断风险。由此可能会使操作人员的人生安全受到威胁。
技术实现要素:4.为解决上述技术问题,本实用新型设计了一种压滤机复合拼焊式主梁。
5.本实用新型采用如下技术方案:一种压滤机复合拼焊式主梁,包括主梁主体和主梁主体两侧设置的止推板,主梁主体还包括上板、下板、左板、右板,上板和下板内侧分别对应垂直固定连接有支撑筋板,左板和右板通过支撑筋板垂直定位与上板和下板焊接固定,组成厢体式结构,能够大幅降低钢材使用量,并且保证其焊接垂直度、平行度,解决了现有技术中焊接过程中变形等问题。
6.作为优选,止推板与主梁主体采用实心板打坡口塞焊方式焊接。
7.作为优选,左板和右板分别对应设置有链轮座安装孔和链条槽安装孔。
8.作为优选,主梁主体上设置有连接螺套,连接螺套采用嵌入式固定实心螺纹套。
9.作为优选,上板顶部设置有不锈钢平行导轨贴板。
10.本实用新型的有益效果是:
11.(1)、采用实心板打坡口塞焊的形式使主梁上下止推板体承受较大油缸拉伸作用力的情况下不断裂,不变形;
12.(2)、厢体式结构能够大幅降低钢材使用量,节省成本,保证其焊接垂直度、平行度,解决了现有技术中焊接过程中变形等问题;
13.(3)、主梁上附加有链轮座和链条槽安装孔,起到固定、定位拉板系统链传动机构的作用;
14.(4)、采用嵌入式实心固定螺套的结构,增大承受轴向拉伸力的抗剪力学性能,避免此处应力集中引起的套筒断裂风险;
15.(5)、不锈钢平行导轨贴板,解决了压滤机滤板在移动过程中摩擦力大,容易刮伤主梁所喷漆面的问题。
附图说明
16.图1是本实用新型的一种结构示意图;
17.图2是图1的a
‑
a、b
‑
b剖面图;
18.图中:1、止推板,2、链轮座安装孔,3、链条槽安装孔,4、平行导轨贴板,5、上板,6、主梁连接螺套,7、左板,8、右板,9、支撑筋板,10、下板。
具体实施方式
19.下面通过具体实施例,并结合附图,对本实用新型的技术方案作进一步的具体描述:
20.实施例:如附图1和附图2所示,一种压滤机复合拼焊式主梁,先将所有板件通过自动切割机下料为后道工序做准备,包括主梁主体和主梁主体两侧设置的止推板1,主梁主体还包括上板5、下板10、左板7、右板8,上板5和下板内10侧分别对应垂直固定连接有支撑筋板9,左板7和右板8通过支撑筋板9垂直定位与上板5和下板10焊接固定,组成厢体式结构,能够大幅降低钢材使用量,并且保证其焊接垂直度、平行度,解决了现有技术中焊接过程中变形等问题。将主梁左板7放置在支撑筋板9上,在自动埋弧焊机上塞焊连接左板7、上板5和下板10,使其完全熔透,满足力学性能。翻转主梁左板7使其底部放置在专用夹具水平台上,放置右板8在支撑筋板9上。使用同样的工艺埋弧焊塞焊右板8、上板5和下板10,使其完全熔透。此时拼焊式主梁主体结构成型。主梁止推板1切割下料后在底部打坡口,采用实心板打坡口塞焊的形式使主梁上下止推板1体承受较大油缸拉伸作用力的情况下不断裂,不变形。并采用二氧化碳气体保护焊的方式将止推板1、上板5和下板10焊接固定。将焊接完毕的拼焊式主梁放置在摇臂钻床上,对主梁左板7和右板8划线打孔,打出相应的链轮座安装孔2,主梁固定螺套镶嵌孔,链条槽安装孔3。金加工主梁连接螺套6,主梁连接螺套6采用嵌入式实心螺纹套,增大承受轴向拉伸力的抗剪力学性能,避免此处应力集中引起的套筒断裂风险。将主梁连接螺套6嵌入拼焊式主梁孔内,采用二氧化碳气体保护焊焊接固定。将主梁平行导轨贴片4放置在拼焊式主梁上板5顶部,采用二氧化碳气体保护焊断续焊接固定,平行导轨贴片4解决压滤机滤板在移动过程中摩擦力大,刮伤主梁所喷面漆的问题。
21.以上所述的实施例只是本实用新型的一种较佳的方案,并非对本实用新型作任何形式上的限制,在不超出权利要求所记载的技术方案的前提下还有其它的变体及改型。