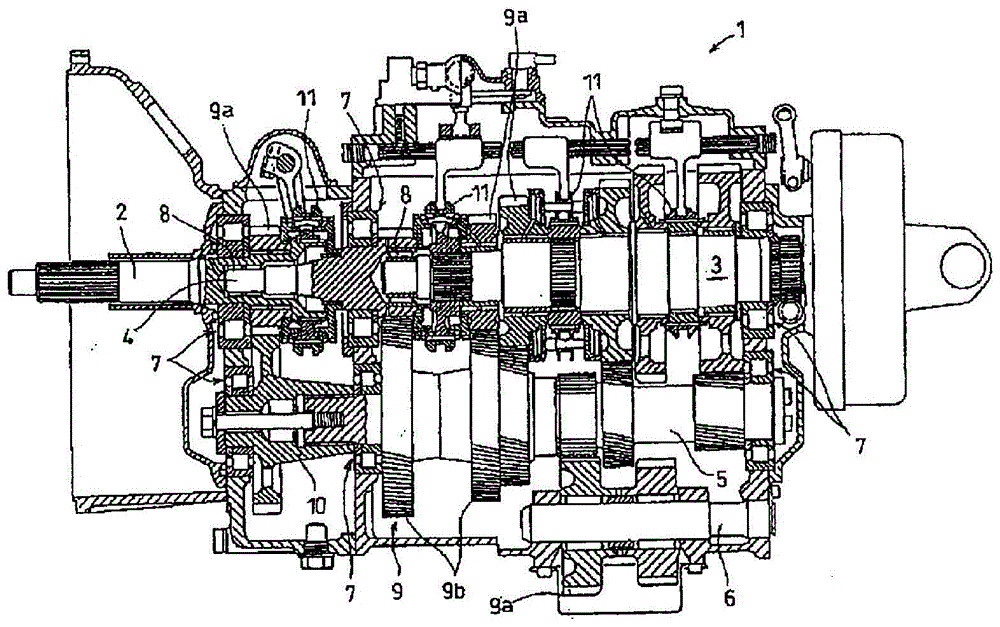
本发明涉及滚动轴承的滚道圈中间部件,更详细而言,本发明规定在制造滚道圈的工序中热处理后的就要进行研磨工序之前的材料(即“滚道圈中间部件”)的表层状态。另外,本发明涉及由上述滚道圈中间部件得到的滚道圈,进而涉及具备上述滚道圈的滚动轴承。进而,本发明涉及滚动轴承的滚道圈的制造方法以及滚动轴承的制造方法,更详细而言涉及一种技术,该技术研究热处理而控制残留应力的分布,抑制研磨后得到的滚道圈的圆度降低,制造高精度的滚动轴承。
背景技术:
:近年来,就圆柱滚子轴承、滚针轴承而言,根据应用而需求小型/轻量化,随之,不仅轴承尺寸需求小型化,其内圈、外圈也需求薄壁化。例如,可举出汽车变速箱、计算机断层扫描仪(ct扫描)等。在现有技术中,通过对滚道圈的表面进行硬化处理以补足因薄壁化、小型化而导致的耐久性的缺失量,例如在专利文献1的变速箱用轴承中,实施渗碳、碳氮共渗来提高滚道圈表面的残留奥氏体量,使得即使在混入异物的润滑环境下也延长寿命。图1是示出车辆用变速箱的一例的剖视图,该变速箱为手动式,在壳体1内直列配置有输入轴2、输出轴3及作为中间轴的导轴4,进而还与输出轴3平行地配置有作为中间轴的副传动轴5和反转轴6。除反转轴6以外的各轴2、3、5以及导轴4被圆柱滚子轴承7、滚针轴承8旋转自如地支承,各轴2、3、5、6安装有多个齿轮组9。另外,副传动轴5还安装有一端被圆柱滚子轴承7支承的齿轮部件10。输入轴2、输出轴3及反转轴6的齿轮9a旋转自如地安装在各轴2、3、6,这些旋转自如的齿轮9a和导轴4与副传动轴5的任一齿轮9b或齿轮部件10啮合。这些齿轮9a,在根据来自外部的操作而换挡的离合器毂11中,对于各安装轴2、3、6选择性地使旋转同步,恰当地选择从输入轴2向输出轴3的力矩传递路径。而且,对圆柱滚子轴承7、滚针轴承8的内圈、外圈进行渗碳、碳氮共渗处理而进行强化,实现薄壁化。现有技术文献专利文献专利文献1:日本特开2001-200851号公报技术实现要素:发明欲解决的技术问题滚动轴承对各部件需求高硬度,因此需要淬火处理,由此而生的椭圆变形不可避免。进而,就实施了通过渗碳、碳氮共渗实现的表面硬化处理的滚道圈而言,大多进行该处理后的淬火以及此后用于组织调整的再淬火,助长了椭圆变形。而且,越是为了小型/轻质化而被薄壁化,变形量越大。因此有时会追加矫正作业,但会影响制造成本中。另外,滚动轴承是用于维持顺畅的旋转的机械元件,在热处理后实施研磨加工以接近正圆。此时要求的圆度大小需要微米级的控制,但在该研磨加工时滚道圈会发生形变,有时无法确保充分的旋转精度。作为其对策,有时反复进行研磨以控制在要求尺寸精度,但研磨工序中的负担会增加而生产率降低,影响制造成本。若圆度不足则轴承的旋转精度变差,会大幅影响汽车的油耗,因此,在变速箱用滚动轴承中,热处理导致的椭圆变形、研磨工序中的圆度下降成为很大的问题。具体而言,若支承输入轴2、输出轴3的圆柱滚子轴承7、滚针轴承8的圆度低,则输入轴2、输出轴3发生偏心,离合器毂11不能很好地与齿轮9a、9b啮合或者会产生金属粉末等,导致变速箱整体发生力矩损耗。作为其结果,引起汽车的油耗变差等。可以考虑使衬垫介于轴承与轴之间以调整轴承的圆度,但另外需要用于调整的作业。于是,本发明的目的在于提供一种滚道圈中间部件,其用于防止研磨工序中的滚道圈的圆度下降,以高效地得到旋转精度优异的滚动轴承。另外,本发明的目的在于提供一种能够防止研磨后得到的滚道圈的圆度下降的方法。进而,实现提供一种圆度高的滚道圈以及具备圆度高的滚道圈而旋转性能优异的滚动轴承。用于解决问题的技术手段本发明人等对上述的圆度下降进行了深入研究,结果得到以下发现。例如在外圈的制造方法中,在研磨工序中,通常在研磨外径侧后研磨内径侧的滚道面。热处理导致的椭圆变形量根据各滚道圈而各不相同,例如在汽车用的变速箱所使用的轴承中为数百微米左右。对这样的滚道圈进行研磨而加工至妥善的圆度(该情况下为10微米左右),但此时,研磨工序中的加工余量在外径和内径侧均会因椭圆变形而变得不均匀。外径侧的研磨能够通过通常的加工而得到妥善的圆度。但是,若接着对内径侧同样进行研磨,则已调整好的外径侧的圆度会被破坏,有时会超出上述的妥善的范围。该现象源于残留应力释放,由于不均匀地去除存在残留应力的部位而产生。虽然准确而言是在研磨外径侧时也会在内径侧产生的现象,但是与热处理变形量相比低至1/10左右,且此后会被研磨,因此不会成为问题。因此,作为解决方案,可以考虑如上所述通过矫正热处理时的变形来使加工余量均匀的方法以及即使加工余量不均匀也将加工余量内的残留应力控制得较少的方法。即可以认为,为了抑制研磨时的变形,缓和加工余量内的残留应力(接近0)的方法是有效的。研磨加工导致的滚道圈的形变由因残留应力的不均匀释放而产生的应力以及滚道圈对变形的抵抗、即刚性决定。对于应力,由加工余量的不均匀差与残留应力的函数表示。加工余量的不均匀由热处理变形量决定,因此若已知热处理时的变形量和加工余量深度、加工余量内的残留应力的平均值,则能够计算因研磨产生的应力值。滚道圈的变形抵抗、即刚性由作为元件的形状和材料的杨氏模量以及外圈的直径和壁厚决定。根据以上理论,在设定为环这样的基本形状的基础上,若确定了目标的圆度、通过研磨加工去除的部位的量(加工余量),则能顾根据弹簧定律(胡克定律)计算出作为目标的残留应力的值。另一方面,残留应力是由于元件产生不均匀形变而产生的应力,其原因在于热处理、机械加工、成分的不均等各种各样的方面。这种不均匀不限于圆周方向的不均匀。例如,由于在上述的渗碳、碳氮共渗中碳、氮从部件表面侵入,部件的截面(深度方向)成为渗碳层与非渗碳层(芯部)这样的不均匀状态,因此产生残留应力。已知通常而言在淬火后渗碳层产生压缩的残留应力。另外,若产生应力则元件发生变形,而变形停止则意味着自然地产生了可将产生的应力抵消这样的应力。已知在以上记述的渗碳的情况下,芯部实现了抵消渗碳层的应力的作用。在大多元件中,芯部比渗碳层具有更大的体积,因此由其整体抵消,芯部的残留应力大致为0,具体而言,大多成为0~+100mpa以下。通常的渗碳层的残留应力大多为约-300mpa左右,表现出从表面到内部明显減少(接近0)的变化。在以下所示的本发明中,通过研究热处理条件而降低在这种渗碳层中产生的残留应力。芯部的残留应力如上所述,仍然为0~+100mpa以下。因此,在本发明中,即使具有与现有产品同样的渗碳深度,也能够通过控制热处理的条件来缓和渗碳层中产生的压缩的残留应力,由此,与现有产品相比,能够明显地使朝向芯部方向的残留应力的梯度变得平缓。具体而言,不仅可使渗碳层中产生的残留应力为压缩范围,甚至成功地使其减半,使其梯度明显变得平缓。本发明基于这样的发现,提供下述的滚动轴承的滚道圈中间部件、滚道圈、滚动轴承及它们的制造方法。(1)一种滚动轴承的滚道圈中间部件,是热处理后且研磨前的状态下的滚道圈中间部件,其特征在于,所述滚道圈中间部件具有表面硬化层,并且,在该中间部件中,从表面到芯部的残留应力的梯度平缓。(2)根据上述(1)所述的滚道圈中间部件,其特征在于,从所述表面到所述芯部的径向上的各部位的平均残留应力的绝对值为0~191mpa。(3)根据上述(2)所述的滚道圈中间部件,其特征在于,从所述表面到所述芯部的径向上的各部位的平均残留应力的绝对值为0~111mpa。(4)根据上述(1)~(3)中任一项所述的滚道圈中间部件,其特征在于,所述滚道圈中间部件由表面硬化钢形成,所述表面硬化层为渗碳表面硬化层、渗氮表面硬化层或碳氮共渗表面硬化层。(5)根据上述(1)~(4)中任一项所述的滚道圈中间部件,其特征在于,是圆锥滚子轴承或球轴承的滚道圈用中间部件。(6)一种滚动轴承的滚道圈中间部件,为热处理后且研磨前的状态下的滚道圈中间部件,其特征在于,所述滚道圈中间部件具有表面硬化层,并且,在所述滚道圈中间部件中,从表面到芯部的径向上的各部位的平均残留应力的绝对值为0~191mpa。(7)一种滚动轴承的滚道圈,其特征在于,由上述(1)~(6)中任一项所述的滚动轴承的滚道圈中间部件而得到。(8)一种滚动轴承,其特征在于,具备上述(7)所述的滚道圈。(9)一种滚动轴承的滚道圈的制造方法,具备从原材料切出圆环部件,形成表面硬化层,进行淬火、回火,然后对所述圆环部件的内径面和外径面进行研磨的一系列工序,所述滚动轴承的滚道圈的制造方法的特征在于,在所述淬火后将所述圆环部件的表面温度急冷至50℃以下而制成滚道圈中间部件,在回火后对所述滚道圈中间部件的内径面和外径面进行研磨。(10)根据上述(9)所述的滚动轴承的滚道圈的制造方法,其特征在于,在所述淬火后,利用清洗液对所述圆环部件一并进行清洗和所述急冷。(11)根据上述(9)或(10)所述的滚动轴承的滚道圈的制造方法,其特征在于,在研磨前的所述滚道圈中间部件中,使从表面到芯部的残留应力的梯度变得平缓。(12)根据上述(9)~(11)中任一项所述的滚动轴承的滚道圈的制造方法,其特征在于,使从表面到芯部的径向的各部位的平均残留应力的绝对值为0~191mpa。(13)一种滚动轴承的制造方法,其特征在于,具有进行上述(9)~(12)中任一项所述的滚道圈的制造方法的工序。发明效果就本发明的滚道圈中间部件而言,在从其表面到芯部的深度方向上,在研磨工序的加工余量内,具体而言,从50μm的深度位置到250μm的深度位置的残留应力与现有产品相比接近0,平缓至朝向非渗碳层即芯部其变化几乎为零的程度。由于芯部的残留应力接近0,因此研磨的加工余量内的残留应力必然被控制得很低。作为结果,在对通常的具有椭圆变形的滚道圈中间部件实施了研磨加工后,滚道圈不易产生变形,能够高效地得到圆度良好的滚道圈的成品。另外,本发明的滚道圈虽然是对上述的滚道圈中间部件的内径面和外径面进行研磨而得到,但由于在研磨时抑制了圆度的下降,因此圆度变高。而且,具备该圆度高的滚道圈的滚动轴承的旋转精度优异。需要说明的是,残留应力的测定通常通过x射线衍射法进行。例如,渗碳等热处理后的最表面的组织由于氧化等而形成有化合物,该状态不适于测定。因此,为了检测金属组织对残留应力的影响,通常利用电解研磨去除该部分,本次考虑表面的影响层的深度而将50μm深度的值与最表面同等地进行评价。在理论上,作为轴承制造界的常识,只要不进行一些有意的处理,则残留应力在更浅的区域本质上不会大幅度变化,基本为同等水平的残量应力值。附图说明图1是示出车辆用变速箱的一例的剖视图。图2是示出预备试验的结果的图像,示出圆环部件的表面温度与残留应力的关系。图3是示出比较例1中的残留应力的深度方向的分布的图像。图4是示出实施例1中的残留应力的深度方向的分布的图像。图5是示出实施例2中的残留应力的深度方向的分布的图像。图6中,(a)是示出实施例1中得到的研磨后的试验片的圆度分布的图像,(b)是示出实施例2中得到的研磨后的试验片的圆度分布的图像,(c)是示出比较例1中得到的研磨后的试验片的圆度分布的图像。符号说明1壳体2输入轴3输出轴4导轴5副传动轴6反转轴7圆柱滚子轴承8滚针轴承9齿轮组9a、9b齿轮10齿轮部件11离合器毂具体实施方式以下参照附图详细说明本发明。需要说明的是,在以下的说明中,也会将滚动轴承的滚道圈中间部件简称为“滚道圈中间部件”。在本发明中,滚动轴承的种类没有限制。作为滚动轴承,通常为圆锥滚子轴承、球轴承、圆柱滚子轴承、滚针轴承等,在本发明中以这些滚动轴承乃至其滚道圈(内圈或外圈)为对象。需要说明的是,在滚道圈被薄壁化的情况下,在t/d(t:滚道圈的有效壁厚;d:滚道圈的外径)为0.1以下的情况下特别有效。在本发明中,首先,准备要成为内圈、外圈的原材料的圆环部件。作为原材料,优选表面硬化钢,以易于通过渗碳处理、渗氮处理、碳氮共渗处理而形成表面硬化层。另外,为了使淬火性提高,也优选添加cr、mn等作为合金成分。然后,使用该圆环部件,与现有技术同样地形成表面硬化层,进行淬火、退火的热处理,制成滚道圈中间部件,然后对滚道圈中间部件的内径面和外径面进行研磨,制造滚道圈。淬火可以是1次,也可以是2次。进而,将得到的滚道圈与滚动体、保持架一同组装,制成滚动轴承。这一系列工序顺序与现有技术相同。但是,在本发明中,在淬火后对圆环部件进行急冷而制成滚道圈中间部件,然后进行回火,进行研磨。另外,在用油冷却的淬火后,可以在清洗附着于圆环部件的油时,一并进行清洗和急冷。作为急冷方法,可以将圆环部件浸渍在水或清洗液的贮槽中,不过由于液温会上升而不适于连续处理,因此优选向圆环部件吹送水、清洗液的方法。考虑到冷却能力、成本、后处理的难度等,用于进行急冷的冷却介质特别优选水,也能够兼顾清洗。作为清洗液,优选在水中加入了表面活性剂而得到的产物,也可以添加防锈剂。就形成有表面硬化层的圆环部件而言,已知会在表面产生压缩的残留应力,这依赖于碳的梯度所伴随的马氏体相变的发生顺序,伴随冷却按照从芯部到表面的顺序发生马氏体相变,由此产生残留应力。马氏体的硬度依赖于碳量,因此会产生从表面到内部与碳浓度的梯度相应的硬度分布和残留应力分布。硬度基本仅依赖于碳浓度,但残留应力依赖于马氏体相变的发生时期。于是,通过使发生马氏体相变比芯部慢的表面快速冷却,从而使表面与芯部的马氏体相变的发生时期同步,能够抑制残留应力的产生。为此,通过淬火后的急冷或者与清洗一并进行的急冷,使圆环部件的表面的冷却速度相对高于芯部的冷却速度。具体发现如下方式有效:在淬火后进行急冷,使环状部件的表面温度为50℃以下,优选为10~40℃。通过该急冷,控制滚道圈中间部件的表面的残留应力及其分布,与表面相当的加工余量、即深度方向上从50μm的深度位置到芯部的残留应力平缓至变化几乎为零的程度。更优选地,研磨加工余量内的平均残留应力的绝对值为0~191mpa,具有从表面到芯部平缓地接近0这样的深度-残留应力分布。另外,将与加工余量内相当的从50μm到250μm的深度位置的残留应力的绝对值设为100mpa以下。进一步优选将与加工余量内相当的从50μm到250μm的深度位置的残留应力的绝对值设为60mpa以下。需要说明的是,急冷时的冷却速度设为10℃/分钟以上,更优选设为15℃/分钟以上。另外,上述的滚道圈中间部件的表面的残留应力分布优选在研磨得到的最终产品即滚道圈中也维持原样。即,即使在最终得到的滚道圈中,从50μm的深度位置到芯部的残留应力变化也平缓至几乎为零的程度,研磨加工余量内的平均残留应力的绝对值为0~191mpa,具有从表面到芯部平缓地接近0这样的深度-残留应力分布,从50μm到250μm的深度位置的残留应力的绝对值优选设为100mpa以下,进一步优选设为60mpa以下。接着,在按照常规方法进行回火后,进行内径面、外径面的研磨而完成滚道圈,但由于通过如上所述淬火后的急冷、或者回火后的清洗和急冷使得滚道圈中间部件的表面的残留应力变小,因此能够抑制研磨时的圆度的下降。另外,将上述的滚道圈与滚动体、保持架一同组装,能够制成滚动轴承。圆度通常被jisb1515标准化,是一个径向平面内的外径的最大值与最小值之差,在jisb1514中,按照轴承外径、等级规定了圆度。圆度相对于滚道圈的直径的要求精度为0.01~0.03%左右,在此说明如下情况:以普通件即0级的最大值作为最低的目标值,优选的目标值为外径的0.015%以内,更优选的目标值为外径的0.01%以内。另外,研磨中的加工余量考虑就热处理品而言的表面的性状等而由jisb0711规定。而且,就本发明中作为对象的变速箱用的滚动轴承而言,外径的加工余量在直径上以0.2mm为大致目标。若圆度和加工余量确定,则能够算出在加工余量的范围内得到作为目标的圆度所要求的残留应力。部件的残留应力能够根据部件的曲率求出,本发明中以该曲率法为基础求出残留应力。即,对于由内圈、外圈的原材料即表面硬化钢形成的圆环部件,测定在形成表面硬化层、实施了进行淬火、回火的热处理后,外径和内径的尺寸变化,根据该变化量,按照基于曲率法的残留应力的定义式,根据外径、壁厚算出成为目标圆度的残留应力。将结果示于表1~3,该表按照圆环部件的外径和壁厚示出在加工余量0.2mm的范围中成为目标圆度所要求的平均残留应力。表1为将目标圆度设为jis标准的0级的最大值以内的情况,表2为将目标圆度设为外径的0.015%以内的情况下,表3为将目标圆度设为外径的0.01%以内的情况。如表1~3所示,就任一圆度而言,在相同壁厚时外径越大则残留应力越小,反之,在相同外径时壁厚越增加则残留应力越大。[表1][表2][表3]然后,根据该表,将壁厚与外径和残留应力的关系图像化,利用最小二乘法求出拟合直线,以求出其斜率和截距。表4示出将圆度设为jis机械的0级的最大值以内的情况,表5示出将圆度设为外径的0.015%以内的情况,表6示出将圆度设为外径的0.01%以内的情况。[表4][表5][表6]进而,分别将壁厚与斜率的关系、壁厚与截距的关系图像化,利用最小二乘法求出拟合直线。然后,根据得到的拟合直线和外径,得到与目标圆度以及从表面到50μm的深度的位置的残留应力相关的下述的式(1)~式(3)。需要说明的是,式中的d为滚道圈的外径,t为滚道圈的壁厚。·目标圆度:为jis的0级的最大值以内的情况,本发明中,残留应力≥(1.04×t-2.2)×d-170.8×t+425···(1)·目标圆度:为外径的0.015%以内的情况,本发明中,残留应力≥(0.90×t-2.6)×d-151.9×t+454···(2)·目标圆度:为外径的0.01%以内的情况,本发明中,残留应力≥(0.61×t-1.8)×d-104.6×t+322···(3)例如,在外径为73mm且有效壁厚为4.8mm的圆锥滚子轴承的外圈的情况下,为了将研磨后的圆度控制在jis0级的最大值以内,根据式(1),将成为外圈的滚道圈中间部件的滚道面的从50μm到250μm的深度的位置的平均残留应力设为约-191mpa以上即可。在要进一步提高圆度的情况下,根据式(2),为了使圆度成为外径的0.015%以内,将该残留应力设为-150mpa以上即可,根据式(3),为了使圆度成为外径的0.01%以内,将该残留应力设为-97mpa以上即可。需要说明的是,就基于渗碳、渗氮、碳氮共渗的表面硬化处理而言,基本上,表面的残留应力为压缩,残留应力为负值。而且,通过对像这样控制残留应力以满足式(1)~式(3)的滚道圈中间部件进行研磨加工,从而即使产生一定的椭圆变形也能够减轻由于加工余量不均匀而产生的应力,能够在滚道圈中确保作为目标的圆度。如上所述,由于滚道圈中间部件的表面性状会反映在得到的滚道圈的表面性状中,因此,例如,若使以满足式(1)的方式进行了热处理的滚道圈中间部件的平均残留应力值为-150mpa,则滚道圈的表面的残留应力成为低于-150mpa的值。需要说明的是,在评价滚道圈的残留应力的值的情况下,需要去除由研磨加工产生的残留应力,为了实现该目的,需要约50μm的电解研磨,研磨后的滚道圈的表面残留应力是指50μm深度位置的残留应力。实施例以下举出实施例进一步说明本发明,但本发明不限于此。(预备试验)准备含有0.4质量%的碳并且还添加了cr、mn等合金元素以确保在油冷下的淬火性的钢材。然后,从该钢材切下外径为75mm左右的圆环部件,进行3.5小时的碳氮共渗处理。接着,在2次加热后,在100℃左右的油中进行淬火,迅速地吹送水进行清洗和急冷,使圆环部件的表面温度为20~50℃,并进行回火,制成试验片。然后,反复进行将试验片的圆周面电解研磨至预定深度并测定该位置的残留应力的操作,求出直到加工余量附近即250μm的深度的残留应力。作为测定的结果,到250μm的深度的平均残留应力在表面温度为20℃时为-37mpa,在30℃时为-34mpa,在40℃时为-46mpa,在50℃时为-138mpa。将测定结果图像化并示于图2,圆环部件的表面温度为40℃以下时平均残留应力恒定为很小的值,为38℃以下时恒定为更小的值。即可知,通过急冷使圆环部件的表面温度为40℃以下,优选为38℃以下即可。(实施例1、实施例2、比较例1)与预备试验同样,从含有0.4质量%的碳且添加了cr、mn等合金元素的钢材切下外径73mm且壁厚4.8mm的圆锥滚子轴承的外圈用圆环部件,进行3.5小时的碳氮共渗处理。接着,在2次加热后,在100℃左右的油中进行淬火,在实施例1中在淬火后急冷至50℃,在实施例2中在淬火后急冷至室温(25℃),然后在180℃进行回火,制成试验片。另一方面,在比较例1中,在淬火后,不特地进行冷却,然后在180℃进行回火,制成试验片。对于这些试验片,对于其中一部分,反复进行将与滚道面接触的圆周面电解研磨至预定深度并测定该位置的残留应力的操作,求出深度方向的残留应力的分布。其中,测定深度设为本工件的利用研削得到的加工余量即最大250μm。表7示出各试验片的残留应力的值。[表7]深度比较例1实施例1实施例2(mm)(mpa)(mpa)(mpa)0.05-330-90-590.1-289-135-620.15-235-106-110.2-263-114-50.25-266-108-8平均值-277-111-29图3~5示出使用表7的结果用图像表示各试验片的深度方向的残留应力分布的结果。如上所述,芯部的残留应力推定基本为0,因此可知:在比较例1中残留应力朝向芯部去而明确地减少,与此相对,在实施例1、实施例2中,加工余量内即50~250μm深度的残留应力值被抑制得很低,因此残留应力朝向芯部去而平缓地减少。接着,评价各事例的研削加工导致的圆度的变化。热处理后的各试验片的圆度基本等同。对于50个各试验片,对外径侧和内径侧分别各研磨1次,测定圆度。将结果示于图6,在比较例1中圆度为3~32μm,存在很大偏差。与此相对,实施例1中任一试验片的圆度均为8μm以下,实施例2中任一试验片的圆度均为4μm以下,圆度小且整齐。就外径73mm且有效壁厚4.8mm的圆锥滚子轴承的外圈而言,根据式(1),为了使圆度成为jis0级的最大值以内,将残留应力设为-191mpa以上即可,根据式(2),为了使圆度成为外径的0.015%以内,将残留应力设为-150mpa以上即可,根据式(3),为了使圆度成为外径的0.01%以内,将残留应力设为-97mpa以上即可。在实施例1中,平均残留应力为-111mpa,满足将上述的圆度控制在外径的0.015%(=11μm)以内所需的残留应力(-150mpa以上),圆度为8μm以下,满足11μm以内。同样地,在实施例2中,平均残留应力为-29mpa,满足将上述的圆度控制在外径的0.01%(=7.3μm)以内所需的残留应力(-97mpa以上),圆度为4μm以下,满足7.3μm以内。与此相对,比较例1的平均残留应力为-277mpa,因此不满足使圆度成为jis0级的最大值以内所需的残留应力(-191mpa以上),圆度最大为32μm,不满足jis0级的圆度。像这样,根据比较例1、实施例1及实施例2,可知目标圆度与式(1)~式(3)存在相关。虽然详细地参照特定实施方式说明了本发明,但是本领域技术人员显然能够在不脱离本发明的精神与范围的前提下加入各种各样的变更、修正。本申请基于2018年4月2日申请的日本专利申请(日本特愿2018-070943)、2018年4月13日申请的日本专利申请(日本特愿2018-077598),在此引入其内容作为参照。产业上的可利用性本发明在各种滚动轴承方面可得到高圆度的滚道圈,且可得到高精度的滚动轴承。例如,可用作汽车变速箱、计算机断层扫描仪(ct扫描)等所使用的滚动轴承。当前第1页12