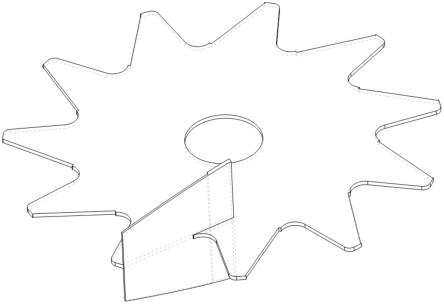
1.本实用新型涉及离心风机叶轮领域,尤其涉及一种整体叶片焊接双吸式离线风机叶轮。
背景技术:2.众所周知,双吸式风机相比单吸式风机,流量系数q更大,因此能够提供相对单吸风机更大的气体流量,特别适用于诸多大流量气体需求的行业领域。
3.目前,行业内的双吸式离心风机均采用单轴双支撑“f”型式,即主轴中部布置离心双吸式叶轮,主轴与叶轮轴向及周向固定一体后,两端分别布置径向定子支撑。一般情况下,双吸式风机叶轮的进口直径、出口直径及叶轮宽度尺寸相对较大。一方面,双吸式风机叶轮的成型要求较高,焊接工艺及工序复杂,成本较高;另一方面,大型双吸式风机叶轮在相同的旋转周速度下,结构力学及动力学性能要求也相对较高。如何在满足结构力学及动力学性能要求,节省叶轮生产制造成本,提高制作效率是本发明的目的。
4.传统的双吸式叶轮主要制作方法:叶轮中盘、叶轮前盘(轮盘)、叶轮叶片数控下料,中盘两侧布置叶片,叶片在中盘上划线定位后焊接成型,焊接总成如图1所示。前盘加工成形后,分别与图1所示的焊接总成的两侧焊合,至此,叶轮整体焊接总成完成如图2。叶轮整体按技术要求机加后,制作基本完成。传统的双吸式叶轮制作主要存在以下缺点:首先,叶片与中盘焊接定位,需要手动划线,消耗大量人工成本。其次,叶片与中盘焊接时采用变位焊接且焊接时严格控制焊接变形,以满足焊后垂直度,平整度,两侧叶轮的对称度等一系列技术要求,需要专业工装,消耗大量制作成本。再者,为了满足叶轮结构力学及动力学性能要求,叶轮结构细节部位需要加强、补刚设计,需要延长叶轮制作时间,降低了制作效率。
5.申请号为202022874359.5的专利文件公开了“一种电炉炼钢除尘增压风机的叶轮结构装置”,该叶轮结构是在中盘上预先切割槽口,将叶片插入槽口进行装配。中盘装配若干叶片,需要加工多个槽口,加工工艺复杂,制作成本高。
技术实现要素:6.本实用新型的目的是提供一种整体叶片焊接双吸式离线风机叶轮,该叶轮节省了生产制造成本,提高了制作效率。
7.为实现上述目的,本实用新型采用以下技术方案实现:
8.一种整体叶片焊接双吸式离线风机叶轮,包括前盘、中盘、叶片,所述叶片一侧带有插口,所述叶片通过插口与中盘插接后焊接固定,所述前盘焊接固定在叶片的两端,所述前盘为不等厚结构。
9.所述前盘是由前盘进口段和前盘出口段构成,所述前盘进口段与前盘出口段焊接固定,所述前盘进口段为锻造成型的不等壁厚结构。
10.所述前盘进口段的外壁为锥形,所述前盘进口段的内壁为弧形。
11.所述前盘出口段为冷压成形的等壁厚锥形。
12.与现有的技术相比,本实用新型的有益效果是:
13.本实用新型提供了一种整体叶片焊接双吸式离心风机叶轮,在不改变原有叶轮整体结构设计的前提下,采用整体式叶片先插接定位后焊接固定,实现了装配过程中的自动定位,降低焊接工艺成本,提高制作效率;轮盘锻造进口段与冷压成型出口段焊接轮盘结构提高了轮盘结构的强度和入口刚度,优化了叶轮的结构力学及结构动力学。
14.本实用新型具有设计新颖、工艺简单,易于成型、安全可靠等优点。
附图说明
15.图1传统双吸式叶轮叶片与中盘的焊接总成图。
16.图2传统双吸式叶轮焊接总成图。
17.图3是本实用新型一种整体叶片焊接双吸式离心风机叶轮示意图。
18.图4是本实用新型一种整体叶片焊接双吸式离心风机叶轮的中盘示意图。
19.图5是本实用新型的插入式整体式叶片示意图。
20.图6是本实用新型的插入式整体式叶片与中盘焊合示意图。
21.图7是本实用新型的不等厚前盘焊接示意图。
22.图8是本实用新型的不等厚前盘焊合示意图。
23.图中:1-中盘、2-叶片、2-1插口、3-前盘、3-1前盘出口段、3-2前盘进口段、4-叶轮本体、5-现有技术的中盘、6-现有技术的叶片、7-现有技术的前盘。
具体实施方式
24.下面结合实施例对本实用新型做详细说明,但本实用新型的实施范围不仅仅限于下述的实施例。
25.如图3-图8所示,一种整体叶片焊接双吸式离线风机叶轮,包括前盘3、中盘1、叶片2,所述叶片2一侧带有插口2-1,所述叶片2通过插口2-1与中盘1插接后焊接固定,所述前盘3焊接固定在叶片2的两端,所述前盘3为不等厚结构。
26.所述前盘3是由前盘进口段3-2和前盘出口段3-1构成,所述前盘进口段3-2与前盘出口段3-1焊接固定,所述前盘进口段3-2为锻造成型的不等壁厚结构。
27.所述前盘进口段3-2的外壁为锥形,所述前盘进口段3-2的内壁为弧形。
28.所述前盘出口段3-1为冷压成形的等壁厚锥形。
29.如图4所示,中盘1由数控下料后机加制作。如图5所示,插入式整体叶片2同样由数控下料后机加制作。插入式整体叶片2通过插口2-1作为“定位槽”插入到中盘1上,焊合一体,如图6所示。
30.见图7,不等厚前盘3分别由前盘进口段3-2和前盘出口段3-1组成,不等厚前盘3中的前盘进口段3-2为锻造加工而成,不等厚前盘3中前盘出口段3-1为数控下料后压型而成,通过焊接将前盘进口段3-2和前盘出口段3-1焊合为不等厚前盘3,见图8。通过焊接将焊合后的不等厚前盘3分别与叶片2和中盘1的焊接体中的叶片2端部焊合,至此,一种整体叶片焊接双吸式离心风机叶轮本体4焊接制作完成。
31.区别于以往传统的双吸式叶轮叶片(两片)对称焊接在中盘两侧的结构,本实用新型的双吸式叶轮叶片为插入式整体叶片(一片),叶片2依据与中盘1的焊接尺寸采用自动定
位的插口“定位槽”的限位设计。实现了装配过程中的自动定位,降低焊接工艺成本,提高制作效率。
32.不等厚前盘3采用两段式焊接设计。其中,前盘进口段3-2采用不等厚的异形锻造件,该不等厚异形锻造件内壁(与工作介质接触一面)按照叶轮流体型线的弧形设计。前不等厚锻造件盘进口段3-2与冷压件前盘出口段3-1焊合为一体制成不等厚前盘。
33.同一叶轮的两侧分别为不等厚与等厚轮盘,有限元仿真计算结果显示:同一叶轮的一侧等厚轮盘的冯米斯应力最大值约为360mpa,同一叶轮的另一侧不等厚轮盘(本实用新型)的冯米斯应力最大值约为234mpa,可见,本实用新型不等厚轮盘的整体强度得到了较大幅度的提高。
34.叶轮固有频率在150hz、165hz、187hz的有限元模态刚度计算,同一叶轮同一振动频率下不等厚轮盘的模态刚度明显优于传统等厚轮盘,在同一外激励下,不等厚轮盘的振动响应要小于传统的等厚轮盘,通过实验证明叶轮采用不等厚轮盘后的振动特性得到了优化。
技术特征:1.一种整体叶片焊接双吸式离线风机叶轮,包括前盘、中盘、叶片,其特征在于,所述叶片一侧带有插口,所述叶片通过插口与中盘插接后焊接固定,所述前盘焊接固定在叶片的两端,所述前盘为不等厚结构。2.根据权利要求1所述的一种整体叶片焊接双吸式离线风机叶轮,其特征在于,所述前盘是由前盘进口段和前盘出口段构成,所述前盘进口段与前盘出口段焊接固定,所述前盘进口段为锻造成型的不等壁厚结构。3.根据权利要求2所述的一种整体叶片焊接双吸式离线风机叶轮,其特征在于,所述前盘进口段的外壁为锥形,所述前盘进口段的内壁为弧形。4.根据权利要求2所述的一种整体叶片焊接双吸式离线风机叶轮,其特征在于,所述前盘出口段为冷压成形的等壁厚锥形。
技术总结本实用新型涉及一种整体叶片焊接双吸式离线风机叶轮,包括前盘、中盘、叶片,所述叶片一侧带有插口,所述叶片通过插口与中盘插接后焊接固定,所述前盘焊接固定在叶片的两端,所述前盘为不等厚结构。与现有的技术相比,本实用新型的有益效果是:本实用新型提供了一种整体叶片焊接双吸式离心风机叶轮,在不改变原有叶轮整体结构设计的前提下,采用整体式叶片先插接定位后焊接固定,实现了装配过程中的自动定位,降低焊接工艺成本,提高制作效率,优化了叶轮的结构力学及动力学。本实用新型具有设计新颖、工艺简单,易于成型、安全可靠等优点。安全可靠等优点。安全可靠等优点。
技术研发人员:王洪磊 闫龙寅 战阳
受保护的技术使用者:鞍山钢峰风机有限责任公司
技术研发日:2022.02.23
技术公布日:2022/10/24