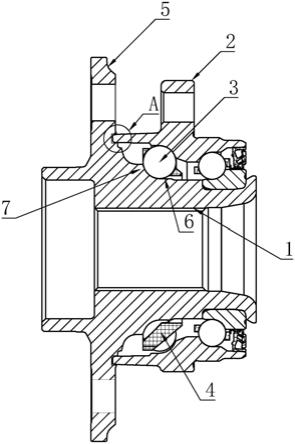
1.本实用新型涉及轴承,具体为抗冲击的轮毂轴承。
背景技术:2.轿车轮毂轴承在轿车高速通过路面凹坑或凸起时,与车轮连接的法兰内圈承受冲击力,并将冲击力传递给钢球部件,从而冲击滚道形成凹痕。冲击的典型失效是汽车轴承运转时产生了噪音或振动,影响客户驾驶体验,造成客户投诉。
3.常见的设计解决方案是增加轴承的直径或轴向尺寸或轴承的滚动体的尺寸或数量,这通常导致轴承质量和成本增加,并使轴承设计在直线运行和转弯能力方面效率降低。轴承滚道的肩高也会随着球的直径增加,在极端的侧向力情况下为钢球提供额外的滚道支撑。但是,这种方法增加了加工成本。所有传统改善措施的代价是增加了轴承质量,旋转力矩以及轴承和与轴承配合的部件的成本。
4.因此,对轿车轮毂轴承而言,除了高载荷能力、高可靠性、长寿命以及轻量化等基本要求之外,耐冲击能力、高力矩刚性的要求也越来越突出。
技术实现要素:5.针对现有技术存在的不足,本实用新型的目的在于提供一种抗冲击的轮毂轴承,能够在不增加用料成本和轴承质量的情况下提高轮毂轴承的抗冲击效果。
6.为实现上述目的,本实用新型提供了如下技术方案:限定在轴向方向的旋转部件(法兰内圈);连接车辆悬架结构(例如,转向节或车轴)的非旋转部件(法兰外圈),和一个由铆接成型的卷边夹紧的内侧小内圈以及将旋转部件联接至非旋转部件的滚动体,以实现旋转部件绕轴线相对于非旋转部件旋转。内侧的小内圈确定内侧的内部轴承滚道以及非旋转的部件确定内侧的外部轴承滚道,旋转部件确定了外侧的内部轴承滚道,非旋转部件确定了外侧的外部轴承滚道。轮毂轴承包含两列滚道,每列滚道可保持多个滚动体运转。当滚动元件是钢球时,滚道的挡边高优选为其各自钢球直径的约30%~50%。所述车轮旋转部件轴颈表面与非旋转的环形表面具有一间隙g,该间隙g的长度应小于约0.30mm。
7.作为本实用新型的进一步改进,所述法兰外圈相对法兰盘的一侧的接触面厚度为2mm~5mm。
8.作为本实用新型的进一步改进,所述法兰盘相对法兰外圈的接触面位置开设有与法兰盘同轴的环形凹槽,所述法兰外圈对应该环形凹槽的位置位于该环形凹槽内,且间隙g位于该环形凹槽的槽底与法兰外圈之间。
9.作为本实用新型的进一步改进,所述法兰外圈位于环形凹槽内的一端的外侧面与环形凹槽之间设置有密封圈,所述密封圈朝向环形凹槽槽底的一侧设置有密封唇,且该密封唇与槽底相贴合。
10.作为本实用新型的进一步改进,间隙g的长度大于等于0.13mm小于0.3mm。
11.作为本实用新型的进一步改进,两列所述滚道对应不同直径的滚子,直径较大的
滚子位于靠近法兰盘的一侧。
12.作为本实用新型的进一步改进,所述法兰外圈相对法兰盘的一端的端面还设置有多个凹槽。
13.作为本实用新型的进一步改进,所述法兰盘与法兰外圈相对应的位置为斜面配合。
14.作为本实用新型的进一步改进,所述法兰盘和法兰外圈配合的斜面由法兰盘靠向滚子方向倾斜。
15.本实用新型的有益效果,
16.1.间隙g的长度小于0.3mm,意味着法兰外圈与法兰内圈之间的距离较近,当轮毂受到冲击时,能够通过极短的行程让法兰外圈与内圈进行抵触,从而能大幅度减小传递至滚道的冲击载荷,避免滚道出现冲击布氏压痕。
17.2.当间隙g的长度为0.13mm时,滚子的肩高可以下降到滚子直径的30%,此时能够大幅减小重量和材料成本。
18.3.通过间隙设计,可以在保持高抗冲击性能同时,采用更小直径的钢球或减少钢球数量,降低材料成本及重量。
19.4.可应用于轴承尺寸受限或轴承内部空间布局受限轴承,既能或的高抗冲击性能,又不降低轴承其他性能。
20.5.由于间隙g较小,能够阻挡碎屑/水泥的进入,一些大的灰尘能够直接阻挡在外,不会损伤密封件。
附图说明
21.图1为本实用新型的其中一种实施方式剖面结构示意图;
22.图2为本实用新型的另一种实施方式剖面结构示意图;
23.图3为图1中的a部结构放大示意图;
24.图4为图2中的b部结构放大示意图;
25.图5为本实用新型平面端部实施例结构示意图;
26.图6为本实用新型斜面端部实施例结构示意图;
27.图7为本实用新型端部开槽实施例结构示意图。
28.附图标号:1、法兰内圈;2、法兰外圈;3、滚子;4、保持架;5、法兰盘;6、滚道;7、肩高;8、环形凹槽;9、密封圈;10、密封唇;11、斜面;12、凹槽。
具体实施方式
29.下面将结合附图所给出的实施例对本实用新型做进一步的详述。
30.参照图1-7所示,
31.抗冲击的轮毂轴承,包括法兰内圈1和套设在法兰内圈1上的法兰外圈2,法兰内圈1与法兰外圈2之间设置有若干滚子3和保持滚子3之间间距的保持架4,法兰内圈1的一端具有同轴的法兰盘5,另一端具有铆接成型的向法兰外圈2翘起的卷边,法兰内圈1上设置有供滚子3滚动的滚道6,滚道6具有两列,且两列滚道6对应不同直径的滚子3,直径较大的滚子3位于靠近法兰盘5的一侧;对应直径较大的滚子3的滚道6相对法兰盘5的一侧的肩高7为滚
子3直径的30%~50%;法兰外圈2与法兰盘5之间具有一间隙g,该间隙g的长度小于0.3mm。
32.基于上述方案,两列滚道6对应的滚子3尺寸不同,而且直径较大的一列滚子3靠近法兰盘5一侧,由于法兰盘5一侧是用于安装轮毂的,因此当轮毂受到冲击时,能够让直径较大的滚子3分摊冲击,配合滚道6的肩高7能够与滚子3配合进行分摊。其中,如图所示,间隙g的长度小于0.3mm,意味着法兰外圈2与法兰内圈1之间的距离较近,当轮毂受到冲击时,能够通过极短的行程让法兰外圈2与内圈进行抵触,此时实验可得对于滚道6的肩高7要求可以降低到滚子3直径的30%~50%之间,对于减小成本来说,具有极大的优势。具体的来说,当间隙g的长度为0.13mm时,滚子3的直径可以下降到滚子3直径的30%,此时能够大幅减小重量和材料成本。而对应的间隙g为0.3mm时,滚道6的肩高7为滚子3直径的50%,对于成本来说也能够保持较低的成本。并且由于间隙g较小,能够阻挡碎屑/水泥的进入,一些大的灰尘能够直接阻挡在外,不会损伤密封件。
33.另外,法兰外圈2相对法兰盘5的一侧的接触面厚度为2mm~5mm。
34.该厚度的设计意味着接触面积的减小,减小接触面积能够摩擦,减少轮毂受到冲击后继续转动带来的摩擦,进而减少损伤,减少噪声和振动的产生。
35.作为另一种实施方式,法兰盘5相对法兰外圈2的接触面位置开设有与法兰盘5同轴的环形凹槽8,法兰外圈2对应该环形凹槽8的位置位于该环形凹槽8内,且间隙g位于该环形凹槽8的槽底与法兰外圈2之间。
36.利用环形凹槽8与法兰外圈2配合,法兰外圈2进入到该环形凹槽8内,在法兰内圈1转动时会产生一定的空气流动,能够利用环形凹槽8进行防尘,能够减少灰尘的进入,并且根据环形凹槽8的尺寸大小进行选择对法兰外圈2进行定位和限位,在对法兰外圈2进行限位之后能够对振动进行优化。
37.基于上述方案的另一种实施例,法兰外圈2位于环形凹槽8内的一端的外侧面与环形凹槽8之间设置有密封圈9,密封圈9朝向环形凹槽8槽底的一侧设置有密封唇10,且该密封唇10与槽底相贴合。
38.本方案下加大了环形凹槽8的尺寸,并利用密封圈9对法兰外圈2和环形凹槽8进行密封,隔绝外部的灰尘,一来通过法兰内圈1转动时带来的空气流动来对灰尘进行扰动,减少进入轴承内部空间,二来隔离体积较大的碎屑等,并且能够利用法兰内圈1的转动来甩出灰尘。
39.上述的滚子3可以是锥形、圆柱形、球形的滚子3,或者任意两个的配合,均可以适用于本方案中。
40.更进一步,所述法兰外圈2相对法兰盘5的一端的端面还设置有多个凹槽12。
41.在法兰外圈2与法兰盘5产生碰撞时,通过凹槽12能够减小因为摩擦产生的异响。同时也能够利用凹槽12吸收一部分的噪声。该凹槽12能够是多种形状的结构,可以是若干个盲孔状的凹槽12,也可以是沿周向开设的环状的凹槽12。
42.上述的法兰盘5与法兰外圈2的配合均可以采用平面配合,当然作为另一种实施方式也可以让法兰盘5与法兰外圈2相对应的位置为斜面11配合。斜面11的配合相比平面的配合具有更大的接触面,进而能够承受更大的冲击。而且能够利用斜面11对冲击力进行分解,减小冲击力,有助于延长使用寿命。
43.具体的来说,所述法兰盘5和法兰外圈2配合的斜面11由法兰盘5靠向滚子3方向倾
斜。
44.上述的倾斜方向更加便于加工,当然本领域技术人员也可以采用相反的倾斜方向,也可以实现本方案所要实现的技术效果。
45.以上所述仅是本实用新型的优选实施方式,本实用新型的保护范围并不仅局限于上述实施例,凡属于本实用新型思路下的技术方案均属于本实用新型的保护范围。应当指出,对于本技术领域的普通技术人员来说,在不脱离本实用新型原理前提下的若干改进和润饰,这些改进和润饰也应视为本实用新型的保护范围。