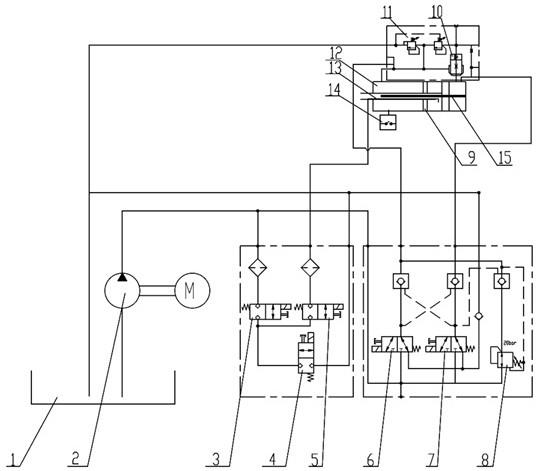
[0001]
本发明属于反击式破碎机技术领域,具体涉及反击式破碎机排料口。
背景技术:[0002]
反击式破碎机结构简单,制造容易,是主要破碎设备之一,广泛运用于矿山、建材、基建部门及建筑垃圾回收部门的粗碎和中碎作业,具有产量高、产品粒度均匀、结构简单、工作可靠、维修简便和运营费用经济等特点。
[0003]
排料口精确定位及自动复位的重要性和必要性;目前反击式破碎机反击板与板锤同为磨耗件,在使用过程中,每时每刻都有不同程度的磨损,而精确的排料口大小是保证破碎物料粒度与质量的重要手段。目前反击式破碎机排料口大小主要的调节形式:丝杠与弹簧相结合的调节形势;液压调节形式。无论哪种调节形式,排料口都需要人工测量及反复调节,且排料口不能精确定位与自动复位。在调节的整个过程中费时费力,且伴有一定的危险性。
技术实现要素:[0004]
为了克服上述现有技术的不足之处,本发明提供一种用于反击式破碎机排料口精确定位的液压系统及控制方法,通过液压系统、三腔油缸以及检测部件来实现排料口的精确定位与自动复位。既能降低工人的劳动强度,又能排除工人操作的安全风险,缩短停机时间,提高产能。
[0005]
本发明是通过如下技术方案实现的:一种用于反击式破碎机排料口精确定位的液压系统,包括液压泵、电磁阀ⅰ、电磁阀ⅱ、电磁阀ⅲ、电磁阀ⅳ、电磁阀
ⅴ
和油缸;油缸的小腔一侧还设有止动环,止动环与活塞环间形成中间腔,所述液压泵的出油口分别与电磁阀ⅰ、电磁阀ⅳ和电磁阀
ⅴ
相连,所述电磁阀ⅰ分别与电磁阀ⅱ和电磁阀ⅲ相连,所述电磁阀ⅱ与油缸的中间腔相连,所述电磁阀ⅲ与油箱相连;所述电磁阀ⅳ的工作油口与油缸的小腔相连,所述电磁阀
ⅴ
的工作油口与油缸的大腔相连,所述电磁阀ⅳ的回油口与所述电磁阀
ⅴ
的回油口均与油箱相连,所述电磁阀ⅳ的工作油口与所述电磁阀
ⅴ
的工作油口之间设有双向液压锁;所述油缸的小腔一侧还设有接近开关,所述油缸内设有磁致伸缩位移传感器。
[0006]
进一步地,所述液压泵的出油口还与减压阀相连,减压阀远离所述液压泵的一端与液控单向阀相连,液控单向阀远离所述减压阀的一端与所述油缸的小腔相连,液控单向阀的控制端与所述电磁阀
ⅴ
的工作油口相连。
[0007]
进一步地,所述液压泵与所述电磁阀ⅰ之间设有过滤器,所述电磁阀ⅲ与所述油缸的中间腔之间也设有过滤器。
[0008]
进一步地,所述电磁阀ⅳ的回油口与所述电磁阀
ⅴ
的回油口相连通,且所述电磁阀
ⅴ
与油箱的回油油路上设有单向阀。
[0009]
进一步地,还包括溢流阀组与先导溢流阀组合的集成阀组,所述油缸与该集成阀组相连。
[0010]
本发明还提供了一种采用上述用于反击式破碎机排料口精确定位的液压系统的控制方法,所述油缸的活塞杆端部通过销轴与反击板连接在一起,通过控制活塞杆的伸缩来控制排料口的大小,控制步骤如下:步骤一、初始时,电磁阀ⅱ、电磁阀ⅲ和电磁阀ⅳ得电使油缸的小腔进油,油缸的中间腔出油;当活塞环到油缸的底部时,此时电磁阀ⅱ、电磁阀ⅲ继续得电t1秒确保油缸的中间腔液压油排净;步骤二、电磁阀ⅰ、电磁阀ⅲ和电磁阀
ⅴ
得电使油缸的大腔和油缸的中间腔进油,活塞杆快速前进,同时检测活塞环位置及止动环信号;步骤三、电磁阀ⅰ、电磁阀ⅲ和电磁阀ⅳ得电使油缸的小腔和油缸的中间腔进油,活塞杆快速远离转子,直至活塞环达到机械限位时停止;步骤四、电磁阀ⅰ、电磁阀ⅲ和电磁阀
ⅴ
得电使油缸的大腔和油缸的中间腔进油,活塞杆快速前进,同时检测活塞环位置s2及止动环信号;此时全部断电启动转子,当转子转速为v1时,电磁阀ⅱ、电磁阀ⅲ和电磁阀
ⅴ
得电使油缸的大腔进油、油缸的中间腔出油,活塞杆缓慢前进,进行碰零点;当装在机架上的加速度传感器检测到信号时,此时检测磁致伸缩位移传感器数值,记录活塞环的位置a即为排料口的零点位置;步骤五、电磁阀ⅰ、电磁阀ⅲ和电磁阀ⅳ得电使油缸的小腔和油缸的中间腔进油,活塞杆快速远离转子,当达到控制面板预设排料口大小位置s-15mm时停止,此时开始检测止动环信号,当检测到止动环信号时,使电磁阀ⅱ、电磁阀ⅲ和电磁阀
ⅴ
得电使油缸的大腔进油、油缸的中间腔出油,活塞杆缓慢前进,达到预设排料口大小s时为止;当检测不到止动环信号时,电磁阀ⅰ和电磁阀ⅲ得电使油缸的中间腔进油,直到检测到止动环信号为止,再使电磁阀ⅱ、电磁阀ⅲ和电磁阀
ⅴ
得电使油缸的大腔进油、油缸的中间腔出油,活塞杆缓慢前进,达到预设排料口大小s时为止;步骤六、当排料口变化到预设值b时,此时先检测止动环信号,当检测到止动环信号时,使电磁阀ⅱ、电磁阀ⅲ和电磁阀
ⅴ
得电使油缸的大腔进油、油缸的中间腔出油,活塞杆缓慢前进,达到预设排料口大小s时为止;当检测不到止动环信号时,电磁阀ⅰ和电磁阀ⅲ得电使油缸的中间腔进油,直到检测到止动环信号为止,再使电磁阀ⅱ、电磁阀ⅲ和电磁阀
ⅴ
得电使油缸的大腔进油、油缸的中间腔出油,活塞杆缓慢前进,达到预设排料口大小s时为止。
[0011]
本发明的有益效果是:通过液压系统、三腔油缸以及检测部件来实现排料口的精确定位与自动复位,该系统主要作用是检测排料口零点位置,计算排料口大小并通过液压调整系统使排料口精确定位,当检测到反击板受到外部碰撞及挤压力使排料口大小偏离设定变化范围值外时,系统自动调节到原排料口大小位置。该系统的实施不会出现油缸、阀芯泄露以及溢流而产生的排料口不准确而造成频繁停机调节排料口的状况。本申请既能降低工人的劳动强度,又能排除工人操作的安全风险,缩短停机时间,提高产能。
附图说明
[0012]
图1为本发明的液压原理图;图2为本发明反击式破碎机的局部示意图;图中,1、油箱,2、液压泵,3、电磁阀ⅰ,4、电磁阀ⅱ,5、电磁阀ⅲ,6、电磁阀ⅳ,7、电磁阀
ⅴ
,8、减压阀,9、止动环,10、先导溢流阀,11、溢流阀组,12、油缸,13、活塞杆,14、接近开关,
15、磁致伸缩位移传感器。
具体实施方式
[0013]
下面根据附图和实施例对本发明进一步说明。
[0014]
如图1所示,一种用于反击式破碎机排料口精确定位的液压系统,包括液压泵2、电磁阀ⅰ3、电磁阀ⅱ4、电磁阀ⅲ5、电磁阀ⅳ6、电磁阀
ⅴ
7和油缸12;油缸12的小腔一侧还设有止动环9,止动环9与活塞环间形成中间腔,所述液压泵2的出油口分别与电磁阀ⅰ3、电磁阀ⅳ6和电磁阀
ⅴ
7相连,所述电磁阀ⅰ3分别与电磁阀ⅱ4和电磁阀ⅲ5相连,所述电磁阀ⅱ4与油缸12的中间腔相连,所述电磁阀ⅲ5与油箱相连;所述电磁阀ⅳ6的工作油口与油缸12的小腔相连,所述电磁阀
ⅴ
7的工作油口与油缸12的大腔相连,所述电磁阀ⅳ6的回油口与所述电磁阀
ⅴ
7的回油口均与油箱相连,所述电磁阀ⅳ6的工作油口与所述电磁阀
ⅴ
7的工作油口之间设有双向液压锁;所述油缸12的小腔一侧还设有接近开关14,所述油缸12内设有磁致伸缩位移传感器15。
[0015]
溢流阀组11与先导溢流阀10为集成阀组,先导溢流阀10与油缸12的大腔相连接,阀芯上节流口与溢流阀组11连接,同时,先导溢流阀10与油缸12的小腔连接,溢流阀组11中间与油缸12的小腔连接(溢流阀组11包括两个溢流阀,即两个溢流阀之间的管路与油缸12的小腔连接),溢流阀组11与油箱1连接。当反击板收到外部冲击,压力大于溢流阀组11第一个溢流阀设定值时,溢流阀组11第一个溢流阀打开,油缸12的大腔油通过溢流阀组11第一个溢流阀进入油缸12的小腔,此时,先导溢流阀10阀芯上下形成压差,先导溢流阀10打开,多余的油通过溢流阀组11的第二个溢流阀流入油箱1。其目的是保证反击板受到外界巨大冲击或者坚硬异物如铁块等冲击,油缸收缩时,油缸大小腔都充满油,同时也起到泄荷作用。
[0016]
进一步地,所述液压泵2的出油口还与减压阀8相连,减压阀8远离所述液压泵2的一端与液控单向阀相连,液控单向阀远离所述减压阀8的一端与所述油缸12的小腔相连,液控单向阀的控制端与所述电磁阀
ⅴ
7的工作油口相连。减压阀8与液控单向阀目的是使小腔在工作时始终有一个背压,避免在工作时止动环与缸头频繁碰撞。
[0017]
进一步地,所述液压泵2与所述电磁阀ⅰ3之间设有过滤器,所述电磁阀ⅲ5与所述油缸12的中间腔之间也设有过滤器,过滤器用于过滤掉液压油内的杂质,保证液压系统的正常运行。
[0018]
进一步地,所述电磁阀ⅳ6的回油口与所述电磁阀
ⅴ
7的回油口相连通,且所述电磁阀
ⅴ
7与油箱的回油油路上设有单向阀。
[0019]
本发明还提供了一种采用上述用于反击式破碎机排料口精确定位的液压系统的控制方法,所述油缸12的活塞杆13端部通过销轴与反击板连接在一起,通过控制活塞杆13的伸缩来控制排料口的大小,控制步骤如下:步骤一、初始时,电磁阀ⅱ4、电磁阀ⅲ5和电磁阀ⅳ6得电,液压泵2提供的液压油经过电磁阀ⅳ6进入油缸12的小腔,液压油推动止动环9朝活塞环一侧运动,止动环9挤压油缸12中间腔的液压油使其通过电磁阀ⅱ4、电磁阀ⅲ5流回油箱1;当活塞环到油缸12的底部时(即油缸12的大腔液压油排净),此时电磁阀ⅱ4、电磁阀ⅲ5继续得电t1秒(根据实际情况预留合理的时间即可)确保油缸12的中间腔液压油排净;
步骤二、电磁阀ⅰ3、电磁阀ⅲ5和电磁阀
ⅴ
7得电,液压泵2提供的液压油分成两路,一路液压油经电磁阀
ⅴ
7流向油缸12的大腔推动活塞杆13伸出,另一路液压油经电磁阀ⅰ3、电磁阀ⅲ5流向油缸12中间腔,推动止动环9朝外移动;油缸12的大腔和油缸12的中间腔的进油,使得活塞杆13快速前进,同时检测活塞环位置(原始默认零点位置为s1,s1指油缸推动反击板碰到转子板锤时,油缸伸出的距离,活塞环初始位置为s2=s1-s3,其中s3为安全距离)及止动环信号;步骤三、电磁阀ⅰ3、电磁阀ⅲ5和电磁阀ⅳ6得电,液压泵2提供的液压油分成两路,一路液压油经电磁阀ⅳ6流向油缸12的小腔,另一路液压油经电磁阀ⅰ3、电磁阀ⅲ5流向油缸12中间腔;油缸12的小腔和油缸12的中间腔的进油,使得活塞杆13快速远离转子,直至活塞环达到机械限位时停止(以上三个步骤主要作用是在开机前排尽油缸大小腔及中间腔空气);步骤四、电磁阀ⅰ3、电磁阀ⅲ5和电磁阀
ⅴ
7得电使油缸12的大腔和油缸12的中间腔进油,活塞杆13快速前进,同时检测活塞环位置s2及止动环信号;此时全部断电启动转子,当转子转速为v1(100转/分<v1<250转/分)时,保证在后续步骤反击板碰撞板锤时产生的加速度适中,电磁阀ⅱ4、电磁阀ⅲ5和电磁阀
ⅴ
7得电使油缸12的大腔进油、油缸12的中间腔出油,活塞杆13缓慢前进,进行碰零点;当装在机架上的加速度传感器检测到信号时,此时检测磁致伸缩位移传感器15数值,记录活塞环的位置a即为排料口的零点位置;步骤五、电磁阀ⅰ3、电磁阀ⅲ5和电磁阀ⅳ6得电使油缸12的小腔和油缸12的中间腔进油,活塞杆13快速远离转子,当达到控制面板预设排料口大小位置s-15mm时停止(该操作的目的1:快速远离转子,避免板锤与反击板持续碰撞;目的2:偏离设定值s远一些,为后续油缸缓慢前进留有反应时间,更精确的达到设定s位置),此时开始检测止动环信号,当检测到止动环信号时,使电磁阀ⅱ4、电磁阀ⅲ5和电磁阀
ⅴ
7得电使油缸12的大腔进油、油缸12的中间腔出油,活塞杆13缓慢前进,达到预设排料口大小s时为止;当检测不到止动环信号时,电磁阀ⅰ3和电磁阀ⅲ5得电使油缸12的中间腔进油,直到检测到止动环信号为止,再使电磁阀ⅱ4、电磁阀ⅲ5和电磁阀
ⅴ
7得电使油缸12的大腔进油、油缸12的中间腔出油,活塞杆13缓慢前进,达到预设排料口大小s时为止。
[0020]
步骤一~步骤五为本系统在开机后的调试过程。
[0021]
步骤六、在工作过程中,无须时刻检测止动环信号,但要实时检测活塞环位置(即磁致伸缩位移传感器数值)。当反击板受到原料冲击及挤压时,由于油缸及阀芯泄露或者受到较大冲击溢流阀溢流时,会使活塞环移动即排料口增大。当排料口变化到预设值b时,此时先检测止动环信号,当检测到止动环信号时,使电磁阀ⅱ4、电磁阀ⅲ5和电磁阀
ⅴ
7得电使油缸12的大腔进油、油缸12的中间腔出油,活塞杆13缓慢前进,达到预设排料口大小s时为止;当检测不到止动环信号时,电磁阀ⅰ3和电磁阀ⅲ5得电使油缸12的中间腔进油,直到检测到止动环信号为止,再使电磁阀ⅱ4、电磁阀ⅲ5和电磁阀
ⅴ
7得电使油缸12的大腔进油、油缸12的中间腔出油,活塞杆13缓慢前进,达到预设排料口大小s时为止。此控制方式就能保证在正常运行工作中排料口能自动复位,不会出现油缸、阀芯泄露以及溢流而产生的排料口不准确而造成频繁停机调节排料口的状况。