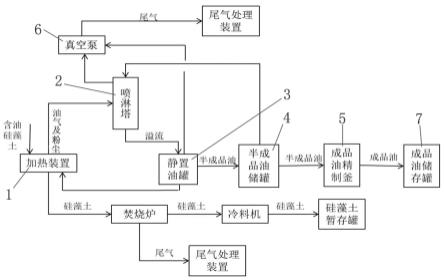
[0001] 本实用新型属于战略性新型产业目录之7 节能环保产业中的7.3 资源循环利用产业重点方向下7.3.2固体废物综合利用 煤矸石、粉煤灰、脱硫石膏、磷石膏、化工废渣、冶炼废渣、尾矿等固体废物的二次利用或综合利用和技术装备;或7.3.6资源再生利用废矿物油再生利用,包括废矿物油过滤与分离设备、减压蒸馏设备记忆溶剂精制、加氢精制设备。
背景技术:[0002]
钢、铁、铝箔带板生产企业产生的废弃含油硅藻土一般含轧制油20%-35%,为了减少资源浪费,通常会将轧制油提取出来。目前含油硅藻土提油方法主要有酸洗法提油、热蒸汽加热提油和电磁涡流加热提油,采用热蒸汽加热提油和电磁涡流加热提油时,为了使硅藻土加热均匀一般在加热时伴随搅拌过程,搅拌的同时会产生粉尘随油气一起进入下一道工序,在进行油气回收时一般需要先除尘,现有除尘设备一般采用旋风除尘器/布袋除尘器/脉冲除尘器等,这些除尘设备在实际运行中要么很容易发生堵塞检修频繁,要么除尘效率低下,无法适应含油硅藻土处理系统除尘,影响工作效率,加高生产成本。
技术实现要素:[0003]
本实用新型为了解决油气和粉尘堵塞除尘装置的技术问题,提供一种新型的含油硅藻土资源化处理系统,摒弃现有的除尘设备,采用喷淋塔代替除尘器,除尘效率高,不会发生堵塞,检修难度低。
[0004]
本实用新型的目的是以下述方式实现的:
[0005]
一种含油硅藻土资源化处理系统,包括加热装置、喷淋塔、静置油罐和半成品油储罐,加热装置上部的油气出口通过管道连接喷淋塔,喷淋塔底部设置暂存池,暂存池设置溢流管连通半成品油储罐的进料口,半成品油储罐出油口通过管道连接喷淋塔的喷淋头。
[0006]
所述加热装置上部设置进料口,下部设置卸料口,加热装置的筒外壁均匀设置电磁加热带,加热装置内部设置搅拌桨叶,搅拌桨叶由搅拌电机驱动。
[0007]
所述加热装置连接真空泵,加热装置上设置第一压力表和破空阀。
[0008]
加热装置两端均设置氮封装置,所述氮封装置包括封装壳体,封装壳体将加热装置端部的机械密封处密封起来,封装壳体通过管道连接氮气罐,封装壳体上设置第二压力表,破空阀连接氮气罐。
[0009]
喷淋塔连接真空泵。
[0010]
静置油罐外部设置保温层,内置循环冷水盘管,静置油罐内还设置减速搅拌装置,静置油罐底部设置排泥口,顶部设置进料口和真空口,所述真空口通过管道连接真空泵。
[0011]
静置油罐底部排泥口连接加热装置的进料口。
[0012]
半成品油储罐的出油口连接成品油精制釜进油口,成品油精制釜出油口连接成品油储存罐。
[0013]
相对于现有技术,本实用新型摒弃现有的除尘设备,采用喷淋塔代替传统除尘器,
除尘效率高,不会发生堵塞,检修难度低;喷淋塔以半成品油储罐内的半成品油为喷淋液,喷淋产生的油及油泥混合物进入喷淋塔底部的暂存池,油通过溢流管道进入静置油罐,油泥留在暂存池内定期清理;喷淋塔连续运行,既能将油气中大部分粉尘清理掉,也能够对喷淋塔与静置油罐之间的溢流管道进行清洗,防止管道堵塞。
附图说明
[0014]
图1是本实用新型的工艺流程图。
[0015]
图2是加热装置的结构示意图。
[0016]
图3是喷淋塔的结构示意图。
[0017]
图4是静置油罐的结构示意图。
[0018]
其中,1-加热装置,11-进料口,12-卸料口,13-电磁加热带,14-搅拌桨叶,15-搅拌电机,16-第一压力表,17-破空阀,18-氮封装置,1801-封装壳体,1802-氮气罐,1803-第二压力表,19-油气出口,2-喷淋塔,21-暂存池,22-溢流管,23-喷淋头,24-油气入口,25-排污口,26-真空接口,3-静置油罐,31-冷水盘管,32-减速搅拌装置,33-排泥口,34-进油口,35-真空口,36-溢流口,4-半成品油储罐,5-成品油精制釜,6-真空泵,7-成品油储存罐。
具体实施方式
[0019]
如图1所示,一种含油硅藻土资源化处理系统,包括加热装置1、喷淋塔2、静置油罐3和半成品油储罐4,加热装置1上部的油气出口19通过管道连接喷淋塔2,喷淋塔2底部设置暂存池21,暂存池21设置溢流管22连通半成品油储罐4的进料口,半成品油储罐4出油口通过管道连接喷淋塔2的喷淋头23。如图3所示,喷淋塔2包括油气入口24,连接加热装置的油气出口19;排污口25,将暂存池21中的油泥排出;真空接口26,连接真空泵6。
[0020]
如图2所示,所述加热装置1选用卧式加热筒,上部设置进料口11,下部设置卸料口12,加热装置1的筒外壁均匀缠绕电磁加热带13,加热装置1内部设置搅拌桨叶14,搅拌桨叶14由搅拌电机15驱动。含油硅藻土经筛分装置筛选除杂后,以负压气力输送方式送入加热装置1,含油硅藻土输送完成后,开启加热装置1筒外壁缠绕的电磁加热带13开始升温对含油硅藻土进行加热,同时开启搅拌电机15,带动加热装置1内部的搅拌桨叶14搅拌,保证含油硅藻土能够均匀加热。加热过程中,含油硅藻土中的轧制油气化,搅拌的过程伴随有灰尘的产生,与气化的轧制油一起经由油气出口19通过管道进入喷淋塔2。
[0021]
为了降低含油硅藻土内轧制油的气化温度,从而降低能耗,在加热过程中可保持加热装置1处于负压状态。所述加热装置1连接真空泵6,通过真空泵实现加热装置1内的负压状态,加热装置1上还设置第一压力表16,第一压力表16显示加热装置1内的压力,方便实时调节。
[0022]
加热装置1的两端机械密封处无法做到完全密封,而加热装置1在高温高负压状态下运行,外部环境中的空气容易进入加热装置内与高温油气混合引起安全事故,为了保证安全生产,在加热装置1的两端设置氮封装置18。所述氮封装置包括封装壳体1801,封装壳体1801将加热装置1端部的机械密封处密封起来,封装壳体1801通过管道连接氮气罐1802,封装壳体上设置第二压力表1803。
[0023]
在系统运行过程中始终保持封装壳体1801内的氮气压力在一定范围内小幅波动,
如果发生剧烈波动,则说明加热装置1两端的机械密封已失效,需要停机检修;本系统氮封装置18的封装壳体上的第二压力表1803与紧急停车程序连锁,当密封壳体1803内氮气压力剧烈波动时,紧急自动停车。
[0024]
加热装置1在高负压状态下运行,卸料时需要打破加热装置1内的负压状态才能够顺利卸料,加热装置1上设置有破空阀17,破空阀17连接氮气罐1802,以氮气充入加热装置1进行破空,安全性更高,可降低操作安全隐患,避免空气与高温油气混合引发安全事故。
[0025]
加热装置1在高负压状态下运行,为了油气与粉尘更顺利的进入喷淋塔2,喷淋塔2底部暂存池21内的粗轧制品油顺利进入静置油罐3,将喷淋塔2和静置油罐3也保持在负压状态运行。实现方式为:喷淋塔2连接真空泵6,静置油罐3也连接真空泵6。
[0026]
如图4所示,静置油罐3全封闭,外部设置保温层(图中未显示),内置循环冷水盘管31,静置油罐3内还设置减速搅拌装置32,保持搅拌装置32低速运转,保证静置油罐3下部的油泥始终处于悬浮状态,方便油泥外排;静置油罐3底部设置排泥口33,顶部设置进油口34、真空口35、溢流口36,所述进油口34连接溢流管22,真空口35通过管道连接真空泵6,溢流口36连接半成品油储罐4。在现有含油硅藻土处理项目实际运行中,静置油罐3底部的油泥若长时间不外排,则会发生板结,难以通过管道外排,需以人工清理,故在静置油罐3设置搅拌装置32,保持油罐底部的油泥处于悬浮状态,方便排放。
[0027]
静置油罐3底部排泥口33连接加热装置1的进料口11,排泥口33排出的油泥循环进入加热装置1,重复加热处理,提高回收率。
[0028]
半成品油储罐4的出油口连接成品油精制釜5进油口,成品油精制釜5出油口连接成品油储存罐7。半成品油罐4内的半成品油定期打入成品油精制釜5内再次精制,产出的成品油进入成品油储存罐7暂存。
[0029]
工作过程:
[0030]
本硅藻土处理系统采用间歇式运行;
[0031]
含油硅藻土经筛分装置筛选除杂后,以负压气力输送方式送入加热装置1,开启加热装置1筒外壁缠绕的电磁加热带开始升温对硅藻土进行加热,同时开启加热装置1内部的搅拌桨叶,保证硅藻土能够均匀加热。
[0032]
加热装置1内产生的油气及携带的粉尘进入喷淋塔2,经喷淋冷凝,油气及油气携带的粉尘所形成的液态混合物进入喷淋塔2底部的暂存池,冷凝后的轧制油经溢流管流入静置油罐3沉淀;加热装置1内含油硅藻土完成提油后,关闭电磁加热带,关闭真空泵6,加热装置1内剩余硅藻土经机械输送装置送入焚烧炉进行高温煅烧,去除掉硅藻土内残余轧制油,保证系统产出的硅藻土不是危废,煅烧后的硅藻土经机械输送装置输送进入冷料机进行降温,降温后的硅藻土输送进入硅藻土暂存罐储存;煅烧产生的尾气经尾气处理装置处理达标排放。
[0033]
静置油罐3上层的洁净轧制油定期排入半成品油储罐4,静置油罐3下层油泥定期排出,然后与含油硅藻土混合重新进入加热装置1加热处理;半成品油储罐4内洁净轧制油作为喷淋塔2的喷淋液,喷淋塔连续式运行,以冲洗喷淋塔2至静置油罐3之间的溢流管道,保证管道通畅;半成品油罐4内的半成品油(洁净轧制油)定期打入成品油精制釜5再次精制,产出的成品油进入成品油储存罐7暂存。
[0034]
以上所述的仅是本发明的优选实施方式,应当指出,对于本领域的技术人员来说,
在不脱离本发明整体构思前提下,还可以作出若干改变和改进,这些也应该视为本发明的保护范围。