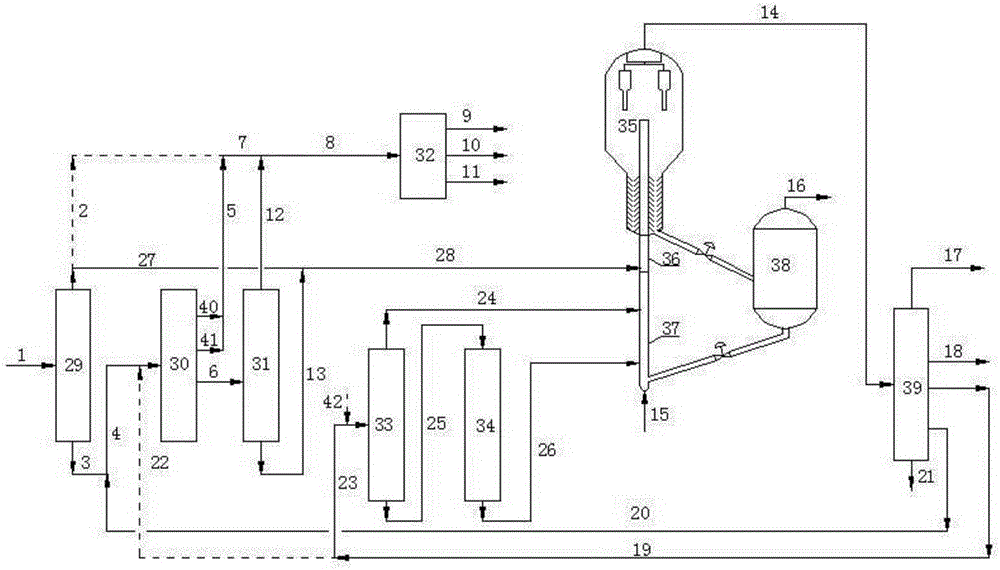
本发明涉及一种多产高辛烷值汽油和低碳烯烃的方法和系统。
背景技术:
:乙烯产业是我国化工行业发展的基础,是生产聚乙烯、环氧乙烷、二氯乙烷等重要化工产品的重要原料。制备乙烯主要以石脑油为原料,但面临着原料资源日趋紧张的问题。我国催化裂化工艺处理量近100mt/a,催化裂化产品在我国商品市场中占重要地位,催化裂化汽油占成品汽油池近80%的比例,但催化裂化汽油中硫、氮含量高、烯烃含量高;催化裂化轻循环油中硫、氮含量高、十六烷值低,只能作为一种质量较差的柴油调合组分或燃料油使用。因此,利用低成本的催化裂化原料进行一系列的预处理、生产清洁的高价值的催化裂化产品兼产乙烯等低碳烯烃具有重大经济效益和现实意义。中国专利cn103773495a公开了一种多产清洁高辛烷值汽油生产的催化转化方法。该方法是将蜡油和催化裂化循环油经加氢处理后送入催化裂化装置,经裂化反应得到干气、液化气、催化裂化汽油、lco、回炼油和油浆产品;催化裂化轻柴油采取自循环,催化裂化循环油循环至加氢处理装置,该方法能够大幅提高催化裂化汽油产品的收率和质量。中国专利cn101724431a公开了一种制取轻质燃料油和丙烯的催化转化方法,该方法将催化裂化蜡油经加氢处理或/和溶剂抽提,得到加氢后的催化蜡油或/和催化蜡油的抽余油作为催化裂化反应器的原料,经该方法处理后的催化裂化原料非常适合催化转化、实现了石油资源的高效利用。中国专利cn104927915a公开了一种以石脑油为原料生产烯烃和芳烃的方法,该方法通过将石脑油进行溶剂抽提得到抽出油和抽余油;抽出油经管线送入到蒸汽裂解装置、抽出油送入到催化重整装置,经重整反应得到的c3~c5馏分返回蒸汽裂解区进行裂解反应。该方法能够有效利用石脑油生产更多的低碳烯烃和轻质芳烃。从上述公开的文献中可以发现:催化裂化原料进行预处理能够有效降低催化裂化原料中硫、氮含量,同时胶质、沥青质和重质芳烃的含量也有效降低。充分基于原料的组成特点,通过不同加工工艺进行组合处理是提高原料的原子利用率的必要条件。但是现有方法,并没有能够在多产高辛烷值清洁催化裂化汽油的同时,能够实现兼产低碳烯烃和轻质芳烃的目的。技术实现要素:本发明的目的是提供一种多产高辛烷值汽油和低碳烯烃的方法和系统,本发明提供的方法和系统能够降低汽油产物中硫含量,提高汽油辛烷值,多产汽油和乙烯、丙烯等低碳烯烃。为了实现上述目的,本发明提供一种多产高辛烷值汽油和低碳烯烃的方法,该方法包括:将重质原料送入溶剂抽提装置进行溶剂抽提处理,得到抽出油和抽余油;将抽出油送入第一加氢装置与第一加氢催化剂接触并进行第一加氢处理,得到加氢石脑油、加氢柴油和加氢尾油;将所得加氢尾油送入第一分馏装置进行第一分馏,得到加氢尾油轻馏分和加氢尾油重馏分;将轻循环油送入第二分馏装置进行第二分馏,得到轻循环油轻馏分和轻循环油重馏分;将轻循环油重馏分送入第二加氢装置与第二加氢催化剂接触并进行第二加氢处理,得到第二加氢产物;将第二加氢产物从第一喷嘴送入提升管反应器的第一反应区的下部和将所述轻循环油轻馏分从第二喷嘴送入所述第一反应区的中部与催化裂化催化剂接触并进行第一催化裂化反应,得到第一产物和半待生催化剂;所述提升管反应器还设置有位于所述第一反应区上方的第二反应区;将所得第一产物和半待生催化剂送入第二反应区中与从第三喷嘴喷入所述第二反应区的所述抽余油和所述加氢尾油重馏分一起进行第二催化裂化反应,得到第二产物和待生催化剂;将第二产物进行分离,得到干气、液化气、汽油产物、轻循环油产物、回炼油产物和油浆;将所得轻循环油产物送入所述第二分馏装置中,将所得回炼油产物送入所述第一加氢装置中;将所述加氢石脑油、加氢柴油和加氢尾油轻馏分送入蒸汽裂解装置进行蒸汽裂解,得到蒸汽裂解产物。可选的,所述重质原料为选自减压蜡油、加氢减压蜡油、焦化蜡油、脱沥青油、常压渣油、减压渣油中的至少一种。可选的,所述溶剂抽提处理的条件包括:所述溶剂抽提装置为抽提塔,抽提溶剂从抽提塔塔顶进入抽提塔,重质原料自抽提塔塔底进入抽提塔,抽提塔的温度为50-70℃,抽提溶剂为糠醛,抽提溶剂与重质原料的重量比为(1-2):1。可选的,所述第一加氢处理的条件包括:氢分压为4-20兆帕,温度为330-450℃,液时体积空速为0.1-3.0小时-1,氢油体积比为250-1800nm3/m3。可选的,第一加氢催化剂包括载体和活性组分,该载体为选自氧化铝、二氧化硅和无定型硅铝中的至少一种,该活性组分为选自第vib族金属和/或第viii族非贵金属中的至少一种。可选的,所述第一分馏的温度为200-300℃,第二分馏的温度为220-270℃。可选的,所述第二加氢处理的条件包括:氢分压为3-30兆帕,温度为310-450℃,液时体积空速为0.1-10.0小时-1,氢油体积比为100-1500nm3/m3。可选的,所述第二加氢催化剂包括载体和活性组分,该载体为选自氧化铝、二氧化硅和无定型硅铝中的至少一种,该活性组分为选自第vib族金属和/或第viii族非贵金属中的至少一种。可选的,所述第一催化裂化反应的条件包括:反应温度为440-680℃,绝对反应压力为0.1-0.5兆帕,剂油重量比为1-50,反应时间为0.1-10秒,水油比为0.01-100;所述第二催化裂化反应的条件包括:反应温度为420-680℃,绝对反应压力为0.1-0.5兆帕,剂油重量比为1-50,反应时间为0.1-10秒,水油比为0.01-100。可选的,所述催化裂化催化剂包括沸石、无机氧化物和任选的粘土,所述沸石为选自含或不含稀土的y、hy、usy和beta沸石中的一种。可选的,所述提升管反应器为等径提升管反应器或变径提升管反应器。可选的,所述蒸汽裂解的温度为750-900℃。可选的,所述提升管反应器中的油气在第一喷嘴和第二喷嘴之间的停留时间为0.1-5秒。可选的,将至少部分所述轻循环油产物和/或外产轻循环油一起送入所述第一加氢装置进行第一加氢处理;所述轻循环油产物和/或外产轻循环油占所述第一加氢装置总进料的0-10重量%;和/或将至少部分抽余油送入所述蒸汽裂解装置进行所述蒸汽裂解。本发明还提供一种多产高辛烷值汽油和低碳烯烃的系统,该系统包括溶剂抽提装置、第一加氢装置、第一分馏装置、第二分馏装置、第二加氢装置、提升管反应器、沉降器、再生器、催化裂化分馏装置和蒸汽裂解装置;所述溶剂抽提装置设置有重质原料入口、抽出油出口和抽余油出口,所述第一加氢装置设置有入口、加氢石脑油出口、加氢柴油出口和加氢尾油出口,所述第一分馏装置设置有入口、加氢尾油轻馏分出口和加氢尾油重馏分出口,所述第二分馏装置设置有入口、轻循环油轻馏分出口和轻循环油重馏分出口,所述第二加氢装置设置有入口和加氢产物出口,所述提升管反应器由下至上设置有同轴且流体连通的第一反应区和第二反应区,所述第一反应区设置有催化剂入口、下部的第一喷嘴和中部的第二喷嘴,所述第二反应区设置有顶部出口和下部的第三喷嘴,所述沉降器套设在所述第二反应区的上部且第二反应区的顶部出口位于所述沉降器中,所述沉降器设置有顶部油气出口和下部催化剂出口,所述再生器设置有催化剂入口和催化剂出口,所述催化裂化分馏装置设置有入口和干气出口、液化气出口、汽油出口、轻循环油出口、回炼油出口和油浆出口,所述蒸汽裂解装置设置有入口和产物出口;所述溶剂抽提装置的抽出油出口、催化裂化分馏装置的回炼油出口和可选的催化裂化分馏装置的轻循环油出口与所述第一加氢装置的入口连通,所述第一加氢装置的加氢尾油出口与所述第一分馏装置的入口连通,所述催化裂化分馏装置的轻循环油出口与所述第二分馏装置的入口连通,所述第二分馏装置的轻循环油重馏分出口与所述第二加氢装置的入口连通,所述第二加氢装置的加氢产物出口与所述第一反应区下部的第一喷嘴连通,所述第二分馏装置的轻循环油轻馏分出口与所述第一反应区中部的第二喷嘴连通,所述溶剂抽提装置的抽余油出口和第一分馏装置的加氢尾油重馏分出口与所述第二反应区下部的第三喷嘴连通,所述沉降器的顶部油气出口与所述催化裂化分馏装置的入口连通,所述沉降器的催化剂出口与所述再生器的催化剂入口连通,所述再生器的催化剂出口与所述第一反应区的催化剂入口连通,所述第一加氢装置的加氢石脑油出口和加氢柴油出口、第一分馏装置的加氢尾油轻馏分出口以及可选的溶剂抽提装置的抽余油出口与所述蒸汽裂解装置的入口连通。本方法和系统的优点在于:1、本发明能够以重质原料、回炼油等为原料,生产低硫高清洁的催化裂化汽油,通过控制加氢深度能够控制催化裂化汽油中硫含量,同时汽油辛烷值得到提升。2、本发明充分根据物料的组成特点,采用多喷嘴不同位置进料,同时采用提升管反应不同反应区的不同单位操作参数控制,能够达到最大化生产清洁高辛烷值汽油的目的。3、本发明能够有效调节催化裂化装置的柴汽比,提高轻质油收率;兼产低碳烯烃。本发明的其他特征和优点将在随后的具体实施方式部分予以详细说明。附图说明附图是用来提供对本发明的进一步理解,并且构成说明书的一部分,与下面的具体实施方式一起用于解释本发明,但并不构成对本发明的限制。根据图示需要,非重要物流未在图中标出,但不限制本发明。在附图中:图1包括本发明方法一种具体实施方式的流程示意图,也包括本发明系统一种具体实施方式的结构示意图。附图标记说明1管线2管线3管线4管线5管线6管线7管线8管线9管线10管线11管线12管线13管线14管线15管线16管线17管线18管线19管线20管线21管线22管线23管线24管线25管线26管线27管线28管线29溶剂抽提装置30第一加氢装置31第一分馏装置32蒸汽裂解装置33第二分馏装置34第二加氢装置35沉降器36第二反应区37第一反应区38再生器39催化裂化分馏塔40管线41管线42管线具体实施方式以下结合附图对本发明的具体实施方式进行详细说明。应当理解的是,此处所描述的具体实施方式仅用于说明和解释本发明,并不用于限制本发明。本发明提供一种多产高辛烷值汽油和低碳烯烃的方法,该方法包括:将重质原料送入溶剂抽提装置进行溶剂抽提处理,得到抽出油和抽余油;将抽出油送入第一加氢装置与第一加氢催化剂接触并进行第一加氢处理,得到加氢石脑油、加氢柴油和加氢尾油;将所得加氢尾油送入第一分馏装置进行第一分馏,得到加氢尾油轻馏分和加氢尾油重馏分;将轻循环油送入第二分馏装置进行第二分馏,得到轻循环油轻馏分和轻循环油重馏分;将轻循环油重馏分送入第二加氢装置与第二加氢催化剂接触并进行第二加氢处理,得到第二加氢产物;将第二加氢产物从第一喷嘴送入提升管反应器的第一反应区的下部和将所述轻循环油轻馏分从第二喷嘴送入所述第一反应区的中部与催化裂化催化剂接触并进行第一催化裂化反应,得到第一产物和半待生催化剂;所述提升管反应器还设置有位于所述第一反应区上方的第二反应区;将所得第一产物和半待生催化剂送入第二反应区中与从第三喷嘴喷入所述第二反应区的所述抽余油和所述加氢尾油重馏分一起进行第二催化裂化反应,得到第二产物和待生催化剂;将第二产物进行分离,得到干气、液化气、汽油产物、轻循环油产物、回炼油产物和油浆;将所得轻循环油产物送入所述第二分馏装置中,将所得回炼油产物送入所述第一加氢装置中;将所述加氢石脑油、加氢柴油和加氢尾油轻馏分送入蒸汽裂解装置进行蒸汽裂解,得到蒸汽裂解产物。根据本发明,重质原料是本领域技术人员所熟知的,例如,所述重质原料可以为选自减压蜡油、加氢减压蜡油、焦化蜡油、脱沥青油、常压渣油、减压渣油中的至少一种。根据本发明,溶剂抽提用于将重质原料分离,得到抽出油和抽余油,从而分别进行合适的工艺进行处理,依据抽出油的组成和性质进入到第一加氢装置进行加氢处理,依据抽余油的组成和性质通过喷嘴进入到提升管反应器的适当位置,该方法能够有效降低焦炭含量,同时提高液体产品收率。所述溶剂抽提处理的条件可以包括:所述溶剂抽提装置为抽提塔,抽提溶剂从抽提塔塔顶进入抽提塔,重质原料自抽提塔塔底进入抽提塔,富含芳烃的抽出油和抽提溶剂从抽提塔塔底流出,送入到后续精制罐处理过后,抽提溶剂返回到抽提塔,精制罐底部得到抽出油和抽提溶剂,富含烷烃的抽余油和少许抽提溶剂从抽提塔塔顶流出,经汽提和蒸发后得到抽余油和抽提溶剂,抽提溶剂返回到抽提塔顶部,抽提塔的温度为50-70℃,优选55-65℃,抽提溶剂为糠醛,抽提溶剂与重质原料的重量比为(1-2):1。根据本发明,第一加氢处理用于将抽出油、回炼油产物和轻循环油产物中的芳烃进行饱和,以利于裂化,所述第一加氢处理的条件可以包括:氢分压为4-20兆帕,优选为6-18兆帕,温度为330-450℃,优选为350-420℃,液时体积空速为0.1-3.0小时-1,优选0.1-2.5小时-1,氢油体积比为250-1800nm3/m3,优选400-1700nm3/m3。第一加氢催化剂可以包括载体和活性组分,该载体可以为选自氧化铝、二氧化硅和无定型硅铝中的至少一种,该活性组分可以为选自第vib族金属和/或第viii族非贵金属中的至少一种。根据本发明,分馏处理用于分离馏分油,以利于进行后续处理,所述第一分馏的温度可以为200-300℃,优选210-270℃,第二分馏的温度可以为220-270℃,优选230-260℃。根据本发明,第二加氢处理用于饱和轻循环油重馏分中的芳烃,所述第二加氢处理的条件可以包括:氢分压为3-30兆帕,优选为4-20兆帕,温度为310-450℃,优选为320-420℃,液时体积空速为0.1-10.0小时-1,优选为0.5-5.0小时-1,氢油体积比为100-1500nm3/m3。所述第二加氢催化剂可以包括载体和活性组分,该载体可以为选自氧化铝、二氧化硅和无定型硅铝中的至少一种,该活性组分可以为选自第vib族金属和/或第viii族非贵金属中的至少一种。根据本发明,根据不同进料的特点可以采取不同的催化裂化条件,例如,所述第一催化裂化反应的条件可以包括:反应温度为440-680℃,优选480-600℃,绝对反应压力为0.1-0.5兆帕,优选0.10-0.3兆帕,剂油重量比为1-50,优选3-25,反应时间为0.1-10秒,即所述提升管反应器中的油气在第一喷嘴和第三喷嘴之间的停留时间为0.1-10秒,优选为0.5-6秒,水油比为0.01-100;所述提升管反应器中的油气在第一喷嘴和第二喷嘴之间的停留时间可以为0.1-5秒。所述第二催化裂化反应的条件可以包括:反应温度为420-680℃,优选460-580℃,绝对反应压力为0.1-0.5兆帕,优选0.10-0.30兆帕,剂油重量比为1-50,优选3-25,反应时间为0.1-5秒,水油比为0.01-100,优选0.02-0.5,优选0.02-0.5。所述催化裂化催化剂可以包括沸石、无机氧化物和任选的粘土,例如以干基计并以催化剂的干基重量为基准,沸石为5-50重量%,无机氧化物为10-90重量%,粘土为5-70重量%,所述沸石可以为选自含或不含稀土的y、hy、usy和beta沸石中的一种,无机氧化物可以为氧化硅和/或氧化铝。所述提升管反应器可以为等径提升管反应器或变径提升管反应器,反应器与再生器可以为高低并列式或同轴式。根据本发明,蒸汽裂解有助于提高轻质馏分油的进一步转化为低碳烯烃,所述蒸汽裂解的温度可以为750-900℃,优选790-840℃。根据本发明,为了有效利用轻循环油,可以将至少部分所述轻循环油产物和/或外产轻循环油一起送入所述第一加氢装置进行第一加氢处理;所述轻循环油产物和/或外产轻循环油占所述第一加氢装置总进料的0-10重量%;和/或将至少部分抽余油送入所述蒸汽裂解装置进行所述蒸汽裂解。如图1所示,本发明还提供一种多产高辛烷值汽油和低碳烯烃的系统,该系统包括溶剂抽提装置29、第一加氢装置30、第一分馏装置31、第二分馏装置33、第二加氢装置34、提升管反应器、沉降器35、再生器38、催化裂化分馏装置39和蒸汽裂解装置32;所述溶剂抽提装置29设置有重质原料入口、抽出油出口和抽余油出口,所述第一加氢装置30设置有入口、加氢石脑油出口、加氢柴油出口和加氢尾油出口,所述第一分馏装置31设置有入口、加氢尾油轻馏分出口和加氢尾油重馏分出口,所述第二分馏装置33设置有入口、轻循环油轻馏分出口和轻循环油重馏分出口,所述第二加氢装置34设置有入口和加氢产物出口,所述提升管反应器由下至上设置有同轴且流体连通的第一反应区37和第二反应区36,所述第一反应区37设置有催化剂入口、下部的第一喷嘴和中部的第二喷嘴,所述第二反应区36设置有顶部出口和下部的第三喷嘴,所述沉降器35套设在所述第二反应区36的上部且第二反应区36的顶部出口位于所述沉降器35中,所述沉降器35设置有顶部油气出口和下部催化剂出口,所述再生器38设置有催化剂入口和催化剂出口,所述催化裂化分馏装置39设置有入口和干气出口、液化气出口、汽油出口、轻循环油出口、回炼油出口和油浆出口,所述蒸汽裂解装置32设置有入口和产物出口;所述溶剂抽提装置29的抽出油出口、催化裂化分馏装置39的回炼油出口和可选的催化裂化分馏装置39的轻循环油出口与所述第一加氢装置30的入口连通,所述第一加氢装置30的加氢尾油出口与所述第一分馏装置31的入口连通,所述催化裂化分馏装置39的轻循环油出口与所述第二分馏装置33的入口连通,所述第二分馏装置33的轻循环油重馏分出口与所述第二加氢装置34的入口连通,所述第二加氢装置34的加氢产物出口与所述第一反应区37下部的第一喷嘴连通,所述第二分馏装置33的轻循环油轻馏分出口与所述第一反应区37中部的第二喷嘴连通,所述溶剂抽提装置29的抽余油出口和第一分馏装置31的加氢尾油重馏分出口与所述第二反应区36下部的第三喷嘴连通,所述沉降器35的顶部油气出口与所述催化裂化分馏装置39的入口连通,所述沉降器35的催化剂出口与所述再生器38的催化剂入口连通,所述再生器38的催化剂出口与所述第一反应区37的催化剂入口连通,所述第一加氢装置30的加氢石脑油出口和加氢柴油出口、第一分馏装置31的加氢尾油轻馏分出口以及可选的溶剂抽提装置29的抽余油出口与所述蒸汽裂解装置32的入口连通。需要说明的是,本发明系统中各装置不限于设置上述入口和出口,还可以设置本领域技术人员所熟知的其它入口和出口,本发明不再赘述。下面结合图1对本发明提供的具体实施方法方式予以进一步说明。来自管线1的重质原料送入到溶剂抽提装置29,经处理后得到抽出油和抽余油,来自管线3的抽出油、管线20的回炼油产物和来自管线22的轻循环油产物在氢气存在的条件下从管线4送入到第一加氢装置30进行第一加氢处理,处理得到的加氢尾油经管线6送入到第一分馏装置31,经馏分切割得到加氢尾油重馏分和加氢尾油轻馏分两种馏分,加氢尾油重馏分经管线13与来自管线27的抽余油通过管线28送入到提升管反应器的第二反应区中进行第二催化裂化反应,来自管线12的加氢重油轻馏分、来自管线40加氢石脑油、来自管线41的加氢柴油和可选的来自管线2的抽余油从管线7和管线8一起送入到蒸汽裂解装置32,得到产物从管线9、管线10和管线11送出。轻循环油产物送入到第二分馏装置33进行馏分切割,得到轻循环油轻馏分和轻循环油重馏分;轻循环油轻馏分经管线24送入到提升管反应器的第一反应区37的中部,轻循环油重馏分经管线25送入到第二加氢装置34,进行第二加氢处理后送入到提升管反应的第一反应区37的下部,在催化裂化催化剂作用下发生第一催化裂化反应,经处理得到包括干气、液化气、汽油产物、轻循环油产物、回炼油产物和油浆。轻循环油产物分成两股物料循环,一股物料(该股物料占催化裂化轻循环油总循环量的0-20重量%)经管线19和管线22循环至第一加氢装置30,另一股物料经管线19和管线23循环至第二分馏装置33,或与可选的来自管线42的外来催化裂化轻循环油混合后进入第二分馏装置33。以下实施例对本发明予以进一步的说明,但实施例对本发明没有任何限制。本发明中,汽油辛烷值测定法(研究法,ron)采用gb/t5487-2015方法进行测定,汽油辛烷值测定法(马达法,mon)采用gb/t503-2016方法进行测定。汽油硫含量采用sh/t0689-2000进行测定。实施例1本实施例采用本发明提供的方法。如图1所示,性质见表1的减压蜡油送入到溶剂抽提装置29,经抽提得到抽出油和抽余油;抽出油、占轻循环油总循环量5重量%的轻循环油和回炼油与氢气混合后送入到第一加氢装置30进行第一加氢处理,得到包括气体、加氢石脑油、加氢柴油和加氢尾油。加氢尾油送入第一分馏装置31进行第一分馏得到加氢尾油轻馏分和加氢尾油重馏分,加氢尾油轻馏分、加氢石脑油和加氢柴油混合送入到蒸汽裂解装置32,占轻循环油总循环量95重量%的轻循环油送入第二分馏装置33进行第二分馏,得到轻循环油轻馏分和轻循环油重馏分,轻循环油轻馏分送入到提升管反应器的第一反应区37的中部,轻循环油重馏分经第二加氢处理后送入到提升管反应器的第一反应区37的下部,一起在催化裂化催化剂作用下发生第一催化裂化反应,得到半待生催化剂和第一反应产物送入第二反应区36中与来自溶剂抽提装置29的抽余油和加氢尾油重馏分一起进行第二催化裂化反应,分离待生催化剂和第二反应产物,经处理得到包括干气、液化气、汽油产物、轻循环油产物、回炼油产物和油浆。回炼油产物循环送入到第一加氢装置30;轻循环油产物循环至第二分馏装置33。所述溶剂抽提装置为抽提塔,抽提溶剂从抽提塔塔顶进入抽提塔,重质原料自抽提塔塔底进入抽提塔,抽提塔的温度为60℃,抽提溶剂为糠醛,抽提溶剂与重质原料的重量比为1:1;轻循环油分馏装置的轻、重两种馏分在第二分馏装置中第二分馏的切割温度控制在260℃;第一分馏装置的第一分馏的切割温度控制在230℃;蒸汽裂解装置温度控制在810℃。实施例中对重馏分进行第二加氢处理的固定床反应器内装填的加氢处理催化剂商业牌号是rn-23v,保护剂商业牌号是rg-1,加氢处理催化剂和保护剂的装填体积比为95:5,均由中国石化催化剂分公司生产。实施例中对抽出油进行的第一加氢处理在双反应器中进行,第一反应器中装填加氢保护剂和加氢脱金属催化剂,在第二反应器总装填加氢脱硫催化剂,三者比例为5:45:50,其中加氢保护剂、加氢脱金属催化剂、加氢脱硫催化剂的商品牌号分别是rg-20b、rdm-33和rms-30。实施例中催化裂化装置采用的催化剂商品牌号是cgp-1。加氢装置操作条件见表2,催化裂化操作条件见表3,蒸汽裂解产品分布4,催化裂化产品分布见表5。对比例1本实施例的溶剂抽提装置、第一加氢装置、第一分馏装置操作参数同实施例1,只是全部轻循环油未经第二分馏和第二加氢直接进入到提升管反应器第一反应区下部。加氢装置操作条件见表2,催化裂化操作条件见表3,蒸汽裂解产品分布4,催化裂化产品分布见表5。从表4-5可以看出,本发明的方法能够降低汽油产物中硫含量,提高汽油辛烷值,多产汽油和乙烯、丙烯等低碳烯烃。表1重质原料性质原料油名称减压蜡油密度(20℃),千克/米3932.1馏程,℃初馏点25650重量%35795重量%585质谱法烃类组成,重量%链烷烃18.4总环烷烃24.9总芳烃55.3胶质1.3表2加氢装置操作条件项目第一加氢装置30第二加氢装置34反应条件氢分压,兆帕6.515体积空速,小时-11.20.9反应温度,℃360380氢油体积比,nm3/m31100700表3催化裂化操作条件表4蒸汽裂解产品分布实施例1对比例1气体产品收率,重量%氢气0.430.45一氧化碳0.030.06甲烷13.9214.10乙烷3.123.43乙烯33.5632.71乙炔0.460.55丙烷0.820.78丙烯18.1517.35丙炔0.190.21丙二烯0.240.25异丁烷0.050.06正丁烷0.130.131-丁烯4.354.15丁二烯6.505.73酸性气体0.040.05液体产品收率,重量%裂解汽油14.2715.67轻柴油1.341.60燃料油2.402.72总计100.00100.00乙烯+丙烯,重量%51.7150.06表5催化裂化产品分布实施例1对比例1产物分布,重%干气4.895.12液化气20.1221.42汽油58.5656.26柴油0.000.00油浆8.679.49焦炭7.658.55损失0.110.16合计100.00100.00乙烯+丙烯,重量%8.127.15汽油辛烷值mon93.192.7ron81.280.3汽油硫含量,微克/克1825当前第1页12