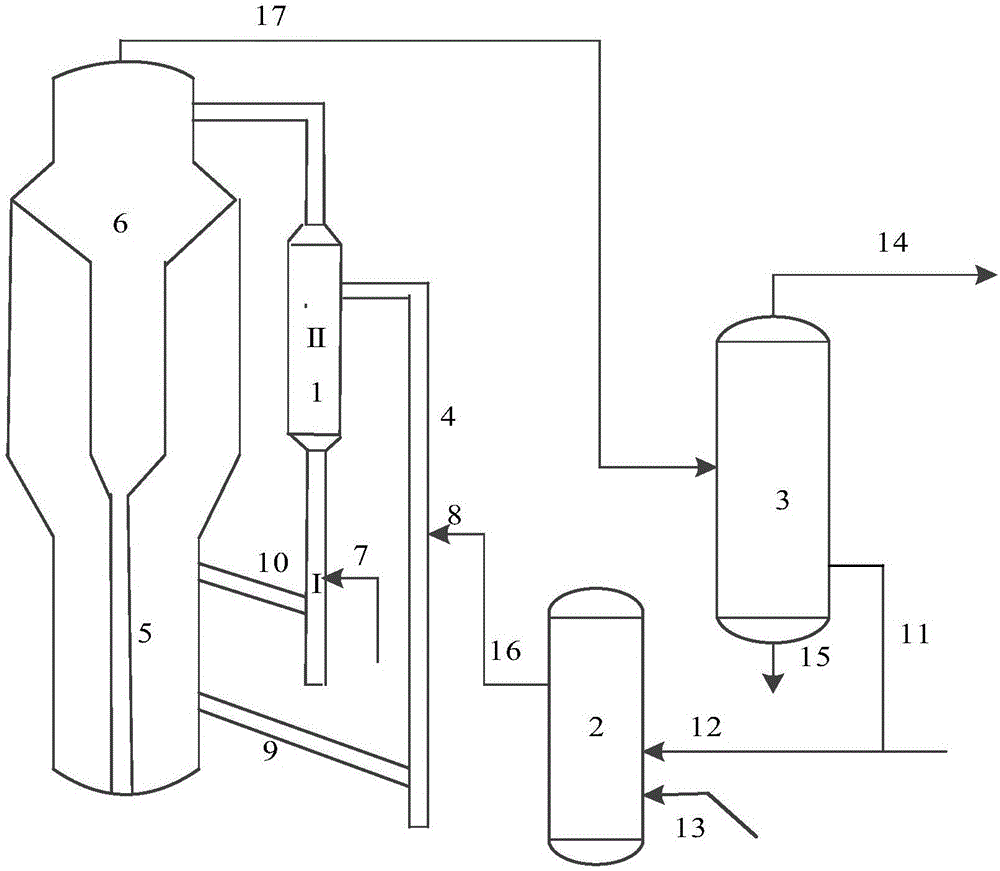
本发明涉及一种采用双提升管进行催化裂化的方法和系统。
背景技术:
:随着原油重质化发展和市场对轻质油品需求的快速增长,在我国,作为重油轻质化的催化裂化技术得到快速发展。然而,必须面对的一个事实是催化裂化柴油(或称轻循环油)的质量却一直相对较差,密度大,芳烃含量高,十六烷值低,即使通过柴油加氢改质技术也难以达到日益严格的柴油规格。如何解决催化裂化轻循环油是一个日益严峻的问题。同时存在的另一个问题是国内成品汽油长期短缺,而催化裂化汽油占成品汽油的80%。因此,如何通过催化裂化工艺来实现重质原料最大化生产高辛烷值汽油而不生产轻循环油可能是解决上述问题的新途径。美国专利us4585545批露了一种将催化裂化轻循环油全馏分先进行加氢处理,得到的加氢柴油再去催化裂化生产富含单环芳烃汽油的催化转化方法。中国专利cn14232327a公开了一种催化裂化循环油改质的方法,是将以重质油为原料的第一催化裂化装置生产的轻循环油进行深度加氢,得到的加氢循环油再进行第二催化裂化装置。在该方法的基础上,中国专利cn423689a强调第二催化裂化装置中的催化剂要求含50-95%的择形沸石和约5-50%的孔径大于或等于约0.7nm的大孔沸石,以选择性地提高轻烯烃产率。中国专利cn1466619a公开了一种催化裂化轻循环油的转化方法,是将催化裂化提升管反应器划分为上、下游两个反应区,其中重质油注入下游区,其催化裂化产物轻循环油经加氢处理后得到的加氢循环油注入上游区。在该方法的基础上,中国专利cn1425054a方法中下游区的进料除了加氢循环油外,还增加了石脑油。该方法中不仅氢耗高,而且加氢循环油在上游区反应会严重影响下游的重质油的转化。从上面公开的文献可以发现,对于催化裂化轻循环油进行加工的重要途径之一是将其先进行加氢处理,然后再催化裂化。必须指出的是,轻循环油无论是否加氢,和重质油大分子相比,其分子小、键能大,因此如何控制催化裂化的操作参数是轻循环油加工的关键之一。同时轻循环油如果进行加氢,加氢过程的操作控制也是轻循环油加工的关键之一。此外,重质石油烃催化裂化过程中最大化生产高辛烷值汽油而不生产轻循环油,则必须兼顾考虑如何实现重质石油烃和轻循环油的选择性催化裂化。技术实现要素:本发明的目的是提供一种采用双提升管进行催化裂化的方法和系统,本发明的方法和系统能够优化加氢轻循环油和重质原料的反应条件,缩短加氢轻循环油的反应时间,多产高辛烷值汽油。为了实现上述目的,本发明提供一种采用双提升管进行催化裂化的方法,该方法包括:将重质原料从第一喷嘴喷入主提升管反应器下部与来自主提升管反应器底部的第一催化裂化催化剂接触并进行第一催化裂化反应,得到第一反应产物和第一待生催化剂从主提升管反应器顶部开口送出;将所得第一反应产物送入产物分离装置进行分离,至少得到催化裂化汽油和催化裂化轻循环油;将催化裂化轻循环油送入加氢反应器中与加氢处理催化剂接触并进行加氢处理,得到加氢轻循环油;将加氢轻循环油从第二喷嘴送入副提升管反应器中与第二催化裂化催化剂接触并进行第二催化裂化反应,所得第二反应产物和第二待生催化剂;其中,所述副提升管反应器的顶部出口通过水平管连通于主提升管反应器中上部;将第二反应产物和第二待生催化剂送入所述主提升管反应器中上部与第一反应产物和第一待生催化剂一起从主提升管反应器顶部开口送出;将所得第一待生催化剂和第二待生催化剂送入再生器中进行烧焦再生,得到再生催化剂;将所得再生催化剂作为所述第一催化裂化催化剂和第二催化裂化催化剂分别送入所述主提升管反应器和副提升管反应器中;将第二反应产物和第一反应产物一起送入产物分离装置中进行分离。可选的,所述重质原料为选自直馏蜡油、焦化蜡油、脱沥青油、加氢精制油、加氢裂化尾油、减压渣油和常压渣油中的至少一种。可选的,所述第一催化裂化反应的条件包括:温度为450-550℃,第一催化裂化催化剂与重质原料的重量比为4-8,油气停留时间2-10秒,压力0.15-0.4兆帕,水蒸汽与重质原料的重量比为0.02-0.08,第一催化裂化催化剂的微反活性不低于60,所述微反活性采用ripp92-90催化裂化工业平衡催化剂的微反活性试验法进行测定。可选的,所述第一催化裂化催化剂和第二催化裂化催化剂各自独立地包括10-50重量%沸石、5-90重量%无机氧化物和0-70重量%的粘土,所述沸石为选自含或不含稀土的y、hy、usy和beta沸石的至少一种。可选的,所述主提升管反应器和副提升管反应器各自独立地为等径提升管反应器或变径提升管反应器。可选的,所述主提升管反应器由下至上同轴设置有第一反应段和第二反应段,所述第二反应段的内径大于第一反应段,所述副提升管反应器的出口通过水平管连通于所述第二反应段。可选的,所述加氢处理催化剂包括活性金属组分和载体,所述活性金属组分为第vib族金属和/或第viii族非贵金属,所述载体为选自氧化铝、二氧化硅和无定型硅铝中的至少一种。可选的,所述活性金属组分为镍-钨、镍-钨-钴、镍-钼或钴-钼。可选的,所述加氢处理的条件为:氢分压5.0-22.0兆帕,反应温度330-450℃,体积空速0.1-10.0小时-1,氢油体积比100-2000nm3/m3。可选的,所述加氢轻循环油中双环芳烃含量不大于20重%。可选的,所述第二催化裂化反应条件包括:反应温度为520-650℃,压力0.15-0.4兆帕,第二催化裂化催化剂与加氢轻循环油的重量比5-100,油气停留时间1-10秒,水蒸汽与加氢轻循环油的重量比为0.01-0.3,第二催化裂化催化剂的微反活性不低于60。本发明还提供一种采用双提升管进行催化裂化的系统,该系统包括主提升管反应器、加氢反应器、产物分离装置、副提升管反应器、再生器和沉降器;所述主提升管反应器设置有下部的原料入口、底部的催化剂入口和顶部的出口,所述副提升管反应器设置有下部的原料入口、底部的催化剂入口和顶部的出口,所述副提升管反应器的顶部出口通过水平管连通于主提升管反应器中上部;所述主提升管反应器的顶部出口与沉降器入口连通,沉降器的催化剂出口与所述再生器连通,所述沉降器的油气出口与所述产物分离装置入口连通,所述产物分离装置设置的轻循环油出口与所述加氢反应器入口连通,加氢反应器的加氢轻循环油出口与所述副提升管反应器的原料入口连通,所述再生器的催化剂出口与所述主提升管反应器催化剂入口和副提升管反应器的催化剂入口连通。可选的,所述主提升管反应器由下至上同轴设置有第一反应段和第二反应段,所述第二反应段的内径大于第一反应段,所述副提升管反应器的顶部出口通过水平管连通于所述第二反应段。本发明的优点在于:1、可以彻底实现重质原料催化裂化不产生轻循环油。2、采用催化裂化装置主、副提升管反应器分别加工重质原料和加氢轻循环油,可以通过采用不同的操作参数,最大限度地优化满足加氢轻循环油催化裂化所需的苛刻条件,同时副提升管反应器出口直接连通主提升管反应器的中上部,可以缩短加氢轻循环油反应时间的同时简化装置构造,从而最大程度地生产催化汽油。本发明的其他特征和优点将在随后的具体实施方式部分予以详细说明。附图说明附图是用来提供对本发明的进一步理解,并且构成说明书的一部分,与下面的具体实施方式一起用于解释本发明,但并不构成对本发明的限制。在附图中:图1包括本发明方法一种具体实施方式的流程示意图,也包括本发明系统一种具体实施方式的结构示意图。附图标记说明1主提升管反应器2加氢反应器3产物分离装置4副提升管反应器5再生器6沉降器7第一喷嘴8第二喷嘴9管线10管线11管线12管线13管线14管线15管线16管线17管线i第一反应区ii第二反应区具体实施方式以下结合附图对本发明的具体实施方式进行详细说明。应当理解的是,此处所描述的具体实施方式仅用于说明和解释本发明,并不用于限制本发明。本发明提供一种采用双提升管进行催化裂化的方法,该方法包括:将重质原料从第一喷嘴喷入主提升管反应器下部与来自主提升管反应器底部的第一催化裂化催化剂接触并进行第一催化裂化反应,得到第一反应产物和第一待生催化剂从主提升管反应器顶部开口送出;将所得第一反应产物送入产物分离装置进行分离,至少得到催化裂化汽油和催化裂化轻循环油;将催化裂化轻循环油送入加氢反应器中与加氢处理催化剂接触并进行加氢处理,得到加氢轻循环油;将加氢轻循环油从第二喷嘴送入副提升管反应器中与第二催化裂化催化剂接触并进行第二催化裂化反应,所得第二反应产物和第二待生催化剂;其中,所述副提升管反应器的顶部出口通过水平管连通于主提升管反应器中上部;将第二反应产物和第二待生催化剂送入所述主提升管反应器中上部与第一反应产物和第一待生催化剂一起从主提升管反应器顶部开口送出;将所得第一待生催化剂和第二待生催化剂送入再生器中进行烧焦再生,得到再生催化剂;将所得再生催化剂作为所述第一催化裂化催化剂和第二催化裂化催化剂分别送入所述主提升管反应器和副提升管反应器中;将第二反应产物和第一反应产物一起送入产物分离装置中进行分离。根据本发明,重油原料是本领域技术人员所熟知的,例如,所述重质原料可以为选自直馏蜡油、焦化蜡油、脱沥青油、加氢精制油、加氢裂化尾油、减压渣油和常压渣油中的至少一种,本领域技术人员也可以处理其他重质原料。根据本发明,还可以将外产催化裂化轻循环油进行加氢后作为所述加氢轻循环油送入副提升管反应器中进行反应,从而提高原料来源,多产高辛烷值汽油。根据本发明,催化裂化是本领域技术人员所熟知的,本发明不再赘述。所述第一催化裂化反应的条件可以包括:温度为450-550℃,第一催化裂化催化剂与重质原料的重量比为4-8,油气停留时间为2-10秒,压力(绝对压力)为0.15-0.4兆帕,水蒸汽与重质原料的重量比为0.02-0.08,第一催化裂化催化剂的微反活性不低于60,优选不低于62,所述微反活性采用ripp92-90催化裂化工业平衡催化剂的微反活性试验法进行测定(石油化工分析方法(ripp试验方法),杨翠定等编,1990版)。所述第二催化裂化反应条件可以包括:反应温度为520-650℃,优选为550-590℃,压力为0.15-0.4兆帕,第二催化裂化催化剂与加氢轻循环油的重量比为5-100,优选为8-50,油气停留时间为1-10秒,优选为2-8秒,水蒸汽与加氢轻循环油的重量比为0.01-0.3,优选为0.02-0.2,第二催化裂化催化剂的微反活性不低于60,优选不低于62。所述第一催化裂化催化剂和第二催化裂化催化剂可以各自独立地包括10-50重量%沸石、5-90重量%无机氧化物和0-70重量%的粘土,所述沸石可以为选自含或不含稀土的y、hy、usy和beta沸石的至少一种。所述主提升管反应器和副提升管反应器可以各自独立地为等径提升管反应器或变径提升管反应器,若主提升管反应器的高度为h,则主提升管反应器的中上部一般是指提升管反应器1/3h以上高度,优选为1/3h以上高度4/5以下高度。根据本发明,加氢处理是本领域技术人员所熟知的,例如,所述加氢处理催化剂可以包括活性金属组分和载体,所述活性金属组分可以为第vib族金属和/或第viii族非贵金属,所述活性金属组分优选为镍-钨、镍-钨-钴、镍-钼或钴-钼,所述载体可以为选自氧化铝、二氧化硅和无定型硅铝中的至少一种。所述加氢处理的条件可以为:氢分压为5.0-22.0兆帕,优选为8.0-15.0兆帕,反应温度为330-450℃,优选为340-380℃,体积空速为0.1-10.0小时-1,氢油体积比为100-2000nm3/m3。加氢处理所得产物,分离得到初馏点>250℃、优选>260℃的馏分,称加氢柴油或加氢轻循环油,所述加氢轻循环油中双环芳烃含量一般不大于20重%,优选不大于10重%。如图1所示,本发明还提供一种采用双提升管进行催化裂化的系统,该系统包括主提升管反应器1、加氢反应器2、产物分离装置3、副提升管反应器4、再生器5和沉降器6;所述主提升管反应器1设置有下部的原料入口、底部的催化剂入口和顶部的出口,所述副提升管反应器4设置有下部的原料入口、底部的催化剂入口和顶部的出口,所述副提升管反应器4的顶部出口通过水平管连通于主提升管反应器1中上部;所述主提升管反应器1的顶部出口与沉降器6入口连通,沉降器6的催化剂出口与所述再生器5连通,所述沉降器6的油气出口与所述产物分离装置3入口连通,所述产物分离装置3设置的轻循环油出口与所述加氢反应器2入口连通,加氢反应器2的加氢轻循环油出口与所述副提升管反应器4的原料入口连通,所述再生器5的催化剂出口与所述主提升管反应器1催化剂入口和副提升管反应器4的催化剂入口连通。一种实施方式,如图1所示,所述主提升管反应器1由下至上同轴设置有第一反应段i和第二反应段ii,所述第二反应段ii的内径大于第一反应段i,所述副提升管反应器4的顶部出口通过水平管连通于所述第二反应段ii。另外,第二反应段ii的上方可以同轴设置有出口段,出口段的内径可以小于第二反应段ii,出口段与沉降器6相连。下面结合附图通过具体实施方式来进一步说明本发明,但是本发明并不因此而受到任何限制。如图1所示,重质原料经第一喷嘴7进入主提升管反应器1中进行第一催化裂化反应,第一反应产物经管线17进入产物分离装置3,从产物分离装置3出来的催化裂化轻循环油经管线11、管线12进入加氢反应器2,氢气经管线13同时引入加氢反应器2,油浆从管线15送出,其他产物从管线14送出。加氢所得加氢轻循环油经管线16通过第二喷嘴8进入副提升管反应器4,在第二催化裂化催化剂存在下发生第二催化裂化反应,第二反应产物和第二待生催化剂进入主提升管反应器中上部与主提升管反应器中的物料汇合,然后经沉降器6分离后进入产物分离装置,待生催化剂经再生器5再生分别经管线10和管线9返回两个反应器。另外,主提升管反应器可以设置第一反应区i和扩径的第二反应区ii,副提升管反应器的出口设置有第二反应区ii中。下面的实施例将对本发明予以进一步说明,但并不因此而限制本发明。实施例中加氢反应器内装填的加氢处理催化剂商业牌号为rn-32v,保护剂商业牌号为rg-1,加氢处理催化剂和保护剂的装填体积比例为95:5,均由中国石化催化剂分公司生产。实施例、对比例中催化裂化装置使用的催化剂的物化性质见表1,其商业牌号为hac,由中国石化催化剂分公司生产。实施例、对比例中所使用的重质原料为90重量%直馏蜡油与10重量%减压渣油的混合原料,其性质列于表2。轻循环油的循环重量比=轻循环油加氢回炼的重量/重质原料的重量;汽油辛烷值测定法(研究法,ron)采用gb/t5487-2015方法进行测定,汽油辛烷值测定法(马达法,mon)采用gb/t503-2016方法进行测定。实施例1本实施例说明采用本发明图1提供的方法,具体流程如前所述,主提升管反应器为等径提升管,催化裂化装置的主要操作参数见表3。轻循环油进入中型加氢反应器,加氢处理的试验条件为:氢分压8.0兆帕,平均床层反应温度为360℃,体积空速0.5小时-1,氢油体积比1100nm3/m3。反应产品分布、氢耗及汽油辛烷值见表4。实施例2与实施例1基本相同,不同之处在于主提升管反应器为变径提升管,从下至上依次设置有预提升段、反应段、扩径段和出口段,反应段的反应条件为:温度为500℃,压力(绝对压力)为0.25兆帕,平衡催化剂活性为64,剂油重量比为6.1,油气停留时间为1.2秒,水蒸汽与原料重量比为0.06,轻循环油的循环重量比为0.07,扩径段的反应条件为:温度为490℃,油气停留时间为5秒。副提升管反应器的条件以及加氢条件同实施例1,反应产品分布、氢耗及汽油辛烷值见表4。对比例1对比例中1催化裂化装置只设置主提升管,不设置副提升管,轻循环油经加氢后的加氢轻循环油和重质原料混合后进入主提升管反应器。其中轻循环油的加氢条件同实施例1。对比例1中的催化裂化装置的操作条件见表3。反应产品分布、氢耗及汽油辛烷值见表4。对比例2对比例2中催化裂化装置常规的主副提升管装置,副提升管与主提升管并列排列并且顶部开口均直接与沉降器相连。轻循环油经过加氢后进入副提升管,其中轻循环油的加氢条件同实施例。对比例2中的催化裂化装置的操作条件见表3,反应产品分布、氢耗及汽油辛烷值见表4。从表4可以看出,本发明的方法和系统能够多产高辛烷值汽油。表1hac催化剂性质表2原料油性质表3操作参数表4项目实施例1实施例2对比例1对比例2氢耗,重量%1.431.402.532.30产品分布,重量%干气3.852.885.64.22液化气15.714.6321.516.3汽油69.370.5057.466.5轻循环油0000重油3.083.044.134.02焦炭8.078.9511.378.96合计100100100.0100汽油辛烷值ron95.694.892.593.6mon85.685.381.482.6当前第1页12