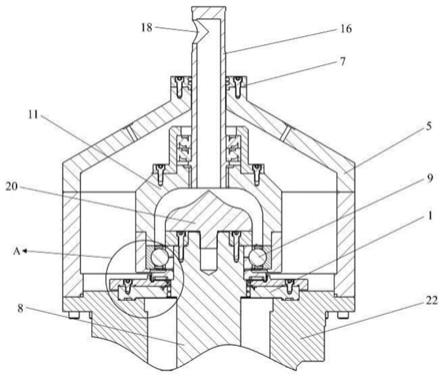
[0001]
本发明属于滚动轴承寿命试验领域,具体涉及一种滚动轴承超低温工况环境装置。
背景技术:[0002]
随着人类对于重型运载火箭需求剧增,应用于火箭发动机的超低温滚动轴承转速与承载要求越来越高,且寿命与可靠性指标愈加苛刻,该类轴承服役于液氧或者液氢所形成超低温环境中,同时承受高速重载工况,且其润滑条件极其恶劣,轴承极易由于剧烈磨损而导致失效。此外,可重复使用火箭对于该类轴承的寿命提出了更高的要求。鉴于超低温轴承寿命对于火箭发动机性能的重要性以及可重复性火箭发动机对于轴承寿命的新要求,亟待开展能够长时间运转的超低温滚动轴承寿命试验装置及试验方法研究。
[0003]
在公开号为cn201920389157.6的发明创造中公开了一种用于超低温高dn值轴承疲劳寿命的试验装置。该发明创造包括一个装置壳体,装置壳体与轴向柔性加载装置、径向柔性加载装置连接,轴向柔性加载装置、径向柔性加载装置分别与试验转子连接,试验转子包括主轴,主轴上安装有被试轴承、支承轴承、加载轴承、轴套,主轴与端盖之间通过皮碗密封件连接,壳体下方设置有三条进介质管路,壳体上方设置有开口。试验装置装配完成后,通过径向柔性加载装置和轴向柔性加载装置施加载荷,模拟液体火箭发动机涡轮泵中轴承所受载荷;冷却介质从进介质管路进入,从壳体上方开口排出,模拟超低温环境;启动试验装置运转至试验转速,模拟轴承工作转速。综上,该装置能够模拟温度、载荷和转速等条件,但由于该装置所采取的的低温介质进入方式使得该装置的冷却效率较低,冷却介质消耗量较大,且该装置被试轴承外圈位于被试轴承外套内,低温介质无法流经被试轴承外圈,被试轴承外圈冷却效果欠佳,无法完全达到火箭发动机涡轮泵轴承真实工作温度。
技术实现要素:[0004]
为克服现有技术中存在的冷却效率较低,冷却介质消耗量较大,被试轴承外圈冷却效果欠佳,无法完全达到火箭发动机涡轮泵轴承真实工作温度的不足,本发明提出了一种滚动轴承超低温工况环境模拟装置。
[0005]
本发明包括低温腔外壳、组合密封结构、低温腔密封端盖、载荷施加组件、加载轴承、加载杆、导流头和试验轴承。其中,所述低温腔外壳和主轴外壳之间有组合密封结构,并使该组合密封结构套装在滚动轴承试验装置的机械主轴上;所述组合密封结构中的分离盘固定在所述主轴外壳的上端面上。所述低温腔密封端盖安装在该低温腔外壳的上端面。所述加载杆的下端穿过所述低温腔密封端盖的中心孔装入该载荷施加组件内。所述加载轴承位于该载荷施加组件的第三载荷施加件内并套装在该加载杆上。在该加载杆的外圆周表面与所述载荷施加组件的第二载荷施加件的内圆周表面之间有加载衬套。所述试验轴承位于低温腔内,套装在该机械主轴的上端,并位于载荷施加组件的第一载荷施加件内。所述试验轴承位于所述组合密封结构的上方。
[0006]
所述由所述低温腔外壳、主轴外壳、组合密封结构和低温腔密封端盖构成了封闭的滚动轴承超低温工况环境模拟装置的低温腔;通过位于腔体内的载荷施加组件与试验轴承将该低温腔的腔体分隔为内腔室与外腔室,形成了双层结构的低温腔。
[0007]
所述低温腔外壳由锥体段和直筒段组成。所述锥体段固定在直筒段的上端面。该锥体段上端中心有用于安装加载杆的过孔;在该低温腔外壳上均布有四个低温介质出口。所述直筒段的内径大于所述组合密封结构的外径。
[0008]
所述组合密封结构套装在所述机械主轴的上端、位于所述载荷施加组件中的第一载荷施加件的下方,并固定在所述主轴外壳的上端面。该组合密封结构中的叶封轮与该机械主轴键连接。该叶封轮的下端位于该密封盘上表面的凹槽内,并使该叶封轮的外圆周表面与该密封盘的内圆周表面之间间隙配合;由轴向排布在所述密封盘凹槽内表面的环形密封槽构成了该密封盘与叶封轮之间的迷宫式密封。在该叶封轮的上表面与位于所述第一载荷施加件内的所述试验轴承之间安装有垫片。
[0009]
所述分离盘中心有所述机械主轴的过孔,并且二者之间为间隙配合。在该分离盘内圆周表面有径向的凹槽,在该凹槽内安装有密封圈,并通过密封圈压盖固紧;该密封圈压盖固定在该分离盘上表面;在该分离盘下表面有密封圈槽。
[0010]
所述密封盘上表面有用于安放所述叶封轮的凹槽。该密封盘下表面的外缘有轴向凸出的定位凸台,该定位凸台的内径与所述分离盘的外径相同;在该密封盘的下表面有安装密封圈的密封槽。在该密封盘内圆周表面有用于安装密封圈的径向凹槽;该密封盘上表面固定有密封圈压盖。所述密封盘的内表面与机械主轴的外表面间隙配合。
[0011]
所述载荷施加组件包括第一载荷施加件、第二载荷施加件、第三载荷施加件和加载轴承。其中:所述第三载荷施加件固定在第二载荷施加件的上端。所述第一载荷施加件固定在该第二载荷施加件的下端。两个加载轴承位于所述第三载荷施加件内。所述加载杆的下端装入加载轴承内,并伸入至第二载荷施加件上端的轴孔内。所述第二载荷施加件上端的轴孔表面与该加载杆外圆周表面之间安装有加载衬套。该加载衬套的外圆周表面与第二载荷施加件上端的轴孔的内表面干涉配合,加载衬套的内圆周表面与加载杆的外圆周表面间隙配合。所述试验轴承安放在该第一载荷施加件内。
[0012]
所述第一载荷施加件下端的内圆周表面有径向凸出的定位止口,用于试验轴承的定位和载荷施加。该第一载荷施加件的外径与所述第二载荷施加件的最大外径相同,该第一载荷施加件的内径与所述试验轴承外圈的外径相同。
[0013]
所述第二载荷施加件的下端为敞口状,上端有端盖,并且所述端盖的中心有所述加载杆的安装孔,该安装孔的内径与加载衬套的外径相同;该第二载荷施加件下端的外圆周表面为阶梯状,在该第二载荷施加件的下端形成了与所述第一载荷施加件配合的定位止口。所述第二载荷施加件的内径大于所述导流头的最大外径,在该导流头与第二载荷施加件内表面之间形成了低温介质的流动通道。
[0014]
所述第三载荷施加件的下端为敞口,在该下端外圆周表面有连接所述第二载荷施加件的法兰;该第三载荷施加件上端盖的中心有所述加载杆的安装孔。所述第三载荷施加件的内径与所述加载轴承外圈的外径相同。
[0015]
所述加载杆为一端封闭的中空杆状。该加载杆的内孔为低温介质的流动通道,在该加载杆上设置有低温介质入口。所述加载杆下端开口的中心与固定在机械主轴的上端端
面的导流头的中心相对应。在靠近该加载杆下端的外圆周表面有径向凸出的加载传力凸台;该加载传力凸台的上表面与所述加载轴承的下表面贴合;该加载传力凸台的外径与该加载轴承内圈的外径相同。
[0016]
所述导流头外形根据低温腔流场分析设计,能够使低温介质更好的导向试验轴承,提高冷却效果。导流头上端的外圆周表面为锥段;该锥段的锥度为102
°
。在该锥段下表面的中心有轴向的等径段,该等径段的直径与所述压盖的外径相同。在该导流头下端面的中心有轴向凸出的连接杆。所述连接杆通过螺纹安装在所述机械主轴上端面。
[0017]
低温介质从低温介质入口进入加载杆并流入低温腔内腔室,然后通过导流头直接流向试验轴承,随后汇入低温腔外腔室并完全浸没试验轴承,最终从低温介质出口排出,从而模拟超低温环境。
[0018]
在试验轴承内圈的下端面与组合密封结构中的叶封轮的上表面之间有垫片,并使该垫片的上表面与所述试验轴承内圈的下表面干涉配合,该垫片的下表面与叶封轮的上表面干涉配合,该垫片的内圆周表面与机械主轴的外圆周表面干涉配合;通过所述垫片防止叶封轮与试验轴承之间相互摩擦。
[0019]
为能够实现超低温轴承长时间测试,本发明的加载杆为一端封闭的中空杆状,其上设置有低温介质入口,低温介质从该低温介质入口进入低温腔内腔室。同时,加载杆上还设置有加载传力凸台,用于向试验轴承传递载荷。因此,该加载杆同时起到充当低温介质流动通道和传递载荷的作用,结构紧凑独特,节省空间。
[0020]
本发明中的导流头基于低温腔流场分析设计,其上端为102
°
的锥段。该导流头能够优化低温腔流场,同时将低温介质直接导向试验轴承,提高了冷却效率。
[0021]
本发明低温腔采用双层结构,分为内腔室与外腔室,能够保证试验轴承外圈浸没在低温介质中,提高试验轴承冷却效果,更加真实的模拟火箭发动机涡轮泵轴承的实际超低温工况环境。在所述低温环境腔与主轴油气润滑腔体之间采用组合密封结构进行隔离,该组合密封结构由叶封轮密封、迷宫式密封和密封圈密封三种形式组合,能够有效阻止低温介质和润滑介质的泄露与交换,实现超低温高压腔与常温低压腔界面密封;同时,组合密封结构具有结构紧凑,节约空间的优点。
[0022]
如图19所示,本发明中低温介质通过中空的加载杆进入低温腔内腔室,而后经过导流头结构直接导向试验轴承,随后流入低温腔外腔室并完全浸没试验轴承,最终从低温介质出口排出。如图20所示,这样的低温介质进入方式和低温腔双层结构可以使试验轴承完全浸没在低温介质中,提高试验轴承冷却效果,降低低温介质用量,节约试验成本。
附图说明
[0023]
图1为滚动轴承超低温工况环境模拟装置的剖视图;
[0024]
图2为低温腔外壳的正视图;
[0025]
图3为低温腔外壳的俯视图;
[0026]
图4为低温腔外壳的局部剖视图;
[0027]
图5为载荷施加组件的结构示意图;
[0028]
图6为载荷施加组件的剖视图;
[0029]
图7为加载杆的剖视图;
[0030]
图8为加载衬套的结构示意图;
[0031]
图9为组合密封结构的结构示意图;
[0032]
图10为组合密封结构的剖视图;
[0033]
图11为图1中a处组合密封结构的结构关系与配合关系图;
[0034]
图12为叶封轮的结构示意图;
[0035]
图13为叶封轮的剖视图;
[0036]
图14为密封盘的结构示意图;
[0037]
图15为密封盘的剖视图;
[0038]
图16为分离盘的结构示意图;
[0039]
图17为分离盘的剖视图;
[0040]
图18为低温介质流动路径图;
[0041]
图19为低温腔流动迹线模拟图;
[0042]
图20为低温腔温度场模拟图。
[0043]
其中;1.组合密封结构;2.分离盘;3.密封盘;4.叶封轮;5.低温腔外壳;6.低温介质出口;7.低温腔密封端盖;8.机械主轴;9试验轴承;10.压盖;11.载荷施加组件;12.第一载荷施加件;13.第二载荷施加件;14.第三载荷施加件;15.加载轴承;16.加载杆;17.加载传力凸台;18.低温介质入口;19.加载衬套;20.导流头;21.垫片;22.主轴外壳。
具体实施方式
[0044]
本实施例是一种滚动轴承超低温工况环境模拟装置,包括低温腔外壳5、组合密封结构1、低温腔密封端盖7、载荷施加组件11、加载轴承15、加载杆16、导流头20、试验轴承9、机械主轴8和主轴外壳22。
[0045]
其中,所述低温腔外壳5与所述主轴外壳22固定连接。所述机械主轴8上端处在低温腔外壳5内,剩余部分位于主轴外壳22内。所述低温腔外壳5和主轴外壳22之间设置有组合密封结构1,所述组合密封结构1套装在机械主轴8上,所述组合密封结构1中的分离盘2固定在所述主轴外壳22的上端面上。所述低温腔密封端盖7安装在该低温腔外壳5的上端面。所述加载杆16的下端穿过所述低温腔密封端盖7的中心孔装入该载荷施加组件11内。所述加载轴承15位于该载荷施加组件11的第三载荷施加件14内并套装在该加载杆16上。在该加载杆16的外圆周表面与所述载荷施加组件11的第二载荷施加件13的内圆周表面之间有加载衬套19。所述试验轴承9位于低温腔内,套装在该机械主轴8的上端,并位于载荷施加组件11的第一载荷施加件12内;通过压盖10将该试验轴承9固定。所述试验轴承9位于所述组合密封结构1的上方,所述试验轴承9内圈的下端面与组合密封结构1中的叶封轮4的上表面之间设置有垫片21。
[0046]
本实施例中,由低温腔外壳5、主轴外壳22、组合密封结构1和低温腔密封端盖7构成了封闭的滚动轴承超低温工况环境模拟装置的低温腔,位于腔体内的载荷施加组件11与试验轴承9将该低温腔的腔体分隔为内腔室与外腔室,形成了双层结构的低温腔。
[0047]
所述低温腔外壳5由锥体段和直筒段组成。所述锥体段固定在直筒段的上端面。该锥体段上端中心有用于安装加载杆16的过孔;在该低温腔外壳5上均布有四个低温介质出口6。所述直筒段的内径大于所述组合密封结构1的外径。
[0048]
所述组合密封结构1套装在所述机械主轴8的上端、位于所述载荷施加组件11中的第一载荷施加件12的下方,并固定在所述主轴外壳22的上端面。该组合密封结构1中的叶封轮4与该机械主轴键连接。该叶封轮的下端位于该密封盘上表面的凹槽内,并使该叶封轮的外圆周表面与该密封盘的内圆周表面之间间隙配合;由轴向排布在所述密封盘凹槽内表面的环形密封槽构成了该密封盘与叶封轮之间的迷宫式密封。在该叶封轮的上表面与位于所述第一载荷施加件12内的所述试验轴承9之间安装有垫片21,该垫片的上表面与所述试验轴承内圈的下表面干涉配合,该垫片的下表面与叶封轮的上表面干涉配合,该垫片的内圆周表面与机械主轴的外圆周表面干涉配合;通过所述垫片21防止叶封轮与试验轴承9之间相互摩擦。
[0049]
与滚动轴承试验装置中的机械主轴8装配时,该组合密封结构1中的叶封轮4与该机械主轴8通过键连接。
[0050]
所述分离盘2为圆盘状,该分离盘2中心有所述机械主轴8的过孔,并且二者之间为间隙配合。在该分离盘2内圆周表面有径向的凹槽,在该凹槽内安装有密封圈,并通过密封圈压盖固紧;该密封圈压盖固定在该分离盘2上表面;在该分离盘下表面有密封圈槽。
[0051]
所述密封盘3亦为中空圆盘状。该密封盘3上表面为阶梯面,有用于安放所述叶封轮4的凹槽。该密封盘3下表面的外缘有轴向凸出的定位凸台,该定位凸台的内径与所述分离盘2的外径相同;在该密封盘3的下表面有安装密封圈的密封槽。
[0052]
所述密封盘3的内表面与机械主轴8的外表面间隙配合。在该密封盘3内圆周表面有用于安装密封圈的径向凹槽;该密封盘3上表面固定有密封圈压盖,通过该密封圈压盖将密封圈固紧。
[0053]
所述叶封轮4采用现有技术。叶封轮4内圆周表面上设置有用于与所述机械主轴8键连接的凹槽。
[0054]
本实施例中,通过所述组合密封结构1实现了叶封轮密封、迷宫式密封和密封圈密封三种形式的组合密封,能够有效阻止低温介质和润滑介质的泄漏与交换,实现超低温高压与常温低压界面密封;同时,组合密封结构1设计紧凑,节约空间。
[0055]
所述载荷施加组件11包括第一载荷施加件12、第二载荷施加件13、第三载荷施加件14和加载轴承15。其中:所述第三载荷施加件14位于第二载荷施加件13的上端,并通过螺栓将二者固连。所述第一载荷施加件12位于该第二载荷施加件13的下端,并通过螺栓将二者固连。两个加载轴承15位于所述第三载荷施加件14内。所述加载杆16的下端装入加载轴承15内,并伸入至第二载荷施加件13上端的轴孔内。所述第二载荷施加件13上端的轴孔表面与该加载杆16外圆周表面之间安装有加载衬套19。该加载衬套19的外圆周表面与第二载荷施加件13上端的轴孔的内表面干涉配合,加载衬套19的内圆周表面与加载杆16的外圆周表面间隙配合。所述试验轴承9安放在该第一载荷施加件12内。试验时,加载机构向加载杆16施加拉力;该加载杆16通过加载轴承15将力传递给第三载荷施加件14,再经第二载荷施加件13和第一载荷施加件12传递至试验轴承9,完成加载。
[0056]
所述第一载荷施加件12为圆环状。该第一载荷施加件12下端的内圆周表面有径向凸出的定位止口,用于试验轴承9的定位和载荷施加。该第一载荷施加件12的外径与所述第二载荷施加件13的最大外径相同,该第一载荷施加件12的内径与所述试验轴承9外圈的外径相同。
[0057]
所述第二载荷施加件13为圆筒状。该第二载荷施加件13的下端为敞口状,上端有端盖,并且所述端盖的中心有所述加载杆16的安装孔,该安装孔的内径与加载衬套19的外径相同;该第二载荷施加件13下端的外圆周表面为阶梯状,在该第二载荷施加件13的下端形成了与所述第一载荷施加件12配合的定位止口。所述第二载荷施加件13的内径大于所述导流头20的最大外径,在该导流头20与第二载荷施加件13内表面之间形成了低温介质的流动通道。
[0058]
所述第三载荷施加件14亦为圆筒状。该第三载荷施加件14的下端为敞口,在该下端外圆周表面有连接所述第二载荷施加件13的法兰;该第三载荷施加件14上端盖的中心有所述加载杆16的安装孔。所述第三载荷施加件14的内径与所述加载轴承15外圈的外径相同。
[0059]
所述加载杆16为一端封闭的中空杆状。该加载杆16的内孔为低温介质的流动通道,在该加载杆16上设置有低温介质入口18。所述加载杆16下端开口的中心与固定在机械主轴8的上端端面的导流头20的中心相对应。在靠近该加载杆16下端的外圆周表面有径向凸出的加载传力凸台17;该加载传力凸台17的上表面与所述加载轴承15的下表面贴合;该加载传力凸台17的外径与该加载轴承15内圈的外径相同。
[0060]
所述导流头20外形根据低温腔流场分析设计,能够使低温介质更好的导向试验轴承,提高冷却效果。本实施例中,导流头20为回转体。该导流头20上端的外圆周表面为锥段;该锥段的锥度为102
°
。在该锥段下表面的中心有轴向的等径段,该等径段的直径与所述压盖10的外径相同。在该导流头20下端面的中心有轴向凸出的连接杆。所述连接杆通过螺纹安装在所述机械主轴8上端面的螺纹孔内。
[0061]
如图18所示,箭头表示低温介质的流动路径。低温介质从低温介质入口18进入加载杆16并流入低温腔内腔室,然后通过导流头20直接流向试验轴承9,随后汇入低温腔外腔室并完全浸没试验轴承9,最终从低温介质出口6排出,从而模拟超低温环境。