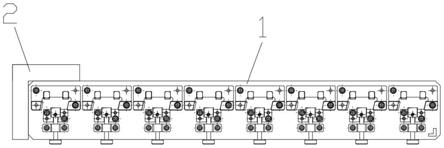
1.本发明涉及叶片检测技术领域,特别涉及基于三坐标测量机的单个工装检测多件叶片的方法。
背景技术:2.精密铸件在铸造完成后需要对其尺寸进行检测,目前对叶片的检测多是采用检测工装夹持待测叶片放入到三坐标测量机内进行检测,现有的精密铸件检测工装一次只能装夹一件,每次装夹会花费十几秒的时间,装夹完需要手动采点建立迭代坐标系,手动建立坐标系至少三分钟时间,造成整个装夹过程和建坐标浪费很多时间。
技术实现要素:3.本发明的主要目的在于提供基于三坐标测量机的单个工装检测多件叶片的方法,可以有效解决背景技术中的问题。
4.为实现上述目的,本发明采取的技术方案为:基于三坐标测量机的单个工装检测多件叶片的方法,包括如下步骤:
5.1)确定夹持工装:所述夹持工装由l型定位直角块和装夹工装组成,所述装夹工装至少为两个,所述装夹工装上设有若干个装夹槽位;
6.2)安装夹持工装:将l型定位直角块采用热熔胶固定在检测平台上,将装夹工装的一角紧靠l型定位直角块;
7.3)建立装夹槽位坐标系:采用软件程序建立装夹工装上每个装夹槽位的坐标;
8.4)建立装夹工装list:在程序的调用路径下建立list,每个list对应一个装夹工装,在使用前更换名称,更换成程序所使用的名称;
9.5)叶片测量:将装夹工装的每个装夹槽位上均装夹叶片,采用大循环测量程序基于每个装夹槽位的坐标对装夹工装上的叶片进行测量;
10.6)数据分析:将测量程序与blade叶片分析软件关联,利用blade叶片分析软件分析叶片具体参数,检测叶片叶型。
11.优选的,所述步骤1中装夹工装为两个,分别为在线检测装夹工装和线下夹持装夹工装,对应的所述步骤4中建立的list为两个,分别为list和list1,其中在线检测装夹工装为list,线下夹持装夹工装为list1。
12.优选的,所述步骤1中的装夹工装包括条板,所述条板的上端面安装若干个装夹槽位。
13.优选的,所述装夹槽位包括u槽型的卡件,所述卡件与条板固定连接,所述卡件的槽口处设有与条板固定连接带有t型滑槽的平块,所述平块内滑动连接限位紧块,所述限位紧块的侧面连接螺杆,所述螺杆螺纹连接与条板固定连接的t块。
14.优选的,每个所述条板上的装夹槽位为8个。
15.优选的,所述步骤4中的list包含有装夹槽位工位数、装夹槽位序号以及叶片模组
号。
16.与传统技术相比,本发明产生的有益效果是:本发明通过l型定位直角块对装夹工装进行定位,且装夹工装上设有的多个装夹槽位,实现一次性检测多个叶片,提高了叶片的检测效率,且采用多个装夹工装,实现轮换,充分利用时间,减少不必要的时间浪费,同时关联blade叶片分析软件,便于分析叶片参数和检测叶片叶型。
附图说明
17.图1为本发明的夹持工装结构示意图;
18.图2为本发明的装夹工装整体结构立体示意图;
19.图3为本发明的装夹工装部分结构立体示意图。
20.图中:1、装夹工装;11、条板;12、装夹槽位;121、卡件;122、平块;123、限位紧块;124、螺杆;125、t块;2、l型定位直角块。
具体实施方式
21.为使本发明实现的技术手段、创作特征、达成目的与功效易于明白了解,下面结合具体实施方式,进一步阐述本发明。
22.实施例1
23.如图1-3所示,基于三坐标测量机的单个工装检测多件叶片的方法,包括如下步骤:
24.1)确定夹持工装:所述夹持工装由l型定位直角块2和装夹工装1组成,所述装夹工装1至少为两个,所述装夹工装1上设有若干个装夹槽位3;
25.2)安装夹持工装:将l型定位直角块2采用热熔胶固定在检测平台上,将装夹工装1的一角紧靠l型定位直角块2;
26.3)建立装夹槽位坐标系:采用软件程序建立装夹工装上每个装夹槽位3的坐标;
27.建立坐标系的程序为:
[0028][0029][0030]
4)建立装夹工装list:在程序的调用路径下建立list,每个list对应一个装夹工装,在使用前更换名称,更换成程序所使用的名称;
[0031]
5)叶片测量:将装夹工装的每个装夹槽位上均装夹叶片,采用大循环测量程序基
于每个装夹槽位的坐标对装夹工装上的叶片进行测量;
[0032]
软件的大循环测量程序为:
[0033]
[0034][0035]
6)数据分析:将测量程序与blade叶片分析软件关联,利用blade叶片分析软件分析叶片具体参数,检测叶片叶型。
[0036]
本实施例中,所述步骤1中装夹工装为两个,分别为在线检测装夹工装和线下夹持装夹工装,对应的所述步骤4中建立的list为两个,分别为list和list1,其中在线检测装夹工装为list,线下夹持装夹工装为list1,在线检测装夹工装所夹持的叶片在进行检测时,线下装夹工装对叶片进行安装夹持,便于替换,节约时间,在安装装夹工装时,只需要把装夹工装的一角与l型定位直角块的直角边对其即可,定位方便,便于安装。
[0037]
本实施例中,所述步骤1中的装夹工装1包括条板11,所述条板11的上端面安装若干个装夹槽位12。
[0038]
本实施例中,所述装夹槽位12包括u槽型的卡件121,所述卡件121与条板11固定连接,所述卡件121的槽口处设有与条板11固定连接带有t型滑槽的平块122,所述平块122内滑动连接限位紧块123,所述限位紧块123的侧面连接螺杆124,所述螺杆124螺纹连接与条板11固定连接的t块125,在安装叶片时,只需要把叶片的叶根处安装在卡件121上,旋转螺杆124,使得限位紧块123抵接叶片的叶根一侧面,从而实现对叶片限位固定。
[0039]
本实施例中,每个所述条板11上的装夹槽位12为8个。
[0040]
本实施例中,所述步骤4中的list包含有装夹槽位工位数、装夹槽位序号以及叶片模组号。
[0041]
本方法能够最大限度的节约检测时间,同时降低工人的劳动强度,只需要每次将叶片安装顺序装夹在装夹工装的装夹槽位上就可以,然后把装夹工装直接放在l型直角定位块上直接检测,一次连续检测多件叶片,中间不用停顿可一次完成,且采用两个装夹工装,一上一下,充分利用时间,提高效率,减少不必要的时间浪费,并且软件程序关联了blade叶片分析软件,实现对叶片的具体参数和叶型进行检测。
[0042]
以上只通过说明的方式描述了本发明的某些示范性实施例,毋庸置疑,对于本领域的普通技术人员,在不偏离本发明的精神和范围的情况下,可以用各种不同的方式对所
描述的实施例进行修正。因此,上述附图和描述在本质上是说明性的,不应理解为对本发明权利要求保护范围的限制。
技术特征:1.基于三坐标测量机的单个工装检测多件叶片的方法,其特征在于:包括如下步骤:1)确定夹持工装:所述夹持工装由l型定位直角块和装夹工装组成,所述装夹工装至少为两个,所述装夹工装上设有若干个装夹槽位;2)安装夹持工装:将l型定位直角块采用热熔胶固定在检测平台上,将装夹工装的一角紧靠l型定位直角块;3)建立装夹槽位坐标系:采用软件程序建立装夹工装上每个装夹槽位的坐标;4)建立装夹工装list:在程序的调用路径下建立list,每个list对应一个装夹工装,在使用前更换名称,更换成程序所使用的名称;5)叶片测量:将装夹工装的每个装夹槽位上均装夹叶片,采用大循环测量程序基于每个装夹槽位的坐标对装夹工装上的叶片进行测量;6)数据分析:将测量程序与blade叶片分析软件关联,利用blade叶片分析软件分析叶片具体参数,检测叶片叶型。2.根据权利要求1所述的基于三坐标测量机的单个工装检测多件叶片的方法,其特征在于:所述步骤1中装夹工装为两个,分别为在线检测装夹工装和线下夹持装夹工装,对应的所述步骤4中建立的list为两个,分别为list和list1,其中在线检测装夹工装为list,线下夹持装夹工装为list1。3.根据权利要求1所述的基于三坐标测量机的单个工装检测多件叶片的方法,其特征在于:所述步骤1中的装夹工装包括条板,所述条板的上端面安装若干个装夹槽位。4.根据权利要求3所述的基于三坐标测量机的单个工装检测多件叶片的方法,其特征在于:所述装夹槽位包括u槽型的卡件,所述卡件与条板固定连接,所述卡件的槽口处设有与条板固定连接带有t型滑槽的平块,所述平块内滑动连接限位紧块,所述限位紧块的侧面连接螺杆,所述螺杆螺纹连接与条板固定连接的t块。5.根据权利要求3所述的基于三坐标测量机的单个工装检测多件叶片的方法,其特征在于:每个所述条板上的装夹槽位为8个。6.根据权利要求1所述的基于三坐标测量机的单个工装检测多件叶片的方法,其特征在于:所述步骤4中的list包含有装夹槽位工位数、装夹槽位序号以及叶片模组号。
技术总结本发明公开了基于三坐标测量机的单个工装检测多件叶片的方法,包括如下步骤:确定夹持工装;安装夹持工装;建立夹持工装上每个装夹槽位坐标系;建立装夹工装List;采用大循环测量程序基于每个装夹槽位的坐标对装夹工装上的叶片进行测量;将测量程序与Blade叶片分析软件关联,利用Blade叶片分析软件分析叶片具体参数,检测叶片叶型;本发明通过L型定位直角块对装夹工装进行定位,且装夹工装上设有的多个装夹槽位,实现一次性检测多个叶片,提高了叶片的检测效率,且采用多个装夹工装,实现轮换,充分利用时间,减少不必要的时间浪费,同时关联Blade叶片分析软件,便于分析叶片参数和检测叶片叶型。和检测叶片叶型。和检测叶片叶型。
技术研发人员:杨中 杜应流 程雪松 董昌盛 潘飞翔
受保护的技术使用者:安徽应流航源动力科技有限公司
技术研发日:2021.11.03
技术公布日:2022/3/11