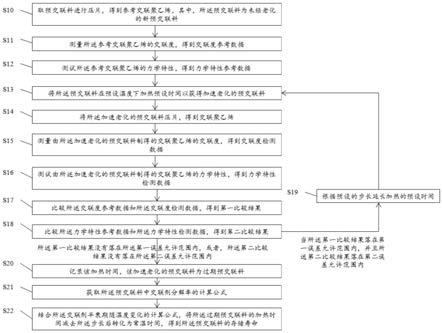
1.本发明涉及高压交流电缆绝缘料性能测试领域,尤其涉及一种高压交流电缆绝缘用预交联料存储寿命检测方法。
背景技术:2.高压交流电缆的绝缘层是以交联聚乙烯作为主绝缘材料,实现聚乙烯交联使用最广泛的方法为化学交联法,其原理为借助过氧化物交联剂受热分解产生的游离自由基将线性结构的聚乙烯交联为具有网状结构的交联聚乙烯,交联挤出的材料是交联聚乙烯预交联料。预交联料的生产工艺为在130
‑
250℃的混炼温度下向聚乙烯中加入质量分数为0.2%的抗氧剂,在螺杆混炼机内混炼均匀后再在110
‑
120℃下的混炼温度下加入质量分数为2%的交联剂,通常为过氧化二异丙苯(dicumyl peroxide,dcp),混炼均匀后再经螺杆挤出机挤出并切粒,经振动筛脱水后形成预交联料成品。
3.交联剂dcp是强氧化剂,在预交联粒投入电缆制造环节之前的存储过程中,会有一定量的dcp自发分解掉,导致预交联料中的dcp含量下降。在预交联料的正式交联挤出中,dcp是交联反应的引发剂,对交联反应的效率及最终产品的交联密度有显著影响,所以存储时间不同的预交联料会由于dcp含量的不同存在活性上的差异,直接影响到成品电缆绝缘层的性能。
4.因此,预交联料的活性及存储寿命对电缆绝缘层的性能至关重要。但目前还没有成熟的检测方法来对高压交流电缆绝缘用预交联料的活性和存储寿命做出判断,也没有对预交联料进行加速老化试验所需老化时间及温度的确定方法。
技术实现要素:5.本发明实施例提供一种高压交流电缆绝缘用预交联料存储寿命检测方法,能确定对预交联料进行加速老化试验所需老化时间及温度,以及对高压交流电缆绝缘用预交联料的存储寿命做出检测。
6.本发明一实施例提供一种高压交流电缆绝缘用预交联料存储寿命检测方法,包括:
7.取预交联料进行压片,得到参考交联聚乙烯,其中,所述预交联料为未经老化的新预交联料;
8.测量所述参考交联聚乙烯的交联度,得到交联度参考数据;
9.测试所述参考交联聚乙烯的力学特性,得到力学特性参考数据;
10.将所述预交联料在预设温度下加热预设时间以获得加速老化的预交联料;
11.将所述加速老化的预交联料压片,得到交联聚乙烯;
12.测量由所述加速老化的预交联料制得的交联聚乙烯的交联度,得到交联度检测数据;
13.测试由所述加速老化的预交联料制得的交联聚乙烯的力学特性,得到力学特性检
测数据;
14.比较所述交联度参考数据和所述交联度检测数据,得到第一比较结果;
15.比较所述力学特性参考数据和所述力学特性检测数据,得到第二比较结果;
16.当所述第一比较结果落在第一误差允许范围内,并且所述第二比较结果落在第二误差允许范围内时,根据预设的步长延长加热的预设时间,重新测试得所述交联度检测数据和所述力学特性检测数据,并与所述交联度参考数据和所述交联度检测数据进行比较,直到所述第一比较结果没有落在所述第一误差允许范围内,或者,所述第二比较结果没有落在所述第二误差允许范围内;
17.当所述第一比较结果没有落在所述第一误差允许范围内,或者,所述第二比较结果没有落在所述第二误差允许范围内时,记录该加热时间,该加速老化的预交联料为过期预交联料;
18.获取基于预交联料中交联剂分解率的计算公式:
[0019][0020]
其中,τ为在温度t下交联剂的半衰期,t为交联剂保存在温度t中经过的时间;
[0021]
结合所述交联剂半衰期随温度变化的计算公式,将所述过期预交联料的加热时间减去所述步长后转化为常温时间,得到所述预交联料的存储寿命。
[0022]
进一步的,测量所述参考交联聚乙烯的介电性能,得到介电性能参考数据,测量由所述过期预交联料制得的交联聚乙烯的介电性能,得到介电性能检测数据,比较所述介电性能参考数据和所述介电性能检测数据,验证所述过期预交联料的劣化。
[0023]
其中,所述参考交联聚乙烯的交联度和所述加速老化的预交联料制得的交联聚乙烯的交联度通过dsc测试和热延伸试验进行测量。
[0024]
而且,所述力学特性包括:拉伸强度、弹性模量及断裂伸长率;所述介电性能包括:直流电导率、交流击穿场强、相对介电常数及介质损耗角正切。
[0025]
本发明对比现有技术有如下的有益效果,本发明实施例提供了高压交流电缆绝缘用预交联料存储寿命检测方法,取新的预交联料进行压片,得到交联聚乙烯,测量其交联度、力学特性及介电性能,将测量结果作为参考值;通过加热加速老化预交联料,并测量加速老化后的预交联料压片得的交联聚乙烯的交联度、力学特性及介电性能,将该测量结果与参考值对比,当结果落在误差允许范围内时,根据预设步长加长加热时间,直到结果不全落在误差允许范围内;根据交联剂分解率计算公式与半衰期随温度变化计算公式,将加热时间减去步长后转化为常温时间,得到预交联料存储寿命。本发明通过采取加热的方式进行加速老化,缩短了试验周期、减少了材料耗费量,根据测量加速老化的预交联料制得的交联聚乙烯的交联度、力学特性,与参考交联聚乙烯的交联度、力学特性进行对比,通过结合预交联料中的交联剂分解率和半衰期随温度变化而变化的规律,从而确定对预交联料进行加速老化试验所需老化时间及温度,实现预交联料存储寿命的检测。
附图说明
[0026]
图1是本发明一实施例提供的一种高压交流电缆绝缘用预交联料存储寿命检测方法流程示意图。
具体实施方式
[0027]
下面将对本发明实施例中的技术方案进行清楚、完整地描述,显然,所描述的实施例仅仅是本发明一部分实施例,而不是全部的实施例。基于本发明中的实施例,本领域普通技术人员在没有作出创造性劳动前提下所获得的所有其他实施例,都属于本发明保护的范围。
[0028]
为说明加速老化实验参数的确定和计算方法,这里先简要介绍交联剂dcp的半衰期及分解率计算方面的理论。
[0029]
研究表明,聚乙烯的交联是一级反应,其反应动力学方程为
[0030][0031]
式(1)中v为反应速率,c为dcp浓度,k为反应速率常数。
[0032]
由式(1)可解得:
[0033]
c=c0·
e
‑
k
·
t
,(2)
[0034]
式(2)中c0为预交联料中dcp初始浓度。
[0035]
因此通过反应动力学理论可得到时刻t时,预交联料内dcp分解率x的计算公式为:
[0036][0037]
式(3)说明,dcp的分解率随保存时间延长而增大,因此会影响到预交联料的活性。而反应速率常数k的计算公式可以由阿累尼乌斯公式得到:
[0038][0039]
式(4)中r为气体常数,e为表观活化能,a为频率因子。因此在不同温度下,反应速率常数的比值为:
[0040][0041]
dcp分解半衰期τ定义为在某一环境温下dcp浓度下降为初始浓度的一半所需的时间。将τ代入dcp分解率的计算公式可解得:
[0042][0043]
将式(6)代入分解率计算公式(3)可得:
[0044][0045]
同时由dcp分解半衰期τ和反应速率常数k的关系式(6)和反应速率常数比值的计算式(5)并结合已测量出的某温度下的dcp半衰期计算得到其他温度下预交联料中dcp的半衰期,计算公式为:
[0046][0047]
式(8)中τ0为已知某温度t0下的dcp半衰期。
[0048]
根据已有实验数据及结论可计算出常温(30℃)下dcp分解半衰期为490年,同样也能计算出其他温度下的半衰期,完整计算结果如下表1所示。
[0049]
表1不同温度下预交联料内dcp分解半衰期
[0050][0051]
结合表1数据和dcp分解率计算公式(7)便可计算得到在室温下存储一定时间后预交联料内dcp的含量。为在预交联料的加速老化实验中达到同样的dcp分解率,以实现等效室温下存储相应时长的效果,还应该同时考虑到预交联料混合体系的稳定性和老化试验时长合理性的问题。
[0052]
在此补充说明,提高存储温度的确可以加速dcp的自发分解,以实现加速老化预交联料这一目的。但同时也会影响到预交联料内的聚乙烯分子,使其由于预交联料混合体系中活性自由基数量增多自行发生微弱的交联,影响后续试验结果。但因为设定的加速老化试验温度通常小于实际交联工艺温度(约180℃),所以老化过程中引发的聚乙烯交联现象可以忽略不计。而且从化学反应原理的角度考虑,由于交联反应是放热反应,因此提高温度,反应平衡会向左移动,交联反应也会在一定程度上受到抑制,交联产物在预交联料体系内所占比例也是减小的,可以认为加速老化实验对预交联料活性的影响主要还是由dcp自发分解而不是影响了聚乙烯分子本身所带来。
[0053]
综合以上结论,我们选择70℃作为加速老化试验的试验温度。在此温度下,由表1可知dcp的分解半衰期为157天,由式(7)计算可知进行3.8小时的加速老化便可等效实现30℃下存储半年的效果,而老化77个小时(约3天)便可等效常温下存储10年。且70℃远小于交联工艺温度,因此这个老化温度兼顾了预交联料体系的稳定性和试验时长的合理性。
[0054]
参见图1,是本发明一实施例提供的一种高压交流电缆绝缘用预交联料存储寿命检测方法流程示意图。所述方法包括:
[0055]
s10、取预交联料进行压片,得到参考交联聚乙烯,其中,所述预交联料为未经老化的新预交联料。
[0056]
s11、测量所述参考交联聚乙烯的交联度,得到交联度参考数据。
[0057]
s12、测试所述参考交联聚乙烯的力学特性,得到力学特性参考数据。
[0058]
示例地,步骤s10~s12具体可以是:
[0059]
先将新出厂预交联料在180℃下交联,使用平板硫化机模压为厚度为0.2mm和1.0mm的薄片,之后使用切刀裁剪成圆形或哑铃形试样。其中0.2mm厚圆形试样用于介电性能测量,1.0mm厚哑铃形试样用于热延伸及力学性能的测量,并按照gb/t 36965
‑
2018中的dsc试验测量交联度方法得到新出厂预交联料制得交联聚乙烯试样的交联度,将测量结果作为后续评估预交联料活性和寿命的标准。
[0060]
s13、将所述预交联料在预设温度下加热预设时间以获得加速老化的预交联料。
[0061]
s14、将所述加速老化的预交联料压片,得到交联聚乙烯。
[0062]
s15、测量由所述加速老化的预交联料制得的交联聚乙烯的交联度,得到交联度检测数据。
[0063]
s16、测试由所述加速老化的预交联料制得的交联聚乙烯的力学特性,得到力学特性检测数据。
[0064]
其中,可通过dsc测试和热延伸试验测量交联度;力学特性包括拉伸强度、弹性模量及断裂伸长率;介电性能包括直流电导率、交流击穿场强、相对介电常数及介质损耗角正切。
[0065]
示例地,步骤s13~s16具体可以是:
[0066]
进行新出厂预交联料的加速老化试验。将新出厂预交联料盛放于烧杯内,烧杯置于恒温烘箱中,烘箱温度设置为70℃,进行3.8小时的加速老化,等效30℃下存储半年。完成后得到老化预交联料,在室温环境下静置24小时。之后进行压片、交联度及力学性能的测试。
[0067]
s17、比较所述交联度参考数据和所述交联度检测数据,得到第一比较结果。
[0068]
s18、比较所述力学特性参考数据和所述力学特性检测数据,得到第二比较结果。
[0069]
s19、当所述第一比较结果落在第一误差允许范围内,并且所述第二比较结果落在第二误差允许范围内时,根据预设的步长延长加热的预设时间,重新测试得所述交联度检测数据和所述力学特性检测数据,并与所述交联度参考数据和所述交联度检测数据进行比较,直到所述第一比较结果没有落在所述第一误差允许范围内,或者,所述第二比较结果没有落在所述第二误差允许范围内。
[0070]
s20、当所述第一比较结果没有落在所述第一误差允许范围内,或者,所述第二比较结果没有落在所述第二误差允许范围内时,记录该加热时间,该加速老化的预交联料为过期预交联料。
[0071]
示例地,步骤s19~s20具体可以为:若老化预交联料及试样的性能测量结果和新出厂预交联料及试样相比基本保持不变,则表明该预交联料在室温下存储半年后仍保持了良好的活性,室温下存储寿命大于半年。
[0072]
为得到该预交联料在常温下的存储寿命,以70℃下老化3.8小时为步长,即等效30℃下保存半年。逐步延长加速老化试验的老化时间,得到等效常温下保存时间更久的老化预交联料。完成延长老化时间的老化试验后进行相应材料的压片及试样交联度和力学性能测试,直至得到性能产生明显变化的试样为止。
[0073]
进一步地,本测试方法还包括测量所述参考交联聚乙烯的介电性能,得到介电性能参考数据,测量由所述过期预交联料制得的交联聚乙烯的介电性能,得到介电性能检测数据,比较所述介电性能参考数据和所述介电性能检测数据,验证所述过期预交联料的劣化。
[0074]
s21、获取基于所述预交联料中交联剂分解率的计算公式:
[0075][0076]
其中,τ为在温度t下交联剂的半衰期,t为交联剂保存在温度t中经过的时间;
[0077]
s22、结合所述交联剂半衰期随温度变化的计算公式,将所述过期预交联料的加热
时间减去所述步长后转化为常温时间,得到所述预交联料的存储寿命。
[0078]
示例地,步骤s22具体可以为:
[0079]
将交联度和力学性能性能产生明显变化的试样的加速老化时间减去一个老化时间延长的步长并进行70℃与30℃下存储时间换算后得到该预交联料在30℃下的存储寿命。
[0080]
本发明实施例提供了高压交流电缆绝缘用预交联料存储寿命检测方法,取新的预交联料进行压片,得到交联聚乙烯,测量其交联度、力学特性及介电性能,将测量结果作为参考值;通过加热加速老化预交联料,并测量加速老化后的预交联料压片得的交联聚乙烯的交联度、力学特性及介电性能,将该测量结果与参考值对比,当结果落在误差允许范围内时,根据预设步长加长加热时间,直到结果不全落在误差允许范围内;根据交联剂分解率计算公式与半衰期随温度变化计算公式,将加热时间减去步长后转化为常温时间,得到预交联料存储寿命。本发明通过采取加热的方式进行加速老化可缩短试验周期、减少材料耗费量,根据测量加速老化的预交联料制得的交联聚乙烯的交联度、力学特性,与参考交联聚乙烯的交联度、力学特性进行对比,通过结合预交联料中的交联剂分解率和半衰期随温度变化而变化的规律,从而确定对预交联料进行加速老化试验所需老化时间及温度,实现预交联料存储寿命的检测。
[0081]
以上所述是本发明的优选实施方式,应当指出,对于本技术领域的普通技术人员来说,在不脱离本发明原理的前提下,还可以做出若干改进和润饰,这些改进和润饰也视为本发明的保护范围。