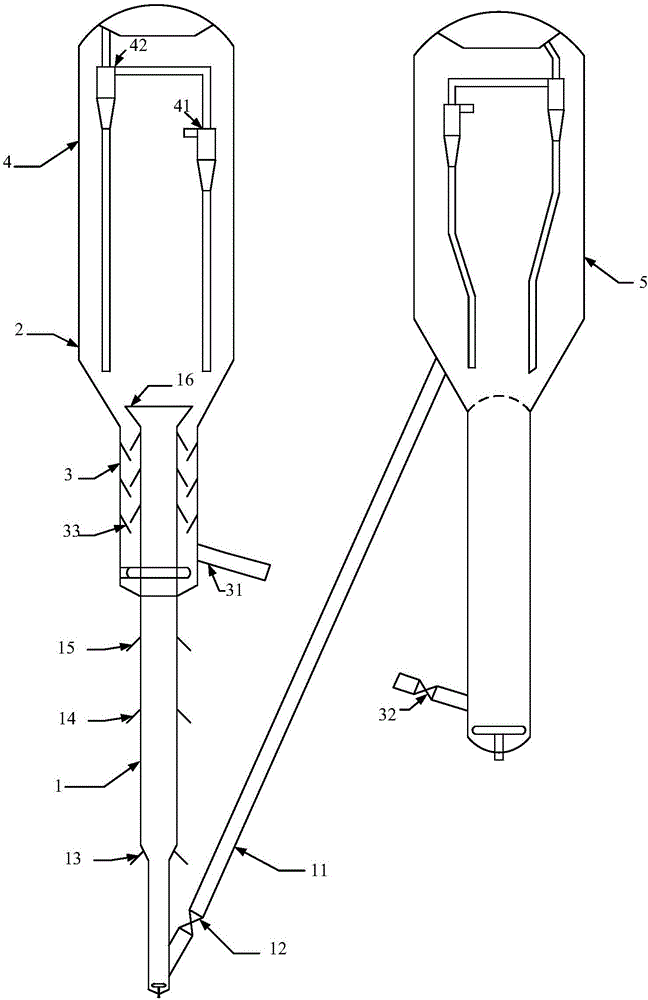
本发明涉及一种加氢生成油催化裂解的方法。
背景技术:
:低碳烯烃如乙烯、丙烯等是重要的有机化工原料,预计中国到2020年乙烯的年当量消费量达到4800万吨,年均增长率约为3.6%,而丙烯的年当量消费量求量将达到4000,年均增长率约为4.7%。从重质原料通过催化裂化等炼油装置生产低碳烯烃、芳烃等化工原料,是解决化工轻油不足的合理技术路径,而传统的催化加氢和催化裂化组合工艺一般是为了提高燃料油(汽油、柴油)的产量、改善催化裂化的产品分布和产品质量。wo0031215公开了一种生产烯烃的催化裂化方法,该方法以减压瓦斯油为原料,采用的催化剂由基质和zsm系列分子筛组成,其中基质部分包括惰性基质和少量活性基质,分子筛则采用大孔分子筛,该方法的低碳烯烃收率能超过13重%,比常规催化裂化方法高。美国专利us4619757公开了一种两段加氢处理从重质馏分油生产烯烃的方法。该方法包括一个加氢处理过程和一个热裂化过程,加氢处理过程由两段组成,第一段主要是选择性脱除多环芳烃,用含有沸石的加氢处理催化剂处理多环芳烃含量高的原料譬如减压瓦斯油,第二段主要是加氢脱硫和加氢脱氮,用不含有沸石的加氢处理催化剂处理多环芳烃含量低的原料譬如常压瓦斯油。该方法氢耗低,但烯烃收率不高。wo0040677公开了一种加氢处理和催化裂化的组合工艺方法。该方法包括至少两个加氢处理装置和两个催化裂化装置。原料油先经第一个加氢处理装置得到第一个加氢尾油;第一个加氢尾油进入第一个催化裂化装置,得到石脑油、柴油和重油,其中重油进入第二个加氢处理装置进行加氢,得到第二个加氢尾油,第二个加氢尾油到第二个催化裂化装置进行裂化,再得到相应产品。该方法流程复杂,投资和操作成本高,丙烯产率较低。中国专利cn1119397a公开了一种渣油加氢处理-催化裂化组合工艺方法,该方法中,渣油和澄清油一起进入渣油加氢处理装置,在氢气和加氢催化剂存在下进行加氢反应;反应所得的加氢渣油进入催化裂化装置,在裂化催化剂存在下进行裂化反应,重循环油在催化裂化装置内部进行循环;反应所得的油浆经分离器分离得到澄清油,返回至加氢装置。此方法使催化裂化油浆转化为轻质油品,提高了汽油和柴油的收率,降低了重油的收率,但此方法丙烯产率较低。上述方法提到加氢生成油进行催化裂化多产丙烯,但没有根据加氢生成油的氢转移反应特点,提出提高加氢生成油低碳烯烃产率和选择性的有效方法。技术实现要素:本发明的目的是提供一种加氢生成油催化裂解的方法,本发明的方法可以提高低碳烯烃产率。为了实现上述目的,本发明提供一种加氢生成油催化裂解的方法,该方法包括:将非加氢生成油从提升管反应器下部的第一喷嘴喷入提升管反应器中与来自提升管反应器底部的催化裂解催化剂接触并进行第一催化裂解反应,得到第一反应产物和半待生催化剂;将加氢生成油从所述第一喷嘴上方的第二喷嘴喷入提升管反应器中与来自第二喷嘴下方的第一反应产物和半待生催化剂接触并进行第二催化裂解反应,得到第二反应产物和待生催化剂;其中,所述第二反应产物至少包括异丁烷和异丁烯;所述方法还包括:通过调整非加氢生成油和加氢生成油的进料比例,控制所述第二反应产物中异丁烷和异丁烯的重量比为0.5-1.2之间;若异丁烷和异丁烯的重量比小于0.5,降低非加氢生成油的进料比例;若异丁烷和异丁烯的重量比大于1.2,提高非加氢生成油的进料比例。可选的,通过调整非加氢生成油和加氢生成油的进料比例,控制所述第二反应产物中异丁烷和异丁烯的重量比为0.9-1.2之间,若异丁烷和异丁烯的重量比小于0.9,降低非加氢生成油的进料比例;若异丁烷和异丁烯的重量比大于1.2,提高非加氢生成油的进料比例。可选的,所述方法还包括:通过调整非加氢生成油和加氢生成油的进料比例,控制所述第二反应产物中异丁烷和异丁烯的重量比为0.5-1.2之间;其中,若异丁烷和异丁烯的重量比小于0.5,降低非加氢生成油的进料比例;若异丁烷和异丁烯的重量比大于1.2,提高非加氢生成油的进料比例。可选的,所述非加氢生成油占加氢生成油的重量比为0.05-2。可选的,所述第一催化裂解反应的条件包括:第二喷嘴处的温度为550-680℃,催化裂解催化剂与非加氢生成油的重量比为20-150,油气停留时间为0.05-2秒。可选的,所述非加氢生成油为选自减压瓦斯油、常压渣油、减压渣油和重油中至少一种。可选的,所述第二催化裂解反应的条件包括:提升管反应器的出口温度为460-620℃,催化裂解催化剂与加氢生成油的重量比为5-50,油气停留时间为0.5-4秒。可选的,所述加氢生成油为选自加氢裂化尾油、加氢精制蜡油、加氢脱硫常压渣油和加氢脱硫减压渣油的至少一种。可选的,所述方法还包括:将第二催化裂解反应所得反应物料送入流化床反应器中进行第三催化裂解反应,得到所述第二反应产物和待生催化剂。可选的,所述第三催化裂解反应的条件包括:温度为450-610℃,重时空速为0.5-30小时-1。可选的,以干基计并以所述催化裂解催化剂的重量为基准,所述催化裂解催化剂含有1-60重量%的沸石混合物、5-99重量%的耐热无机氧化物和0-70重量%的粘土,其中,以所述沸石混合物的总重量为基准,所述沸石混合物含有1-75重量%的改性β沸石和25-99重量%的具有mfi结构的沸石。可选的,以干基计并以所述催化裂解催化剂的重量为基准,所述催化裂解催化剂含有10-50重量%的沸石混合物、10-70重量%的耐热无机氧化物和0-60重量%的粘土。本发明的方法将加氢生成油和非加氢生成油进行分层进料,并可以调节反应系统的氢转移活性,提高低碳烯烃产率。本发明的其他特征和优点将在随后的具体实施方式部分予以详细说明。附图说明附图是用来提供对本发明的进一步理解,并且构成说明书的一部分,与下面的具体实施方式一起用于解释本发明,但并不构成对本发明的限制。在附图中:图1是本发明方法所采用催化裂解系统一种具体实施方式的结构示意图。附图标记说明1提升管反应器11再生剂输送管12流量控制阀13第一喷嘴14第二喷嘴15蒸汽喷嘴16出口分布器2流化床反应器3汽提器31待生剂输送管32流量控制阀4沉降器5再生器具体实施方式以下结合附图对本发明的具体实施方式进行详细说明。应当理解的是,此处所描述的具体实施方式仅用于说明和解释本发明,并不用于限制本发明。本发明提供一种加氢生成油催化裂解的方法,该方法包括:将非加氢生成油从提升管反应器下部的第一喷嘴喷入提升管反应器中与来自提升管反应器底部的催化裂解催化剂接触并进行第一催化裂解反应,得到第一反应产物和半待生催化剂;将加氢生成油从所述第一喷嘴上方的第二喷嘴喷入提升管反应器中与来自第二喷嘴下方的第一反应产物和半待生催化剂接触并进行第二催化裂解反应,得到第二反应产物和待生催化剂;其中,所述第二反应产物至少包括异丁烷和异丁烯;所述方法还包括:通过调整非加氢生成油和加氢生成油的进料比例,控制所述第二反应产物中异丁烷和异丁烯的重量比为0.5-1.2之间;若异丁烷和异丁烯的重量比小于0.5,降低非加氢生成油的进料比例;若异丁烷和异丁烯的重量比大于1.2,提高非加氢生成油的进料比例。根据本发明,为了调整反应系统的氢转移活性,本发明通过调整非加氢生成油和加氢生成油的进料比例,控制所述第二反应产物中异丁烷和异丁烯的重量比为0.5-1.2之间,优选为0.9-1.2之间;其中,若异丁烷和异丁烯的重量比小于0.5,优选小于0.9,降低非加氢生成油的进料比例;若异丁烷和异丁烯的重量比大于1.2,提高非加氢生成油的进料比例。根据本发明,所述的非加氢生成油占加氢生成油的比例与非加氢生成油的生焦率成反比关系,即非加氢生成油的生焦率高,非加氢生成油占加氢生成油的比例较低。所述的非加氢生成油占加氢生成油的比例与反应系统氢转移活性成正比关系,即反应系统氢转移活性高,则非加氢生成油占加氢生成油的比例则较高。通过调节非加氢生成油与加氢生成油的比例,控制反应器中反应系统的氢转移活性,可以有效提高加氢生成油的低碳烯烃产率和选择性。所述非加氢生成油占加氢生成油的重量比可以为0.05-2。根据本发明,催化裂解反应是本领域技术人员所熟知的,本发明不再赘述。所述第一催化裂解反应的条件可以包括:第二喷嘴处的温度为550-680℃,优选为590-660℃,压力(绝压)为0.15-0.4兆帕,优选0.18-0.35兆帕,催化裂解催化剂与非加氢生成油的重量比为20-150,油气停留时间为0.05-2秒,优选为0.08-1.5秒。所述第二催化裂解反应的条件可以包括:提升管反应器的出口温度为460-620℃,优选为500-620℃,进一步优选为520-600℃,压力(绝压)为0.15-0.4兆帕,优选0.18-0.35兆帕,催化裂解催化剂与加氢生成油的重量比为5-50,油气停留时间为0.5-4秒,优选为0.8-3.5秒。根据本发明,非加氢生成油是指未经加氢处理的原料油,例如,所述非加氢生成油可以为选自减压瓦斯油、常压渣油、减压渣油和重油中至少一种。加氢生成油是指经过加氢处理的原料油,例如,所述加氢生成油可以为选自加氢裂化尾油、加氢精制蜡油、加氢脱硫常压渣油(英文简写:ards)和加氢脱硫减压渣油(英文简写:vrds)的至少一种。根据本发明,所述方法还可以包括:将第二催化裂解反应所得反应物料送入流化床反应器中进行第三催化裂解反应,得到所述第二反应产物和待生催化剂。进行第三催化裂解反应可以进一步提高低碳烯烃例如丙烯的产率,离开提升管反应器的油气和催化剂从流化床反应器的底部引入流化床反应器,离开流化床反应器的待生催化剂也从流化床反应器的底部引出,离开流化床反应器的第二反应产物从其顶部引出,流化床反应器反应后的第二反应产物引入沉降器,分离出其中夹带的催化剂后引入分馏系统;反应后的催化剂引入汽提器,汽提出吸附的烃类物质后引入再生器再生。所述第三催化裂解反应的条件可以包括:温度为450-610℃,压力(绝压)0.15-0.4兆帕,重时空速为0.5-30小时-1。根据本发明,催化裂解催化剂是本领域技术人员所熟知的,例如,以干基计并以所述催化裂解催化剂的重量为基准,所述催化裂解催化剂可以含有1-60重量%的沸石混合物、5-99重量%的耐热无机氧化物和0-70重量%的粘土,优选含有10-50重量%的沸石混合物、10-70重量%的耐热无机氧化物和0-60重量%的粘土,其中,以所述沸石混合物的总重量为基准,所述沸石混合物可以含有1-75重量%的改性β沸石和25-99重量%的具有mfi结构的沸石,优选含有10-70重量%的改性β沸石和30-90重量%的具有mfi结构的沸石,所述改性β沸石可以为磷和过渡金属m改性的β沸石。该改性β沸石可以采用各种常规方法进行制备,例如,可以在合成β沸石的过程中引入磷和过渡金属m,或者在合成β沸石后采用铵交换、磷改性、过渡金属m改性及焙烧处理等步骤来引入磷和所述过渡金属m。所述的过渡金属m可以选自fe、co、ni和cu中的一种或多种,优选为fe和/或cu。所述具有mfi结构的沸石可以为具有pentasil结构的高硅沸石,例如选自zsm-5和zrp系列沸石中的一种或多种。优选地,具有mfi结构的沸石为含稀土的zrp沸石(参见cn1052290a、cn1058382a、us5232675)、含磷的zrp沸石(参见cn1194181a、us5951963)、含磷和稀土的zrp沸石(参见cn1147420a)、含磷和碱土金属的zrp沸石(参见cn1211469a、cn1211470a、us6080698)以及含磷和过渡金属的zrp沸石(参见cn1465527a、cn1611299a)中的一种或多种。所述β沸石和所述具有mfi结构的沸石可以采用市售品,也可以采用本领域公知的各种方法进行制备,在此不再赘述。所述耐热无机氧化物可以选自sio2和/或al2o3。所述粘土可以为本领域常规使用的各种粘土,如高岭土和/或多水高岭土。为降低反应器中油气分压,在进行所述催化裂解反应的过程中可以向所述反应器中注入稀释剂,所述稀释剂可以为选自水蒸气、氮气和c1-c4烷烃中的一种或多种,优选为水蒸气,水蒸气与加氢生成油的重量比优选为(0.01-2):1。本发明还提供一种可用于本发明提供的催化裂解方法的催化裂解反应装置,包括提升管反应器、与提升管反应器串联的流化床反应器,流化床反应器反应管的直径与提升管反应区反应管的直径比可以为(2-6):1,提升管反应器上下依次设置第二喷嘴和第一喷嘴。所述提升管反应器可以为等直径提升管、等线速提升管和变直径提升管中的一种或几种,优选为等直径提升管。所述流化床反应器可以为散式流化床反应区、鼓泡床反应区或湍动床反应区的一种或几种。下面通过具体实施方式进一步说明本发明,但是并不因此而限制本发明。如图1所示,非加氢生成油通过第一喷嘴13进入提升管反应器1下部,与来自再生器5、再生剂输送管11和流量控制阀12的热再生催化剂接触进行第一催化裂解反应,第一反应产物与半待生催化剂继续提升,与经过第二喷嘴14引入的加氢生成油接触并进行第二催化裂解反应,期间可以通过蒸汽喷嘴15,所得反应物料通过提升管反应器1出口处的出口分布器16进入流化床反应器3进一步进行第三催化裂解反应;流化床反应器2中反应后的待生催化剂通过流化床反应器底部进入汽提器3,汽提后通过待生剂输送管31和流量控制阀32进入再生器5再生,流化床反应器2反应后的第二反应产物通过流化床反应器2的顶部进入沉降器4,再经旋风分离器除去其中携带的催化剂进入分馏装置分馏。另外,由于汽提器3与流化床反应器2气固连通,因此,通过调节汽提3向再生器5排出待生催化剂的流量控制阀32,可以直接控制流化床反应器2中催化剂的量,进而控制流化床反应器内反应的重时空速,由此可以增加催化裂解反应的工艺灵活度。再生器5再生后的催化剂通过再生剂输送管11引入提升管反应器1中。下面通过实施例来进一步说明本发明,但是本发明并不因此而受到任何限制。实施例及对比例中所用催化剂在800℃,用100%水蒸气老化12小时。使用中型试验装置,装置中催化剂的装量为60千克,提升管反应器1的内径为18毫米,高度为6米,流化床反应器3的内径为64毫米,高度为0.5米。实施例1本实施例所用催化剂组成如下:以干基计并以催化剂总重量为基准,含20重量%y沸石、10重量%zrp-1沸石、45重量%高岭土和25重量%的铝粘结剂。所述催化剂制备方法如下:将dasy沸石(含re2o32重量%,中石化催化剂齐鲁分公司产品)与zrp-1(中石化催化剂齐鲁分公司产品,含1.1重量%re2o3,1.2重量%p)用水打浆,制得固含量为30重量%的浆液,将高岭土(苏州中国高岭土公司出品)、拟薄水铝石(山东铝业公司出品)以及水混合打浆制备固含量30重量%浆液,将上述两种浆液混合,于50℃下搅拌30分钟得到催化剂浆液,将催化剂浆液喷雾干燥即得到催化剂。本实施例反应流程如图1所示,非加氢生成油(性质见表1)进提升管反应区1与来自再生器5的再生催化剂接触进行第一催化裂解反应后,第一反应产物与半待生催化剂继续提升,与引入的加氢生成油(性质见表2)继续接触第二催化裂解反应;反应后的油气和催化剂引至流化床反应器2的底部,并在流化床反应器2中进行第三催化裂解反应,反应后的第二待生催化剂从流化床反应器2的底部离开流化床反应器进入汽提器,第二反应产物从流化床反应器2的顶部离开,进入沉降器,分离出携带的催化剂后进入分馏装置;反应条件以及反应结果见表3。非加氢生成油与加氢生成油的比例为0.15。实施例2本实施例的流程同实施例1,不同的是,使用的催化剂为:以干基计并以催化剂的总重量为基准,所用催化剂含有15重量%的β沸石(中石化催化剂齐鲁分公司产品)、15重量%的zsm-5沸石(硅铝比为40)、45重量%的高岭土和25重量%的氧化铝粘结剂,其中,β沸石中含以元素计1重量%的铁和1.5重量%的磷;反应条件以及反应结果见表3。实施例3本实施例的流程同实施例1,不同的是,使用的催化剂为:以干基计并以催化剂的总重量为基准,所用催化剂含有20重量%的β沸石(中石化催化剂齐鲁分公司产品)、10重量%的zsm-5沸石(硅铝比为40)、45重量%的高岭土和25重量%的氧化铝粘结剂,其中,β沸石中含以元素计1.5重量%的铁和1.0重量%的磷;反应条件以及反应结果见表3。实施例4本实施例的流程同实施例4,不同的是,非加氢生成油与加氢生成油的比例为0.095。反应条件及结果见表3。实施例5本实施例的流程同实施例4,不同的是,非加氢生成油与加氢生成油的比例为0.21。反应条件及结果见表3。对比例1非加氢生成油(性质见表1)进提升管反应器1与来自再生器的再生催化剂接触反应后,反应后的油气和催化剂引至流化床反应器2的底部,并在流化床反应器2中进行反应,反应后的催化剂从流化床反应器2的底部离开流化床反应区进入汽提器,油气从流化床反应区2的顶部离开,进入沉降器,分离出携带的催化剂后进入分馏系统;催化剂同实施例3。反应条件以及反应结果见表4。对比例2同对比例1,所不同的是原料为加氢生成油(见表2)。反应条件及结果见表4。对比例3同实施例1,所不同的是非加氢生成油与加氢生成油的比例为0.04。反应条件及结果见表4。从表3-4可以看出,采用本发明的方法低碳烯烃产率高。表1项目非加氢生成油密度(20℃)/(克/厘米3)0.9008折光(70℃)1.4883运动粘度/(毫米2/秒)80℃39.95100℃22.31凝固点/℃44残炭/重量%5.05碱性氮/(毫克/千克)786四组分/重量%饱和烃58.0芳烃24.3胶质17.7沥青质<0.1元素分析/重量%c86.50h12.94s0.17n0.20金属分析/(微克/克)ca7.5cu0.5fe12.1na1.2ni8.1v1.0减压馏程,℃初馏点2865重量%36410重量%39030重量%45650重量%53256.9重量%546表2原料油名称加氢生成油密度(20℃)/(克/厘米3)0.8333运动粘度(80℃)/(毫米2/秒)4.579运动粘度(100℃)/(毫米2/秒)3.332凝点/℃32苯胺点/℃108.6残炭/%<0.05折光指数,(nd70)1.4408碱性氮/(微克/克)1.5元素组成/重量%c86.05h14.34n/(微克/克)<1s/(微克/克)7.2族组成/重量%饱和烃98.9芳烃0.8胶质0.3沥青质金属含量/(微克/克)ca0.7cu<0.1fe0.3na0.8ni<0.1v<0.1馏程/℃初馏点1925重量%26610重量%31630重量%38850重量%41370重量%43390重量%46895重量%492表3项目实施例1实施例2实施例3实施例4实施例5第一催化裂解反应条件进料量/(千克/小时)0.780.780.780.521.04反应温度/℃638638638645630油气停留时间/秒0.310.310.310.350.28剂油比77777711558第二催化裂解反应条件进料量/(千克/小时)5.225.225.225.484.96反应温度/℃582582582580584油气停留时间/秒1.821.821.821.791.82剂油比11.511.511.510.912.1第三催化裂解反应条件床层反应温度/℃562562562560564床层空速/小时-144444总注水(占总进料)/重量%2525252525物料平衡/重量%干气8.528.358.448.438.44液化气52.0653.8653.9754.553.48c5汽油26.0925.1425.9725.9425.95柴油4.954.473.423.253.76重油1.781.651.651.631.69焦炭6.66.536.556.256.68总计100100100100100气体产率/重量%乙烯产率5.125.155.35.335.23丙烯产率24.0124.9524.9224.6222.63丁烯产率15.9816.451716.7816.83乙烯+丙烯+丁烯45.1146.5547.2246.7344.69氢转移系数(异丁烷/异丁烯)1.101.091.011.171.16表4项目对比例1对比例2对比例3第一催化裂解反应条件进料量/(千克/小时)6.00/0.23反应温度/℃580/638油气停留时间/秒2.38/0.31剂油比10/260.9第二催化裂解反应条件进料量/(千克/小时)/6.005.77反应温度/℃/580585油气停留时间/秒/2.151.83剂油比/1010.40第三催化裂解条件反应温度/℃561564565重时空速/小时-1444总注水(占总进料)/重量%252525物料平衡/重量%干气8.568.438.45液化气42.1555.7453.92c5汽油25.4926.0425.89柴油10.922.073.02重油3.381.241.45焦炭9.56.487.27总计100100100气体产率/重量%乙烯产率4.354.94.71丙烯产率16.2520.4219.57丁烯产率10.3211.7613.17乙烯+丙烯+丁烯30.9237.0837.45氢转移系数(异丁烷/异丁烯)1.293.042.76当前第1页12