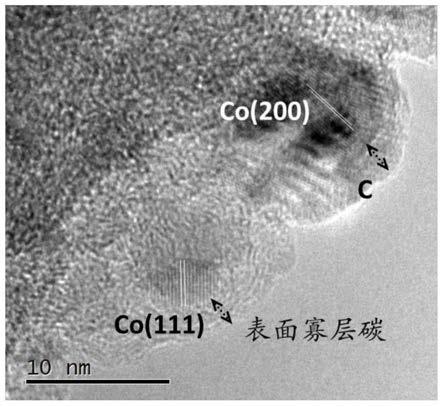
1.本发明属于有机化工技术领域,涉及到一种寡层碳保护的金属基催化剂及其在环氧乙烷羰基化中的应用。
背景技术:2.环氧化物衍生物通过羰基化方法可以转化为双官能团化合物,包括经过氢甲酰化反应合成3
‑
羟基醛衍生物以及经氢酯基化反应合成3
‑
羟基酯衍生物。其中,环氧化物
‑
环氧乙烷(eo),具有强生物活性,比重大,沸点极低,直接排放非常危险的,例如一次性口罩生产过程中eo污染物的排放等,很容易导致中毒和爆炸等危害。因此,在工业化应用中,尤其是针对环氧乙烷废气污染的治理,成为工业进程中重要的一环。目前工业上主要采用燃烧法、水合法、吸附法等对eo废气进行治理,造成eo资源的不完全利用及能源耗费。同时,我国eo产能已明显过剩,目前eo资源趋于丰富、价格趋于合理,大力发展以eo为原料的下游产业,能有效提升相关企业及产品的市场竞争力。
3.美国专利us5770776公开了shell公司采用环氧乙烷经氢甲酰化反应生成3
‑
羟基丙醛的工艺过程。该产物可通过进一步加氢将醛基转化为醇基,生成烷烃链二醇
‑
1,3
‑
丙二醇。然而,由于3
‑
羟基丙醛中间体极不稳定,容易形成低聚物,催化分离技术复杂,需采用压力大于10mpa的高压反应器,设备要求高,综合技术难度大,投资成本极高。需要指出的是,1,3
‑
丙二醇之所以不断吸引国际巨头企业的瞩目,还源于其是新型聚酯纤维
‑
聚对苯二甲酸丙二醇酯(ptt)的合成单体之一。ptt具有明显超越pet和pbt材料的优势,1998年被美国评为六大石化新产品之一。然而到目前为止,我国仍没有生产ptt的大规模成熟的企业,主要源于其原料单体之一的1,3
‑
丙二醇技术仍有待改进,成为卡脖子的核心技术。
4.通过上游产物3
‑
羟基丙酸甲酯进行选择性加氢过程,是目前生产1,3
‑
丙二醇的最具前景的手段之一。另一方面,作为一种双官能团化合物,3
‑
羟基羧酸酯是工业生产高附加值化学品的重要中间体,能被用作溶剂、树脂、涂料等,此外也可作为治疗阿兹海默氏症和帕金森症等多种疾病的药物的原料或中间体,同时也可以进一步生产烷链二醇。
5.美国专利us4973741使用贵金属铑催化剂和三苯基膦配体,在14.0mpa的压力下,用环氧乙烷羰化制备β
‑
羟基丙酸甲酯,是一种合成双官能团化合物的方法,但该方法转化率仅为26.3%,副产物多,目标产物的选择性仅为43.5%。
6.美国专利us6191321公开了通过环氧乙烷氢酯基化合成3
‑
羟基丙酸甲酯的方法。以co2(co)8/1,10
‑
菲咯啉为催化剂,甲基叔丁基醚为溶剂,在90℃、1125psi的压力下反应18小时,得到目标产物3
‑
羟基丙酸甲酯。然而,环氧乙烷的转化率较低,仅为11%,目标产物3
‑
羟基丙酸甲酯的选择性为74%。
7.中国专利cn101973881a公布了一种使用适当的羰基钴功能化离子液体催化剂[bmim][co(co)4]并辅以特殊的溶剂和促进剂,在同一体系下实现环氧乙烷氢酯基化制备3
‑
羟基丙酸酯以及加氢合成1,3
‑
丙二醇。保持反应温度70~75℃,反应压力3.7mpa,反应10
小时环氧乙烷转化率90.2%,3
‑
羟基丙酸甲酯的收率达82.5%。尽管这些催化剂表现出良好的反应活性,并在一定程度上实现了催化剂的循环利用,但[bmim][co(co)4]催化剂的制备过程复杂且成本昂贵,反应物和溶剂需预先脱水脱氧维持催化剂活性,相关工艺的大规模工业化仍有待于进一步发展。
[0008]
综上所述,现有研究成果显示了羰基化技术用于制备β
‑
丙酸酯的可行性,然而,应用于该过程的新型高效高选择性的金属基催化剂的开发仍存在大幅度的改进空间,探究催化羰基化环氧乙烷的新型催化剂仍具有极大地挑战性及必要性。
技术实现要素:[0009]
本发明提供了一种寡层碳保护的金属基催化剂的制备方法,并将其应用于环氧乙烷羰基化过程,致力于高选择性生产3
‑
羟基丙酸甲酯,一种可进一步生产1,3
‑
丙二醇的平台化合物。采用金属盐与含碳有机化合物在研磨或搅拌条件下形成的均匀金属盐配位前驱体,并通过固载化作用、气氛处理及反应条件下使催化剂中生成寡层碳保护的纳米金属颗粒。采用本方法制备的金属催化剂,通过制备过程或反应条件下原位生成有机碳层保护的体相金属颗粒催化剂,也可以得到固载化的薄层碳保护的金属催化剂。
[0010]
该类催化剂在一氧化碳气氛下,采用连续搅拌釜式反应器中,以醇类为溶剂及反应物,在较低的温度(20℃
‑
150℃)和压力(0.1
‑
15mpa)条件下,实现环氧乙烷羰基化过程,催化转化为3
‑
羟基丙酸甲酯。与先前使用的方法相比,所述的方法制得的寡层碳为1
‑
10个原子层,可以有效保护金属纳米颗粒不被进一步氧化。
[0011]
本发明的技术方案:
[0012]
一种寡层碳保护的金属基催化剂的制备方法,制得的金属基催化剂为体相金属催化剂或固载化金属催化剂,制备步骤如下:
[0013]
(1)制备催化剂的前驱体
[0014]
体相金属催化剂的前驱体:将金属前驱体与含碳有机物在n2手套箱中用研钵研磨均匀即为体相金属催化剂的前驱体;其中,含碳有机物与金属前驱体中金属离子的摩尔比为0.5~100,优选为1~10;
[0015]
固载化金属催化剂的前驱体:向体相金属催化剂的前驱体中加入载体,同时滴加液体试剂,混合搅拌1
‑
10min,并老化0.5
‑
72小时,经离心、洗涤得到干燥粉末,作为固载化金属催化剂的前驱体;
[0016]
(2)制备金属基催化剂
[0017]
采用热分解
‑
反应气氛处理两步法或一步还原处理法,对体相金属催化剂的前驱体或固载化金属催化剂的前驱体进行热气氛处理,使表层碳载体在金属颗粒表面部分热分解或甲烷化形成寡层碳保护的金属基催化剂:
[0018]
采用热分解
‑
反应气氛处理两步法时,首先在20
‑
1000℃温度范围内,将前驱体在n2、空气或o2/ar气氛中处理2
‑
10h,随后在co、co/o2或h2s/o2/ar的反应气氛中于20
‑
450℃温度范围内处理2
‑
72h,得到金属基催化剂;采用一步法时,在h2/ar气氛下20
‑
1000℃温度范围内处理2
‑
10h,得到金属基催化剂;
[0019]
当制备固载化金属催化剂时,采用碳材料为载体或氧化硅作为结构骨架;氧化硅作为模板需要进一步去除,经上述热处理后,再通过氢氟酸在30
‑
90℃刻蚀0.5
‑
12h,洗涤干
燥后得到寡层碳保护的金属基催化剂。
[0020]
所述的载体为碳材料时,包括碳纳米管、活性炭、石墨烯、纳米碳球、原位生成的无定型碳层;所述的载体为氧化硅时,包括氧化硅球、规则介孔氧化硅形成催化剂骨架。
[0021]
所述的金属前驱体包括硝酸镍、草酸镍、硝酸铜、乙酸铜、环烷酸铜、硝酸钴、乙酸钴、环烷酸钴、硬脂酸钴、八羰基二钴、硝酸铁、乙酸铁、硬脂酸铁、氯金酸、乙酸亚锡中一种或两种以上的组合;所述的金属基催化剂中金属组分的质量分数为0.5
‑
40wt%。
[0022]
所述的含碳有机物包括聚乙烯醇水溶液、聚乙烯吡咯烷酮水溶液、吡啶、二甲基取代的吡啶、羟基吡啶、咪唑、菲咯啉、喹啉、二氰二胺及其衍生物一种或两种以上组合。
[0023]
所述的液体试剂包括甲醇、乙醇、n,n
‑
二甲基甲酰胺、四氢呋喃、二氧六环、乙酸乙酯或硼氢化钠水溶液。
[0024]
所述热处理气氛中,o2/ar混合气中o2的体积百分比范围为5%
‑
40%,以ar为平衡气;co/o2/ar中co及o2的体积百分比为5%
‑
10%及20%
‑
95%,ar为平衡气;h2s/o2/ar混合气中h2s及o2的体积百分比为0.1%
‑
5%及5%
‑
40%,ar为平衡气。
[0025]
一种寡层碳壳保护的金属基催化剂在环氧乙烷羰基化中的应用,将环氧乙烷通过液体输送泵与溶剂输送到装有催化剂粉末的连续搅拌釜式反应器中,环氧乙烷在溶剂中的摩尔分数为0.1
‑
20mol%;通入0.1
‑
15mpa的co,在室温~150℃温度区间实现环氧乙烷的氢酯基化反应;反应后样品经过冷却器降温进入气液分离器,回收co气体;液固混合物进入精馏塔,塔顶采用不同馏出温度得到1,1
‑
二甲氧基乙烷、eo及甲醇,对eo及甲醇进行回收;塔底得到3
‑
羟基丙酸甲酯及催化剂残渣,经过过滤分离液固相得到高纯度3
‑
羟基丙酸甲酯,并对催化剂残渣进行回收。
[0026]
所述的环氧乙烷与金属基催化剂中金属组分的摩尔比为5:1~150:1。
[0027]
所述的溶剂是是二甘醇二甲醚、二苯醚、四氢呋喃、苯甲醚、水、甲醇、乙醇或甲酸。
[0028]
本发明的有益效果:本发明提供了一种寡层碳保护的钴基催化剂及其在环氧乙烷羰基化中的应用。采用含碳有机物为促进剂及碳源,通过与金属化合物形成化学作用、固载化、热气氛处理及反应条件下形成表面存在寡层碳保护的体相或负载型金属催化剂。通过连续搅拌釜式反应器,实现环氧乙烷为原料羰基化转化为3
‑
羟基丙酸甲酯的过程,反应设备简单,操作灵活、简便;反应过程条件温和,反应温度及压力较低;原料环氧乙烷可由工业废气回收获得,降低成本的同时减少环境污染。依据本发明的方法,于部分实施例中,依据所设定的反应参数,环氧化物的转化率达92.6%以上,3
‑
羟基丙酸甲酯选择性可达98.6%以上,具有良好的经济效益及工业应用前景。
附图说明
[0029]
图1为co/c
‑
1催化剂的透射电子显微镜图像。
[0030]
图2为co/c
‑
2催化剂的透射电子显微镜图像。
[0031]
图3为au/c
‑
5催化剂的x射线衍射图谱。
[0032]
图4为au/c
‑
5催化剂的透射电子显微镜图像。
[0033]
图5为本发明的工艺流程示意图。
[0034]
图6为co/c
‑
7催化剂的透射电子显微镜图像。
[0035]
图7为co/c
‑
7催化剂的元素能谱数据图。
具体实施方式
[0036]
以下部分结合技术方案和附图详细叙述本发明的具体实施方式。
[0037]
实施例1:
[0038]
将4.5g的乙酸钴c4h4coo4前驱体与3
‑
羟基吡啶以摩尔比为1:4在n2手套箱于研钵中混合均匀。加入5.0g活性炭载体后,同时逐滴滴加50ml乙酸乙酯分散载体及金属前驱体,搅拌2小时后,老化10小时,经离心、洗涤得到干燥粉末,在25%的h2/ar气氛下于400℃下热还原处理8h,得到催化剂粉末,命名为co/c
‑
1。其透射电子显微镜图像如图1中所示,通过测量样品中的黑色颗粒展示出0.20nm及0.18nm的晶格尺寸,分别隶属与co晶体的(111)及(200)晶面,可证实活性炭表面存在尺寸为4
‑
8nm的co纳米颗粒,且其表面被4
‑
6层无定型碳层保护。
[0039]
实施例2:
[0040]
将1.3g的co(no3)2·
6h2o前驱体与2
‑
甲基咪唑以摩尔比为1:4在n2手套箱于研钵中混合均匀。加入2.5g活性炭载体后,同时逐滴滴加20ml甲醇浸没并分散载体及金属前驱体,搅拌2小时后,老化10小时,经离心、洗涤得到干燥粉末,在20%的h2/ar气氛下于400℃下热还原处理8h,得到催化剂粉末,命名为co/c
‑
2。其透射电子显微镜图像如图2中所示,通过测量图中颗粒表面的晶格尺寸,确认样品中存在大量单分散且均一的co纳米颗粒。其表面指纹状分布的是寡层无定形碳保护层,在高温热处理过程中可保护细小的co纳米颗粒免于发生团聚现象,经过还原气氛处理,样品中co颗粒尺寸均一且保持在4
‑
7nm范围内。
[0041]
实施例3:
[0042]
将2.5g的co(no3)2·
6h2o前驱体与二氰二胺以摩尔比为1:5在n2手套箱中研磨混合均匀。加入5g的sba
‑
15载体,同时逐滴滴加50ml的n,n
‑
二甲基甲酰胺分散载体及金属前驱体,机械搅拌2小时后,老化10小时,经离心、洗涤得到干燥粉末,在5%的h2/ar气氛下于550℃下热还原处理3h,得到粉末样品。将还原后的粉末投入10%的氢氟酸溶液中,在30℃下刻蚀5h,经过离心洗涤至上层清液为中性,在120℃下过夜干燥,得到干燥的催化剂粉末,命名为co/c
‑
3。
[0043]
实施例4:
[0044]
将2.9g的cu(no3)2·
3h2o前驱体与二氰二胺以摩尔比为1:5在n2手套箱于研钵中混合均匀。加入5g的球形氧化硅载体粉末,同时逐滴滴加35ml的n,n
‑
二甲基甲酰胺分散载体及金属前驱体,机械搅拌2小时后,老化10小时,经离心、洗涤得到干燥粉末,在5%的h2/ar气氛下于550℃下热还原处理3h,得到粉末样品。随后将还原后的粉末投入10%的氢氟酸溶液中,在30℃下刻蚀2h,经过离心洗涤至上层清液为中性,在120℃下过夜干燥,得到干燥的催化剂粉末,命名为cu/c
‑
4。
[0045]
实施例5:
[0046]
将6.5ml氯金酸溶液(10
‑3mol/l)、质量分数为1%的聚乙烯醇(pva)水溶液以au/pva质量比为1:5混合均匀。加入5g球形碳载体,随后滴加4ml浓度为0.1mol/l硼氢化钠水溶液,机械搅拌2小时并老化10小时,经离心、洗涤得到干燥粉末,在空气气氛下于300℃下热处理3h,进一步采用体积分数3%h2s/7%o2/ar气氛在230℃下处理20h,得到粉末样品命名为au/c
‑
5。该样品的x射线衍射图谱如图3所示,其透射电子显微镜如图4所示,由黑色纳米颗粒与载体的对比度差异及表面晶格尺寸0.24nm对应于au晶体的(111)晶面可知,制得的
样品中的金纳米颗粒表面被薄层碳壳保护。
[0047]
实施例6:
[0048]
将2.6g的co(no3)2·
6h2o与6.5ml的haucl4溶液(10
‑3mol/l)、质量分数为1%的聚乙烯醇(pva)水溶液以金属/pva质量比为1:5混合均匀。加入5g载体sba
‑
15,随后滴加4ml浓度为0.1mol/l硼氢化钠水溶液,上层形成均匀的紫红色透明胶体溶液,机械搅拌2小时并老化10小时,上层溶液转变为澄清透明,金属前驱体被载体孔道完全吸收。经离心、洗涤得到干燥粉末,在空气气氛中于300℃下热处理3h,得到粉末样品。随后将粉末投入10%的氢氟酸溶液中,在30℃下刻蚀5h,经过离心洗涤至上层清液为中性,在120℃下过夜干燥,进一步采用5%co/o2气氛在90℃下处理36h,得到粉末样品命名为aucu/c
‑
6。
[0049]
实施例7:
[0050]
将2g的co2(co)8金属前驱体与3
‑
羟基吡啶以摩尔比为1:4在n2手套箱中混合均匀。将上述催化剂通过进料口投入反应釜内,通过输送泵将浓度为3mol/l的环氧乙烷与辅助有机配体的甲醇溶液泵入反应釜内,控制金属钴与环氧乙烷摩尔比为1:4,如图5中所示。同时通入压力为6mpa的co气体,在室温至100℃温度区间进行eo氢酯基化反应。反应后样品经过冷却器降温后,进入高压分离器,直接回收co气体。液固混合物进入精馏塔,塔顶采用不同馏出温度得到1,1
‑
二甲氧基乙烷、eo及甲醇,对eo及甲醇进行回收;塔底得到3
‑
羟基丙酸甲酯及催化剂残渣,经过柱层析色谱过滤分离液固相得到高纯度3
‑
羟基丙酸甲酯,并对催化剂残渣进行回收。反应后催化剂co/c
‑
7的透射电子显微镜图像如图6所示。图中可见,催化剂由有机碳薄层保护的co纳米颗粒组成,图7中该催化剂的元素能谱数据图证实样品中存在co、c及o元素,cu元素来源于测试采用的铜支架。由于反应条件下原位生成寡层碳物质对co颗粒起到保护的作用,导致催化剂即使在反应后,依然以稳定的姜黄色体相co溶胶颗粒存在。
[0051]
表1
[0052][0053]
由表1中的反应结果可知,30
‑
50℃低温条件下,环氧乙烷eo的转化率最高可达92.6%,3
‑
羟基丙酸甲酯选择性98.5%,对应的产物3
‑
羟基丙酸甲酯收率为91.2%。高温条件下,3
‑
羟基丙酸甲酯的收率显著降低,副产物1,1
‑
二甲氧基乙烷的收率明显上升。
[0054]
实施例8:
[0055]
采用实施例7中的反应工艺,通过进料口将1gco/c
‑
1催化剂投入反应釜内,通过输
送泵将浓度为3mol/l的环氧乙烷与辅助有机配体的甲醇溶液泵入反应釜内,控制金属钴与环氧乙烷摩尔比为1:4。通入压力为6mpa的co气体,在40℃条件下进行eo氢酯基化反应。反应后4小时,环氧乙烷转化率为36%,3
‑
羟基丙酸甲酯选择性73%。
[0056]
参照例1:
[0057]
采用沉积沉淀法制备co/mgo参比催化剂。将1.85g硝酸钴和1.5g氧化镁溶解在30ml去离子水中,搅拌30min混合均匀,配置0.1mol/l的naoh溶液作为沉淀剂,在45℃恒温及搅拌条件下,持续滴入金属离子母液调节ph至10。老化8小时后通过去离子水进行过滤、洗涤、110℃下干燥10小时,并研磨得到干燥粉末,在马弗炉中500℃下焙烧4h得到催化剂前驱体。将催化剂前驱体在20%h2/ar混合气中650℃下还原6h得到催化剂粉末。
[0058]
通过进料口将上述催化剂投入反应釜内,通过输送泵将一定比例的环氧乙烷与辅助有机配体的甲醇溶液泵入反应釜内。同时通入压力为6mpa的co气体,在40℃条件下进行eo氢酯基化反应。反应4小时,反应液中未检测到3
‑
羟基丙酸甲酯。
[0059]
上面以示例性而非限制性的方式描述了本发明及其若干实施例。本领域的普通技术人员在阅读本说明书后能够联想到其他可替代的实施方案,这些实施方案也在本发明的范围之内。