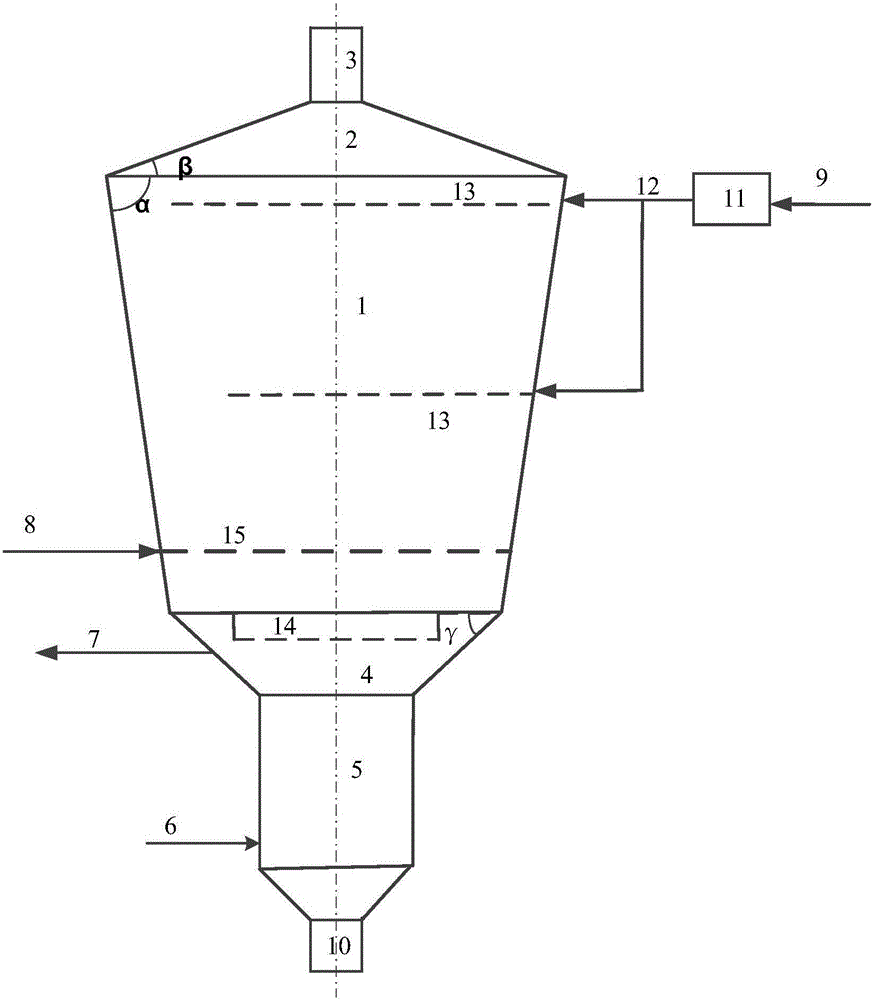
本发明涉及一种用于流化催化转化的反应器和催化转化方法。
背景技术:
:流化催化转化工艺如催化裂化工艺,通常是以重质油为原料,在酸性催化剂的作用下,转化成干气、液化气、汽油、轻循环油、油浆和焦炭的过程。伴随着分子筛催化剂的出现,催化裂化工艺的反应器主要包括两大类:一类是提升管反应器;另一类是下流式反应器。提升管反应器又可分为两大类:一类是常规的等直径的提升管反应器;另一类为变径的提升管反应器。对于等直径提升管反应器,主要的改进是为不同性质的烃类原料油提供适宜的反应条件,如中国专利cn1415700a披露的一种采用套管式反应器的催化裂化方法。对于变径提升管反应器,中国专利cn1237477a披露了一种沿垂直方向从下至上依次为互为同轴的预提升段、第一反应区、扩径的第二反应区、直径缩小了的出口区的变径提升管反应器,可以实现两个反应区的工艺条件的优化控制。在此基础上,中国专利cn100409936a通过改变进料喷嘴的角度以提高原料的雾化程度,从而改善产品分布和产品性质。中国专利cn1095392a披露了一种反应器横截面圆的直径随反应器高度不同而连续变化的变径提升管反应器,以尽可能实现流体入口流速与出口流速基本相同、以满足多产气态烯烃工艺的需求。中国专利cn101191070a披露的一种生产低碳烯烃的方法中采用的反应器与中国专利cn1095392a基本类似,反应器横截面积沿物流流动方向不断扩大,以尽可能使反应器内的催化剂密度、非催化剂物流空塔气速保持相对稳定。自上世纪80年代以来,国外许多著名石油公司分别提出了高温、短接触时间的下流式反应器专利技术,如美国专利us4514285、us5296131、us4985136、以及中国专利cn1546610a、cn1453334a等等,目的主要是减少非理想的二次反应,减少焦炭等产率,提高汽油和烯烃产率。对于上述的催化裂化反应器,无论是提升管反应器还是下流式反应器,原料油和催化剂瞬间接触反应后产生的反应油气和催化剂流的流动方向是同向一致的,由于此时的催化剂上已经积炭,这意味着该反应油气在离开反应器与催化剂分离之前,会一直与低活性的积碳催化剂接触,那么带来的结果是该反应油气随后可能伴随发生低选择性的副反应,如热裂化反应等等,导致最终产品选择性变差。此外,无论是提升管反应器还是下流式反应器,从入口到出口,均存在较大的温度梯度,不同的温度梯度对反应的选择性产生影响。此外,催化裂化的主要目的产品是汽油,但对于一些低生焦率、但由于自身结构特征或者由于自身含有较多催化剂污染物从而导致较难转化的原料油,无论采用提升管反应器还是下流式反应器,目的产品汽油产率和选择性均较低,反应产物主要是性质较差的轻循环油,极大地降低了装置的经济效益。技术实现要素:本发明的目的是提供一种用于流化催化转化的反应器和催化转化方法,本发明提供的反应器和方法能够提高催化转化反应的选择性,提高汽油收率和选择性。为了实现上述目的,本发明提供一种用于流化催化转化的反应器,所述密相流化床的内径由下至上逐渐增大,该反应器主体为密相流化床,所述密相流化床的下部设置有第一原料油入口、顶部设置有反应油气出口和底部设置有催化剂出口,所述密相流化床在所述第一原料油入口的上方设置有多个催化剂入口,所述多个催化剂入口沿高度方向从上至下分布。可选的,最上方的催化剂入口距所述密相流化床顶部的距离为0-2米,相邻催化剂入口的距离不低于2米,不高于h/n米,其中,h为所述密相流化床的高度,h≥4米,n为所述催化剂入口的个数,n≥2,h/n>2。可选的,所述催化剂入口为2-4个。可选的,所述密相流化床还设置有至少一个第二原料油入口,所述第二原料油入口沿竖直方向设置于相邻两个催化剂入口之间。可选的,每个催化剂入口的下方均对应设置有一个第一原料油入口或第二原料油入口,每个催化剂入口与其对应的原料油入口的距离不低于1米,不高于h/n米,其中,h为所述密相流化床的高度,h≥4米,n为所述催化剂入口的个数,n≥2,h/n>1;所述第一原料油入口距所述密相流化床底部的竖直距离为0-2米。可选的,所述密相流化床为倒圆台形,且纵剖面为等腰梯形,该等腰梯形的顶角α为20-85°。可选的,所述反应器还包括位于所述密相流化床外部的外取热器,所述外取热器设置有催化剂进口和催化剂出口,所述外取热器的催化剂出口与所述密相流化床的催化剂入口相连通,所述外取热器的催化剂进口用于连接再生器的催化剂出口。可选的,所述密相流化床的第一原料油入口处设置有进料分布板,每个所述催化剂入口处设置有催化剂分配器,所述进料分布板和催化剂分配器沿所述密相流化床的径向水平设置。可选的,所述反应器还设置有出口段、过渡段和汽提器,所述出口段、密相流化床、过渡段和汽提器由上至下同轴设置且之间流体连通;所述汽提器的底部设置有汽提后催化剂出口,下部设置有汽提蒸汽入口;所述过渡段设置有汽提后油水混合物出口;所述出口段的顶部设置有反应油气出口。可选的,所述出口段为正圆台形,且纵剖面为等腰梯形,该等腰梯形的底角β为10-45°;所述过渡段为倒圆台形,且纵剖面为等腰梯形,该等腰梯形的顶角γ为20-60°。可选的,所述过渡段中设置有分布来自密相流化床中催化剂的大孔分布板。本发明还提供一种采用本发明所提供的反应器进行催化转化的方法,该方法包括:将催化转化原料油送入所述密相流化床中与催化转化催化剂接触并由下至上逆流进行催化转化反应。可选的,所述催化转化原料油包括选自加氢柴油、油母页岩油、油母页岩油馏分油、焦化蜡油和劣质重油中的至少一种。可选的,所述密相流化床的空塔气速为0.2-3米/秒,重时空速为0.1-80小时-1,床层密度为80-700千克/米3,所述催化转化催化剂的温度不高于620℃。本发明提供的反应器的优点在于:1、本发明的反应器可以使催化转化原料油和催化转化催化剂梯级密相逆流接触,可以保证催化转化原料油以及所产生的油气随时和高活性的催化转化催化剂接触反应,大大提高了催化转化反应汽油的选择性。2、本发明的反应器内轴向、均向温度相对均一,且反应器内径由下至上逐渐增大的结构可以确保催化剂和油气流动状态相对稳定,有利于大幅度减少热裂化等副反应的发生,可以极大地提高汽油的选择性。3、与常规的提升管反应器或常规的密相床层反应器相比,本发明有利于提高原料油转化能力,大幅度提高汽油产率。本发明的其他特征和优点将在随后的具体实施方式部分予以详细说明。附图说明附图是用来提供对本发明的进一步理解,并且构成说明书的一部分,与下面的具体实施方式一起用于解释本发明,但并不构成对本发明的限制。在附图中:图1是本发明反应器一种具体实施方式的结构示意图。附图标记说明1密相流化床2出口段3油气出口管4过渡段5汽提器6管线7管线8管线9管线10催化剂出口管11外取热器12管线13催化剂分配器14大孔分布板15进料分布板具体实施方式以下结合附图对本发明的具体实施方式进行详细说明。应当理解的是,此处所描述的具体实施方式仅用于说明和解释本发明,并不用于限制本发明。本发明中,如无特殊说明,顶、底、上和下相对于反应器实际使用的顶、底、上和下而言的,超过50%高度称为上,50%高度以下称为下;两个部件之间的距离是指两个部件最短连线的长度。如图1所示,本发明提供一种用于流化催化转化的反应器,该反应器主体为密相流化床1,所述密相流化床1的内径由下至上逐渐增大,所述密相流化床1的下部设置有第一原料油入口、顶部设置有反应油气出口和底部设置有催化剂出口,所述密相流化床1在所述第一原料油入口的上方设置有多个催化剂入口,所述多个催化剂入口沿高度方向从上至下分布。本发明通过催化转化原料油和催化转化催化剂梯级密相逆流接触,可以保证催化转化原料油以及所产生的油气随时和高活性的催化转化催化剂接触反应,大大提高了催化反应的选择性,可以提高汽油的选择性。根据本发明,设置多个催化剂入口可以使催化剂呈现梯级分布,使位于密相流化床不同高度的反应油气均能接触到高活性的催化剂,从而提高反应的转化率。例如,最上方的催化剂入口距所述密相流化床顶部的距离可以为0-2米,相邻催化剂入口的距离不低于2米,不高于h/n米,其中,h为所述密相流化床的高度,h≥4米,n为所述催化剂入口的个数,n≥2,优选为2-4,更优选为2-3,h/n>2。根据本发明,所述密相流化床1还可以设置有至少一个第二原料油入口,所述第二原料油入口可以沿竖直方向设置于相邻两个催化剂入口之间,该第二原料油入口可以为1-3个。一种实施方式,每个催化剂入口的下方均对应设置有一个第一原料油入口或第二原料油入口,每个催化剂入口与其对应的原料油入口(第一原料油入口或第二原料油入口)的距离不低于1米,不高于h/n米,其中,h为所述密相流化床的高度,h≥4米,n为所述催化剂入口的个数,n≥2,h/n>1;所述第一原料油入口距所述密相流化床1底部的竖直距离为0-2米。根据本发明,由于催化转化反应是体积增加的反应,为了使反应气流更加平缓,所述密相流化床的内径可以由下至上逐渐增大,例如密相流化床可以为喇叭形、倒锥形和倒圆台形等,优选地,如图1所示,所述密相流化床为倒圆台形,且纵剖面可以为等腰梯形,该等腰梯形的顶角α可以为20-85°,下底直径优选比常规提升管反应器直径大。如图1所示,所述反应器还可以包括位于所述密相流化床1外部的外取热器11,所述外取热器11设置有催化剂进口和催化剂出口,所述外取热器11的催化剂出口可以与所述密相流化床1的催化剂入口相连通,所述外取热器11的催化剂进口可以用于连接再生器的催化剂出口。根据本发明,原料油入口(包括第一原料油入口和第二原料油入口)可以由一套喷油系统构成,例如包括进料管和进料分布板,喷油系统和常规的密相床层反应器喷油系统可以相同,本发明对此没有特殊要求,其尺寸由本领域技术人员根据装置的加工量自行确定,进入每层原料油入口的原料油类型可以相同,也可以不同。如图1所示,所述密相流化床1的第一原料油入口处可以设置有进料分布板15,同时第二原料油入口处也可以设置进料分布板15,每个所述催化剂入口可以处设置有催化剂分配器13,设置进料分布板和催化剂适配器可以防止引入反应器的原料油和催化剂在反应器内产生偏流,提高催化剂和原料油的分散性以及混合程度,并进一步提高原料油的转化率,降低剂油比焦,进一步地,所述进料分布板15和催化剂分配器13优选沿所述密相流化床1的径向水平设置,从而使催化剂和原料油的分散性更好。如图1所示,所述反应器还可以设置有出口段2、过渡段4和汽提器5,所述出口段2、密相流化床1、过渡段4和汽提器5可以由上至下同轴设置且之间流体连通;所述汽提器5的底部可以设置有汽提后催化剂出口,下部设置有汽提蒸汽入口;所述过渡段4可以设置有汽提后油水混合物出口;所述出口段2的顶部设置有反应油气出口。出口段2、过渡段4和汽提器5可以与常规的密相流化床设置方式一致,优选地,所述出口段2可以为正圆台形(或近圆锥形),且纵剖面可以为等腰梯形,该等腰梯形的底角β可以为10-45°,出口段的顶部可以连通出口管,类似于常规提升管反应器的出口,其作用是将反应生产的产物与少量夹带的催化剂输送至分离系统进行气固分离,例如可以直接与后续的旋风分离器相连进行旋风分离,分离后的油气去后续分离单元,分离后的催化剂返回汽提器。所述过渡段4可以为倒圆台形,且纵剖面可以为等腰梯形,该等腰梯形的顶角γ可以为20-60°,从汽提器出来的含油气的汽提蒸汽从该过渡段的汽提后油水混合物出口引出,本发明对汽提器没有特殊要求,汽提器的直径、高度及其内部人字型挡板的设置均与现有技术中常规汽提器要求相同,例如为圆筒形,也可以采用填料型汽提器。为了提高汽提效率,如图1所示,所述过渡段4中可以设置有分布来自密相流化床1中催化剂的大孔分布板14,大孔分布板14的直径与反应器底部直径可以相同,开孔直径可以为0.5-40里面,优选1-25厘米。开孔面积可以占整个反应器底部面积的10-90%,优选15-80%。本发明对大孔分布板没有特殊限制要求,可以凹形、凸形、锅底形等等。另外,本发明提供的反应器的材质要求与常规的提升管反应器可以完全相同。本发明还提供一种所提供的反应器进行催化转化的方法,该方法包括:将催化转化原料油送入所述密相流化床1中与催化转化催化剂接触并由下至上逆流进行催化转化反应。具体地,若仅设置第一原料油入口,则原料油可以全部从密相流化床下部的第一原料油入口送入密相流化床中;若设置第一原料油入口和第二原料油入口,则原料油可以按照一定的比例分别从第一原料油入口和一个或多个第二原料油入口送入,本领域技术人员可以根据需要进行操作。本发明对催化转化原料油并无特殊限制,优选采用较难转化的原料油,例如所述催化转化原料油可以包括选自加氢柴油、油母页岩油、油母页岩油馏分油、焦化蜡油和劣质重油中的至少一种,上述原料油中,加氢柴油由于本身含有的烃类而较难转化,其余原料油则由于其中污染物(例如碱氮或金属)的含量较高而较难转化,本领域其它原料油也可以用于本发明,本发明并无特殊限制。根据本发明,基于本发明反应器的内径可以由下至上逐渐增大,因此,所述密相流化床1的空塔气速可以稳定在0.2-3米/秒,优选为0.4-2.5米/秒,从而提高了反应的稳定性;另外,根据常规的密相流化床的条件,重时空速可以为0.1-80小时-1,优选为0.5-50小时-1,床层密度可以为80-700千克/米3,优选为150-600千克/米3;所述催化转化催化剂的温度一般不高于620℃,优选不高于600℃,该控制催化转化催化剂的温度的方式可以采用外取热器11进行。为了提高反应的稳定性,减小温度梯度,所述密相流化床1的轴向竖直方向)温差不超过10℃,优选不超过5℃,径向(水平方向)温差不超过5℃,优选不超过3℃。下面结合附图对本发明所提供的催化转化反应器作进一步说明,但本发明并不因此而受到任何限制。如图1所示,反应器从上往下依次为油气出口管3、出口段2、倒圆台形的密相流化床1、过渡段4、汽提器5和催化剂出口管10。催化转化原料油经管线8并通过进料分布板15进入倒圆台形的密相流化床1,从再生器来的高温再生催化剂经管线9进入外取热器11冷却后分两层经管线12进入倒圆台形的密相流化床1内的催化剂分配器13,催化剂呈密相往下流动,与从管线8来的催化转化原料油接触,在催化转化条件下发生催化裂化反应,反应油气向上流动,与催化剂梯级逆流接触,反应后的油气经反应器出口段2,经油气出口管3流出。反应后的待生催化剂经大孔分布板14经过渡段4进入汽提器5,汽提后的待生催化剂经催化剂出口管10去再生器再生。汽提蒸汽由管线6进入,汽提后的蒸汽和油气混合物经管线7从过渡段4引出。下面的实施例将对本发明予以进一步的说明,但并不因此而限制本发明。实施例和对比例中催化转化反应器使用的催化剂的物化性质见表1,其商业牌号为hac,由中国石化催化剂分公司齐鲁催化剂厂生产。实施例和对比例中所使用的原料(催化裂化轻循环油经加氢后得到的加氢柴油)性质列于表2。表4和表5中:转化率=干气产率+液化气产率+汽油产率+焦炭产率;汽油选择性=汽油产率/转化率。实施例1本实施例说明在中型规模本发明提供的倒圆台形的密相流化床上,使用hac催化剂生产汽油的过程。如图1所示,倒圆台形的密相流化床1底部直径为1.0米,反应器高度为6米,纵剖面等腰梯形的顶角α为60°。出口区2纵剖面等腰梯形的底角β为20°,过渡段9纵剖面等腰梯形的顶角γ为45°,汽提段为圆筒形。反应器底部过渡段9中的大孔分布板10开孔直径5厘米,开孔面积和下部的汽提段8横截面积相同,均为0.1256平方米。高温再生催化剂经催化剂冷却器16冷却至560℃后,分两层从两个催化剂入口进入倒圆台形的密相流化床1,上层催化剂从距离密相流化床1顶部的0.3米位置的催化剂入口进入,下层催化剂从距离上层2.7米位置的催化剂入口进入。仅设置一个第一原料油入口,第一原料油入口位置距离密相流化床1下底的0.5米,反应器内催化剂床层密度为350千克/米3,具体反应条件见表3,具体反应结果见表4。对比例1与实施例1相比,对比例1中使用的反应器为常规的中型等径提升管,提升管内径0.25米,高度为15米,具体反应条件见表3,具体反应结果见表4。对比例2与实施例1相比,对比例中使用的反应器为常规的中型床层反应器。反应器内径2.5米,密相床层高度为5米,具体反应条件见表3,具体反应结果见表4。将实施例1和对比例1、对比例2相比,可以发现,实施例均具有更高的汽油产率和汽油选择性。表1hac催化剂性质表2原料油性质项目数值密度(20℃)/千克·米-3899.2运动粘度/毫米2.秒-120℃3.84550℃2.004折射率(20℃)1.5036苯胺点,℃<3010%残炭,重量%<0.1硫含量,毫克/升142氮含量,毫克/升13碳含量,重量%88.74氢含量,重量%11.26碱性氮,毫克/千克3闭口闪点,℃78凝固点,℃-39酸度,毫克koh/100毫升<0.2实际胶质,毫克/100毫升56分子量192表3操作条件表4实施例实施例1对比例1对比例2产品分布,重量%干气2.72.34.5液化气12.814.516.2汽油58.248.846.3轻柴油20.729.623.4重油1.41.22.8焦炭4.23.66.8合计100100100转化率,重量%79.370.476.6汽油选择性,重量%73.469.360.4当前第1页12