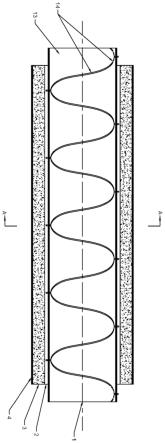
1.本发明涉及保温管道减阻技术领域,特别是涉及一种螺旋焊缝余高打磨的减阻性保温管道及其减阻方法。
背景技术:2.伴随着城镇化的不断推入,供热需求的迅猛增加也对集中供热管网的供热能力提出了更高的要求,供热距离越来越远,保温管道内径越来越大已经成为了主流趋势。保温管道可选用无缝管道和螺旋焊缝钢管。其中,无缝管道由于表面光滑阻力小,输送能耗低的优点,但同时其造价成本高,随着管径的增加制造工艺和成本也快速升高,而螺旋焊缝管在制造成本上具有明显优势,但管道阻力较大,输送泵功能耗较高。因此,降低管道制造成本的同时减小管道阻力对于热力管道的制造和运行具有重要意义。
3.为了减小管道的流动阻力,其关键在于降低表面阻力系数。采用表面涂层技术是当前的一种新思路,但由于制造工艺等问题,容易出现涂层剥落现象导致其存在堵塞热力站换热器的风险,因此表面涂层技术不满足热力管道应用的要求。此外,改善表面特征,减小阻力系数的同时,保证管道的原有机械强度特征也是技术实现广泛应用的必要条件。在管道连接的工艺中,存在一种通过双面打磨焊缝余高的工艺,该工艺可以保证管道强度要求的前提下达到接口对接的目的,但该技术解决的是接口焊接的难题,并不涉及管道减阻的问题,因此其仅对接口处的焊缝进行了处理。同时,该工艺方法是通过双面打磨焊缝余高以保证机械强度不低于原有值,对于保温管道而言,双面打磨焊缝余高的工艺成本仍然过高。因此,如何进一步降低焊缝余高打磨成本的同时保证管道的机械强度特征是焊缝余高打磨减阻工艺亟待解决的难题。
技术实现要素:4.为了解决上述问题,本发明提供了一种螺旋焊缝余高打磨的减阻性保温管道及其减阻方法。
5.本发明所采用的技术方案是:
6.第一方面,本发明提供了一种螺旋焊缝余高打磨的减阻性保温管道,其包括螺旋焊缝钢管、外防腐层、保温层以及外防护层;螺旋焊缝钢管分为主管段与接口段,主管段和接口段外壁面涂覆外防腐层;主管段依次同轴紧密敷设有保温层和外防护层;螺旋焊缝钢管由光滑钢卷板通过焊缝焊接连接,且焊缝在焊接过程中在外侧和内侧分别存在焊缝余高,其中位于主管段上的第一内焊缝余高经过打磨处理,而位于主管段上的第一外焊缝余高未经打磨处理,位于接口段上的第二内焊缝余高与第二外焊缝余高均经过打磨处理。
7.作为优选,所述的螺旋焊缝钢管采用螺旋焊缝钢管,管径范围为600~1600mm,单管长度为10~12m,材质包括但不限于q235a、q235b、q345金属管材。
8.作为优选,所述主管段上的第一内焊缝余高经过打磨处理后,其余高高度应小于1.0mm或为原焊缝余高的0.5倍以下,但应高于0.2mm。
9.作为优选,所述接口段上的第二内焊缝余高和第二外焊缝余高经过打磨处理后,其余高高度应小于0.2mm且不伤及原表面。
10.作为优选,所述的光滑钢卷板板宽范围为0.4m~2.5m。
11.第二方面,本发明提供了一种根据上述第一方面所述的螺旋焊缝余高打磨的减阻性保温管道的减阻方法,其具体为:将螺旋焊缝钢管作为保温管道的工作管,且主管段管外经防腐、保温和外防护工艺后依次形成外防腐层、保温层以及外防护层,最终得到输送热水工质的保温管道;其中,对两段主管段之间的接口段上的第二内焊缝余高和第二外焊缝余高均需事先进行打磨,在不伤及原表面的情况下降内外焊缝余高打磨至高度小于0.2mm,保证其抗拉强度不低于打磨前的同时,保证了接口的焊接工艺;同时,对位于主管段上的第一内焊缝余高也需事先进行打磨处理使内焊缝余高降低到原有高度的0.5倍以下或1mm以下,但又高于0.2mm,以保证焊缝处抗拉强度不小于打磨处理前抗拉强度的同时减小管内当量粗糙度降低管道阻力系数,从而达到降低热水在管内输送的泵功损失,加强螺旋焊缝钢管焊缝处强度特征的效果。
12.与现有技术相比,本发明的特色与创新在于:
13.1.本发明提出通过对整个螺旋焊缝钢管的焊缝余高进行打磨,进而有效降低管道整体的表面粗糙特征,减小管道阻力。
14.2.本发明针对保温管道的减阻要求和制造成本问题,提出螺旋焊缝钢管主管段仅进行内焊缝打磨,且提出满足不低于原管道机械强度特征要求的打磨余高范围,既保证了减阻的效果和强度要求,又降低了成本。
15.3.本发明针对接口段和主管段的不同要求,提出了不同的打磨工艺和参数要求,兼顾了成本和技术的可行性。
附图说明
16.图1为螺旋焊缝余高打磨的减阻性保温管道结构示意图。
17.图2为图1a-a截面的断面图。
18.图3为螺旋焊缝钢管结构示意图。
19.图4为不同焊缝余高处理管壁施力后位移变化图。
20.图5为不同焊缝余高处理管壁施力后断裂位置图,从上到下依次为双面打磨、双缝不打磨、内焊缝打磨、外焊缝打磨。
21.图6为螺旋焊缝钢管打磨前后长输管网总压降损失对比图。
22.图中:螺旋焊缝钢管1、外防腐层2、保温层3、外防护层4、主管段11、接口段12、光滑钢卷板13、焊缝14、第一内焊缝余高111、第一外焊缝余高112、第二内焊缝余高121、第二外焊缝余高122。
具体实施方式
23.下面结合附图和具体实施方式对本发明做进一步阐述和说明。
24.如图1、图2和图3所示,为本发明提供了一种螺旋焊缝余高打磨的减阻性保温管道,其包括螺旋焊缝钢管1、外防腐层2、保温层3以及外防护层4;螺旋焊缝钢管1分为主管段11与接口段12,接口段12位于相邻两段主管段11之间。主管段11外壁面涂覆外防腐层2,并
依次同轴紧密敷设有保温层3和外防护层4,接口段12不做防腐、保温和外防护处理。螺旋焊缝钢管1由光滑钢卷板13通过焊缝14焊接连接,且焊缝14在焊接过程中在外侧和内侧分别存在焊缝余高。为了便于描述,将位于主管段11处的内焊缝余高和外焊缝余高分别记为第一内焊缝余高111和第一外焊缝余高112,将位于接口段12处的内焊缝余高和外焊缝余高分别记为第二内焊缝余高121与第二外焊缝余高122。其中主管段11处的第一内焊缝余高111经过打磨处理,而第一外焊缝余高112未经打磨处理,接口段12处的第二内焊缝余高121与第二外焊缝余高122均经过打磨处理。在该减阻性保温管道中,螺旋焊缝钢管1可采用螺旋焊缝钢管,管径范围为600~1600mm,单管长度为10~12m,材质包括但不限于q235a、q235b、q345金属管材。光滑钢卷板13板宽范围为0.4m~2.5m。
25.在该减阻性保温管道中,主管段11处的第一内焊缝余高111经过打磨处理后,其余高高度应当进行合理的优化设计,兼顾减阻效果和加工工艺可靠性。优选的,第一内焊缝余高111经过打磨处理后的余高高度应小于1.0mm或为原焊缝余高的0.5倍以下,但应高于0.2mm。其中,第一内焊缝余高111余高高度打磨至小于1.0mm或为原焊缝余高的0.5倍以下的目的是降低管内当量粗糙度低,进而降低阻力系数和低热水在管内输送的泵功损失。第一内焊缝余高111余高高度高于0.2mm的目的是为了保证管道强度不受影响同时防止在打磨焊缝余高过程对保温管道内壁造成破坏。由于主管段11处的第二外焊缝余高112并不会影响管道内的阻力,因此无需进行打磨,保留原始的余高高度即可。
26.进一步的,在该减阻性保温管道中,接口段12处的第二内焊缝余高121和第二外焊缝余高122经过打磨处理后,其余高高度应保证管道的安装,同时防止在打磨焊缝余高过程对保温管道外壁造成破坏。优选的,第二内焊缝余高121和第二外焊缝余高122经过打磨处理后的余高高度应小于0.2mm且不伤及原表面。
27.进一步的,本发明还提供了一种基于上述螺旋焊缝余高打磨的减阻性保温管道的减阻方法,其做法为:将螺旋焊缝钢管1作为保温管道的工作管,且主管段11管外经防腐、保温和外防护工艺后依次形成外防腐层2、保温层3以及外防护层4,最终得到输送热水工质的保温管道;其中,对两段主管段11之间的接口段12上的第二内焊缝余高121和第二外焊缝余高122均需事先进行打磨,在不伤及原表面的情况下降内外焊缝余高打磨至高度小于0.2mm,保证其抗拉强度不低于打磨前的同时,保证了接口的焊接工艺;同时,对位于主管段11上的第一内焊缝余高111也需事先进行打磨处理使内焊缝余高降低到原有高度的0.5倍以下或1mm以下,但又高于0.2mm,以保证焊缝处抗拉强度不小于打磨处理前抗拉强度的同时减小管内当量粗糙度降低管道阻力系数,从而达到降低热水在管内输送的泵功损失,加强螺旋焊缝钢管焊缝处强度特征的效果。
28.需说明的是,上述对内外焊缝余高的打磨工序,可在对管道进行防腐、保温和外防护工艺之前进行。
29.为了展示上述螺旋焊缝余高打磨的减阻性保温管道的实际减阻效果,下面进一步通过以下实施案例对其进行阐述。
30.在一实施案例中,某长输管网工程包括长输管网和市内一次管网两部分,其中长输管网管径为1400mm,全长约36500m。长输管网供热介质为热水,设计流量13164t/h,设计温度125/35.5℃,设计压力2.5mpa。长输管网的所用螺旋焊缝钢管壁厚10mm,板宽2m。对管网中的主管段11和接口段12分别进行打磨。主管段11中,打磨前内焊缝余高为1.78mm,打磨
后内焊缝余高为0.63mm,打磨前后内焊缝宽度均为15.99mm,外焊缝余高无需打磨。而接口段12中,内外焊缝余高均进行打磨使其高度小于0.2mm,但不能伤及管道的原表面。
31.经过上述打磨处理后,按照《焊接接头拉伸试验方法》gb/t 2651-2008对不同焊缝结构件进行抗拉强度测试,以验证打磨处理对焊缝强度的影响。试样尺寸按照板及管板状试样的相关规定进行取样,具体尺寸为12mm钢板,材质为q235b,尺寸均为8cm
×
8cm,边长误差在1cm以内,试样边缘打磨去毛刺,带焊缝的试样其焊缝位置在中心
±
0.5cm范围内。为了进行对比,保持试样的接口段打磨方式不变,对试样的主管段做四种不同的焊缝余高处理:双缝不打磨(即内外双侧焊缝均不打磨)、双面打磨(即内外双侧焊缝均打磨)、内焊缝打磨(即仅打磨内焊缝)、外焊缝打磨(即仅打磨外焊缝)。未打磨内焊缝余高为1.78mm,打磨后内焊缝余高为0.63mm,打磨前后内焊缝宽度均为15.99mm,每种试样各2件。对四种试样逐渐连续加载并确定试验结果。表1为螺旋焊缝钢管不同打磨方式下的抗拉强度。四种不同焊缝余高处理的试样焊接接头处的抗拉强度均符合《低压流体输送用焊接钢管》gb/t 3091-2015中对钢管力学性能的要求,其中双缝不打磨的试样抗拉强度最低,为405mpa,焊缝余高打磨后试样抗拉强度有不同程度的提升,外焊缝打磨和内焊缝打磨的试样抗拉强度分别为428mpa和445mpa,双面打磨的试样抗拉强度最高,为457mpa。图4为不同焊缝余高处理管壁施力后位移变化图,图5为不同焊缝余高处理管壁施力后断裂位置图。
32.表1螺旋焊缝钢管不同打磨方式下的抗拉强度
[0033][0034]
进一步,基于上述信息对螺旋焊缝钢管打磨前后长输管网的总压降损失进行对比计算。具体而言,计算过程包括六个步骤:第一步、判断流态:假定未打磨螺旋焊缝钢管管内当量粗糙度k1为0.5mm,按照公式(2)分别计算re、re1和re2,当re1≤re≤re2时,流态处于混合摩擦区;当re>re2,流态处于阻力平方区。第二步、λ计算阻力系数:流态处于混合摩擦区时,λ采用公式(3a)计算;流态处于阻力平方区时,λ采用公式(3b)计算。第三步、计算未打磨螺旋焊缝钢管直管压降损失和总压降损失:直管压降损失采用公式(1)计算,总压降损失采用公式(7)计算。第四步、采用公式(4)计算打磨后螺旋焊缝钢管管内当量粗糙度k2。第五步、采用公式(5)计算修正系数m。第六步、计算打磨后螺旋焊缝钢管直管压降损失和总压降损失:直管压降损失采用公式(6)计算,总压降损失采用公式(7)计算,且局部压降损失为未打磨螺旋焊缝钢管直管压降损失的0.15倍。
[0035][0036][0037][0038][0039][0040][0041]
δp
f,after
=mδp
f,before
ꢀꢀꢀꢀꢀꢀꢀꢀꢀꢀꢀꢀꢀꢀꢀꢀꢀꢀꢀꢀꢀꢀꢀ
(6)
[0042]
δp
p
=δpf+δp
t
=δpf+0.15δpfꢀꢀꢀꢀꢀꢀꢀꢀꢀꢀꢀꢀꢀꢀꢀꢀꢀꢀꢀꢀ
(7)
[0043]
式中:
△
p
p
、
△
pf、
△
p
t
分别为总压降损失、直管压降损失和局部压降损失,kpa;l为管道长度,m;d为管道内径,m;λ为阻力系数,无量纲;k为管内当量粗糙度,mm;re为雷诺数,无量纲;u为供热介质流速,m/s;ρ为供热介质密度,kg/m3;μ为供热介质动力粘度,pa
·
s。
[0044]
按照上述算法计算案例中螺旋焊缝钢管打磨前后长输管网的总压降损失可得:未打磨前螺旋焊缝钢管内焊缝余高为1.78mm,当量粗糙度k1为0.5mm,阻力系数为0.01529,直管压降损失为1121.16kpa,总压降损失为1289.33kpa。打磨后螺旋焊缝钢管内焊缝余高为0.63mm,当量粗糙度k2为0.177mm,修正系数m为0.7713,阻力系数为0.01203,直管压降损失为864.76kpa,总压降损失为1032.93kpa,总压降损失减小率为19.89%。对比结果如图6所示。
[0045]
以上所述的实施例只是本发明的一种较佳的方案,然其并非用以限制本发明。有关技术领域的普通技术人员,在不脱离本发明的精神和范围的情况下,还可以做出各种变化和变型。因此凡采取等同替换或等效变换的方式所获得的技术方案,均落在本发明的保护范围内。