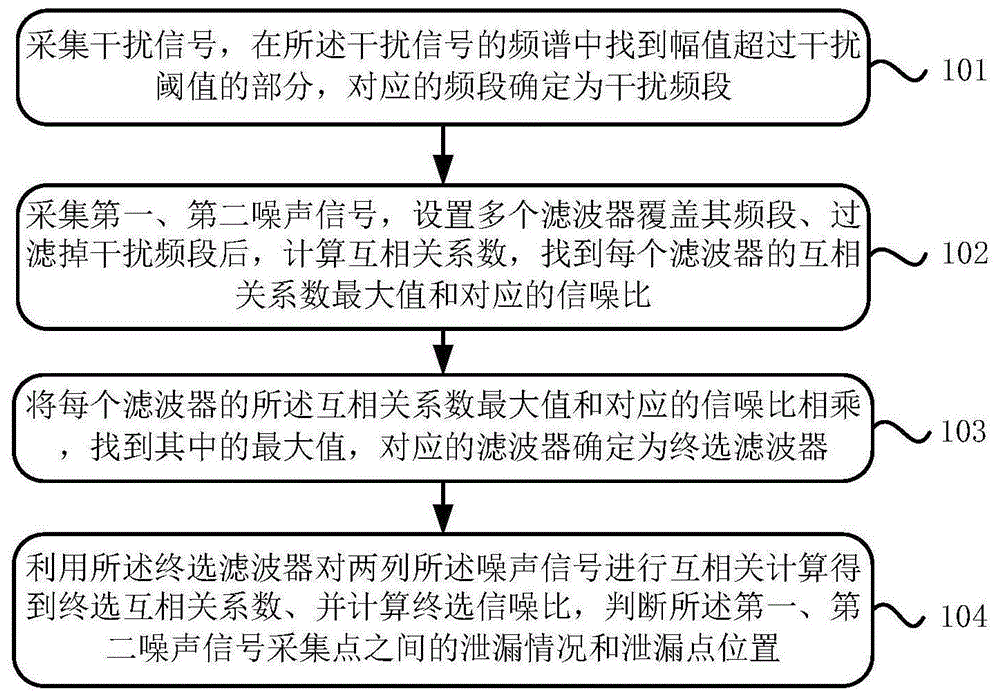
本发明涉及燃气管线检测
技术领域:
,尤其涉及一种燃气管线泄漏点定位方法和系统。
背景技术:
:燃气管线泄漏引发的爆炸等事故时有发生,严重危害公共安全,燃气管网安全尤为重要。燃气管线泄漏检测和泄漏点定位是管线日常运行维护的重要工作。目前使用的检漏方法多种多样,各有利弊,地面气体探测法虽然结果直观准确,但探测成功率较低,探测速度慢;示踪气体探测效果稍好,但是气体注入困难,对气体热值影响较大,且探测时地面需开孔;防腐层破损探测法只适用于防腐层发生破裂的泄漏点,探测速度也非常慢。因此急需一种操作方便、结果准确可靠、成本低廉的泄漏点定位方法和装置,解决燃气管网泄漏定位难的问题。技术实现要素:本发明提供一种燃气管线泄漏点定位方法和系统,解决现有方法和系统探测可靠性差、探测速度慢、成本高的问题。为解决上述问题,本发明具体是这样实现的:第一方面,本发明实施例指出一种燃气管线泄漏点定位方法,包含以下步骤:采集干扰信号,在所述干扰信号的频谱中找到幅值超过干扰阈值的部分,对应的频段确定为干扰频段;采集第一、第二噪声信号,对每列所述噪声信号设置多个滤波器覆盖其频段、过滤掉所述干扰频段后,对每个滤波器计算两列噪声信号的互相关系数,找到每个滤波器的互相关系数最大值和对应的信噪比;将每个滤波器的所述互相关系数最大值和对应的信噪比相乘,找到其中的最大值,对应的滤波器确定为终选滤波器;利用所述终选滤波器对两列所述噪声信号进行互相关计算得到终选互相关系数、并计算终选信噪比,判断所述第一、第二噪声信号采集点之间的泄漏情况和泄漏点位置:当所述终选信噪比大于设定信噪比阈值时,存在泄漏,否则,不存在泄漏;当存在泄漏时,由所述终选互相关系数中的最大值确定传播时间差,并计算得到泄漏点位置:其中,l为所述泄漏点位置与所述第二噪声信号采集点之间的距离,d为所述两列噪声信号的采集点之间的距离,v为噪声信号在所述燃气管线中的传播速度,td为所述传播时间差。进一步地,根据所述第一、第二噪声信号的同步误差计算定位误差为:其中,△l为所述定位误差,△td为所述同步误差,v为噪声信号在所述燃气管线中的传播速度。进一步地,所述第一、第二噪声信号的频段为500-5000hz,每个所述滤波器中心频率的间隔为100hz、带宽为不小于300hz。优选地,所述干扰阈值为所述干扰信号的频谱幅值最大值的优选地,所述设定信噪比阈值为6优选地,所述第一、第二噪声信号、干扰信号均需满足:每组数据包含5000个点,每个点为24bit二进制数据,数据传输速率不小于100kb/s,采用crc校验。优选地,所述噪声信号在燃气管线中的传播速度与燃气管线材质和管径相关。第二方面,本发明实施例还指出一种燃气管线泄漏点定位系统,使用所述的方法,包含:第一~第三传感器、第一~第三控制模块、主控模块;所述第一、第二传感器,放置在燃气管线两端、吸附在管壁外侧,用于采集和传输第一、第二噪声信号;所述第三传感器,放置在干扰源处,用于采集和传输干扰信号;所述第一、第二、第三控制模块,用于,接收所述主控机工作指令,并向对应的所述第一、第二、第三传感器发送开始或停止采集指令;从对应的第一、第二、第三传感器接收采集数据并上传至所述主控模块;所述主控模块,用于,向所述第一、第二、第三传感器发送开始或停止工作指令;在所述干扰信号的频谱中找到幅值超过干扰阈值的部分对应的频段,确定干扰频段;对每列所述噪声信号设置多个滤波器覆盖其频段、过滤掉所述干扰频段后,对每个滤波器计算两列噪声信号的互相关系数,找到每个滤波器的互相关系数最大值和对应的信噪比,将每个滤波器的所述互相关系数最大值和对应的信噪比相乘,找到其中的最大值,对应的滤波器确定为终选滤波器;利用所述终选滤波器对两列所述噪声信号进行互相关计算得到终选互相关系数、并计算终选信噪比,判断所述第一、第二噪声信号采集点之间的泄漏情况和泄漏点位置。优选地,所述第一、第二、第三传感器采用压电陶瓷加速度传感器。优选地,所述第一、第二传感器最大有效距离为400米。本发明有益效果包括:本发明立足于城市地下燃气管线日常的泄漏检测工作面临的难题,提出了泄漏点定位方法,该方法能够准确判断每一条管段是否发生泄漏,并精确定位泄漏点的位置,同时提出了相应的软硬件装置,能够应用到燃气公司日常运维工作之中,为开挖修复提供可靠的技术支撑。该方法在现场检测时操作简单,对市政安全影响小,仅需两人即可操作,大大节省人力成本。该方法基于声学原理,不改变管线内外运行状况,不影响管线正常运行和用户的使用。该方法判断是否泄漏成功率达到85%,泄漏点定位精度达到1米以内,一次测量覆盖的最大距离可以达到400米,能够有效避免城市道路误开挖,最大限度减少马路拉链的形成,大大节省开挖和恢复路面产生的人力物力成本,同时减少对城市道路通行的影响,提高市民满意度。提出的检测装置研发和制造成本较低,有利于推广普及;同时重量较轻,便于携带;操作简单,容易上手。该方法和装置将会在各大燃气公司得到有效的推广应用。附图说明此处所说明的附图用来提供对本发明的进一步理解,构成本发明的一部分,本发明的示意性实施例及其说明用于解释本发明,并不构成对本发明的不当限定。在附图中:图1为一种燃气管线泄漏点定位方法流程实施例;图2为燃气管线泄漏检测技术实施例;图3为一种燃气管线泄漏点定位系统实施例。具体实施方式为使本发明的目的、技术方案和优点更加清楚,下面将结合本发明具体实施例及相应的附图对本发明技术方案进行清楚、完整地描述。显然,所描述的实施例仅是本发明一部分实施例,而不是全部的实施例。基于本发明中的实施例,本领域普通技术人员在没有做出创造性劳动前提下所获得的所有其他实施例,都属于本发明保护的范围。本发明的创新点为:第一,本发明基于声学原理判断是否泄漏,不改变管线内外运行状况,不影响管线正常运行和用户的使用,且判断成功率高;第二,本发明通过测量干扰信号,能够排除干扰信号影响,判断结果准确可靠。以下结合附图,详细说明本发明各实施例提供的技术方案。图1为一种燃气管线泄漏点定位方法流程实施例,可用于检测燃气管线泄漏点位置,不改变管线内外运行状况,不影响管线正常运行和用户的使用,一种燃气管线泄漏点定位方法,包含以下步骤:步骤101,采集干扰信号,在所述干扰信号的频谱中找到幅值超过干扰阈值的部分,对应的频段确定为干扰频段。在步骤101中,处理干扰信号,提取干扰频率,具体地:将干扰信号利用快速傅里叶变换转换到频域,在频谱中找到幅值超过干扰阈值的频段,作为干扰频段。在步骤101中,需要说明的是,所述干扰阈值为所述干扰信号频谱幅值最大值的所述干扰阈值也可以是其他数值,这里不做特别限定。步骤102,采集第一、第二噪声信号,对每列所述噪声信号设置多个滤波器覆盖其频段、过滤掉所述干扰频段后,对每个滤波器计算两列噪声信号的互相关系数,找到每个滤波器的互相关系数最大值和对应的信噪比。在步骤102中,通过第一传感器采集所述第一噪声信号,通过第二传感器采集所述第二噪声信号,所述第一、第二传感器放置在燃气管线两端,泄漏点在所述第一、第二传感器的位置之间。在步骤102中,互相关系数的计算方法为:其中,rxy(τ)、ryx(-τ)为所述互相关函数的两种表示方式,τ为时间变量,t为所述第一、第二噪声信号的采集时间,x(t)、y(t)分别为所述第一噪声信号、第二噪声信号。在步骤102中,信噪比的计算方法为:其中,snr为信噪比,rxy(τ)为所述互相关函数,max(rxy(τ))为所述互相关函数的最大值,avg(rxy(τ))为所述互相关函数的平均值。在步骤102中,将两列噪声信号变换到频域,利用带通滤波器过滤掉噪声信号的干扰频段。根据实验确定了燃气泄漏噪声覆盖的频段为500-5000hz,因此遍历该频段,使用带通滤波器处理去除干扰后的噪声信号,遍历步长为100hz,遍历频段上下限频率差不小于300hz,记录每个带通滤波器的互相关系数的最大值,并计算对应的信噪比。在步骤101和步骤102中,采集数据回传应保证一定的传输速率,并保证通信的稳定性和数据的完整性。噪声采集到的每组数据包含5000个点,每个点24bit二进制数据,数据量达到117kb,为保证数据及时回传到主机,一般应保证通信模块数据传输速率达到100kb/s。数据传输采用crc校验,保证数据正确性,如校验未通过应重新传输,即包含重传机制。步骤103,将每个滤波器的所述互相关系数最大值和对应的信噪比相乘,找到其中的最大值,对应的滤波器确定为终选滤波器。在步骤103中,对于每一个带通滤波器的互相关系数最大值,将其与信噪比做乘积,取乘积最大一个频段,作为最终的带通滤波器。步骤104,利用所述终选滤波器对两列所述噪声信号进行互相关计算得到终选互相关系数、并计算终选信噪比,判断所述第一、第二噪声信号采集点之间的泄漏情况和泄漏点位置:当所述终选信噪比大于设定信噪比阈值时,存在泄漏,否则,不存在泄漏;当存在泄漏时,由所述终选互相关系数中的最大值确定传播时间差,并计算得到泄漏点位置:其中,l为所述泄漏点位置与所述第二噪声信号采集点之间的距离,d为所述两列噪声信号的采集点之间的距离,v为噪声信号在所述燃气管线中的传播速度,td为所述传播时间差。在步骤104中,可通过硬件指标来缩小传输误差,根据所述第一、第二噪声信号的同步误差计算定位误差为:其中,△l为所述定位误差,△td为所述同步误差,v为噪声信号在所述燃气管线中的传播速度。在步骤104中,传感器采集的量包含管线噪声信号和周围环境干扰信号。管线噪声信号的监测需要把传感器吸附在管壁外侧,一般是放置在地下管井中,利用两个相同的传感器监测一段管线两端的信号。由于定位原理基于两列信号的时延差,所以两列信号需要同步采集。对于实际装置,通信模块的延时不可避免,需考虑由此产生的误差,并对通信模块的延时进行控制。通信模块延时对定位产生的误差为其中v是噪声在管道中传播速度,对于金属材质一般是1200m/s左右;△td是传感器同步误差,△l是定位结果误差。当传感器同步误差是500微秒时,给最终定位结果产生的大约是30cm左右,属于可接受范围,同时500微秒的时间同步误差是可实现的。需要说明的是,时间同步误差的来源由单片机、采集电路、通信模块带来的延迟这几部分组成,应分别测试和控制,最后叠加起来应满足指标要求。在步骤104中,所述设定信噪比阈值为6,需要说明的是,所述设定信噪比阈值还可以是其他数值,这里不做特别限定。在步骤104中,利用最终的带通滤波器,对两列噪声信号进行互相关计算,如信噪比大于6,则可判定存在泄漏,在互相关系数图谱上选取互相关系数最大的点,对应信号传播时间差td,利用td计算泄漏点与两个传感器的距离,如信噪比小于6,则可判定未泄露。在步骤104中,所述噪声信号在燃气管线中的传播速度与燃气管线材质和管径相关,即泄漏噪声在管线中的传播速度与材质和管径有关,利用示波器测量了不同条件下的声速,共13种材质,对应不同的管径范围,具体数值如下表1所示。表1不同管材、管径下的声速表(1)球铁直径下限直径上限声速09913201001991250200299119030039911604005991130600799108080099910601000-1030(2)铸铁直径下限直径上限声速099128010019912202002991160300399113040049911005006991080700-1030(3)钢直径下限直径上限声速0191400209913001001991200200299112030049910405006991020700899970900-900(4)铜(5)铅直径下限直径上限声速019120020-1150(6)水泥直径下限直径上限声速09911001001991000200349960350499960500699910700899900900-880(7)pvc直径下限直径上限声速01765018226302327600284954050745207599480100199460200-440(8)hdpe直径下限直径上限声速0173601822330237430075199300200-300(9)mdpe(10)玻璃钢直径下限直径上限声速049130050991280100199121020039911804007991160800119911501200199911502000-1140(11)混凝土直径下限直径上限声速0499116050069911007008991030900119910201200179910101800--1000(12)粘土直径下限直径上限声速099110010019911002003491100350499110050069911007008991100900-1100(13)ldpe直径下限直径上限声速0173101822290237423075230需要说明的是,所述燃气管线的材质和管径不限于上表1,还可以是其他材质和管径,这里不做特别限定。在本发明实施例中,燃气管线泄漏点定位方法包含前端信号采集、信号回传主机和信号分析处理三个部分。其中信号分析处理又分为干扰信号频段解析、干扰信号排除、以及最关键的带通滤波器选择和定位结果判断等步骤。该方法只有前端信号采集需要人为操作,其他步骤可通过软件算法实现自动计算。本发明实施例公开了一种燃气管线泄漏点定位方法,该方法采用燃气管线泄漏噪声信号精确提取技术来采集噪声信号和干扰信号,能够通过采集干扰信号排除单一干扰源的干扰,进而排除周围主要干扰,该方法投入成本低,操作方便,泄漏判断结果准确可靠,泄漏点定位精度达到1米以内,有效距离达到400米。图2为燃气管线泄漏技术实施例,详细介绍了泄露定位技术,具体地:当存在泄漏时,由所述终选互相关系数中的最大值确定传播时间差,并计算得到泄漏点位置:其中,l为所述泄漏点位置与所述第二噪声信号采集之间的距离,d为所述两列噪声信号的采集点之间的距离,v为噪声信号在所述燃气管线中的传播速度,td为所述传播时间差。其技术原理是,当管道发生泄漏时,能够产生比未泄露情况下管线内噪声频率高很多的声压波沿管道传播。利用振动传感器对管线中的噪声声音信号进行监测。通过放置在管道两端(泄漏点包围在中间)的振动传感器测量泄漏信号,泄漏噪声信号传播到达两个传感器的时间不同。利用两列信号的互相关分析,即可确定泄漏噪声到达两个传感器的时间差td。根据该时间差,通过两个传感器间的距离和声波在该管材中的传播速度,即可计算出泄漏点距两个传感器的距离。其中,通过监测周围噪声源的信号,来排除干扰频段的影响。本发明实施例论述了利用传感器时间差计算泄漏点位置的技术原理,实现简单、计算量小。图3为一种燃气管线泄漏点定位系统实施例,可使用本发明中所述燃气管线泄漏点定位方法,作为本发明实施例,一种燃气管线泄漏点定位系统,包含:第一传感器1、第二传感器2、第三传感器3、第一控制模块4、第二控制模块5、第三控制模块6、主控模块7。所述第一、第二传感器,放置在燃气管线两端、吸附在管壁外侧,用于采集和传输第一、第二噪声信号;所述第三传感器,放置在干扰源处,用于采集和传输干扰信号;所述第一、第二、第三控制模块,用于,接收所述主控机工作指令,并向对应的所述第一、第二、第三传感器发送开始或停止采集指令;从对应的第一、第二、第三传感器接收采集数据并上传至所述主控模块;所述主控模块,用于,向所述第一、第二、第三传感器发送开始或停止工作指令;在所述干扰信号的频谱中找到幅值超过干扰阈值的部分对应的频段,确定干扰频段;对每列所述噪声信号设置多个滤波器覆盖其频段、过滤掉所述干扰频段后,对每个滤波器计算两列噪声信号的互相关系数,找到每个滤波器的互相关系数最大值和对应的信噪比,将每个滤波器的所述互相关系数最大值和对应的信噪比相乘,找到其中的最大值,对应的滤波器确定为终选滤波器;利用所述终选滤波器对两列所述噪声信号进行互相关计算得到终选互相关系数、并计算终选信噪比,判断所述第一、第二噪声信号采集点之间的泄漏情况和泄漏点位置。在本发明实施例中,周围环境干扰信号的采集利用第三个传感器同时监测,即噪声采集部分包含3个传感器。干扰信号的采集应直接在干扰源本体上进行,以获得较好的采集效果,不与泄漏噪声混淆。在本发明实施例中,所述第一、第二、第三传感器采用压电陶瓷加速度传感器。具体地,前端信号采集采用压电陶瓷加速度传感器,该类型传感器基于压电原理,当压电材料受到外力作用的时候,它的表面会形成电荷,电荷通过电荷放大器、测量电路的放大以及变换阻抗以后,被转换成为与所受到的外力成正比关系的电量输出。可以用来测量力以及可以转换成为力的非电物理量,比如加速度和压力。其变化规律可以通过实验掌握。其采用的主要的压电材料是磷酸二氢胺、酒石酸钾钠和石英,其中酒石酸钾钠具有很大的压电系数和压电灵敏度,特别适合于微弱振动信号的采集。压电陶瓷加速度传感器具有重量较轻、工作可靠、结构很简单、信噪比很高、灵敏度很高、信频宽以及成本低廉等优点。本发明在实际环境中测试了泄漏噪声信号,确定了传感器需要达到的性能指标,如下表2所示。表2传感器指标要求在本发明实施例中,燃气管线泄漏点定位装置由一台主机和前端采集装置组成,主机即为所述主控模块,用来收发指令和数据、执行算法流程、显示计算结果等;前端采集装置由传感器和控制器组成,每台装置包含3组传感器和控制器,即第一传感器、第一控制模块、第二传感器、第二控制模块、第三传感器、第三控制模块。主机是整个装置的中枢,控制整个装置的运转。整个装置在现场布设好以后,通过主机下发数据采集指令,使得前端3组控制器分别利用传感器采集泄漏噪声信号和干扰信号。信号采集完成后,主机下发数据上传指令,3组控制器上传采集到的信号。主机调用算法接口进行计算,并通过用户软件显示泄漏判断结果和泄漏点定位信息。控制器完全受主机控制,无论是信号采集还是信号上传都受主机控制。控制器通过自身的控制电路完成主机的指令。控制器内部的供电模块给控制电路、通信模块和传感器供电。通信模块用来进行指令和数据的收发。装置的使用方法是,泄漏检测人员携带装置到达检测现场,将待检测管网按照400米有效距离要求、管井位置分布划分为若干段,利用该装置对每一段分别检测,并根据检测结果进行后续开挖和修复。本发明实施例提供的一种燃气管线泄漏点定位系统,研发和制造成本较低,有利于推广普及;同时重量较轻,便于携带;操作简单,容易上手。该方法和装置将会在各大燃气公司得到有效的推广应用。需要说明的是,术语“包括”、“包含”或者其任何其他变体意在涵盖非排他性的包含,从而使得包括一系列要素的过程、方法、商品或者设备不仅包括那些要素,而且还包括没有明确列出的其他要素,或者是还包括为这种过程、方法、商品或者设备所固有的要素。在没有更多限制的情况下,由语句“包括一个……”限定的要素,并不排除在包括所述要素的过程、方法、商品或者设备中还存在另外的相同要素。以上所述仅为本发明的实施例而已,并不用于限制本发明。对于本领域技术人员来说,本发明可以有各种更改和变化。凡在本发明的精神和原理之内所作的任何修改、等同替换、改进等,均应包含在本发明的权利要求范围之内。当前第1页1 2 3