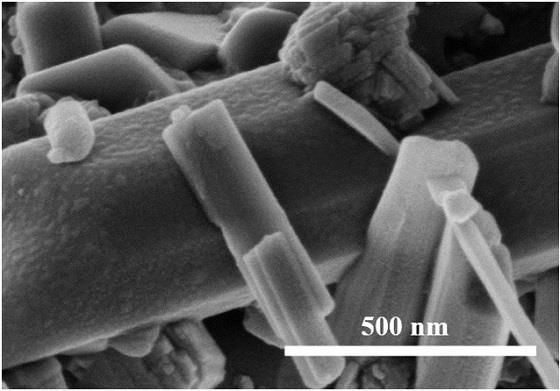
3wt%,mg:1-2wt%,zn:≤0.5wt%,mn:≤2wt%,al:≤1wt%,s:≤1wt%。
8.进一步的,以元素计,钠盐-高炉粉尘催化剂中na含量为23-26.5wt%。
9.进一步的,所述钠盐包括碳酸钠、硅酸钠、铬酸钠、十水碳酸钠中的至少一种。
10.本发明的另一目的在于提供一种催化剂,所述催化剂由前述方法制备得到。
11.本发明的再一目的在于提供一种前述钠盐-高炉粉尘催化剂在生物柴油制备中的应用。
12.本发明的又一目的在于提供一种生物柴油的制备方法,所述方法具体包括以下步骤:(1)将油与低碳醇按n
油
:n
醇
=1:(10-15)mol的摩尔比在反应容器中混合,然后按照相对于油7-10%的剂量加入前述催化剂;(2)密封反应容器,在65-75
º
c反应2h以上;(3)反应结束后,上层是醇和副产物,中层为生物柴油,催化剂位于下层,静置后催化剂与液体产物自动分离,移出液体产物,催化剂留在反应容器以备再次利用。
13.进一步的,所述的油为市售的或者是工业生产的、可食用的(包括但不限定于大豆油)或者不可食用的油脂。
14.进一步的,所述的低碳醇包括但不限定于甲醇。
15.相对于现有技术,本发明具有如下优点:1、本专利以高炉粉尘为原料,通过钠盐浸渍高炉粉尘在低温加热的条件下湿法浸渍磁力搅拌,并将得到的混合物控制煅烧相关工艺参数促进相关晶型转变获得高催化活性的催化剂;由于高炉粉尘中含有caco3、fe2o3与钠盐经过高温煅烧晶型转变形成了ca2fe2o5、nafeo2等物质从而获得具有高活性的催化剂,根据本发明的反应体系,煅烧后的催化剂微观结构为圆柱形颗粒结构,由此将获得的催化剂催化效率大幅提升至95%以上。
16.2、本专利合成的高炉粉尘催化剂可以在反应后与液体产物自动分离,后处理简单,无需多次水洗。
17.3、本专利合成的高炉粉尘催化剂在生物柴油制备中具有非常好的催化活性、稳定性和应用价值,16次反应后生物柴油得率仍能保持在90%以上,并且该催化剂可以直接用于低酸值油脂的反应,同样也能达到前述催化效果。
18.4、本专利通过回收利用高炉粉尘实现了资源回收再利用同时还有效减少环境污染。
附图说明
19.图1为本发明实施例1得到的钠盐-高炉粉尘催化剂微观形貌;图2为本发明对比例1得到的钠盐-高炉粉尘催化剂微观形貌。
具体实施方式
20.下面结合附图和实施例对本发明作进一步的详细说明,但附图和实施例并不是对本发明技术方案的限定。
21.实施例1-3取fe:33.42wt%,ca:10.17wt%,na:2.09wt%,mn:1.26wt%,mg:1.64wt%,al:
0.89wt%,zn:0.35wt%,s:0.89wt%的高炉粉尘利用球磨机进行研磨,研磨后粉尘过200目筛,过筛后粉尘至于烘箱中在105℃条件烘干5h,获得干燥后颗粒均匀的含铁高炉粉尘原料。
22.按照钠盐-高炉粉尘催化剂中na含量为26.18%配置碳酸钠的浸渍液,将高炉粉尘原料倒入浸渍液中置于油浴锅磁力搅拌2h,浸渍温度为65℃,得到的样品干燥后过200目筛,将得到的样品置于管式炉中于氮气中高温煅烧,煅烧后的样品过200目筛,获得钠盐-高炉粉尘催化剂。其中实施例1-3的参数及效果如表1所示。
23.表 1 实施例1-3的参数及效果 煅烧温度(℃)煅烧时间(h)气体流量(ml/min)催化剂微观形貌实施例1500210圆柱形实施例2600210圆柱形实施例3700210圆柱形实施例4重复实施例1,有以下不同点:高炉粉尘的组分fe:33.32wt%,ca:10.02wt%,na:2.00wt%,mg:1.57wt%,zn:0.32wt%,mn:1.23wt%,al:0.83wt%,s:0.82wt%,按照钠盐-高炉粉尘催化剂中na含量为24.58%配置碳酸钠的浸渍液。
24.实施例5重复实施例1,有以下不同点:高炉粉尘的组分fe:32.37wt%,mg:1.51wt%,zn:0.30wt%,ca:9.62wt%,mn:1.13wt%,al:0.79wt%,na:1.95wt%,s:0.77wt%,按照钠盐-高炉粉尘催化剂中na含量为23.26%配置碳酸钠的浸渍液。
25.实施例6-10采用实施例1-5制备的钠盐-高炉粉尘催化剂用于催化大豆油制备生物柴油的方法,包括按照醇油摩尔比例,向橡胶密封的玻璃瓶中加入的大豆油、甲醇和钠盐-高炉粉尘催化剂,进行反应,即获得生物柴油-甲醇混合产物,钠盐-高炉粉尘催化剂可通过静置分离进行回收。相关工艺参数及效果如表2所示。
26.表2 实施例6-10的工艺参数及效果
实施例催化剂来源大豆油含量甲醇含量催化剂含量反应温度反应时间生物柴油产率回收率6实施例10.01mol(7g)0.15mol(4.8g)0.49g65℃2h100.00%97.30%7实施例20.01mol(7g)0.15mol(4.8g)0.49g65℃2h100.00%95.30%8实施例30.01mol(7g)0.15mol(4.8g)0.49g65℃2h99.44%95.10%9实施例40.01mol(7g)0.15mol(4.8g)0.49g65℃2h99.54%97.02%10实施例50.01mol(7g)0.15mol(4.8g)0.49g65℃2h98.32%96.95%
实施例11-31重复实施例6的方法步骤及参数,不同之处在于:所采用的催化剂如表3所示。经测定,生物柴油产率如表3所示。
27.表 3 实施例11-31的工艺参数及效果实施例催化剂来源生物柴油产率11实施例6回收得到100.00%12实施例11回收得到100.00%13实施例12回收得到99.98%14实施例13回收得到98.78%
15实施例14回收得到99.66%16实施例15回收得到99.60%17实施例16回收得到98.40%18实施例17回收得到99.25%19实施例18回收得到99.14%20实施例19回收得到99.05%21实施例20回收得到98.97%22实施例21回收得到98.56%23实施例22回收得到98.21&24实施例23回收得到98.23%25实施例24回收得到95.84%26实施例25回收得到93.22%27实施例26回收得到92.89%28实施例27回收得到91.58%29实施例28回收得到90.69%30实施例29回收得到82.96%31实施例30回收得到78.44%可见,经实施例1制备得到的催化剂,在回收循环15次后仍能达到95%以上的生物柴油产率,回收循环19次后能达到90%以上的生物柴油产率。
28.实施例32-49采用实施例7的方法步骤及参数,不同之处在于:所采用的催化剂如表4所示。经测定,生物柴油产率如表4所示。
29.表 4 实施例32-49的工艺参数及效果实施例催化剂来源生物柴油产率32实施例7回收得到100.00%33实施例32回收得到100.00%34实施例33回收得到99.77%35实施例34回收得到99.56%36实施例35回收得到99.55%37实施例36回收得到98.94%38实施例37回收得到98.10%39实施例38回收得到98.02%40实施例39回收得到97.67%41实施例40回收得到97.59%42实施例41回收得到96.55%43实施例42回收得到96.08%44实施例43回收得到93.21%45实施例44回收得到92.56%46实施例45回收得到91.98%
47实施例46回收得到91.36%48实施例47回收得到90.38%49实施例48回收得到82.65%可见,经实施例2制备得到的催化剂,在回收循环12次后仍能达到95%以上的生物柴油产率,在回收循环17次后仍能达到90%以上的生物柴油产率。
30.实施例50-66采用实施例9的方法步骤及参数,不同之处在于:所采用的催化剂如表5所示。经测定,生物柴油产率如表5所示。
31.表 5 实施例50-66的工艺参数及效果实施例催化剂来源生物柴油产率%50实施例8回收得到99.44%51实施例50回收得到98.75%52实施例51回收得到98.22%53实施例52回收得到97.36%54实施例53回收得到97.27%55实施例54回收得到96.49%56实施例55回收得到96.32%57实施例56回收得到96.12%58实施例57回收得到96.03%59实施例58回收得到95.88%60实施例59回收得到94.92%61实施例60回收得到94.55%62实施例61回收得到93.87%63实施例62回收得到93.11%64实施例63回收得到92.45%65实施例64回收得到91.05%66实施例65回收得到84.22%可见,经实施例3制备得到的催化剂,在回收循环10次后仍能达到95%以上的生物柴油产率,在回收循环16次后仍能达到90%以上的生物柴油产率。
32.实施例67制备钠盐-高炉粉尘催化剂的方法采用实施例1的步骤和参数,不同点在于:配置的钠盐浸渍液为硅酸钠。
33.采用上述催化剂制备生物柴油的方法,其步骤和参数与实施例7相同,经测定,生物柴油产率为99.25%。
34.回收上述制备生物柴油完成后的催化剂,循环利用该催化剂继续制备生物柴油,其所采用的步骤和参数与实施例7相同。经测定,在回收循环13次后仍能达到95%以上的生物柴油产率,在回收循环18次后仍能达到90%以上的生物柴油产率。
35.实施例68制备钠盐-高炉粉尘催化剂的方法采用实施例1的步骤和参数,不同点在于:配置
的钠盐浸渍液为铬酸钠。
36.采用上述催化剂制备生物柴油的方法,其步骤和参数与实施例7相同,经测定,生物柴油产率为98.96%。
37.回收上述制备生物柴油完成后的催化剂,循环利用该催化剂继续制备生物柴油,其所采用的步骤和参数与实施例7相同。经测定,在回收循环11次后仍能达到95%以上的生物柴油产率,在回收循环17次后仍能达到90%以上的生物柴油产率。
38.对比例1本对比例钠盐-高炉粉尘催化剂的制备采用实施例1所述的相关工艺条件,唯一区别在于煅烧温度控制为300℃,经扫描电镜观察,生成的钠盐-高炉粉尘催化剂微观结构为不规则球形。
39.将上述钠盐-高炉粉尘催化剂用于催化大豆油制备生物柴油的方法,包括:按照油醇摩尔比1:15,向50 ml橡胶密封的玻璃瓶中加入的大豆油7g、甲醇4.8g和钠盐-高炉粉尘催化剂0.49g,于65℃下反应2h,即获得生物柴油-甲醇混合产物,钠盐-高炉粉尘催化剂可通过静置分离进行回收。
40.经测量,生物柴油的产率为94.11%,催化剂的第一次回收后的生物柴油产率为94.5%,生物柴油产率在90%以上的催化剂回收循环次数为4次。
41.对比例2本对比例钠盐-高炉粉尘催化剂的制备采用实施例1所述的相关工艺条件,唯一区别在于煅烧温度控制为400℃,经扫描电镜观察,生成的钠盐-高炉粉尘催化剂微观结构为不规则球形。
42.将上述钠盐-高炉粉尘催化剂用于催化大豆油制备生物柴油的方法,包括:按照油醇摩尔比1:15,向橡胶密封的玻璃瓶中加入的大豆油7g、甲醇4.8g和钠盐-高炉粉尘催化剂0.49g,于65℃下反应2h,即获得生物柴油-甲醇混合产物,钠盐-高炉粉尘催化剂可通过静置分离进行回收。
43.经测量,生物柴油的产率为97.11%,催化剂的第一次回收后的生物柴油产率为94.6%,生物柴油产率在90%以上的催化剂回收循环次数为5次。
44.对比例3本对比例钠盐-高炉粉尘催化剂的制备采用实施例1所述的相关工艺条件,唯一区别在于煅烧温度控制为900℃,经扫描电镜观察,生成的钠盐-高炉粉尘催化剂微观结构为块状结构。
45.将上述钠盐-高炉粉尘催化剂用于催化大豆油制备生物柴油的方法,包括:按照油醇摩尔比1:15,向橡胶密封的玻璃瓶中加入的大豆油7g、甲醇4.8g和钠盐-高炉粉尘催化剂0.49g,于65℃下反应2h,即获得生物柴油-甲醇混合产物,钠盐-高炉粉尘催化剂可通过静置分离进行回收。经测量,生物柴油的产率为2.53%,其原因是由于煅烧温度过高,催化剂表面发生烧结团聚,孔径堵塞,从而导致催化活性大幅度降低。
46.对比例4采用实施例1生产条件得到的高炉粉尘原料用于催化大豆油制备生物柴油的方法,步骤如下:按照油醇摩尔比1:15,向50 ml橡胶密封玻璃瓶中加入7g的大豆油、4.8g的甲醇和0.49g的高炉粉尘原料,将其置于65℃反应2h,获得生物柴油-甲醇混合产物。经测量,
生物柴油的产率为0.29%,可见,高炉粉尘本身并不具备催化活性。
47.对比例5取fe:33.42wt%,ca:10.17wt%,na:2.09wt%,mn:1.26wt%,mg:1.64wt%,al:0.89wt%,zn:0.35wt%,s:0.89wt%的高炉粉尘利用球磨机进行研磨,研磨后粉尘过200目筛,过筛后粉尘至于烘箱中在105
º
c条件烘干5h,获得干燥后颗粒均匀的含铁高炉粉尘原料。按照钠盐-高炉粉尘催化剂中na含量为26.18%配置碳酸钠的浸渍液,将高炉粉尘原料倒入浸渍液中置于油浴锅磁力搅拌2h,浸渍温度为65℃,得到的样品干燥后过200目筛,得到钠盐浸渍后的钠盐-高炉粉尘催化剂。
48.将上述钠盐-高炉粉尘催化剂用于催化大豆油制备生物柴油的方法,包括:按照油醇摩尔比1:15,向橡胶密封的玻璃瓶中加入的大豆油7g、甲醇4.8g和钠盐-高炉粉尘催化剂0.49g,于65℃下反应2h,即获得生物柴油-甲醇混合产物,钠盐-高炉粉尘催化剂可通过静置分离进行回收。
49.经测量,生物柴油的产率为97.11%,生物柴油产率在90%以上的催化剂回收循环次数为14次,显然,未经煅烧处理的催化剂产率达90%以上的回收循环次数远低于在500-700℃条件下经过煅烧处理的催化剂。