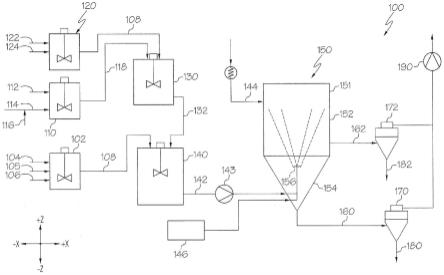
用于烯烃复分解和裂化的双功能复合催化剂
1.相关申请的交叉引用
2.本技术要求于2019年12月2日提交的美国非临时专利申请序列号16/700,197的优先权,其全部内容通过引用并入本公开。
技术领域
3.本公开涉及烃加工,特别是复合催化剂和制备用于进行烯烃复分解和裂化的复合催化剂的方法。
背景技术:4.近年来,对丙烯的需求急剧增加,以供应不断增长的聚丙烯、环氧丙烷和丙烯酸市场。目前,全球生产的丙烯(7400万吨/年)中大多数是来自主要生产乙烯的蒸汽裂化装置的副产物(57%),或是来自主要生产汽油的流化催化裂化(fcc)装置的副产物(30%)。这些方法无法充分应对丙烯需求的快速增长。
5.由含丁烯流(诸如萃余液流或其他含丁烯流)生产丙烯可以通过将丁烯复分解成丙烯和其他化合物并且组合裂化、异构化或两者来完成。一些丙烯工艺包括复分解、异构化和裂化,以便增加反应系统的总产率和丙烯选择性。这些类型的反应中的每种反应可能需要不同类型的催化剂,诸如用于裂化反应的裂化催化剂、用于复分解反应的复分解催化剂和用于异构化反应的异构化催化剂。在用于将丁烯转化为丙烯的常规反应系统中,单独的催化剂可以在单独的催化剂区中分离,诸如通过将每种单独的催化剂装入单独的反应器或通过将催化剂装入单个反应器,并且用惰性间隔物诸如石英棉或碳化硅分离每种催化剂。将催化剂分离到单独的反应器容器中显著增加了反应系统的初始资本成本。此外,用惰性间隔物分离催化剂会在反应器中产生死体积,这可能降低反应器的效率。
6.为了降低成本并且消除死区,可以使用两种或更多种单独的固体颗粒催化剂材料的物理催化剂混合物。然而,由于随着持续使用和处理而发生沉降,不同固体催化剂材料的这些物理催化剂混合物可能会随着时间推移而逐渐在反应器中分离。例如,当单独的固体颗粒催化剂材料的物理性质相对于物理催化剂混合物中的其他催化剂材料显著不同时,这种分离或沉降效应可能变得越来越剧烈。因此,随着单独的催化剂通过沉降而分离,固体催化剂颗粒的物理催化剂混合物的有效性可能随着时间推移而降低。
技术实现要素:7.因此,存在对于多功能复合催化剂和合成复合催化剂的方法的持续需要。本公开涉及多功能复合催化剂和生产复合催化剂的方法。本公开的复合催化剂可以包括多个复合催化剂颗粒并且每个复合催化剂颗粒可以包括多个不同的催化活性成分。复合催化剂中的多种催化活性成分中的每种催化活性成分可以为复合催化剂颗粒提供不同的催化功能。因此,多功能复合催化剂可以将多个催化功能组合到单个颗粒中。特别地,本公开的复合催化剂可以包括至少部分或完全嵌入催化剂载体材料中的沸石颗粒和沉积在催化剂载体材料、
沸石颗粒或两者的表面上的催化活性化合物。复合催化剂可以具有催化活性化合物在催化剂载体材料、沸石颗粒或两者的外表面和孔表面上的均匀分布。因此,复合催化剂可以具有基本均匀的物理性质并且不会遇到与物理催化剂混合物的沉降相关联的缺点。多功能复合催化剂可以使得能够将单个颗粒催化剂装入反应器中以进行多种不同的化学反应,例如,诸如用于由2-丁烯产生丙烯的异构化、复分解和裂化的组合。
8.根据本公开的实施方案,一种制备复合催化剂的方法可以包括:将催化剂载体材料、沸石颗粒、三嵌段共聚物表面活性剂、催化活性化合物前体和稀释剂组合以产生催化剂前体组合物。该方法还可以包括:混合催化剂前体组合物以产生催化剂前体混合物,其中催化剂载体材料和沸石颗粒悬浮在稀释剂中;以及喷雾干燥催化剂前体混合物。喷雾干燥可以包括:雾化催化剂前体混合物以产生多个液滴;以及在干燥室中干燥所述多个液滴。干燥可以使从所述多个液滴中的每个液滴中除去稀释剂以形成包含至少部分地固定在催化剂载体材料内的沸石颗粒的附聚物。干燥还可以使催化活性化合物前体反应以形成沉积在催化剂载体材料、沸石颗粒或两者的外表面和孔表面上的催化活性化合物。
9.根据本公开的实施方案,一种用于生产丙烯的方法可以包括:使含丁烯进料与复合催化剂在反应温度下接触。该接触可以使丁烯的至少一部分历经化学反应以产生包含至少丙烯的反应流出物。复合催化剂可以通过可以包括以下的方法制备:将催化剂载体材料、沸石颗粒、三嵌段共聚物表面活性剂、催化活性化合物前体和稀释剂组合以产生催化剂前体组合物。制备复合催化剂的方法还可以包括:混合催化剂前体组合物以产生催化剂前体混合物,其中催化剂载体材料和沸石颗粒悬浮在稀释剂中;以及喷雾干燥催化剂前体混合物。喷雾干燥可以包括:雾化催化剂前体混合物以产生多个液滴;以及在干燥室中干燥所述多个液滴。干燥可以使从所述多个液滴中的每个液滴中除去稀释剂以形成包含至少部分地固定在催化剂载体材料内的沸石颗粒的附聚物。干燥还可以使催化活性化合物前体反应以形成沉积在催化剂载体材料、沸石颗粒或两者的外表面和孔表面上的催化活性化合物。用于生产丙烯的方法还可以包括:从反应器流出物中分离丙烯的至少一部分。
10.所描述的实施方案的附加特征和优点将在下面的具体实施方式中阐述,并部分对本领域技术人员而言根据该具体实施方式将是显而易见的,或通过实践所描述的实施方案,包括具体实施方式、权利要求以及附图而认识到。
附图说明
11.对本公开的特定实施方案的以下详细描述在结合以下附图阅读时可最好地理解,在附图中用相同的附图标记指示相同的结构并且在附图中:
12.图1示意性地描绘了根据本公开中所示和所述的一个或多个实施方案的用于制备复合催化剂的喷雾干燥器系统;
13.图2示意性地描绘了根据本公开中所示和所述的一个或多个实施方案的用于进行复分解反应的反应器系统;
14.图3图解地描绘了根据本公开中所示和所述的一个或多个实施方案的丝光沸石骨架倒置(inverted)(mfi)结构沸石的x射线衍射(xrd)曲线;
15.图4图解地描绘了现有技术的复分解催化剂的xrd曲线,所述复分解催化剂包含负载在介孔二氧化硅载体上的氧化钨;
16.图5图解地描绘了根据本公开中所示和所述的一个或多个实施方案的复合催化剂的xrd曲线;
17.图6图解地描绘了根据本公开中所示和所述的一个或多个实施方案的来自用图5的复合催化剂进行的复分解反应的乙烯、丙烯、c5烃和c6+烃的总转化率和产率;以及
18.图7图解地描绘了来自用包含图3的mfi结构沸石和图4的现有技术的复分解催化剂的双催化剂体系进行的复分解反应的乙烯、丙烯、c5烃和c6+烃的总转化率和产率。
19.出于描述图1和图2的简化示意性图示和描述的目的,未包含在某些化学加工操作领域中可以采用且为所述领域的普通技术人员所熟知的众多阀、温度传感器、电子控制器和类似的加工部件。另外,可以不对通常包含在典型的化学加工操作、载气供应系统、泵、容器搅拌器、压缩机、熔炉或其他子系统中的伴随部件进行描绘。应当理解,这些部件和子系统处于所公开的本发明实施方案的精神和范围内。然而,可以在本公开中所描述的实施方案中添加操作部件,诸如本公开中所描述的那些部件。
20.附图中的箭头指代工艺流。然而,箭头可以等效地指代可以用于在两个或更多个系统部件之间传输工艺流的传输线。此外,连接到系统部件的箭头可以限定每个给定系统部件中的入口或出口。箭头方向通常对应于包含在箭头所指的物理传输线内的流的材料的主要移动方向。另外,未连接两个或更多个系统部件的箭头可以表示离开所描绘的系统的产物流或进入所描绘的系统的系统入口流。产物流可以在伴随系统中被进一步加工,或者可以商业化为最终产物。
21.此外,附图中的箭头可以示意性地描绘将流从一个系统部件运输到另一个系统部件的工艺步骤。例如,从一个系统部件指向另一个系统部件的箭头可以表示将系统部件流出物“传递”到另一个系统部件,所述传递可以包括:工艺流的内容物“离开”一个系统部件或从一个系统部件中被“除去”以及将该产物流的内容物“引入”另一个系统部件。
22.应当理解,当两条或更多条线在图1和图2的示意性流程图中相交时,两个或更多个工艺流“混合”或“组合”。混合或组合还可以包括:通过将两股流直接引入诸如容器、反应器、分离器或其他系统部件等类似的系统部件中来进行混合。例如,应当理解,当两股流被描绘为在进入系统部件之前直接组合时,可以等效地将流引入系统部件中并且可以在系统部件中进行混合。
23.现在将更详细地参考各个实施方案,在附图中示出了其中一些实施方案。在任何可能的情况下,将贯穿附图使用相同的附图标记来指代相同或相似的部分。
具体实施方式
24.本公开涉及多功能复合催化剂和制备复合催化剂的方法。特别地,复合催化剂可以包括:催化剂载体材料;至少部分或完全嵌入催化剂载体材料内的沸石颗粒;以及在催化剂载体材料、沸石颗粒或两者的外表面和孔表面处提供催化活性位点的催化活性化合物。复合催化剂可以通过喷雾干燥法制备,所述喷雾干燥法包括:将催化剂载体材料、沸石颗粒、三嵌段共聚物表面活性剂、至少一种催化活性化合物前体和稀释剂组合以产生催化剂前体组合物。该方法还可以包括:混合催化剂前体组合物以产生催化剂前体混合物,其中催化剂载体材料和沸石颗粒悬浮在稀释剂中。该方法还可以包括:喷雾干燥催化剂前体混合物,其可以包括雾化催化剂前体混合物以产生多个液滴并在干燥室中干燥液滴。该干燥可
以使从液滴中除去稀释剂以形成包含至少部分地固定在催化剂载体材料内的沸石颗粒的附聚物,并且可以使催化活性化合物前体反应以形成沉积在催化剂载体材料、沸石颗粒或两者的外表面和孔表面上的催化活性化合物。
25.复合催化剂可以提供具有多种不同催化物种的多功能催化剂,每种催化物种可以能够独立于复合催化剂中的其他催化物种而催化不同的反应。例如,复合催化剂可以用于通过复分解将2-丁烯转化为丙烯,并且可以包括沸石颗粒和金属氧化物(诸如但不限于氧化钨)作为催化活性化合物。金属氧化物可以具有催化活性以使1-丁烯和2-丁烯交叉复分解以产生丙烯、戊烯和任选的其他c6+烯烃。沸石颗粒可以在复分解反应期间催化戊烯或其他c6+烯烃裂化成丙烯和其他较小的烯烃。
26.复合催化剂可以使得反应系统能够在无需处理和管理多种催化剂材料的情况下执行多种催化反应,诸如复分解和裂化。另外,使用复合催化剂可以消除或减少在反应器中安装间隔物材料以分离具有不同催化剂的催化剂床的需要。这可以消除或减少来自反应器的死区。死区是诸如由于惰性间隔材料的存在而无反应发生的区。在一些常规的反应系统中,两种单独的干燥颗粒催化剂的共混物或物理混合物可以被制备并装入反应器。尽管两种颗粒催化剂的干燥共混物最初可以在反应器系统内提供多功能催化环境,但颗粒催化剂之一最终可以在重力作用下沉降到反应器的底部,这可以形成将该两种共混催化剂分离到反应器中的单独区中。随着单独的催化剂沉降并在催化剂床内形成具有不同浓度的两种共混催化剂的区时,这种分离可能导致反应系统效率的不期望的变化。本公开中所描述的复合催化剂可以减少或消除与共混催化剂在反应系统中随时间推移而沉析相关联的问题。
27.如本公开中所使用的,“催化剂”可以指包含至少一种催化活性化合物的固体颗粒,该催化活性化合物增加特定化学反应的速率、增加反应中某些产物的选择性产生或两者兼有。
28.如贯穿本公开所使用的,术语“介孔”可以指材料具有从2纳米(nm)到50nm的平均孔径。
29.如本公开中所使用的,“催化活性化合物”可以指增加特定化学反应的速率、增加反应中某些产物的选择性产生或两者兼有的物质。催化活性化合物和用本公开中所描述的催化活性化合物制备的催化剂可以用于促进各种反应,诸如但不限于异构化、复分解、裂化、氢化、脱金属、脱硫、脱氮、其他反应或这些的组合。
30.如本公开中所使用的,“催化活性”可以指催化剂或催化活性化合物增加反应的反应速率的程度。与催化活性较小的催化剂相比,催化活性较大的催化剂增加反应的反应速率。
31.如本公开中所使用的,“稳定的”混合物是指固-液混合物,其中液体部分包含不从液体部分沉淀出来的溶解固体。例如,稳定的混合物的液体部分中的溶解固体不会在本文所公开的方法的后续加工步骤期间沉淀出来。
32.如贯穿本公开所使用的,术语“丁烯(butene)”或“丁烯(butenes)”可以指包含1-丁烯、反式-2-丁烯、顺式-2-丁烯、异丁烯或这些异构体的混合物中的一者或多者的组合物。如贯穿本公开所使用的,术语“正丁烯”可以指包含1-丁烯、反式-2-丁烯、顺式-2-丁烯或这些异构体的混合物中的一者或多者且不包含异丁烯的组合物。如贯穿本公开所使用的,术语“2-丁烯”可以指反式-2-丁烯、顺式-2-丁烯或这两种异构体的混合物。
33.如前所述,复合催化剂可以是喷雾干燥的催化剂,其包含至少部分或完全被以下附聚物包围或嵌入以下附聚物中的沸石颗粒:所述附聚物由催化剂载体材料和沉积在催化剂载体材料、沸石颗粒或两者的表面上的至少一种催化活性化合物形成。催化剂载体材料和沸石颗粒的附聚物可以通过在喷雾干燥期间催化剂载体材料的附聚来形成。催化剂载体材料可以是金属或准金属的氧化物,诸如硅、铝、钛、铈中的一者或多者的氧化物或这些的组合。催化剂载体材料可以是二氧化硅、气相二氧化硅、氧化铝、气相氧化铝、二氧化钛、气相二氧化钛、二氧化铈、气相二氧化铈或这些的组合。
34.在一个或多个实施方案中,催化剂载体材料可以是二氧化硅。适用于制备复合催化剂的二氧化硅催化剂载体材料的实例可以包括介孔二氧化硅载体。介孔二氧化硅载体可以具有从2.5纳米(nm)到40nm的平均孔径以及至少0.600毫升每克(ml/g)的总孔体积。在一个或多个实施方案中,催化剂载体材料的二氧化硅可以具有从2.5nm到40nm、或从2.5nm到20nm、或从2.5nm到4.5nm、或从2.5nm到3.5nm、或从8nm到18nm、或从12nm到18nm的平均孔径。适用于催化剂载体材料的二氧化硅载体可以具有从0.600ml/g到2.5ml/g、或从0.600ml/g到1.5ml/g、或从0.600ml/g到1.3ml/g、或从0.600ml/g到0.800ml/g、或从0.600ml/g到0.700ml/g、或从0.900ml/g到1.3ml/g的总孔体积。适用于催化剂载体材料的二氧化硅载体可以具有从250平方米每克(m2/g)到600m2/g的表面积。二氧化硅载体可以具有从450m2/g到600m2/g、或从250m2/g到500m2/g、或从275m2/g到400m2/g、或从275m2/g到350m2/g的表面积。
35.在一个或多于一个实施方案中,二氧化硅载体可以基本上不含可能对系统的催化活性产生不利影响的外来金属或元素。如本公开中使用的,术语“基本上不含”某种组分可以指组合物(诸如催化剂载体材料、沸石、催化剂或催化剂前体混合物)具有在该组合物中小于1重量百分比(wt.%)的该组分。例如,基本上不含外来金属或元素的二氧化硅载体可以包含小于1wt.%的这些外来金属或元素。一种合适的二氧化硅载体可以是santa barbara无定形(sba-15)介孔二氧化硅分子筛。替代性地,二氧化硅载体的另一个合适的实例可以是二氧化硅载体(可从总部位于日本爱知县的富士硅化学株式会社(fuji silysia chemical ltd)商购获得)。在一个或多个实施方案中,催化剂载体材料可以是q-10级二氧化硅载体颗粒,其具有10nm的平均孔径、1ml/g的孔体积、300m2/g的表面积以及从75微米(μm)到150μm的平均粒度。在一个或多个实施方案中,催化剂载体材料可以是q-10级二氧化硅颗粒,其具有从75μm到500μm的平均粒度。
36.本公开的复合催化剂和制备复合催化剂的方法利用预制的催化剂载体颗粒(诸如二氧化硅或其他金属氧化物颗粒)代替其他催化剂载体源用于催化剂载体材料。因此,本公开用于制备复合催化剂的方法可以不包括在喷雾干燥之前、在喷雾干燥过程期间或在附加的煅烧步骤期间由一种或多种前体形成催化剂载体材料(诸如由一种或多种二氧化硅前体制备二氧化硅)的步骤。最初提供具有表面积、孔径和孔体积的最佳性质的预制催化剂载体材料引起可靠地形成均匀的催化剂组合物。二氧化硅前体(诸如原硅酸四乙酯)的使用需要在喷雾干燥器中形成sio2的附加步骤,并且不会产生均匀的负载结构。此外,当使用二氧化硅前体时,催化活性化合物前体的至少一部分可能被捕获在二氧化硅内而不是沉积在二氧化硅表面上,这可能致使这部分催化活性化合物无法使用,并可能增加所需的昂贵的催化活性化合物前体的量。因此,复分解反应中的丙烯选择性和产率受到影响。
37.复合催化剂可以包括足以形成以下附聚物的量的催化剂载体材料:所述附聚物部分或完全包围和截留催化剂载体材料的附聚物内的沸石颗粒。基于复合催化剂的总重量,复合催化剂可以具有从20wt.%到90wt.%的催化剂载体材料。基于复合催化剂的总重量,复合催化剂可以包含从20wt.%到85wt.%、从20wt.%到80wt.%、从20wt.%到75wt.%、从20wt.%到70wt.%、从20wt.%到60wt.%、从30wt.%到90wt.%、从30wt.%到85wt.%、从30wt.%到80wt.%、从30wt.%到75wt.%、从30wt.%到70wt.%、从50wt.%到90wt.%、从50wt.%到85wt.%、从50wt.%到80wt.%、从50wt.%到75wt.%、从50wt.%到70wt.%、从60wt.%到90wt.%、从60wt.%到85wt.%或从60wt.%到85wt.%的催化剂载体材料。
38.如前所述,复合催化剂还可以包括至少部分或完全被催化剂载体材料包围或嵌入催化剂载体材料中的沸石颗粒。沸石颗粒可以包括一种或多于一种沸石组合物。如本公开中所使用的,沸石组合物是指具有特定沸石骨架结构并具有特定材料组成的沸石。因此,沸石组合物可以通过骨架结构、组成或两者而彼此不同。沸石组合物可以分组成“沸石类型”,诸如mfi骨架类型沸石(诸如zsm-5沸石)、fau骨架类型沸石(诸如y沸石)或*bea骨架类型沸石(诸如β沸石),所述沸石类型中的每种沸石类型随后在本公开中进行描述。具有其他骨架类型和组成的其他沸石类型也可以用于产生复合催化剂。
39.在一个或多个实施方案中,沸石颗粒可以包含一种或多种mfi骨架类型沸石,诸如zsm-5。如本公开中所使用的,“zsm-5”是指具有根据国际纯化学与应用化学联合会(iupac)沸石命名法的mfi骨架类型且由二氧化硅和氧化铝组成的沸石。zsm-5是指“zeolite socony mobil-5”并且是pentasil族沸石,其可以由化学式nanalnsi
96-no192
·
16h2o表示,其中0《n《27。可商购获得的沸石zsm-5的实例包括但不限于cbv2314、cbv3024e、cbv5524g和cbv28014(可从分子筛催化剂国际公司(zeolyst international)获得)。mfi骨架类型沸石可以包含一种或多种含磷化合物,诸如氧化磷,诸如五氧化二磷(“p2o
5”)。
40.在一个或多个实施方案中,催化剂组合物可以包含fau骨架类型沸石,诸如y沸石。如本公开中所使用的,“y沸石”是指具有根据iupac沸石命名法的fau骨架类型且由二氧化硅和氧化铝组成的沸石,其中二氧化硅与氧化铝的摩尔比为至少3。例如,y沸石中二氧化硅与氧化铝的摩尔比可以为至少5、至少12或甚至至少30,诸如从5到30、从12到30或从约15到约30。y沸石的晶胞大小可以为从约24埃到约25埃,诸如24.56埃。
41.在一个或多个实施方案中,催化剂组合物可以包含一种或多种*bea骨架类型沸石,诸如β沸石。如本公开中所使用的,“β沸石”是指具有根据iupac沸石命名法的*bea骨架类型且由二氧化硅和氧化铝组成的沸石。β沸石中二氧化硅与氧化铝的摩尔比可以为至少10、至少25或甚至至少100。例如,β沸石中二氧化硅与氧化铝的摩尔比可以为从5到500、诸如从25到300。可商购获得的β沸石组合物的实例可以包括但不限于(由分子筛催化剂国际公司生产的)cp814c、cp814e和cp811c-300。β沸石可以呈h-β的形式。h-β是指通常经由煅烧衍生自铵-β(nh
4-β)的酸性形式的β沸石。在一个或多个实施方案中,β沸石可以通过与磷酸(h3po4)直接反应或通过用磷酸氢二铵((nh4)2hpo4)浸渍来稳定。根据一个或多个实施方案,*bea骨架类型沸石可以包含一种或多种含磷化合物,诸如氧化磷或五氧化二磷(“p2o
5”)。
42.沸石颗粒可以具有从10:1到6000:1的二氧化硅与氧化铝的重量比。例如,基于沸石的总重量,沸石可以具有从10:1到4000:1、从10:1到2000:1、从10:1到1000:1、从10:1到
500:1、从10:1到300:1、从100:1到6000:1、从100:1到4000:1、从100:1到2000:1、从100:1到1000:1、从100:1到500:1、从200:1到6000:1、从200:1到4000:1、从200:1到2000:1、从200:1到1000:1、从200:1到500:1、从500:1到6000:1、从500:1到4000:1、从500:1到2000:1、从500:1到1000:1、从1000:1到6000:1、从1000:1到4000:1或从1000:1到2000:1的二氧化硅与氧化铝的重量比。在一种或多种实施方案中,沸石颗粒可以是mfi 2000沸石裂化催化剂,其具有2000:1的二氧化硅与氧化铝的重量比。
43.沸石颗粒的平均粒度可以小于复合催化剂的平均粒度。沸石颗粒可以具有小于或等于35μm、小于或等于30μm、小于或等于25μm、或甚至小于或等于20μm的平均粒度。沸石颗粒可以具有大于或等于5μm、大于或等于10μm、或甚至大于或等于15μm的平均粒度。沸石颗粒可以具有从5μm到35μm、从5μm到30μm、从5μm到25μm、从5μm到20μm、从10μm到35μm、从10μm到30μm、从10μm到25μm、从10μm到20μm、从15μm到35μm、从15μm到30μm、从15μm到25μm、从15μm到20μm、从5μm到10μm、或甚至从5μm到20μm的平均粒度。
44.复合催化剂可以包含足以在丁烯复分解期间进行催化裂化反应以产生丙烯和其他轻质烯烃的量的沸石颗粒。基于复合催化剂的总重量,复合催化剂可以包含从5wt.%到50wt.%的沸石颗粒。基于复合催化剂的总重量,复合催化剂可以包含从5wt.%到40wt.%、从5wt.%到30wt.%、从10wt.%到50wt.%、从10wt.%到40wt.%、从10wt.%到30wt.%、从15wt.%到50wt.%、从15wt.%到40wt.%、从15wt.%到30wt.%、或从20wt.%到30wt.%的沸石颗粒。
45.在一些实施方案中,本公开的复合催化剂颗粒可以是催化剂载体材料和沸石颗粒的附聚物。例如,催化剂载体材料和沸石颗粒可以形成附聚物,其中沸石颗粒至少部分或完全嵌入催化剂载体材料中。此外,催化活性化合物可以沉积在整个复合催化剂颗粒的表面上,并且可以在催化剂载体材料、沸石颗粒或两者的外表面和孔表面处产生催化活性位点。
46.如前所述,复合催化剂可以具有由催化剂载体材料、沸石颗粒或两者负载的至少一种催化活性化合物。催化活性化合物不同于沸石颗粒和催化剂载体材料。催化活性化合物可以包括具有促进复分解反应、异构化反应或两者的催化活性的化合物。催化活性化合物也可以起到从反应物流中除去污染物和催化剂毒物的作用。催化活性化合物可以包含复分解催化剂。在一个或多个实施方案中,催化活性化合物可以包含异构化催化剂。
47.催化活性化合物可以是金属、金属氧化物、其他催化活性化合物或这些的组合。催化活性化合物可以是金属,诸如但不限于铂、金、钯、铑、铱、铬、其他金属或这些的组合。催化活性化合物可以包含金属氧化物,诸如来自国际纯化学与应用化学联合会元素周期表(iupac周期表)的第6-10族的金属的一种或多于一种氧化物。金属氧化物可以包括钼、铼、钨、锰、钛、铈的至少一种氧化物或这些的任何组合。在一些实施方案中,金属氧化物可以是氧化钨。沉积在催化剂载体表面上的催化活性化合物的形态、类型和量可以决定复合催化剂的催化活性。
48.复合催化剂可以包含由催化剂载体材料、沸石颗粒或两者负载的一种或多种催化活性化合物。例如,复合催化剂可以包含1种、2种、3种、4种、5种、6种或多于6种催化活性化合物。理论上,可以并入复合催化剂中的不同催化活性化合物的数量可以是无限制的。然而,可以包含在复合催化剂中的不同催化活性化合物的数量可能受可以同时进行的反应类型限制。不同催化活性化合物的数量也可能受必须依次进行的反应限制。不同催化活性化
10族的金属的一种或多种氧化物的金属氧化物前体。金属氧化物可以是钼、铼、钨、锰、钛、铈的至少一种氧化物或这些的任何组合。替代性地,金属氧酸盐前体可以是钨酸盐前体。钨酸盐前体的实例可以包括但不限于偏钨酸铵((nh4)6h2w
12o40
)、仲钨酸铵、钨酸、磷钨酸、钨酸钠、其他钨酸盐前体或这些的组合。在一个或多个实施方案中,钨酸盐前体可以包括偏钨酸铵、偏钨酸铵六水合物或仲钨酸铵。在一个或多个实施方案中,金属氧酸盐前体可以是氧化钨(诸如氧化钨(iv)、氧化钨(vi))、其他钨氧化物或钨氧化物的组合。在一个或多个实施方案中,金属氧化物是氧化钨(wo3)。催化剂前体混合物可以包含多种催化活性化合物前体以产生复合催化剂,该复合催化剂具有沉积在催化剂载体材料、沸石颗粒或两者的外表面和孔表面上的多种催化活性化合物。
54.基于催化剂前体混合物的干重,催化剂前体混合物可以包含从0.1wt.%到25wt.%的催化活性化合物前体。基于催化剂前体混合物的干重,催化剂前体混合物可以包含从0.1wt.%到20wt.%、从0.1wt.%到15wt.%、从0.1wt.%到10wt.%、从0.1wt.%到8wt.%、从1wt.%到25wt.%、从1wt.%到20wt.%、从1wt.%到15wt.%、从1wt.%到10wt.%、从1wt.%到8wt.%、从4wt.%到25wt.%、从4wt.%到20wt.%、从4wt.%到15wt.%、从4wt.%到10wt.%、从4wt.%到8wt.%、从8wt.%到25wt.%、从8wt.%到20wt.%、从8wt.%到15wt.%、从6wt.%到8wt.%、从6wt.%到10wt.%、或从6wt.%到15wt.%的催化活性化合物前体。
55.聚合物表面活性剂可以包含在催化剂前体混合物中以增强催化活性化合物前体在催化剂前体混合物中的分散,从而改善催化活性化合物在催化剂载体材料、沸石颗粒或两者的表面上的分布。表面活性剂可以是对称三嵌段共聚物表面活性剂,诸如p123表面活性剂(可从总部位于美国新泽西州弗洛勒姆帕克的巴斯夫公司(basf corporation)获得),它是聚(乙二醇)-嵌段-聚(丙二醇)-嵌段-聚(乙二醇)共聚物(peg-ppg-peg共聚物)。三嵌段共聚物peg-ppg-peg由聚(环氧乙烷)(peo)和聚(环氧丙烷)(ppo)共聚单体组成,并且在高于288开尔文的温度下表现出疏水性,并在低于288开尔文的温度下表现出水溶性。这种双重特性引起形成包含peg-ppg-peg三嵌段共聚物的胶束。溶解的p123表面活性剂形成胶束,所述胶束用作制备结构化介孔二氧化硅(诸如sba-15)的骨架。相比之下,本文公开了三嵌段共聚物用于促进催化活性化合物(诸如氧化钨)在催化剂载体材料上的沉积的用途。在常规合成中,将表面活性剂添加到金属前体中,然后使该混合物经受热处理。金属前体分解生成金属氧化物。在本公开的方法和组合物中,表面活性剂可以用于增强催化剂前体混合物中催化剂载体材料(诸如二氧化硅载体)和催化活性化合物前体(诸如钨前体)之间的混合。由表面活性剂提供的增强混合可以改善催化活性化合物(诸如氧化钨)在热处理后在催化剂载体材料和沸石颗粒的表面上的分布。表面活性剂性质(诸如表面活性剂是离子型、阳离子型还是非离子型)在聚合物表面活性剂的有效性中起着重要作用。三嵌段共聚物的使用使得本公开的复合催化剂的大规模制备方法容易且可靠。
56.催化剂前体混合物可以具有足以将催化活性化合物前体均匀分散在整个催化剂前体混合物中的量的表面活性剂。基于催化剂前体混合物的干重,催化剂前体混合物可以包含从1wt.%到20wt.%的表面活性剂。基于催化剂前体混合物的干重,催化剂前体混合物可以包含从1wt.%到15wt.%、从1wt.%到18wt.%、从1wt.%到15wt.%、从5wt.%到
20wt.%、从5wt.%到18wt.%、从5wt.%到15wt.%、从8wt.%到20wt.%、从8wt.%到18wt.%、从8wt.%到15wt.%、从10wt.%到20wt.%、从10wt.%到18wt.%、或从10wt.%到15wt.%的表面活性剂。
57.稀释剂可以是水、有机溶剂或水与至少一种有机溶剂的组合。示例性有机溶剂可以包含甲醇、乙醇、丙酮或溶剂的组合。在一个或多个实施方案中,稀释剂可以是水,使得催化剂前体混合物是水性催化剂前体混合物。稀释剂还可以包括与醇(诸如乙醇)组合的水,这可以提高在制备催化剂前体混合物期间将三嵌段共聚物表面活性剂溶解在稀释剂中的能力。催化剂前体混合物可以具有足以使喷雾干燥器中的催化剂前体混合物雾化的量的稀释剂。催化剂前体混合物可以具有足以产生通过喷雾干燥法制备的复合催化剂颗粒的期望平均粒度的量的稀释剂。例如,由于催化剂载体材料、沸石颗粒、催化活性化合物前体和表面活性剂在每个液滴中的降低的浓度,增加稀释剂的量可以减小复合催化剂的平均粒度。基于催化剂前体混合物的总重量,催化剂前体混合物可以包含从50wt.%到95wt.%的稀释剂。例如,基于催化剂前体混合物的总重量,催化剂前体混合物可以包含从50wt.%到90wt.%、从50wt.%到85wt.%、从50wt.%到80wt.%、从70wt.%到95wt.%、从70wt.%到90wt.%、从70wt.%到85wt.%、从80wt.%到95wt.%、或从80wt.%到90wt.%的稀释剂。
58.参考图1,在图1中以附图标记142表示的催化剂前体混合物可以通过以下方式来制备:将催化剂载体材料、沸石颗粒、催化活性化合物前体、三嵌段共聚物表面活性剂和稀释剂组合以形成催化剂前体组合物,然后混合催化剂前体组合物以产生催化剂前体混合物。催化剂前体组合物可以通过一个或多个混合过程来制备。催化剂前体混合物142的制备可以包括第一混合过程102,该过程可以包括:将沸石颗粒104、催化剂载体材料105和稀释剂的第一部分106组合以产生第一混合物108。第一混合过程102还可以包括:在足以将固体沸石颗粒和固体催化剂载体材料分散在稀释剂中的条件下混合第一混合物108。第一混合过程102可以在具有混合器或搅拌器的容器中进行。在一个或多个实施方案中,该容器可以是喷雾干燥器150的进料容器。第一混合物108可以以大于或等于600转每分钟(rpm)、大于或等于700rpm、或甚至大于或等于800rpm、诸如从800rpm到1200rpm的转速混合。第一混合物108可以混合持续至少30分钟,诸如从30分钟到24小时。
59.催化剂前体混合物142的制备可以包括第二混合过程110,其中表面活性剂112(诸如三嵌段共聚物表面活性剂)可以与稀释剂的第二部分114组合,并且混合直到表面活性剂完全溶解在稀释剂中以产生第二混合物118。当表面活性剂是三嵌段共聚物表面活性剂时,稀释剂的第二部分114可以包括醇116,例如,诸如乙醇,其可以添加到稀释剂的第二部分114中。乙醇116可以帮助溶解表面活性剂112以形成均质的第二混合物118。第二混合物118可以在具有混合器或搅拌器的容器中制备,并且可以在足以使表面活性剂112完全溶解在稀释剂中的条件下混合。例如,第二混合物118可以以大于或等于600rpm、大于或等于700rpm、或大于或等于800rpm、诸如从600rpm到2000rpm、或从700rpm到1500rpm的转速混合。第二混合物118可以混合持续至少30分钟(诸如从30分钟到24小时)的时间段。
60.催化剂前体混合物142的制备还可以包括第三混合过程110,其中至少一种催化活性化合物前体122可以与稀释剂(诸如水)的第三部分124组合,并且混合直到催化活性化合物前体122完全溶解在稀释剂的第三部分124中以产生第三混合物128。第三混合物128可以在具有混合器或搅拌器的容器中制备,并且可以在足以将催化活性化合物前体122完全溶
解在稀释剂中的条件下混合。例如,第三混合物128可以以大于或等于600rpm、大于或等于700rpm、或大于或等于800rpm、诸如从600rpm到2000rpm、或从700rpm到1500rpm的转速混合。第三混合物128可以混合持续至少30分钟(诸如从30分钟到24小时)的时间段。
61.仍然参考图1,催化剂前体混合物142的制备可以包括将第二混合物118和第三混合物128组合以产生第四混合物132,所述第四混合物包含表面活性剂112和溶解在稀释剂中的所述至少一种催化活性化合物前体122。第四混合物132可以在足以产生表面活性剂和催化活性化合物前体的均质混合物的条件下混合。
62.第四混合物132可以添加到第一混合物108中,所述第一混合物包含分散在稀释剂中以产生催化剂前体组合物的沸石颗粒和催化剂载体材料。第四混合物132和第一混合物108可以在喷雾干燥器150的进料容器140中组合。可以混合催化剂前体组合物以产生催化剂前体混合物142,其中催化剂载体材料和沸石颗粒悬浮在稀释剂中,并且在喷雾干燥期间不会从催化剂前体混合物142中沉淀或沉降出来。催化剂前体组合物可以在足以减少或防止催化剂载体材料、沸石颗粒或两者在喷雾干燥期间沉淀或沉降的条件下混合。催化剂前体组合物可以以高达700rpm(诸如从500rpm到700rpm)的转速混合。催化剂前体组合物可以混合足够的时间段以产生催化剂前体混合物,所述催化剂前体混合物可以是胶态混合物,其中催化剂载体颗粒、沸石颗粒或两者在喷雾干燥期间不沉淀或沉降。催化剂前体组合物可以混合持续大于或等于72小时(诸如从72小时到120小时,或从72小时到96小时)的时间段以产生催化剂前体混合物142。在混合之后,催化剂前体混合物142可以是胶态溶液,其可以是稳定的混合物。换句话说,在混合之后,催化剂前体混合物142可以是均质胶态混合物,与混合之前的催化剂前体组合物相比,所述均质胶态混合物可以具有降低的固体从溶液中脱出和沉降的倾向。当混合时间少于72小时时,催化剂前体混合物142可能不会形成稳定的胶态溶液,并且可能在喷雾干燥期间表现出催化剂载体材料的沉降,这可能对通过该方法生产的复合催化剂产生不利影响。这种沉降可能会影响喷雾干燥过程的效率,当复合催化剂用于复分解过程中时,这可能会降低产物产率。
63.基于催化剂前体混合物142的干重,催化剂前体混合物可以包含从20.0wt.%到85.0wt.%的催化剂载体材料104、从5.0wt.%到50.0wt.%的沸石颗粒105、从1wt.%到20wt.%的表面活性剂以及从0.1wt.%到25.0wt.%的催化活性化合物前体。基于催化剂前体混合物142的总重量,催化剂前体混合物142可以具有从1wt.%到50wt.%、从1wt.%到30wt.%、从1wt.%到20wt.%、从5wt.%到50wt.%、从5wt.%到30wt.%、从5wt.%到20wt.%、从10wt.%到50wt.%、从10wt.%到30wt.%、从10wt.%到20wt.%、从15wt.%到50wt.%、从15wt.%到30wt.%、从15wt.%到20wt.%、或从20wt.%到50wt.%的量的固体,其中所述固体包含沸石颗粒、催化剂载体材料、催化活性化合物前体和共聚物表面活性剂(除稀释剂外的所有物质)。
64.再次参考图1,催化剂前体混合物142可以在喷雾干燥器150中被喷雾干燥以生产复合催化剂。喷雾干燥器150可以是任何可商购获得的喷雾干燥器系统。喷雾干燥器150可以包括干燥室151,所述干燥室包括柱形部分152和锥形部分154。喷雾干燥器150还可以包括喷雾喷嘴156,所述喷雾喷嘴设置在干燥室151内并且可操作为雾化干燥室151内的催化剂前体溶液142。可以将加热的气体144引入干燥室151。所述气体可以是空气或惰性气体,诸如但不限于氮气、氦气、氩气或其他惰性气体。此外,水146可以流体联接到喷雾喷嘴156
以供在喷雾干燥器150的启动期间使用。在将催化剂前体混合物142引入喷雾喷嘴156之前,可以将催化剂前体混合物142加热到喷雾温度。催化剂前体混合物142的喷雾温度可以大于或等于50℃、大于或等于75℃、或甚至大于或等于100℃。催化剂前体混合物的喷雾温度可以为从50℃到150℃、从50℃到125℃、从75℃到150℃、从75℃到125℃、从100℃到150℃、或甚至从100℃到125℃。如果喷雾温度太低,则在干燥室151的表面温度下,稀释剂从干燥室151中的催化剂前体混合物142的液滴的蒸发可能不充分。如果喷雾温度太高,则稀释剂的蒸发可能太快,导致复合催化剂内的凝聚力降低,这可能影响复合催化剂的耐久性。
65.在喷雾干燥器150的稳态操作期间,催化剂前体混合物142可以通过催化剂前体泵143递送到喷雾喷嘴156。喷雾喷嘴156可以将催化剂前体混合物142雾化成催化剂前体混合物142的多个液滴。喷雾喷嘴156的类型可能影响干燥室151中催化剂前体混合物142的液滴的平均液滴大小,这可能影响从喷雾干燥器150回收的复合催化剂的平均粒度。例如,配置成产生较小尺寸液滴的喷雾喷嘴156可以产生具有较小平均粒度的复合催化剂。此外,递送到喷雾喷嘴156的催化剂前体混合物142的压力、流速或两者也可能影响复合催化剂的液滴大小和平均粒度。
66.参考图1,催化剂前体混合物142的液滴被雾化到喷雾干燥室151中,其中液滴被加热的气体144加热。喷雾干燥器150的干燥室151可以维持在足以从催化剂前体混合物142的液滴蒸发稀释剂106以形成多个固体复合催化剂颗粒的表面温度。干燥室151的表面温度是指在干燥室151的内表面测量到的温度。加热的气体144可以被加热到足以维持干燥室151的表面温度的温度。干燥室151可以维持在从200℃到300℃、诸如从200℃到285℃、从200℃到280℃、从200℃到275℃、从250℃到300℃、从250℃到285℃、从250℃到280℃、从250℃到275℃、从260℃到300℃、从260℃到285℃、从260℃到280℃、或从260℃到275℃的表面温度。如果干燥室的表面温度太低,则催化剂前体混合物142的液滴中的稀释剂可能不会完全蒸发以产生固体复合催化剂颗粒。
67.在干燥室151中,来自加热的气体144的热量可以使从催化剂前体混合物142的液滴中除去稀释剂,诸如通过稀释剂的蒸发。随着稀释剂从催化剂前体混合物142的液滴中蒸发,催化剂前体混合物142中的每个液滴的体积可以减小,并且催化剂载体前体142的催化剂载体材料可以会聚形成附聚物,所述附聚物可以至少部分或完全包围和固定或捕获催化剂载体材料内的沸石颗粒以形成复合催化剂颗粒。
68.随着稀释剂被除去,催化活性化合物前体可以沉积到催化剂载体材料、沸石颗粒或两者的表面上。催化剂前体混合物中的三嵌段共聚物表面活性剂可以操作为将催化活性化合物前体隔开并防止催化活性化合物前体在干燥过程中固结成较大的晶体或附聚物。这可以使得催化活性化合物前体能够更均匀地分布在催化剂载体材料、沸石颗粒或两者的表面(外表面和孔表面)上。随着稀释剂在干燥室151中从催化剂前体混合物142的液滴中被除去,沉积在催化剂载体材料、沸石颗粒或两者的表面上的催化活性化合物前体可以经历化学反应以从催化活性化合物前体转变为催化活性化合物。例如,包含钨化合物(诸如偏钨酸铵)的催化活性化合物前体可以在干燥室151中的温度下经历氧化以将钨化合物转化为氧化钨。因此,从喷雾干燥器150的干燥室151回收的复合催化剂可以包含沉积在催化剂载体材料、沸石颗粒或两者的外表面和孔表面上的催化活性化合物。
69.再次参考图1,喷雾干燥器150可以包括在干燥室151中的一个或多个催化剂出口,
每个出口流体联接到固体分离器和鼓风机190,所述鼓风机可操作为将空气和喷雾干燥的复合催化剂抽出干燥室151。可以从设置在干燥室151的锥形部分154的会聚端处的第一出口除去第一复合催化剂流160。锥形部分154的转化端可以设置在干燥室151的底端处,使得第一出口处于干燥室151的底部。在干燥室151中喷雾干燥的复合催化剂最终可以下降到干燥室151的锥形部分154。第一复合催化剂流160可以从干燥室151中流出并进入第一固体分离器170。第一固体分离器170可以流体联接到鼓风机190,所述鼓风机可以可操作为将包含复合催化剂和加热的空气的第一复合催化剂流160从第一催化剂出口抽出干燥室151,并且将第一复合催化剂流160传输到第一固体分离器170。第一固体分离器170可以可操作为将第一复合催化剂180与第一复合催化剂流160中的加热的空气分离。第一固体分离器170可以是旋风分离器、过滤器或其他固-气分离装置。第一复合催化剂180可以从第一固体分离器170回收。加热的气体可以被鼓风机190抽吸通过第一固体分离器并从该过程被除去。
70.可以从干燥室151的第二出口除去第二复合催化剂流162。相对于向下通过干燥室151的复合催化剂的流,第二出口可以设置在第一出口的上游。第二出口可以设置在干燥室151的柱形部分152中或靠近干燥室151的锥形部分154的发散端。随着催化剂前体混合物142的液滴在干燥室151中转变为固体复合催化剂颗粒,与较轻的固体复合催化剂颗粒相比,较重的固体复合催化剂颗粒可以沿图1中的坐标轴的-z方向向下更快速地下降。如贯穿本公开所使用的,“较重的”复合催化剂颗粒可以指与“较轻的”复合催化剂颗粒相比具有较大的密度或较大的平均粒度的复合催化剂颗粒。因此,在喷雾干燥器150的稳态操作期间,颗粒密度、平均粒度或两者的梯度可以在干燥室151中沿竖直方向(图1中的坐标轴的+/-z方向)形成。从干燥室151的不同竖向位置除去复合催化剂可以使得能够回收具有不同的平均粒度、不同的密度或两者的复合催化剂。通常,从干燥室151内的较高位置(在较大的+z位置)除去复合催化剂颗粒可以产生复合催化剂流,与从干燥室151的底部回收的第一复合催化剂180相比,所述复合催化剂流包含具有较小的密度、平均粒度或两者的复合催化剂。
71.第二复合催化剂流162可以从干燥室151流出并进入第二固体分离器172。第二固体分离器172可以流体联接到鼓风机190,所述鼓风机可以可操作为将包含复合催化剂和加热的空气的第二复合催化剂流162从第二催化剂出口抽出干燥室151,并且将第二复合催化剂流162传输到第二固体分离器172。第二固体分离器172可以可操作为将第二复合催化剂182与第二复合催化剂流162中的加热的气体分离。第二固体分离器172可以是旋风分离器、过滤器或其他固-气分离装置。第二复合催化剂182可以从第二固体分离器172回收。加热的气体可以被鼓风机190抽吸通过第二固体分离器172并从该过程被除去。与从干燥室151底部回收的第一复合催化剂180相比,第二复合催化剂182可以具有较小的密度、较小的平均粒度或两者。尽管描述了第一复合催化剂180和第二复合催化剂182,但是应当理解,一个或多个复合催化剂流可以在不同的位置从干燥室被除去以产生多种复合催化剂,每种复合催化剂具有不同的平均粒度、平均密度或两者。
72.在复合催化剂的喷雾干燥之后,可以在煅烧炉中煅烧复合催化剂,诸如第一复合催化剂、第二复合催化剂或两者。煅烧过程可以是两步煅烧过程。这种两步煅烧过程可以确保分解三嵌段共聚物表面活性剂(诸如p123表面活性剂),以及从催化活性化合物前体形成稳定且具有活性的催化活性化合物。例如,煅烧可以确保由钨前体(诸如偏钨酸铵)形成稳定且具有活性的氧化钨物种。煅烧可以在以下气体中的一者或多者的存在下进
行:空气、氧气、氢气和氮气。煅烧可以在从200℃到700℃的煅烧温度下进行。热处理条件,包括气体环境的类型和煅烧温度,可能会影响形成的氧化钨物种。形成的氧化钨物种的类型影响催化剂组合物的稳定性和复分解活性,包括丙烯产率。这里描述的两步煅烧过程可以产生稳定的氧化钨相,以用于自复分解和交叉复分解。煅烧过程的第一步是在偏钨酸铵热分解后转化为氧化钨。在实施方案中,该第一步在空气的存在下在约200℃到250℃下进行。钨前体有显著的重量损失。钨前体的降解和钨前体向氧化钨的转化一直持续到第二步,所述第二步在从500℃到600℃的煅烧温度下进行,此时钨前体的重量损失稳定,并且形成用于复分解的活性氧化钨物种。在一个或多个实施方案中,复合催化剂可以首先在250℃下经受煅烧2小时,然后在550℃下经受煅烧8小时,其中在达到第一温度之前的升温速率为每分钟1℃,并且在达到第二温度之前的升温速率为每分钟3℃。尽管已经针对具有氧化钨作为催化活性化合物的复合催化剂描述了煅烧过程,但是应当理解,煅烧过程可以用于完成具有其他催化活性化合物的复合催化剂的形成。
73.喷雾干燥的复合催化剂的物理特性的评估表明,催化活性材料(诸如氧化钨)均匀分散在催化剂载体材料的外表面和孔表面上。与通过常规技术(诸如湿浸渍或初湿浸渍)制备的常规复分解催化剂相比,催化活性材料的这种均匀分散可以转化为复合催化剂更高的转化率以及更高的丙烯和乙烯产率。
74.与通过常规技术(诸如湿浸渍或初湿浸渍)制备的复分解催化剂的平均粒度相比,根据本公开通过喷雾干燥制备的复合催化剂可以具有减小的平均粒度。复合催化剂可以具有小于或等于80微米(μm)、小于或等于50μm、小于或等于30μm、或者甚至小于或等于20μm的平均粒度。本公开的复合催化剂可以具有从1μm到80μm、从1μm到50μm、从1μm到30μm、从1μm到20μm、从5μm到80μm、从5μm到50μm、从5μm到30μm、从5μm到20μm、从8μm到80μm、从8μm到50μm、从8μm到30μm、或从8μm到20μm的平均粒度。平均粒度可以通过扫描电子显微镜(sem)或其他已知的分析方法来确定。
75.包含嵌入催化剂载体材料中的沸石颗粒和沉积在催化剂载体材料、沸石颗粒或两者的外表面和孔表面上的催化活性化合物的复合催化剂可以用于复分解反应过程中以将丁烯转化为丙烯、乙烯和其他烯烃。复分解反应过程可以包括与丁烯异构化、裂化或两者结合的复分解反应。如反应1(rxn 1)中所示,2-丁烯异构化为1-丁烯以及1-丁烯异构化为2-丁烯是平衡反应,如单头双向箭头所示。2-丁烯和1-丁烯的异构化可以用异构化催化剂来实现。如本公开中使用的,术语“异构化催化剂”可以指促进烯烃的异构化(包括,例如,2-丁烯异构化为1-丁烯)的催化剂。如反应2(rxn 2)中所示,1-丁烯和2-丁烯的交叉复分解可产生1-丙烯和2-戊烯。如本公开中所使用的,术语“交叉复分解”可以指涉及通过碳-碳双键的断裂和再生来重新分布烯烃片段的有机反应。在2-丁烯和1-丁烯之间的交叉复分解的情况下,这些碳-碳双键通过复分解进行的重新分布产生丙烯和c
5-c6烯烃。1-丁烯和2-丁烯的交叉复分解可以用复分解催化剂(诸如氧化钨)来实现。如本公开中所使用的,术语“复分解催化剂”可以指促进烯烃的复分解反应以形成其他烯烃的催化剂。复分解催化剂还可以通过“自复分解”反应机制将2-丁烯异构化为1-丁烯。
[0076][0077]
参考rxn 1和rxn 2,异构化和复分解反应不限于这些反应物和产物;然而,rxn 1和rxn 2提供了反应方法的简化说明。如rxn 2中所示,复分解反应可以在两种烯烃之间发生。键合到碳-碳双键的碳原子的基团可以在分子之间交换以产生具有交换基团的两种新烯烃。选择的特定复分解催化剂通常可以确定是否形成顺式异构体或反式异构体,因为顺式异构体或反式异构体的形成可以至少部分取决于烯烃与催化剂的配位。1-丁烯也可以在复分解催化剂的存在下通过相似的反应机制自复分解以产生乙烯和3己烯。
[0078]
进一步地,如随后在本公开中所提供的以下反应3(rxn 3)中所示,“裂化”可以指将c4+烯烃催化转化为丙烯以及其他烷烃、烯烃或烷烃和烯烃,例如,c
2-c3烯烃。裂化反应不限于rxn3中所示的反应物和产物;然而,rxn 3提供了裂化反应的简化说明。
[0079][0080]
通过在足以进行复分解反应的反应条件下使含丁烯原料与本公开的复合催化剂接触,可以通过复分解和裂化使丁烯转化为丙烯和其他烯烃。在一个或多个实施方案中,复合催化剂可以包含嵌入包含介孔二氧化硅的催化剂载体材料中的zsm-5沸石颗粒。复合催化剂还可以包含作为催化活性化合物分散在介孔二氧化硅催化剂载体、zsm-5沸石颗粒或两者的外表面和孔表面上的氧化钨。复分解过程可以任选地包括附加的异构化催化剂以维持反应器中1-丁烯和2-丁烯的平衡浓度。异构化催化剂可以是设置在复合催化剂上游或与复合催化剂混合的单独的颗粒催化剂。
[0081]
现在参考图2,示意性地描绘了用于进行丁烯复分解的反应器系统200。反应器系统200可以包括复分解反应器210和复分解反应器210下游的复分解流出物分离系统230。复分解反应器210可以是固定床反应器或适用于进行复分解反应的任何其他类型的反应器。复分解反应器210可以包括串联或并联的多个复分解反应器。复分解反应器210可以可操作为在复分解反应区212中使含丁烯进料202与本公开的复合催化剂接触。复分解反应器210可以包括复分解反应区212上游和下游的惰性填充材料216以将复合催化剂固定在复分解反应区212中。
[0082]
含丁烯进料202可以包含1-丁烯、反式-2-丁烯、顺式-2-丁烯或这些的组合。含丁
烯进料202进一步可以包含其他c
1-c6组分。基于含丁烯进料202的总重量,含丁烯进料202可以包含从10wt.%到100wt.%的1-丁烯。例如,基于含丁烯进料202的总重量,含丁烯进料202可以包含从10wt.%到80wt.%、从10wt.%到60wt.%、从10wt.%到40wt.%、从10wt.%到20wt.%、从20wt.%到100wt.%、从20wt.%到80wt.%、从20wt.%到60wt.%、从20wt.%到40wt.%、从40wt.%到100wt.%、从40wt.%到80wt.%、从40wt.%到60wt.%、从60wt.%到100wt.%、从60wt.%到80wt.%、或从80wt.%到100wt.%的1-丁烯。基于含丁烯进料202的总重量,含丁烯进料202可以包含从10wt.%到100wt.%的2-丁烯(即顺式-2-丁烯、反式-2-丁烯或两者)。例如,基于含丁烯进料202的总重量,原料140可以包含从10wt.%到80wt.%、从10wt.%到60wt.%、从10wt.%到40wt.%、从10wt.%到20wt.%、从20wt.%到100wt.%、从20wt.%到80wt.%、从20wt.%到60wt.%、从20wt.%到40wt.%、从40wt.%到100wt.%、从40wt.%到80wt.%、从40wt.%到60wt.%、从60wt.%到100wt.%、从60wt.%到80wt.%、或从80wt.%到100wt.%的2-丁烯。此外,含丁烯进料202可以基本上不含乙烯。例如,基于含丁烯进料202的总重量,可以基本上不含乙烯的含丁烯进料202可以包含小于1wt.%的乙烯。
[0083]
在一个或多个实施方案中,含丁烯进料202可以是c4萃余液流,诸如但不限于萃余液-2流。萃余液是从石脑油裂化工艺或气体裂化工艺中除去一种或多种成分后的残留c4流(c4流通常含有作为其主要组分的正丁烷、1-丁烯、2-丁烯、异丁烯和1,3-丁二烯以及与所述主要组分一起形成c4流的高达95%或更多的任选的一些异丁烷)。含丁烯进料202可以包括萃余液-1流。萃余液-1是从c4萃余液流中分离出1,3-丁二烯后获得的c4残余物,并且主要包含2-丁烯、1-丁烯和异丁烯,它们可占萃余液-1流的从55wt.%到99wt.%。例如,基于萃余液-1流的总重量,萃余液-1流可以包含从10wt.%到30wt.%的2-丁烯、从25wt.%到50wt.%的1-丁烯以及从20wt.%到50wt.%的异丁烯。含丁烯进料202可以包含萃余液-2流。萃余液-2是从c4萃余液流中分离出1,3-丁二烯和异丁烯后获得的c4残余物,并且主要包含2-丁烯、1-丁烯和正丁烷,它们可占萃余液-2流的从45wt.%到99wt.%。例如,基于萃余液-2流的总重量,萃余液-2流可以包含从20wt.%到60wt.%的2-丁烯、从10wt.%到60wt.%的1-丁烯以及从15wt.%到25wt.%的正丁烷。含丁烯进料202可以包含萃余液-3流。萃余液-3是从c4萃余液流中分离出1,3-丁二烯、异丁烯和1-丁烯后获得的c4残余物,并且主要包含2-丁烯、正丁烷和未分离的残留1-丁烯,它们组合起来可占萃余液-3流的从40wt.%到99wt.%。例如,基于萃余液-3流的总重量,萃余液-3流可包含从30wt.%到70wt.%的2-丁烯以及从10wt.%到30wt.%的正丁烷。含丁烯进料202中异丁烯、惰性气体和非烯烃(诸如正丁烷)的存在可能不会对目标复分解反应产生负面影响,但可能会通过与复合催化剂中的沸石颗粒接触而经历裂化反应。
[0084]
如图1所示,含丁烯进料202可以被引入复分解反应器210中并在复分解反应区212中与复合催化剂接触,复合催化剂可以包含:嵌入介孔二氧化硅催化剂载体材料中的zsm-5沸石颗粒;以及氧化钨,所述氧化钨作为催化活性化合物分散在介孔二氧化硅催化剂载体、zsm-5沸石颗粒或两者的外表面和孔表面上。含丁烯进料202与复合催化剂的接触可以引起含丁烯进料202中的至少一部分丁烯反应形成丙烯和其他烯烃。所述反应可以包括交叉复分解、裂化或两者。
[0085]
复分解反应区212可以维持在足以促进2-丁烯和1-丁烯的交叉复分解反应的复分
解反应温度。复分解反应温度可以为从100摄氏度(℃)到600℃。例如,复分解反应区212可以维持在从100℃到550℃、从100℃到450℃、从100℃到400℃、从100℃到300℃、从100℃到250℃、从100℃到150℃、从150℃到600℃、从150℃到550℃、从150℃到450℃、从150℃到400℃、从150℃到300℃、从150℃到250℃、从250℃到600℃、从250℃到550℃、从250℃到450℃、从250℃到400℃、从250℃到300℃、从300℃到600℃、从300℃到550℃、从300℃到450℃、从300℃到400℃、从400℃到600℃、从400℃到550℃、从400℃到450℃、从450℃到600℃、从450℃到550℃、或从550℃到600℃的复分解反应温度。
[0086]
与通过常规技术(诸如湿浸渍或初湿浸渍)制备的常规复分解催化剂相比,以及与包含复分解催化剂和裂化催化剂的组合的双催化剂体系相比,通过本公开的喷雾干燥法制备的复合催化剂可以表现出增强的复分解性能。本公开的喷雾干燥的复合催化剂的催化活性在固定床反应器中对丁烯到丙烯的转化进行了评价,并将其性能与双催化剂反应体系进行比较,所述双催化剂反应体系包含通过湿浸渍制备的常规复分解催化剂和单独的沸石裂化催化剂。喷雾干燥的复合催化剂具有高度的活性和稳定性,并且其性能可与具有常规复分解催化剂和单独的裂化催化剂的双催化剂体系相当。因此,本公开的复合催化剂可以提供与单一催化剂相当的复分解性能,其不需要制备催化剂混合物或隔离和分离复分解反应器内的两个或更多个反应区(这可能导致反应器内未利用的死区)。
[0087]
包含丙烯和其他烯烃的复分解流出物214可以从复分解反应器210中流出。复分解流出物214可以流到复分解流出物分离系统230,所述复分解流出物分离系统可操作为将复分解流出物214分离成多个产物流,诸如但不限于乙烯流232、丙烯流234、c4流236、c5+流238或这些的组合。乙烯流232、丙烯流234或两者可以传递到下游加工单元以纯化乙烯、丙烯或两者。乙烯、丙烯或两者可以用作聚合物和其他有价值的化学产品的生产中有价值的中间体。c4流236可以再循环回到复分解反应器210或传递到一个或多个下游加工操作。c5+流238可以传递到一个或多个下游加工操作以进行进一步加工。
[0088]
实例
[0089]
以下实例示出了先前描述的本公开的一个或多个附加的特征。应当理解,这些实例不旨在以任何方式限制本公开或所附权利要求的范围。
[0090]
实例1:沸石的制备——mfi 2000裂化催化剂
[0091]
在典型的合成中,将17.04克四丙基溴化铵(tpabr)和2.96g氟化铵溶解在300克去离子水中并充分搅拌20分钟以产生tpabr溶液。将48克气相二氧化硅和0.30克硝酸铝同时逐渐加入到tpabr溶液中,同时剧烈搅拌。一旦溶液凝胶化,则用刮刀将凝胶混合约10分钟直到均质化。将获得的凝胶置于衬有的酸消化弹中并在200℃下保持2天。两天后,将消化弹从烘箱中取出并在冷水中淬火30分钟。将消化弹的内容物过滤并用1升去离子水洗涤。凝胶的摩尔组成为1sio2:0.0005al2o3:0.08(tpa)br:0.10nh4f:20h2o。得到的固体产物用水洗涤并在80℃下干燥过夜。通过在空气中在750℃下以每分钟4℃的升温速率煅烧6小时来除去模板。
[0092]
使用x射线衍射(xrd)分析实例1的mfi-2000裂化催化剂。参考图3,实例1的mfi-2000裂化催化剂的xrd图表显示了mfi-2000裂化催化剂在等于8度(
°
)、9
°
、23
°
和24
°
的2θ处的特征峰。
[0093]
比较例2:通过湿浸渍制备的二氧化硅复分解催化剂上的氧化钨
[0094]
在比较例2中,制备了包含负载在中孔二氧化硅载体上的氧化钨的比较复分解催化剂。通过湿浸渍技术制备了比较例2的复分解催化剂。将约2克二氧化硅载体材料和约0.235g偏钨酸铵(基于99.99%痕量金属)加入到圆底烧瓶中。二氧化硅载体材料是从富士硅化学株式会社获得的q-10级介孔二氧化硅,并且在200℃下煅烧3小时然后在575℃下煅烧五小时,其中升温速率为每分钟3℃。然后将约20ml的去离子水加入到烧瓶中。将磁力搅拌棒加入到烧瓶中,并且将烧瓶置于编程为以500rpm运行大约两小时的搅拌板上。从烧瓶中取出磁力搅拌棒,并且将烧瓶连接到旋转蒸发器。旋转蒸发器的操作条件为:转速设置为171rpm,水浴温度设置为80℃,真空设置为292毫巴,并且冷却液(50%水和50%乙二醇)维持在6℃。之后,将催化组合物置于80℃下的干燥烘箱中过夜。将干燥的催化剂在250℃下煅烧2小时并且在550℃下煅烧8小时,其中在达到第一温度之前的升温速率为每分钟1℃,并且在达到第二温度之前的升温速率为每分钟3℃。这些样品的煅烧在3-550炉(可从总部位于美国宾夕法尼亚州约克郡的登士柏喜美乐(dentsply ceramco)商购获得)中进行。基于比较复分解催化剂的总重量,比较例2的比较复分解催化剂包含10重量百分比的氧化钨负载量。
[0095]
使用x射线衍射(xrd)分析了比较例2的复分解催化剂。使用来自布鲁克axs有限公司(bruker axs gmbh)(德国卡尔斯鲁厄(karlsruhe,germany))的d4 endeavor x射线衍射仪收集了本公开的实例的xrd数据,并使用diffrac.eva v4.1.1版本(可从布鲁克获得)进行了分析,该版本具有匹配完美扫描的内置pdf库。在从20度到80度的2-θ范围内的室温下进行了分析。如图4所示,比较例2的复分解催化剂的xrd图表包括二氧化硅的特征峰以及氧化钨的特征峰,其在20
°
到30
°
之间的2-θ范围内。
[0096]
此外,使比较例2的复分解催化剂经受了扫描电子显微镜检查法(sem)以确定平均粒度。通过湿浸渍而不进行喷雾干燥制备的比较例2的复分解催化剂具有81.012微米(μm)的平均粒度。
[0097]
实例3:复合催化剂的制备
[0098]
在实例3中,使用实例1的mfi-2000裂化催化剂根据本发明的方法制备了复合催化剂。通过将33.55克二氧化硅、13克来自实例1的mfi-2000裂化催化剂和250毫升(ml)水组合制备了第一溶液。二氧化硅是来自富士硅化学株式会社的catirac
tm q-10级二氧化硅。将二氧化硅和mfi-2000裂化催化剂在水中的混合物以大于800转/分钟(rpm)的速度搅拌30分钟。制备了包含7克表面活性剂、35ml水和70ml乙醇的第二溶液,并以大于800rpm的速度搅拌30分钟以完全溶解表面活性剂。表面活性剂是从西格玛奥德里奇(sigma aldrich)获得的p123聚(乙二醇)-嵌段-聚(丙二醇)-嵌段-聚(乙二醇)表面活性剂。通过将4克钨前体(偏钨酸铵六水合物)与40ml水混合制备了第三种溶液,并且剧烈摇动第三溶液直到所有钨前体溶解。然后将第三溶液与第二溶液组合,并且将所得混合物搅拌10分钟。然后将第二溶液和第三溶液的组合的混合物加入到包含二氧化硅和mfi-2000裂化催化剂的第一溶液中以制备喷雾干燥器溶液。将喷雾干燥器溶液以大于700rpm的速度搅拌三天。所得喷雾干燥器溶液外观呈乳状且均质。
[0099]
然后使用gea niro喷雾干燥器mobile minor
tm
将喷雾干燥器溶液针对水性进料进行了喷雾干燥。喷雾干燥器的干燥室具有793毫米(mm)的主体大小、660mm的高度和60度的锥角。喷雾干燥以每分钟240毫升(ml/min)的目标进料流速进行,然而不断调节流速以维持
排气温度低于110℃。干燥室的表面温度维持在275℃,并且将空气和复合催化剂从干燥室抽出的风扇的风扇速度设置为2009rpm。
[0100]
为了开始喷雾干燥过程,打开喷雾干燥器并使其逐渐加热,同时加入去离子水。一旦干燥室的表面温度达到275℃的目标温度并且出口空气的温度稳定,则将喷雾干燥器溶液引入喷雾干燥器以代替去离子水。在两个位置从喷雾干燥器中除去复合催化剂:干燥室的锥形部分底部,以及干燥室侧面的正好在干燥室锥形部分上方的位置。将从干燥室底部取出的复合催化剂称为复合催化剂3a,并且将从干燥室侧面取出的复合催化剂称为复合催化剂3b。复合催化剂3b包含与复合催化剂3a相比密度更轻且平均粒度稍小的催化剂颗粒。
[0101]
根据实例1中先前所述的煅烧过程对复合催化剂3a和复合催化剂3b进行了煅烧。使用x射线衍射(xrd)分析了实例3的复合催化剂3a。参考图5,实例3的复合催化剂3a的xrd图表包括实例1的mfi-2000裂化催化剂在等于8度(
°
)、9
°
、23
°
和24
°
的2θ处的特征峰以及氧化钨在等于约23.3
°
的2θ处的特征峰。
[0102]
另外,使复合催化剂3a、复合催化剂3b以及复合催化剂3a和3b的重量比为50:50的混合物经受了扫描电子显微镜检查法(sem)以确定平均粒度。实例3的复合催化剂和比较例2的复分解催化剂的平均粒度的值在表1中提供。如表1所示,实例3中的喷雾干燥过程产生的复合催化剂的平均粒度显著小于通过湿浸渍制备的常规复分解催化剂(诸如比较例2中制备的那些)的平均粒度。
[0103]
表1
[0104][0105]
实例4:使用实例2的复合催化剂的丁烯复分解
[0106]
在实例4中,使用实例3的复合催化剂3b进行了含丁烯进料的复分解。复分解反应在大气压下在固定床反应器中进行。固定床反应器是16倍高通量反应器单元。将0.2克固定量的复合催化剂3b装入反应器中位于两层碳化硅之间。碳化硅用作惰性填充材料以将催化剂保持在反应器中并且不参与复分解反应。
[0107]
实例2的复合催化剂3b首先在550℃的温度下在氮气下以每分钟120毫升(ml/min)的流速预处理和活化24小时。在大气压下将固定床反应器的温度调节到500℃,并且将含丁烯进料引入固定床反应器。基于含丁烯进料的总重量,含丁烯进料包含10wt.%的异丁烷、20wt.%的正丁烷、12.5wt.%的反式-2-丁烯、12.5wt.%的顺式-2-丁烯和45wt.%的1-丁烯。含丁烯进料以每小时7.175(h-1
)的重时空速(whsv)传递通过固定床反应器30小时。使用带有热导检测器(tcd)和两个火焰离子化检测器(fid)的气相色谱仪(可作为agilent gc-7890b商购获得)对反应器流出物进行了定量分析。
[0108]
参考图6,以百分比形式提供了丁烯的总转化率以及乙烯、丙烯、五碳烃(c5)和具有6个或更多个碳(c6+)的烃中的每一者的产率。图6中的转化率和产率是历经30小时的实验运行时间定期采集的11个样品的平均值。实例3的复合催化剂3b所得的总转化率为53.7%,丙烯的产率为19.3%,并且乙烯的产率为5.9%。
[0109]
比较例5:使用双催化剂体系的丁烯复分解
[0110]
在比较例5中,使含丁烯进料与包含比较例2的复分解催化剂和实例1的mfi-2000
裂化催化剂的双催化剂体系接触。将比较例2的复分解催化剂(0.1克)和实例1的mfi-2000催化剂(0.1克)装入固定床反应器中,其中复分解催化剂设置在mfi-2000裂化催化剂的上游。将比较例2的复分解催化剂放置在实例1的mfi-2000裂化催化剂的上游。
[0111]
将比较例5的双催化剂体系的催化剂根据实例4所述的过程进行了预处理和活化。在预处理之后,将反应器温度在大气压下调节到500℃,并且将含丁烯进料引入固定床反应器。含丁烯进料以每小时7.175(h-1
)的重时空速(whsv)传递通过固定床反应器30小时。使用带有热导检测器(tcd)和两个火焰离子化检测器(fid)的气相色谱仪(可作为agilent gc-7890b商购获得)对反应器流出物进行了定量分析。
[0112]
参考图7,以百分比形式提供了丁烯的总转化率以及乙烯、丙烯、五碳烃(c5)和具有6个或更多个碳(c6+)的烃中的每一者的产率。图7中的转化率和产率是历经30小时的实验运行时间定期采集的11个样品的平均值。比较例5的双催化剂体系所得的总转化率为53.2%,丙烯的产率为20%,并且乙烯的产率为5.9%。
[0113]
如图6和图7所示,实例3(图6)的复合催化剂产生的结果与实例5的具有比较例2的复分解催化剂和实例1(图7)的沸石的双催化剂体系相当。事实上,实例3的复合催化剂表现出更高的丁烯总转化率,这表明了与比较例2的复分解催化剂相比总体上更高的催化活性。不旨在受任何特定理论的束缚,认为与通过湿浸渍制备的比较例2的复分解催化剂相比,根据本公开的用于制备实例3的复合催化剂的方法减小了平均粒度,并且增加了复合催化剂的表面积以及催化活性化合物在复合催化剂表面上分散度。认为与使用常规湿浸渍或初湿浸渍合成方法制备的复分解催化剂相比,这种更小的平均粒度、更大的表面积和催化活性化合物在表面上的更大分散引起通过本公开的方法制备的复合催化剂具有更高的催化活性。
[0114]
实例6:丁烯的复分解——实例3的复合催化剂的平均粒度对总转化率和产率的影响
[0115]
在实例6中,通过用复合催化剂3a、复合催化剂3b以及包含3a和3b两者的复合催化剂混合物根据实例4中的方法进行复分解反应研究了实例3的复合催化剂的平均粒度对丁烯的复分解的影响。如前所述,复合催化剂3a的平均粒度大于复合催化剂3b的平均粒度。对于复合催化剂和复合催化剂混合物中的每一者,根据实例4中所述的方法在450℃、500℃和550℃的温度下进行了丁烯复分解反应。复合催化剂混合物包含等重量的复合催化剂3a和复合催化剂3b。实例6的每个丁烯复分解反应所得的丙烯、乙烯、c5烃和c6+烃的平均产率在下表2中提供。
[0116]
表2
[0117]
产率复合催化剂3a(重)复合催化剂3b(轻)复合催化剂混合物平均粒度(微米)13.3329.86614.212在450℃下的丙烯(%)21.6120.3821.53在450℃下的乙烯(%)4.974.934.96在450℃下的c5(%)9.959.569.77在450℃下的c6+(%)22.5320.8022.02在500℃下的丙烯(%)30.2930.2630.32在500℃下的乙烯(%)8.418.858.50
在500℃下的c5(%)8.127.717.90在500℃下的c6+(%)22.2520.2821.63在550℃下的丙烯(%)30.0232.1731.45在550℃下的乙烯(%)9.4511.1510.29在550℃下的c5(%)6.735.736.22在550℃下的c6+(%)19.6717.3018.83
[0118]
如表2中的结果所示,与具有较大平均粒度的复合催化剂3a相比,具有较小平均粒度的复合催化剂3b在较高的复分解温度下对丙烯产生更好的选择性。在较低温度下,复合催化剂3a在丙烯选择性方面提供了更好的复分解性能。
[0119]
计算方法
[0120]
根据式1计算了“转化率”的测定。
[0121]
转化率=100-(顺丁烯产率+反丁烯产率)
ꢀꢀꢀꢀꢀꢀꢀꢀꢀꢀꢀꢀꢀꢀꢀ
(1)
[0122]
类似地,根据式2计算了“转化率-c
4”的测定。
[0123]
转化率-c4=100-(顺丁烯产率+反丁烯产率+异丁烯产率+1-丁烯产率)
ꢀꢀꢀꢀꢀ
(2)
[0124]
根据式3计算了“选择性”的测定。
[0125][0126]
本公开的第一方面涉及一种制备复合催化剂的方法。该方法可以包括:将催化剂载体材料、沸石颗粒、三嵌段共聚物表面活性剂、催化活性化合物前体和稀释剂组合以产生催化剂前体组合物。该方法还可以包括:混合催化剂前体组合物以产生催化剂前体混合物,其中催化剂载体材料和沸石颗粒悬浮在稀释剂中;以及喷雾干燥催化剂前体混合物。喷雾干燥可以包括:雾化催化剂前体混合物以产生多个液滴;以及在干燥室中干燥所述多个液滴。干燥可以使从所述多个液滴中的每个液滴中除去稀释剂以形成包含至少部分地固定在催化剂载体材料内的沸石颗粒的附聚物。干燥还可以使催化活性化合物前体反应以形成沉积在催化剂载体材料、沸石颗粒或两者的外表面和孔表面上的催化活性化合物。
[0127]
本公开的第二方面可以包括第一方面,其中催化剂载体材料可以包含固体颗粒,该固体颗粒包含二氧化硅、气相二氧化硅、氧化铝、气相氧化铝、二氧化钛、气相二氧化钛中的至少一者或这些的组合。
[0128]
本公开的第三方面可以包括第一或第二方面中的任一方面,其中催化剂载体材料可以包含介孔二氧化硅。
[0129]
本公开的第四方面可以包括第一至第三方面中的任一方面,其中催化剂载体材料可以包括预制催化剂载体材料。
[0130]
本公开的第五方面可以包括第一至第四方面中的任一方面,其中该方法可以不包括由一个或多个前体合成催化剂载体材料。
[0131]
本公开的第六方面可以包括第一至第五方面中的任一方面,其中催化剂载体材料可以具有从2.5纳米到40纳米的平均孔径。
[0132]
本公开的第七方面可以包括第一至第六方面中的任一方面,其中催化剂载体材料可以具有至少0.600毫升每克的总孔体积。
[0133]
本公开的第八方面可以包括第一至第七方面中的任一方面,其中催化剂载体材料可以具有从250平方米每克到600平方米每克的表面积。
[0134]
本公开的第九方面可以包括第一至第八方面中的任一方面,其中沸石颗粒可以包括丝光沸石骨架倒置结构沸石。
[0135]
本公开的第十方面可以包括第一至第九方面中的任一方面,其中沸石颗粒可以包括zsm-5沸石。
[0136]
本公开的第十一方面可以包括第一至第十方面中的任一方面,其中沸石颗粒可以包含二氧化硅和氧化铝,并且二氧化硅与氧化铝的重量比为从10:1到6000:1。
[0137]
本公开的第十二方面可以包括第一至第十一方面中的任一方面,其中沸石颗粒可以具有从5微米到35微米的平均粒度。
[0138]
本公开的第十三方面可以包括第一至第十二方面中的任一方面,其中三嵌段共聚物表面活性剂可以是聚(乙二醇)-嵌段-聚(丙二醇)-嵌段-聚(乙二醇)。
[0139]
本公开的第十四方面可以包括第一至第十三方面中的任一方面,包括将催化剂前体混合物混合足够的时间段以产生稳定的催化剂前体混合物。
[0140]
本公开的第十五方面可以包括第一至第十四方面中的任一方面,包括将催化剂前体组合物混合持续大于或等于72小时的时间。
[0141]
本公开的第十六方面可以包括第一至第十五方面中的任一方面,其中该组合可以包括制备第一混合物、第二混合物和第三混合物。第一混合物可以包含催化剂载体材料、沸石颗粒以及稀释剂的第一部分。第二混合物可以包含三嵌段共聚物表面活性剂以及稀释剂的第二部分。第三混合物可以包括催化活性化合物前体以及稀释剂的第三部分。
[0142]
本公开的第十七方面可以包括第十六方面,其中该组合进一步可以包括:将第二混合物和第三混合物组合以产生第四混合物,以及将第一混合物和第四混合物组合以产生催化剂前体组合物。
[0143]
本公开的第十八方面可以包括第一至第十七方面中的任一方面,其中催化剂前体混合物进一步可以包含醇。
[0144]
本公开的第十九方面可以包括第一至第十八方面中的任一方面,其中干燥室维持在从200℃到300℃的温度。
[0145]
本公开的第二十方面可以包括第十九方面,进一步包括:在设置在干燥室底部的第一出口处从干燥室中除去第一复合催化剂,以及在第一出口上游的第二出口处从干燥室中除去第二复合催化剂。
[0146]
本公开的第二十一方面可以包括第二十方面,其中第二复合催化剂的平均粒度可以小于第一复合催化剂的平均粒度。
[0147]
本公开的第二十二方面可以包括第二十或第二十一方面中的任一方面,其中第二复合催化剂的密度可以小于第一复合催化剂的密度。
[0148]
本公开的第二十三方面可以包括第一至第二十二方面中的任一方面,进一步包括在从200℃到700℃的温度下煅烧复合催化剂。
[0149]
本公开的第二十四方面可以包括第一至第二十三方面中的任一方面,其中催化活性化合物前体可以包含选自钼、铼、钨、锰、钛、铈的金属或这些的任何组合。
[0150]
本公开的第二十五方面可以包括第一至第二十四方面中的任一方面,其中催化活性化合物前体可以包含钨。
[0151]
本公开的第二十六方面可以包括第一至第二十五方面中的任一方面,其中催化活
性化合物前体可以包含偏钨酸铵水合物。
[0152]
本公开的第二十七方面可以包括第一至第二十四方面中的任一方面,其中催化活性化合物可以包含选自钼、铼、钨、锰、钛、铈的金属的氧化物或这些的任何组合。
[0153]
本公开的第二十八方面可以包括第一至第二十七方面中的任一方面,其中催化活性化合物可以包含氧化钨。
[0154]
本公开的第二十九方面可以包括第一至第二十八方面中的任一方面,其中基于催化剂前体混合物的干重,催化剂前体混合物可以包含从5重量百分比到50重量百分比的沸石颗粒。
[0155]
本公开的第三十方面可以包括第一至第二十九方面中的任一方面,其中基于催化剂前体混合物的干重,催化剂前体混合物可包含从20重量百分比到90重量百分比的载体材料。
[0156]
本公开的第三十一方面可以包括第一至第三十方面中的任一方面,其中基于催化剂前体混合物的干重,催化剂前体混合物可包含从0.1重量百分比到25重量百分比的催化活性化合物前体。
[0157]
本公开的第三十三方面可以包括第一至第三十二方面中的任一方面,其中基于催化剂前体混合物的干重,催化剂前体混合物可以包含从1重量百分比到20重量百分比的三嵌段共聚物表面活性剂。
[0158]
本公开的第三十四方面可以包括第一至第三十三方面中的任一方面,其中基于催化剂前体混合物的总重量,催化剂前体混合物可以包含从50重量百分比到95重量百分比的稀释剂。
[0159]
本公开的第三十五方面可以包括第一至第三十四方面中的任一方面,其中催化剂前体混合物可以包含从1重量百分比到50重量百分比的固体。
[0160]
本公开的第三十六方面可以包括第一至第三十五方面中的任一方面并且可以涉及通过第一至第三十五方面中的任一方面的方法制备的催化剂。
[0161]
本公开的第三十七方面可以包括第一至第三十六方面中的任一方面,其中复合催化剂可以具有从1微米到80微米的平均粒度。
[0162]
本公开的第三十八方面可以包括第一至第三十七方面中的任一方面,其中基于复合催化剂的总重量,复合催化剂可以包含从5重量百分比到50重量百分比的沸石颗粒。
[0163]
本公开的第三十九方面可以包括第一至第三十八方面中的任一方面,其中基于复合催化剂的总重量,复合催化剂可以包含从20重量百分比到90重量百分比的催化剂载体材料。
[0164]
本公开的第四十方面可以包括第一至第三十九方面中的任一方面,其中基于复合催化剂的总重量,复合催化剂可以包含从0.1重量百分比到25重量百分比的催化活性化合物。
[0165]
本公开的第四十一方面可以包括第一至第四十方面中的任一方面并且可以涉及用于生产丙烯的方法。该方法可以包括在反应温度下使含丁烯进料与复合催化剂接触,其中复合催化剂可以通过第一至第四十方面的任何方法制备。该接触可以使丁烯的至少一部分历经化学反应以产生包含至少丙烯的反应流出物。该方法还可以包括从反应器流出物中分离至少一部分丙烯。
[0166]
本发明的第四十二方面可以涉及一种用于生产丙烯的方法。该方法可以包括在反应温度下使含丁烯进料与复合催化剂接触。该接触可以使丁烯的至少一部分历经化学反应以产生包含至少丙烯的反应流出物。复合催化剂可以通过可以包括以下的方法制备:将催化剂载体材料、沸石颗粒、三嵌段共聚物表面活性剂、催化活性化合物前体和稀释剂组合以产生催化剂前体组合物。制备复合催化剂的方法还可以包括:混合催化剂前体组合物以制备催化剂前体混合物,其中催化剂载体材料和沸石颗粒悬浮在稀释剂中;以及喷雾干燥催化剂前体混合物。喷雾干燥可以包括:雾化催化剂前体混合物以产生多个液滴;以及在干燥室中干燥所述多个液滴。干燥可以使从所述多个液滴中的每个液滴中除去稀释剂以形成包含至少部分地固定在催化剂载体材料内的沸石颗粒的附聚物。干燥还可以使催化活性化合物前体反应以形成沉积在催化剂载体材料、沸石颗粒或两者的外表面和孔表面上的催化活性化合物。用于生产丙烯的方法还可以包括:从反应器流出物中分离丙烯的至少一部分。
[0167]
本公开的第四十三方面可以包括第四十一至第四十二方面中的任一方面,其中含丁烯的进料可以包含1-丁烯、反式-2丁烯、顺式-2-丁烯或这些的组合。
[0168]
本公开的第四十四方面可以包括第四十一至第四十三方面中的任一方面,其中含丁烯进料可以基本上不含乙烯,诸如包含小于1重量百分比的乙烯。
[0169]
本公开的第四十五方面可以包括第四十一至第四十四方面中的任一方面,其中含丁烯进料可以包含萃余液-2流、萃余液-3流或这些的组合。
[0170]
本发明的第四十六方面可以包括第四十一方面至第四十五方面中的任一方面,其中反应温度可以为从400℃到600℃。
[0171]
本公开的第四十七方面可以包括第四十一至第四十六方面中的任一方面,进一步包括:使含丁烯进料与异构化催化剂接触以产生异构化流出物,并且使异构化流出物与复合催化剂接触以产生包含丙烯的反应流出物。
[0172]
本公开的第四十八方面可以包括第四十一至第四十七方面中的任一方面,包括将反应流出物分离成多个产物流。
[0173]
本公开的第四十九方面可以包括第四十八方面,其中产物流可以包含乙烯流、丙烯流、c4流、c5+流中的至少一者或这些的组合。
[0174]
应当注意,以下权利要求中的一项或多项使用术语“其中”作为过渡词。出于限定本技术的目的,应注意,所述术语在权利要求中作为开放式过渡短语引入,所述短语用于引入结构的一系列特征的叙述,并且应当以与更常用的开放式前导词术语“包括”同样方式地理解。
[0175]
应当理解,分配给某特性的任何两个定量值可以构成所述特性的范围,并且在本公开中涵盖由给定特性的所有所述定量值形成的范围的所有组合。应当理解,流或反应器中的化学成分的组成范围应理解为在一些实施方案中包含该成分的异构体的混合物,例如,指定丁烯的组成范围可以包括各种丁烯的异构体。应当理解,这些实例提供了各种流的组成范围,并且具体化学组成的异构体的总量可以构成一个范围。
[0176]
已详细并且参考具体实施方案描述本公开的主题,应当注意,甚至在特定要素在伴随本公开描述的附图中的每一者中示出的情况下,在本公开中所描述的各种细节不应视为暗示这些细节涉及在本公开中所描述的各种实施方案为必需的组成部分的要素。实际上,所附权利要求应视为对本公开的宽度和本公开中所描述的各个实施方案的对应范围的
唯一表示。另外,显然在不脱离所附权利要求的范围的情况下可以进行修改和变化。