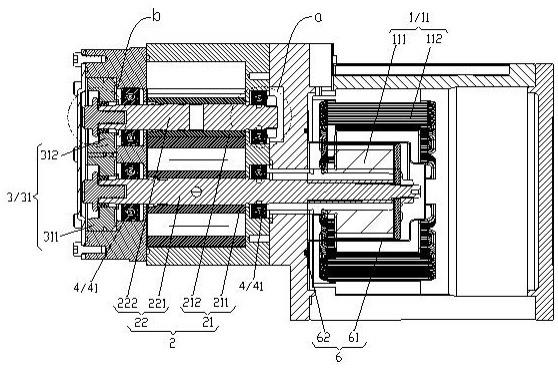
1.本发明涉及氢气循环泵技术领域,特别涉及一种耐高温水气低功耗燃料电池氢气循环泵。
背景技术:2.燃料电池是一种清洁且高效率的能源,燃料电池通过氢气与氧(空气)等氧化剂发生电化学反应,将化学能转化为电能。作为燃料电池系统的子零部件,氢气循环泵的作用就是将燃料电池系统中未完全利用的氢气再次输送回燃料电池系统,提高氢气的利用效率。
3.基于其应用场景,氢气循环泵内部压缩腔会直接与氢气、氮气、水蒸气、液态水混合接触,气体温度在70~90℃之间,液态水ph为3~5之间的偏酸性,这种高温,多变且复杂的气体混合工况对燃料电池氢气循环泵的结构设计有更高的要求,基于传统的氢气循环泵,其存在的缺陷在于:(1)关于轴承的设计:a、轴承在运行的过程中要防止在高温运行时外圈和轴承室相对的滑动和蠕动,一但长时间的滑动或者蠕动配合间隙变大会造成设备故障停机或者轴承提前失效,密封失效后的轴承使用寿命也不能满足要求;b、由于高温的液态水和高温气体混合物会直接对运行过程中的燃料电池氢气循环泵轴承进行侵蚀和冲击,造成轴承失效,影响燃料电池系统的正常运行;c、恶劣的运行环境下,高温的水和水蒸气容易造成轴承的锈蚀;同时在高温环境下轴承易出现松动,产生运行不稳定,工作失效的问题,甚至会引发设备故障。
4.(2)关于润滑方式的设计:针对轴承而言,如果轴承油脂选择不当,如选用锂皂-矿物油基润滑脂的轴承,一旦失效,轴承内部的油脂会随着混合气体一起进入到燃料电池系统内部,轴承油脂高温挥发性成分可以分散和附着在燃料电池内部的膜片上,使燃料电池系统中毒,造成燃料电池系统功率降低或停机;针对传动结构处的润滑而言,传统润滑方式采用液体润滑油,液体润滑油粘性小,流动性强,高温易挥发,容易泄漏;灰尘和水进入后会发生乳化。
5.(3)关于转子结构的设计:a、采用金属转子,并需在其外表面增加一层ptfe涂层,在高温酸性条件下运行时ptfe图层会出现剥落现象产生颗粒物,危害燃料电池;b、现有转子材料多为铝合金和不锈钢,铝合金转子在高温下运行容易与端盖或壳体发生粘结现象造成氢气循环泵停机;c、金属转子工艺复杂,成本高,报废率高;重量大,噪音大,运行时离心力和不平衡质量力大,功率高;d、金属转子热膨胀系数大,设计时需要留较大间隙,减小了氢气循环泵的容积效率;且抗冲击能力弱,松脱力小。
6.(4)关于传动结构的设计:在氢气循环泵中,采用一对啮合的齿轮实现传动,因而为防止齿轮的径向位置偏移,其固定安装尤为重要;现有技术中,通过机床打销孔,传递齿轮动力,工序比较复杂,需要额外工装制具的投入;销孔传递力矩有限,长时间运行容易产生间隙,若重复启停将导致使用寿命很短。
7.因此基于现有技术中存在的缺陷,本发明研制了一种耐高温水气低功耗燃料电池氢气循环泵,以解决现有技术中存在的问题。
技术实现要素:8.本发明目的是:提供一种耐高温水气低功耗燃料电池氢气循环泵,以解决现有技术中氢气循环泵的密封性与自润滑能力不足,在长时间工作后稳定性降低的问题。
9.本发明的技术方案是:一种耐高温水气低功耗燃料电池氢气循环泵,包括:驱动件,包括电机总成,用于提供动力;执行件,包括转子结构及转轴结构,将氢气泵送至燃料电池中;传动件,包括相啮合的齿轮结构,实现转子结构同步转动;支承件,包括供转轴结构平稳执行动作的轴承;其中,所述传动件,和/或支承件内构成有自润滑密封系统,所述自润滑密封系统形成于:具有密封腔室的轴承内,包括处于密封腔室内具有自润滑能力的保持架,以及容纳于密封腔室内部的固体润滑脂;和/或,齿轮结构安装的具有密封性能的齿轮腔内,所述齿轮腔内填充有固体润滑脂。
10.优选的,所述自润滑密封系统中:所述轴承具有一对密封件,所述密封腔室形成于一对密封件、以及轴承的内圈与外圈之间,并将固体润滑脂、轴承的滚动体及保持架容纳于其中;以g为单位的所述固体润滑脂的用量与以ml为单位的密封腔室体积成正比,比值范围为0.2~0.3;和/或,所述齿轮腔一侧端部具有一端盖,所述端盖的连接端面处设置有第一密封圈,所述齿轮腔的另一侧端部具有轴承;所述第一密封圈以及具有密封性能的轴承使所述齿轮腔内呈密封状,并将固体润滑脂容纳于其中,以g为单位的所述固体润滑脂的用量与以ml为单位的齿轮腔体积成正比,比值范围为0.2~0.35。
11.优选的,所述轴承中,具有自润滑能力的保持架采用peek与pa的组合,或者peek与cf、gf、ptfe的组合中的任意一种制成;所述密封件采用fkm或者fkm的改性材料制成,与内圈之间形成用于接触的第一密封部,与外圈之间形成用于接触的第二密封部,所述第一密封部采用多唇密封结构或面接触密封结构中的任意一种,所述第二密封部采用多唇密封结构或面接触密封结构中与第一密封部相异的另一种。
12.优选的,所述多唇密封结构包括外伸设置的第一唇口,至少一个第二唇口,以及第三唇口,对应接触的内圈或外圈上具有与第一唇口接触的第一面,与第二唇口接触的第二面,以及与第三唇口接触的第三面;所述第一面、第二面及第三面非同面设置,与第一唇口、
第二唇口及第三唇口形成多级密封防泄漏;所述面接触密封结构包括第一密封面及第二密封面,对应接触的内圈或外圈上具有与第一密封面相抵贴合的第四面,以及与第二接触面相抵贴合的第五面;所述第四面与第五面非同面设置,与第一密封面及第二密封面全接触增大接触面积防泄漏。
13.优选的,所述轴承中添加的固体润滑脂采用合成烃油、酯油、醚油及硅油中任意一种或多种的组合作为基础油,li、na、ba和ca的金属络合物皂及其混合物作为增稠剂,氧化镁和锆酸镁、磺酸盐、琥珀酸酯、亚硝酸盐中任意一种或多种的组合作为防锈剂,全氟辛基丙烯酸酯作为表面活性剂;其质量比为:基础油56%~72%,增稠剂12%~32%,防锈剂0.5%~2%,全氟辛基丙烯酸酯作为表面活性剂0.1%~0.5%;和/或,所述齿轮腔内的固体润滑脂采用氟系润滑剂作为基础油,聚四氟乙烯作为增稠剂,磺酸金属盐作为防锈剂,二硫代氨基甲酸碲和二硫代氨基甲酸硒作为磨损抑制剂;其质量比为:基础油50%~68%,增稠剂15%~32%,防锈剂1.2%~2.5%,磨损抑制剂0.5%~0.8%。
14.优选的,所述执行件,和/或传动件,和/或支承件内构成有增稳系统,所述增稳系统形成于:转子结构处,包括采用树脂材料制成的转子结构;和/或,轴承外壁处,包括开设于轴承外壁处的偏心槽,以及与偏心槽配合设置并具有弹性变形能力的防松圈;和/或,齿轮结构处,包括实现齿轮结构与转轴结构固定连接的胀套结构。
15.优选的,所述增稳系统中:所述转子结构包括同步转动的主动转子及从动转子,所述主动转子及从动转子均包括保持件,以及注塑成型于保持件外侧的树脂转子本体;所述保持件与转轴结构过盈配合,并通过定位孔及定位销的配合实现固定连接,所述保持件完全嵌合于树脂转子本体内;和/或,所述防松圈嵌合于偏心槽内,并能在不同状态下相对于偏心槽发生转动;常态下,所述防松圈内壁与偏心槽任意位置相抵时,最外缘始终凸出外圈;装配状态下,所述防松圈受压,通过弹性变形实现蓄能涨紧;工作状态下,所述防松圈在轴承松动过程中与外圈发生相对运动增加蓄能量;和/或,所述胀套结构包括内衬套及外衬套,以及将内衬套及外衬套锁止于转轴结构外壁与齿轮结构内壁之间的螺丝;由内至外依次设置的转轴结构、内衬套、外衬套及齿轮结构中,相接触的端面均采用过盈配合。
16.优选的,所述防松圈呈弓形,包括对称设置的第一弧形段,以及连接一对第一弧形段的第二弧形段;常态下,所述第一弧形段内壁与偏心槽内壁相抵;所述第二弧形段的内径小于第一弧形段的内径;所述防松圈在偏心槽内任意位置处时,所述第二弧形段中部均凸出外圈,因防松圈位置调整使凸出的距离形成一可调节的范围,该范围为0.1~0.5mm。
17.优选的,所述转轴结构包括主动转轴及从动转轴;
所述主动转轴上连接的部件由电机总成、一对轴承、主动转子、齿轮结构及胀套结构构成;一对所述轴承分设于主动转子两侧,具有密封性,缩短主动转轴的轴向长度,减小工作抱紧力矩;所述从动转轴上连接的部件由一对轴承、从动转子、齿轮结构及胀套结构构成;一对所述轴承分设于从动转子两侧,具有密封性,缩短从动转轴的轴向长度,减小工作抱紧力矩。
18.优选的,所述转子结构中,所述保持件包括一体成型的连接部及加强部,所述连接部呈管状结构,与转轴结构过盈配合,并通过贯穿连接部及转轴结构的定位销实现定位;所述加强部由连接部一侧向外延伸,呈弧线形结构,端面上具有若干贯穿设置的通口,增强树脂转子本体在注塑成型时的联结。
19.与现有技术相比,本发明的优点是:(1)本发明采用自润滑密封系统,满足氢气循环泵在高温、偏酸性的环境下的工作要求,因结构改进的同时解决氢气循环泵功耗、结构空间占用率问题;同时通过设计增稳系统,解决氢气循环泵强度及使用寿命的问题。
20.(2)通过对轴承的密封性进行改进,选择合适的密封件材料以及密封件结构,解决在燃料电池系统中,密封件密封失效的问题;通过对轴承的润滑方式进行改进,选择具有自润滑能力的保持架以及少量(相较于传统液体润滑油的用量)固体润滑脂,实现轴承的自润滑;通过密封与润滑方式的结合,解决油脂挥发及电堆中毒的问题。
21.(3)通过对齿轮腔的密封性进行改进,避免灰尘和水的进入、减少固体润滑脂的流失及变质;通过对齿轮腔内部的润滑方式进行改进,将传统的液体润滑油改为固体润滑脂,有效提高齿轮结构齿面的抗疲劳性能,降低传动过程中的噪音,减少齿面磨损,避免齿面粘接的损伤;同时,基于固体润滑脂本身的特性,粘附性好、流动性小,能牢固地粘附在被润滑表面上,即使在倾斜甚至垂直表面上也不易流失,具有良好的抗水性,通水不易乳化变质。
22.(4)基于轴承具有高效密封性,使得氢气循环泵中可以取消传统的油封和气封结构形式,直接采用轴承实现密封;在保证相同流量和压力等一系列的要求下,大大降低了抱紧力,减小功耗,其扭矩只有传统氢气循环泵的四分之一,功耗也只有传统氢气循环泵的二分之一;同时,因取消油封和气封结构,可有效缩短转轴结构轴向的长度,进而缩小氢气循环泵的长度尺寸及体积,降低空间占用率;再者,因传统的油封和气封结构采用ptfe材质,长时间转轴结构和气封、油封高转速高功耗磨合后,容易产生黑色颗粒物,黑色颗粒物质的直径在50-500μm之间,对燃料电池系统流道容易堵塞,而本发明基于轴承的密封,在满足同等的密封基础可以做到氢气循环泵对燃料电池系统零堵塞。
23.(5)通过对转子结构进行改进,采用树脂转子替换传统的金属转子,通过树脂转子本体与保持件的结合,制造工艺简单且成本低,基于树脂材料的选择,在高温酸性的条件下,运行时不会由于剥落产生颗粒物,进而避免危害燃料电池,也避免因磨损而产生稳定性降低的问题;同时解决传统转子高温下容易与端盖或壳体发生粘结的问题;再者,树脂材料的重量低,减少运行时的功率,降低运行时产生的噪音,增加转子的抗冲击能力及松脱力,同时树脂材料可以降低转子的热膨胀系数,减少设计时的间隙,提高氢气循环泵的容积效率。
24.(6)通过对轴承外壁处进行改进,增设偏心槽及防松圈,解决在恶劣的高温环境
下,轴承松动的问题,采用具有弹性变形能力的防松圈,在轴承安装后通过弹性变形蓄能实现防松,并结合偏心槽的设计,实现防松圈相较于外圈发生相对运动时蓄能量的调整,防止在高温运行过程中轴承出现松动,稳定性强。
25.(7)通过对齿轮结构与转轴结构的连接进行改进,增设胀套结构,解决氢气循环泵内部因齿轮结构安装易发生径向偏移的问题,通过胀套结构实现过盈配合进而完成齿轮结构的定位,优化了安装加工工序,实现简洁化,并且无需额外工装治具的投入,拆卸维修十分便利;再者,因胀套结构的设计,使得氢气循环泵长时间运行后齿轮的安装不会产生间隙,稳定性强,使用寿命也得到了有效的提高。
附图说明
26.下面结合附图及实施例对本发明作进一步描述:图1为本发明所述的一种耐高温水气低功耗燃料电池氢气循环泵的剖面图;图2为本发明所述的一种耐高温水气低功耗燃料电池氢气循环泵中a处的轴承示意图;图3为本发明所述轴承的爆炸图;图4为本发明所述轴承中密封件的设置结构示意图;图5为本发明所述轴承中密封件与装配结构处的分解图;图6为本发明所述轴承中偏心槽的设置结构示意图;图7为本发明所述防松圈的结构示意图;图8为本发明所述齿轮腔的结构示意图;图9为本发明所述转子结构的示意图;图10为本发明所述转子结构垂直于轴线方向的剖视图;图11为本发明所述转轴结构与保持件的连接结构示意图;图12为本发明所述主动转子与从动转子工作状态下的剖视图;图13为本发明所述的一种耐高温水气低功耗燃料电池氢气循环泵中b处的胀套结构的示意图;图14为本发明所述胀套结构的爆炸图。
27.其中:1、驱动件,11、电机总成,111、电机转子,112、电机定子;2、执行件,21、转子结构,22、转轴结构;211、主动转子,212、从动转子,221、主动转轴,222、从动转轴,23、树脂转子本体,24、保持件,241、连接部,242、加强部,243、通口;3、传动件,31、齿轮结构;311、主动齿轮,312、从动齿轮,32、齿轮腔,33、端盖,34、第一密封圈;4、支承件,41、轴承;411、内圈,412、外圈,413、滚动体,414、保持架,415、密封件,416、密封腔室,417、偏心槽,418、防松圈;42、多唇密封结构,421、第一唇口,422、第二唇口,423、第三唇口;43、面接触密封结构,431、第一密封面,432、第二密封面;44、第一面,45、第二面,46、第三面,47、第四面,48、第五面,49、第六面;
5、胀套结构;51、内衬套,52、外衬套,53、螺丝;6、液态水排放隔离装置;61、隔离罩,62、第二密封圈。
具体实施方式
28.下面结合具体实施例,对本发明的内容做进一步的详细说明:如图1所示,一种耐高温水气低功耗燃料电池氢气循环泵,包括驱动件1、执行件2、传动件3及支承件4。
29.驱动件1设置于壳体内,包括电机总成11,用于提供氢气循环泵工作所需的动力。
30.执行件2包括转子结构21及转轴结构22,转子结构21包括同步转动的主动转子211及从动转子212,转轴结构22包括与主动转子211固定连接的主动转轴221,以及与从动转子212固定连接的从动转轴222,通过主动转子211与从动转子212的同步转动将氢气泵送至燃料电池中。
31.传动件3包括相啮合的齿轮结构31,齿轮结构31包括主动齿轮311及从动齿轮312,主动齿轮311与主动转轴221固定连接,从动齿轮312与从动转轴222固定连接,通过齿轮结构31的传动用于实现转子结构21同步转动。
32.支承件4包括供转轴结构22平稳执行动作的轴承41,主动转子211两侧及从动转子212两侧均设置有该轴承41。
33.本发明中,传动件3,和/或支承件4内构成有自润滑密封系统;执行件2,和/或传动件3,和/或支承件4内构成有增稳系统。
34.a、关于支承件4内的自润滑密封系统:如图2所示,形成于轴承41内的密封腔室416中,包括处于密封腔室416内具有自润滑能力的保持架414,以及容纳于密封腔室416内部的少量固体润滑脂。
35.关于“自润滑密封系统”所体现的性能是“密封”与“自润滑”的结合,因润滑能力的优势是基于结构的密封性才得以实现的,因此,关于轴承41内的“密封”结构主要如下:结合图2、图3所示,轴承41包括内圈411、外圈412、滚动体413、保持架414及一对密封件415,密封腔室416形成于一对密封件415、以及内圈411与外圈412之间,进而将固体润滑脂、轴承41的滚动体413及保持架414容纳于其中。
36.密封件415采用fkm或者fkm的改性材料制成,如图4所示,与内圈411之间形成用于接触的第一密封部,与外圈412之间形成用于接触的第二密封部,第一密封部采用多唇密封结构42或面接触密封结构43中的任意一种,第二密封部采用多唇密封结构42或面接触密封结构43中与第一密封部相异的另一种。
37.结合图5所示,多唇密封结构42包括外伸设置的第一唇口421,至少一个第二唇口422,以及第三唇口423,对应接触的内圈411上具有与第一唇口421接触的第一面44,与第二唇口422接触的第二面45,以及与第三唇口423接触的第三面46;上述第一面44、第二面45及第三面46是基于在内圈411的外壁处开设有第一槽口而形成的,其中第一面44为内圈411的外壁面,属于一弧形面,第二面45为第一槽口处对应的台阶面,第三面46也属于一弧形面,其对应的外径小于内圈411主体结构的外径;基于此,第一面44、第二面45及第三面46即为
非同面设置,与第一唇口421、第二唇口422及第三唇口423形成多级密封防泄漏。
38.面接触密封结构43包括第一密封面431及第二密封面432,对应接触的外圈412上具有与第一密封面431相抵贴合的第四面47,以及与第二接触面相抵贴合的第五面48;上述第四面47及第五面48是基于在外圈412的内壁处开设有第二槽口而形成的,其中第四面47为第二槽口处对应的台阶面,第五面48为第二槽口内壁对应的弧形面;基于此,第四面47与第五面48即为非同面设置,与第一密封面431及第二密封面432全接触增大接触面积防泄漏;同时,第二槽口处与第四面47相对的端面为第六面49,并与第四面47呈非平行设置,结合第二面45、第四面47及第六面49,实现密封件415沿轴向的限位;第一面44、第三面46及第五面48的设置,实现密封件415沿径向的限位。
39.上述第一槽口与第二槽口的设置,形成了若干非同面设置的面结构,用于实现与密封件415的多级密封,并使密封件415限制于内圈411与外圈412之间;通过一对密封件415的设置,在内圈411与外圈412之间形成具有密封性且防止物质挥发的密封腔室416。
40.因轴承41具有密封性,因此本发明中主动转轴221上连接的部件仅由电机总成11、一对轴承41、主动转子211、齿轮结构31及胀套结构5构成;从动转轴222上连接的部件仅由一对轴承41、从动转子212、齿轮结构31及胀套结构5构成;其中关于胀套结构5在下文中具有详细赘述;相较于传统的氢气循环泵结构,本发明中无需采用油封与气封的结构形式,缩短主动转轴221及从动转轴222的轴向长度,缩小氢气循环泵的长度尺寸及体积,减小工作抱紧力矩,降低了功耗。同时也避免了传统油封、气封结构在长期工作磨损后所产生的弊端。
41.基于上述“密封”结构的设计,关于轴承41内的“自润滑”设计主要如下:采用“具有自润滑能力的保持架414”与“少量固体润滑脂”的组合。
42.保持架414的自润滑能力是基于其材料的选择,本实施例中采用peek与pa的组合,或者peek与cf、gf、ptfe的组合中的任意一种制成。
43.少量固定润滑脂中少量的定义是基于传统轴承41中液体润滑油的用量而言,具体的,以g为单位的固体润滑脂的用量与以ml为单位的密封腔室416体积成正比,比值范围为0.2~0.3;而传统的轴承41,以g为单位的液体润滑油的用量与以ml为单位的腔室体积成正比,比值范围为0.6~0.8。而关于固体润滑脂的组分,采用合成烃油、酯油、醚油及硅油中任意一种或多种的组合作为基础油,li、na、ba和ca的金属络合物皂及其混合物作为增稠剂,氧化镁和锆酸镁、磺酸盐、琥珀酸酯、亚硝酸盐中任意一种或多种的组合作为防锈剂,全氟辛基丙烯酸酯作为表面活性剂;其质量比为:基础油56%~72%,增稠剂12%~32%,防锈剂0.5%~2%,全氟辛基丙烯酸酯作为表面活性剂0.1%~0.5%。
44.结合上述“密封”及“自润滑”,能够有效减少固体润滑脂的挥发,同时可以尽量避免因固体润滑脂挥发到系统内部造成电堆中毒的可能性。
45.b、关于传动件3内的自润滑密封系统:如图8所示,形成于齿轮结构31安装的具有密封性能的齿轮腔32内,齿轮腔32内填充有固体润滑脂。
46.关于“自润滑密封系统”所体现的性能是“密封”与“自润滑”的结合,因此,齿轮腔32内的“密封”结构主要如下:如图8所示,齿轮腔32一侧端部具有一端盖33,端盖33的连接端面处设置有第一密
封圈34,进而实现图示中左侧端的密封;齿轮腔32的另一侧端部具有轴承41,因轴承41本身具有密封性,进而实现图示中右侧端的密封,最终实现了齿轮腔32的密封。
47.基于上述“密封”结构的设计,关于齿轮腔32内的“自润滑”设计主要如下:采用固体润滑脂替代传统的液体润滑油,以g为单位的固体润滑脂的用量与以ml为单位的齿轮腔32体积成正比,比值范围为0.2~0.35;其组份采用氟系润滑剂作为基础油,聚四氟乙烯作为增稠剂,磺酸金属盐作为防锈剂,二硫代氨基甲酸碲和二硫代氨基甲酸硒作为磨损抑制剂;其质量比为:基础油50%~68%,增稠剂15%~32%,防锈剂1.2%~2.5%,磨损抑制剂0.5%~0.8%。
48.结合上述“密封”及“自润滑”,因固体润滑脂相对于传动的液体润滑油而言,粘附性好、流动性小,能牢固地粘附在被润滑表面上,即使在倾斜甚至垂直表面上也不易流失,具有良好的抗水性,通水不易乳化变质;因此本发明中端盖33结构无需设计传统的注油孔、观察孔及漏油腔,成型工艺简单且端盖33处的体积能够实现缩小,进一步实现氢气循环泵的体积减小。
49.c、关于执行件2内的增稳系统:如图9、图10所示,形成于转子结构21处,包括采用树脂材料制成的转子结构21,具体包括保持件24,以及注塑成型于保持件24外侧的树脂转子本体23;保持件24与转轴结构22过盈配合,并通过定位孔及定位销的配合实现固定连接,保持件24完全嵌合于树脂转子本体23内。
50.结合图11所示,保持件24包括一体成型的连接部241及加强部242,连接部241呈管状结构,与转轴结构22过盈配合,并通过贯穿连接部241及转轴结构22的定位销实现定位;加强部242由连接部241一侧向外延伸,呈弧线形结构,端面上具有若干贯穿设置的通口243,增强树脂转子本体23在注塑成型时的联结。
51.如图12所示,工作时,主动转子211与从动转子212同步转动,两者之间必然存在摩擦,而采用树脂注塑成型的树脂转子本体23运行时不会由于剥落产生颗粒物,进而避免危害燃料电池;成型工艺简单,结构重量减小,降低了运行时的功率及噪音,增加转子结构21的抗冲击能力及松脱力,同时降低转子结构21的热膨胀系数,减少设计时的间隙,提高氢气循环泵的容积效率。
52.d、关于支承件4内的增稳系统:如图2、图6所示,形成于轴承41外壁处,包括开设于轴承41外壁处的偏心槽417,以及与偏心槽417配合设置并具有弹性变形能力的防松圈418;如图7所示,防松圈418呈弓形,包括对称设置的第一弧形段4181,以及连接一对第一弧形段4181的第二弧形段4182,其嵌合于偏心槽417内,并能在不同状态下相对于偏心槽417发生转动。
53.常态下,第一弧形段4181内壁与偏心槽417内壁相抵;第二弧形段4182的内径小于第一弧形段4181的内径;防松圈418内壁与偏心槽417任意位置相抵时,最外缘始终凸出外圈412;装配状态下,防松圈418受压,通过弹性变形实现蓄能涨紧;工作状态下,防松圈418在轴承41松动过程中与外圈412发生相对运动增加蓄能量。
54.基于上述动作过程,防松圈418在偏心槽417内任意位置处时,第二弧形段4182中
部均凸出外圈412,因防松圈418位置调整使凸出的距离形成一可调节的范围,该范围为0.1~0.5mm。
55.在装配时,需将轴承41连同防松圈418压装至轴承室内,初始阶段,防松圈418处于偏心槽417偏离中心最小值位置处,压装完成后,防松圈418会发生弹性变形而实现蓄能,此时具有压装状态下的最小蓄能量,防止在高温运行过程中轴承41出现松动;若因高温环境引发轴承41出现松动问题,防松圈418与轴承41之间会发生相对运动,蓄能量增加,进一步增加防松效果,当防松圈418运行至偏心槽417偏离中心最大值位置处时,此时具有压装状态下的最大蓄能量。
56.综合偏心槽417及防松圈418的设计,本发明解决在恶劣的高温环境下,轴承41松动的问题,采用具有弹性变形能力的防松圈418,在轴承41安装后通过弹性变形蓄能实现防松,并结合偏心槽417的设计,实现防松圈418相较于外圈412发生相对运动时蓄能量的调整,防止在高温运行过程中轴承41出现松动。
57.e、关于传动件3内的增稳系统:如图13、图14所示,形成于齿轮结构31处,包括实现齿轮结构31与转轴结构22固定连接的胀套结构5;胀套结构5包括内衬套51及外衬套52,以及将内衬套51及外衬套52锁止于转轴结构22外壁与齿轮结构31内壁之间的螺丝53;由内至外依次设置的转轴结构22、内衬套51、外衬套52及齿轮结构31中,相接触的端面均采用过盈配合;相较于传统的孔与销的配合,本发明工序简单,且无需额外的工装治具,拆卸维修也十分便利。
58.综合上述,基于本发明的“自润滑密封系统”及“增稳系统”,与之带来的结构尺寸及体积的缩小、功耗的降低、内部零堵塞的优势也十分明显;其中:结构尺寸及体积的缩小,基于油封和气封的结构形式取消、以及端盖33中注油孔、观察孔及漏油腔的取消;功耗的降低,基于油封和气封的结构形式取消、树脂转子本体23与保持件24的组合替换传统金属转子;内部零堵塞,基于油封和气封的结构形式取消、树脂转子本体23与保持件24的组合替换传统金属转子。
59.作为本实施例的进一步优化,驱动件内还设置有液态水排放隔离装置6,该液态水排放隔离装置包括隔离罩61及第二密封圈62;关于电机总成11,包括电机转子111及电机定子112,其中隔离罩61采用灌胶固定形式与电机定子112结合成一体,端面与连接驱动件1及执行件2的法兰盘端面相抵,法兰盘端面上开设有供第二密封圈62安装的密封槽,安装第二密封圈62后通过法兰盘螺丝及电机壳体螺丝实现整体结构的固定安装,以通过第二密封圈62的压缩保证法兰盘与隔离罩61之间的平面密封,有效解决氢气循环泵长时间运行导致高温水气进入电机转子111内而无法正常工作的一系列问题。
60.上述实施例只为说明本发明的技术构思及特点,其目的在于让熟悉此项技术的人能够了解本发明的内容并据以实施,并不能以此限制本发明的保护范围。对于本领域技术人员而言,显然本发明不限于上述示范性实施例的细节,而且在不背离本发明的精神或基本特征的情况下,能够以其他的具体形式实现本发明,因此无论从哪一点来看,均应将实施例看作是示范性的,而且是非限制性的,本发明的范围由所附权利要求而不是上述说明限定,因此旨在将落在权利要求的等同要件的含义和范围内的所有变化囊括在本发明内。