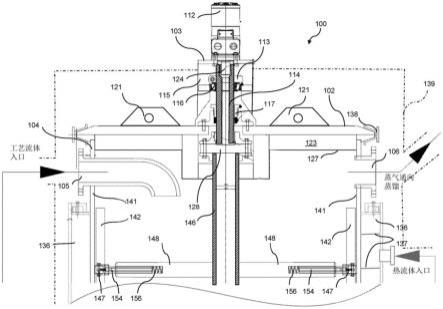
用于聚合物的液相催化热解的反应容器
1.相关申请
2.本技术要求于2020年4月7日提交的临时申请第63/006,540号的优先权的权益,所述临时申请通过引用整体并入本文。
技术领域
3.本发明涉及一种具有改进的经济性和能量效率的用于聚合物的热解的方法和设备。
背景技术:4.在现代生活中,塑料是普遍存在的。塑料是廉价的、易于模制的且用途广泛的。塑料性质具有许多优点,所述优点使得塑料对于商业应用而言是令人期望的,然而,塑料废弃物对环境(尤其是海洋生物群)的不利影响正变得日益明显。废纸和塑料,主要是包装材料,是发展中国家的环境和公共健康问题,在这些发展中国家,城市废弃物拾取和填埋处置是罕见的或不存在的。在全球范围内,在2018年,塑料产量据估计为3.8亿吨。从1950年至2018年,全世界生产了约63亿吨的塑料,其中9%和12%塑料分别被再循环和焚烧。研究人员表示,到2050年,海洋中含有的塑料的重量可能超过鱼类的重量。每年,使用大约5000亿个塑料袋,其中估计有1300万吨最终进入海洋,从而造成大约100,000只海洋生物死亡。最近的研究已经报道,可以在人体的几乎每个器官中发现源自塑料污染的微塑料和纳米塑料,并且怀疑所述微塑料和纳米塑料在癌症和神经退行性病状中可能发挥作用。
5.金属,尤其是铝被收集和再循环,因为所述金属具有市场。不幸的是,塑料的再循环仍然是主要挑战。存在用于限制塑料再循环的进展的技术问题和经济问题两者。塑料再循环领域的较慢发展产生了严重问题,其中全球每年有数百万公吨的使用过的聚合物材料被丢弃。绝大多数使用过的塑料被焚烧、填埋或倾倒的事实意味着这些材料作为一种资源将永远失去,尽管塑料有可能进行再利用和再循环。塑料生产需要大量的资本投资和大量的碳足迹。再利用塑料将不仅减少这些投资需要,而且还可以有助于减少工业碳排放总量。
6.许多常见类型的热塑性塑料,如聚烯烃(hdpe、ldpe、lldpe、pp)和聚芳香族化合物(ps、eps),可以使用可商购获得的基于密度的分离方法容易地分离。虽然机械再循环技术对于这些塑料中的一些塑料是有效的,但所述机械再循环技术目前不能处理混合的聚合物流。
7.化学再循环使用称为“热解”的化学反应,所述热解包含将热塑性聚合物的化学键裂解成烃气态和液体产物。热解是处理混合的聚合物以及已经耗尽所述聚合物用于进一步机械再循环的潜力的聚合物的重要方法。由于热解反应的温度较高,在430℃至550℃的范围内,并且反应停留时间较长,因此维持热解反应所需的能量很高。此外,许多裂化方法要求使用危险化学品,这会降低再循环的预期环境益处。
8.除了所述方法的高能量消耗之外,聚合物裂化还产生大量的碳,这些碳可能积聚在裂化塔的底部上,从而干扰混合和热交换的效率。较大分子裂化的速率受所述较大分子
可以与催化剂表面物理接触的速率限制。由于分子碰撞之间的平均自由程在蒸气中比在液相中大两至三个数量级,并且较高的温度意味着较大的热动力学运动,因此在原油裂化塔的流化床中发现的湍流(其中非常热的催化剂颗粒与热石油蒸气一起吹制)足以维持令人满意的反应速率,而无需借助于在液相中必要的机械混合(旋转桨叶等)。
技术实现要素:9.本发明涉及针对大型有机分子(又名催化解聚或cdp)的热解(裂化)的若干个主要缺点,特别是借助于非均相(固体)催化剂在烃溶剂中的聚合物的解决方案。具体地,本发明方法提供了一种将热供应到反应容器的改进方法。所述方法还改进了将热传递到反应物中的方式、增加了反应物与催化剂的混合效率并且有助于处理原料中的元素碳副产物和非反应性固体。
10.根据本发明的实施例,提供了一种“剪切板反应器”,所述剪切板反应器包括具有旋转臂的圆柱形桶,所述旋转臂将“剪切板”或刀片引导成靠近反应器壁,使得产生非常高的剪切应变速率。这种混合发生在吸热反应所需的热进入反应器的表面。
11.在一些实施例中,剪切板反应器的一般配置和尺寸以及新剪切板反应器设计的显著增强提供了多反应器设施的效率和有效性,使得有可能产生生产能力为100吨/天和更高的cdp设备。
12.在本发明的一方面,用于液相热解的反应器容器包含:圆柱形反应器桶,所述圆柱形反应器桶具有桶直径和桶长度;热交换壳,所述热交换壳围绕所述反应器桶,所述热交换壳连接到热交换回路并且被配置成使热交换流体在所述反应器桶的外表面之上流动;反应器顶板,所述反应器顶板安置在所述反应器桶的顶部处;反应器底板,所述反应器底板安置在所述反应器桶的底部处;中心轴,所述中心轴同心且可旋转地支撑在所述反应器桶内;至少一个臂组,所述至少一个臂组从所述中心轴径向延伸,每个臂具有远端,所述远端被配置成以距所述反应器桶的内壁一定间距支撑平行于所述中心轴延伸的剪切板,所述间距被配置成通过库埃特流动(couette flow)在所述剪切板与所述内壁之间产生预定应变速率;驱动马达,所述驱动马达由所述反应器顶板支撑并且被配置成驱动所述中心轴的旋转;入口,所述入口用于将流体引入到所述反应器桶中以供处理;以及至少一个出口,所述至少一个出口用于从所述反应器桶中取出加工产物。每个臂可以进一步支撑刮刀,所述刮刀被配置成移除沉积在所述内壁上的固体,所述刮刀的长度基本上等于所述剪切板的长度。所述至少一个臂组包括多个臂组,所述多个臂组沿所述中心轴的长度间隔开,并且其中所述多个臂组中的每个臂组中的一个臂支撑单个剪切板,所述单个剪切板的剪切板长度基本上等于所述桶长度。所述剪切板的后缘可以远离所述内壁弯曲,以使流体流扩散并且引导所述流体流远离所述内壁。每个臂可以包含活塞,所述活塞被配置成对所述臂的所述远端施加可变压力。
13.在一些实施例中,导电线可以延伸穿过每个臂并且在远端处电子连接到所述剪切板并且在近端处电子连接到导电性检测器,其中测量电导率以指示所述剪切板与所述内壁之间的物理接触。
14.所述热交换回路包括熔融盐回路,所述熔融盐回路包含多个太阳能聚光器。由剪切板实现的预定应变速率可以为大约102/秒至103/秒。所述桶长度与所述桶直径之间的纵
横比优选地在5∶1至10∶1的范围内。所述驱动马达是液压马达,所述液压马达被配置成以40rpm至60rpm驱动所述中心轴的旋转。
15.在本发明的另一方面,加工设施包含多个上述反应器容器,其中所述反应器容器串联连接。所述多个反应器容器中的每个反应器容器可以被配置成在不同的加工温度下操作,其中所述加工温度从所述串联反应器容器中的第一个反应器到所述串联反应器容器中的最后一个反应器逐渐增加。多个输入罐可以平行安置,每个输入罐具有与第一反应器容器流体连通的出口,使得要加工的材料在交替的输入罐中进行预加工,以将基本上连续的材料流提供到所述第一反应器容器中。
16.在本发明的仍另一方面,用于再循环或升级改造塑料的方法包含:将塑料颗粒、溶剂油和催化剂的分散体混合以形成浆料;将所述浆料加热至加工温度;以及将经加热的浆料进给到上述加工设施中,以对所述浆料进行加工。
17.在本发明的又另一方面,用于液相热解的改良型反应器容器包含剪切板组合件,所述剪切板组合件安置在可旋转轴上,所述可旋转轴同心地安置在圆柱形反应器容器内,所述剪切板组合件包括剪切板,所述剪切板安置在从所述轴径向延伸的臂上并且平行于容器内壁表面,所述剪切板和所述臂被配置成在所述容器内旋转,以在所述容器内壁表面与所述剪切板的外表面之间产生粘性阻力。所述改良型反应器容器可以进一步包括刮刀,所述刮刀安置在所述剪切板的前缘上以移除沉积在所述容器内壁表面上的材料。
18.可以提供热交换壳以围绕所述反应器容器,其中所述热交换壳连接到热交换回路并且被配置成使热交换流体在所述反应器容器的外表面之上流动。所述热交换回路可以是熔融盐回路,所述熔融盐回路包含太阳能聚光器。
19.所述臂可以是多个臂组,所述多个臂组沿所述可旋转轴的长度间隔开,使得所述多个臂组中的每个臂组中的一个臂支撑单个剪切板,所述单个剪切板的剪切板长度基本上等于所述反应器容器的长度。所述剪切板的所述后缘可以远离所述容器内壁表面弯曲,以使流体流扩散并且引导所述流体流远离所述容器内壁表面。每个臂可以包含活塞,所述活塞被配置成对所述臂的远端施加可变压力。在一些实施例中,导电线延伸穿过每个臂并且在远端处电子连接到所述剪切板并且在近端处电子连接到导电性检测器,从而允许测量电导率以指示所述剪切板与所述容器内壁表面之间的物理接触。
20.由所述剪切板产生的粘性阻力对应于大约102/秒至103/秒的应变速率。反应器容器长度与反应器容器直径之间的纵横比可以在5∶1至10∶1的范围内。附接到所述轴的液压马达被配置成以40rpm至60rpm驱动所述可旋转轴的旋转。
附图说明
21.图1是根据本发明的一实施例的反应器头部组合件的上部的横截面侧视图。
22.图2是根据本发明的一实施例的反应器头部组合件内部内的剪切板臂的图解顶视图。
23.图3a和3b分别是根据本发明的一实施例的剪切板臂组合件的透视图和分解视图。
24.图4a和4b是具有剪切刀片的剪切板臂的实施例的部分横截面顶视图。
25.图5a和5b是圆柱形反应容器内部的图解透视图,示出了根据本发明的一实施例的剪切板和刮刀。
26.图6是根据本发明的一实施例的反应器容器的底部的横截面视图。
27.图7是根据本发明的一实施例的反应器容器的底部的透视图。
28.图8是用于cdp处理的示例性准备序列的框图。
29.图9是根据本发明的一实施例的结合多个反应器的示例性设备示意图。
30.图10是根据本发明的一实施例的用于转化设备中的熔融盐回路的示意图。
具体实施方式
31.虽然塑料和原油的cdp均使用固体催化剂进行热解(即,“裂化”),但石油通常作为蒸气并且在比cdp最佳温度和压力更高的温度和压力下加工,其中液相用于调节反应温度。本文所公开的改进涉及cdp反应容器和加工的多个方面,每个改进本身代表向用于塑料再循环的更有效且环境可持续工艺的显著进步。
32.对于热源,电阻热是有吸引力的,因为电阻热易于控制并且已经直接应用于中试规模(大约1至10吨/天)设备中的反应容器并且通过实验商业规模(约100吨/天)设备中的热交换流体间接应用,其中已经提出燃气轮机废热的回收但未在实践中尝试。
33.已经提出,可以使用机械能而不是热能来驱动吸热热解。此类建议包含使用冲击射流、高性能(尽管是外部加热的)混合器以及破裂的空化气泡。授予c.koch的美国专利第7,473,348号描述了向反应容器的壁施加电热,其中通过高速射流冲击水力旋流器的逆流循环来机械地供应另外的能量。授予spitzauer等人的美国专利第9,371,492号中描述了搅拌的反应容器外部的热交换器。
34.尽管已经使用电阻加热来供应大部分能量,并且机械(粘性耗散)加热据称为cdp的中试规模测试提供一些另外的能量输入,但在商业规模操作中使用这些方法通常在经济上是不可行的,因为与直接施加热能相比,必须消耗三至五倍的热能来供应电阻热或马达所需的电能。
35.虽然电能和轴功到热的转换是100%有效的,但热到功的转换限于卡诺δt/t的某一分数(通常小于一半)。这种热与发电效率、传动效率和马达效率的乘积导致总效率为大约20-30%。
36.将聚合物(例如,聚乙烯)的温度从环境温度(20℃)升高至柴油的沸点(390℃)所需的热能
[0037][0038]
而在给定每种物质的生成焓的情况下(来自用nist检查的propep),必须供应以引起聚乙烯吸热热解成柴油的能量为:
[0039][0040]
使得用于升高反应物温度的能量是用于驱动热解的能量的十四倍以上。(注意,美国海军推进剂评估计划(propellent evaluation program,propep)数据库值用于h
f,p e
和h
f,d
,其给出比nist更大的h
pyr
。(nist具有十六烷c
16h34
而不是柴油的hf)。)
[0041]
在cdp反应器中,随着工艺混合物加热至其刚好高于柴油沸程的最终温度,许多分
子量和蒸气压力增加的产物将从工艺混合物中出现。关于c
p
δt>>h
pyr
的论点适用于所有产物,并且当将溶解热和蒸发热添加到整合的热容量时,显然对于大规模热解反应器,电或机械功不是可行的能量输入机制。
[0042]
cdp反应器需要在略高于390℃的柴油沸程下操作,并且有用的传热流体必须比这一柴油沸程高至少20-30℃而稳定,以避免过大的热交换表面积和过高的流体泵送速率带来的经济负担。
[0043]
联苯和二苯醚的混合物(bdom)可能是可获得的最耐热的有机传热流体。一种这样的混合物(eastman)已经用作电加热器之间的传热流体,并且与cdp工艺流体进行热交换。(参见例如,美国专利第9,371,492号。)
[0044]
eastman75的最高操作温度是385℃,而eastman vp-1的最高操作温度稍高(400℃),其蒸气压必须调节到10巴以在390℃下保持液态。虽然沸腾的bdom的蒸发热是控制放热反应的温度的优异方式,但其不适合作为吸热热解与热源之间的热交换流体,所述吸热热解需要在vp-1的t
max
附近操作,所述热源如比t
max
高至少150℃的聚光太阳能、涡轮机或往复式发动机排气约500℃>t
max
或者甚至约1000℃>t
max
的烃/空气火焰。
[0045]
传热回路中高于设定点温度的偏移可能由于泄漏、阀故障、泵故障、操作者误差、控制器对瞬变的过冲响应等而发生。在bdom沸腾液体和蒸气的情况下,温度增加引起压力增加,除非蒸气通过膨胀或通过热交换器/冷凝器或优选地两者冷却。
[0046]
由于bdom泄漏或排放到环境中导致易燃或爆炸性雾,因此使用bdom需要高于10巴操作压力(对环境压力加上cdp工艺的适度sf)的大过压安全系数,以及大膨胀罐和冷凝器。在美国专利第9,371,492号中描述的商业规模试验设备使用具有通向环境的备用泄压口的大型vp-1膨胀罐。
[0047]
反应物必须达到可以发生热解的温度,在此之后必须产生连续的能量供应以维持反应温度,从而促进聚合物轻度吸热分解成更小的分子,所述分子对于运输燃料是特别有用的。通常,烃,尤其是烃和多糖聚合物,以及可以在高反应器温度(至多约400℃)下抵抗分解的热交换油溶剂具有低热导率、低扩散率(α=k/ρc
p
)和高粘度,这阻碍了对流和平流热交换。
[0048]
在美国专利第9,371,492号中,使用搅拌反应容器外部的热交换器,其中电加热的vp-1在壳侧循环。工艺流体在热交换管中循环,其中结垢和堵塞是预期的并且在商业规模的试验设备中经历。
[0049]
反应物聚合物需要通过剧烈混合接近固体催化剂表面。热稳定的基于烃的溶剂以及反应物聚合物的相对高的粘度增加了实现必要混合的机械功。
[0050]
各种现有技术教导包含驱动吸热热解的能量应该来自冲击射流、破裂的空化气泡和特殊混合器,如授予koch的美国专利公开第2008/0116116号中所描述的。
[0051]
加热的反应容器表面上和热交换器流动通道中的碳累积在历史上一直是工艺问题。由于碳涂层而变得无活性的催化剂(即,“废”催化剂)和固体副产物(主要是进料质量的约10%的元素碳)必须被移除以进行进一步处理或处置。
[0052]
在授予koch的专利公开wo2008/061484和us2008/0116116中,所述专利公开各自通过引用并入本文,固体(碳加上不反应的物质)通过重力进行分离。还授予koch的随后的专利(美国专利第7,473,348号)用刮刀移除工艺容器壁上的碳累积并且用水力旋流器从工
艺流体中移除碳累积。将废催化剂连同其它未反应的固体一起加热至550℃以烧掉焦炭,使得催化剂可以返回至工艺中,如通常利用石油气相裂化进行的。
[0053]
根据本发明的方法,与常规刮刀刀片一起使用的剪切板在解决由以下原因中的每个原因引起的问题方面是高度有效的:1)缓慢热交换成油性(粘性、低导热性)液体;2)反应物与催化剂的混合不完全且缓慢;以及3)副产物碳污染热交换器和反应器表面。此外,虽然通过混合功供应的反应能量的物理学是合理的,但是在商业规模上的经济学却是不合理的。
[0054]
具有旋转刮刀的圆柱形反应器与刮板式表面热交换器(sshe)共享这一特征,但是与sshe的不同之处在于所述圆柱形反应器使用剪切板来有效地产生与如在连续搅拌罐式反应器中发现的小型高速的刀片或桨式叶轮相当的非常高的应变速率。当执行剪切板的预期功能时,所述剪切板实际上不会刮擦。
[0055]
由本文公开的剪切板反应器产生的库埃特流动与在泰勒-库埃特反应器(taylor-couette reactor)中发现的库埃特流动不同,所述泰勒-库埃特反应器具有相对宽间隔的同心圆柱体,所述同心圆柱体产生被称为“泰勒单元(taylor cell)”的多个涡流单元。本发明的剪切板反应器设计采用非常靠近反应器壁延伸的离散刀片,以产生所期望的高应变速率。
[0056]
具有跟踪槽式收集器的聚光太阳能(csp)达到的温度满足cdp工艺的要求。csp阵列的热输出的投入到cdp中的部分产生对csp的持续时间较短的热能储存进行补充的长期可储存能量形式。图10提供了用于塑料转换设备的示例性csp加热的熔融盐回路502的示意图。(参见例如,图9中所示的盐回路502。)
[0057]
特别令人期望的是,能够用价值较低的塔顶气体和较不容易储存的馏分来运行热力发动机,如埃里克森(ericsson)、布雷顿(brayton)、迪塞尔(diesel)、斯特灵(stirling)、奥托(otto)、朗肯(rankin)(按优先顺序),并且能够利用发动机的废热进行催化热解工艺。由发动机产生的电力最适合用于“酒店负载(hotel load)”——与加热的主要电力需求无关的系统组件,如泵、混合器、致动器、控制器等,其中任何过量电力都是在场外销售的,而不是用于加热热解反应容器。
[0058]
用于csp设备的硝酸盐熔融盐(有时被称为“太阳盐”(60%nano3,40%kno3))是用作cdp工艺的传热流体的良好候选材料,而不管太阳能是否是主要热源。熔融盐可以在至多550℃下操作并且也可在环境压力下操作。泄漏仅发生固化,而不是像有机传热流体那样形成爆炸性雾。在启动时,必须规定在具有电、燃气或发动机废热的辅助热交换器中使工艺流体上升到高于盐熔点(对于太阳盐,熔点为约250℃,但是热处理盐的熔点低至135℃)。
[0059]
反应室配置:圆柱形(304l ss)反应容器具有高轴向比(长度/直径为5∶1至大约10∶1),使得维持合理的表面/体积比以进行通过容器壁的热交换。最大直径为约一米,但是略微更小的直径落入标准焊接管的范围内以获得更好的结构经济性,并且具有更好的热交换表面/体积比。
[0060]
下表1中提供了内径(id)为0.761m且长度为5m、估计比重为1.30[g/cm3]的反应器的粗略质量累积。
[0061]
表1
[0062][0063]
在表1中,如果选择典型的预期溶剂和反应物密度和质量分数,则反应器质量累积将为:
[0064]
表2
[0065][0066]
这是在工业规模设施中用于经济制造、运输、厂内安装和更换或维护的适当尺寸和质量。
[0067]
图1示出了根据本发明的一实施例的示例性反应器头部组合件100的横截面。组件被设计成用于在高温下制造、维护和操作的经济性。反应器板102位于圆柱形反应容器104的顶部上,为驱动马达112提供支撑,所述驱动马达在容器内使轴146旋转。反应器板102可以通过夹具138(如马尔曼夹具)附接并密封到容器104的上板,以利用所述夹具的强度和易于附接和移除的优势。可替代地,可以使用螺栓环。通常为低速、高扭矩液压马达(例如,伊顿h系列shar-lynn(eaton h-series shar-lynn))的马达112安装在反应器板顶部103上并且通过伍德鲁夫键(woodruff key)连接到上轴夹具124。上轴114封闭在焊接钢框架115内,所述焊接钢框架栓接到顶板103。轴114由一个或多个轴承116引导,所述一个或多个轴承可以是锥形滚柱轴承或止推轴承,如glacier-garlock cbm自润滑烧结石墨-青铜。上轴114通过凸缘128连接到中心轴146。凸缘128和轴114通过高密度陶瓷纤维板或云母盘与中心轴146绝缘。反应器顶板和附接到所述反应器顶板的驱动组件也通过50mm(2
″
)的闭孔陶瓷泡沫绝缘材料层123绝缘,所述闭孔陶瓷泡沫绝缘材料层由20号不锈钢板127支撑和保护。所有经加热的组件在其外表面上具有至少50mm至75mm(2
″‑3″
)的热稳定绝缘材料(t形玻璃或等效物),总体上由虚线139指示。以90
°
间距围绕反应器板102径向布置的四个凸耳121允许当反应器正在操作时移除和更换驱动头部和剪切板组合件,提升整个反应器,和/或附接横联。
[0068]
要加工的流体通过入口端口105引入到容器104中。蒸气在出口端口106处离开容器。入口105和出口106位于反应器容器104的桶中,以便于移除头部和剪切板组合件。图中
示出了反应器头部组合件的另外的组件,但未进行单独标记。这些组件包含密封件、腺体、轴承、夹具、紧固件、绝缘材料以及在此类系统中常用的其它组件。此类组件的标识和选择将在本领域的技术人员的水平内并且不在本文中进行描述。
[0069]
热交换壳136可以由钢(优选地不锈钢)管形成,所述钢管的半径比反应容器的外径大约5cm(2
″
),以便提供用于传热流体的通道。为了使壳与反应器壁之间的热膨胀差异最小化,壳136优选地由与反应器容器104(304l)相同的合金制成。热交换壳136围绕圆柱形反应容器140同心地安置,并且通过焊接凸缘栓接到反应器桶上的环形凸缘上,以便提供用于传热流体的通道。钢挡板137被铜焊到圆柱形反应容器104的外表面,其中在交替侧上具有45
°
间隙以将传热流体(例如,太阳盐流体)引导到外反应器圆柱体壁的所有区域。所有经加热的组件在其外表面上具有至少50mm至75mm(2
″‑3″
)的热稳定绝缘材料。
[0070]
从中心轴146径向延伸的是多组臂148。中心轴146由马达112驱动,从而使得所述中心轴使执行多个功能的一组或多组刀片以约40rpm至60rpm旋转。在所展示的实例中,刀片组合件包含支撑在臂148上的一对刀片,所述臂在轴146上分开180
°
布置。如对于本领域的技术人员而言将显而易见的,可以采用另外的臂和刀片,例如,以120
°
分开的三个刀片或以90
°
分开的四个刀片。因此,提供两个刀片布置作为说明性实例。
[0071]
参考图2,每个刀片的关键元件是剪切板142和刮刀143,所述刮刀移除大部分沉积在传热表面141上的碳(焦灰)。支撑约5mm(3/16
″
)厚的不锈钢剪切板142,使得所述剪切板的表面基本上平行于反应器容器壁141并且与所述反应器容器壁间隔开约2mm至3mm,使得通过在剪切板142与壁141之间的库埃特流动维持大约102/秒至103/秒的应变速率。如图所示,工艺流体流由剪切板142的后缘和刮刀143扩散,偏离壁141并且在剪切板组合件的后部形成涡流。
[0072]
刮刀刀片143的前缘使新反应的材料和尚未反应的材料两者的工艺流体偏转远离反应器壁141并且朝向圆柱形反应容器的中心部分,同时刮刀刀片下游的涡流使工艺流体从主体平流输送回经加热的反应器壁141,从而增加总体热交换速率。剪切板142的后缘122远离反应器壁141弯曲,以加强剪切板组合件,扩散流动,并且与刮刀刀片143的前部一起引导所述流动远离反应器壁,利用由于在蒸气热解和释放时体积增加产生的在刀片运动方向上的小推力。
[0073]
剪切板臂148焊接到中心轴146,并且接头可以用环形角撑板158加固。在每个臂内,活塞164在青铜衬套165内径向移动。活塞164的远端焊接到框架147,所述框架承载轮149的轮轴(每个臂2个)。支架151通过三个螺栓附接到框架147以允许进行调节。轮149可以是青铜衬套的或仅是铜的。刮刀143安装在刮刀臂155上,所述刮刀臂通过轮轴157附接到框架147。
[0074]
活塞164被室161中的弹簧162向外偏压。轮149和活塞164的组合允许剪切板142顺应反应器桶的小离圆偏差(out of round deviation)或轴146的偏心位置。
[0075]
图3a和3b展示了具有比在图2中示出的设计更稳健的“支架(truck)”组合件的剪切板臂的实施例。这种配置通过增加前导轮204为剪切板242和刮刀243提供增加的支撑,使得两个轮204和210跨在剪切板242上。为了容许中心轴与反应器桶之间更大的不对称性,将青铜腕部轴承296装配在焊接到框架224的腕部轴承壳体297内部。腕部销包含两个半部:第一半部295具有用于收纳螺栓294的中心孔,而另一写入销半部298是有螺纹的,以用于将两
个腕部销半部夹持到活塞293的螺栓。被弹簧偏压的活塞293在臂291内的青铜衬套292内滑动。
[0076]
后轮210和前轮204各自在青铜衬套203上运行并且由大的止推垫圈202轴向保持。轮衬套203和止推垫圈202通过螺栓201和螺母206夹持到框架224。剪切板242、刮刀243以及支架本身的重量由青铜止推轴承299承载,所述青铜止推轴承保持在具有弹性挡圈210的腕部衬套壳体297的上端中。
[0077]
在示例性5米长的反应器中,5米长的剪切板242通常将沿其长度由五个臂支撑。(参考例如,图5a和5b。)为了使五个支架中的每个支架承受剪切板重量的相等部分,设置加强杆214,对所述加强杆进行攻丝以用于机器螺钉并且紧固以将所述杆保持到蹄板207,所述艉包板又附接到框架224。然后,作为组装的最后步骤,将剪切板或构成剪切板的区段焊接到加强杆214。
[0078]
刮刀243保持在刮刀臂和弹簧组合件215上,所述弹簧组合件从由耐热合金形成的弹簧212延伸,以在刮刀上提供反向力。刮刀臂枢轴设置有青铜衬套。这种刮刀组合件用将后轮210夹持到框架224的相同的螺母和螺栓固定。弹簧力调节螺栓213通过焊接到框架的小支架起作用。
[0079]
图4a和4b展示了剪切板组合件的另外的实施例,所述实施例采用通过支架341附接到活塞364的远端的柔性剪切刀片342、343。剪切刀片342、343由如(一种奥氏体镍铬基超合金)等合金制成。刀片的未偏斜/自由形状被示出为虚线。
[0080]
使用清洁的涡轮机油(即,工艺溶剂)通过液压通过活塞364将可调节力施加到剪切刀片,所述涡轮机油从下轴轴承正下方的液压回转沿驱动轴46向上引导。活塞364在ggb-cbm石墨/青铜轴承363内移动并且采用graphoil密封件365。刀片夹具341与剪切刀片电共用,其中绝缘材料将刀片与活塞364隔离。活塞364的中心填充有炉水泥以将活塞密封,并且引导和保护连续性传感导线366。导线366连接到刀片342并且与欧姆表电连通允许电导率测量用于指示剪切刀片与141壁之间的物理接触。调节活塞364上的液压,直到刀片342、343在存在高应变速率的表面层上产生液压。在高液压和低或无转速下,可以检测在刀片342、343与壁141之间形成半导体通路的碳累积。如果没有安装专用刮刀,则可以采用剪切刀片342、343通过将旋转方向反转几转直到电导率降低以指示不存在碳层来从壁刮擦碳。
[0081]
图5a和5b展示了图2的剪切板组合件的稍微不同的实施方案的圆柱形反应容器140的俯视图。如图所示,六螺栓凸缘144通过支撑剪切板142和刮刀143的五组臂148焊接到中心轴146。除了框架147和轮149的构造略有不同之外,组合件基本上是相同的。
[0082]
图6是反应器容器的实施例的底部部分的横截面,其示出了剪切板驱动轴146如何通过简单的花键联接到底部刮刀轴451,所述花键包含栓接到刮刀轴451的两个花键齿453。齿453在驱动轴146中铣削的狭槽452中竖直地移动,从而允许底部刮刀组合件通过反应器容器的顶部被向上抽出。具有至少五个直径的两个轴146与451之间的重叠确保轴是同心的,并且轴向轴承455可以保持剪切板组合件的下端的同心度。轴向轴承455保持在底盖457内,所述底盖栓接到反应器容器底板460。底板460通过马尔曼夹具462附接到反应器容器的下端。固体材料被底部刮刀456扫至出口459。
[0083]
通过螺钉附接到板454的底部的止推轴承445承受底部刮刀组合件的重量并且保持底部刮刀456与底板460的上表面轻接触。热交换器壳配件458为逆流初级传热流体提供
热交换器壳136的出口。如先前所述,钢挡板137被铜焊到圆柱形反应容器的外表面,以将传热流体引导到反应器容器的外表面。
[0084]
图7提供了图6中所示的反应器容器的底部部分的透视图,其中用相同的附图标记标识相同的组件。这个视图中的旋转是顺时针的,如臂148上的箭头所指示的。底部刮刀456的轴线被板454偏置,使得固体材料被迫朝向出口459。
[0085]
本发明方法的关键方面是通过旋转剪切板提供的混合和此混合与反应器容器的经加热的表面紧密接近的组合。这种组合有效地将吸热热解传导到工艺流体中。
[0086]
与如叶轮、桨叶或螺旋桨等其它机械装置相比,可以通过库埃特流动用更少的电力产生高得多的剪切应变速率。为了说明,可以比较粘性阻力对流体动力学阻力如何取决于速度。(应注意,声音或超声实现了高应变速率,但转导效率较低(约10%)。此外,在高温下,磁性组件和电组件表现不佳,或甚至无法存活。)
[0087]
在以角速度ω(rad/秒)=2πfr=2πrpm/60在半径为r的反应器容器的圆柱形壁附近以切向速度v
t
=ωr旋转的剪切板和刮刀组合件上的流体动力学阻力为
[0088]fhy
=cdqaf,其中动态压力
[0089]
阻力系数cd取决于雷诺数re=ρ v
t
l/μ,当(102<re<105)时,可以估计所述雷诺数处于0.5<cd<1.5的范围内。μ是绝对粘度并且l是本体的特性长度(在此处,)。
[0090]
具有面积as(在此处,约10cm
×
5m=0.5m2)的剪切板与反应器壁之间的粘性阻力为
[0091][0092]
其中δr~2.5mm是板与反应器壁之间的剪切间隙。在加载有轻弹簧力f
sp
~22n并且进一步由作用在质量(ms=2.32kg)上的离心力加载的刮刀刀片上的摩擦阻力f
fr
为
[0093]ffr
=fnμk,其中fn=f
sp
+msrω2[0094]
以及不锈钢罐壁上的青铜刮刀的动摩擦系数μk~0.2。使用表3中列出的系统参数运行模拟。在考虑流体动力学阻力、库埃特流动(粘性)阻力和刮刀摩擦阻力的情况下,表4中示出了模拟结果,包含总扭矩τ=r(f
hy
+f
vi
+f
fr
)和功率p=ωτ。
[0095]
表3
[0096][0097]
剪切板组合件上的(粘性)阻力f
vi
随着rpm线性增加,而流体动力学力f
hy
随着旋转速度的平方增加,使得流体动力学(压力)阻力f
hy
在所有旋转速度下占主导地位并且阻止在远高于约60rpm的速度下的操作。
[0098]
对于具有m
feed
=100吨/天的cdp设备,使用2∶1的溶剂油与进料比以及工艺流体密度ρ
pf
~1.0吨/m3(由于ρ
oil
≤1吨/m3并且ρ
feed
≥1吨/m3),工艺流体的体积流量v
p
=3m
feed
/ρ
pf
=0.21m3/分钟。
[0099]
反应器中的工艺流体的体积vr=(π/4)d2l=2.95m3,使得流体包(parcel of fluid)在反应器中的平均停留时间将为vr/v
p
=2.95/0.21=14.0分钟。
[0100]
对于在本文中建议的规模(d=0.75m)
×
l=5m)的液相热解反应器,在反应器壁与剪切板(每个反应器两个剪切板)之间加工的每流体单位时间的体积为v
·
=v
tagap
。例如,如果40rpm选自以下表4,其中切向速度v
t
=1.6米/秒并且a
gap
=(2mm)
×
(5m)
×
2个板=0.025m2,则v
·
=.04m3/秒=2.4m3/分钟。
[0101]
穿过剪切板与反应器壁之间的工艺流体的体积率与所述工艺流体流过设备的体积率的比率pf为每个反应器v
·s/v
·
p
=11.4。在每个设备具有最少三个反应器的情况下,每个工艺流体包将在经加热的反应器壁附近经受平均34次的高剪切速率。(注意,这是低估值,因为工艺流体体积随着产物以蒸气形式离开蒸馏塔而降低。)
[0102]
表4
[0103]
[0104]
这种工业规模的v
·
是在应变速率ε
·
=798/秒(表4中的
′
sdot
′
)下实现的,所述应变速率等于最大值并且是通过由s.vlaev等人(《工程科学与技术杂志(j.eng.sci.tech.)》,2(2):177-87,2007)描述的cstr叶轮中的最佳实现的平面内流场上的平均值的大约两倍。
[0105]
使用本发明反应器的原料的cdp加工包含制备工艺流体混合物。图9,下面所讨论的,展示了用于这种加工的示例性装置。参考图8,在步骤802中,将新鲜催化剂与再循环的溶剂油在适度温度(约100℃)下充分混合。在步骤804中,在低速机械混合器中将油/催化剂分散体添加到传入的原料装料中,以便制备浆料。
[0106]
为了提高效率,包含两个(或更多个)输入罐(参见例如,图9中的罐562)的加工装置允许在罐之间进行交替以供应连续的反应物流。当将连续的反应物材料流进给到第一输入罐中时,预加工预备步骤可以在两个或更多个罐中的另一个罐中进行:
[0107]
步骤806:使用浆料泵来将装料转移到输入罐中。
[0108]
步骤808:装料通过液环真空泵除气。
[0109]
步骤810:将装料升温至约200℃,以引入第一级反应器。
[0110]
步骤812:室空距(ullage)由释放的蒸汽和其它挥发性气体和蒸气进行吹扫。如果氧传感器发信号通知必要性,则可以注入塔顶气体或石脑油以完成吹扫。
[0111]
在预加工已经完成之后,在步骤814中,工艺流体混合物进一步被加热以达到工艺温度,并且在步骤816中被转移到反应器(第一级,如果多级装置的话)中进行加工。启动反应器马达,以使用搅拌、剪切力和热的组合来加工如本文进一步所描述的混合物持续预定时间段。如下面参考图9所描述的,多个反应器可以串联连接以允许在不同的温度下加工和在不同级去除所提取的组分。
[0112]
出于许多原因,本文所公开的具有其同心永久热交换壳和用旋转剪切板/刮刀刀片扫过的内表面的圆柱形反应容器是废纸和塑料热解设备的通用组件。优点包含:(1)所述圆柱形反应容器可以串联部署使得所述圆柱形反应容器的温度可以分级增加;(2)每个温度级中的停留时间可以通过以下方式进行调节:(a)改变在温度级中并联部署的反应器的数量;和/或(b)改变在温度级中反应器的长度以保持热交换所需的表面/体积比;以及(3)由可互换模块构成的设备可以根据产品需求和原料组成和可用性进行调整。
[0113]
图9提供结合本发明剪切板反应器的cdp设备500的一个可能实施方案的示意图。示出了在每个级中分别具有相等长度的剪切板反应器567l、567m和567h的三个热级,即低、中和高(四个热级,如果对进料/锁定级进行计数的话)。温度级的数量、反应器长度和每个温度级的反应器的数量可以有所不同。例如,如果偏向于将柴油燃料作为产物,则可以存在呈串联和并联组合的多个高温反应器(所述高温反应器全都在柴油沸程(至多约390℃)内),以增加工艺流体在这一级的停留时间。
[0114]
热电联产(chp)的使用对于废塑料加工的经济可行性即使不是必要的,也是重要的。涡轮机驱动的发电机(发电机组)优于柴油机,这是因为柴油机在过低的温度下将大部分废热排出到其液体冷却系统而无法使用。因此,在图9中描绘的cdp设备500采用熔融盐传输回路502(灰线)和工艺蒸汽热传输回路504(虚线)。黑实线表示溶剂+聚合物回路506。涡轮机废气首先在交换器566中加热熔融盐,并且然后在锅炉572中连续产生工艺蒸汽。
[0115]
在从环境温度启动时,依靠所储存的压缩气体573运行的chp燃气轮机产生工艺蒸
汽,所述工艺蒸汽被引导到盐罐563中的预热交换器564s(盐回路在关闭时排到所述交换器)和交换器564p,以在溶剂循环时预热工艺溶剂并且因此预热反应器。蒸馏再沸器569和蒸馏塔568的预热通过冷凝工艺流体蒸气来实现。在操作中,一个熔融盐回路加热蒸馏再沸器569,并且另一个回路通过同心的带挡板的热交换壳577加热串联的高温反应容器567h、中温反应容器567m和低温反应容器567l。
[0116]
将研磨和分选的塑料进给到料斗561中,并且在进料锁定罐562中与催化剂和溶剂混合,所述进料锁定罐可以交替地工作以提供连续的塑料浆料流进行加工。在蒸汽进入罐空距之前,通过液环真空泵在轻微搅动下对装料进行除气,其中在进入同心热交换壳的蒸汽将变化加热到120℃至140℃以引入到第一反应器热级中时,压力保持高于环境压力。
[0117]
工艺流体(溶剂和溶质聚合物)前进通过热分级剪切板反应器567h、567m和567l,其中通过改变反应器的竖直长度和通过使熔融盐平行流过反应器的热交换壳保持在相同温度下的所述反应器的数量如先前所述调节每个热级中的停留时间。
[0118]
来自每个热级的蒸气通过绝缘管576被带到蒸馏塔568的不同竖直高度,所述不同竖直高度与所述蒸馏塔的相应温度相匹配。蒸馏“底部产物”通过571返回以再循环共蒸馏的溶剂以及高沸点聚合物碎片,用于另一次通过高温反应器567h。将蒸馏“馏分”作为液体冷凝物的一部分从584处的冷凝器中回收,其中余量作为回流返回到蒸馏塔。
[0119]
工艺流体从高温级取出并且通过水力旋流器579进行处理,其中以保持反应器中的流体水平的速率取出含有较粗颗粒的底流。旋流器溢流(通过路径570)循环通过较低温度的反应器壳,以便在再循环到进料锁/预加热器562之前与传入的流体交换(回收)热。然后,倾析离心机或螺杆压机580加工旋流器底流,在此之后,使湿固体经受蒸汽的逆流,以从焦炭(和粘附到“废”催化剂的焦炭)的表面共蒸馏出溶剂和其它吸附材料。蒸汽和共蒸馏物质与空气或水冷却一起传送到冷凝器581,然后传送到分离器582,水从所述分离器返回到锅炉进料,并且烃相再循环到工艺流体。
[0120]
共蒸馏设备是具有同心螺旋输送机的水平管,所述同心螺旋输送机具有用于焦炭的入口和出口的滑阀,使得所述管可以被密封以用于蒸汽的周期性循环。使焦炭适合用作土壤改良剂或暴露于环境中的其它应用的焦炭净化的最后步骤避免了在流化床裂化器中作为标准炼油厂实践从催化剂燃烧的焦炭产生co2。
[0121]
本发明方法通过将反应器随着温度升高串联放置而将许多改进引入到cdp系统设计中:
[0122]
·
在低温下移除进料的水分和挥发性组分,从而节省了用于将所述进料的温度升高到单个热反应器的温度的能量。
[0123]
·
可以在各级之间添加新鲜催化剂。
[0124]
·
由于新的冷材料未被添加到单个热反应容器中,因此在每个级中,温度可以更加均匀。
[0125]
·
通过在工艺流体前进通过各级时传热流体与工艺流体的逆流而更有效地使用热源。废催化剂和工艺流体也与传入的工艺流体逆流。
[0126]
·
随后的蒸馏工艺的效率得到提高:从温度较低的级抽出的蒸气可以路由穿过单独的较小蒸馏塔或路由到单个塔,但是在塔上与较低级的蒸气排气温度相匹配的较高位置处路由到所述塔。
[0127]
·
与单个大反应容器相比,串联连接的多个反应容器,虽然不是真正的连续(即不间断)工艺,可以通过控制反应物在不同反应器内的停留时间而容易地达到连续工艺的效果。
[0128]
关于以上最后一点,单个混合反应容器本质上是分批过程,其中给予所期望的反应足够的时间,以在添加新装料之前充分进展至完成。然而,如果将反应物、催化剂和溶剂连续地添加到单个反应容器的内容物中,则为了平衡废催化剂、副产物碳和非反应性材料的累积,必须连续地移除反应器内容物中的一些反应器内容物。这种移除的不利后果是,成比例量的最近添加的原料和尚未反应的原料也将从工艺流中被移除。
[0129]
考虑到对于设计有相同安全压力裕度的罐,相同质量的罐材料将含有相同的内部体积,无论罐材料是在一个大直径的罐内加工还是在许多较小直径的罐内加工,将串联的若干个较小直径的罐与单个大直径罐进行比较是合理的。
[0130]
为了说明,假设反应容器连续地供应有反应物和催化剂,使得10%的未反应的进料和催化剂使该工艺发生“短路”,找到其不发生反应的出口路径。
[0131]
在串联的三个罐具有与单个罐相同的每单位体积混合功率并且因此具有相同的10%未反应分数的情况下,串联的三个反应器的输出的净未反应分数将是乘积(0.1)3=0.001或0.1%(即,三个连续存活事件的条件概率)。对于串联的较小罐,这个优点(0.1%未反应分数对10%)适用于混合控制反应速率的情况。当加热控制速率时,串联的较小罐比在(伪)连续工艺中使用的单个罐具有甚至更大的优点,因为较小的罐在每单位体积的工艺流体中具有更大的较薄壁接触面积。
[0132]
图10展示了具有太阳能聚光槽的实施例。在这种情况下,废气被引导通过
‘
回热式换热器’热交换器,以增加涡轮机的效率而不是加热化学工艺。
[0133]
本发明方法通过将反应器随着温度升高串联放置而将许多改进引入到cdp系统设计中:
[0134]
·
在低温下移除进料的水分和挥发性组分,从而节省了用于将所述进料的温度升高到单个热反应器的温度的能量。
[0135]
·
可以在各级之间添加新鲜催化剂。
[0136]
·
由于新的冷材料未被添加到单个热反应容器中,因此在每个级中,温度可以更加均匀。
[0137]
·
通过在工艺流体前进通过各级时传热流体与工艺流体的逆流而更有效地使用热源。废催化剂和工艺流体也与传入的工艺流体逆流。
[0138]
·
随后的蒸馏工艺的效率得到提高:从温度较低的级抽出的蒸气可以路由穿过单独的较小蒸馏塔或路由到单个塔,但是在塔上与较低级的蒸气排气温度相匹配的较高位置处路由到所述塔。
[0139]
·
串联连接的反应容器可以作为连续工艺操作,其中可以控制反应物的停留时间。
[0140]
·
(单个混合反应容器本质上是分批工艺。否则,如果将反应物、催化剂和溶剂连续地添加到单个反应容器的内容物中,则为了平衡废催化剂、副产物碳和非反应性材料的累积,必须连续地移除反应器内容物中的一些反应器内容物。这种移除的不利后果是,成比例量的最近添加的原料和尚未反应的原料也将从工艺流中被移除。)
[0141]
如对于本领域的技术人员而言将显而易见的是,可以对本文所述的各种元件和组件进行不同的组合,以实现提供用于再循环塑料和其它烃的有效且高效的系统和方法的预期目标。因此,在本文中提供并且在附图中示出的说明性实例并非旨在进行限制。