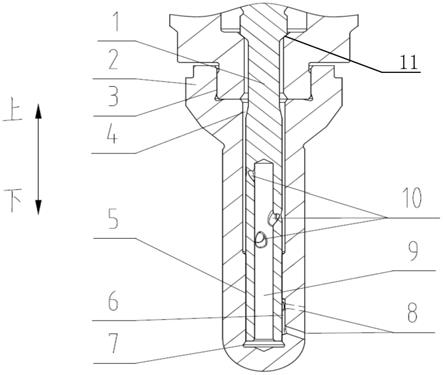
1.本实用新型涉及共轨燃油系统技术领域,具体涉及一种船用低速柴油机燃油喷嘴。
背景技术:2.随着全球石油资源消耗加剧,以石油为原材料的精制燃油在成本上更难得到控制。因此,可适用劣质燃油且经济性较好的低速大功率柴油机越来越受到远洋航运行业的青睐。然而劣质燃油具有成分复杂,杂质多,燃烧后易产生固态微粒和粘性液滴,若喷油器中的关键零件——针阀的密封座面与这种废气长时间接触,密封座面受到黏性或固态微粒物附着,针阀的密封性能将受到恶性影响,同时气缸内燃烧时燃气的高温高冲击力也会进一步减少针阀的寿命。因此,如何解决这一问题,是提高船用低速柴油机使用寿命的重要课题。
3.现有技术的低速柴油机多是通过增长喷油油嘴,使针阀的密封座面从距离上远离燃烧环境,来降低燃后杂质与高温高冲击引起的负面影响。然而,喷嘴长度增加的同时喷嘴内孔长度也随之增长,导致内孔容积增大。针阀密封座面关闭后喷嘴内孔残余油量增多,与此同时喷嘴内油压迅速降低,会引发滴油现象,这部分燃油雾化不良,易燃烧不完全,不但会增加废气污染物排放,严重时甚至可能导致气缸内产生结焦,降低燃油系统寿命。
4.为解决上述问题,在专利号为“cn211038879u”的专利中提供了一种喷嘴,上述喷嘴的问题在于:腰形通孔与滑杆的中孔之间呈90
°
设置,高压燃油在进油该处时会因流动弯度过大产生流阻而不利于高压燃油流动的稳定性;此外,由于该腰形通孔对称布置,高压燃油在经由腰形通孔进入到中孔内时,两股高压燃油经由对称设置的腰形通孔进入中孔内发生对撞而产生湍流,进一步不利于高压燃油流动的稳定性,最终导致喷油时工作稳定性较差。
技术实现要素:5.针对上述情况,本方案提供了一种船用低速柴油机燃油喷嘴,用于提高喷嘴的工作稳定性。
6.本实用新型的技术方案为:
7.本实施例提供了一种船用低速柴油机燃油喷嘴,包括:
8.与所述喷嘴的针阀体形成过盈配合的喷嘴主体;
9.与所述喷嘴主体配合的滑杆,所述滑杆与所述喷嘴的针阀头部形成刚性连接或形成为一体;
10.所述滑杆与所述喷嘴主体之间形成有紧密配合面,所述紧密配合面将所述滑杆和所述喷嘴主体之间的油腔分隔为上油腔和下油腔;
11.所述滑杆上设置有斜向侧孔和轴向中孔,所述斜向侧孔将所述上油腔和所述轴向中孔连通,所述轴向中孔连通所述下油腔;所述喷嘴主体的紧密配合面上设置有偏心油槽,
所述喷嘴主体上设置有与所述偏心油槽连通的喷油油孔;
12.当喷油器处于喷射状态时,所述滑杆与所述喷嘴主体之间的紧密配合面错开,使所述偏心油槽和所述下油腔连通;
13.当喷油器处于停喷状态时,所述滑杆与所述喷嘴主体之间的下侧紧密配合面紧密配合,使所述偏心油槽和所述下油腔错开。
14.其中,所述滑杆上沿纵向布置有多个所述斜向侧孔;
15.各所述斜向侧孔的中心线的延长线在所述轴向中孔的中心线上的交点均不相交;且多个斜向侧孔的中心线的延长线在所述轴向中孔的中心线上的交点从上至下均匀间隔特定距离排列。
16.其中,各所述斜向侧孔的中心线的延长线与所述轴向中孔的中心线之间形成的角度相同。
17.其中,在所述轴向中孔的中心线上的相邻两个交点所对应的两个斜向侧孔的中心线在圆周方向上的角度相同。
18.其中,所述滑杆的底部外周圈形成阶梯状或锥面状。
19.其中,所述偏心油槽的槽底相对于所述轴向中孔的中心线的偏离方向与所述喷油油孔的中心线相对于所述轴向中孔的中心线的偏离方向一致。
20.本实用新型的有益效果为:
21.1)、喷嘴的长度和与滑杆的配合密封能够避免针阀高压密封座面与气缸燃烧环境直接接触,降低劣质燃油燃烧后产生的高温高冲击力及残留杂质对针阀的高压密封座面的侵蚀,且这种细长形喷嘴能够节省安装空间。
22.2)、通过滑杆的体积占据了喷嘴内空腔容积,缓解喷嘴内的空腔积油较多导致的滴油现象,进一步缓解未雾化油液滴的不充分燃烧,提高燃油系统的使用寿命。
23.3)、通过四个斜向分布形式的斜向侧孔与偏心油槽的设计,提高滑杆的使用寿命与工作稳定性。
24.4)、除原方案外,该喷嘴的滑杆底端还可以有阶梯、锥面两种结构形式。可以根据气缸内环境与滑杆材质的硬度、韧性区别进行二次优化。
附图说明
25.图1是背景技术中的喷嘴的结构示意图;
26.图2为图1的a
‑
a剖面图;
27.图3为背景技术的燃油喷射时的流动示意图;
28.图4为图3的a处放大示意图;
29.图5为本实施例中的喷嘴的结构示意图;
30.图6为本实施例中燃油喷射时的流程示意图;
31.图7为图6的b处放大示意图;
32.图8为本实施例中的滑杆底部为阶梯状的结构示意图;
33.图9为本实施例中的滑杆底部为锥面的结构示意图;
34.其中,1
‑
滑杆、2
‑
喷嘴主体;3
‑
过盈装配面;4
‑
上油腔;5
‑
紧密配合面;6
‑
偏心油槽;7
‑
下油腔;8
‑
喷油油孔;9
‑
轴向中孔;10
‑
斜向侧孔;11
‑
高压密封座面。
具体实施方式
35.以下结合附图对本专利进行详细描述。
36.参见图5至图9所示,本实用新型实施例中提供了一种船用低速柴油机燃油喷嘴,其包括喷嘴主体2和与之配合的滑杆1。喷嘴主体2过盈连接在应用此喷嘴的针阀体头部的过盈装配面3上,滑杆1刚性连接针阀头部或与针阀头部形成一体,滑杆1布置在针阀的高压密封座面11下端。
37.参照图5,本实施例中,喷嘴主体2和滑杆1之间形成有紧密配合面5,依靠着该紧密配合面5,使喷嘴主体2和滑杆1之间的油腔被分隔为上油腔4和下油腔7两个油腔。
38.参照图5,喷嘴主体2与滑杆1之间形成的紧密配合面5处,滑杆1和喷嘴主体2之间的间隙很小,该间隙对滑杆1有导向作用,同时有较好的密封能力。
39.参照图5,在滑杆1的内部开设有轴向中孔9,在滑杆1的外表面开设有四个斜向侧孔10,轴向中孔9和四个斜向侧孔10连通,通过这些轴向中孔9和斜向侧孔10将上油腔4与下油腔7连通。
40.其中,本实施例中的四个斜向侧孔10沿圆周方向互成90
°
且四个斜向侧孔10在纵向上各有一定距离。
41.此外,在本实施例中喷嘴主体2和滑杆1之间的紧密配合面5下侧开有偏心油槽6,该偏心油槽6的偏心侧连通喷嘴主体2上设置的喷油油孔8。
42.本实施例中,该喷嘴的工作原理如下:
43.参见图6和图7所示。喷油器开始喷油时,针阀受弹簧力和液压力作用,针阀体上的密封锥面与针阀上的高压密封座面11贴合,待喷射的高压燃油积聚于针阀的高压密封座面11的上方。
44.当喷油器开始工作,针阀受力上移,高压密封座面11打开,同时针阀带动滑杆1上移,喷嘴主体2与滑杆1之间的紧密配合面5有一段错开,使下油腔7与偏心油槽6连通。此时,针阀的高压密封座面11上部的高压燃油经由高压密封座面11、上油腔4、四个斜向侧孔10、轴向中孔9和下油腔7流入偏心油槽6,最终从布置于偏心油槽6中的喷油油孔8喷入气缸内部,雾化燃烧。
45.当喷油器工作结束,针阀受到弹簧力作用落座,重新压紧于针阀的高压密封座面11,高压燃油被封于高压密封座面11之上。喷嘴主体2与滑杆1间的紧密配合面5底端互相贴合,使下油腔7与偏心油槽6间的燃油通路断开。滞留于下油腔7的残余燃油受密封作用无法流向喷油油孔8,喷油过程停止。此时,气缸内燃气仅能通过喷油油孔8与偏心油槽接触,不会接触到针阀的高压密封座面11,降低劣质燃油燃烧后产生的高温高冲击力及残留杂质对针阀的高压密封座面11的侵蚀。同时喷嘴的长度和能够避免针阀的高压密封座面11与气缸燃烧环境直接接触,且由于喷嘴呈细长形,所需安装空间小,节省气缸壁顶的安装空间,为冷却油道等的布置让出空间。
46.参照图1至图4,背景技术中,连接滑杆101的顶部油腔108与中孔104的是横向布置的腰形通孔103,该腰形通孔103虽然加工便利,但由于腰形通孔103与滑杆101的中孔104之间呈90
°
夹角,液体经过该处时会因流动弯度过大产生流阻;且由于腰形通孔103是对称设置的,对称设置的两个腰形通孔103均有高压燃油流入,两股高压燃油汇聚于同一点而发生冲击,进而产生湍流。上述两点均不利于高压燃油流动的稳定,进而对喷油器工作的稳定性
产生不利影响。
47.而本实施例中的方案,利用四个斜向侧孔10使上油腔4与轴向中孔9连接,液体在经过斜向侧孔10时,会因流动弯度减小,而使产生的流阻降低;同时,由于斜向侧孔9在纵向上单独布置,每一斜向侧孔9均不存在与其相对设置的另一斜向侧孔,使通过各斜向侧孔9流入的高压燃油不会发生对冲,进而可以避免湍流。相对于现有技术的方案来说,有益于高压燃油的流动稳定性。
48.此外,由于孔所在位置处往往是杆件的受力薄弱点,本实施例中,由于斜向侧孔10在纵向上单独布置,每个斜向侧孔10对应的滑杆1的横截面上斜向侧孔10占用空间小于现有技术中的两个的腰形通孔103所占用的空间,,因此本实施例中的滑杆1相较现有技术的滑杆101的结构强度更好。
49.此外,由于本实施例中的斜向侧孔10在纵向上依次间隔一定距离且四个斜向侧孔10中沿圆周方向两两互成90
°
,两股高压燃油也不会冲击相撞于同一点,而是各自流入轴向中孔9内并形成一定的冲击(冲击力度相对于对撞力度要小很多),然后在高压燃油与轴向中孔9的内壁进行冲击时依靠轴向中孔9的内壁吸收一定的冲击力,以此减缓湍流趋势。
50.此外,参照图1至图4,在滑杆1受力方面,背景技术中与喷油油孔107连接的喷嘴中腔105采用环槽形式,虽然该形式布置喷油油孔107较为自由,但针对于喷油油孔107需布置于同一侧的低速柴油机喷油器,喷油过程中环槽不同位置燃油流向不均匀。靠近喷油油孔107的一侧由于喷油油孔107向外喷油导致该侧燃油压力偏低,而另一侧的燃油由于要补充喷油油孔107侧流出的燃油而朝喷油油孔107的一侧流动,此滑杆1会因为环槽中燃油的流向方向而受到朝向喷油油孔107一侧的液压力,进而使滑杆朝喷油油孔的一侧方向产生微小形变(图3放大图中为夸张性绘制,仅为体现形变方向)。由于喷嘴主体2与滑杆1是紧密配合,间隙较小,在每次针阀落座时上述的微小形变都会导致滑杆1与喷嘴中腔105的边缘碰撞,加剧磨损,影响喷嘴寿命。
51.而本实施例中此处采用偏心油槽6,且偏心油槽6的槽底相对于轴向中孔9的中心线的偏离方向与喷油油孔8的中心线相对于轴向中孔9的中心线的偏离方向一致。因此即使靠近喷油油孔8的一侧由于喷油油孔8向外喷油导致该喷油油孔一侧的燃油压力偏低,但与喷油油孔8相反的另一侧由于喷嘴主体2与滑杆1 仍是紧密配合,使燃油并没有足够的空间流入该喷油油孔8一侧,也就无法因流动产生朝向喷油油孔8一侧的液压力,反而是喷油油孔8一侧会提供液压力使滑杆1远离偏心油槽6的边缘,使喷嘴寿命增加。
52.如图8和图9,本实施例中,滑杆1底端可以设计成阶梯或锥面两种结构形式,使滑杆1在受到液压侧偏力产生形变时,滑杆1的形变侧底端由于切去一部分而不会与喷嘴主体2的内孔壁相刮蹭。由于这两种结构形式均会导致的紧密配合面5的长度减小,故适用于气缸内爆燃压力较低的场合。具体来说,阶梯结构更适用于滑杆1材料强度好,不需过担心应力集中的场合。锥面结构由于受空间制约锥度受限,更适用于应力情况较差,但允许锥面有轻微节流的场合。
53.本实施例中的该低速柴油机用燃油喷嘴,其喷嘴主体2采用耐腐耐热且热膨胀系数小的材料。这样可减少喷嘴主体2受热而产生的热变形,间接使喷嘴主体2与滑杆1间的间隙宽度稳定,确保工作平稳。