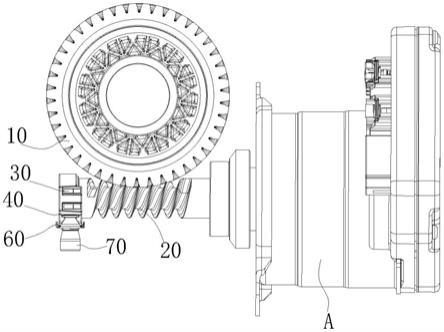
1.本实用新型涉及汽车转向系统技术领域,具体涉及一种蜗轮蜗杆间隙调整机构。
背景技术:2.目前,借助于液压或电机提供的外力辅助转向实现车辆助力转向即所谓的液压阻力或电动助力转向系统,已被广范地使用在各种车辆上,由于控制方便、响应迅捷且耗能低等特点,电动助力转向的使用范围正逐步扩大。电动助力转向系统主要是由电机驱动蜗轮蜗杆减速传动机构中的蜗杆转动,车辆正常行驶时,车轮会将路面施加的交变外力及时传递到转向节、横拉杆等部件上,而后在传递到蜗轮蜗杆减速传动机构中,相互啮合的蜗轮蜗杆的齿面会出现磨损,这种磨损将导致回转轴芯相对固定蜗轮和蜗杆的啮合齿面之间出现间隙,这种间隙的存在又给路面施加的经由转向节、横拉杆等部件传递到蜗轮蜗杆减速传动机构的交变外力提供了齿面冲击振动的机会,一方面这种冲击振动会进一步的损坏蜗轮蜗杆减速传动机构,另一方面有会产生振动噪音。同时,在设计时,不可避免的会出现蜗轮蜗杆加工偏差,壳体安装尺寸加工偏差以及装配偏差等造成蜗轮蜗杆空载转动力矩一致性较差的问题。
3.现有技术中,蜗轮蜗杆减速机构大都设有间隙调整机构,即蜗轮蜗杆啮合初始状态使用不同类型的弹簧给蜗杆施加一定的预紧力,使蜗杆顶紧蜗轮盘而消除起始啮合间隙,但因为空间结构的限制,弹簧力的大小设定,弹簧位移量的大小等都受到限制,提供的预紧力太大往往造成蜗轮蜗杆间隙过小,摩擦力过大难装配,且易磨损;而预紧力太小则不能抵制受到逆向冲击时蜗杆受到的逆向作用力,从而与蜗轮盘之间产生碰撞异响,所以整个间隙调整机构的结构设计和弹簧刚度的选择往往很难达到平衡。
技术实现要素:4.本实用新型的目的是提供一种既能保证摩擦较低,又能有效抑制蜗杆受到的逆向力的蜗轮蜗杆间隙调整机构。
5.为了实现上述目的,本实用新型采用的技术方案为:一种蜗轮蜗杆间隙调整机构,包括相互啮合的蜗轮和蜗杆,蜗杆的一端与助力电机的输出轴同轴相连,蜗杆另一端的轴承与减速器壳体之间设置有轴承衬套,轴承衬套的外壁上卡接有叶片弹簧,叶片弹簧在径向方向上的变形驱使蜗杆始终靠近蜗轮并有效啮合。
6.上述方案中,蜗轮蜗杆啮合传动时,由叶片弹簧给蜗杆提供预紧力,使蜗杆一直压向蜗轮,消除两者之间传动间隙,保证方向盘在初始转动时不会有间隙感,提升手感;同时蜗轮蜗杆磨损后,根据弹簧特性叶片弹簧再次提供弹簧力以使蜗杆靠向蜗轮,从而消除间隙,起到间隙调整作用。叶片弹簧具有更小的弹性刚度,在保证良好nvh性能的同时,有效降低蜗轮蜗杆之间的内摩擦力,保证装配容易,且大幅降低蜗轮蜗杆的磨损程度。
附图说明
7.图1为蜗轮蜗杆减速机构示意图;
8.图2为蜗轮蜗杆间隙调整机构剖面图;
9.图3为蜗轮蜗杆间隙调整机构的立体图;
10.图4为轴承衬套的立体图;
11.图5为叶片弹簧的立体图;
12.图6为调整销的立体图。
具体实施方式
13.如图1-图3所示,一种蜗轮蜗杆间隙调整机构,包括相互啮合的蜗轮10和蜗杆20,蜗杆20的一端与助力电机a的输出轴同轴相连,蜗杆20另一端的轴承30与减速器壳体50之间设置有轴承衬套40,轴承衬套40的外壁上卡接有叶片弹簧60,叶片弹簧60在径向方向上的变形驱使蜗杆20始终靠近蜗轮10并有效啮合。先将蜗杆20小端轴承30内圈压装至蜗杆20上,再将轴承衬套40压装至轴承30上,将电机端的钟摆轴承压装至蜗杆20大端处,蜗杆20总成组装完成,将组装好的蜗轮合件、蜗杆合件装入减速器壳体50中,将叶片弹簧60压入减速器壳体50待蜗杆20大端螺母装配完成,蜗轮蜗杆调整机构装配完成。蜗轮蜗杆啮合传动时,由叶片弹簧60给蜗杆20提供预紧力,使蜗杆20一直压向蜗轮10,消除两者之间传动间隙,保证方向盘在初始转动时不会有间隙感,提升手感。同时蜗轮蜗杆磨损后,根据弹簧特性叶片弹簧60再次提供弹簧力以使蜗杆20靠向蜗轮10,从而消除间隙,起到间隙调整作用。叶片弹簧60具有更小的弹性刚度,在保证良好nvh性能的同时,有效降低蜗轮蜗杆之间的内摩擦力,保证装配容易,且大幅降低蜗轮蜗杆的磨损程度。
14.参阅图4,所述的轴承衬套40整体呈环形块状,中间开设有与轴承30配合的过孔45,轴承衬套40的外壁设置有连接座41,连接座41的外平面上凸出设置有与叶片弹簧60卡接的卡接块42,叶片弹簧60的卡爪61与卡接块42构成卡接配合。轴承衬套40作为支撑抽成30的支撑座,同时也为叶片弹簧60提供卡接位置,轴承衬套40的材料选型经过高强度的耐久计算及试验验证,保证耐久后仍能有效支撑轴承30及蜗杆20。
15.减速器壳体50、叶片弹簧60上开设有通孔a,调整销70依次穿过两个通孔a后与轴承衬套40过盈压合。采用定位销70限制机构对蜗杆20的摆动进行限制,当助力电机a带动蜗杆20转动产生助力时,蜗轮蜗杆齿面之间会产生一个很大的力,这个力会让蜗轮和蜗杆产生相对分离的趋势,通常蜗轮10的固定很稳,但是带有摆动机构的蜗杆20在这个力作用下会远离蜗轮10方向摆动,为了保证蜗轮蜗杆的齿形良好啮合,就需要蜗杆20的限位机构限制蜗杆20的摆动角度(预紧弹簧的力远远不够),调整销70提供足够的反力让蜗轮蜗杆啮合并传递力矩。轴承衬套40在径向采用调整销70以限制蜗杆20在高负载下的摆动量,具体的做法是:可以通过调整销70的压入位移及深度来调整叶片弹簧60预紧力的大小,来补偿并消除磨损增加的这部分间隙,从而可以满足装调的性能,进一步消除了噪声和异响。
16.进一步的,叶片弹簧60呈扩口状的u形板,包括腹板62以及两侧的翼板63,卡爪61设置在腹板62的两侧位置处,且通孔a开设在腹板62的中间位置处,翼板63的两悬置端与连接座41的外平面相抵。由于叶片弹簧60自身的结构特性,其在径向上有一定的变形及恢复能力,能够提供足够的弹力驱动蜗杆20靠向蜗轮10。如图5所示,翼板63的两悬置端端部设
置成圆滑面,防止对轴承衬套40造成损坏。
17.轴承衬套40的外壁还包括与减速器壳体50内壁吻合的圆弧面43以及平面44,其中平面44上设有支撑块441,支撑块441凸出于平面44布置,与减速器壳体50直接接触,有效支撑蜗杆20,同时支撑块441设计为低刚度结构,能在一定范围内吸收蜗杆20摆动冲击,有效提升nvh性能。
18.如图6所示,调整销70呈圆锥状,通孔a的孔径小于调整销70的最大外径且大于调整销70的最小外径,调整销70沿其轴向开设有工艺孔71,用于与压装工具配合。通过调整销70的压入位移及深度来调整叶片弹簧60预紧力的大小,来补偿并消除磨损增加的这部分间隙,从而可以满足装调的性能,进一步消除了噪声和异响。
19.此外,通过上述调整机构的设计,在一定程度上也降低了对减速器壳体50、蜗轮10和蜗杆20等加工精度的要求,提高了生产效率,降低了生产成本,蜗杆20与助力电机a连接端采用钟摆轴承,提供蜗杆20的角度摆动,易装配且蜗杆20不会被限制死,同时摆动量不影响蜗杆20的预紧效果。
技术特征:1.一种蜗轮蜗杆间隙调整机构,包括相互啮合的蜗轮(10)和蜗杆(20),蜗杆(20)的一端与助力电机(a)的输出轴同轴相连,其特征在于:蜗杆(20)另一端的轴承(30)与减速器壳体(50)之间设置有轴承衬套(40),轴承衬套(40)的外壁上卡接有叶片弹簧(60),叶片弹簧(60)在径向方向上的变形驱使蜗杆(20)始终靠近蜗轮(10)有效啮合。2.根据权利要求1所述的蜗轮蜗杆间隙调整机构,其特征在于:所述的轴承衬套(40)整体呈环形块状,中间开设有与轴承(30)配合的过孔(45),轴承衬套(40)的外壁设置有连接座(41),连接座(41)的外平面上凸出设置有与叶片弹簧(60)卡接的卡接块(42),叶片弹簧(60)的卡爪(61)与卡接块(42)构成卡接配合。3.根据权利要求1所述的蜗轮蜗杆间隙调整机构,其特征在于:减速器壳体(50)、叶片弹簧(60)上开设有通孔(a),调整销(70)依次穿过两个通孔(a)后与轴承衬套(40)过盈压合。4.根据权利要求2所述的蜗轮蜗杆间隙调整机构,其特征在于:叶片弹簧(60)呈扩口状的u形板,包括腹板(62)以及两侧的翼板(63),卡爪(61)设置在腹板(62)的两侧位置处,且通孔(a)开设在腹板(62)的中间位置处,翼板(63)的两悬置端与连接座(41)的外平面相抵。5.根据权利要求2所述的蜗轮蜗杆间隙调整机构,其特征在于:轴承衬套(40)的外壁还包括与减速器壳体(50)内壁吻合的圆弧面(43)以及平面(44),其中平面(44)设有支撑块(441),支撑块(441)凸出于平面(44)表面,支撑块与减速器壳体(50)抵靠。6.根据权利要求3所述的蜗轮蜗杆间隙调整机构,其特征在于:调整销(70)呈圆锥状,通孔(a)的孔径小于调整销(70)的最大外径且大于调整销(70)的最小外径,调整销(70)沿其轴向开设有工艺孔(71)。
技术总结本实用新型的目的是提供一种既能保证摩擦较低,又能有效抑制蜗杆受到的逆向力的蜗轮蜗杆间隙调整机构,蜗轮蜗杆啮合传动时,由叶片弹簧给蜗杆提供预紧力,使蜗杆一直压向蜗轮,消除两者之间传动间隙,保证方向盘在初始转动时不会有间隙感,提升手感;同时蜗轮蜗杆磨损后,根据弹簧特性叶片弹簧再次提供弹簧力以使蜗杆靠向蜗轮,从而消除间隙,起到间隙调整作用。叶片弹簧具有更小的弹性刚度,在保证良好NVH性能的同时,有效降低蜗轮蜗杆之间的内摩擦力,保证装配容易,且大幅降低蜗轮蜗杆的磨损程度。的磨损程度。的磨损程度。
技术研发人员:李彩霞 陶薛磊 吴罡 孙国军
受保护的技术使用者:奇瑞汽车股份有限公司
技术研发日:2021.09.18
技术公布日:2022/3/16