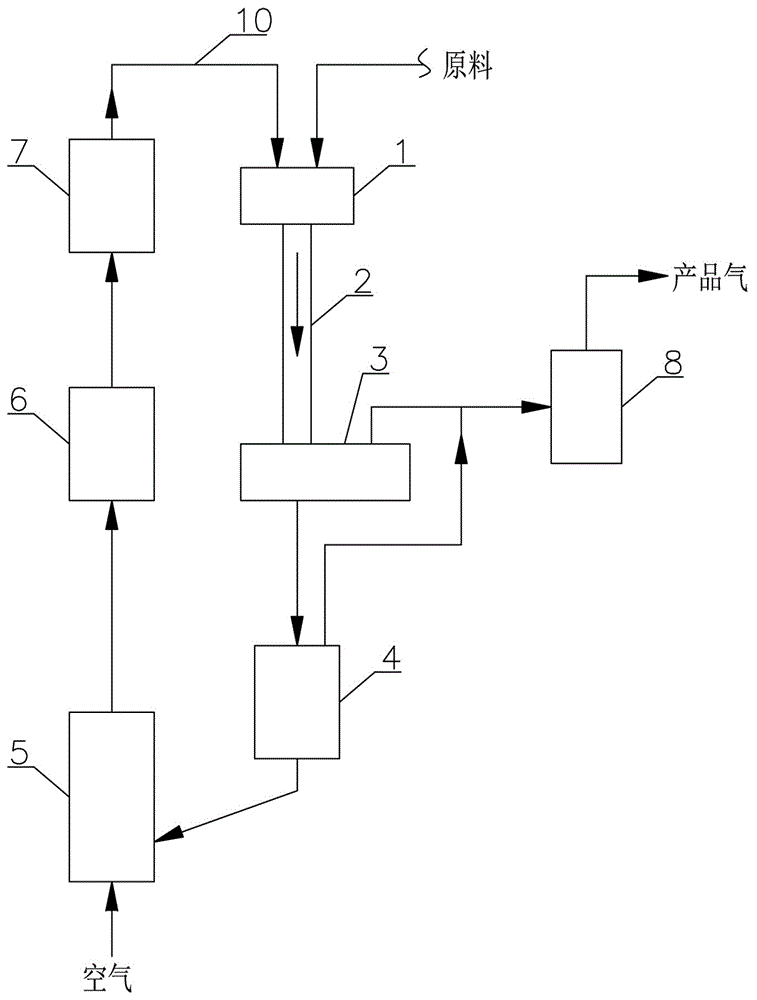
本发明属于烃类的催化转化方法,特别涉及利用下行床反应器进行烃类的催化转化。
背景技术:
:由于原油价格不断提高,不断增长的轻质油需求,环保法规的日益严格,利用催化裂化技术加工重质原料油,生产更清洁的燃料产品,同时降低催化裂化装置本身的排放量成为技术开发的热点。在提升管催化裂化反应过程中,预热后的原料与来自再生器的高温再生催化剂接触、汽化并进行反应,反应时间大约在2~3秒。研究表明,提升管出口处的催化剂活性只有初始活性的1/3左右;反应进行1秒钟左右,催化剂的活性下降50%左右。由于提升管反应过程中生成的焦炭沉积在催化剂表面及活性中心上,使催化剂的活性急剧下降,催化作用大为减弱,热裂化反应增多,产生较多干气和焦炭。提升管反应器和下行床反应器各有自己的优势。提升管反应器具有催化剂浓度高,气固接触面积较大,气固接触效率高等优点,但是由于其气固并流逆重力场流动,提升管内轴径向流动的不均匀,催化剂滑落返混较大,停留时间分布不均匀。而下行床反应器为气固并流顺重力场流动,径向流动更加均匀,催化剂无轴向返混,颗粒浓度及速度的径向分布较上行式的提升管有明显改善,特别适合超短接触(反应)时间(与提升管相比通常要缩短1-3倍)、超大剂油比(与提升管相比通常要增大1-3倍)的催化转化反应,如渣油的深度催化转化、催化热裂解、汽油催化裂解制烯烃等,能充分利用催化剂的初始活性,提高轻油收率,降低干气与焦炭的生成。因此,国内外的研究普遍集中在开发下行床反应器的入口结构、气固快速分离以及耦合提升管反应器和开发高活性催化剂等方面,以强化原料与催化剂在入口端的混合,提高反应的总转化率和选择性。cn1113689c公开了一种气固并流折叠式快速流化床反应装置;cn1162514c公开一种气固并流下行与上行耦合的催化裂化反应装置。研究表明,提高下行床反应器中催化剂浓度,可提高下行床催化转化反应过程的转化率和反应选择性,从而获得较高的目的产品收率。但却没有如何提高剂油比的技术方案或措施的研究与开发成果的报道。事实上,要提高烧焦效率和再生效果,通常要采用较高的再生温度(如700-730℃),因而再生催化剂(简称再生剂)温度都很高,远高于下行床反应器系统热量平衡所需的再生剂温度;也就是说,要大幅度地提高剂油比,就必须降低再生剂的温度,这样才能维持反应系统的热量平衡。同时,超短反应时间也必须要靠超大剂油比来保证;否则,如果通过提高反应温度来实现超短反应时间下的高转化率,就势必会加剧热裂化等非理想反应,从而会导致焦炭和干气产率的增高、汽油和轻烯烃等目的产品产率的下降。本发明的目的是在保证良好的再生效果的前提下,采用冷再生剂循环方法,实现大剂油比操作,降低进入下行床反应器的再生剂的温度,打破下行床反应器系统的热量平衡限制,从而提高催化剂的循环量,提高下行床反应器中催化剂浓度,提高催化剂活性和活性中心数,促进催化转化、氢转移、异构化、芳构化等理想反应,降低热裂化等非理想反应,提高反应选择性,从而提高汽油和轻烯烃等目的产品的产率,降低焦炭和气体的产率。本发明的另一目的是通过调节进入下行床反应器的再生剂温度,实现优化下行床反应器反应温度的目的,以适宜的反应温度和适宜的剂油比,优化下行床反应器的温度分布,优化反应深度和产品分布,从而更进一步地提高反应选择性,降低焦炭和气体的产率,提高汽油和轻烯烃等目的产品的产率。技术实现要素:本发明的要解决的技术问题是采用再生剂冷却技术,打破下行床反应器系统的热量平衡限制,真正实现大剂油比操作,提高下行床反应器中催化剂浓度和催化剂活性;同时采用适宜的反应温度(相对低0-50℃),优化下行床反应器的温度分布,实现反应深度的优化控制,从而提高反应选择性,提高丙烯等轻烯烃和汽油产率,提高汽油中的芳烃含量,降低汽油中的烯烃含量,同时降低焦碳和干气产率。本发明提供一种下行床反应器烃类催化转化方法,来自再生器的再生催化剂经再生剂冷却器冷却降温后进入下行床反应器,与烃类原料在入口端混合、接触,在下行床反应器内进行烃类的催化转化反应,并流下行至下行床反应器末端进行快速分离;分离出的待生催化剂(简称待生剂)经汽提后进入再生器烧焦再生,再生后的催化剂经再生剂冷却器冷却后返回下行床反应器循环使用。其具体工艺过程如下:1)经过预热(或不预热)后烃类原料与来自再生剂冷却器的低温再生剂进入下行床反应器入口端,沿反应器向下流动发生反应,反应油气与催化剂的混合物下行至反应器末端进行快速分离,实现催化剂与油气的快速分离。主要操作条件如下:反应温度为460~680℃(优选480~660℃,最佳490~650℃)、反应压力为0.11~0.4mpa,接触时间为0.05~2秒(优选0.1~1.5秒),催化剂与原料重量比(剂油比)为6~50(优选8~40)。2)分离出的待生催化剂(简称待生剂)经待生剂汽提器汽提后,进入再生器烧焦再生,再生温度控制在630-800℃(优选630-730℃,最佳650~730℃)。3)来自再生器的再生剂进入再生剂冷却器冷却到200-720℃,冷却后的再生剂(简称冷再生剂)进入下行床反应器入口端循环使用;或者设置热再生剂(即来自再生器未经冷却的再生剂)旁路,一部分热再生剂与上述冷再生剂混合后,混合再生剂进入下行床反应器入口端循环使用。更进一步地,上述下行床反应器的反应温度主要通过调节剂油比(即在上述冷再生剂输送管上设置控制元件如滑阀、塞阀等),或/和主要通过调节冷再生剂温度或混合再生剂的温度进行控制,使其分别保持在最佳值。通过调节进入上述下行床反应器的再生剂的温度,实现调节下行床反应器反应温度的目的,进而采用适宜的反应温度和适宜的剂油比,优化下行床反应器的温度分布,优化反应深度和产品分布,从而更进一步地提高反应选择性,降低焦炭和气体的产率,提高汽油和轻烯烃等目的产品的产率。所述的冷再生剂温度通过调节进入再生剂冷却器的流化介质流量和/或返回再生器的冷催化剂的流量和/或其它参数进行控制。所述的流化介质可以是空气、蒸汽或其它气体或者是它们的混合物,取热介质可以是水、蒸汽、空气或其它气体、各种油品等或者是它们的混合物。所述的进入下行床反应器的混合再生剂的温度可通过调节上述冷热再生剂的比例而得到独立控制。所述的进入下行床反应器的冷再生剂温度主要通过调节流化介质和/或取热介质的流量或/和其它参数进行控制;或者冷再生剂温度主要通过调节流化介质和/或取热介质和/或返回再生器的冷催化剂的流量或/和其它参数进行控制。因此,下行床反应器的剂油比(再生催化剂与原料的重量比)和反应温度均可得到独立控制。当然也可有许多其他控制设备和控制方法,不构成对本发明构思的任何具体实施方式的限制。本发明的方法及其装置,还可在所述的再生剂冷却器的下游设置催化剂混合缓冲空间,强化再生剂的混合,消除非均匀传热和非均匀流动而产生的径向温差(以使再生剂温度达到均衡),以满足下游反应温度控制的要求,提高下游反应温度控制的精准性和灵活性。同时,还可提高再生剂的密度,提高再生剂循环系统的推动力,以克服剂油比增大引起的循环系统阻力增大,实现大剂油比操作。所述催化剂混合缓冲空间采用低速密相流化床操作,其表观气速(流化介质流量与设备的空塔横截面之比)小于0.3m/s(优选0.0001~0.1999m/s)。所述催化剂混合缓冲空间的流化介质可以是空气、蒸汽或其它气体或者是它们的混合物(优选蒸汽),以减少循环催化剂夹带的空气量,降低干气中氮气等非烃类气体含量,提高干气热值,降低富气压缩机的功率消耗。本领域普通技术人员对其具体结构、连接型式、操作和控制过程非常清楚,不构成对本发明构思的任何具体实施方式的限制。上述与反应器相连接的再生剂冷却器可以设置于再生器外部,也可以设置于再生器内部。上述的再生剂冷却器可以与再生器、下行床反应器和/或催化剂混合缓冲空间连为一体,也可以通过输送管与其相连。本领域普通技术人员对其具体结构、连接型式、操作和控制过程非常清楚,不构成对本发明构思的任何具体实施方式的限制。催化剂冷却器为成熟工业设备,本发明的方法及其装置可采用各种结构形式(如上流式、下流式等),催化剂输送通道也可采用各种具体连接结构(如内循环管、y型、u型外输送(循环)管等),设置或不设脱气(平衡)管,本领域普通技术人员对其具体结构、连接型式、操作和控制过程非常清楚,不构成对本发明构思的任何具体实施方式的限制。本发明所述的烃类原料可以是经过加氢或未经加氢处理的任何重油包括直馏蜡油(馏分油)、焦化蜡油(馏分油)、加氢裂化尾油、常压渣油、减压渣油、页岩油、合成油、原油、煤焦油、回炼油、油浆、脱沥青油、热裂化重油、减粘重油、重柴油等中的一种、两种及两种以上的混合物;所述的蜡油(馏分油)馏分包括高密度环烷基或环烷中间基蜡油(馏分油)等;所述的蜡油(馏分油)馏分可以是全馏分,例如初馏点至565℃左右的馏分;也可以是其中的部分窄馏分,例如,450~520℃馏分。本发明所述的烃类原料也可以是轻烃原料为炼油厂或石油化工厂各种含烯烃或饱和液态轻烃类,包括液化石油气、轻油等中的任意一种或一种以上的任意比例的混合物;所述的液态轻烃可以是主要富含丁烯、戊烯的c4、c5馏分或者是它们的任意比例的混合物;所述的轻油可以是汽油馏份,包括直馏汽油、凝析油、催化裂化汽油、热裂化汽油、减粘汽油、焦化汽油、裂解制乙烯汽油在内的汽油中的一种、两种、多种及其任意比例的混合汽油,可以是全馏分汽油如初馏点至220℃左右的馏分或其中的部分窄馏分如初馏点至80℃的馏分;所述的轻油还可以是柴油馏份,包括催化裂化柴油,可以是全馏分柴油油如初馏点至365℃左右的馏分或其中的部分窄馏分如初馏点至300℃的馏分。本发明的催化转化方法可以单独实施,也可以与提升管反应器耦合使用,例如:可采用cn1113689c公开的气固并流折叠式快速流化床反应`装置或者cn1162514c公开的气固并流下行与上行耦合的催化裂化反应装置等。本发明的方法及其装置可采用各种反应再生型式,如设置第一再生器、第二再生器等,本领域普通技术人员对其组合型式、操作和控制过程非常清楚,不构成对本发明构思的任何具体实施方式的限制。采用本发明的方法及其装置,其反应产物的分离及催化剂的再生均按常规方法进行,待生催化剂在再生器中于常规催化转化催化剂再生条件下进行烧焦再生,一般再生温度控制在650~800℃(优选630-730℃,最佳650~730℃)。本发明的方法及其装置可以采用任何工业上使用的催化转化催化剂及助剂,包括多产丙烯zsm催化剂、超温分子筛催化剂等。流化催化转化工艺及装置为成熟工业过程,本领域普通技术人员对其组合型式、操作和控制过程非常清楚,对其操作条件(如进料温度、反应温度、反应压力、接触时间、剂油比等)和催化剂的选用也非常清楚,均不构成对本发明构思的任何具体实施方式的限制。为保证催化剂烧焦再生的适宜温度,维持反应再生系统的热平衡,还可以采取下列措施中的一种、两种或多种单独或联合使用:1)可以向再生器注入可燃固体、液体燃料或气体燃料中的任意一种、两种、多种及其混合物;2)可以用进入再生器的主风(烧焦空气)与再生烟气换热,或者作为再生催化剂冷却器的取热介质与再生剂换热,将主风进入再生器时的温度提高160-650℃(优选200-520℃)。3)可以用固体、液体或气体燃料中的一种、两种、多种及其混合物将主风加热升温至200-1800℃(优选600-1500℃)进入再生器。与现有技术相比有如下优点:本发明的催化转化方法采用冷再生剂循环技术,打破了反应器中的热量平衡和反应再生系统的热量平衡,使大剂油比成为可能,从而可优化下行床反应器的操作条件(如:可采用超短反应时间和更大的剂油比),在适宜的(相对低)反应温度下,有效地实现反应深度的优化控制,大大促进催化转化(裂化)等理想反应,抑制热裂化等非理想反应,从而提高了反应选择性。1.增大了催化剂循环量,降低了催化剂的结焦率(即再生剂与待生剂的碳差),提高了下行床反应器内单位催化剂的活性中心数。2.增大了催化剂循环量,提高了下行床反应器内催化剂的浓度,增大了油剂接触面积,改善了油剂接触效果;同时增加了单位原料接触的催化剂活性中心数,大大促进了催化裂化、氢转移、异构化、芳构化等理想反应。3.增大了催化剂循环量,下行床反应器内的出入口温度差大为减小,优化了下行床反应器的温度分布状况,有效地抑制了热裂化等非理想反应。4.采用低温再生剂循环,减轻了再生剂在输送过程中(到下行床反应器前)的水热失活,提高再生催化剂活性,降低了催化剂消耗。5.本发明采用低温再生剂循环,可以提高进料温度,改善原料油的雾化效果,与高活性催化剂和大剂油比以及适宜的反应温度协同作用,在大大降低不希望的产物(如焦炭和气体等)的产率的同时,极大地提高汽油和轻烯烃等目的产品的产率2.0-3.0个百分点,提高汽油辛烷值0.5-2.0单位,从而提高了该技术的经济性。6.设置下游催化剂混合缓冲空间,强化催化剂的混合,使再生剂温度达到均衡,均匀稳定,提高了下游反应温度控制的精准性和灵活性。同时,还有效地提高了再生剂的密度和缓冲能力,提高再生剂循环系统的推动力,从而提高操作的安全性、可靠性、稳定性、可控性和灵活性,实现了反应温度的优化控制和反应深度的优化控制。7.流化介质采用蒸汽,消除了循环催化剂夹带的空气,消除了干气中氮气等非烃类气体,提高了干气热值,降低了富气压缩机的功率消耗,降低了气体分离部分的设备尺寸和消耗。8.本发明的下行床反应器催化转化工艺,反应温度、剂油比等操作条件的调节相对独立,更加灵活,可以根据原料种类和市场情况灵活调整,以实现不同的产品分布。例如:1)可采用较低的反应温度,生产低烯烃高辛烷值汽油。此时,反应温度可以较低(如460-520℃,优选490-510℃),促进催化裂化、异构化、芳构化等理想反应,生产低烯烃高辛烷值汽油。2)可采用较高的反应温度,多产乙烯、丙烯等轻烯烃,同时生产芳烃等化工原料。当需要多产轻烯烃和芳烃时,反应温度又可以很高(如520-650℃,优选540-630℃),使烯烃裂化和芳构化等反应占主导,多产乙烯、丙烯等轻烯烃,同时生产高芳烃含量的汽油调和组份,进而可以通过芳烃抽提生产芳烃等化工原料。附图说明附图1-3:为本发明的下行床反应器催化转化装置的典型示意图。下面结合附图详细说明本发明,附图是为了说明本发明而绘制的,不构成对本发明构思的任何具体实施方式的限制。附图1为本发明的下行床反应器催化转化方法的方块流程示意图。如附图1所示:本发明的催化转化方法包括下行床反应器入口端1、下行床反应器2、快速分离装置3、待生剂汽提器4、再生器5、再生剂冷却器6、催化剂混合缓冲空间7、二级分离器8。原料油经预热升温后进入原料喷嘴内。在雾化蒸汽的作用下雾化,此时原料油以微细液滴形式进入到下行床反应器2内混合段,与此同时,由再生器5过来的高温催化剂,经再生剂冷却器6冷却降温,再经下游(或下部)催化剂混合缓冲空间7混合缓冲使其温度达到均衡后,进入下行床反应器入口端1,进入到下行床反应器2内并与雾化后的原料油混合;气固两相在混合段内快速接触和充分混合后,并流沿反应器2向下流动,同时进行发生催化转化反应。反应产物与催化剂的混合物并流下行至下行床反应器2末端气固快速分离装置3将催化剂和产品油气快速分离,或者产品油气被急冷(图中未画出,以避免二次反应的发生),而后进入二级分离器8(如旋风分离器等)进一步脱除催化剂后再进入下游分馏或分离系统进行进一步分离,从而得到所需要的气体产品和液体产品。主要操作条件如下:反应温度为460~680℃(优选480~660℃,最佳490~630℃)、反应压力为0.1l~0.4mpa,接触时间为0.05~2秒(优选0.1~1.5秒),催化剂与原料重量比(剂油比)为6~50(优选8~40)。分离出的待生剂经待生剂汽提器4汽提后,进入再生器5进行烧焦再生,再生温度控制在630-730℃(优选650-730℃)。。来自再生器5的再生剂进入再生剂冷却器6冷却到200-720℃直接返回下行床反应器2循环使用;或者离开再生剂冷却器6下部或底部的冷再生剂,再经混合缓冲空间7混合缓冲使其温度均衡后,返回下行床反应器2循环使用。流化介质可以是空气、蒸汽或其它气体或者是它们的混合物(优选蒸汽)。为实现反应温度的优化控制和反应深度的优化控制,在所述的再生剂冷却器6的下游设置催化剂混合缓冲空间7,强化再生剂的混合,在进入下行床反应器2前使再生剂温度达到均衡,以满足下游反应温度控制的要求。为实现节约空间和节省投资,催化剂混合缓冲空间7也可以采用与再生剂冷却器6等直径的一体式结构(如附图3所示)。催化剂混合缓冲空间7采用低速密相流化床操作,其表观气速小于0.3m/s(优选0.0001~0.1999m/s)。附图2为本发明的下行床反应器催化转化装置的一种同轴式再生的流程示意图。如附图2所示:本发明的催化转化方法及其装置包括下行床反应器入口端1、下行床反应器2、快速分离装置3、待生剂汽提器4、再生器5、再生剂冷却器6、催化剂混合缓冲空间7、二级分离器8和沉降器9。再生器5通过再生剂输送管与再生剂冷却器6相连再生剂经再生剂冷却器6冷却降温,再经下游(或下部)催化剂混合缓冲空间7混合缓冲后,通过冷再生剂输送管10与下行床反应器入口端1相连。离开再生剂冷却器6的冷再生剂温度通过调节流化介质35(包括空气、蒸汽等)流量进行控制。控制阀21是为了方便控制冷再生催化剂的流量而设置的具体控制元件。输送介质35可以是蒸汽或其它气体或者是它们的混合物(优选蒸汽)。取热介质37可以是水、蒸汽、空气或其它气体、各种油品等或者是它们的混合物。为方便控制进入下行床反应器的再生剂温度,还可以可设置热再生剂旁路管(包括控制阀)(图中未画出)直接与催化剂混合缓冲空间7相连,冷再生剂与热再生剂在此混合均匀后使其温度达到均衡。当然也可有许多其他控制设备和控制方法,不构成对本发明构思的任何具体实施方式的限制。烃类原料与再生剂在反应入口端1混合后进入下行床反应器2,在催化转化条件下进行反应,主要操作条件如下:反应温度为460~680℃(优选480~660℃,最佳490~630℃)、反应压力为0.11~0.4mpa,接触时间为0.05~2秒(优选0.1~1.5秒),催化剂与原料重量比(剂油比)为6~50(优选8~40)。反应油气和催化剂的混合物并流下行至下行床反应器2末端的快速分离装置3,将催化剂和产品油气快速分离,或者高温产品油气被急冷(图中未画出,以避免二次反应的发生),而后进入二级分离器8(如旋风分离器等)进一步脱除催化剂后再进入下游分馏或分离系统进行进一步分离,从而得到所需要的气体产品和液体产品。待生剂经沉降器9再经待生剂汽提器4汽提后,通过待生剂输送管13和控制阀(图中未画出)进入再生器5,在主风38(含氧气体包括空气等)的存在下烧焦再生。再生剂由再生器5下部引出进入再生剂冷却器6后进入催化剂混合缓冲空间7混和均匀后,冷再生剂经输送管11(或与热再生剂混合)循环使用(也可以设置另一路催化剂输送管返回再生器)。(当然,也可以根据工艺需要设置单独的外取热器,以实现多工况下的灵活操作)。来自再生器5的再生剂进入再生剂冷却器6冷却到200-720℃。离开再生剂冷却器6下部或底部的冷再生剂,再经催化剂混合缓冲空间7混合缓冲使其温度均衡后,返回下行床入口端1和反应器2循环使用。流化介质39可以是空气、蒸汽或其它气体或者是它们的混合物(优选蒸汽)。为实现反应温度的精准控制和优化控制,在所述的再生剂冷却器6的下游设置催化剂混合缓冲空间7,强化再生剂的混合,在进入下行床入口端1和反应器2前使再生剂温度达到均衡,以满足下游反应温度精准控制的要求。为实现节约空间和节省投资,催化剂混合缓冲空间7也可以设计为与再生剂冷却器6等直径的一体式结构。催化剂混合缓冲空间7采用低速密相流化床操作,其表观气速小于0.3m/s(优选0.0001~0.1999m/s)。附图3为本发明的下行床反应器催化转化装置的一种快速床再生的流程示意图。如附图3所示:本发明的催化转化方法及其装置包括下行床反应器入口端1、下行床反应器2、快速分离装置3、待生剂汽提器4、再生器5、再生剂冷却器6、催化剂混合缓冲空间7、二级分离器8和沉降器9。再生器5通过再生剂输送管与再生剂冷却器6相连,再生剂经再生剂冷却器6冷却降温,再经下游(或下部)催化剂混合缓冲空间7混合缓冲温度达到均衡后,通过冷再生剂输送管10与下行床反应器入口端1相连。离开再生剂冷却器6的冷再生剂温度通过调节流化介质35(包括空气、蒸汽等)的流量进行控制。控制阀21是为了方便控制冷再生剂的流量而设置的具体控制元件。为方便控制进入下行床反应器的再生剂温度,还可以可设置热再生剂输送管(包括控制阀,图中未画出)直接与再生剂混合缓冲空间7相连,冷再生剂与热再生剂在此混合后使其温度达到均衡。当然也可有许多其他控制设备和控制方法,不构成对本发明构思的任何具体实施方式的限制。上述的催化剂冷却器可以与再生器、下行床连为一体,也可以通过管线与其相连。烃类原料与再生剂混合进入下行床反应器,在催化转化条件下进行反应,主要操作条件如下:反应温度为460~680℃(优选480~660℃,最佳490~630℃)、反应压力为0.1l~0.4mpa,接触时间0.05~2秒(优选0.1~1.5秒),催化剂与原料重量比(剂油比)为6~50(优选8~40)。反应油气和催化剂的混合物并流下行至下行床反应器2末端快速分离装置3,中高温油气被急冷(以避免二次反应的进行),而后进入二级分离器8(如旋风分离器等)进一步脱除催化剂后再进入中高温油气急冷器(以避免二次反应的进行)冷却后,进入下游分馏或分离系统进行进一步分离,从而得到所需要的气体产品和液体产品。分离出的待生剂经待生剂汽提器4汽提后,通过待生剂输送管13和控制阀20进入烧焦罐5a,在主风38a(含氧气体包括空气等)的存在下经快速烧焦,向上输送至再生器5进一步烧焦再生,再生器5底部补充二次风38b(含氧气体包括空气等)。再生剂由再生器5下部引出,进入再生剂冷却器6,再生剂混合缓冲空间7和冷再生剂经输送管11(或与热再生剂混合)循环使用,另一路经输送管12(也可以不设输送管12)返回再生器(当然,也可以根据工艺需要设置单独的外取热器,以实现多工况下的灵活操作)。来自再生器5的再生剂进入再生剂冷却器6冷却到200-720℃。离开再生剂冷却器6下部或底部的冷再生剂,再经催化剂混合缓冲空间7混合缓冲使其温度均衡后,返回下行床反应器入口端和反应器2循环使用。流化介质39可以是空气、蒸汽或其它气体或者是它们的混合物(优选蒸汽)。取热介质37可以是水、蒸汽、空气或其它气体、各种油品等或者是它们的混合物。输送介质36可以是空气、蒸汽或其它气体或者是它们的混合物。为实现反应温度的精准控制和优化控制,在所述的再生剂冷却器的下游设置混合缓冲空间7,强化再生剂的混合,在进入下行床反应器2前使再生剂温度达到均衡,以满足下游反应温度控制的要求。为实现节约空间和节省投资,催化剂混合缓冲空间7采用与再生剂冷却器6等直径的一体式结构。催化剂混合缓冲空间7采用低速密相流化床操作,其表观气速小于0.3m/s(优选0.0001~0.1999m/s)。具体实施方式实例1为验证本发明的效果,采用图2或图3所示的工艺流程、表1所示的重油原料性质和表2所示的现有技术和本发明的工艺条件及多产丙烯的分子筛催化剂(chp-1),试验结果列于表3。表3的结果表明,由于现有下行床反应器热量平衡的限制,在进料温度为230℃的情况下,现有技术的剂油比也仅能达到11.5,因而并不能实现下行床反应器所需的大剂油比操作。本发明与现有技术相比,焦碳和干气产率下降1.8个百分点,总轻收(lpg+汽油+柴油)提高2.1个百分点,总液收(总轻+油浆)提高1.8个百分点,同时柴油收率降低10个百分点,具有很好的产品分布。对于一套100万吨/年的重油催化裂化装置,年增经济效益约9000多万元。表1重油原料性质原料重油密度,20/4℃0.881残炭0.4%(wt)硫含量0.15%(wt)表2现有技术和本发明的工艺条件对比表3现有技术和本发明的试验结果对比产物现有技术本发明产品收率wt%燃料气+h2s5.14.1lpg13.125.1汽油38.539.2柴油29.719.1油浆5.35.0焦炭8.37.5合计100.0100.0总轻收81.383.4总液收86.688.4实例2对于实例2,下行床反应器的原料为催化裂化汽油,下行床反应器需采用约30的超大剂油比,才能实现优化反应温度分布,提高反应选择性,提高丙烯和汽油收率,提高汽油中的芳烃含量和辛烷值,降低汽油中的烯烃含量的目的。本实例采用图2或图3所示的工艺流程、表4所示的现有技术和本发明的工艺条件及多产丙烯的分子筛催化剂(chp-1),汽油原料和试验结果列于表5。表4所示的结果表明,由于下行床反应器热量平衡的限制,现有技术方案b采用进料温度400℃时,热平衡下的剂油比仅有12.1。如此低的剂油比将严重影响下行床反应器的转化率和选择性。方案a进料温度40℃时,虽然可将剂油比提高至25.9,但这将严重影响装置低温热的回收与利用。表5的结果表明,本发明与现有技术相比,高附加值的丙烯产率提高1.2个百分点,焦碳干气产率相当,总轻收相当;汽油中芳烃含量降低3.7个百分点,烯烃含量降低3个百分点,辛烷值(ron)提高0.8-2个单位。同时,表4表明因采用400℃高温进料,本发明还能最大程度地提高余热回收效率。这些都说明了本发明的汽油催化转化方法具有显著的有益效果。表4汽油原料性质表5现有技术和本发明的工艺条件对比实例3对于实例3,下行床反应器的原料为富含烯烃的混合碳四。本实例采用图2或图3所示的工艺流程、表6所示的现有技术和本发明的工艺条件及zsm-5分子筛催化剂。下行床反应器通常要采用大于30的超大剂油比操作,才能实现优化反应温度分布,提高反应选择性,提高乙烯、丙烯收率的目的。然而表6的结果表明采用400℃高温进料,由于下行床反应器热量平衡的限制,现有技术热平衡下的剂油比仅有16.3。如此低的剂油比将严重影响下行床反应器的转化率和选择性。本发明采用的混合碳四原料和试验结果列于表7。表7表明高附加值的丙烯产率约47.2%,乙烯产率10.6%,说明本发明的混合碳四催化转化方法具有显著的有益效果。表6现有技术和本发明的工艺条件对比表7混合碳四原料性质和试验结果项目参数本发明原料组成:mol%c3+c5:0.6丁烷:11.9丁烯87.5合计100产品收率:wt%<c215.8其中乙烯10.6丙烷4.3丙烯47.2丁烷10.3丁烯11.7液体+焦炭+损失10.7其中乙烯+丙烯57.8合计100.0当前第1页12