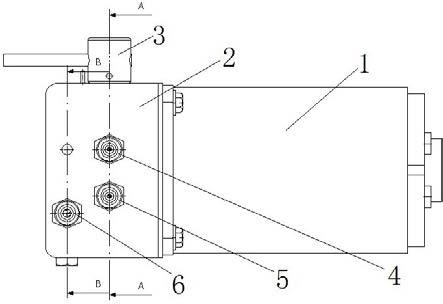
[0001]
本发明属于液压泵技术领域。
背景技术:[0002]
驾驶室举升泵是大型汽车的驾驶室上升和下降比不可缺的举升装置,举升泵的性能能够保证举升过程中的安全、效果等性能。现有的举升泵有多种,大部分是简单的举升油缸,其不但使用寿命短,还经常出现事故,相应的就会出现一些油缸式举升装置,即有手动,也有电动,这些相对于常规泵解决了许多的问题,但在使用过程,还会出现多多少少的问题。
技术实现要素:[0003]
本发明的目的是通过对油路的改进,从而能够更改供油形式的配合差速式油缸的电动泵。
[0004]
本发明电机安装在泵体上,在泵体侧面有分别与液压缸两端供油的下降端供油管和上升端供油管以及与油缸连接的油缸油管,调节杆在侧面插入泵体内部;调节杆插入泵体内部的表面开有第一环槽和第二环槽,并且在调节杆内部开有第一通道,第一通道内部分为窄端和宽端,窄端和宽端的交接处有第一单项球封,第一单项球封通过置于宽端内的第一单项球封弹簧弹压在窄端和宽端的交接处,第一通道的窄端通过第一支通道与第一环槽相通,在第一通道的宽端开有第一油孔、第二油孔和第三油孔,第二油孔和第三油孔在同轴位置上,分别与下降端供油管和上升端供油管的入口对应,第一油孔与第二油孔在同心位置上;第二通道与第一环槽相通;在泵体的内腔内通过卡簧安装有内泵体,内腔上端通过电机的底座密封,在内泵体对应柱塞油通道处开有第四环槽,密封铜垫、弹性密封圈和软质密封环依次置于第四环槽内;内泵体下端与泵体内底面之间留有过渡油腔;第三通道通过第二支通道与第三环槽相通,第三环槽是软质密封环内侧的凹形槽,软质密封环的凹形两端突出部分紧密的封堵在柱塞油通道的外围,在柱塞油通道的出口处有密封铜垫,在密封铜垫的外围环绕套装有弹性密封圈;第三通道通过第三通道油口与第七通道相通;在柱塞油通道插装有柱塞杆,柱塞杆顶端是柱塞杆帽,柱塞杆帽卡装在偏心轴与回位环之间,回位环同心固定安装在偏心轴上,偏心轴上端为电机轴安装座,电机的电机轴固定安装在电机轴安装座上;电机轴安装座通过轴承安装在内泵体内侧;柱塞油通道通过第二过渡通道与过渡油腔相通,过渡油腔与第四通道相通,第四通道通过第四通道油口与第五通道相通,第五通道一端与第六通道的宽端相通,另一端与油缸油管连通;第六通道内部分为窄端和宽端,在窄端与宽端连接处有第二单项球封,第二单项球封通过置于宽端内的第二单项球封弹簧弹压在窄端和宽端的交接处,第六通道窄端与第七通道相通;
第二通道与过渡通道相通,过渡通道通过过渡通道油口与第七通道相通;第八通道与第二环槽相通,并且通过第二过渡通道的第二过渡通道油口与第五通道相通。
[0005]
本发明第六通道的宽端与外界相通,并通过油封帽封堵。
[0006]
本发明设计合理,调节方便,操作简单实用,入油和出油的油路更加安全可靠,为驾驶室的举升或下降提供了便捷即安全性。本发明不会产生密封失效、漏油等现象,经过实践,在使用过程中,基本能够达到10000次以上,甚至更多,节省大量的成本。
附图说明
[0007]
图1是本发明外部结构示意图;图2是本发明图1的a-a示意图,油缸上升油路示意图;图3是本发明图1的b-b示意图;图4是本发明图2的d-d示意图;图5是本发明图2的c-c示意图;图6是本发明图5的f部分放大图;图7是本发明图5的e-e示意图;图8是本发明图1的a-a示意图,油缸下降油路示意图。
具体实施方式
[0008]
本发明电机1安装在泵体2上,在泵体2侧面有分别与液压缸两端供油的下降端供油管4和上升端供油管5以及与油缸连接的油缸油管6,液压缸与油缸都是现有驾驶室举升的常规设备,通过本发明的泵体向其供油,从而完成驾驶室的举升和下降。调节杆3在侧面插入泵体2内部,调节杆3是个手动操作设备,用来转换泵体2内部的供油方向的,通过转换来实现液压缸是举升还是下降。
[0009]
调节杆3插入泵体2内部的表面开有第一环槽8和第二环槽12,第一环槽8和第二环槽12是两个格子独立的环槽,与泵体2内壁形成两个独立的油槽。
[0010]
在调节杆内部开有第一通道9,第一通道9内部分为窄端和宽端,窄端和宽端的交接处有第一单向球封10,第一单向球封10通过置于宽端内的第一单项球封弹簧13弹压在窄端和宽端的交接处,第一单向球封10在窄端油压大约宽端油压时,在油压的作用下压缩弹簧,从而使油从第一通道9的窄端进入宽端,但如果窄端的油压低于宽端油压,则第一单向球封10会将第一通道9的窄端和宽端封闭,防止宽端的油流入窄端,所以可以看出,第一单向球封10起到一个单向阀的作用。为了封闭效果更好,可以将窄端和宽端接触处设计成与球面匹配形式。
[0011]
第一通道9的窄端通过第一支通道7与第一环槽8相通,在第一通道9的宽端开有第一油孔11、第二油孔26和第三油孔27,第二油孔26和第三油孔27在同轴位置上,分别与下降端供油管4和上升端供油管5的入口对应,第一油孔11与第二油孔26在同心位置上;第二通道24与第一环槽8相通;第一油孔11和第二油孔26对应下降端供油管4,通过旋转调节杆3来完成下降端供油管4与第一油孔11和第二油孔26其中之一相通,而上升端供油管5在旋转调节杆3后,分别与第三油孔27、第二环槽12,也就是说,当下降端供油管4与第一油孔11连通时,上升端供油管5与第二环槽12连通(见图8),成液压缸下降通路;当下降端供油管4与第
二油孔26连通时,上升端供油管5与第三油孔27连通(见图2),成液压缸上升通路。
[0012]
在泵体2的内腔49内通过卡簧34安装有内泵体33,由于内泵体33与泵体2是独立的分立体,为了固定,通过卡簧34来固定,防止内泵体33移动。内腔49就是泵体2内部的腔体,用于安装内泵体33等,并且内泵体33等部件的工作也在其中完成。内腔49上端通过电机1的底座46密封,通过底座46的密封,可以是整个内腔49是一个完全密封的腔体。在内泵体33对应柱塞油通道39处开有第四环槽48,第四环槽48是围绕整个内泵体33外周一圈,并且与柱塞油通道39对应。密封铜垫40、弹性密封圈41和软质密封环42依次置于第四环槽48内,此部分详细描述在下面详述。内泵体33下端与泵体2内底面之间留有过渡油腔50;过渡油腔50与内腔49是一个腔,只不过是位于内泵体33下端与泵体2内底面之间,为了方便语言描述而单独起的名称。
[0013]
第三通道31通过第二支通道32与第三环槽47相通,第三环槽47是软质密封环42内侧的凹形槽,软质密封环42的凹形两端突出部分紧密的封堵在柱塞油通道39的外围,在柱塞油通道39的出口处有密封铜垫40,在密封铜垫40的外围环绕套装有弹性密封圈41;第三通道31通过第三通道油口22与第七通道16相通;此部分是关于柱塞杆38工作时的供油通路,当柱塞杆38挤压供油时,在油压的作用下,将密封铜垫40挤压,从而脱离对柱塞油通道39出口处的密封,同时密封铜垫40将弹性密封圈41膨胀变形,也同时弹性密封圈41在第三环槽47内挤压软质密封环42,软质密封环42是一个凹形,即使变形,也是凹形中部变形,而凹形的两端基本为脱离柱塞油通道39外围侧壁,而从柱塞油通道39挤压出来的油大部分进入第三环槽47,少部分可能被挤入第四环槽48,但第三环槽47内的油,完全可以进行下面的工作需求。由于设置了多个柱塞杆38进行挤压供油,所以,相对于每个柱塞杆38的供油力度不是太大即可以足够油量供应,所以,凹形的软质密封环42的两端大部分时候是不会脱离内泵体33侧壁,这样在大部分情况下,从柱塞油通道39出来的油大部分会流入第三环槽47内,从而保证了第三环槽47保持充足的油。弹性密封圈41是一个弹性较好的材质,其作用是通过弹性力将密封铜垫40加持在柱塞油通道39的出油口处,当柱塞油通道39内的出油压力大于弹性密封圈41的弹力时,就会使弹性密封圈41膨胀变形,从而使密封铜垫40脱离柱塞油通道39的出油口并解除密封。在弹性密封圈41膨胀变形有可能同时挤压断面为凹形的软质密封环42,此部分不是必须的,因为,本发明的此部分只要保证柱塞油通道39内的油进入到第三环槽47即可,但当油压稍大时,就有可能产生断面为凹形的软质密封环42变形,部分多余的油就会从软质密封环42两侧流入第四环槽48内,这样软质密封环42即保持了密封作用(密封效果),也保持了第三环槽47内的油压大致恒定(泄压效果)。
[0014]
在柱塞油通道39插装有柱塞杆38,柱塞杆38顶端是柱塞杆帽45,柱塞杆帽45卡装在偏心轴36与回位环44之间,回位环44同心固定安装在偏心轴36上,偏心轴36上端为电机轴安装座37,电机1的电机轴35固定安装在电机轴安装座37上;电机轴安装座37通过轴承安装在内泵体33内侧;偏心轴36与回位环44夹持着柱塞杆帽45,由于偏心轴36的偏心转动,所以,可以依次将柱塞杆38逐个反复推动或拉回(见图7),而回位环44是卡住柱塞杆帽45,在偏心轴36运动的短轴侧时,将柱塞杆38拉回。电机1的电机轴35是带动偏心轴36进行偏心运动的动力,偏心轴36的偏心就是相对于电机轴而进行的偏心运动。电机轴35、电机轴安装座37、偏心轴36的转动均是在内泵体33中间完成的,为了便于转动,在电机轴安装座37与内泵体33之间安装了轴承。偏心轴36底部插在泵体2上,而这个插入部分与电机轴35同轴转动。
其结构也可以是:电机轴安装座37、偏心轴36、偏心轴36的底部为一体,但中间部位加工成与电机轴安装座37和偏心轴36的底部偏心运动的偏心轴36。
[0015]
柱塞油通道39通过第二过渡通道43与过渡油腔50相通,过渡油腔50与第四通道30相通,第四通道30通过第四通道油口18与第五通道15相通,第五通道15一端与第六通道21的宽端相通,另一端与油缸油管6连通;此部分的通道的连通结构是油箱供油及向油箱回油的通道,以及通道间过渡供油的通道。
[0016]
第六通道21内部分为窄端和宽端,在窄端与宽端连接处有第二单项球封20,第二单项球封20通过置于宽端内的第二单项球封弹簧19弹压在窄端和宽端的交接处,第六通道21窄端与第七通道16相通;第六通道21的结构形式与第一通道9的结构形式相同,此处不做赘述。通过第六通道21的窄端和宽端以及第二单项球封20设置,保证第六通道21内的油只能从窄端进入宽端,却不能反向流动。
[0017]
第二通道24与过渡通道25相通,过渡通道25通过过渡通道油口17与第七通道16相通;第八通道28与第二环槽12相通,并且通过第二过渡通道29的第二过渡通道油口14与第五通道15相通。此部分是整个泵体2内的油路完全连通的油路通路。
[0018]
本发明第六通道21的宽端与外界相通,并通过油封帽23封堵。这个油封帽23仅仅是方便对泵体2内清洗而设置的。清洗时打开油封帽23,工作时用油封帽23封堵。
[0019]
以下进行针对驾驶室举升和下降过程油路的走向详细说明:液压泵举升(上升)过程(图2与其它图): 首先旋转调节杆3,使下降端供油管4与第二油孔26连通、上升端供油管5与第三油孔27连通,打开电机,此时储油箱内的油依次经过第五通道15、第四通道油口18、第四通道30、过渡油腔50、第二过渡通道43,再经过柱塞杆39挤压入第三环槽47,再经过第二支通道32、第三通道31、第三通道油口22进入第七通道16,再经过过渡通道油口17、过渡通道25、第二通道24进入第一环槽8,最后经过第一支通道7、第一通道9、上升端供油管5送入液压泵上升端。而液压泵下降端的出油经下降端供油管4进入第一通道9,并通过上升端供油管5进入液压泵上升端。
[0020]
液压泵下降过程(图8与其它图):首先旋转调节杆3,使下降端供油管4与第一油孔11连通、上升端供油管5与第二环槽12连通,打开电机,此时储油箱内的油依次经过第五通道15、第四通道油口18、第四通道30、过渡油腔50、第二过渡通道43,再经过柱塞杆39挤压入第三环槽47,再经过第二支通道32、第三通道31、第三通道油口22进入第七通道16,再经过过渡通道油口17、过渡通道25、第二通道24进入第一环槽8,最后经过第一支通道7、第一通道9、下降端供油管4送入液压泵下降端。而液压泵上升端的出油依次经过上升端供油管5、第二环槽12、第八通道28、第二过渡通道29、第二过渡通道油口14进入第五通道15,此时与储油箱进油混合,或者向液压泵供油,多余的回到储油箱。