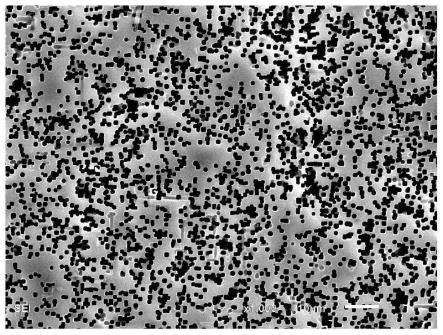
1.本发明属于腐蚀箔技术领域,具体涉及一种制备高比容腐蚀箔的前处理方法及其应用。
背景技术:2.铝点解电容器具有容量大和耐电压等优点,是电子工程中极为重要的一种基础元器件。电极箔是铝电解电容器的关键性原材料,其制造技术很大程度上决定了铝电解电容器的技术水平。为了满足电子产品日益小型化和集成化的要求,需要实现铝电解电容器用电极箔的高比容化。其中,腐蚀箔比容是铝电极箔比容的基础。
3.现有技术中,腐蚀箔的制备过程为:前处理-第一级发孔腐蚀-第二级扩孔腐蚀-后处理制得。为提高腐蚀箔的比容,通常采用改变处理温度、电流密度或者反应物浓度等来进行优化,但是仅通过参数优化腐蚀箔性能已经无法突破腐蚀箔比容的瓶颈。因此,为了进一步提高腐蚀箔的比容,需要开发一种更好的制备高比容腐蚀箔的前处理方法。
技术实现要素:4.本发明的目的在于克服现有技术不足,提供了一种制备高比容腐蚀箔的前处理方法,所述前处理方法施加微波能量,可以改善后续腐蚀工艺中腐蚀位点数量少,密度低的问题,同时可以有效提高腐蚀箔的折弯强度和静电容量。
5.为实现上述目的,本发明通过以下技术方案来实现的:
6.将铝箔放入前处理液中进行浸泡,并施加第一微波能量,所述第一微波能量密度为20~50w/m3,控制所述前处理液的温度为315~335k。
7.上述方案中,采用施加微波能量,可以有效提升前处理液体系中分子振动的频率和振幅,增加分子的内能,促进反应体系中粒子之间有效碰撞,促进腐蚀位点形成和分布均匀性,再经腐蚀发孔扩孔后,可以使得腐蚀箔形成大量的腐蚀孔洞,腐蚀箔的发孔数量明显增加,且静电容量和折曲强度有明显提升。
8.优选地,所述第一微波能量密度为40~50w/m3。
9.优选地,所述将铝箔放入前处理液中进行浸泡,包括如下步骤:先将铝箔在第一前处理液浸泡,再在第二前处理液浸泡。
10.具体地,所述第一前处理液为含有0.2~0.3mol/l氢氧化钠的溶液;所述第二前处理液为含有0.8~1.2mol/l盐酸和3.0~4.0mol/l硫酸的混合溶液。
11.优选地,所述第一前处理液的浸泡时间为110~130s。
12.优选地,所述第二前处理液的浸泡时间为110~130s。
13.本发明的另一目的在于提供一种前处理铝箔。
14.本发明的另一目的在于提供一种高比容腐蚀箔的制备方法。
15.一种高比容腐蚀箔的制备方法,包括以下步骤:将上述方法制得的前处理铝箔依次进行加电腐蚀腐蚀、后处理、烘干处理。
16.具体地,所述高比容腐蚀箔的制备方法包括以下步骤:
17.s1.应用所述前处理方法对铝箔进行前处理得到前处理铝箔;
18.s2.将所述前处理铝箔放入第一电解槽液中加电腐蚀,清洗,得到第一电解腐蚀箔;
19.s3.将步骤s2.中第一电解腐蚀箔放入第二电解槽液中加电腐蚀,清洗,得到第二电解腐蚀箔;
20.s4.将步骤s3.中第二电解腐蚀箔放入硝酸溶液处理,清洗,烘干。
21.本发明中,可以参考现有技术中腐蚀箔制备方法选用常用的第一电解槽液。优选地,步骤s2.中,所述第一电解槽液为盐酸和硫酸的混合溶液,盐酸浓度为0.8~1.2mol/l,硫酸浓度为3.0~4.0mol/l。
22.本发明中,可以参考现有技术中腐蚀箔制备方法选用常用的第一电解槽液温度范围。优选地,步骤s2.中,所述第一电解槽液温度为320~360k。
23.优选地,步骤s2.中,所述加电腐蚀的电流密度为0.2~0.4a/cm2。
24.优选地,步骤s2.中,所述加电腐蚀的时间为120~180s。
25.为进一步促进腐蚀箔的孔洞深入和孔径增长.在步骤s3.中,还施加第二微波能量,所述第二微波能量密度为20~50w/m3。
26.优选地,步骤s3.中,所述第二电解槽液为0.3~0.7mol/l硝酸。
27.优选地,步骤s3.中,所述第二电解槽液温度为320~360k。
28.优选地,步骤s3.中,所述加电腐蚀的电流密度为0.2~0.4a/cm2。
29.优选地,步骤s3.中,所述加电腐蚀的时间为250~320s。
30.优选地,步骤s4.中,所述硝酸溶液的质量分数为3~8%。
31.优选地,步骤s4.中,所述硝酸溶液的温度为60~70℃。
32.一种高比容腐蚀箔,采用上述方法制得。
33.本发明的另一目的在于提供一种高比容化成箔的制备方法。
34.与现有技术相比,本发明具有如下有益效果:
35.本发明提供一种制备高比容腐蚀箔的前处理方法,本发明采用在前处理中引入微波能量,并控制微波能量密度,可以有效提升前处理液体系中分子振动的频率和振幅,增加分子的内能,促进腐蚀位点形成和均匀性分布,可以使腐蚀箔的发孔数量明显增加;在第二电解腐蚀中引入微波能量,有助于孔洞的深入和孔径增长,可以使腐蚀箔经40μm抛光后孔洞保持率提升,且静电容量进一步提升。
附图说明
36.图1为实施例1前处理方法后制备的腐蚀箔抛光10μm后的表面形貌图;
37.图2为实施例4前处理方法后制备的腐蚀箔抛光10μm后的表面形貌图;
38.图3为对比例1前处理方法后制备的腐蚀箔抛光10μm后的表面形貌图;
39.图4为对比例2前处理方法后制备的腐蚀箔抛光10μm后的表面形貌图;
40.图5为实施例4前处理方法后制备的腐蚀箔抛光40μm后的表面形貌图;
41.图6为实施例6制备的腐蚀箔抛光40μm后的表面形貌图;
42.图7为实施例9制备的腐蚀箔抛光40μm后的表面形貌图。
具体实施方式
43.下面结合具体实施例对本发明做出进一步地详细阐述,所述实施例只用于解释本发明,并非用于限定本发明的范围。下述实施例中所使用的试验方法如无特殊说明,均为常规方法;所使用的材料、试剂等,如无特殊说明,为可从商业途径得到的试剂和材料。
44.实施例中所用的铝箔:厚度为130μm,纯度为99.99%,立方织构度大于95%的铝箔,购自乳源东阳光优艾杰精箔有限公司;所用盐酸、硫酸、硝酸均为市售分析纯。
45.实施例和对比例中前处理方法均在可控温的槽体中进行。
46.实施例1
47.一种制备高比容腐蚀箔的前处理方法,其特征在于,包括如下步骤:
48.将铝箔放在第一前处理液中浸泡120s,再放入第二前处理液中浸泡120s,并在浸泡第一前处理液和第二前处理液的时控制温度在320k且施加第一微波能量,所述第一微波能量密度为20w/m3;所述第一前处理液为含有0.25mol/l氢氧化钠的溶液,所述第二前处理液为含有1mol/l盐酸和3.5mol/l硫酸的混合溶液。
49.实施例2
50.一种制备高比容腐蚀箔的前处理方法,其特征在于,包括如下步骤:
51.将铝箔放在第一前处理液中浸泡120s,再放入第二前处理液中浸泡120s,并在浸泡第一前处理液和第二前处理液的时控制温度在320k且施加第一微波能量,所述第一微波能量密度为30w/m3;所述第一前处理液为含有0.25mol/l氢氧化钠的溶液,所述第二前处理液为含有1mol/l盐酸和3.5mol/l硫酸的混合溶液。
52.实施例3
53.一种制备高比容腐蚀箔的前处理方法,其特征在于,包括如下步骤:
54.将铝箔放在第一前处理液中浸泡120s,再放入第二前处理液中浸泡120s,并在浸泡第一前处理液和第二前处理液的时控制温度在320k且施加第一微波能量,所述第一微波能量密度为40w/m3;所述第一前处理液为含有0.25mol/l氢氧化钠的溶液,所述第二前处理液为含有1mol/l盐酸和3.5mol/l硫酸的混合溶液。
55.实施例4
56.一种制备高比容腐蚀箔的前处理方法,其特征在于,包括如下步骤:
57.将铝箔放在第一前处理液中浸泡120s,再放入第二前处理液中浸泡120s,并在浸泡第一前处理液和第二前处理液的时控制温度在320k且施加第一微波能量,所述第一微波能量密度为50w/m3;所述第一前处理液为含有0.25mol/l氢氧化钠的溶液,所述第二前处理液为含有1mol/l盐酸和3.5mol/l硫酸的混合溶液。
58.对比例1
59.一种制备高比容腐蚀箔的前处理方法,其特征在于,包括如下步骤:
60.将铝箔放在第一前处理液中浸泡120s,再放入第二前处理液中浸泡120s,并在浸泡第一前处理液和第二前处理液的时控制温度在320k;所述第一前处理液为含有0.25mol/l氢氧化钠的溶液,所述第二前处理液为含有1mol/l盐酸和3.5mol/l硫酸的混合溶液。
61.对比例2
62.一种制备高比容腐蚀箔的前处理方法,其特征在于,包括如下步骤:
63.将铝箔放在第一前处理液中浸泡120s,再放入第二前处理液中浸泡120s,并在浸
泡第一前处理液和第二前处理液的时控制温度在320k且施加第一微波能量,所述第一微波能量密度为60w/m3;所述第一前处理液为含有0.25mol/l氢氧化钠的溶液,所述第二前处理液为含有1mol/l盐酸和3.5mol/l硫酸的混合溶液。
64.本发明中,实施例1~4中调整前处理液的温度在315~335k范围内也可制备得到性能相当的前处理铝箔。
65.实施例5
66.一种高比容腐蚀箔的制备方法,包括以下步骤:
67.第一电解腐蚀:将上述实施例1~4和对比例1~2中前处理后的铝箔放在345k的1mol/l盐酸和3.5mol/l硫酸的混合溶液中进行一级直流发孔腐蚀,电流密度是0.3a/cm2,加电时间为150s,再用清水清洗得到第一电解腐蚀箔;
68.第二电解腐蚀:将第一电解腐蚀箔放入341k的含有0.5mol/l的硝酸溶液中进行二级直流扩孔腐蚀,电流密度为0.18a/cm2,加电时间为280s,再用清水清洗得到第二电解腐蚀箔;
69.后处理:将第二电解腐蚀箔放入65℃的含有质量分数为5%的硝酸溶液中处理180s,随后用清水清洗、烘干收箔,采用实施例1~4前处理后的铝箔制得的为高比容腐蚀箔1~4,采用对比例1~2前处理后的铝箔制得的为对比腐蚀箔1~2。
70.实施例6
71.一种高比容腐蚀箔的制备方法,包括以下步骤:
72.第一电解腐蚀:将上述实施例4中前处理后的铝箔放在345k的1mol/l盐酸和3.5mol/l硫酸的混合溶液中进行一级直流发孔腐蚀,电流密度是0.3a/cm2,加电时间为150s,再用清水清洗得到第一电解腐蚀箔;
73.第二电解腐蚀:将第一电解腐蚀箔放入341k的含有0.5mol/l的硝酸溶液中进行二级直流扩孔腐蚀,电流密度为0.18a/cm2,加电时间为280s,并在第二电解腐蚀过程中施加第二微波能量,所述第二微波能量密度为20w/m3,再用清水清洗得到第二电解腐蚀箔;
74.后处理:将第二电解腐蚀箔放入65℃的含有质量分数为5%的硝酸溶液中处理180s,随后用清水清洗、烘干收箔,得高比容腐蚀箔5。
75.实施例7
76.一种高比容腐蚀箔的制备方法,包括以下步骤:
77.第一电解腐蚀:将上述实施例4中前处理后的铝箔放在345k的1mol/l盐酸和3.5mol/l硫酸的混合溶液中进行一级直流发孔腐蚀,电流密度是0.3a/cm2,加电时间为150s,再用清水清洗得到第一电解腐蚀箔;
78.第二电解腐蚀:将第一电解腐蚀箔放入341k的含有0.5mol/l的硝酸溶液中进行二级直流扩孔腐蚀,电流密度为0.18a/cm2,加电时间为280s,并在第二电解腐蚀过程中施加第二微波能量,所述第二微波能量密度为30w/m3,再用清水清洗得到第二电解腐蚀箔;
79.后处理:将第二电解腐蚀箔放入65℃的含有质量分数为5%的硝酸溶液中处理180s,随后用清水清洗、烘干收箔,得高比容腐蚀箔6。
80.实施例8
81.一种高比容腐蚀箔的制备方法,包括以下步骤:
82.第一电解腐蚀:将上述实施例4中前处理后的铝箔放在345k的1mol/l盐酸和
3.5mol/l硫酸的混合溶液中进行一级直流发孔腐蚀,电流密度是0.3a/cm2,加电时间为150s,再用清水清洗得到第一电解腐蚀箔;
83.第二电解腐蚀:将第一电解腐蚀箔放入341k的含有0.5mol/l的硝酸溶液中进行二级直流扩孔腐蚀,电流密度为0.18a/cm2,加电时间为280s,并在第二电解腐蚀过程中施加第二微波能量,所述第二微波能量密度为40w/m3,再用清水清洗得到第二电解腐蚀箔;
84.后处理:将第二电解腐蚀箔放入65℃的含有质量分数为5%的硝酸溶液中处理180s,随后用清水清洗、烘干收箔,得高比容腐蚀箔7。
85.实施例9
86.一种高比容腐蚀箔的制备方法,包括以下步骤:
87.第一电解腐蚀:将上述实施例4中前处理后的铝箔放在345k的1mol/l盐酸和3.5mol/l硫酸的混合溶液中进行一级直流发孔腐蚀,电流密度是0.3a/cm2,加电时间为150s,再用清水清洗得到第一电解腐蚀箔;
88.第二电解腐蚀:将第一电解腐蚀箔放入341k的含有0.5mol/l的硝酸溶液中进行二级直流扩孔腐蚀,电流密度为0.18a/cm2,加电时间为280s,并在第二电解腐蚀过程中施加第二微波能量,所述第二微波能量密度为50w/m3,再用清水清洗得到第二电解腐蚀箔;
89.后处理:将第二电解腐蚀箔放入65℃的含有质量分数为5%的硝酸溶液中处理180s,随后用清水清洗、烘干收箔,得高比容腐蚀箔8。
90.对比例3
91.步骤和参数同实施例6,区别在于,第二电解腐蚀中,所述第二微波能量密度为60w/m3,得对比腐蚀箔3。
92.性能测试:
93.将上述方法制备的高比容腐蚀箔1、高比容腐蚀箔4和对比腐蚀箔1~2经抛光10μm后进行表面形貌分析,结果如图1~4所示。
94.将高比容腐蚀箔4~5和高比容腐蚀箔8经抛光40μm后进行表面形貌分析,结果如图5~7所示。
95.通过比较图1~4可以看出,当采用本发明的前处理方法制得的腐蚀箔表面发孔数量明显增加;图4中虽然发孔数量明显增加,但是从图中可以看出腐蚀箔表面出现了过腐蚀现象,导致腐蚀孔位点密度过大,出现大量的并孔和粗孔。
96.比较图5~7可以看出,当第二电解腐蚀过程中施加微波能量时,可以进一步提升孔洞深入生长能力,随着第二微波能量密度的增加,经40μm抛光后的孔洞数量明显增加。
97.将上述方法制备的高比容腐蚀箔1~8和对比腐蚀箔1~3进行比容和折弯性能测试,结果如表1所示,其中孔洞保持率=抛光40μm的孔径/抛光10μm的孔径*100%。
98.将上述腐蚀箔采用日本eiaj标准程序在520v下进行化成,用数显lcr计测试比容(4263b)。具体地,将上述腐蚀箔先在沸水中煮5min,随后先以0.05a/cm2电流密度在质量分数12%的硼酸溶液中升压至520v,再在520v化成15min。第一次化成后,将处理后的铝箔在773k下热处理2min,然后在520v化成3min。
99.表1高比容腐蚀箔1~8和对比腐蚀箔1~3的测试结果
[0100][0101][0102]
从表1中可以看出,采用本技术前处理方法后制得的高比容腐蚀箔的静电含量均不低于0.842μf/cm2,折弯可达55回以上,且抛光10μm后孔数不低于1931个。
[0103]
从实施例1~4和对比例1~2所述前处理方法制得的高比容腐蚀箔可以看出,当前处理过程中施加第一微波能量,可将抛光10μm后孔数由1379个提升到1931个以上,且静电容量由0.821μf/cm2提升至不低于0.842μf/cm2。但是当第一微波能量密度为60w/m3时,虽然腐蚀箔抛光10μm后孔数增加,但是由于能量过高导致出现大量的并孔和粗孔现象,使得腐蚀箔的静电容量下降,且折曲强度明显降低。优选地,当前处理过程中施加的第一微波能量密度为40~50w/m3时,发孔数量可以进一步增加,抛光10μm后的孔数可达2360个以上,静电含量不低于0.858μf/cm2。
[0104]
比较高比容腐蚀箔4~高比容腐蚀箔8可以看出,当第二电解腐蚀时,施加能量密度为20~50w/m3的第二微波能量,可以进一步提高高比容腐蚀箔的比容和孔洞保持率,当第二电解腐蚀过程中施加第二微波能量时,制得的高比容腐蚀箔经40μm后的孔数可达870个以上。且孔洞保持率由25.46%提升至32.85%以上,这是由于适度地引入第二微波能量,可以有效增加第二电解槽液中例子的活化能,提高例子与铝箔孔壁的碰撞几率和能量,提升孔洞升入能力。但是从对比腐蚀箔3可以看出,若第二微波能量密度过高时,制得的腐蚀
箔经40μm后的孔数虽然增加,但是由于能量过高,会出现过腐蚀和团簇孔等现象,造成静电容量和折曲强度下降。
[0105]
上述实施例为本发明较佳的实施方式,但本发明的实施方式并不受上述实施例的限制,其他的任何未背离本发明的精神实质与原理下所作的改变、修饰、替代、组合、简化,均应为等效的置换方式,都包含在本发明的保护范围之内。