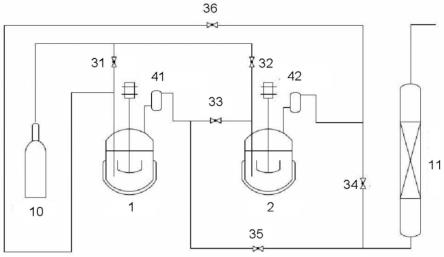
1.本发明涉及一种用于气液相反应的反应系统,该反应系统能确保气液相反应连续进行,无需由于装填反应原料、反应催化剂等因素而使整个反应系统停车,极大地提高了生产效率。本发明还涉及所述反应系统在二氯吡啶氯化制备更多氯吡啶中的用途。
背景技术:2.气液相反应是一种非常常见的化学反应。以常见的多氯吡啶合成为例,其合成技术以氯气为氯源,使含1-3个氯原子的氯代吡啶在氯化铁、溴化铁等路易斯酸催化剂的作用下进行反应。例如,陈熙等的“2,3,6-三氯吡啶的合成”(《精细石油化工》,第三期,2000年5月)公开了以2,6-二氯吡啶为原料通过亲电取代反应 (使用路易斯酸催化剂)合成2,3,6-三氯吡啶。所述亲电取代反应在在一个单独的反应容器中在180-220℃下进行,反应产率为93%。
3.中国专利cn1944408a提出了一种生产2,3,5,6-四氯吡啶的方法,它以含1-3个氯原子的氯代吡啶和氯气为原料,采用三级串联反应釜进行反应。具体地说,其氯化反应在串联的三级反应器中进行:首次反应时,往串联的三只反应器中投入相同的氯代吡啶和催化剂后加热,当一级反应器中的物料达到反应终点时,放出一级反应器中的产物,然后将二级反应器中的物料放入一级反应器,三级反应器中的物料放入二级反应器,再向空的三级反应器中投入相同的氯代吡啶和催化剂。反应过程中,氯气从一级氯化器通入,经一级氯化器内的氯代吡啶吸收反应后,出来的尾气进入二级氯化器,其中未反应的氯气与二级氯化器内的氯代吡啶进行氯化反应,从二级氯化器出来的尾气进入三级氯化器,其中未反应的氯气与三级氯化器内的氯代吡啶进行氯化反应,从三级氯化器出来的尾气经缓冲罐被送入吸收塔,用水吸收制成盐酸。尽管该方法能有效地提高氯气的利用率,但是每当一级反应釜达到反应终点后必须进行停车并转移反应物料的操作,不利于连续生产,该缺点随反应釜串联个数增加时越发明显。
4.因此,本领域仍需要开发用于气液相反应的反应系统,这种反应系统不仅能提高气体的利用效率,而且整个系统可连续运行,无需由于装填反应原料、反应催化剂等因素而使整个反应系统停车,极大地提高了生产效率。
技术实现要素:5.本发明的一个发明目的是提供一种用于气液相反应的反应系统,这种反应系统不仅能提高气体的利用效率,而且整个系统可连续运行,无需由于装填反应原料、反应催化剂等因素而使整个反应系统停车,极大地提高了生产效率。
6.本发明的另一个发明目的是提供一种气液相反应方法,这种方法不仅能提高气体的利用效率,而且整个反应系统可连续运行,无需由于装填反应原料、反应催化剂等因素而使整个反应系统停车,极大地提高了生产效率。
7.因此,本发明的一个方面涉及一种用于气液相反应的反应系统,包括多个串联的
反应釜和气体吸收塔,每个反应釜带有气体入口和气体出口;
8.每个反应釜的气体入口均通过阀门与气源流体相连,每个反应釜的气体出口均通过阀门与气体吸收塔相连;
9.第一个反应釜的气体入口还通过阀门与最后一个反应釜的气体出口流体相连;其余反应釜的气体入口还与前一级反应釜的气体出口通过阀门流体相连。
10.本发明的另一方面涉及一种气液相反应方法,它包括如下步骤:
11.提供本发明用于气液相反应的反应系统;
12.在各反应釜中装填液相原料和任选的催化剂;
13.调节各阀门使得反应系统中气流以这样的方式流动,即气流从上一级反应釜气体入口流入,反应后的尾气从该级反应釜的气体出口流至下一级反应釜的气体入口,最后一级反应釜的气体从该级反应釜的气体出口流至气体吸收塔;
14.当某一级反应釜反应完成需要更换液相原料时,通过控制阀门将其从串联系统中割裂,重新装填后再连接回所述反应系统。
15.本发明再一方面涉及本发明所述气液相反应系统在制备多氯吡啶中的用途。
附图说明
16.下面结合附图进一步说明本发明,附图中:
17.图1是本发明一个较好实施方式中两个反应釜串联系统的示意图;
18.图2是本发明一个较好实施方式中三个反应釜串联系统的示意图。
具体实施方式
19.在本发明中,术语“流体相连”是指两个装置通过阀门相连接,当阀门开启时,两个装置之间的流体可自由地流动。
20.本发明用于气液相反应的反应系统包括多个串联的反应釜,例如2-5个,较好2-4个或者2-3个串联的反应釜,上一级和下一级反应釜之间通过管道和阀门流体相连。
21.本发明反应系统中每个反应釜均带有气体入口和气体出口。在一个较好的实例中,有一个或多个,较好每个反应釜带有搅拌装置。
22.本发明反应系统中每个反应釜的气体入口均通过阀门与气源流体相连。在本发明用于氯化反应的一个实例中,所述气源是氯气源,例如氯气钢瓶。
23.本发明反应系统中每个反应釜的气体出口均通过阀门与气体吸收塔相连。
24.本发明反应系统中第一个反应釜的气体入口还通过阀门与最后一个反应釜的气体出口流体相连;其余反应釜的气体入口还与前一级反应釜的气体出口通过阀门流体相连。
25.在本发明的一个实例中,一个或多个反应釜,较好每个反应釜的气体出口带有一个气体冷凝器,所述反应釜通过该气体冷凝器与其它装置流体相连。
26.在本发明的一个实例中,所述反应系统还包括一个气体吸收塔,它与每个反应釜的气体出口流体相连,用于在需要时吸收反应釜排出的尾气。
27.图1是本发明一个较好实例的反应系统的示意图。如图1所示,本发明反应系统包括反应釜1和反应釜2、气源10和气体吸收塔11。反应釜1和反应釜2各自带有气体入口,所述
气体入口各自通过阀门31和32与气源10流体相连。反应釜1的气体出口通过任选的气体冷凝器41和阀门33与反应釜2的气体入口流体相连。反应釜2 的气体出口通过任选的气体冷凝器42和阀门34和35与反应釜1任选的冷凝器41的出口端流体相连,反应釜2的气体出口通过任选的气体冷凝器42和阀门36与反应釜 1的气体入口端流体相连。气体吸收塔11与阀门34和35之间的管道流体相连。
28.使用时,所述反应系统视情况可以有以下运行方式(以下称图1工况):
29.工况1:反应釜1与反应釜2串联反应
30.开启阀门31、33、34,关闭阀门32、36、35,氯气先进入反应釜1进行反应,部分没反应的氯气和生成的hcl进入反应釜2继续消耗掉没反应的氯气,生成的 hcl和余下的氯气进入气体吸收塔后11处理。
31.工况2:反应釜2单独反应
32.当反应釜1反应结束需要更新液体原料和/或催化剂时,开启阀门32、34,关闭阀门31、33、36、35,此时氯气仅通过反应釜2后进入气体吸收塔,可以对反应釜1进行卸料并再装填操作。
33.工况3:反应釜2与反应釜1串联反应
34.当反应釜1再装填完毕后,开启阀门32、36、35,关闭阀门31、33、34,此时氯气依次通过反应釜2和反应釜1,生成的hcl和未反应的氯气再进入气体吸收塔后处理。
35.工况4:反应釜1单独反应
36.当反应釜2反应结束后,开启阀门31、35,关闭阀门33、34、32、36,此时氯气仅通过反应釜1后进入气体吸收塔,对反应釜2进行卸料并再装填操作。
37.当反应釜2再装填完毕后,重新进入工况1。
38.若追求更高的氯气利用率,工况2和工况4可停止通入氯气,待物料再装填结束后直接进入下一工况。
39.本发明反应系统带有串联的反应釜,如果以与气源最近的反应釜为第一级反应釜的话,则其串联的次序可以按需改变,确保原料利用率最大化。例如,当反应接近尾声时,反应釜中液体原料的浓度明显下降,此时增加气体原料的量可有助于反应更快更彻底地完成。本发明通过改变串联次序,可以使液体原料浓度下降的反应釜作为第一级反应釜,使之与高浓度原料气结合,有助于反应更快更彻底地完成,提高反应效率和原料的利用率,取得改进的经济效益。
40.图2是本发明另一个较好实例的反应系统的示意图。如图2所示,本发明反应系统包括反应釜1、反应釜2和反应釜3、气源10和气体吸收塔11。反应釜1、反应釜2和反应釜3各自带有气体入口,所述气体入口各自通过阀门31、32和51与气源 10流体相连。反应釜1的气体出口通过任选的气体冷凝器41和阀门33与反应釜2的气体入口流体相连,反应釜2的气体出口通过任选的气体冷凝器42和阀门52与反应釜3的气体入口流体相连。反应釜3的气体出口通过任选的气体冷凝器43和阀门34 和35与反应釜1任选的气体冷凝器41的出口端流体相连,反应釜3的气体出口通过任选的气体冷凝器43和阀门34和53与反应釜2任选的气体冷凝器42的出口端流体相连,反应釜3的气体出口通过任选的气体冷凝器43和阀门36与反应釜1的气体入口端流体相连。气体吸收塔11与阀门34和35之间的管道流体相连。
41.使用时,所述反应系统视情况可以有以下运行方式(以下称图2工况):
42.工况1:反应釜1、反应釜2、反应釜3串联反应
43.保持阀门31、33、52、34开启,其余阀门关闭,氯气先进入反应釜1进行反应,部分没反应的氯气和生成的hcl依次进入反应釜2和反应釜3继续消耗掉没反应的氯气,生成的hcl和余下的氯气进入气体吸收塔后处理。
44.工况2:反应釜2、反应釜3串联反应
45.当反应釜1反应结束后,保持阀门32、52、34开启,其余阀门关闭,此时氯气先进入反应釜2进行反应,部分没反应的氯气和生成的hcl进入反应釜3继续消耗掉没反应的氯气,生成的hcl和余下的氯气进入气体吸收塔后处理,对反应釜1 进行卸料并再装填操作。
46.工况3:反应釜2、反应釜3、反应釜1串联反应
47.当反应釜1再装填完毕后,保持阀门32、52、36、35开启,其余阀门关闭,此时氯气先进入反应釜2进行反应,部分没反应的氯气和生成的hcl进入反应釜3和反应釜1继续消耗掉没反应的氯气,生成的hcl和余下的氯气进入气体吸收塔后处理。
48.工况4:反应釜3、反应釜1串联反应
49.当反应釜2反应结束后,保持阀门51、36、35开启,其余阀门关闭,此时氯气先进入反应釜3进行反应,部分没反应的氯气和生成的hcl进入反应釜1继续消耗掉没反应的氯气,生成的hcl和余下的氯气进入气体吸收塔后处理,对反应釜2 进行卸料并再装填操作。
50.工况5:反应釜3、反应釜1、反应釜2串联反应
51.当反应釜2再装填完毕后,保持阀门51、36、33、53开启,其余阀门关闭,此时氯气先进入反应釜3进行反应,部分没反应的氯气和生成的hcl进入反应釜1和反应釜2继续消耗掉没反应的氯气,生成的hcl和余下的氯气进入气体吸收塔后处理。
52.工况6:反应釜1、反应釜2串联反应
53.当反应釜3反应结束后,保持阀门31、33、53开启,其余阀门关闭,此时氯气先进入反应釜1进行反应,部分没反应的氯气和生成的hcl进入反应釜2继续消耗掉没反应的氯气,生成的hcl和余下的氯气进入气体吸收塔后处理,对反应釜3 进行卸料并再装填操作。
54.当反应釜3再装填完毕后,重新进入工况1。
55.若追求更高的氯气利用率,工况2、工况4和工况6可停止通入氯气不进行反应,待物料再装填结束后直接进入下一工况。
56.本发明还涉及一种气液相反应方法。本发明方法包括如下步骤:
57.提供本发明上述用于气液相反应的反应系统;
58.在各反应釜中装填液相原料和任选的催化剂;
59.调节各阀门使得反应系统中气流以这样的方式流动,即气流从上一级反应釜气体入口流入,反应后的尾气从该级反应釜的气体出口流至下一级反应釜的气体入口,最后一级反应釜的气体从该级反应釜的气体出口流至气体吸收塔;
60.当某一级反应釜反应完成需要更换液相原料时,通过控制阀门将其从串联系统中割裂,重新装填后(较好作为最后一级反应釜)再连接回所述反应系统。
61.在本发明的一个较好实例中,所述气液相反应系统用于制备多氯吡啶,例如2,3,6-三氯吡啶。因此,所述气体是氯气,所述液相选自氯代吡啶如2,6-二氯吡啶,所述催化剂选自氯化铁、溴化铁等路易斯酸催化剂,优选氯化铁。
62.所述气液相反应系统用于制备多氯吡啶时的反应釜反应条件是本领域已知的,例
如催化剂用量一般为氯代吡啶质量的1-6%,反应温度180-230℃,压力 0-0.08mpa。
63.本发明还涉及本发明所述气液相反应系统在制备多氯吡啶中的用途。
64.实施例
65.以下结合具体实例帮助进一步理解本发明,但本发明的保护范围并不限于此。
66.实施例1
67.用2,6-二氯吡啶制备2,3,6-三氯吡啶
68.采用图1所示的两釜首尾串联工艺。向反应釜1和反应釜2中均投入1200g 2,6-二氯吡啶和36g氯化铁。氮气保护下将物料温度升到190℃,然后通入氯气并按图1工况1开始操作。6h后反应釜1结束反应。按图1的工况2继续反应,对反应釜1进行卸料和再装填操作,持续时间30min。当反应釜1装填好后进入工况3,4h后反应釜2结束反应。按图1的工况4继续反应,对反应釜2进行卸料和再装填操作,持续时间30min。各工况结束时反应的情况和氯气利用率见下表。
69.表1.各工况下反映情况与氯气利用率
[0070] 工况1工况2工况3工况4反应釜1转化率%82.39\30.5237.03反应釜1选择性%96.42\98.8198.79反应釜2转化率%36.0442.3384.73\反应釜2选择性%98.9698.7198.55\氯气利用率%83.0453.6482.7953.81
[0071]
实施例2
[0072]
用2,6-二氯吡啶制备2,3,5,6-四氯吡啶
[0073]
采用两釜首尾串联工艺。向反应釜1和反应釜2中均投入1200g 2,6-二氯吡啶和48g氯化铁。氮气保护下将物料温度升到200℃,然后通入氯气并按工况 1开始操作。12h后反应釜1结束反应。按图1工况2继续反应,对反应釜1进行卸料和再装填操作,持续时间30min。当反应釜1装填好后进入图1工况3,6h 后反应釜2结束反应。按图1工况4继续反应,对反应釜2进行卸料和再装填操作,持续时间30min。各工况结束时反应的情况和氯气利用率见下表。
[0074]
表2各工况下反映情况与氯气利用率
[0075] 工况1工况2工况3工况4反应釜1转化率%94.77\23.4227.13反应釜1选择性%96.41\97.6797.51反应釜2转化率%41.4344.1593.29\反应釜2选择性%97.2897.7297.81\氯气利用率%85.3556.3085.0256.17
[0076]
实施例3
[0077]
用2,3,6-二氯吡啶制备2,3,5,6-四氯吡啶
[0078]
采用图1两釜首尾串联工艺。向反应釜1、反应釜2中均投入1200g 2,3,6
‑ꢀ
三氯吡啶和39g氯化铁。氮气保护下将物料温度升到205℃,然后通入氯气并按图1工况1开始操作。6h后反应釜1结束反应。按图1工况2继续反应,对反应釜1进行卸料和再装填操作,持续时间
30min。当反应釜1装填好后进入图1工况3,3h后反应釜2结束反应。按图1工况4继续反应,对反应釜2进行卸料和再装填操作,持续时间30min。各工况结束时反应的情况和氯气利用率见下表。
[0079]
表3.各工况下反映情况与氯气利用率
[0080] 工况1工况2工况3工况4反应釜1转化率%93.51\20.4227.13反应釜1选择性%97.28\97.6797.51反应釜2转化率%39.9445.7293.29\反应釜2选择性%97.8897.9297.81\氯气利用率%84.1755.8384.7454.99
[0081]
实施例4
[0082]
用2,6-二氯吡啶制备2,3,6-三氯吡啶
[0083]
采用图2三釜首尾串联工艺。向反应釜1、反应釜2和反应釜3中均投入1200 g 2,6-二氯吡啶和36g氯化铁。氮气保护下将物料温度升到190℃,然后通入氯气并按图2工况1开始操作。6h后反应釜1结束反应。按图2工况2继续反应,对反应釜1进行卸料和再装填操作,持续时间30min。当反应釜1装填好后进入图2工况3,4h后反应釜2结束反应。按图2工况4继续反应,对反应釜2进行卸料和再装填操作,持续时间30min。按图2工况5继续反应,3h后各工况结束。按图2工况6继续反应,对反应釜3进行卸料和再装填操作,持续时间30min。各工况结束时反应的情况和氯气利用率见下表。
[0084]
表4.各工况下反映情况与氯气利用率
[0085][0086][0087]
实施例5
[0088]
用2,6-二氯吡啶制备2,3,5,6-四氯吡啶
[0089]
采用图2三釜首尾串联工艺。向反应釜1、反应釜2和反应釜3中均投入1200 g 2,6-二氯吡啶和48g氯化铁。氮气保护下将物料温度升到200℃,然后通入氯气并按图2工况1开始操作。12h后反应釜1结束反应。按图2工况2继续反应,对反应釜1进行卸料和再装填操作,持续时间30min。当反应釜1装填好后进入图2工况3,4h后反应釜2结束反应。按图2工况4继续反应,对反应釜2 进行卸料和再装填操作,持续时间30min。按图2工况5继续反应,6h后各工况结束。按图2工况6继续反应,对反应釜3进行卸料和再装填操作,持续时间 30min。各工
况结束时反应的情况和氯气利用率见下表。
[0090]
表5.各工况下反映情况与氯气利用率
[0091] 工况1工况2工况3工况4工况5工况6反应釜1转化率%94.18\5.988.9139.9643.73反应釜1选择性%97.62\98.6998.4298.3197.19反应釜2转化率%56.7560.8695.53\7.9111.83反应釜2选择性%98.7098.4498.20\98.4498.04反应釜3转化率%17.0419.7641.3745.9095.14/反应釜3选择性%98.9298.3198.0397.9197.68/氯气利用率%94.9684.1994.0383.5193.8783.54
[0092]
实施例6
[0093]
用2,3,6-三氯吡啶制备2,3,5,6-四氯吡啶
[0094]
采用图2三釜首尾串联工艺。向反应釜1、反应釜2和反应釜3中均投入1200 g 2,3,6-三氯吡啶和39g氯化铁。氮气保护下将物料温度升到205℃,然后通入氯气并按图2工况1开始操作。6h后反应釜1结束反应。按图2工况2继续反应,对反应釜1进行卸料和再装填操作,持续时间30min。当反应釜1装填好后进入图2工况3,3h后反应釜2结束反应。按图2工况4继续反应,对反应釜2进行卸料和再装填操作,持续时间30min。按图2工况5继续反应,3h后各工况结束。按图2工况6继续反应,对反应釜3进行卸料和再装填操作,持续时间30min。各工况结束时反应的情况和氯气利用率见下表。
[0095]
表6.各工况下反映情况与氯气利用率
[0096] 工况1工况2工况3工况4工况5工况6反应釜1转化率%92.31\7.8211.0214.5222.26反应釜1选择性%97.77\98.4398.0797.6897.82反应釜2转化率%37.2645.0191.07\7.7810.94反应釜2选择性%98.5898.3997.89\97.8397.33反应釜3转化率%14.8117.9536.7244.1990.71/反应釜3选择性%98.0297.8497.9197.4297.66/氯气利用率%93.2482.7793.9282.1994.1181.94
[0097]
比较例1
[0098]
用2,6-二氯吡啶制备2,3,6-三氯吡啶
[0099]
采用单釜反应。向反应釜中投入1200g2,6-二氯吡啶和36g氯化铁。氮气保护下将物料温度升到190℃,然后通入氯气进行反应。6h后反应结束。测得2,6
‑ꢀ
二氯吡啶的转化率为83.41%,2,3,6-三氯吡啶选择性为96.18%,氯气利用率51.72%
[0100]
比较例2
[0101]
用2,6-二氯吡啶制备2,3,5,6-四氯吡啶
[0102]
采用单釜反应。向反应釜中投入1200g2,6-二氯吡啶和48g氯化铁。氮气保护下将物料温度升到200℃,然后通入氯气进行反应。12h后反应结束。测得2,6
‑ꢀ
二氯吡啶的转化率为94.28%,2,3,5,6-四氯吡啶选择性为97.87%,氯气利用率 54.17%
[0103]
比较例3
[0104]
用2,3,6-三氯吡啶制备2,3,5,6-四氯吡啶
[0105]
采用单釜反应。向反应釜中投入1200g2,3,6-三氯吡啶和39g氯化铁。氮气保护下将物料温度升到205℃,然后通入氯气进行反应。6h后反应结束。测得2,3,6-三氯吡啶的转化率为90.94%,2,3,5,6-四氯吡啶选择性为96.18%,氯气利用率53.55%。