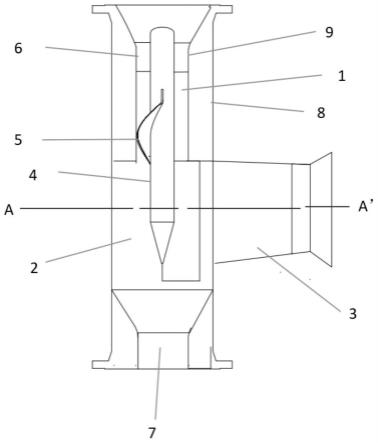
1.本实用新型总体地涉及天然气制乙炔技术领域,具体地涉及一种与乙炔炉配套的气体逆向双旋混合器。
背景技术:2.乙炔是一种重要的化工原料,主要用于制取醋酸、醋酸乙烯、乙烯基乙炔、丙烯酸、丁二烯、1,4-丁二醇等一系列化工产品,亦作为合成橡胶、合成纤维和塑料等材料的单体。烃类部分氧化制备乙炔是目前乙炔主要的制备方法之一,随着天然气原料的开采、使用技术的成熟,天然气部分氧化制乙炔的技术得到广泛关注。
3.天然气部分氧化制备乙炔的方法,是通过将天然气和氧气分别预热至600-650℃,在反应器的混合区进行充分混合,然后经过预混的扩散器进行反应器的反应区进行反应,并在反应后用一种水或渣油作急冷介质迅速急冷低于300℃的温度。在混合区中,天然气和氧气需要实现快速混合,确保气体流速大于火焰传播速度,防止反应室内的火焰发生回火返回至混合区。
4.目前,国内乙炔裂解的核心设备-乙炔炉,多采用多管立式炉,其乙炔炉的混合器装置包括顶部的氧气进口,中部的天然气进口,底部的混合气喷口,随着混合器装置流通截面积的放大,两种气体混合效果会有所下降,只能达到98%,同时混合所需的时间增加,不利于乙炔炉的安全、稳定运行。
5.专利cn1951885a和cn1951884a公开了两种用于乙炔炉的混合器装置。cn1951884a中的两入口混合器装置包括与氧气进口相连接的氧气喷管,在氧气喷管内由漩涡器定位片连接定位的漩涡器,在漩涡器下部圆周上均匀固定的氧气旋流片,与混合气喷口上端连接的天然气喷嘴,一端与天然气喷嘴上端连接、另一端与氧气喷管外侧连接的天然气进口滤网,天然气喷嘴上端内侧圆周均匀设置与氧气旋流片旋流方向相反的天然气旋流片,气体混合效果增强,混均度达到99.97%。专利cn1951885a则增加了天然气进口滤网中部位置处的圆周上设置的通孔经连通管与漩涡器圆周上设置的通孔连接的结构,形成三入口混合器,混合效果增强,混均度达到99.8%。专利cn105879806a公开的烃部分氧化制备乙炔和合成气的大型反应器中,在混合区设置有旋流器和侧向进气栅,烃和氧气中的一股通过旋流器,另一股通过侧向进气栅,然后两股气流在混合区充分均匀混合,烃和氧气的混均度达到99.9%。由于天然气侧向进气存在气体流速不均,不同混合位置,天然气和氧气混合效果会有较大影响,如何保证在最短时间内实现天然气和氧气的充分混合是本实用新型要解决的重要问题。
6.专利de4422815中提到用氧通过烃的部分氧化制备乙炔和合成气的设备,具有一个混合室,一个具有管道可连通骤冷室的燃烧器区段,其中燃烧器区段的管道是用穿孔的板覆盖进口端。其中混合器的作用是使烃和氧气充分和快速混合,但是该专利没有公开混合器的具体结构和实现方法。
技术实现要素:7.本实用新型的目的在于提供一种与乙炔炉配套的气体逆向双旋混合器,它通过在圆筒形壳体内的轴向和切向分别向壳体内的气体混合区送入不同的反应原料气,使两种原料气在毫秒数量级的时间混合时间内实现天然气和氧气的99.99%以上的混均度,从而提高乙炔产量。
8.本实用新型旨在通过结合计算流体力学和工程实验,寻找最佳的流体混合角度和方式,简化混合装置的结构,实现高温气体快速高效混合,满足乙炔合成的气体混合条件。通过实际工况发现,天然气切向进料能保证最大的气速,与氧气形成的反向旋流相对速度最大,能达到最佳的混均效果。
9.本实用新型的技术方案是,一种与乙炔炉配套的气体逆向双旋混合器,其特征在于,它包括第一进气口、气体混合区和第二进气口;所述第一进气口为圆筒状结构的壳体的一个端口,第一进气口下部的壳体内区域为气体混合区,第一进气口用于向气体混合区送入第一种气体;所述第二进气口与气体混合区位置的壳体连通,用于向气体混合区送入第二种气体;所述第二进气口的进气壁与壳体的筒壁之间的连接切向连接;所述第一进气口中心设置有锥柱,所述锥柱为下部锥形的圆柱结构;锥柱上固定有旋流翼片,所述旋流翼片为沿锥柱圆柱部分的外周从上向下同向螺旋设置的条片状结构,旋流翼片相对于锥柱横截面的倾角为15~45
°
;所述第二进气口向气体混合区的进气方向与旋流翼片在壳体中从上向下的螺旋方向相反。
10.本实用新型将两个进气口分别设置在圆筒状壳体的一端和侧向,两个进气口均与壳体中的气体混合区连通,实现气体从壳体的不同方向进入,为旋流混合提供设计空间:从圆筒壳体顶部端口(第一进气口)进入的气体经旋流翼片,以绕锥柱随旋流翼片的螺旋方向转动的方式从上向下进入气体混合区,形成第一环流,第一环流运动方向是向下和绕锥柱旋转两个运动方向的合成;从圆筒壳体筒壁切向(第二进气口)进入的气体,因为气体切向进入筒体,在筒体内形成绕筒壁向内旋转的旋流,当第二进气口的进气方向与旋流翼片的旋转方向相反时,两种气体在气体混合区内绕筒壁中心轴(假设中心轴存在的话)的旋转方向相反,形成逆向双旋的混合气体流,能实现从第一进气口和第二进气口进入的两种不同原料气的最大程度的混合,在天燃气至乙炔工艺中,能实现天然气和氧气的99.99%以上的混均度。
11.进一步的,上述壳体的筒壁与第二进气口的连接口部为长方形,长方形的长边设置在壳体的高度方向、短边设置在壳体的圆周方向,短边对应的壳体弧形段占所述壳体圆周的1/7-1/10;第二进气口的两个进气壁从壳体圆周上的同一方向与长方形连接口部的长边连接,其中一个进气壁相切于壳体连接处,另一个进气壁与壳体连接处的切线成0-30
°
夹角。
12.该第二进气口及其与壳体筒壁的连接口结构是实现第二进气口切向进气的优选和具体方案,在圆周上的足够小的弧形段能够保证进气的方向性,因为当弧形段大到一定程度后,进入的气体将难以在壳体中形成绕壁旋转的持续流动;在保证进气量的前提下,提高长方形连接口部的长宽比是才能提高进气的持续旋转流动效应;同时,使第二进气口的进气壁在一定长度内与连接的圆周保持切向,用于对气体形成引导和流向控制,也是为了保证进气形成足够的旋流;另外,第二进气口的两个进气壁在壳体圆周上在同一方向与长
方形口部的长边连接并保证其中一个相切,另一个接近相切,也是为了充分保证第二进气口的进气在壳体中形成单向旋流,且旋流在一定进气速度的保证下,能够在壳体中旋转足够的行程。
13.进一步的,上述第一进气口中还设置有内套筒和定位翅片;所述内套筒为外径与壳体的内径相同、内径呈漏斗型收口的结构,设置在第一进气口位置的壳体筒壁内,用于增加进入的第一种气体的流速,壳体的内径与内套筒下部的内径与之比为2:1-4:1;所述定位翅片为连接内套筒和锥柱的条片状结构,所述定位翅片与锥柱之间的连接、和定位翅片与内套筒之间的连接均为焊接,实现锥柱在第一进气口中心的固定;所述旋流翼片设置在第一进气口中定位翅片的下部,旋流翼片的内缘与锥柱之间焊接连接,外缘与内套筒之间预留有缝隙。
14.第一进气口形成的整体结构从上至下为:顶端为大口径进气,以保证足够的进气量;经内套筒的漏斗型收口后变成较小的口径,以增加气流速度,便于气体在旋流翼片位置形成预定速度的旋流;内套筒的上部为固定锥柱的定位翅片,定位翅片为沿圆周径向分布的片状结构,一侧连接内套筒,一侧连接锥柱外壁,并与两者均通过焊接固定,这样保证锥柱在壳体中心的稳固连接;内套筒的下部为旋流翼片,用于使进气形成向气体混合区的旋流,旋流翼片固定在锥柱外径上,并与内套筒内壁有空隙,以避免气流在旋流翼片周围形成压强差,导致气流不稳定或其他危险发生。因此,经第一进气口进入的第一种气体经变径增速后被旋流翼片的螺旋旋转改变流动方向,以绕锥柱旋转方式进入气体混合区。
15.进一步的,上述长方形连接口部的高度为:上沿与内套筒的下沿平齐,下沿与所述气体混合区的下沿平齐。
16.长方形连接口部的高度时保证经第二进气口进入的气体在气体混合区的整个高度方向形成旋转流动,以增大与第一进气口进气的混合面,以提高混匀度。
17.更进一步的,上述第二进气口从气体进口向第二进气口与壳体连接方向为口径渐缩结构,第二进气口的进口面积与所述长方形连接口部的面积比为4:1-10:1,所述口径渐缩结构用于使进入其中的第二种气体流速增加,快速进入所述气体混合区。
18.第二进气口的口径渐缩同样是为了增加长方形连接口部的进气速度,在长方形的长和宽为了保证进气切向被限定的情况下,从第二进气口的远端增加其进口面积,以保证足够的进气和缩径。设计合理的口部缩径比,相比于提高原始进气速度来保证气体的进气方向,更易实现工艺控制和节约耗材,且危险性降低。
19.进一步的,本实用新型装置还包括排气部;所述排气部设置在壳体中气体混合区的下部,排气部为漏斗型收口结构,漏斗形的底端为气体出口,气体出口连接乙炔反应炉;所述壳体的内径与气体出口的内径比为2:1-4:1,漏斗型收口结构用于使混合后的气体集中排出,所述锥柱的外径为排气部下部气体出口内径的0.4~0.75倍。
20.排气部设置和设计是为了更好地匹配下面的乙炔炉,使混合的气体经进一步增速后进入乙炔炉中反应。
21.本实用新型同时提供了一种天然气制乙炔工艺中的原料气混合工艺,它使用上述与乙炔炉配套的气体逆向双旋混合器,包括以下步骤:
22.从所述第一进气口的口部向内套筒中送入氧气或烃气中的一种;
23.从所述第二进气口的口部向壳体中送入氧气或烃气中的另一种;
24.两种气体在所述气体混合区中混合。
25.进一步的,从所述第一进气口进入气体混合区的气速为120~320m/s;从第一进气口进入气体混合区的气速为120~280m/s。
26.进一步的,从所述两种气体在气体混合区的混合时间为0.001~0.01s,然后从所述排气部进入乙炔反应炉中;从所述第二进气口的口部进入壳体中气体混合区的气体为天然气原料气。
27.进一步的,从所述气体混合区混合器中的温度在600-700℃,压力为0-0.3mpa。
28.从不同口部进入气体混合区的速度对保证各自气体的旋转方向以及两种气体的逆向双旋混合均匀度有重要影响,气体速度高,方向性更强,混合所需时间更短,混合均匀度更高。
29.本实用新型相比于现有技术的益处在于:
30.1)本实用新型通过第一进气口中的锥柱和旋流翼片,实现进气(高温氧气)的环轴向流动进入,第二进气口与壳体的切向连接,实现了进气(天然气)的切向进入,从而实现两种原料气的轴切向错流旋转进料,保证天然气和氧气瞬间混合均匀;
31.2)本实用新型通过设置各口部的缩径比,以增加进气速度,结合工艺控制对进气流量和速度,实现两种气体的混合时间仅为0.001~0.01s,混均度极高,从而增加了高温气体的传质效率,利用轴切向错流旋转进料实现两气体高效快速混合。
32.本实用新型设备简单,混合均匀度高,提高了气体混合器的混合效率,有效地降低了生产成本。
附图说明
33.从下面结合附图对本实用新型实施例的详细描述中,本实用新型的这些和/或其它方面和优点将变得更加清楚并更容易理解,其中:
34.图1为本实用新型实施例中一种与乙炔炉配套的气体逆向双旋混合器的结构示意图;
35.图2为图1中a-a’所示位置的剖面仰视图;
36.图3为本实用新型实施例中旋流翼片与锥柱固定连接的结构示意图;
37.其中,1-第一进气口,2-气体混合取,3-第二进气口,4-锥柱,5-旋流翼片,6-定位翅片,7-排气部,8-壳体,9-内套筒。
具体实施方式
38.为了使本领域技术人员更好地理解本实用新型,下面结合附图和具体实施方式对本实用新型作进一步详细说明。
39.实施例1
40.一种与乙炔炉配套的气体逆向双旋混合器,其结构如图1所示,包括第一进气口1、气体混合区2和第二进气口3;第一进气口1为圆筒状结构的壳体8的一个端口,第一进气口1下部的壳体8内区域为气体混合区2,第一进气口1用于向气体混合区2送入第一种气体;第二进气口3与气体混合区2位置的壳体8连通,用于向气体混合区2送入第二种气体。
41.第一进气口1的具体和优选结构如下:第一进气口1中心设置有内套筒9、定位翅片
6和锥柱4;内套筒9为外径与壳体8的内径相同、内径呈漏斗型收口的结构,设置在第一进气口1位置的壳体8筒壁内,用于增加进入的第一种气体的流速,壳体8的内径与内套筒9下部的内径与之比为2:1-4:1;定位翅片6为连接内套筒9和锥柱4的片状结构,定位翅片6与锥柱4之间的连接、和定位翅片6与内套筒9之间的连接均为焊接,实现锥柱4在第一进气口1中心的固定;锥柱4为下部锥形的圆柱结构;锥柱上固定有旋流翼片5,旋流翼片5及其在锥柱4上的连接如图3所示,旋流翼片5为沿锥柱4圆柱部分的外周从上向下同向螺旋设置的片状结构,旋流翼片5相对于锥柱4横截面的倾角为15~45
°
;旋流翼片5设置在第一进气口1中定位翅片6的下部,旋流翼片5的内缘与锥柱4之间焊接连接,外缘与内套筒9之间预留有缝隙。
42.第二进气口3具体和优选结构如下:第二进气口3的进气壁与壳体8的筒壁之间的连接切向连接,其中的切向连接的优选方案如图2所示,具体为:壳体8的筒壁与第二进气口3的连接口部为长方形,长方形的长边设置在壳体8的高度方向(优选长方形连接口部的高度为:上沿与内套筒9的下沿平齐,下沿与气体混合区2的下沿平齐。)、短边设置在壳体8的圆周方向,短边对应的壳体8弧形段占壳体8圆周的1/7-1/10;第二进气口3的两个进气壁从壳体8圆周上的同一方向与长方形连接口部的长边连接,其中一个进气壁相切于壳体8连接处,另一个进气壁与壳体8连接处的切线成0-30
°
夹角;为了使进入气体混合区2的第二种气体流速增加,快速进入气体混合区2,设计第二进气口3从气体进口向第二进气口3与壳体连接方向为口径渐缩结构,第二进气口3的进口面积与长方形连接口部的面积比为4:1-10:1。
43.其中,第二进气口3向气体混合区2的进气方向与旋流翼片5在壳体8中从上向下的螺旋方向相反。这是本实用新型实现两种进气逆向双旋高效混合的关键。
44.为了实现与下部的乙炔反应炉匹配,本实施例装置还设计包括排气部7;排气部设置在壳体8中气体混合区2的下部,排气部7为漏斗型收口结构,漏斗形的底端为气体出口,气体出口连接乙炔反应炉;壳体8的内径与气体出口的内径比为2:1-4:1,漏斗型收口结构用于使混合后的气体集中排出,锥柱4的外径为排气部7下部气体出口内径的0.4~0.75倍。
45.实施例2
46.一种天然气制乙炔工艺中的原料气混合工艺,它使用实施例1中的与乙炔炉配套的气体逆向双旋混合器,包括以下步骤:
47.从第一进气口1的口部向内套筒9中送入氧气或烃气中的一种;
48.从第二进气口3的口部向壳体中送入氧气或烃气中的另一种;
49.两种气体在气体混合区2中混合。
50.优选从第一进气口1进入气体混合区2的气速为120~320m/s;从第一进气口1进入气体混合区2的气速为120~280m/s;两种气体在气体混合区的混合时间为0.001~0.01s,然后从排气部7进入乙炔反应炉中;从第二进气口3的口部进入壳体8中气体混合区的气体为天然气原料气;气体混合区2混合器中的温度在600-700℃,压力为0-0.3mpa。
51.本实施例的混合装置与乙炔炉等工艺装置装配连接后,将原料天然气与氧气分别在各自的预热炉中预热至630~650℃的温度,再输入本实施例混合气装置在混合区进行充分混合,通过扩散道后在乙炔炉的反应道内进行反应,反应温度为1450~1500℃,经几毫秒的反应时间后,接着用冷水对反应产物(即裂解气)进行急冷降温,并终止反应,随后用常规方法用适当的溶剂分级吸收再解吸,得到产物合成气和高纯度乙炔。在使用本实施例的混合装置后,可以确保在天然气部分氧化制备乙炔和合成气的生产中,在工艺装置安全、稳
定、可靠的前提下将其生产能力从1万吨/年提高到2万吨/年以上。
52.以上已经描述了本实用新型的各实施例,上述说明是示例性的,并非穷尽性的,并且也不限于所披露的各实施例。在不偏离所说明的各实施例的范围和精神的情况下,对于本技术领域的普通技术人员来说许多修改和变更都是显而易见的。因此,本实用新型的保护范围应该以权利要求的保护范围为准。