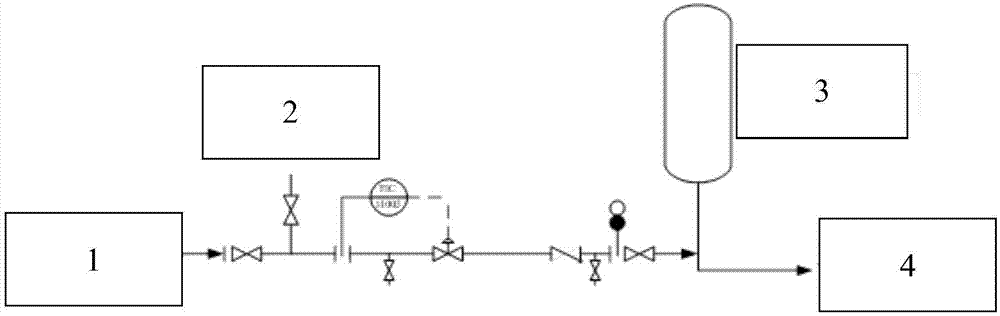
本发明涉及一种阻燃剂的使用方法,具体涉及一种shyz-1加氢催化剂阻燃剂的使用方法,属于化工
技术领域:
。
背景技术:
:加氢裂化技术是石油炼制中最为重要的二次加工技术之一,原料适应性强、产品方案灵活,能在石油轻质化的过程中直接生产质量优异的清洁油品。加氢裂化的核心是催化剂,而加氢裂化催化剂的级配技术则是加氢裂化技术升级发展的关键所在。国内中、高压加氢裂化和中压加氢改质工艺中催化剂的级配主要分为两类:一是精制催化剂和裂化剂的级配使用;二是不同裂化剂的级配使用。前者不仅可以提高装置对劣质原料的适应能力,而且可以根据不同油品性质灵活调整适宜的加工方案;后者主要是在原料性质相似的情况下,通过裂化剂的级配,提高裂化段整体活性,调整裂化产品的分布,多产高附加值油品,降低能耗。催化剂级配使用的重要影响因素是原料性质和加工方案,催化剂级配技术将是未来加氢裂化的发展方向,为催化剂的升级换代争取了更多宝贵时间。(《中外能源》,2015,20(11):79-85作者姜维,金爱军)加氢催化剂常见处理方法:器内再生存在周期长、费用高、易腐蚀等缺点,适于重复使用。惰性气保护卸剂(氮气),无氧操作具有一定风险,需特殊作业,适用于器外再生或报废催化剂。水或者苏打水喷淋卸剂,适用于报废催化剂。中国发明专利《一种加氢裂化催化剂的硫化剂及制备方法》申请号:201410275506.3,介绍了石油加工
技术领域:
,一种加氢裂化催化剂的硫化剂及制备方法;硫化剂是由二硫化碳、溶剂油或石油馏分油、抗氧剂、阻燃剂、降凝剂、分散剂组成。在氮气保护和常温、常压下,在轻度搅拌下依次加入溶剂油、二硫化碳及分散剂、降凝剂、抗氧剂、阻燃剂等物质,制得含二硫化碳的复配新型硫化剂。解决了常用硫化剂二硫化碳自然点低、挥发性强问题,使用时不需水封,操作安全、简便;可以替代二甲基二硫,无明显气味,能显著降低硫化剂成本,适于推广应用。上述技术虽然有了改进,但是还有缺点:渣油加氢装置经过长周期运行,因渣油加氢催化剂上沉积了太多的硫化亚铁,卸催化剂时催化剂接触空气发生自燃现象。shyz-1加氢催化剂阻燃剂是用于加氢装置卸剂时防止催化剂自燃的一种钝化剂。由于催化剂在使用状态为硫化态,因此在卸剂接触空气时极易引起自燃,本阻燃剂能够在催化剂表面形成一种保护膜来阻止催化剂和空气的接触,以防止自燃。技术实现要素:本发明的目的在于,提供一种shyz-1加氢催化剂阻燃剂的使用方法,以克服现有技术所存在的上述缺点和不足。申请人将该技术应用到中国石油化工股份有限公司石家庄炼化分公司150万吨/年渣油加氢装置催化剂卸剂工程中,使反应器内的催化剂钝化后,阻止硫化亚铁的自燃。本发明所需要解决的技术问题,可以通过以下技术方案来实现:一种shyz-1加氢催化剂阻燃剂的使用方法,其特征在于,包括以下步骤:(1)降温降量;(2)蜡油油置换;(3)柴油置换;(4)注阻燃剂;(5)成膜;(6)气体冷却置换。其中,步骤(1)降温降量:以每小时15-20℃的速度,将反应器床层温度首先从操作温度降至350℃;降温所需时间约3小时,同时反应器的进料逐步降至200t/h。进一步,反应系统压力以每小时1-1.5mpa/h降至14.0mpa。其中,步骤(2)蜡油油置换:当反应器温度降至350℃后,从开工直馏蜡油管线以50t/h的速度引入蜡油,置换反应系统渣油,稳定后逐步提高蜡油量至泵的最大量200t/h,并相应降低渣油进量至零;反应系统在320℃进行循环18小时;同时在循环期间及时联系质检中心分析热低分油组分含量,当大于538℃组分小于5%时表明置换完成,如第一次分析不符合要求,每隔2小时再联系质检中心进行分析,直至热低分油大于538℃组分小于5%;蜡油油置换大约22小时。进一步,蜡油置换合格后,继续以15℃~20℃/h的降温速度降低反应器温度至290℃,反应系统压力以每小时1-1.5mpa/h降至12.0mpa。其中,步骤(3)柴油置换:以50t/h速度引柴油置换反应系统,逐步提高柴油进料量至泵的最大量(200t/h),并进行循环;同时将反应温度继续以5℃/h的速度向220℃降温;同时联系质检中心分析热低分油的组分含量,柴油置换大约9小时。当温度降至220℃以下,并且置换合格后(50℃粘度小于12cst),从反应进料泵入口管线注入shyz-1加氢催化剂阻燃剂,混合油置换所需时间约30小时。进一步,所述混合油为蜡油和柴油的混合物,其重量份数比为1~10:1~100。其中,步骤(4)注shyz-1加氢催化剂阻燃剂在注剂之前测定反应系统循环油的粘度是否合格,并保持反应系统循环最大量200t/h;由于yshz-1阻燃剂在常温粘度较大,为注剂操作顺利进行,在注剂之前,应当用低压蒸汽将shyz-1加氢催化剂阻燃剂加热约8小时;用临时注剂设备在循环线路的低压部,即进料泵入口,注剂,注剂前,用yshz-1置换注剂管线内的气体;循环流量:最大量200t/h,阻燃剂使用量:30桶,注入时间:2小时,准备时间:1小时,合计:3小时,注剂完成后用2桶柴油lgo冲洗注剂设备后,将注剂管线内的shyz-1加氢催化剂阻燃剂也压送到循环系统内;在注剂过程中,将反应器床层温度从220℃降温到170℃左右。其中,步骤(5)成膜:加注完shyz-1加氢催化剂阻燃剂后,反应系统温度保持170℃闭路循环12个小时,对催化剂进行表面钝化处理,使催化剂表面上形成一层约10微米的薄膜;系内油量:700kl,循环时间:12小时,如果系统压降较大,可以适当降低循环油流量,同时相应延长成膜时间;进一步,催化剂进行表面钝化处理结束,油循环停止的二条件为:5.1、油已经循环12小时以上;5.2、催化剂温度已降到170℃以下;5.3、最终油粘度小于12cst@50度。其中,步骤(6)气体冷却置换:油循环冷却停止后,应继续气体循环冷却;同时,将催化剂内、管道内以及装置里的油吹洗出去;油在140度循环停止后,不要停留在此温度上,应尽快由循环气体对催化剂继续冷却降温;在140℃高温下停留时间过长>4小时,将会对催化剂表面成膜效果有影响;在降温过程中,根据反应器材质的冷脆温度,参照附录施工方案图,开始系统降压;当反应器器壁温度降到120℃以下时,反应器内的压力不应高于40kg/cm2。进一步,为加速反应器催化剂床层的冷却,可以釆用以下措施:(1)循环气体系统尽可能保持高的系统压力;(2)循环气体压缩机以最大流量运转;(3)空冷式热交换器通风口全开;(4)加热炉通风量开到最大;(5)尽可能早地停止醇胺液(破化氢吸收液)循环;(6)为均勾地减低前后反应器内催化剂温度,反应器以从后往前的顺序加入冷氢,其流量从后往前逐渐减少;在冷却过程中,导入氮气对改善循环气体压缩机的运转是有利的。但是,导入氮气后,系统压降将上升,气体压缩比的增大将导致压缩机出口温度的上升;实践已经证明,釆用氮气冷却,将会使催化剂冷却总时间变长;当反应器床层温度降到50℃度以下时,停止循环气体压缩机运转;约需要冷却时间为:84小时;反应器冷却完成后,根据贵公司装置操作规程,开始对系统泄压;然后进行氮气置换、测定反应器内气体的lel,co,h2s等成分,直至满足生产的要求。本发明的有益效果:1、本发明的阻燃剂具有良好的阻燃效果,可有效地抑制卸剂过程中反应后加氢催化剂自燃的发生。2、推荐阻燃剂的使用量为系统内循环油量的3%,循环时间为二个周期。n2、h2汽提温度275℃,汽提时间8小时。3、本发明的阻燃剂对催化剂再生后的物化性能和再生活性没有不良影响,对不再生的催化剂活性也没有不良影响。4、本发明的阻燃剂的应用减少了催化剂卸剂和再生过程中的破损,提高了催化剂的再生利用率。5、适当降低热氢汽提温度和氮气置换温度,对停工过程和加氢设备没有不良影响。附图说明图1为阻燃剂注入的示意图。图2待生催化剂经阻燃剂处理前后。图3为275℃h2和n2汽提后的阻燃效果。图4为300℃h2和n2汽提后阻燃效果。图5为370℃h2和n2汽提后阻燃效果。附图标记:1为阻燃剂、2为硫化剂p、3为滤后缓冲罐、4为反应进料泵。具体实施方式以下结合具体实施例,对本发明作进一步说明。应理解,以下实施例仅用于说明本发明而非用于限定本发明的范围。实施例1装置基本数据1、系统内存油量循环系统内存油量=(原料罐、分离器、塔通常液位以下的体积)+(换热器、管道体积)+(反应器内催化剂体积*30%)=678.6kl(m3)2、运载油减压蜡油+柴油3、进料流量进料流量180,000-200,000nm3/hr降量速度25t/h4、系统压力正常操作压力16.6mpa反应器冷脆温度和压力93.3℃,48mpa泄压速度小于1.5mpa/hr5、温度反应操作最高温度410℃降温速度小于20℃/h6、循环气体循环气体流量180,000-200,000nm3/hr7、催化剂床层最高温度催化剂床层最终温度小于50℃(循环氢出口温度80度)图1为阻燃剂注入的示意图,1为阻燃剂自阳申自带设备、2为硫化剂p、3为滤后缓冲罐、4为反应进料泵。如图1所示,一种shyz-1加氢催化剂阻燃剂的使用方法,包括以下步骤:1、降温降量,2、蜡油油置换,3、柴油置换,4、注shyz-1加氢催化剂阻燃剂,5、成膜,6、气体冷却置换(赶油)。表1yshz-1催化剂表面成膜钝化处理操作步骤总时间约134小时,分为6个步骤序号工艺处理步骤时间(h)备注1降温降量42蜡油油置换223柴油置换94注shyz-1加氢催化剂阻燃剂35成膜126气体冷却(赶油)84合计1341、降温降量以每小时15-20℃的速度,将反应器床层温度首先从操作温度降至350℃。降温所需时间约3小时,同时反应器的进料逐步降至200t/h。反应系统压力以每小时1-1.5mpa/h降至14.0mpa。2、蜡油油置换当反应器温度降至350℃后,从开工直馏蜡油管线以50t/h的速度引入蜡油,置换反应系统渣油,稳定后逐步提高蜡油量至泵的最大量(200t/h),并相应降低渣油进量至零。反应系统在320℃进行循环18小时。同时在循环期间及时联系质检中心分析热低分油组分含量,当大于538℃组分小于5%时表明置换完成,如第一次分析不符合要求,每隔2小时再联系质检中心进行分析,直至热低分油大于538℃组分小于5%。蜡油油置换大约22小时。蜡油置换合格后,继续以15℃~20℃/h的降温速度降低反应器温度至290℃,反应系统压力以每小时1-1.5mpa/h降至12.0mpa。3、柴油置换以50t/h速度引柴油置换反应系统,逐步提高柴油进料量至泵的最大量(200t/h),并进行循环。同时将反应温度继续以5℃/h的速度向220℃降温。同时联系质检中心分析热低分油的组分含量,柴油置换大约9小时。当温度降至220℃以下,并且置换合格后(50℃粘度小于12cst),从反应进料泵入口管线注入yshz-1阻燃剂,油(蜡油和柴油)置换所需时间约30小时。4、注shyz-1加氢催化剂阻燃剂在注剂之前测定反应系统循环油的粘度是否合格,并保持反应系统循环最大量(200t/h)。由于shyz-1加氢催化剂阻燃剂在常温粘度较大,为注剂操作顺利进行,在注剂之前,应当用低压蒸汽将阻燃剂加热约8小时。用临时注剂设备在循环线路的低压部(进料泵入口)注剂,注剂前,用yshz-1置换注剂管线内的气体。循环流量:最大量(200t/h)阻燃剂使用量:30桶注入时间:2小时准备时间:1小时合计:3小时注剂完成后用2桶柴油(lgo)冲洗注剂设备后,将注剂管线内的yshz-1阻燃剂也压送到循环系统内。在注剂过程中,将反应器床层温度从220℃降温到170℃左右。5、成膜加注完yshz-1阻燃剂后,反应系统温度保持170℃闭路循环12个小时,对催化剂进行表面钝化处理,使催化剂表面上形成一层约10微米的薄膜。系内油量:700kl循环时间:12小时如果系统压降较大,可以适当降低循环油流量,同时相应延长成膜时间。催化剂进行表面钝化处理结束,油循环停止的二条件为:5.1、油已经循环12小时以上;5.2、催化剂温度已降到170℃以下;5.3、最终油粘度小于12cst@50度;6、气体冷却置换(亦称为赶油)油循环冷却停止后,应继续气体循环冷却。同时,将催化剂内、管道内以及装置里的油吹洗出去。油在140度循环停止后,不要停留在此温度上,应尽快由循环气体对催化剂继续冷却降温。在140℃高温下停留时间过长(>4小时),将会对催化剂表面成膜效果有影响。在降温过程中,根据反应器材质的冷脆温度,参照附录施工方案图,开始系统降压。当反应器器壁温度降到120℃以下时,反应器内的压力不应高于40kg/cm2。为加速反应器催化剂床层的冷却,可以釆用以下措施:(1)循环气体系统尽可能保持高的系统压力;(2)循环气体压缩机以最大流量运转;(3)空冷式热交换器通风口全开;(4)加热炉通风量开到最大;(5)尽可能早地停止醇胺液(破化氢吸收液)循环;(6)为均勾地减低前后反应器内催化剂温度,反应器以从后往前的顺序加入冷氢,其流量从后往前逐渐减少;在冷却过程中,导入氮气对改善循环气体压缩机的运转是有利的。但是,导入氮气后,系统压降将上升,气体压缩比的增大将导致压缩机出口温度的上升。实践已经证明,釆用氮气冷却,将会使催化剂冷却总时间变长。当反应器床层温度降到50℃度以下时,停止循环气体压缩机运转。约需要冷却时间为:84小时反应器冷却完成后,根据贵公司装置操作规程,开始对系统泄压。然后进行氮气置换、测定反应器内气体的lel,co,h2s等成分,直至满足生产的要求。图2待生催化剂经阻燃剂处理前后。图3为275℃h2和n2汽提后的阻燃效果。图4为300℃h2和n2汽提后阻燃效果。图5为370℃h2和n2汽提后阻燃效果。从图2~图5,汽提温度对阻燃效果的影响,275℃至300℃条件下,阻燃剂可以表现出较好的阻燃效果。370℃条件下,阻燃效果严重下降。如果加氢装置停工过程中需要热氢汽提或热氮脱氢,温度不要超过275℃。表2不同汽提条件对催化剂含油量的影响汽提时间达到8小时后,催化剂含油量符合器外再生时催化剂含油量不大于2%的要求。表3阻燃剂对催化剂物化性能的影响7、阻燃剂处理后再生的催化剂物化性能阻燃剂处理过的催化剂经再生后各项物化性能与未经阻燃剂处理过而直接再生的催化剂基本没有差别未经阻燃剂处理过的催化剂再生的破损率为3—6%,而经阻燃剂处理过的催化剂的破损率几乎为零,提高了催化剂的再生利用率。渣油加氢装置阻燃剂主要技术指标(1)渣油加氢装置经过长周期运行,因渣油加氢催化剂上沉积了太多的硫化亚铁,为防止卸催化剂时催化剂接触空气发生自燃,在装置停工前用成膜剂进行油闭路循环,在催化剂表面形成膜,经成膜后的催化剂在空气中不发生自燃现象。(2)物性参考指标:见表4。表4物性参考指标项目指标燃点,℃≥165凝点,℃≤15水分,%(体积分数)痕迹运动粘度(50℃),mm2/s≥35硫含量,%(质量分数)≤0.5密度(20℃),kg/m31020~1050铜片腐蚀,级≤1关键组份:脂肪烃+缩环烃,wt%100(3)加入方式:加注点在原料泵前,直接注入或加热后注入。确认油置换合格后,利用装置开工线,开始油闭路循环,其循环流量约为145吨/小时(约为设计流量的70%)or全量210吨/小时。(4)技术保证值乙方向甲方保证催化剂表面成膜剂成膜效果,经成膜后的催化剂在空气中不发生自燃现象,保证反应器设备及施工人员的安全,从而达到消除安全隐患、满足环保要求的目的。以上对本发明的具体实施方式进行了说明,但本发明并不以此为限,只要不脱离本发明的宗旨,本发明还可以有各种变化。当前第1页12