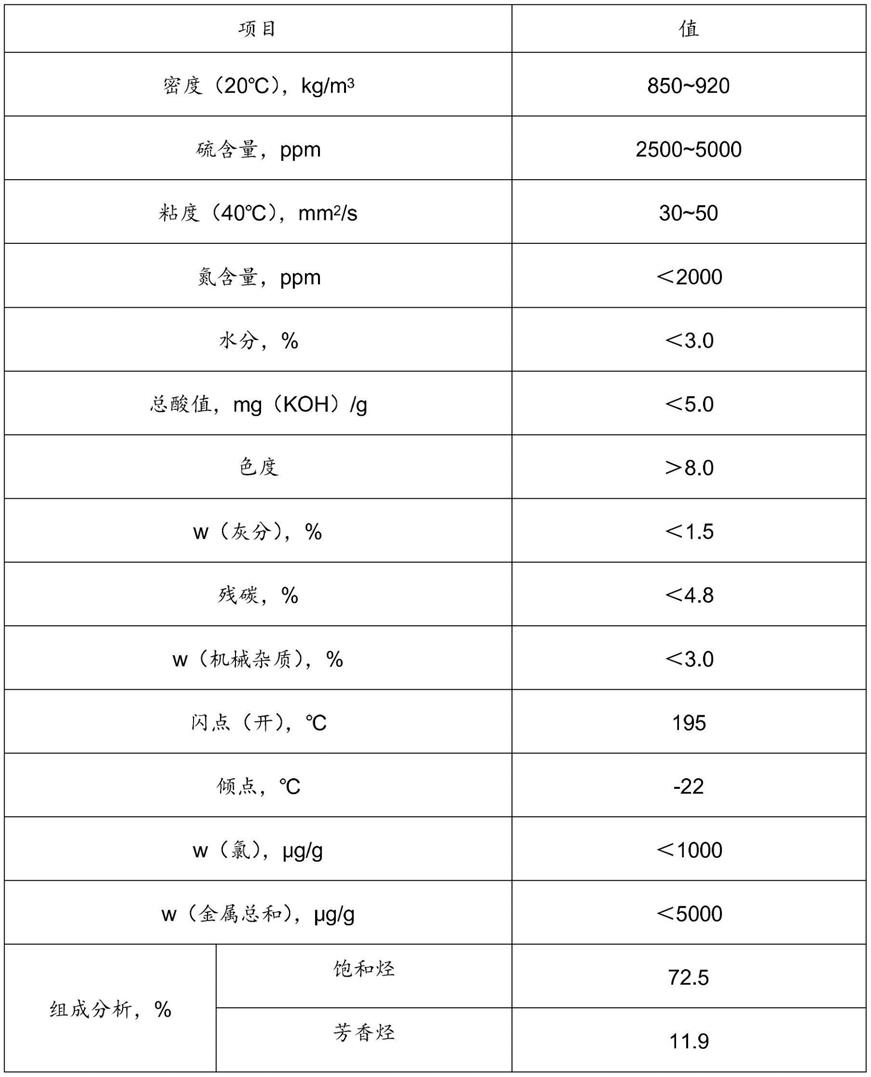
1.本发明涉及废润滑油回收技术领域,具体是一种废润滑油回收利用工艺。
背景技术:2.废润滑油作为一种可再生的工业危废,大部分被处理成非标燃料油、非标汽油、非标柴油流向市场,小部分再生成基础油,资源浪费严重。随着石油资源的日益紧张及环保意识的增强,废润滑油的回收再利用受到了社会各界的广泛关注,研究符合客观实际的再生工艺,确定适宜的操作条件已成为有效处理hw08类危险固废——废润滑油,提高石油资源利用率、减少环境污染的关键。用废润滑油作为原料,不仅解决了废润滑油带来的环境污染和资源浪费的问题还提高了废润滑油的经济效益。
3.润滑油在使用的过程中由于高温、空气氧化,逐渐老化变质,再加上机械部件摩擦产生的金属粉末、从环境中进入的水分、杂质等,造成矿物油等污染、氧化,因此,废润滑油中除了常规润滑油成分外,还会含有少量的其他元素,包括fe、cu、al、ni、pb、na、ca、zn、mg、b、si、mo等。其中:fe、cu、al、ni和pb属于磨损金属元素;si是吸入的灰尘;b和na是混入的防冻剂;mg、ca、zn和mo是添加剂元素。
4.废润滑油回收利用的方法有:硫酸-白土工艺、加氢精制工艺、分子蒸馏工艺、溶剂精制工艺、膜分离工艺等。硫酸-白土工艺反应残留的酸渣与碱渣对环境造成了很大的影响,该工艺会逐渐被市场所淘汰;溶剂精制工艺对溶剂的损耗很大,同时基础油的收率较低,基础油产品的含硫量较高;膜分离工艺对膜材料要求较高,开发合适的膜材料成为面临的最大问题;分子蒸馏工艺过程中会发生相变,能耗大。加氢精制工艺是废润滑油处理的最终路线,加氢精制的工艺路线十分清晰,主要问题是在催化剂的适应性与持久性上,油品中的杂质对催化剂寿命的影响很明显,催化剂失活加氢装置就无法生产。
技术实现要素:5.针对现有技术存在的技术问题,本发明提供一种废润滑油回收利用工艺,该工艺可适用于氧化时间长、金属含量高的废润滑油,生产符合标准要求的精制汽油、精制柴油、基础油馏分。
6.本发明提供的一种废润滑油回收利用工艺,包括下述步骤:
7.s1、破乳:向废润滑油中加入破乳剂进行破乳处理,得到油水混合物;
8.s2、脱水:将所述油水混合物进行油水分离处理,得到油品;
9.s3、脱金属:向所述油品中加入絮凝剂进行脱金属处理;
10.s4、加氢精制:将脱金属处理后的油品加热至320-370℃,与氢气进行加氢精制处理;
11.s5、气液分离:将加氢精制处理后的油品进行气液分离处理;
12.s6、脱酸:将气液分离处理后的油品进行脱酸处理;
13.s7、常减压蒸馏:将脱酸处理后的油品加热至320-370℃,进行馏程切割处理得到
合格产品。
14.优选地,s1中,所述破乳剂为酰胺、烷基胺聚氧乙烯、聚丙烯酰胺、油酸、多乙烯多胺、烷基二乙醇胺、氢氧化钠中的至少两种混合或聚合而成。
15.优选地,s2中,将所述油水混合物通入汽提脱水塔进行油水分离;其中,所述汽提脱水塔的塔顶操作温度为230-250℃,塔底操作温度为340-360℃,塔顶操作压力为180-200kpa,压降为50kpa。
16.优选地,s3中,所述絮凝剂为氢氧化钠、氢氧化钾、硅酸钠中的一种和三乙烯四胺、乙二酸、二乙烯三胺、聚酰亚胺中的一种混合而成的复合型碱性絮凝剂。
17.优选地,s3中,所述脱金属处理在脱金属罐中进行,所述脱金属罐的底部设有金属排除装置;所述脱金属处理中,搅拌时间为1-2h,静置时间为3-5h,操作温度为60-70℃,操作压力为常压。
18.优选地,s4中,所述加氢精制处理在加氢反应系统中进行;所述加氢反应系统包括四台串联的脱硫反应器、精制反应器、脱氧反应器和补充精制反应器。
19.优选地,所述脱硫反应器中填充加氢脱硫催化剂,所述脱硫反应器的操作温度为350-400℃,操作压力为17-22mpa,氢油体积比为300-1000:1,体积空速为0.3-1.5h-1
;所述精制反应器中填充贵金属加氢精制催化剂,所述精制反应器的操作温度为350-400℃,操作压力为17-22mpa,氢油体积比为300-1000:1,体积空速为0.3-1.5h-1
;所述脱氧反应器中填充加氢脱氧催化剂,所述脱氧反应器的操作温度为350-400℃,操作压力为17-22mpa,氢油体积比为300-1000:1,体积空速为0.3-1.5h-1
;所述补充精制反应器中填充贵金属加氢精制催化剂,所述补充精制反应器的操作温度为300-350℃,操作压力为15-20mpa,氢油体积比为300-1000:1,体积空速为0.3-1.5h-1
。
20.优选地,s5中,所述气液分离处理在气液分离系统中进行;所述气液分离系统包括:热高压分离器、冷高压分离器、热低压分离器和冷低压分离器,其中,所述冷高压分离器的顶部排出循环氢,所述冷低压分离器的顶部排出低分气,所述冷高压分离器和所述冷低压分离器的底部均设有含油污水排出装置。
21.优选地,s6中,所述脱酸处理在汽提塔中进行,所述汽提塔的顶部和中部各设有一个进料口;所述汽提塔的塔顶操作温度为125-145℃,塔底操作温度为235-255℃,塔顶操作压力为700-900kpa,压降为100kpa。
22.优选地,s7中,所述馏程切割处理在减压精馏塔中进行;所述减压精馏塔的塔顶操作温度为110-125℃,塔底操作温度为310-330℃,塔顶操作压力为15-25kpa,压降为60kpa;所述减压精馏塔的塔顶采出精制汽油,中上段采出精制柴油,塔底采出基础油馏分。
23.相对于现有技术,本发明的有益效果为:本发明通过采用絮凝剂高效脱除油品中含有的金属等杂质,有效降低加氢过程中结焦现象的产生,同时工艺简单、操作灵活,工艺过程中污染小,能够实现废润滑油回收利用,具有巨大的社会效益和经济效益。
附图说明
24.图1为本发明实施例一种废润滑油回收利用工艺的流程图。
具体实施方式
25.为了使本发明实现的技术手段、创作特征、达成目的与功效易于明白了解,下面结合具体图示,进一步阐述本发明。
26.实施例1
27.参照图1,一种废润滑油回收利用工艺,包括下述步骤:
28.s1、破乳:将流量为27000kg/h的废润滑油通入破乳罐,加入破乳剂进行破乳处理,得到油水混合物;所述破乳剂为酰胺、烷基胺聚氧乙烯混合而成;
29.s2、脱水:将所述油水混合物通入汽提脱水塔采用流量为300kg/h、温度为350℃的汽提蒸汽进行油水分离处理,得到油品;油气、不凝气、含油污水从塔顶采出,流量为250kg/h,所述汽提脱水塔的塔顶操作温度为240℃,塔底操作温度为350℃,塔顶操作压力为190kpa,压降为50kpa;
30.s3、脱金属:将所述油品通入带有搅拌器的脱金属罐,加入絮凝剂对油品中含有的少量fe、cu、al、ni、pb、na、ca、zn、mg金属进行脱金属处理;所述絮凝剂为氢氧化钠和三乙烯四胺混合而成的复合型碱性絮凝剂;所述脱金属罐的底部设有金属排除装置;所述脱金属处理中,搅拌时间为1.5h,静置时间为4h,操作温度为65℃,操作压力为常压,金属杂质由所述金属排除装置排出,金属脱除率高达98%;
31.s4、加氢精制:将脱金属处理后流量为25000kg/h的油品经过加热炉加热至350℃,与氢气先通入填充有ni系催化剂,操作温度为380℃,操作压力为20mpa,氢油体积比为500:1,体积空速为0.5h-1
的脱硫反应器进行加氢脱硫,再通入填充有主要成分为pd-pt的贵金属催化剂,操作温度为370℃,操作压力为20mpa,氢油体积比为500:1,体积空速为0.5h-1
的精制反应器进行加氢精制,再通入填充有主要成分为co-mo的加氢脱氧催化剂,操作温度为360℃,操作压力为20mpa,氢油体积比为500:1,体积空速为0.5h-1
的脱氧反应器进行加氢脱氧,最后通入填充有主要成分为pd-pt的贵金属加氢精制催化剂,操作温度为330℃,操作压力为18mpa,氢油体积比为500:1,体积空速为0.5h-1
的补充精制反应器再进行加氢精制;
32.s5、气液分离:将加氢精制处理后流量为31200kg/h的油品通入气液分离系统进行气液分离处理;所述气液分离系统包括:热高压分离器、冷高压分离器、热低压分离器和冷低压分离器,循环氢由冷高压分离器的顶部排出,流量为5500kg/h,含油污水由冷高压分离器的底部排出,流量为125kg/h,热低分油由热低压分离器的底部排出,流量为24450kg/h,冷低分油由冷低压分离器的底部排出,流量为900kg/h,含油污水由冷低压分离器的底部排出,流量为25kg/h,低分气由冷低压分离器的顶部排出,流量为200kg/h;
33.s6、脱酸:气液分离后的冷低分油和冷高分油分别从汽提塔的顶部和中部通入汽提塔,采用流量为200kg/h,温度为350℃的汽提蒸汽进行脱酸处理;所述汽提塔的塔顶操作温度为130℃,塔底操作温度为240℃,塔顶操作压力为800kpa,压降为100kpa;酸性干气由塔顶的分液罐顶部采出,流量为250kg/h,含油污水由塔顶的分液罐底部采出,流量为140kg/h;
34.s7、常减压蒸馏:将脱酸处理后流量为25160kg/h的油品经过加热炉加热至350℃,通入设有中间换热和侧线汽提塔的减压蒸馏塔采用流量为500kg/h,温度为350℃的汽提蒸汽,进行馏程切割得到合格产品;所述减压精馏塔的塔顶操作温度为115℃,塔底操作温度为320℃,塔顶操作压力为20kpa,压降为60kpa;所述减压蒸馏塔的塔顶设有回流罐,中上段
设有测线汽提塔,中段设有中间冷凝器;所述回流罐的顶部设有不凝气排放口,底部设有含油污水排放口;所述不凝气排放口排出流量为100kg/h的不凝气去火炬燃烧,所述含油污水排放口排出流量为510kg/h的含油污水,所述减压精馏塔的塔顶采出流量为250kg/h的精制汽油,中上段采出流量为1100kg/h的精制柴油,塔底采出流量为23700kg/h的基础油馏分。
35.实施例2
36.参照图1,一种废润滑油回收利用工艺,包括下述步骤:
37.s1、破乳:将流量为27000kg/h的废润滑油通入破乳罐,加入破乳剂进行破乳处理,得到油水混合物;所述破乳剂为聚丙烯酰胺、油酸混合而成;
38.s2、脱水:将所述油水混合物通入汽提脱水塔采用流量为300kg/h、温度为350℃的汽提蒸汽进行油水分离处理,得到油品;油气、不凝气、含油污水从塔顶采出,流量为250kg/h,塔顶操作温度为230℃,塔底操作温度为340℃,塔顶操作压力为180kpa,压降为50kpa;
39.s3、脱金属:将所述油品通入带有搅拌器的脱金属罐,加入絮凝剂对油品中含有的少量fe、cu、al、ni、pb、na、ca、zn、mg金属进行脱金属处理;所述絮凝剂为氢氧化钾和乙二酸混合而成的复合型碱性絮凝剂;所述脱金属罐的底部设有金属排除装置;所述脱金属处理中,搅拌时间为1h,静置时间为3h,操作温度为60℃,操作压力为常压,金属杂质由所述金属排除装置排出,金属脱除率高达98%;
40.s4、加氢精制:将脱金属处理后流量为25000kg/h的油品经过加热炉加热至320℃,与氢气先通入填充有ni系催化剂,操作温度为350℃,操作压力为17mpa,氢油体积比为300:1,体积空速为0.3h-1
的脱硫反应器进行加氢脱硫,再通入填充有主要成分为pd-pt的贵金属催化剂,操作温度为350℃,操作压力为17mpa,氢油体积比为300:1,体积空速为0.3h-1
的精制反应器进行加氢精制,再通入填充有主要成分为co-mo的加氢脱氧催化剂,操作温度为350℃,操作压力为17mpa,氢油体积比为300:1,体积空速为0.3h-1
的脱氧反应器进行加氢脱氧,最后通入填充有主要成分为pd-pt的贵金属加氢精制催化剂,操作温度为300℃,操作压力为15mpa,氢油体积比为300:1,体积空速为0.3h-1
的补充精制反应器再进行加氢精制;
41.s5、气液分离:将加氢精制处理后流量为31200kg/h的油品通入气液分离系统进行气液分离处理;所述气液分离系统包括:热高压分离器、冷高压分离器、热低压分离器和冷低压分离器,循环氢由冷高压分离器的顶部排出,流量为5500kg/h,含油污水由冷高压分离器的底部排出,流量为125kg/h,热低分油由热低压分离器的底部排出,流量为24450kg/h,冷低分油由冷低压分离器的底部排出,流量为900kg/h,含油污水由冷低压分离器的底部排出,流量为25kg/h,低分气由冷低压分离器的顶部排出,流量为200kg/h;
42.s6、脱酸:气液分离后的冷低分油和冷高分油分别从汽提塔的顶部和中部通入汽提塔,采用流量为200kg/h,温度为350℃的汽提蒸汽进行脱酸处理;所述汽提塔的塔顶操作温度为125℃,塔底操作温度为235℃,塔顶操作压力为700kpa,压降为100kpa;酸性干气由塔顶的分液罐顶部采出,流量为250kg/h,含油污水由塔顶的分液罐底部采出,流量为140kg/h;
43.s7、常减压蒸馏:将脱酸处理后流量为25160kg/h的油品经过加热炉加热至320℃,通入设有中间换热和侧线汽提塔的减压蒸馏塔采用流量为500kg/h,温度为350℃的汽提蒸汽,进行馏程切割得到合格产品;所述减压精馏塔的塔顶操作温度为110℃,塔底操作温度为310℃,塔顶操作压力为15kpa,压降为60kpa;所述减压蒸馏塔的塔顶设有回流罐,中上段
设有测线汽提塔,中段设有中间冷凝器;所述回流罐的顶部设有不凝气排放口,底部设有含油污水排放口;所述不凝气排放口排出流量为100kg/h的不凝气去火炬燃烧,所述含油污水排放口排出流量为510kg/h的含油污水,所述减压精馏塔的塔顶采出流量为250kg/h的精制汽油,中上段采出流量为1100kg/h的精制柴油,塔底采出流量为23700kg/h的基础油馏分。
44.实施例3
45.参照图1,一种废润滑油回收利用工艺,包括下述步骤:
46.s1、破乳:将流量为27000kg/h的废润滑油通入破乳罐,加入破乳剂进行破乳处理,得到油水混合物;所述破乳剂为多乙烯多胺、烷基二乙醇胺、氢氧化钠聚合而成;
47.s2、脱水:将所述油水混合物通入汽提脱水塔采用流量为300kg/h、温度为350℃的汽提蒸汽进行油水分离处理,得到油品;油气、不凝气、含油污水从塔顶采出,流量为250kg/h,塔顶操作温度为250℃,塔底操作温度为360℃,塔顶操作压力为200kpa,压降为50kpa;
48.s3、脱金属:将所述油品通入带有搅拌器的脱金属罐,加入絮凝剂对油品中含有的少量fe、cu、al、ni、pb、na、ca、zn、mg金属进行脱金属处理;所述絮凝剂为硅酸钠和二乙烯三胺混合而成的复合型碱性絮凝剂;所述脱金属罐的底部设有金属排除装置;所述脱金属处理中,搅拌时间为2h,静置时间为5h,操作温度为70℃,操作压力为常压,金属杂质由所述金属排除装置排出,金属脱除率高达98%;
49.s4、加氢精制:将脱金属处理后流量为25000kg/h的油品经过加热炉加热至370℃,与氢气先通入填充有ni系催化剂,操作温度为400℃,操作压力为22mpa,氢油体积比为1000:1,体积空速为1.5h-1
的脱硫反应器进行加氢脱硫,再通入填充有主要成分为pd-pt的贵金属催化剂,操作温度为400℃,操作压力为22mpa,氢油体积比为1000:1,体积空速为1.5h-1
的精制反应器进行加氢精制,再通入填充有主要成分为co-mo的加氢脱氧催化剂,操作温度为400℃,操作压力为22mpa,氢油体积比为1000:1,体积空速为1.5h-1
的脱氧反应器进行加氢脱氧,最后通入填充有主要成分为pd-pt的贵金属加氢精制催化剂,操作温度为350℃,操作压力为20mpa,氢油体积比为1000:1,体积空速为1.5h-1
的补充精制反应器再进行加氢精制;
50.s5、气液分离:将加氢精制处理后流量为31200kg/h的油品通入气液分离系统进行气液分离处理;所述气液分离系统包括:热高压分离器、冷高压分离器、热低压分离器和冷低压分离器,循环氢由冷高压分离器的顶部排出,流量为5500kg/h,含油污水由冷高压分离器的底部排出,流量为125kg/h,热低分油由热低压分离器的底部排出,流量为24450kg/h,冷低分油由冷低压分离器的底部排出,流量为900kg/h,含油污水由冷低压分离器的底部排出,流量为25kg/h,低分气由冷低压分离器的顶部排出,流量为200kg/h;
51.s6、脱酸:气液分离后的冷低分油和冷高分油分别从汽提塔的顶部和中部通入汽提塔,采用流量为200kg/h,温度为350℃的汽提蒸汽进行脱酸处理;所述汽提塔的塔顶操作温度为145℃,塔底操作温度为255℃,塔顶操作压力为900kpa,压降为100kpa;酸性干气由塔顶的分液罐顶部采出,流量为250kg/h,含油污水由塔顶的分液罐底部采出,流量为140kg/h;
52.s7、常减压蒸馏:将脱酸处理后流量为25160kg/h的油品经过加热炉加热至370℃,通入设有中间换热和侧线汽提塔的减压蒸馏塔采用流量为500kg/h,温度为350℃的汽提蒸汽,进行馏程切割得到合格产品;所述减压精馏塔的塔顶操作温度为125℃,塔底操作温度
为330℃,塔顶操作压力为25kpa,压降为60kpa;所述减压蒸馏塔的塔顶设有回流罐,中上段设有测线汽提塔,中段设有中间冷凝器;所述回流罐的顶部设有不凝气排放口,底部设有含油污水排放口;所述不凝气排放口排出流量为100kg/h的不凝气去火炬燃烧,所述含油污水排放口排出流量为510kg/h的含油污水,所述减压精馏塔的塔顶采出流量为250kg/h的精制汽油,中上段采出流量为1100kg/h的精制柴油,塔底采出流量为23700kg/h的基础油馏分。
53.实施例1-3中废润滑油的性质如下表所示:
[0054][0055][0056]
以上仅为本发明的实施方式,并非因此限制本发明的专利范围,凡是利用本发明
说明书及附图内容所作的等效结构,直接或间接运用在其他相关的技术领域,均同理在本发明的专利保护范围之内。