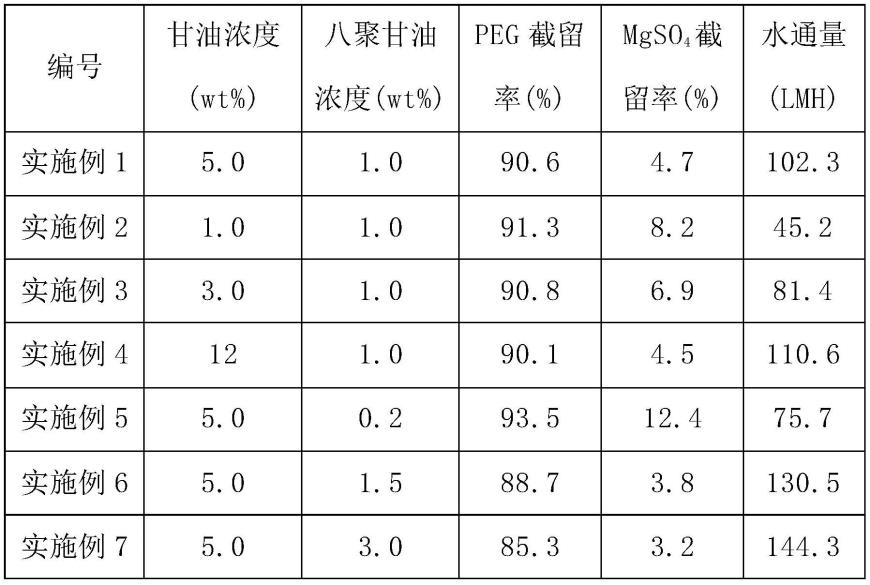
1.本发明涉及水处理膜技术领域,具体涉及一种高通量高选择性物料膜及其制备方法与应用。
背景技术:2.垃圾渗滤液是生活垃圾处理处置过程中产生的高浓度有机废水,具有污染物浓度高、硬度高、碱度高、水质及水量波动大等特点。目前,垃圾渗滤液的主流处理工艺为“预处理+生物处理+双膜法(nf+ro)”组合工艺。该工艺成熟、运行稳定、出水水质好,但生化出水经过纳滤浓缩分离后会产生大量的膜浓缩液。浓缩液中主要含有大分子腐殖酸和二价盐,属于高盐高有机物废液,处理难度高,如何有效处理纳滤浓缩液是目前生活垃圾渗滤液处置项目的重难点问题。
3.腐植酸是一种复杂的混合物,分为黄腐酸、棕腐酸和黑腐酸。腐植酸含有较多的功能团,具有很好的生物活性,可作为肥料、医药添加剂、吸附剂等。如果能将纳滤浓缩液中的腐植酸分离提取出来,剩余浓缩液返回生化系统,既可以避免纳滤浓缩液的外排,提高膜系统整体回收率,又能实现腐殖酸的资源化回用。
4.物料膜,截留分子量约800da(800
±
200da),对cod的去除率约65%(65
±
20%),对二价盐基本无截留能力。物料膜与垃圾渗滤液纳滤浓缩液的进料管连接,用于拦截浓缩液中的腐殖酸进行资源化回收利用,过物料膜后获得的淡相液重新返回生化系统循环处理,整个处理过程无浓缩液外排,从而实现了垃圾渗滤液纳滤浓缩液的零排放。
5.物料膜相比于传统纳滤膜对于小分子量的高截留率,更专注于对特定分子量物质的分离,在制备过程中通过控制相关参数使分离层在一定孔径范围内进行反应,以达到限定截留分子量的目的。现有物料膜的制备方法大多跟传统纳滤膜相似,通过界面聚合法、相转化法或共沉积法制备分离层,制得的物料膜虽然能在一定程度上将截留分子量控制在相应的范围内,但整体孔径的分布仍不够均匀,且会改变膜表面电荷,会出现对部分小于截留分子量的物质仍有较高截留率的现象。因此,急需一种简便高效的物料膜制备方法,在增强膜孔径均匀性的同时,不改变膜表面电荷,制得能够有效处理垃圾渗滤液纳滤浓缩液的高通量高选择性物料膜。
技术实现要素:6.本发明基于孔径筛分效应,提出了一种高通量高选择性物料膜的制备工艺,该工艺解决了现有技术制备物料膜时存在的诸多问题,具有十分重要的经济价值和研究意义。
7.本发明是通过如下技术方案实现的:
8.一种高通量高选择性物料膜的制备方法,其特征在于,该方法包括如下步骤:
9.(1)配制水相液:将高哌嗪、吸酸剂和水混合,配制成水相液;
10.(2)第一次浸渍处理:将基膜置于所述水相液中浸渍处理,然后分离并除去所述基膜表面的液体;
11.(3)配制油相液:将均苯三甲酰氯溶于有机溶剂,配制油相液;
12.(4)第二次浸渍处理:将经过第一次浸渍处理后的所述基膜再浸渍于所述油相液中进行界面聚合反应,然后分离并去除基膜表面液体,清洗后再置于碱液中浸泡,得到覆盖聚酰胺分离层的湿膜;
13.(5)配制保孔液:将甘油、聚甘油和水混合,配制成保孔液;
14.(6)第三次浸渍处理:将覆盖聚酰胺分离层的湿膜置于所述保孔液中浸渍处理,然后分离并去除膜表面液体;
15.(7)配制后处理溶液:将聚碳化二亚胺和水混合,配制成后处理溶液;
16.(8)干膜片制备:将所述后处理溶液均匀滴涂在经过第三次浸渍处理后的膜表面,然后分离并除去膜表面液体,干燥,得到高通量高选择性物料膜。
17.具体的,聚甘油是两个或多个甘油分子间的羟基经脱水后生成醚键的多元醇,是重要的精细化工产品及合成中间体,有着广泛的用途,但目前还没有将聚甘油用于物料膜制备中的报道。而本发明在该高通量高选择性物料膜制备过程中,通过对界面聚合反应形成的聚酰胺分离层使用氢氧化钠(碱液)浸泡处理,在清洗残油的同时,可以打断部分聚酰胺网状交联结构、有效扩大交联孔径大小。同时本发明工艺在后段工序中将分子量较大的聚甘油引入到干膜片制备中,聚甘油分子通过占位作用有效防止烘干过程中聚酰胺交联孔的塌陷,同时利用聚碳化二亚胺交联剂修复部分断裂的高分子链,在保证物料膜对二价盐高透过率的同时不会降低对peg800的截留性能。
18.具体的,本发明所述的高通量高选择性物料膜的制备方法:将聚甘油物质作为保孔剂引入到物料膜干膜片制备过程中;本发明的制备方法简单、成本低廉,与传统界面聚合生产工艺具有良好的兼容性,易于生产放大。在聚甘油和聚碳化二亚胺交联剂的协同作用下,制备的物料膜截留分子量约800da左右,对二价盐截留率小于5%,体现出优异的有机物/二价盐选择性。本发明制备的高通量高选择性物料膜在极低压力下(0.2mpa),其水通量大于100lmh。
19.进一步的,一种高通量高选择性物料膜的制备方法:步骤(1)配制水相液:所述水相液中高哌嗪的浓度为0.1-2.0wt%、吸酸剂的浓度为0.5-3.0wt%;且所述的吸酸剂选自碳酸钠、磷酸三钠、三乙胺、氢氧化钠中的一种或几种。优选的,所述水相液中高哌嗪的浓度为0.2-1.0wt%、吸酸剂的浓度为1.0-2.5wt%;优选的吸酸剂为磷酸三钠。
20.进一步的,一种高通量高选择性物料膜的制备方法:步骤(2)第一次浸渍处理:其中所述的基膜为聚砜基膜;所述浸渍处理的时间为0.5-5分钟。
21.进一步的,一种高通量高选择性物料膜的制备方法:步骤(3)配制油相液:其中所述的有机溶剂选自正己烷、环己烷、乙基环己烷、正庚烷、异构烷烃溶剂中至少一种;所述油相液中所述均苯三甲酰氯的浓度为0.05-0.5wt%。
22.进一步的,一种高通量高选择性物料膜的制备方法:步骤(4)第二次浸渍处理:将经过第一次浸渍处理后的所述基膜再浸渍于所述油相液中进行界面聚合反应5-20秒,然后分离并去除膜表面液体,清洗后再置于浓度0.1-4.0wt%的氢氧化钠水溶液中浸泡0.5-5分钟,得到覆盖聚酰胺分离层的湿膜。
23.进一步的,一种高通量高选择性物料膜的制备方法:步骤(5)配制保孔液:所述保孔液中甘油的浓度为1.0-15.0wt%、聚甘油的浓度为0.2-3.0wt%;所述的聚甘油为n聚甘
油,其中n=6~10,优选为八聚甘油。优选的,所述保孔液中甘油的浓度为3.0-8.0wt%、聚甘油的浓度为0.5-1.5wt%。
24.进一步的,一种高通量高选择性物料膜的制备方法:步骤(6)第三次浸渍处理:将覆盖聚酰胺分离层的湿膜置于所述保孔液中浸渍处理0.5-5分钟,然后分离并去除膜表面液体。
25.进一步的,所述高通量高选择性物料膜的制备方法:步骤(7)配制后处理溶液:所述后处理溶液中所述聚碳化二亚胺的浓度为0.05-1.0wt%。
26.进一步的,所述高通量高选择性物料膜的制备方法:步骤(8)干膜片制备:所述干燥温度为30-90℃,干燥时间为2-10分钟。
27.一种所述高通量高选择性物料膜,其特征在于,采用上述的制备方法制得。
28.一种高通量高选择性物料膜的应用,其特征在于,将上述的制备方法制得的高通量高选择性物料膜用于需要对有机物和无机盐选择分离的废水处理领域或物料分离领域,优选用于垃圾渗滤液纳滤浓缩液处理领域。
29.本发明的有益效果:
30.(1)本发明的制备工艺简单,且制备的高通量高选择性物料膜截留分子量约800da左右,对二价盐硫酸镁的截留率小于5%,可以实现对有机物与二价盐的精确分离。
31.(2)本发明制备过程中引入的聚甘油对聚酰胺层交联结构具有溶胀作用,在碱液浸泡和聚甘油的作用下可均匀扩大交联网状结构中的孔径大小,有效提高水的透过效率,制备的高通量高选择性物料膜在极低压力下(0.2mpa),水通量大于100lmh。
32.(3)本发明提供的高通量高选择性物料膜的制备方法简单、成本低廉,与传统界面聚合生产工艺具有良好的兼容性,易于生产放大,具有十分重要的经济效益。
33.(4)本发明所提供的高通量高选择性物料膜的制备方法:在传统界面聚合操作的基础上使用碱液(氢氧化钠溶液)浸泡破坏部分聚酰胺网状交联结构,并在干膜片制备中引入聚甘油,利用聚甘油的占位作用扩大聚酰胺层孔径大小,最后再使用聚碳化二亚胺交联剂修复部分断裂的高分子链,从而使得制备的物料膜截留分子量约800da左右,对二价盐硫酸镁的截留率小于5%,在极低压力下仍能保持较高的水通量,使其对有机物和无机盐选择分离的废水处理领域或物料分离领域以及在垃圾渗滤液纳滤浓缩液处理领域具有很好的应用前景和经济价值。
具体实施方式
34.下面将结合具体实施例,对本发明的技术方案进行清楚、完整地描述,显然,所描述的实施例仅仅是本发明的一部分实施例,而不是全部的实施例。以下对至少一个示例性实施例的描述实际上仅仅是说明性的,决不作为对本发明及其应用或使用的任何限制。基于本发明中的实施例,本领域普通技术人员在没有做出创造性劳动前提下所获得的所有其他实施例,都属于本发明保护的范围。
35.一种高通量高选择性物料膜的制备方法,包括如下步骤:
36.(1)配制水相液:将高哌嗪、吸酸剂和水混合,配制成水相液;该水相液中高哌嗪的浓度为0.1-2.0wt%(优选浓度为0.2-1.0wt%)、吸酸剂的浓度为0.5-3.0wt%(优选浓度为1.0-2.5wt%);吸酸剂选自碳酸钠、磷酸三钠、三乙胺和氢氧化钠中的一种或几种,优选的
吸酸剂采用磷酸三钠;
37.(2)第一次浸渍处理:将基膜(聚砜基膜)置于所述水相液中浸渍处理0.5-5分钟,然后分离并除去所述基膜表面液体;
38.(3)配制油相液:将均苯三甲酰氯溶于有机溶剂中,配制成油相液;该油相液中均苯三甲酰氯的浓度为0.05-0.5wt%;其中有机溶剂可以选自正己烷、环己烷、乙基环己烷、正庚烷、异构烷烃溶剂中一种或几种;
39.(4)第二次浸渍处理:将经过第一次浸渍处理后的所述基膜再浸渍于所述油相液中进行界面聚合反应5-20秒,然后分离并去除基膜表面的液体,清洗后再置于浓度0.1-4.0wt%的氢氧化钠水溶液中浸泡0.5-5分钟,即得到覆盖聚酰胺分离层的湿膜;
40.(5)配制保孔液:将甘油、聚甘油和水混合,配制成保孔液;该保孔液中甘油的浓度为1.0-15.0wt%(优选浓度为3.0-8.0wt%)、聚甘油的浓度为0.2-3.0wt%(优选浓度为0.5-1.5wt%);其中聚甘油为n聚甘油,n=6~10,n为正整数,聚甘油可以优选为八聚甘油;
41.(6)第三次浸渍处理:将覆盖聚酰胺分离层的湿膜置于所述保孔液中浸渍处理0.5-5分钟,然后分离并去除膜表面液体;
42.(7)配制后处理溶液:将聚碳化二亚胺和水混合,配制成后处理溶液;后处理溶液中聚碳化二亚胺的浓度为0.05-1.0wt%;
43.(8)干膜片制备:将后处理溶液均匀滴涂在经过第三次浸渍处理后的膜表面,然后分离并除去膜表面液体,并在30-90℃下干燥2-10分钟,获得高通量高选择性物料膜。
44.实施例1
45.一种高通量高选择性物料膜的制备方法,包括如下具体步骤:
46.(1)配制水相液:将高哌嗪(hpip)、磷酸三钠(吸酸剂)和水混合,配制成水相液;且所述水相液中高哌嗪的浓度为0.6wt%,磷酸三钠的浓度为2.0wt%;
47.(2)第一次浸渍处理:将聚砜基膜置于上述水相液中浸渍处理1分钟,然后分离并除去聚砜基膜表面液体;
48.(3)配制油相液:将均苯三甲酰氯(tmc)溶于乙基环己烷中,配制成油相液;且油相液中均苯三甲酰氯的浓度为0.15wt%;
49.(4)第二次浸渍处理:将经过第一次浸渍处理后的聚砜基膜再浸渍于上述油相液中进行界面聚合反应10秒,然后分离并去除膜表面液体,清洗后置于1.0wt%氢氧化钠水溶液中浸泡1分钟,得到覆盖聚酰胺分离层的湿膜;
50.(5)配制保孔液:将甘油、八聚甘油和水混合,配制成保孔液;所述保孔液中甘油的浓度为5.0wt%、八聚甘油的浓度为1.0wt%;
51.(6)第三次浸渍处理:将上述覆盖聚酰胺分离层的湿膜置于所述保孔液中浸渍处理1分钟,然后分离并去除膜表面液体;
52.(7)配制后处理溶液:将聚碳化二亚胺和水混合,配制成后处理溶液;且后处理溶液中聚碳化二亚胺的浓度为0.2wt%;
53.(8)干膜片制备:将后处理溶液均匀滴涂在经过第三次浸渍处理后的膜表面,然后分离并除去膜表面液体,并在60℃烘箱中干燥5分钟,得到高通量高选择性物料膜。
54.实施例2
55.实施例2与上述实施例1的区别在于,实施例2步骤(5)所述的保孔液中甘油的浓度
为1.0wt%;实施例2的其余制备条件均与实施例1相同。
56.实施例3
57.实施例3与上述实施例1的区别在于,实施例3步骤(5)所述的保孔液中甘油的浓度为3.0wt%;实施例3的其余制备条件均与实施例1相同。
58.实施例4
59.实施例4与上述实施例1的区别在于,实施例4步骤(5)所述的保孔液中甘油的浓度为12.0wt%;实施例4的其余制备条件均与实施例1相同。
60.实施例5
61.实施例5与上述实施例1的区别在于,实施例5步骤(5)所述的保孔液中八聚甘油的浓度为0.2wt%;实施例5的其余制备条件均与实施例1相同。
62.实施例6
63.实施例6与上述实施例1的区别在于,实施例6步骤(5)所述的保孔液中八聚甘油的浓度为1.5wt%;实施例6的其余制备条件均与实施例1相同。
64.实施例7
65.实施例7与上述实施例1的区别在于,实施例7步骤(5)所述的保孔液中八聚甘油的浓度为3.0wt%;实施例7的其余制备条件均与实施例1相同。
66.实施例8
67.实施例8与上述实施例1的区别在于,实施例8步骤(4)所述的界面聚合反应时间为20秒;实施例8的其余制备条件均与实施例1相同。
68.实施例9
69.实施例9与上述实施例1的区别在于,实施例9步骤(7)所述的后处理溶液中聚碳化二亚胺的浓度为0.05wt%;实施例9的其余制备条件均与实施例1相同。
70.实施例10
71.实施例10与上述实施例1的区别在于,实施例10步骤(7)所述的后处理溶液中聚碳化二亚胺的浓度为1.0wt%;实施例10的其余制备条件均与实施例1相同。
72.实施例11
73.实施例11与上述实施例1的区别在于,实施例11步骤(5)中所述的保孔液由甘油、六聚甘油和水混合配制而成;即将实施例1中的八聚甘油替换为六聚甘油;实施例11保孔液中甘油的浓度为5.0wt%、六聚甘油的浓度为1.0wt%;实施例11的其余制备条件均与实施例1相同。
74.实施例12
75.实施例12与上述实施例1的区别在于,实施例12步骤(5)中所述的保孔液由甘油、十聚甘油和水混合配制而成;即将实施例1中的八聚甘油替换为十聚甘油;实施例12保孔液中甘油的浓度为5.0wt%、十聚甘油的浓度为1.0wt%;实施例12的其余制备条件均与实施例1相同。
76.对比例1
77.对比例1与上述实施例1的区别在于,对比例1步骤(5)所述的保孔液中不添加八聚甘油;对比例1的其余制备条件均与实施例1相同。
78.对比例2
79.对比例2与上述实施例2的区别在于,对比例2步骤(5)所述的保孔液中不添加八聚甘油;对比例2的其余制备条件均与实施例2相同。
80.对比例3
81.对比例3与上述实施例3的区别在于,对比例3步骤(5)所述的保孔液中不添加八聚甘油;对比例3的其余制备条件均与实施例3相同。
82.对比例4
83.对比例4与上述实施例4的区别在于,对比例4步骤(5)所述的保孔液中不添加八聚甘油;对比例4的其余制备条件均与实施例4相同。
84.对比例5
85.对比例5与上述实施例1的区别在于,对比例5步骤(4)所述的界面聚合反应时间为40秒;对比例5的其余制备条件与实施例1相同。
86.对比例6
87.对比例6与上述实施例1的区别在于,对比例6步骤(4)所述的界面聚合反应后不经过氢氧化钠水溶液浸泡处理;对比例6的其余制备条件均与实施例1相同。
88.对比例7
89.对比例7与上述实施例1的区别在于,对比例7步骤(7)所述的后处理溶液中聚碳化二亚胺的浓度为0;对比例7的其余制备条件与实施例1相同。
90.测试:
91.测试上述实施例1-12以及对比例1-7所得物料膜的性能:对上述制备的物料膜分离性能进行评价,主要通过两个特征参数来表征,即膜的水通量(lmh)和溶质截留率。
92.水通量(lmh)定义为:在一定操作压力条件下,单位时间内透过有效膜面积的水的体积。
93.溶质截留率计算公式:r=(1
–cp
/cf)
×
100%,式中r代表截留率,cf和c
p
分别为透过液和进料液中溶质的浓度(ppm)。
94.物料膜分离性能的测试条件为:进料液分别为2000ppm的硫酸镁水溶液和200ppm的分子量为800da的聚乙二醇(peg)水溶液,料液温度为25℃,操作压力为0.2mpa。
95.peg浓度通过总有机碳分析仪(toc-vchp,shimadzu,japan)进行测定。一般认为,当膜对peg截留达到90%时对应的相对分子量就是膜的截留分子量。
96.采用以上方法对上述实施例1-7以及对比例1-4制备的物料膜进行性能测试,测试结果参见下表1。
97.表1为实施例1-7及对比例1-4制备的物料膜分离性能测试结果
[0098][0099][0100]
从表1的测试结果可以看出,保孔液中八聚甘油的添加能够明显降低物料膜对二价盐硫酸镁的截留率,同时对peg截留保持在90%左右,截留分子量精准控制在800da左右;同时,八聚甘油相比于甘油来说保孔能力更强,对聚酰胺层交联结构具有溶胀作用,添加较低浓度的三聚甘油就可以提高膜的水通量。
[0101]
采用以上方法对上述实施例8-12以及对比例5-7制备的物料膜进行性能测试,测试结果参见下表2。
[0102]
表2为实施例8-12及对比例5-7制备的物料膜分离性能测试结果
[0103][0104]
从表2的测试结果可以看出,不同分子量的聚甘油对制备的物料膜性能影响存在差异,相比如八聚甘油,分子量更大的十聚甘油对聚酰胺交联层的溶胀作用更强,制得的物料膜虽然水通量更大,但对peg截留有所降低,而利用分子量较小的六聚甘油制得的物料膜孔径有所变小,对peg和硫酸镁的截留明显上升。此外,物质膜制备过程中的界面聚合反应时间不易过长,否则形成的聚酰胺层较为致密,无法有效降低对硫酸镁的截留率。
[0105]
上述实施例1-14及对比例1-5中所用原料的来源,参见下表3。
[0106]
原料名称参数指标生产厂家高哌嗪纯度≥98%阿拉丁试剂磷酸三钠纯度≥98%西陇试剂均苯三甲酰氯纯度≥99%三力本诺氢氧化钠纯度≥97%麦克林甘油纯度≥99%康迪斯聚甘油纯度≥99%康迪斯聚碳化二亚胺un-557工业级上海尤恩硫酸镁纯度≥98%北京伊诺凯聚乙二醇800纯度≥99%北京伊诺凯
[0107]
上述为本发明的较佳实施例仅用于解释本发明,并不用于限定本发明。凡由本发明的技术方案所引伸出的显而易见的变化或变动仍处于本发明的保护范围之中。