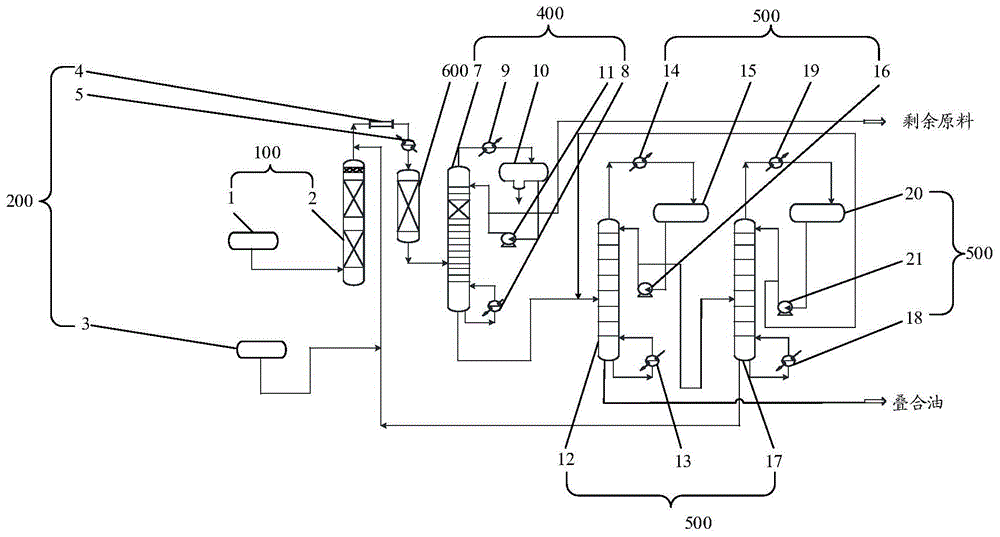
本申请涉及石油化工
技术领域:
,尤其涉及一种异丁烯叠合系统及叠合方法。
背景技术:
:2017年9月7日,国家质监总局联合标准化管理委员会发布并同步实施gb18351《车用乙醇汽油(e10)》与gb22030《车用乙醇汽油调合组分油》两个标准,标准中明确规定车用乙醇汽油中除乙醇外,其它有机含氧化合物含量(质量分数)不大于0.5%且不得人为加入;2017年9月13日,国家发改委等15部委联合发布《关于扩大生物燃料乙醇生产和推广使用车用乙醇汽油的实施方案》,确定2017年起在东北等多省市推广使用乙醇汽油,到2020年全国基本实施全覆盖。由于mtbe(methyltert-butylether,甲基叔丁基醚,简称:mbte)是含氧量较高的乙醇汽油调合组分,因此,这些法规的颁布使得mtbe无法作为乙醇汽油的调合组分添加至乙醇汽油中。异丁烯作为mtbe的合成原料,在mtbe停产后可以采用异丁烯为原料生产叠合油,因为叠合油中不含氧,因此叠合油可以作为乙醇汽油的调合组分。相关技术中提出了一种生产mtbe的装置,该装置包括顺次连通的预处理装置、醚化反应装置、催化蒸馏装置与萃取回收装置。由于mtbe的装置只能生产mtbe,无法用其生产异丁烯叠合油,因此亟需一种异丁烯叠合系统及叠合方法。该叠合系统和叠合方法可以生产出更多的叠合油以作为不含氧的高辛烷值乙醇汽油的调合组分。技术实现要素:本申请提供了一种异丁烯叠合系统及叠合方法,可以解决相关技术中无法生产异丁烯叠合油的问题。所述技术方案如下:第一方面,本申请实施例提供了一种异丁烯叠合系统,所述系统包括:预处理装置、混合装置、叠合反应装置、催化蒸馏装置与蒸馏装置;所述预处理装置与所述混合装置的一端连接,所述预处理装置用于对原料进行预处理,得到第一原料,所述混合装置用于混合第一原料与添加物,得到混合原料;所述混合装置的另一端与所述叠合反应装置的一端连接,所述叠合反应装置用于所述混合原料进行叠合反应,得到第一反应产物;所述叠合反应装置的另一端与所述催化蒸馏装置连接,所述催化蒸馏装置用于对所述第一反应产物进行进一步反应与分离,得到第二反应产物与未反应的剩余原料产品;所述催化蒸馏装置与所述蒸馏装置连接,所述蒸馏装置用于对所述第二反应产物中异丁烯叠合产物与所述添加物进行分离,最终得到异丁烯叠合产物。可选地,所述预处理装置包括顺次连接的第一原料罐和水洗塔,所述水洗塔用于脱除所述原料中的金属阳离子和碱性化合物;所述混合装置包括顺次连接的第二原料罐、混合器和加热器,所述混合器用于混合所述脱除了金属阳离子和碱性化合物的原料与所述添加物;所述水洗塔与所述混合器连接,所述混合器与所述加热器连接,所述加热器与所述叠和反应装置连接。可选地,所述催化蒸馏装置包括催化蒸馏塔、第一重沸器、第一冷凝器、第一回流罐和第一回流泵;所述催化蒸馏塔的一侧与所述叠合反应装置的底部连接,所述催化蒸馏塔的底部与所述第一重沸器的进口连接,所述第一重沸器的出口与所述催化蒸馏塔的另一侧连接,所述催化蒸馏塔的顶部与所述第一冷凝器的一侧连接,所述第一冷凝器的另一侧与所述第一回流罐的顶部连接,所述第一回流罐的底部与所述第一回流泵的一侧连接,所述第一回流泵的另一侧分别与所述催化蒸馏塔的另一侧连接和产品输出装置连接。可选地,所述催化蒸馏塔包括从上至下顺次连通的精馏段、反应段和提馏段;所述精馏段的塔板数包括10~29块,所述反应段内的催化剂床层的层数包括2~16层,所述提馏段的塔板数包括13~35块。可选地,所述蒸馏装置包括高压蒸馏装置与低压蒸馏装置;所述高压蒸馏装置包括高压塔、第二重沸器、第二冷凝器、第二回流罐和第二回流泵;所述高压塔的底部和所述第二重沸器的进口连接,所述高压塔的顶部与所述第二冷凝器的一侧连接,所述第二冷凝器的另一侧与所述第二回流罐的顶部连接,所述第二回流罐的底部与所述第二回流泵的一侧连接,所述第二回流泵的另一侧具有两个出液口,其中一个出液口与所述高压塔塔顶的一侧连接,另一个出液口与低压塔连接;所述低压蒸馏装置包括所述低压塔、第三重沸器、第三冷凝器、第三回流罐和第三回流泵;所述低压塔的一侧与所述第二回流泵的另一侧连接,所述低压塔的底部与所述混合器的一侧连接,所述低压塔的底部设置有所述第三重沸器,所述低压塔的顶部与所述第三冷凝器的一侧连接,所述第三冷凝器的另一侧与所述第三回流罐的顶部连接,所述第三回流罐的底部与所述第三回流泵的一侧连接,所述第三回流泵的另一侧分为两路,其中一路与所述低压塔塔顶的另一侧连接,另一路作为高压塔的部分进料与高压塔连接;可选地,所述高压塔包括从上至下顺次连通的精馏段和提馏段;所述精馏段的塔板数为10~19块,所述提馏段的塔板数为12~24块;所述低压塔包括从上至下顺次连通的精馏段和提馏段;所述精馏段的塔板数为5~20块,所述提馏段的塔板数为25~50块。第二方面,本申请实施例提供了一种异丁烯叠合方法,所述方法应用于上述任一所述的异丁烯叠合系统,所述方法包括以下步骤:原料与脱除剂在预处理装置混合后脱除原料中的金属阳离子和碱性化合物,得到第一原料;所述第一原料与添加物在混合装置中进行混合,得到混合原料;所述混合原料在叠合反应装置中进行叠合反应,得到第一反应产物;所述第一反应产物在催化蒸馏装置中进行进一步反应与分离,得到第二反应产物与剩余原料产品;所述第二反应产物中的异丁烯叠合产物和所述添加物在蒸馏装置中蒸馏,得到异丁烯叠合产物。可选地,所述第一反应产物在催化蒸馏装置中进行进一步反应与分离,包括在如下操作条件下对所述第一反应产物进行反应分离:所述催化蒸馏塔的塔顶的温度为50-70℃,反应段的温度为60~95℃,塔底的温度为135-175℃,操作压力为0.5~0.8mpa。可选地,所述第二反应产物中的异丁烯叠合产物和所述添加物在蒸馏装置中蒸馏,得到异丁烯叠合产物,包括:对所述第二反应产物在蒸馏装置中的高压塔内蒸馏,得到叠合油与第一共沸产物,将所述叠合油作为所述异丁烯叠合产物;对所述第一共沸产物在低压塔内进一步蒸馏,得到添加物和第二共沸产物。可选地,所述第二反应产物中的异丁烯叠合产物和所述添加物在蒸馏装置中蒸馏,包括:在如下操作条件下对所述第二反应产物中的异丁烯叠合产物和添加物进行蒸馏:其中高压塔的操作压力为0.8~1.0mpa,低压塔的操作压力为0.10~0.20mpa;所述添加物为叔丁醇。本申请提供的技术方案至少可以带来以下有益效果:本申请实施例提供的异丁烯叠合系统中通过预处理装置可以去除原料中会使叠合反应催化剂失活的毒物;通过混合装置可以使得原料与添加剂混合,从而避免或减少副反应的发生;通过叠合反应装置可以使原料进行叠合反应,生成叠合产物;通过催化蒸馏装置可以对叠合产物进一步进行叠合反应,使得叠合反应更加彻底,并分离出了剩余原料产品;通过高压蒸馏装置和低压蒸馏装置,可以获得高辛烷值的叠合油和高纯度的添加物。通过上述装置,可以生产出高辛烷值的叠合油和可循环使用的高纯度添加物,其中叠合油可以作为乙醇汽油的调合组分,添加物可以循环至混合装置与原料混合。附图说明为了更清楚地说明本发明实施例中的技术方案,下面将对实施例描述中所需要使用的附图作简单地介绍,显而易见地,下面描述中的附图仅仅是本发明的一些实施例,对于本领域普通技术人员来讲,在不付出创造性劳动的前提下,还可以根据这些附图获得其他的附图。图1是本申请实施例提供的第一种异丁烯叠合系统的结构示意图;图2是本申请实施例提供的第二种异丁烯叠合系统的结构示意图;图3是本申请实施例提供的一种异丁烯叠合方法的流程图;图4是现有技术提供的一种生产mtbe装置的结构示意图。附图标记:100:预处理装置;200:混合装置;400:催化蒸馏装置;500:蒸馏装置;600:叠合反应装置;1:第一原料罐;2:水洗塔;3:第二原料罐;4:混合器,5:加热器;7:催化蒸馏塔;8:第一重沸器;9:第一冷凝器;10:第一回流罐;11:第一回流泵;12:高压塔;13:第二重沸器;14:第二冷凝器;15:第二回流罐;16:第二回流泵;17:低压塔;18:第三重沸器;19:第三冷凝器;20:第三回流罐;21:第三回流泵;22:第一原料泵;23:第二原料泵;24:第三原料泵;25:换热器;26:冷却器;27:共沸物泵。具体实施方式除非另有定义,本发明实施例所用的所有技术术语均具有与本领域技术人员通常理解的相同的含义。随着国家政策的推出,mtbe无法作为乙醇汽油的调合组分添加至乙醇汽油中。异丁烯作为mtbe的合成原料,在mtbe停产后可以采用异丁烯为原料生产叠合油,因为叠合油中不含氧,因此叠合油可以作为乙醇汽油的调合组分。mtbe停产后,异丁烯也可作为生产化工产品的原料,但国内以异丁烯为原料生产的化工产品普遍存在产品牌号过少、新产品开发能力弱、生产成本高等问题,且化工产品的市场容量有限,无法解决千万吨级异丁烯出路。因此有必要开发出一种节能、经济、以混合c4中异丁烯为原料生产二异丁烯的工艺,不但可以生产出更多的高辛烷值乙醇汽油添加组分二异丁烯,也可以解决千万吨级异丁烯的出路问题。cn109354567a介绍了一种由甲基叔丁基醚装置改造转化的异丁烯叠合系统装置及叠合工艺方法,该装置包括供料单元、叠合单元、催化蒸馏单元和抑制剂回收单元。其中,供料单元包括原料混合器前端的碳四净化供料支路和抑制剂供料支路,抑制剂回收单元由原甲醇萃取塔作为抑制剂萃取塔和原甲醇精馏回收塔作为抑制剂精馏回收塔连接组成。该装置及方法存在的主要问题是:1)供料单元中并没有对碳四原料中的会使叠合反应催化剂失活的物质如碱氮化合物或金属阳离子进行脱除,因此催化剂使用寿命短,在叠合单元中需要更多的催化剂,而且由于催化剂活性的下降,导致碳四原料中异丁烯叠合的转化率下降,造成经济效益下降;2)由于采用萃取水对催化蒸馏单元产生的抑制剂和二异丁烯的混合物进行萃取,因此在抑制剂萃取塔的塔顶所得到的是抑制剂与水形成共沸物,该共沸物中水的质量分数约为12.6%,这部分共沸物返回叠合单元时会使碳四原料中的异丁烯与水发生反应,从而生成大量的叔丁醇,导致最终获得的叠合油产品收率下降;3)作为萃取剂的萃取水需要定期排放,由于萃取水中含有大量叔丁醇,这部分含醇废水较难处理。《石油炼制与化工》第50卷第9期的《异丁烯选择性叠合技术研究开发进展》介绍了一种对碳四原料进行预处理及异丁烯叠合方法,其提供的碳四原料预处理方法是将含异丁烯的混合碳四原料与调节剂混合后进入净化器的方法来脱除混合碳四原料中的有害杂质,具体措施是在原料进料管线上设两台互为备用的小型净化器,每台净化器中内都装与叠合催化剂性能基本相同的保护性催化剂,混合碳四原料在进入反应器之前会先进入净化器,这样混合碳四原料中的金属阳离子等杂质会首先使净化器中的催化剂失活,从而达到保护反应器内催化剂的目的。但设置净化器对乙腈等碱氮化合物的作用较小,因为乙腈等碱氮化合物造成催化剂中毒的方式不是递推式的,具体的说,不是造成首先与反应物接触的那部分催化剂中毒,然后才会引起与中毒催化剂相邻的催化剂中毒失活,而是被吸附于整个催化剂床层,然后再进行水解反应,导致整个催化剂活性下降,因此设置净化器无法将乙腈等碱氮化合物有效脱除,碱氮化合物仍然会进入反应器,进而会使得反应器内的催化剂失活;其异丁烯叠合方法是从侧线抽出调节剂,调节剂再返回反应系统,但侧线抽出的调节剂中含有大量与其共沸的二异丁烯,如常压下调节剂叔丁醇与二异丁烯的共沸组成为:调节剂叔丁醇占55.2%(质量)、二异丁烯占44.8%(质量),由于侧线抽出的调节剂中含有大量的二异丁烯,过多的二异丁烯就会与原料中异丁烯反应生成三聚产物,三聚产物再与异丁烯反应生成四聚产物,四聚产物的沸点为230~250℃,己经完全超出了汽油馏程范围,如果产物中的四聚产物过多,则产品质量不合格而造成巨大损失。以混合c4中异丁烯为原料生产二异丁烯工艺的主要反应是异丁烯(ib)二聚生成2,4,4-三甲基戊烯(dib),dib是三甲基戊烯的异构体。其反应式如下:ib+ib→dib(1)副反应包括ib与dib反应生成三聚产物(tib)及ib再与tib反应生成四聚产物(teb)。其反应式如下:ib+dib→tib(2)ib+tib→teb(3)异丁烯和水还会发生水合反应生成叔丁醇,其反应式如下:反应(4)为可逆反应。h2o和tba的存在对ib的转化率及ib选择性生成dib所产生的影响是非常显著的。随着h2o和tba的增加,二者覆盖催化剂的活性中心的比例也相应增加,从而会造成ib的转化率降低,进而会使得tib和teb的生成量减少,提高了dib的生成量。另外,c4烯烃的二聚产物加氢后生成的c8异构烷烃的沸点在99~118℃之间,正好处于乙醇汽油的馏程中。但是在二聚反应过程中往往还会伴随三聚反应甚至多聚反应,而三聚产物的沸点一般在170~180℃,已处于乙醇汽油馏程的末端,其加入量必须严格控制,否则会影响乙醇汽油的干点,一般其加入量不超过10%,四聚产物的沸点为230~250℃,己经完全超出了乙醇汽油的馏程,因而不能加入乙醇汽油中。以混合c4为原料生产二异丁烯(叠合油)工艺的关键在于提高二聚产物的选择性。二聚产物的选择性低将会导致大量宝贵的异丁烯资源生成低价值的三聚产物和四聚产物,从而会造成资源的浪费,且会加大后续分离操作的费用。实践证明,极性物质tba或水等的加入可大幅度提高生成二聚产物的选择性,而过多的二异丁烯返回至反应部分会大幅度提高三聚、四聚副反应物的产率从而降低生成二聚产物的选择性。第一方面,本申请实施例提供了一种异丁烯叠合系统。参见图1,该系统包括:预处理装置100、混合装置200、叠合反应装置600、催化蒸馏装置400与蒸馏装置500;预处理装置100与混合装置200的一端连接,预处理装置100用于对原料进行预处理,得到第一原料,混合装置200用于混合第一原料与添加物,得到混合原料;混合装置200的另一端与叠合反应装置600的一端连接,叠合反应装置600用于混合原料进行叠合反应,得到第一反应产物;叠合反应装置600的另一端与催化蒸馏装置400连接,催化蒸馏装置400用于对第一反应产物进行进一步反应与分离,得到第二反应产物与未反应的剩余原料产品;催化蒸馏装置400与蒸馏装置500连接,蒸馏装置500用于对第二反应产物中异丁烯叠合产物与添加物进行分离,最终得到异丁烯叠合产物。本申请实施例提供的系统至少具有以下技术效果:本申请实施例中,预处理装置100的设置可以去除原料中会使叠合反应催化剂失活的物质,从而保证了叠合反应的长周期平稳进行;混合装置200的设置可以使得第一原料与添加物充分混合,保证了第一原料在进行叠合反应时,降低副反应发生的可能性;叠合反应装置600的设置可以使得混合原料在其中进行叠合反应;催化蒸馏装置的设置,可以使得混合原料的叠合反应进行地更加充分,而且混合原料分别在固定床反应器和催化蒸馏内进行串级叠合反应,可以降低反应的苛刻度,进而可以延长叠和反应装置600中催化剂的使用寿命;蒸馏装置500的设置可以使最终获得的叠合油具有较高的纯度,还可以将分离出的添加物再次循环至混合装置200中,从而可以降低操作成本。需要说明的是,原料在预处理装置100中进行预处理,以脱除其中会使叠合反应催化剂失活的物质,从而使得后续叠合反应长周期高效进行。可选地,第一原料与添加物在混合装置200进行混合,添加物用于抑制第一原料进行三聚、四聚甚至多聚反应,示例地,添加物可以为叔丁醇。可选地,叠和反应装置600用于进行叠合反应,示例的,叠和反应装置600中可以装有大孔阳离子交换树脂叠合催化剂,该催化剂可加快叠合反应的反应速率。叠和反应装置600的类型可以根据使用需求进行预先设置,例如,叠和反应装置600可利用原mtbe装置的醚化反应器,或对原醚化反应器改造后再进行利用。值得注意的是,叠和反应装置600的反应液时体积空速为0.5~5h-1,反应压力为0.6~1.5mpa。示例地,反应液时体积空速可以为0.5h-1、1.5h-1、2.5h-1、3.5h-1、4.5h-1或5h-1等,反应压力可以为0.6mpa、1mpa或1.5mpa等。可选地,催化蒸馏装置400用于第一反应产物的进一步反应与分离,得到第二反应产物(即,叠合反应产物)和剩余原料产品。第一反应产物中的未反应的混合原料在催化蒸馏装置400进行进一步的叠合反应,其中,催化蒸馏塔的塔底物料为第二反应产物,该产物主要包括在反应器及催化蒸馏塔的反应段进行叠和反应生成的叠合产物与混合在其中的添加物。可选地,蒸馏装置500用于对第二反应产物进行分离提纯,最终可获得纯度较高的添加物和高辛烷值的叠合油。示例地,在使用本申请实施例提供的异丁烯叠合系统对原料中的异丁烯进行叠合时,可以先将原料送入预处理装置100,使原料在预处理装置100中脱除其含有的会使叠合催化剂失活的物质。然后将预处理过的原料送入混合装置200,使其与添加物混合。之后再送入叠和反应装置600进行叠合反应,主要是使原料中的异丁烯进行二聚反应。然后再将反应得到的第一反应产物送入催化蒸馏装置400,然后第一反应产物中未反应的异丁烯在催化蒸馏装置400中进一步进行叠合反应,并在催化蒸馏装置400中分离出第二反应产物及剩余原料产品。之后将得到的第二反应产物送入蒸馏装置500进行分离提纯,从而可以获得纯度较高的异丁烯叠合产物。可选地,参见图1,预处理装置100包括顺次连接的第一原料罐1和水洗塔2,水洗塔2用于脱除原料中的金属阳离子和碱性化合物等;混合装置200包括顺次连接的第二原料罐3、混合器4和加热器5,混合器4用于混合脱除了金属阳离子和碱性化合物的原料与添加物;水洗塔2与混合器4连接,混合器4与加热器5连接,加热器5与叠和反应装置600连接。需要说明的是,第一原料罐1用于存储原料。第一原料罐1的类型可以根据使用需求进行预先设定,例如,第一原料罐1可以对原mtbe装置的碳四原料罐进行利用,或对碳四原料罐改造后再进行利用。值得注意的是,参见图2,预处理装置100还可以包括第一原料泵22。将第一原料罐1中的原料送至水洗塔2时,若原料的压力不满足水洗塔2所需的压力,此时可在第一原料罐1与水洗塔2之间设置第一原料泵22。该第一原料泵22用于对第一原料罐1中存储的原料进行升压,以使其的压力满足所需。第一原料泵22的类型可以根据使用需求进行预先设定,例如,第一原料泵22可以利用原mtbe装置的碳四原料泵,或对碳四原料泵改造后再进行利用。需要说明的是,水洗塔2中注有脱除剂,利用金属阳离子和碱性化合物等易溶于水的特点,可以使得二者从原料中分离出来。例如,脱除剂可以为脱氧水、除盐水或蒸汽凝结水,其中,除盐水为除去悬浮物、胶体和无机的阳离子、阴离子等水中杂质后,所得到的成品水,脱氧水为除盐水进一步除去其溶解的微量氧气的水。水洗塔2的类型可以根据使用需求进行预先设置,例如,水洗塔2可以利用原mtbe装置的甲醇萃取塔,或对甲醇萃取塔改造后再进行利用。当以混合c4为原料生产二异丁烯(叠合油)工艺中采用阳离子交换树脂催化剂进行叠合反应时,其易受原料中碱性氮化物、金属阳离子等物质的影响。研究表明催化剂失活存在如下六种机理:物理失活、化学失活、热力学降解、有机物聚合结垢、阳离子失活、碱氮化合物水解失活。金属阳离子如钠、钙、铁、镁离子等,会将酸性阳离子交换树脂催化剂中的磺酸基团上的h+置换掉,使催化剂失去酸性而失活,以nacl为例,造成中毒的反应如下式所示:由金属阳离子造成的中毒是递进式或活塞式的,即首先与原料接触的催化剂中毒失活、然后才会引起与中毒催化剂相邻的部分催化剂中毒失活。碱氮化合物水解失活为原料中的腈类(主要为乙腈、丙腈)水解后与催化剂中的阳离子交换树脂发生反应而引起的催化剂失活。腈类的中和反应可分为两步:第一步,原料中的腈被吸附于阳离子交换树脂中,吸附量取决于腈在原料与阳离子交换树脂之间的分配系数(partitioncoefficient)。实验表明,存在于醇类与非活性c4原料中的腈,在饱和状态下,其被吸附量可达6kg/100kg树脂(干基)。第二步,被吸附的腈与水反应首先反应生成氨基化合物,氨基化合物再与水反应生成有机酸和氨离子,氨离子与阳离子交换树脂中的磺酸基发生中和反应,造成催化剂中毒失活。水解反应中的水有三处来源:原料携带的水、水洗塔中的水及装置正常生产时补充的脱氧水。由乙腈水解造成的催化剂中毒失活不同于前五种情况,前五种情况造成的中毒失活都是递推式的,即首先与反应物接触的催化剂中毒失活,然后才会引起与中毒催化剂相邻的催化剂中毒失活。而后者则是碱氮化合物首先被吸附于整个催化剂中,然后再进行水解反应,导致整个催化剂活性下降,因此该中毒失活过程更具危害性。腈化物含量对酸性阳离子交换树脂催化剂寿命的影响如表1所示。表1腈化物含量对异丁烯叠合催化剂寿命的影响腈化物含量/mg.kg-1<13~15>30催化剂寿命/a20.5~0.7<0.3利用c4原料中金属离子、碱性化合物易溶于水的特点,采用水洗的方式可有效地脱除这些有害杂质,使其含量均<1mg/kg,确保催化剂长周期运行。虽然省去水洗部分可使异丁烯叠合系统的总投资降低大约10%,但催化剂寿命缩短将导致催化剂费用大幅度增加,从经济上远不如增加水洗合适。值得注意的是,与《异丁烯选择性叠合技术研究开发进展》中预处理方法相比,采用水洗塔对混合c4原料进行水洗,不仅可以脱除混合c4原料中的金属阳离子、氮化物等杂质,还可以脱除混合c4原料中的碱氮化合物,从而保证了叠合反应装置600中的催化剂不会失活。需要说明的是,第二原料罐3用于存储添加物,该添加物可以抑制叠合反应的副反应的进行。第二原料罐3的类型可以根据使用需求进行预先设置,例如,第二原料罐3可以利用原mtbe装置的甲醇原料罐,或对甲醇原料罐改造后再进行利用。值得注意的是,参见图2,混合装置200还可以包括第二原料泵23。将第一原料与添加物混合时,若添加物的压力不满足混合器4所需的压力,此时可在第二原料罐3与混合器4之间设置第二原料泵23。该第二原料泵23用于对添加物进行升压,以使其的压力满足所需。第二原料泵23的类型可以根据使用需求进行预先设定,但是由于第二原料泵23的正常操作流量远低于原mtbe装置的甲醇原料泵的正常操作流量,因此第二原料泵23不能利用,需要更换。需要说明的是,混合器4用于混合脱除金属阳离子和碱性化合物等的原料与添加物叔丁醇。混合器4的类型可以根据使用需求进行预先设置,例如,混合器4可以利用原mtbe装置的混合器,或对混合器改造后再进行利用。需要说明的是,加热器5用于加热混合的原料与添加物,使其的温度达到进行叠合反应所需的温度。加热器5的类型可以根据使用需求进行预先设置,例如,加热器5可以利用原mtbe装置的加热器,或对加热器改造后再进行利用。示例地,经第一原料罐1缓冲、第一原料泵22升压后的原料,进入水洗塔2脱除其中的金属阳离子、碱性化合物等物质后,再与经第二原料罐3储存、第二原料泵23升压的添加物,例如叔丁醇,在混合器4内充分混合。之后混合好的混合原料经加热器5加热后进入叠合反应装置600进行异丁烯的叠合反应。可选地,参见图1,催化蒸馏装置400包括催化蒸馏塔7、第一重沸器8、第一冷凝器9、第一回流罐10和第一回流泵11;催化蒸馏塔7的一侧与叠和反应装置600的底部连接,催化蒸馏塔7的底部与第一重沸器8的进口连接,第一重沸器8的出口与催化蒸馏塔7的另一侧连接,催化蒸馏塔7的顶部与第一冷凝器9的一侧连接,第一冷凝器9的另一侧与第一回流罐10的顶部连接,第一回流罐10的底部与第一回流泵11的一侧连接,第一回流泵11的另一侧分别与催化蒸馏塔7的另一侧连接和产品输出装置连接。需要说明的是,催化蒸馏塔7用于将来自叠和反应装置600的叠合反应产物进行分离,其中催化蒸馏塔7塔底的物料即为第二反应产物,主要包括在叠和反应装置600及催化蒸馏塔7的反应段进行叠和反应生成的叠合产物和混合在其中的惰性添加物,催化蒸馏塔7塔顶的物料为剩余原料产品。催化蒸馏塔7的类型可以根据使用需求进行预先设置,例如,催化蒸馏塔7可以利用原mtbe装置的催化蒸馏塔,或对其改造后再进行利用。其中,催化蒸馏塔7包括从上至下顺次连通的精馏段、反应段和提馏段,精馏段的塔板数包括10~29块,反应段内的催化剂床层的层数包括2~16层,提馏段的塔板数包括13~35块;反应段的液时空速为0.5~5.0h-1,塔顶温度为50~70℃,反应段的温度为60~95℃,塔底温度为135~175℃,操作压力为0.5~0.8mpa;回流比0.5~2.5。示例地,精馏段的塔板数可以为10块、20块或29块等,反应段内的催化剂床层的层数可以为2层、8层或16层,提馏段的塔板数可以为13块、20块、30块或35块;反应段的液时空速可以为0.5h-1、1.5h-1、2.5h-1、3.5h-1或5.0h-1等,塔顶温度可以为50℃、60℃或70℃等,反应段的温度可以为60℃、75℃或95℃等,塔底温度可以为135℃、155℃或175℃等,操作压力可以为0.5mpa、0.6mpa、0.7mpa或0.8mpa等;回流比可以为0.5、1.5或2.5等。值得注意的是,若原mtbe装置采用的是共沸塔而不是催化蒸馏塔,相应地,异丁烯叠合系统也可采用共沸塔并利用原mtbe装置的共沸塔,或对该塔改造后再进行利用。需要说明的是,第一重沸器8用于给催化蒸馏塔7提供热源,使催化蒸馏塔7内的分离充分进行。由于催化蒸馏塔7塔底的温度较生产mtbe时塔底的温度高,因此不能利用原mtbe装置的重沸器,需要更换一台新的重沸器。需要说明的是,第一冷凝器9用于冷凝、冷却催化蒸馏塔7塔顶馏出物,第一回流罐10用于储存和缓冲催化蒸馏塔7的塔顶馏出物,第一回流泵11用于将第一回流罐10内液体升压,从而使得第一回流罐10内一部分液体回流至催化蒸馏塔7,另一部分作为剩余原料产品出装置。其中,第一冷凝器9、第一回流罐10和第一回流泵11均可利用原mtbe装置的催化蒸馏塔所附属的冷凝器、回流泵、回流罐,或对这些设备改造后再进行利用。需要说明的是,参见图2,若从催化蒸馏塔7输送至蒸馏装置500的第二反应产物和添加物的压力不满足蒸馏装置500所需的压力,则需要在催化蒸馏塔7与蒸馏装置500之间设置第三原料泵24。示例地,来自叠合反应装置600的第一反应产物进入催化蒸馏塔7,第一反应产物中未反应物料向催化蒸馏塔7的上部移动进入反应段进行叠合反应,获得叠合产物,催化蒸馏塔7塔底物料为第二反应产物,主要包括在反应器及催化蒸馏塔的反应段进行叠和反应生成的叠合产物与混合在其中的惰性添加物。其中叠合产物中未反应的异丁烯等物料离开反应段上升至精馏段,将其中的重组分分离出去后,离开塔顶并经第一冷凝器9冷凝、升压后分为两个部分:第一部分作为回流,返回至催化蒸馏塔7;另一部分为添加物含量小于或等于50mg/kg的剩余原料,其作为产品送出系统。催化蒸馏塔7塔底的第二反应产物经催化蒸馏塔7底部连接的第三原料泵24升压后送入蒸馏装置500。其中,在催化蒸馏塔7进行催化蒸馏的优点主要有三点:一是叠合反应产物即二聚物的浓度在反应段可以保持在较低的水平,从而抑制后续的多聚反应的发生;二是催化蒸馏还可把叠合反应所放出的反应热直接用于分离过程,从而降低能耗;三是叠合反应的反应温度容易控制,没有明显的热点,不需要冷却设备。可选地,参见图1,蒸馏装置500包括高压蒸馏装置与低压蒸馏装置;高压蒸馏装置包括高压塔12、第二重沸器13、第二冷凝器14、第二回流罐15和第二回流泵16;高压塔12的底部和第二重沸器13的进口连接,高压塔12的顶部与第二冷凝器14的一侧连接,第二冷凝器14的另一侧与第二回流罐15的顶部连接,第二回流罐15的底部与第二回流泵16的一侧连接,第二回流泵16的另一侧具有两个出液口,其中一个出液口与高压塔12塔顶的一侧连接,另一个出液口与低压塔17连接;低压蒸馏装置包括低压塔17、第三重沸器18、第三冷凝器19、第三回流罐20和第三回流泵21;低压塔17的一侧与第二回流泵16的另一侧连接,低压塔17的底部与混合器4的一侧连接,低压塔17的底部设置有第三重沸器18,低压塔17的顶部与第三冷凝器19的一侧连接,第三冷凝器19的另一侧与第三回流罐20的顶部连接,第三回流罐20的底部与第三回流泵21的一侧连接,第三回流泵21的另一侧分为两路,其中一路与低压塔17塔顶的另一侧连接,另一路与高压塔12连接。需要说明的是,高压蒸馏塔12用于对来自催化蒸馏塔7的第二反应产物与来自低压塔17的第二共沸产物的混合物进行分离,得到叠合产物与第一共沸产物。其中,高压塔12包括从上至下顺次连通的精馏段和提馏段;精馏段的塔板数为10~19块,提馏段的塔板数为12~24块。塔顶温度为120~150℃,塔底温度为170~210℃,操作压力为0.8~1.0mpa,回流比为0.2~2.2。示例地,精馏段的塔板数可以为10块、12块、15块或19块等,提馏段的塔板数可以为12块、16块、18块或24块等,塔顶温度可以为120℃、130℃、140℃或150℃等,塔底温度可以为170℃、190℃或210℃等,操作压力可以为0.8mpa、0.9mpa或1.0mpa等,回流比可以为0.2、0.8、1.4或2.2等。需要说明的是,第二重沸器13用于给高压塔12提供热源,第二冷凝器14用于冷凝、冷却高压塔12的塔顶馏出物,第二回流罐15用于储存和缓冲高压塔12的塔顶馏出物,第二回流泵16用于将第二回流罐15内液体升压,从而使得第二回流罐15内一部分液体回流至高压塔12,另一部分作为第一共沸物送至低压塔17作为低压塔17进料。值得注意的是,由于高压塔12在mtbe装置中无可利用设备,故该高压塔12、第二重沸器13、第二冷凝器14、第二回流罐15和第二回流泵16均为新增设备。需要说明的是,参见图2,高压蒸馏装置还可以包括换热器25和冷却器26。换热器25用于将高压塔12塔底得到的叠合油与送至低压塔17的产物进行换热,从而达到节能的目的。冷却器26用于冷却从高压塔12的塔底得到的叠合油,使其的温度达到产品输送所要求的温度。需要说明的是,低压塔17用于对来自高压塔12的第一共沸产物进行分离提纯。其中,低压塔17包括从上至下顺次连通的精馏段和提馏段;精馏段的塔板数为5~20块,提馏段的塔板数为25~50块。塔顶温度为65~80℃,塔底温度为85~100℃,操作压力为0.10~0.20mpa,回流比为0.5~4.0。示例地,精馏段的塔板数可以为5块、10块、15块或20块等,提馏段的塔板数可以为25块、30块、35块、40块、45块或50块等,塔顶温度可以为65℃、70℃、75℃或80℃等,塔底温度可以为85℃、90℃、95℃或100℃等,操作压力可以为0.10mpa、0.15mpa或0.20mpa等,回流比可以为0.5、1.5、2.5、3.5或4.0等。需要说明的是,第三重沸器18用于给低压塔17提供热源,第三冷凝器19用于冷凝、冷却低压塔17的塔顶馏出物,第三回流罐20用于储存和缓冲低压塔17的塔顶馏出物,第三回流泵21用于将第三回流罐20内液体升压,从而使得第三回流罐20内一部分液体回流至低压塔17,另一部分作为第二共沸产物送至高压塔12作为高压塔12的部分进料。值得注意的是,低压塔17、第三重沸器18、第三冷凝器19、第三回流罐20和第三回流泵21可以利用原mtbe装置中的甲醇回收塔及其附属的冷凝器、回流泵、回流罐、重沸器。需要说明的是,输送至蒸馏装置500的第二反应产物与添加物叔丁醇的混合物为二异丁烯与叔丁醇的共沸体系。其中,二异丁烯及叔丁醇间存在多种共沸体系,若含叔丁醇的共沸体系直接循环至叠合反应部分,由于共沸体系中含有大量的二异丁烯,过多的二异丁烯就会与原料中异丁烯反应生成三聚产物,三聚产物再与异丁烯反应生成四聚产物,从而有可能造成产品的辛烷值下降、产品的干点超标等问题,故应将添加物叔丁醇从二异丁烯与叔丁醇的共沸体系中分离出去。采用改变压力的方法可实现共沸体系的分离。利用大型化工流程模拟软件aspenplus的unifac物性模型,对不同操作压力下二异丁烯(以2,4,4-三甲基戊烯为代表)与叔丁醇共沸体系的共沸组成、共沸温度及二异丁烯沸点进行了计算,结果见表2。表2不同压力下叔丁醇与二异丁烯共沸体系的共沸组成及二异丁烯沸点由表2可见,以2,4,4-三甲基戊烯为代表的二异丁烯与叔丁醇共沸体系,随着压力的增大,共沸体系中叔丁醇的摩尔分数增大,因此可以看出共沸体系对压力较敏感,因而采用改变压力方法将叔丁醇从以二异丁烯为主要组分的叠合油中分离出来,这在理论上是完全可行的。由表2也可以看出,当压力超过0.20mpa时,共沸体系组成变化幅度呈下降趋势;当在压力超过1.0mpa时,共沸体系中二异丁烯的沸点温度超过210℃。作为一种示例,本申请通过实验发现,当压力为1.1mpa时,其沸点温度为216.97℃,在这样的温度下,二异丁烯易聚合且常规加热介质已不适合做重沸器热源。示例地,根据上述操作原理,来自催化蒸馏塔7塔底的第二反应产物与来自低压塔17的第二共沸产物的混合物经催化蒸馏塔7塔底的第三原料泵24升压后送入高压塔12。在高压塔12的塔底得到叔丁醇含量小于或等于100mg/kg、主要成分为二异丁烯的叠合油产品,这部分叠合油经换热器25与低压塔17的进料进行换热、经冷却器26冷却至40℃左右后作为产品输出装置;在高压塔12的塔顶得到二异丁烯与叔丁醇的共沸产物,这部分共沸产物中叔丁醇的摩尔组成为77.0~78.0%,经第二回流泵16升压后一部分作为回流,另一部分作为第一共沸产物经降压后送至低压塔17作为低压塔17进料。由于压力的改变,共沸体系中叔丁醇的摩尔组成由进料时的77.0~78.0%降低至64.5~70.5%,从而可在低压塔17的塔底得到摩尔纯度大于99.99%的叔丁醇,这部分叔丁醇基本不含二异丁烯,这部分叔丁醇升压后再循环至混合器4中继续作为添加物;在低压塔17的塔顶得到叔丁醇的摩尔组成为64.5~70.5%的二异丁烯与叔丁醇的共沸物,这部分共沸物一部分经第三回流泵21升压后作为回流,另一部分作为第二共沸产物升压后返至高压塔12,与来自催化蒸馏塔底7的物流混合后作为高压塔12的进料。值得注意的是,参见图2,当经第三回流泵21升压后返回至高压塔12的另一部分的压力仍不满足高压塔12所需的压力时,可在第三回流泵21与高压塔12之间设置共沸物泵27,该共沸物泵27用于对该部分物料进行升压。其中,共沸物泵27不能利用原有的mbte装置。值得注意的是,由于叔丁醇及二异丁烯间存在多种共沸物,若将含叔丁醇的共沸物直接循环至叠合反应装置600中,由于共沸物中含有大量的二异丁烯,过多的二异丁烯就会与第一原料中的异丁烯进行反应,从而会生成三聚体,三聚体再与第一原料中的异丁烯反应,会生成四聚体,进而有可能会造成最终的异丁烯叠合产物的辛烷值下降、干点超标。而采用高压蒸馏和低压蒸馏的变压蒸馏手段,可以分离出共沸物中的叔丁醇和二异丁烯,从而可以使得循环至叠合反应装置600中的共沸物仅为叔丁醇,进而保证了最终的异丁烯叠合产物具有较高的辛烷值和干点不超标。与cn109354567a所介绍的抑制剂回收单元相比,采用本申请实施例所提供的高压蒸馏装置和低压蒸馏装置可以将共沸物中的叔丁醇和二异丁烯分离开,而且,由于未采用萃取水,因此返回至叠合反应装置600中的叔丁醇不含水,进而可以保证第一原料中的异丁烯不会与水进行反应,从而避免了过多的叔丁醇的生成导致产品严重变质问题,也不存在萃取水定期排放时含醇污水较难处理的问题。第二方面,本申请实施例提供了一种异丁烯叠合方法,该方法用于上述任一的异丁烯叠合系统。参见图3,该方法包括以下步骤:步骤101:原料与脱除剂在预处理装置100混合后脱除原料中的金属阳离子和碱性化合物,得到第一原料。需要说明的是,原料在与脱除剂进行混合前,原料需要先经过第一原料罐1的缓冲,在经过第一原料泵升压至1.0~1.8mpa,从而使得第一原料的压力满足所需。示例地,原料可以被升压至1.0mpa、1.5mpa或1.8mpa等。需要说明的是,脱除剂用于吸收原料中的金属阳离子和碱性化合物。脱除剂可以为脱氧水、除盐水或凝结水,脱除剂的质量占原料的质量的25~35%,示例地,脱除剂的质量可以占原料质量的25%、30%或35%等。需要说明的是,原料在预处理装置100中经过脱除剂水洗后会产生污水,污水中的含量油小于等于200mg/kg,较为清洁,可直接用作常减压、催化裂化、加氢等装置的注水或直接排至污水处理厂进行处理。步骤102:第一原料与添加物在混合装置200中进行混合,得到混合原料。需要说明的是,添加物用于抑制叠合反应的副反应,从而达到降低三聚、四聚副反应产物产率的目的。示例地,添加物可以为叔丁醇。随着叔丁醇含量的增加,其覆盖催化剂活性中心的比例也相应增加,从而会造成异丁烯转化率的降低,进而会使得三聚副反应产物和四聚副反应产物的生成量减少,提高了二异丁烯的选择性。作为添加物的叔丁醇与第一原料中所含异丁烯的摩尔比为0.01~0.09:1。示例地,摩尔比可以为0.01:1、0.03:1、0.05:1、0.07:1或0.09:1等。需要说明的是,添加物在开工阶段需一次性购买,在正常生产时由蒸馏装置500分离出并循环使用。但添加物在与第一原料混合前,添加物的压力须达到1.0~1.8mpa,从而使得添加物与第一原料的充分混合。示例地,添加物的压力可以为1.0mpa、1.5mpa或1.8mpa等。需要说明的是,第一原料与添加物进行混合后,其压力为0.8~1.6mpa。示例地,压力可以为0.8mpa、1.2mpa或1.6mpa等。需要说明的是,混合原料在进入叠和反应装置600之前需要对混合原料进行加热,使其温度达到50~95℃,从而使得后续的叠合反应高效地进行。示例地,加热所达到的温度可以为50℃、65℃、80℃或95℃等。值得注意的是,在第一原料与添加物混合时,还可以混合脱氧水。脱氧水不但可以抑制叠合反应副反应的进行,还可以与第一原料中的异丁烯在阳离子交换树脂催化剂的作用下反应生成叔丁醇作为添加物,从而可以保证整个反应系统里循环的添加物的量保持不变。步骤103:混合原料在叠合反应装置600中进行叠合反应,得到第一反应产物。需要说明的是,由于混合原料中具有添加物,因此混合原料在进行叠合反应时,其主要进行的是二聚反应。需要说明的是,混合原料的叠合反应转化率≥92%,其中,生成的叠合产物中c8烯烃的选择性≥90%,c12烯烃的选择性<10%。步骤104:第一反应产物在催化蒸馏装置400中进行进一步反应与分离,得到第二反应产物与剩余原料产品。需要说明的是,第一反应产物中仍含有一部分未反应物料。该物料会向催化蒸馏塔7的上部移动,从而进入催化蒸馏塔7的反应段进行叠和反应,最终在催化蒸馏塔7底部得到第二反应产物,在催化蒸馏塔7顶部得到剩余原料产品。需要说明的是,第二反应产物为催化蒸馏塔的塔底物料,主要包括在反应器及催化蒸馏塔的反应段进行叠和反应生成的叠合产物与混合在其中的添加物。需要说明的是,未反应的原料会离开反应段上升至精馏段,在精馏段将其中所含有的重组分分离出去后,离开催化蒸馏塔7的塔顶并经第一冷凝器9冷凝及冷却后进入第一回流罐10,再经第一回流泵11升压后分为两部分:一部分作为回流,另一部分作为剩余原料产品送出装置。需要说明的是,第一反应产物在催化蒸馏装置400中进行进一步反应与分离,包括在如下操作条件下对第一反应产物进行反应与分离操作:催化蒸馏塔7的反应温度为60~95℃,操作压力为0.5~0.8mpa。示例地,反应温度可以为60℃、75℃或95℃等,操作压力可以为0.5mpa、0.6mpa、0.7mpa或0.8mpa等。步骤105:第二反应产物中的异丁烯叠合产物和添加物在蒸馏装置500中蒸馏,得到异丁烯叠合产物。需要说明的是,第二反应产物中的异丁烯叠合产物和添加物在蒸馏装置500中蒸馏,得到叠合产物,包括:对第二反应产物中的异丁烯叠合产物和添加物在蒸馏装置500中的高压塔12内蒸馏,得到异丁烯叠合产物与第一共沸产物,将该叠合油作为该叠合产物;对第一共沸产物在低压塔17内进一步蒸馏,可以得到添加物和第二共沸产物,添加物用于与第一原料混合,第二共沸产物用于与第二反应产物进行混合,进行进一步地蒸馏。需要说明的是,对第二反应产物中的异丁烯叠合产物和添加物在蒸馏装置500中蒸馏,包括在如下操作条件下对第二反应产物进行蒸馏:其中高压塔12的塔顶温度为120~150℃,塔底温度为170~210℃,操作压力为0.8~1.0mpa,回流比为0.2~2.2;低压塔17的塔顶温度为65~80℃,塔底温度为85~100℃,操作压力为0.10~0.20mpa,回流比为0.5~4.0。示例地,高压塔12的塔顶温度可以为120℃、130℃、140℃或150℃等,塔底温度可以为170℃、180℃、190℃、200℃或210℃等,操作压力可以为0.8mpa、0.9mpa或1.0mpa等,回流比可以为0.2、0.6、1.0、1.4、1.8或2.2等;低压塔17的塔顶温度可以为65℃、70℃、75℃或80℃等,塔底温度可以为85℃、90℃、95℃或100℃等,操作压力可以为0.10mpa、0.15mpa或0.20mpa等,回流比可以为0.5、1.0、1.5、2.0、2.5、3.0、3.5或4.0等。为使本申请的技术方案和优点更加清楚,以下将通过可选地实施例进行详细阐述。实施例某炼油厂原有一套产量为8万吨/年的mtbe装置,该装置的加工原料为来自上游气分装置的混合c4原料。混合c4原料的组成参见表3。进料量为32.82吨/小时,年处理量为27.57万吨/年。表3混合c4原料组成序号混合c4原料组成质量分数1c3h60.07172c3h80.12313nc4h106.44054ic4h1044.95125nc4h89.88306ic4h822.17947tc4h810.82978cc4h85.5203相关技术提供的异丁烯叠合系统的主要工艺流程见图4:首先混合c4原料自外界进入碳四原料罐,用碳四原料泵将碳四原料送至混合器与甲醇完全混合。从界区来的新鲜甲醇和装置内的循环甲醇进入甲醇原料罐,经甲醇原料泵增压后在混合器中与碳四原料充分混合。混合后的物料经加热器预热至反应温度后再进入醚化反应器,醚化反应器中装大孔的阳离子交换树脂叠合催化剂,异丁烯与甲醇在催化剂的作用下反应生成mtbe。醚化反应器流出的反应产物经换热器加热后进入催化蒸馏塔,在催化蒸馏塔内未反应的异丁烯与甲醇同时进行反应和分馏,随着反应的进行,mtbe产品也不断被分离出来,这样有利于反应向生成mtbe的方向进行,催化蒸馏塔的塔底得到合格的mtbe产品,该mtbe产品经催化蒸馏塔底泵升压、换热器换热及mtbe产品冷却器冷却后送至罐区贮存。反应剩余的甲醇与未反应c4形成共沸物从塔顶流出,经冷凝器1冷凝后进入回流罐1,再经回流泵1升压后分为两部分:一部分作为回流,另一部分从底部进入甲醇萃取塔,在甲醇萃取塔内与萃取水逆流接触,反应剩余的甲醇被水从c4中萃取出来,在甲醇萃取塔的塔顶得到基本上不含甲醇的剩余c4,作为产品送出装置到罐区贮存。从甲醇萃取塔的底部流出的甲醇与萃取水混合物,经萃取水换热器换热后进入甲醇回收塔,在甲醇回收塔内进行萃取水和甲醇的分离,甲醇回收塔的塔顶的甲醇蒸气经冷凝器2冷凝后进入回流罐2,再经回流泵2升压后分为两部分:一部分作为回流,另一部分循环至反应部分。已脱除甲醇的萃取水自甲醇回收塔的塔底流出并经萃取水循环泵加压、萃取水换热器换热、萃取水冷却器冷却后循环至甲醇萃取塔。由于需要,本申请中通过将mtbe装置改造为异丁烯叠合系统,可以生产出高辛烷值的叠合油和可循环使用的高纯度添加物,其中叠合油可以作为乙醇汽油的调合组分,添加物可以循环至混合装置与原料混合。通过本申请提供的异丁烯叠合系统对异丁烯进行叠合反应,其中,改造后装置物料平衡及叠合油组成分别见表4和表5。表4改造后物料平衡表备注:表4中叠合油出料72751.3t/a中含叔丁醇7.3t/a,剩余c4出料202938.9t/a中含叔丁醇1.7t/a。表5叠合油组成序号叠合油组成质量分数(%)1c6~c70.742c8烯烃90.793c9~c110.204c12烯烃8.235c12+0.036叔丁醇0.017合计100.00装置改造后的主要设备规格或型号、数量、操作介质、操作温度、操作压力及设备利用情况见表6。表6异丁烯叠合系统主要设备操作条件及利用情况备注:在泵类的操作压力栏中,第一个数字为泵的入口操作压力,第二个数字为泵的出口操作压力。从表6可以看出,本申请出的流程可使原mtbe装置中绝大部分设备得到利用,从而降低了异丁烯叠合装置的建设费用。上述所有可选技术方案,可以采用任意结合形成本公开的可选实施例,在此不再一一赘述。以上所述仅为本发明的说明性实施例,并不用以限制本发明的保护范围,凡在本发明的精神和原则之内,所作的任何修改、等同替换、改进等,均应包含在本发明的保护范围之内。当前第1页1 2 3