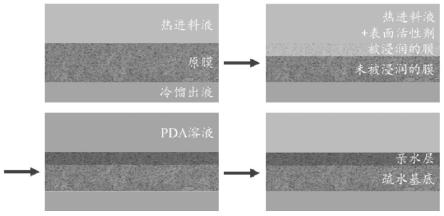
1.本发明属于水处理工程领域,具体涉及一种亲水层厚度可控的亲水疏油型非对称蒸馏膜的原位制备方法。
背景技术:2.膜蒸馏(md)是一项将膜分离和蒸馏技术相结合的新型热力驱动的工艺
1.,在高盐废水处理、页岩气废水处理等方面拥有广阔的应用前景
[2-4]
。传统的膜蒸馏系统使用的是疏水性膜,近年来,针对各种原水的特点,许多研究致力于新型膜材料的制备开发
[5]
。对于页岩气废水等含油脂等疏水性污染物的废水,一系列制备表面亲水疏油型非对称膜的方法应运而生
[6]
。
[0003]
亲水疏油型非对称膜是指表面具有一层亲水材料,基底为疏水材料的膜,在md中,亲水层可以起到抗油污的效果,而疏水基底保证md的截盐率。已有的制备方法通常是采用表面喷涂或接枝,对膜表面进行亲水化改性,但这些方法具有以下缺点:1)亲水层厚度不可控;2)亲水层易脱落;3)可能造成部分膜孔堵塞,降低蒸气通量
[7,8]
。此外,这些方法均是在离线状态对商品膜进行改性,具有一定的限制性。
[0004]
多巴胺是一种具有亲水基团和强粘附力的物质
[9]
,多用于商品膜的亲水化改性中
[10,11]
。膜浸润指的是进料液直接穿透膜孔到达馏出液侧的现象,是md中独有的技术挑战,但膜浸润同时也可以加以利用。在膜被浸润一定厚度但还未完全浸润的时候,将润湿层浸泡入多巴胺溶液,就能达到亲水化改性的效果,得到亲水疏油型非对称膜。通过控制表面活性剂的浓度和浸润时间,可以有效的控制润湿层的厚度,从而实现非对称蒸馏膜的原位可控制备。
[0005]
参考文献:
[0006]
[1]leej.-g.,jangy.,fortunatol.,etal.anadvancedonlinemonitoringapproachtostudythescalingbehaviorindirectcontactmembranedistillation[j].journalofmembranescience,2018,546(50-60.
[0007]
[2]thomasn.,mavukkandym.o.,loutatidous.,etal.membranedistillationresearch&implementation:lessonsfromthepastfivedecades[j].separationandpurificationtechnology,2017,189(108-127.
[0008]
[3]changh.,lit.,liub.,etal.potentialandimplementedmembrane-basedtechnologiesforthetreatmentandreuseofflowbackandproducedwaterfromshalegasandoilplays:areview[j].desalination,2019,455(34-57.
[0009]
[4]luk.-j.,chungt.-s.membranedistillation:membranes,hybridsystemsandpilotstudies[m].crcpress,2019:
[0010]
[5]huangy.-x.,wangz.,jinj.,etal.noveljanusmembraneformembranedistillationwithsimultaneousfoulingandwettingresistance[j]
.environmentalscience&technology,2017,51(22):13304-13310.
[0011]
[6]liny.,salemm.s.,zhangl.,etal.developmentofjanusmembranewithcontrollableasymmetricwettabilityforhighly-efficientoil/wateremulsionsseparation[j].journalofmembranescience,2020,606(118141.
[0012]
[7]wangz.,lins.membranefoulingandwettinginmembranedistillationandtheirmitigationbynovelmembraneswithspecialwettability[j].waterresearch,2017,112(38-47.
[0013]
[8]wuj.,wangn.,wangl.,etal.unidirectionalwater-penetrationcompositefibrousfilmviaelectrospinning[j].softmatter,2012,8(22):5996-5999.
[0014]
[9]leeh.,dellatores.m.,millerw.m.,etal.mussel-inspiredsurfacechemistryformultifunctionalcoatings[j].science,2007,318(5849):426-430.
[0015]
[10]yangh.-c.,liaok.-j.,huangh.,etal.mussel-inspiredmodificationofapolymermembraneforultra-highwaterpermeabilityandoil-in-wateremulsionseparation[j].journalofmaterialschemistrya,2014,2(26):10225-10230.
[0016]
[11]yangz.,wuy.,wangj.,etal.insitureductionofsilverbypolydopamine:anovelantimicrobialmodificationofathin-filmcompositepolyamidemembrane[j].environmentalscience&technology,2016,50(17):9543-9550.
技术实现要素:[0017]
本发明的目的在于提供一种亲水层厚度可控的亲水疏油型非对称蒸馏膜的原位制备方法。
[0018]
本发明的目的通过下述技术方案实现:
[0019]
一种亲水层厚度可控的亲水疏油型非对称蒸馏膜的原位制备方法,包括如下步骤:
[0020]
(1)在膜蒸馏系统中,用表面活性剂诱导膜浸润破坏疏水膜进料液侧表层的疏水性形成润湿层;
[0021]
(2)将膜用水洗净后,用多巴胺溶液对润湿层进行亲水化改性得到拥有亲水表层的亲水疏油型非对称蒸馏膜。
[0022]
所述的膜蒸馏系统包括进料液水箱、膜蒸馏膜组件、馏出液水箱、加热器、冷凝水机、循环泵和管路等;所述进料液用加热器加热;所述馏出液用冷凝水机冷凝;进料液与馏出液在膜组件中疏水膜的两侧形成各自的循环。
[0023]
进一步地,所述的表面活性剂诱导膜浸润的过程为,将进料液配制为一定浓度的表面活性剂的盐溶液并加热,在膜蒸馏系统运行过程中,表面活性剂诱导疏水膜进料液侧发生浸润,被浸润的膜表层即为润湿层。通过控制表面活性剂的浓度和浸润时间,可以有效的控制润湿层的厚度,而朝向馏出液的膜表面仍旧疏水。所述的表面活性剂的浓度≥能诱导浸润的最低浓度即可,对于不同的表面活性剂适用浓度不同,如对于tritonx-100,需大
于40mg/l;所述的盐溶液优选为0.6mol/l的nacl溶液;所述的加热的温度范围优选为40-70℃。
[0024]
进一步地,用表面活性剂诱导膜浸润破坏疏水膜进料液侧表层疏水性形成润湿层时,用光学相干断层成像扫描仪对疏水膜进行原位在线观测,以此实时监测表面活性剂浸润疏水膜的厚度,实现润湿层厚度的可控制备。
[0025]
进一步地,用表面活性剂诱导膜浸润破坏疏水膜进料液侧表层疏水性形成润湿层时,润湿层厚度控制在适当范围内,》5μm保证光学相干断层扫描仪可以分辨,小于疏水膜厚度的一半以防由于浸润的不均匀性而导致有部分膜孔完全浸润穿透。
[0026]
进一步地,所述的疏水膜材质包括pvdf、ptfe、pp等,厚度宜大于100μm,宜采用平板膜。
[0027]
进一步地,所述的多巴胺溶液的配制优选为:将多巴胺溶于ph=8.5、10mmol/l tris-hcl缓冲溶液中,配成2g/l的多巴胺溶液。
[0028]
进一步地,所述的亲水层厚度可控的亲水疏油型非对称蒸馏膜的原位制备方法,包括如下步骤:
[0029]
(1)将疏水膜置于膜蒸馏系统的膜组件中,运行膜蒸馏系统,当进料液盐溶液稳定在 50-70℃、馏出液稳定在10-30℃,向盐溶液中加入表面活性剂,诱导膜浸润破坏疏水膜进料液侧表层的疏水性形成润湿层,在线监测控制表面活性剂浸润疏水膜的厚度。
[0030]
(2)将进料液换为水,将膜表面和亲水膜孔润湿层内部残留的表面活性剂洗净;再将进料液换为多巴胺溶液,用循环泵循环进料液,在膜组件中形成错流对膜进行亲水化改性,使得浸润得到的润湿层可以保持长久有效的亲水性。所述的亲水化改性的时间≥6h。
[0031]
(3)亲水化改性完成后,将进料液换为水,将膜表面和亲水膜孔内部残留的聚合多巴胺洗净,得到亲水疏油型非对称蒸馏膜。
[0032]
本发明方法制备出的亲水疏油型的非对称膜,可以在膜被洗净后,直接投入使用。在一系列的md运行中表现出优良的抗油污染的性能,且膜的通量与原膜相比基本无变化,在膜蒸馏工艺对含油废水的处理中有广阔的应用前景。
[0033]
本发明的创新之处在于:
[0034]
1)利用膜蒸馏中的浸润现象,让疏水膜在深度方向上的一定厚度被浸润,以便于亲水化改性;
[0035]
2)非对称膜的亲水层厚度可以通过控制表面活性剂的浓度和浸润时间来控制;
[0036]
3)原位实现亲水疏油型非对称膜的制备。
[0037]
本发明的优点和有益效果:本发明方法制备出的亲水疏油型的非对称蒸馏膜,亲水层厚度可控,多巴胺的涂覆改性对商品膜本身疏松多孔的结构没有产生影响,且亲水层是由原膜的疏水部分改性而来的,不会脱落。此外,本方法是一种原位在线的制备方法,技术性难度低,在实际操作中减少了一定的人力需求。
附图说明
[0038]
图1是本发明的制膜过程示意图。
[0039]
图2是对比例1-2和实施例1-3所制备的蒸馏膜的亲水性测试结果图。
[0040]
图3是对比例1-2和实施例1-3所制备的蒸馏膜的纯水通量和盐水通量测试结果
图。
[0041]
图4是对比例1-2和实施例1-3所制备的蒸馏膜的含油盐水运行测试结果图。
[0042]
图5是对比例1-2和实施例1-3所制备的蒸馏膜的傅里叶变换红外光谱图。
具体实施方式
[0043]
以下实施例用于进一步说明本发明,但不应理解为对本发明的限制,其他的任何未背离本发明的精神实质与原理下所作的改变、修饰、替代、组合、简化,均应为等效的置换方式,都包含在本发明的保护范围之内。
[0044]
若未特别指明,实施例中所用的技术手段为本领域技术人员所熟知的常规手段。
[0045]
下述实施例中所使用的膜蒸馏系统包含:进料液和馏出液循环齿轮泵(wt3000-1jb, longer,中国),恒温磁力搅拌器(rct digital,ika,德国),冷凝水机(dc0510,cnshp,中国),电子天平(ah-a3002g,anheng,中国),电导率仪(sin-tds310,sinomeasure,中国),以及亚克力膜组件。其中电子天平和电导率仪用于记录馏出液的质量和电导率,以此计算膜的通量和截留率。
[0046]
实施例1
[0047]
一种亲水层厚度可控的亲水疏油型非对称蒸馏膜的原位制备方法,所述非对称蒸馏膜,具有一面亲水、一面疏水的非对称结构,制备过程包括以下步骤:
[0048]
首先,选择合适的疏水性商品膜置于膜蒸馏系统的膜组件中,本实施例中所使用的是疏水聚偏氟乙烯微滤膜,膜孔径为0.45μm,孔隙率70%,膜厚度约为116μm。
[0049]
其次,在膜蒸馏系统中,利用表面活性剂诱导的膜浸润,破坏靠近进料液一侧的膜的疏水性,本实施例中所使用的表面活性剂为非离子型表面活性剂triton x-100。当进料液0.6 mol/l nacl溶液加热并稳定在60℃,馏出液稳定在20℃,系统的通量稳定后,向进料液中投加一定量的triton x-100母液,使进料液含60mg/l的triton x-100。膜浸润的过程,用光学相干断层扫描仪进行在线观测,表面活性剂投加后15s,膜被浸润的厚度达到5μm左右。
[0050]
将膜蒸馏系统的进料液换为纯水,将膜表面的表面活性剂洗净。
[0051]
然后进行多巴胺涂覆亲水化改性。多巴胺溶液现用现配,首先配制10mmol/l的tris-hcl缓冲溶液,并用盐酸调节ph=8.5,再将多巴胺固体粉末溶解在tris-hcl缓冲溶液中,得到2g/l 的多巴胺溶液。将膜蒸馏系统的进料液换为多巴胺溶液,错流循环6h,对膜表面进行改性。
[0052]
最后将膜蒸馏系统的进料液换为纯水,将膜表面的残留溶液洗净,得到亲水疏油型非对称膜,靠近进料液侧为亲水层,靠近馏出液侧为疏水层,该膜的亲水层厚度为5μm左右。
[0053]
实施例2
[0054]
一种亲水层厚度可控的亲水疏油型非对称蒸馏膜的原位制备方法,所述非对称蒸馏膜,具有一面亲水,一面疏水的非对称结构,包括以下步骤:
[0055]
首先,选择合适的疏水性商品膜置于膜蒸馏系统的膜组件中,本实施例中所使用的是疏水聚偏氟乙烯微滤膜,膜孔径为0.45μm,孔隙率70%,膜厚度约为116μm。
[0056]
其次,在膜蒸馏系统中,利用表面活性剂诱导的膜浸润,破坏靠近进料液一侧的膜
的疏水性,本实施例中所使用的表面活性剂为非离子型表面活性剂triton x-100。当进料液 0.6mol/l nacl溶液加热并稳定在60℃,馏出液稳定在20℃,系统的通量稳定后,向进料液中投加一定量的triton x-100母液,使进料液含60mg/l的triton x-100。膜浸润的过程,用光学相干断层扫描仪进行在线观测,表面活性剂投加后1min,膜被浸润的厚度达到20μm左右。
[0057]
将膜蒸馏系统的进料液换为纯水,将膜表面的表面活性剂洗净。
[0058]
然后进行多巴胺涂覆亲水化改性。多巴胺溶液现用现配,首先配制10mmol/l的tris-hcl缓冲溶液,并用盐酸调节ph=8.5,再将多巴胺固体粉末溶解在tris-hcl缓冲溶液中,得到2g/l 的多巴胺溶液。将膜蒸馏系统的进料液换为多巴胺溶液,错流循环6h,对膜表面进行改性。
[0059]
最后将膜蒸馏系统的进料液换为纯水,将膜表面的残留溶液洗净,得到亲水疏油型非对称膜,靠近进料液侧为亲水层,靠近馏出液侧为疏水层,该膜的亲水层厚度为20μm左右。
[0060]
实施例3
[0061]
一种亲水层厚度可控的亲水疏油型非对称蒸馏膜的原位制备方法,所述非对称蒸馏膜,具有一面亲水,一面疏水的非对称结构,包括以下步骤:
[0062]
首先,选择合适的疏水性商品膜置于膜蒸馏系统的膜组件中,本实施例中所使用的是疏水聚偏氟乙烯微滤膜,膜孔径为0.45μm,孔隙率70%,膜厚度约为116μm。
[0063]
其次,在膜蒸馏系统中,利用表面活性剂诱导的膜浸润,破坏靠近进料液一侧的膜的疏水性,本实施例中所使用的表面活性剂为非离子型表面活性剂triton x-100。当进料液 0.6mol/l nacl溶液加热并稳定在60℃,馏出液稳定在20℃,系统的通量稳定后,向进料液中投加一定量的triton x-100母液,使进料液含60mg/l的triton x-100。膜浸润的过程,用光学相干断层扫描仪进行在线观测,表面活性剂投加后2min,膜被浸润的厚度达到40μm左右。
[0064]
将膜蒸馏系统的进料液换为纯水,将膜表面的表面活性剂洗净。
[0065]
然后进行多巴胺涂覆亲水化改性。多巴胺溶液现用现配,首先配制10mmol/l的tris-hcl 缓冲溶液,并用盐酸调节ph=8.5,再将多巴胺固体粉末溶解在tris-hcl缓冲溶液中,得到2g/l 的多巴胺溶液。将膜蒸馏系统的进料液换为多巴胺溶液,错流循环6h,对膜表面进行改性。
[0066]
最后将膜蒸馏系统的进料液换为纯水,将膜表面的残留溶液洗净,得到亲水疏油型非对称膜,靠近进料液侧为亲水层,靠近馏出液侧为疏水层,该膜的亲水层厚度为40μm左右。
[0067]
对比例1
[0068]
一种蒸馏疏水膜,对称结构,聚偏氟乙烯微滤膜,膜孔径为0.45μm,孔隙率70%,膜厚度约为116μm。
[0069]
对比例2
[0070]
一种表面亲水的复合疏水蒸馏膜的原位制备方法,包括以下步骤:
[0071]
首先,选择合适的疏水性商品膜置于膜蒸馏系统的膜组件中,本实施例中所使用的是疏水聚偏氟乙烯微滤膜,膜孔径为0.45μm,孔隙率70%,膜厚度约为116μm。
[0072]
其次,进行多巴胺涂覆亲水化改性。多巴胺溶液现用现配,首先配制10mmol/l的tris-hcl 缓冲溶液,并用盐酸调节ph=8.5,再将多巴胺固体粉末溶解在tris-hcl缓冲溶液中,得到2g/l 的多巴胺溶液。膜蒸馏系统的进料液为多巴胺溶液,错流循环6h,对膜表面进行改性。
[0073]
最后将膜蒸馏系统的进料液换为纯水,将膜表面的残留溶液洗净,得到表面亲水疏油型复合膜,该膜的亲水层厚度为0μm。
[0074]
为了更好地评估蒸馏膜的性能,对实施例1-3和对比例1-2的蒸馏膜进行了以下性能测试:
[0075]
(1)亲水性测试
[0076]
采用接触角测试仪测试对比例1-2和实施例1-3所制备的蒸馏膜的空气中水接触角和水下油滴接触角,测试结果见图2。
[0077]
(2)纯水通量测试
[0078]
在膜蒸馏系统中,运行工况为进料液为加热并循环稳定至60℃的纯水,馏出液为冷却并循环稳定至20℃的纯水,错流流速均为20cm/s,测试对比例1-2和实施例1-3所制备的蒸馏膜的纯水通量,测试结果见图3。对比例与实施例制备的膜的通量相差不大。
[0079]
(3)盐水通量测试
[0080]
在膜蒸馏系统中,运行工况为进料液为加热并循环稳定至60℃的0.6mol/l nacl溶液,馏出液为冷却并循环稳定至20℃的纯水,错流流速均为20cm/s,测试对比例1-2和实施例1-3 所制备的蒸馏膜的盐水通量,测试结果见图3。
[0081]
(4)含油盐水运行测试
[0082]
在膜蒸馏系统中,进料液为加热并循环稳定至60℃、含1g/l矿物油的0.6mol/l nacl溶液,馏出液为冷却并循环稳定至20℃的纯水,错流流速均为20cm/s,测试对比例1-2和实施例1-3所制备的蒸馏膜的运行性能,结果见图4。其中,对比例制备的膜均被矿物油浸润,截留率降低;而实施例制备的膜都表现出很好的抗油浸润的能力,并能稳定运行24h以上。
[0083]
(5)傅里叶变换红外光谱(ftir)表征
[0084]
对比例1-2和实施例1-3所制备的蒸馏膜进行ftir表征,结果见图5。波长1608cm-1
为聚合多巴胺的特征峰。对比例1未检测出多巴胺特征峰,对比例2检测出较弱的多巴胺特征峰,实施例1-3均检测出多巴胺特征峰,且多巴胺改性的亲水层厚度越大,多巴胺特征峰越强。